LLC inverter design procedure for induction heating with quantitative analysis of power transfer
Induction heating has been an advanced process for industrial quenching applications, aiming
to increase the material's hardness to a desirable depth of penetration, with advantages such as
high energy conversion efficiency, clean, safe and especially localized heating. In this process, an
L coil with the right shape and size for the material to be heated will be normally used, and the
matching between the coil size and the quenched material has a great effect on heating performance as well as the operation of the power converter, because it affects the airgap in the electromagnetic-thermal energy conversion system. Although induction heating has attracted a great
deal of attention in recent years, design consideration of inductance in resonant circuits for specific
requirements is still very limited. Specifically, there remains a need for a design process that uses the
transferred power and workhead size as inputs, in practice. In this paper, the operating principle of
an LLC resonant circuit for induction heating will be explained, from which a quantitative analysis
of the transferred power to the workhead will be performed to help design the resonant circuit. An
LLC circuit design procedure will be proposed, using the results from a quantitative analysis of the
transferred power and taking into account the physical cons traints of the workhead. In addition,
a simple technique for monitoring the soft-switching state of the power switches in a resonant inverter, based on monitoring the phase difference between the resonant capacitor voltage and the
resonant circuit voltage, is also proposed. The feasibility of the proposed design process and phase
tracking algorithm will be illustrated and verified through simulation and experiments on a 2 kW,
100 kHz LLC induction heating circuit for hardening hollow steel tubes up to 4 cm diameter.
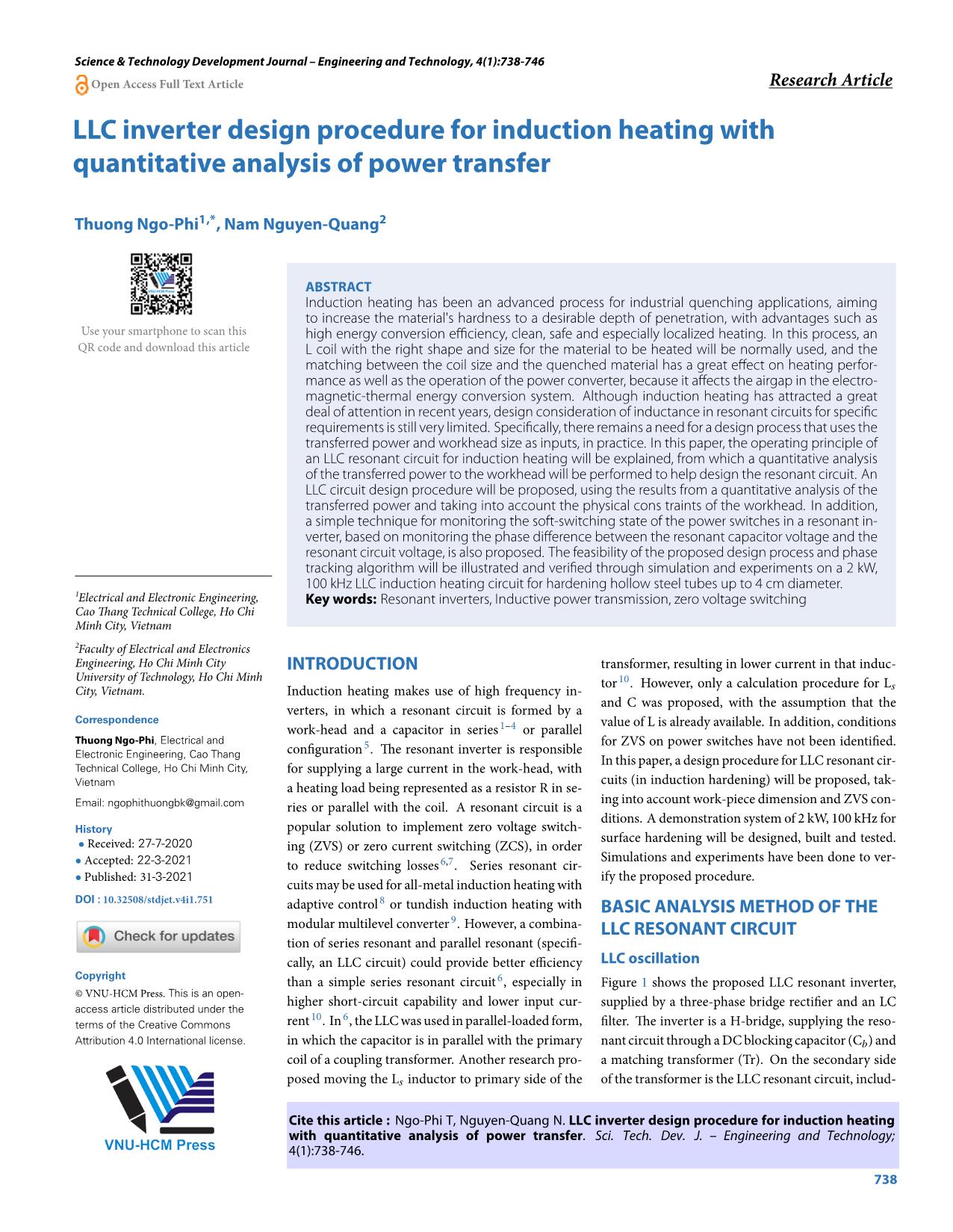
Trang 1
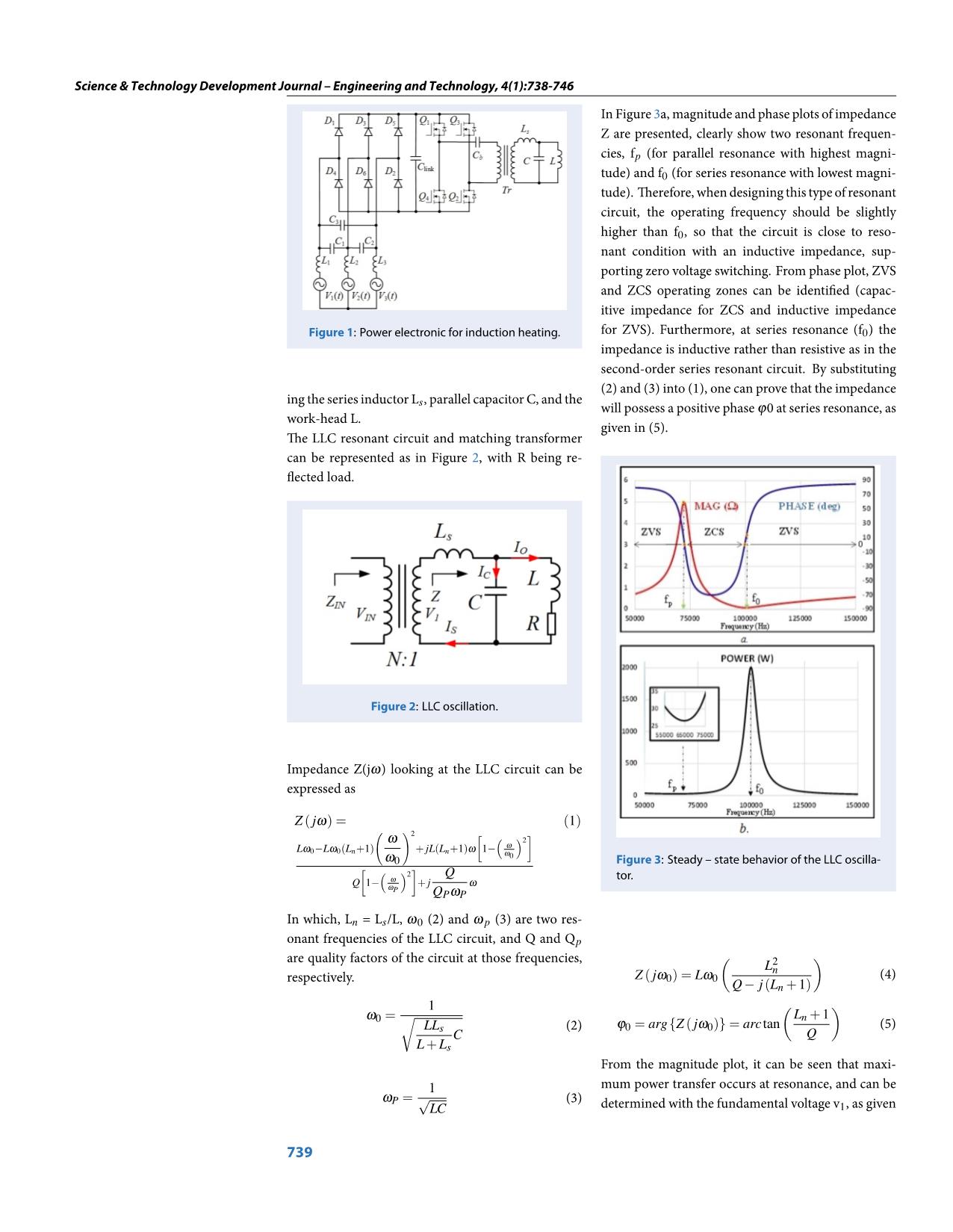
Trang 2
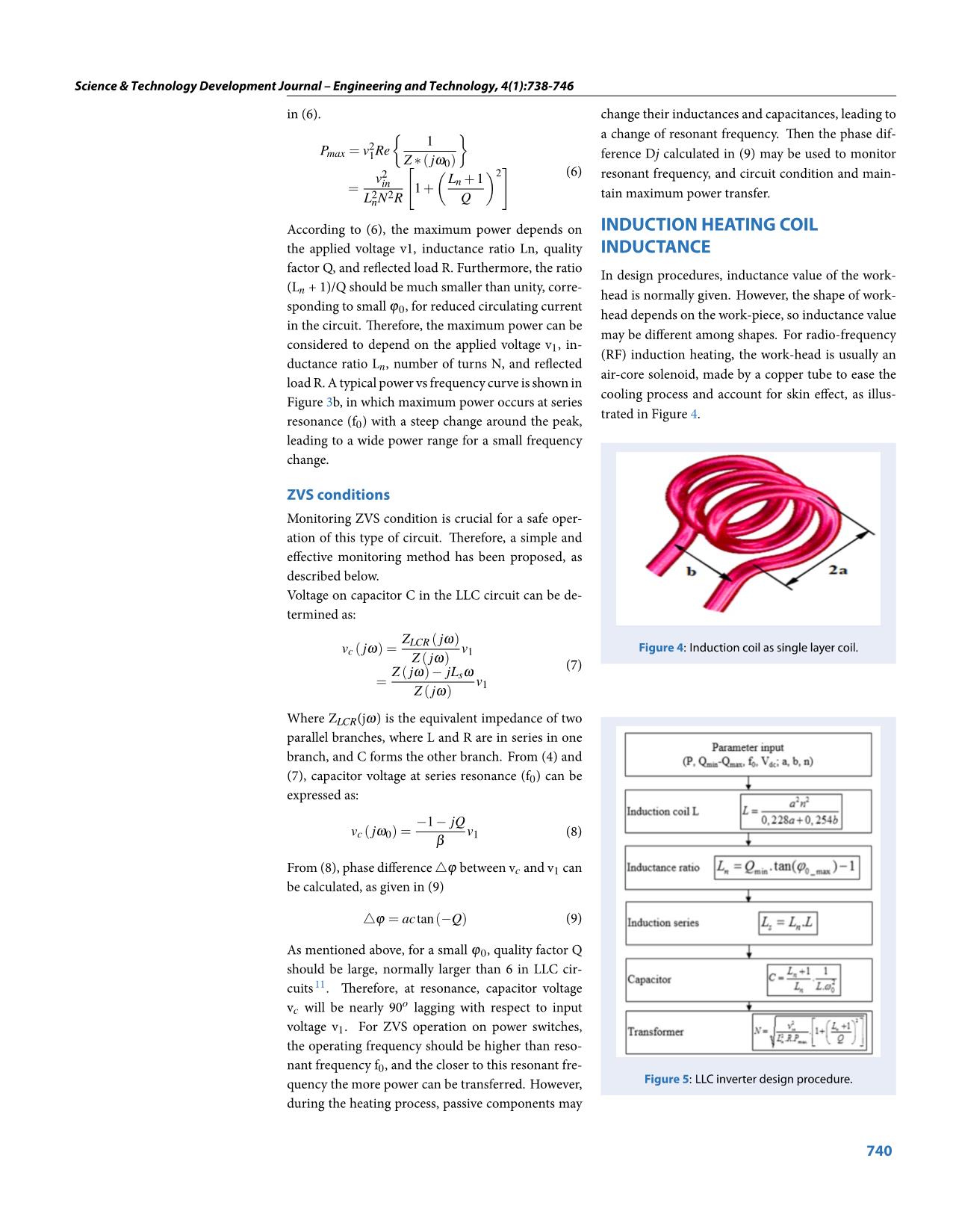
Trang 3
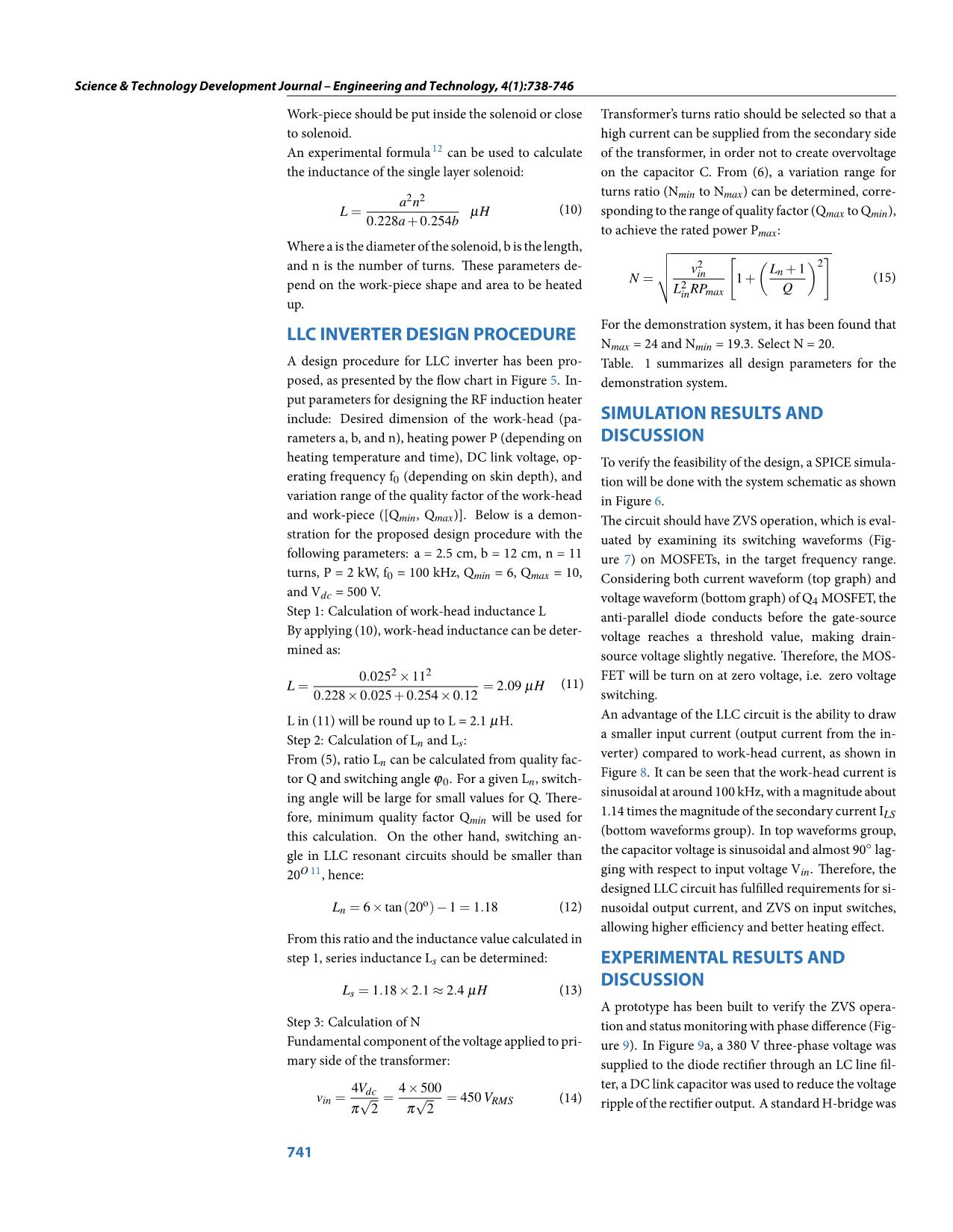
Trang 4
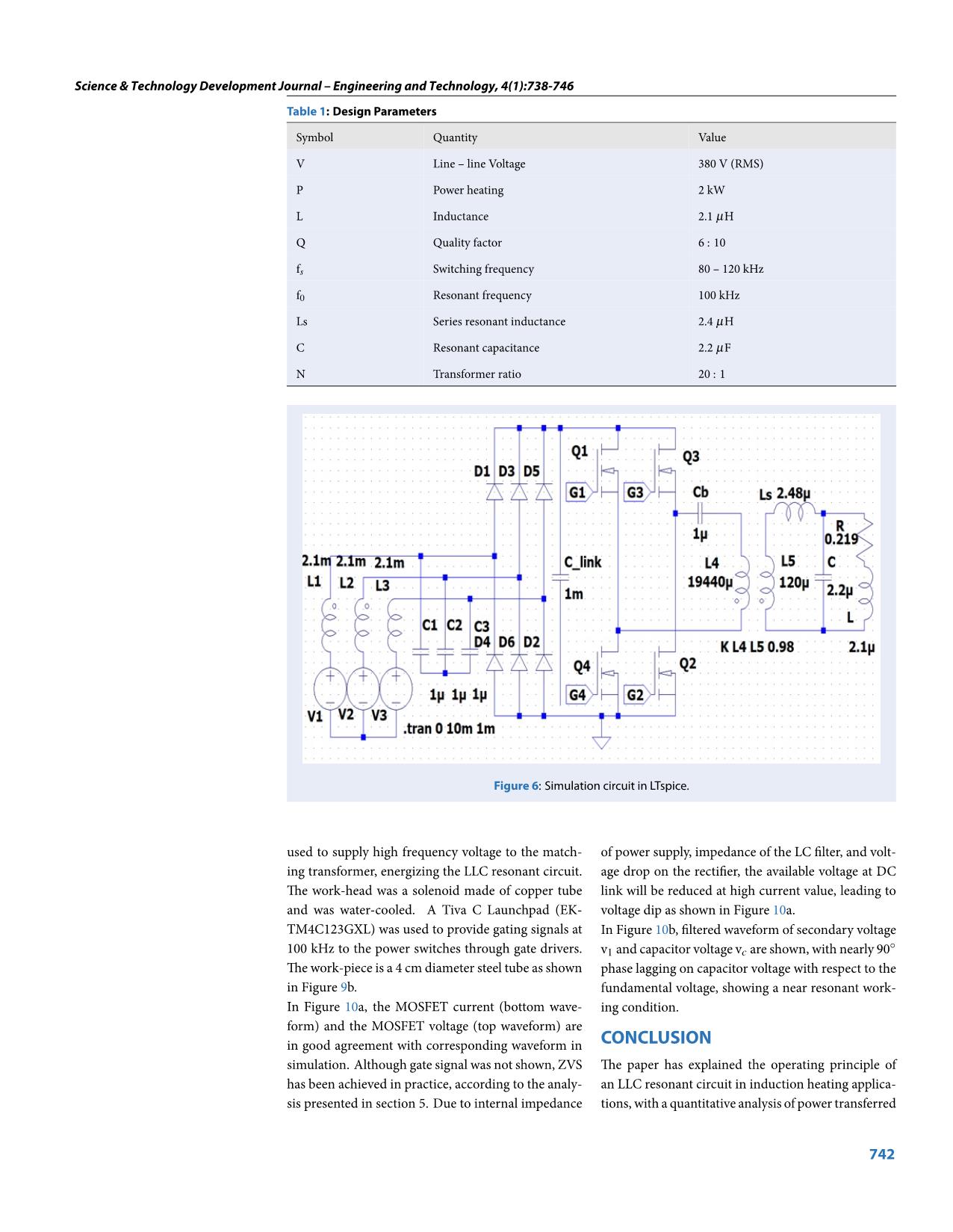
Trang 5
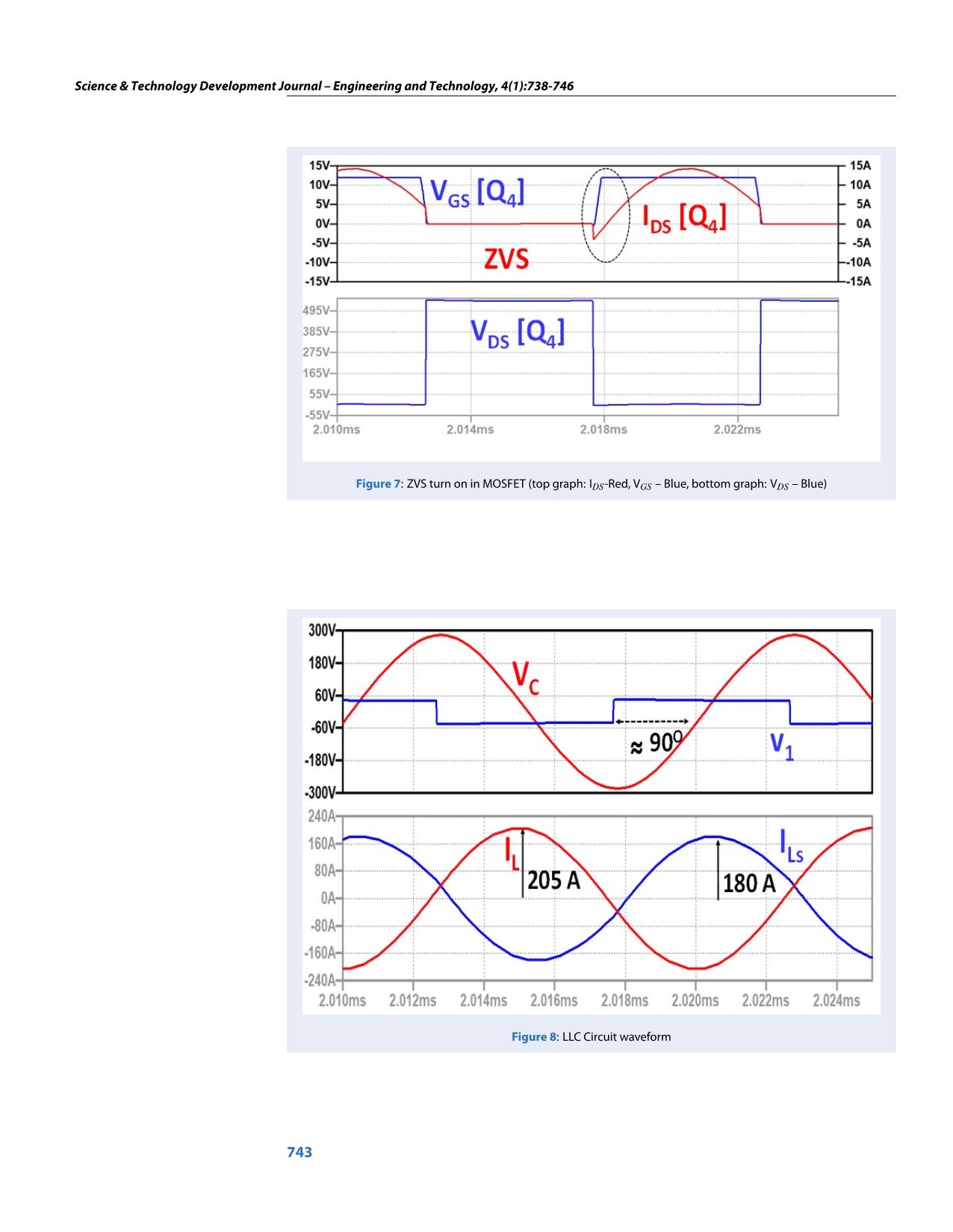
Trang 6
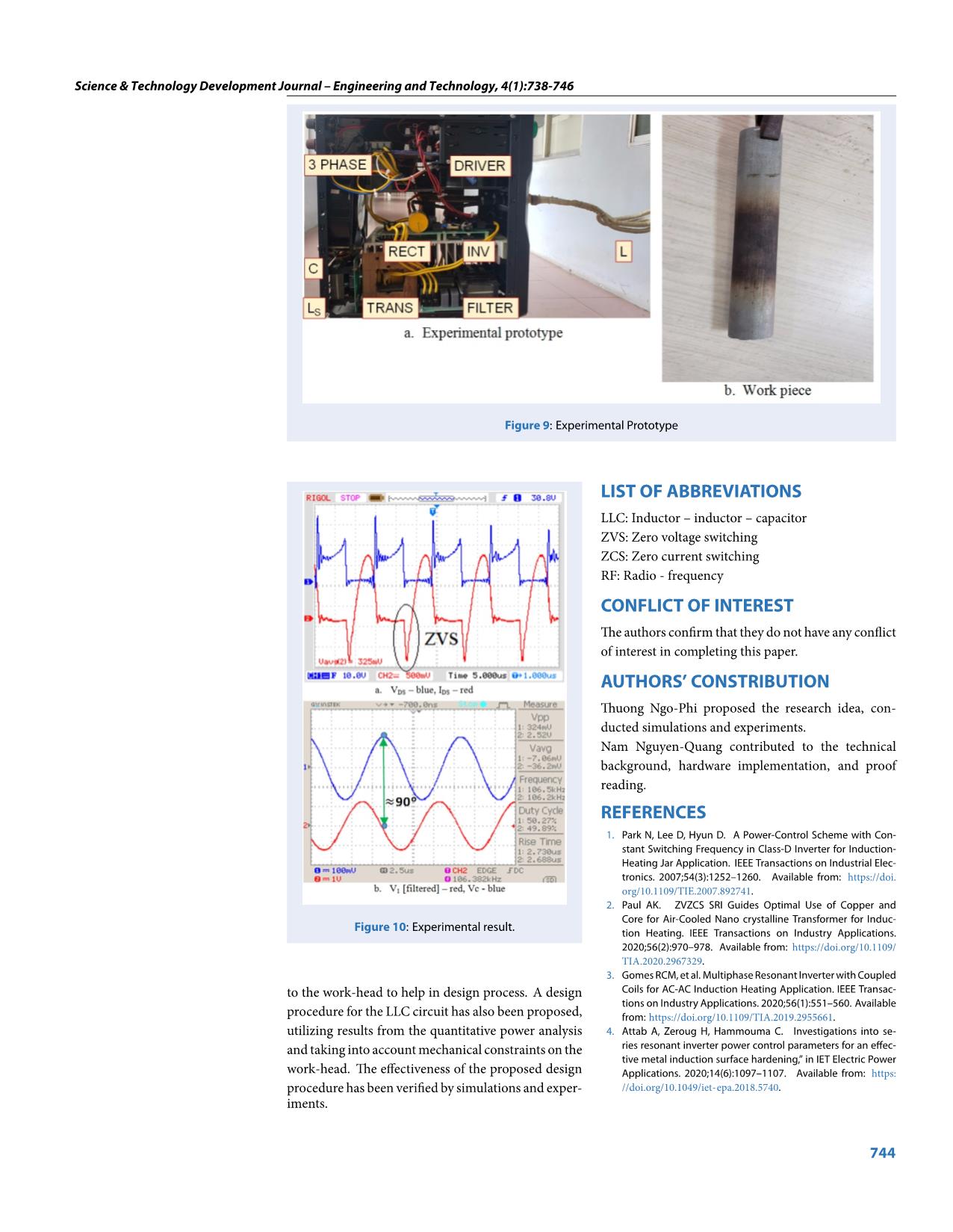
Trang 7
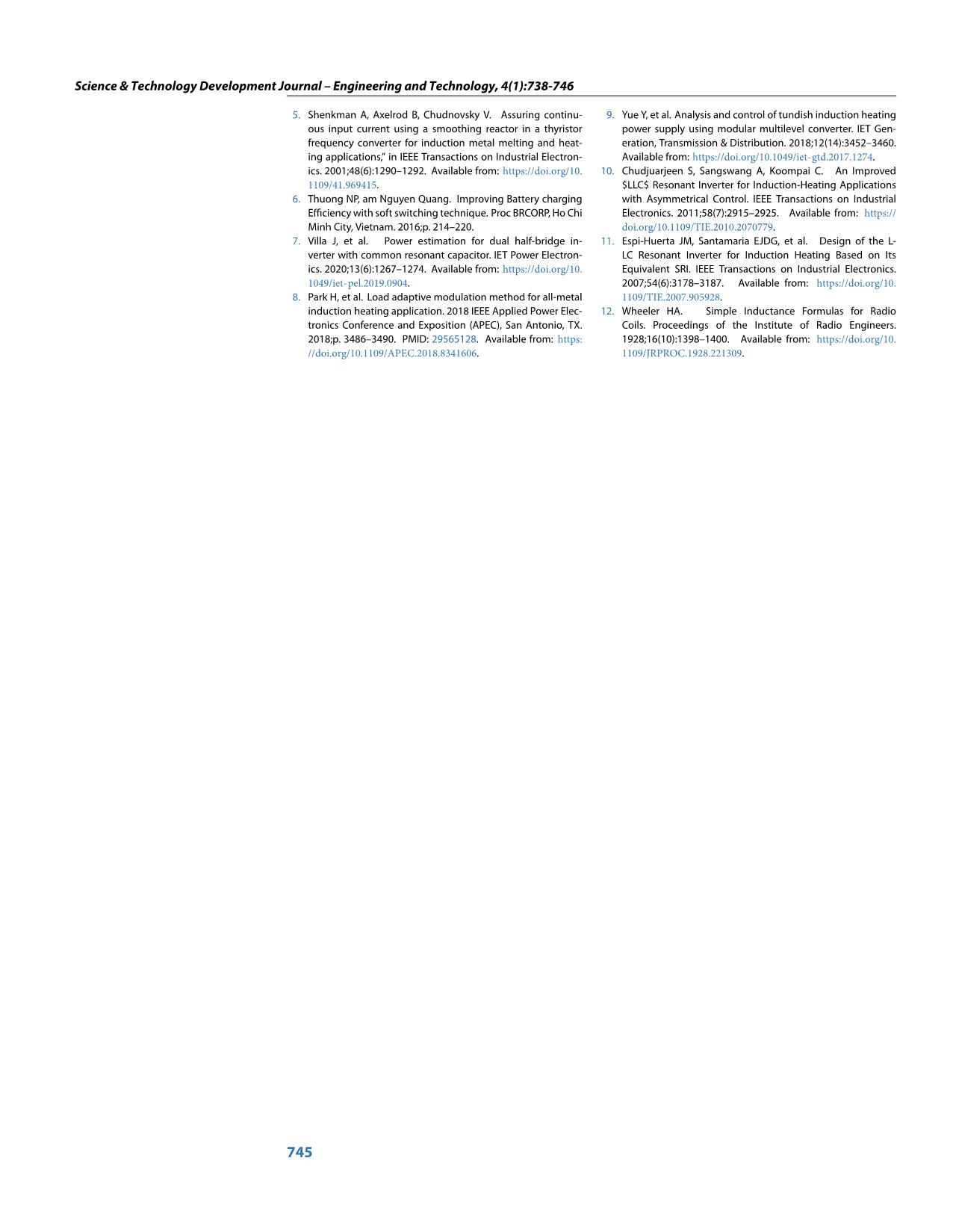
Trang 8
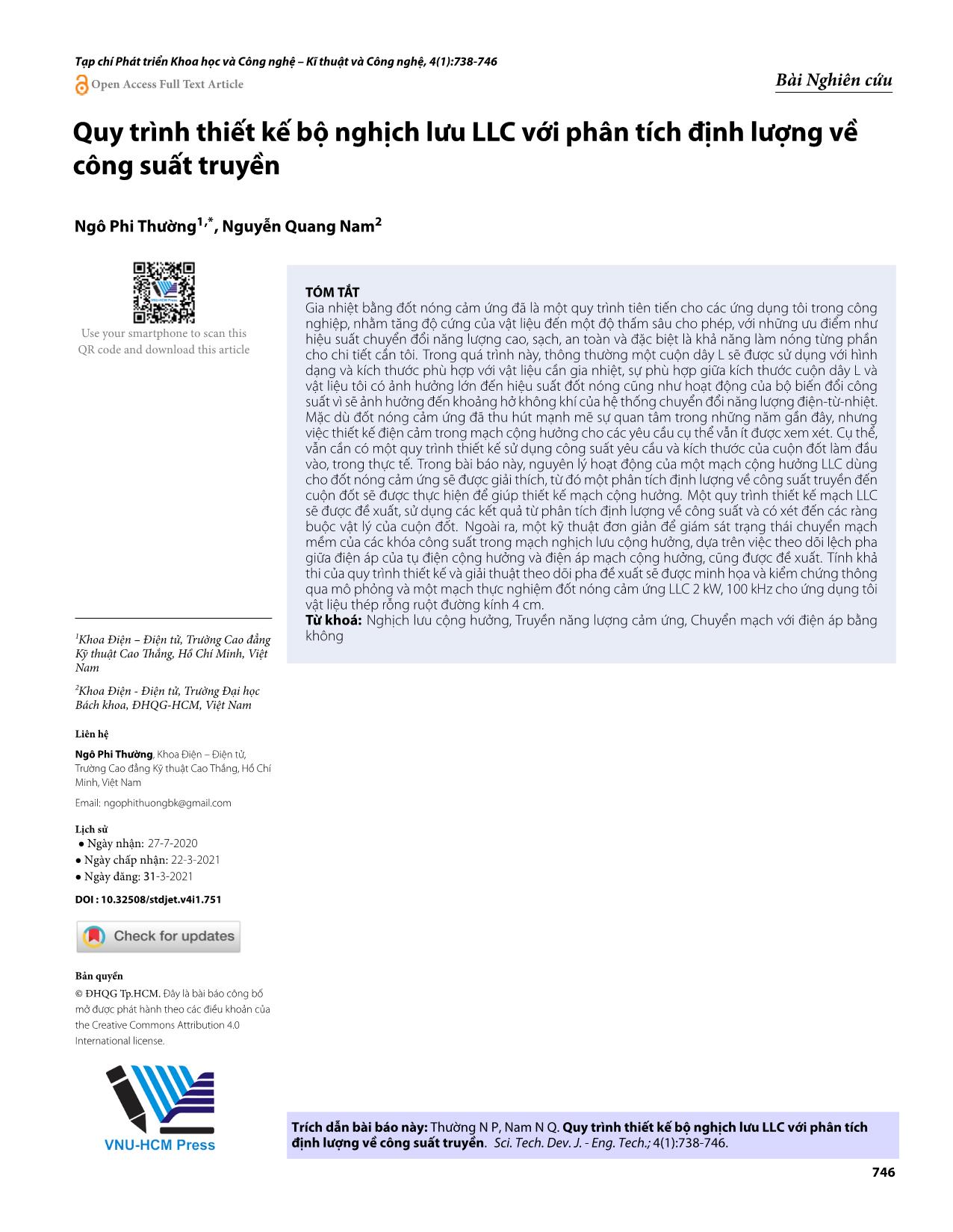
Trang 9
Tóm tắt nội dung tài liệu: LLC inverter design procedure for induction heating with quantitative analysis of power transfer
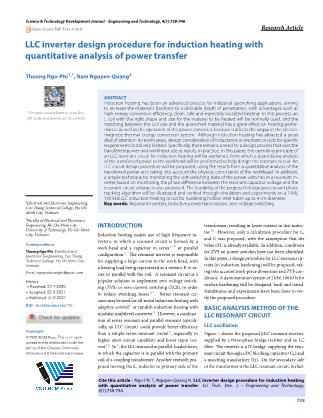
Science & Technology Development Journal – Engineering and Technology, 4(1):738-746 Open Access Full Text Article Research Article 1Electrical and Electronic Engineering, Cao Thang Technical College, Ho Chi Minh City, Vietnam 2Faculty of Electrical and Electronics Engineering, Ho Chi Minh City University of Technology, Ho Chi Minh City, Vietnam. Correspondence Thuong Ngo-Phi, Electrical and Electronic Engineering, Cao Thang Technical College, Ho Chi Minh City, Vietnam Email: ngophithuongbk@gmail.com History Received: 27-7-2020 Accepted: 22-3-2021 Published: 31-3-2021 DOI : 10.32508/stdjet.v4i1.751 Copyright © VNU-HCM Press. This is an open- access article distributed under the terms of the Creative Commons Attribution 4.0 International license. LLC inverter design procedure for induction heating with quantitative analysis of power transfer Thuong Ngo-Phi1,*, NamNguyen-Quang2 Use your smartphone to scan this QR code and download this article ABSTRACT Induction heating has been an advanced process for industrial quenching applications, aiming to increase the material's hardness to a desirable depth of penetration, with advantages such as high energy conversion efficiency, clean, safe and especially localized heating. In this process, an L coil with the right shape and size for the material to be heated will be normally used, and the matching between the coil size and the quenched material has a great effect on heating perfor- mance as well as the operation of the power converter, because it affects the airgap in the electro- magnetic-thermal energy conversion system. Although induction heating has attracted a great deal of attention in recent years, design consideration of inductance in resonant circuits for specific requirements is still very limited. Specifically, there remains a need for a design process that uses the transferred power and workhead size as inputs, in practice. In this paper, the operating principle of an LLC resonant circuit for induction heating will be explained, from which a quantitative analysis of the transferred power to the workhead will be performed to help design the resonant circuit. An LLC circuit design procedure will be proposed, using the results from a quantitative analysis of the transferred power and taking into account the physical cons traints of the workhead. In addition, a simple technique for monitoring the soft-switching state of the power switches in a resonant in- verter, based on monitoring the phase difference between the resonant capacitor voltage and the resonant circuit voltage, is also proposed. The feasibility of the proposed design process and phase tracking algorithm will be illustrated and verified through simulation and experiments on a 2 kW, 100 kHz LLC induction heating circuit for hardening hollow steel tubes up to 4 cm diameter. Key words: Resonant inverters, Inductive power transmission, zero voltage switching INTRODUCTION Induction heating makes use of high frequency in- verters, in which a resonant circuit is formed by a work-head and a capacitor in series 1–4 or parallel configuration5. The resonant inverter is responsible for supplying a large current in the work-head, with a heating load being represented as a resistor R in se- ries or parallel with the coil. A resonant circuit is a popular solution to implement zero voltage switch- ing (ZVS) or zero current switching (ZCS), in order to reduce switching losses 6,7. Series resonant cir- cuitsmay be used for all-metal induction heating with adaptive control8 or tundish induction heating with modular multilevel converter9. However, a combina- tion of series resonant and parallel resonant (specifi- cally, an LLC circuit) could provide better efficiency than a simple series resonant circuit6, especially in higher short-circuit capability and lower input cur- rent10. In6, the LLCwas used in parallel-loaded form, in which the capacitor is in parallel with the primary coil of a coupling transformer. Another research pro- posed moving the Ls inductor to primary side of the transformer, resulting in lower current in that induc- tor10. However, only a calculation procedure for Ls and C was proposed, with the assumption that the value of L is already available. In addition, conditions for ZVS on power switches have not been identified. In this paper, a design procedure for LLC resonant cir- cuits (in induction hardening) will be proposed, tak- ing into account work-piece dimension and ZVS con- ditions. A demonstration system of 2 kW, 100 kHz for surface hardening will be designed, built and tested. Simulations and experiments have been done to ver- ify the proposed procedure. BASIC ANALYSIS METHODOF THE LLC RESONANT CIRCUIT LLC oscillation Figure 1 shows the proposed LLC resonant inverter, supplied by a three-phase bridge rectifier and an LC filter. The inverter is a H-bridge, supplying the reso- nant circui ... Where ZLCR(jw) is the equivalent impedance of two parallel branches, where L and R are in series in one branch, and C forms the other branch. From (4) and (7), capacitor voltage at series resonance (f0) can be expressed as: vc ( jw0) = 1 jQ b v1 (8) From (8), phase difference4j between vc and v1 can be calculated, as given in (9) 4j = ac tan( Q) (9) As mentioned above, for a small j0, quality factor Q should be large, normally larger than 6 in LLC cir- cuits11. Therefore, at resonance, capacitor voltage vc will be nearly 90o lagging with respect to input voltage v1. For ZVS operation on power switches, the operating frequency should be higher than reso- nant frequency f0, and the closer to this resonant fre- quency the more power can be transferred. However, during the heating process, passive components may change their inductances and capacitances, leading to a change of resonant frequency. Then the phase dif- ference Dj calculated in (9) may be used to monitor resonant frequency, and circuit condition and main- tain maximum power transfer. INDUCTION HEATING COIL INDUCTANCE In design procedures, inductance value of the work- head is normally given. However, the shape of work- head depends on the work-piece, so inductance value may be different among shapes. For radio-frequency (RF) induction heating, the work-head is usually an air-core solenoid, made by a copper tube to ease the cooling process and account for skin effect, as illus- trated in Figure 4. Figure 4: Induction coil as single layer coil. Figure 5: LLC inverter design procedure. 740 Science & Technology Development Journal – Engineering and Technology, 4(1):738-746 Work-piece should be put inside the solenoid or close to solenoid. An experimental formula 12 can be used to calculate the inductance of the single layer solenoid: L= a2n2 0:228a+0:254b mH (10) Where a is the diameter of the solenoid, b is the length, and n is the number of turns. These parameters de- pend on the work-piece shape and area to be heated up. LLC INVERTER DESIGN PROCEDURE A design procedure for LLC inverter has been pro- posed, as presented by the flow chart in Figure 5. In- put parameters for designing the RF induction heater include: Desired dimension of the work-head (pa- rameters a, b, and n), heating power P (depending on heating temperature and time), DC link voltage, op- erating frequency f0 (depending on skin depth), and variation range of the quality factor of the work-head and work-piece ([Qmin, Qmax)]. Below is a demon- stration for the proposed design procedure with the following parameters: a = 2.5 cm, b = 12 cm, n = 11 turns, P = 2 kW, f0 = 100 kHz, Qmin = 6, Qmax = 10, and Vdc = 500 V. Step 1: Calculation of work-head inductance L By applying (10), work-head inductance can be deter- mined as: L= 0:0252112 0:2280:025+0:2540:12 = 2:09 mH (11) L in (11) will be round up to L = 2.1 mH. Step 2: Calculation of Ln and Ls: From (5), ratio Ln can be calculated from quality fac- tor Q and switching angle j0. For a given Ln, switch- ing angle will be large for small values for Q. There- fore, minimum quality factor Qmin will be used for this calculation. On the other hand, switching an- gle in LLC resonant circuits should be smaller than 20O 11, hence: Ln = 6 tan(20o) 1= 1:18 (12) From this ratio and the inductance value calculated in step 1, series inductance Ls can be determined: Ls = 1:182:1 2:4 mH (13) Step 3: Calculation of N Fundamental component of the voltage applied to pri- mary side of the transformer: vin = 4Vdc p p 2 = 4500 p p 2 = 450VRMS (14) Transformer’s turns ratio should be selected so that a high current can be supplied from the secondary side of the transformer, in order not to create overvoltage on the capacitor C. From (6), a variation range for turns ratio (Nmin to Nmax) can be determined, corre- sponding to the range of quality factor (Qmax toQmin), to achieve the rated power Pmax: N = vuut v2in L2inRPmax " 1+ Ln+1 Q 2# (15) For the demonstration system, it has been found that Nmax = 24 and Nmin = 19.3. Select N = 20. Table. 1 summarizes all design parameters for the demonstration system. SIMULATION RESULTS AND DISCUSSION To verify the feasibility of the design, a SPICE simula- tion will be done with the system schematic as shown in Figure 6. The circuit should have ZVS operation, which is eval- uated by examining its switching waveforms (Fig- ure 7) on MOSFETs, in the target frequency range. Considering both current waveform (top graph) and voltage waveform (bottom graph) of Q4 MOSFET, the anti-parallel diode conducts before the gate-source voltage reaches a threshold value, making drain- source voltage slightly negative. Therefore, the MOS- FET will be turn on at zero voltage, i.e. zero voltage switching. An advantage of the LLC circuit is the ability to draw a smaller input current (output current from the in- verter) compared to work-head current, as shown in Figure 8. It can be seen that the work-head current is sinusoidal at around 100 kHz, with amagnitude about 1.14 times themagnitude of the secondary current ILS (bottom waveforms group). In top waveforms group, the capacitor voltage is sinusoidal and almost 90 lag- ging with respect to input voltage Vin. Therefore, the designed LLC circuit has fulfilled requirements for si- nusoidal output current, and ZVS on input switches, allowing higher efficiency and better heating effect. EXPERIMENTAL RESULTS AND DISCUSSION A prototype has been built to verify the ZVS opera- tion and statusmonitoring with phase difference (Fig- ure 9). In Figure 9a, a 380 V three-phase voltage was supplied to the diode rectifier through an LC line fil- ter, a DC link capacitor was used to reduce the voltage ripple of the rectifier output. A standardH-bridgewas 741 Science & Technology Development Journal – Engineering and Technology, 4(1):738-746 Table 1: Design Parameters Symbol Quantity Value V Line – line Voltage 380 V (RMS) P Power heating 2 kW L Inductance 2.1 mH Q Quality factor 6 : 10 fs Switching frequency 80 – 120 kHz f0 Resonant frequency 100 kHz Ls Series resonant inductance 2.4 mH C Resonant capacitance 2.2 mF N Transformer ratio 20 : 1 Figure 6: Simulation circuit in LTspice. used to supply high frequency voltage to the match- ing transformer, energizing the LLC resonant circuit. The work-head was a solenoid made of copper tube and was water-cooled. A Tiva C Launchpad (EK- TM4C123GXL) was used to provide gating signals at 100 kHz to the power switches through gate drivers. The work-piece is a 4 cm diameter steel tube as shown in Figure 9b. In Figure 10a, the MOSFET current (bottom wave- form) and the MOSFET voltage (top waveform) are in good agreement with corresponding waveform in simulation. Although gate signal was not shown, ZVS has been achieved in practice, according to the analy- sis presented in section 5. Due to internal impedance of power supply, impedance of the LC filter, and volt- age drop on the rectifier, the available voltage at DC link will be reduced at high current value, leading to voltage dip as shown in Figure 10a. In Figure 10b, filtered waveform of secondary voltage v1 and capacitor voltage vc are shown, with nearly 90 phase lagging on capacitor voltage with respect to the fundamental voltage, showing a near resonant work- ing condition. CONCLUSION The paper has explained the operating principle of an LLC resonant circuit in induction heating applica- tions, with a quantitative analysis of power transferred 742 Science & Technology Development Journal – Engineering and Technology, 4(1):738-746 Figure 7: ZVS turn on in MOSFET (top graph: IDS-Red, VGS – Blue, bottom graph: VDS – Blue) Figure 8: LLC Circuit waveform 743 Science & Technology Development Journal – Engineering and Technology, 4(1):738-746 Figure 9: Experimental Prototype Figure 10: Experimental result. to the work-head to help in design process. A design procedure for the LLC circuit has also been proposed, utilizing results from the quantitative power analysis and taking into accountmechanical constraints on the work-head. The effectiveness of the proposed design procedure has been verified by simulations and exper- iments. LIST OF ABBREVIATIONS LLC: Inductor – inductor – capacitor ZVS: Zero voltage switching ZCS: Zero current switching RF: Radio - frequency CONFLICT OF INTEREST Theauthors confirm that they do not have any conflict of interest in completing this paper. AUTHORS’ CONSTRIBUTION Thuong Ngo-Phi proposed the research idea, con- ducted simulations and experiments. Nam Nguyen-Quang contributed to the technical background, hardware implementation, and proof reading. REFERENCES 1. Park N, Lee D, Hyun D. A Power-Control Scheme with Con- stant Switching Frequency in Class-D Inverter for Induction- Heating Jar Application. IEEE Transactions on Industrial Elec- tronics. 2007;54(3):1252–1260. Available from: https://doi. org/10.1109/TIE.2007.892741. 2. Paul AK. ZVZCS SRI Guides Optimal Use of Copper and Core for Air-Cooled Nano crystalline Transformer for Induc- tion Heating. IEEE Transactions on Industry Applications. 2020;56(2):970–978. Available from: https://doi.org/10.1109/ TIA.2020.2967329. 3. GomesRCM, et al. MultiphaseResonant InverterwithCoupled Coils for AC-AC Induction Heating Application. IEEE Transac- tions on Industry Applications. 2020;56(1):551–560. Available from: https://doi.org/10.1109/TIA.2019.2955661. 4. Attab A, Zeroug H, Hammouma C. Investigations into se- ries resonant inverter power control parameters for an effec- tive metal induction surface hardening,” in IET Electric Power Applications. 2020;14(6):1097–1107. Available from: https: //doi.org/10.1049/iet-epa.2018.5740. 744 Science & Technology Development Journal – Engineering and Technology, 4(1):738-746 5. Shenkman A, Axelrod B, Chudnovsky V. Assuring continu- ous input current using a smoothing reactor in a thyristor frequency converter for induction metal melting and heat- ing applications,” in IEEE Transactions on Industrial Electron- ics. 2001;48(6):1290–1292. Available from: https://doi.org/10. 1109/41.969415. 6. Thuong NP, am Nguyen Quang. Improving Battery charging Efficiencywith soft switching technique. Proc BRCORP, Ho Chi Minh City, Vietnam. 2016;p. 214–220. 7. Villa J, et al. Power estimation for dual half-bridge in- verter with common resonant capacitor. IET Power Electron- ics. 2020;13(6):1267–1274. Available from: https://doi.org/10. 1049/iet-pel.2019.0904. 8. Park H, et al. Load adaptive modulation method for all-metal induction heating application. 2018 IEEE Applied Power Elec- tronics Conference and Exposition (APEC), San Antonio, TX. 2018;p. 3486–3490. PMID: 29565128. Available from: https: //doi.org/10.1109/APEC.2018.8341606. 9. Yue Y, et al. Analysis and control of tundish induction heating power supply using modular multilevel converter. IET Gen- eration, Transmission & Distribution. 2018;12(14):3452–3460. Available from: https://doi.org/10.1049/iet-gtd.2017.1274. 10. Chudjuarjeen S, Sangswang A, Koompai C. An Improved $LLC$ Resonant Inverter for Induction-Heating Applications with Asymmetrical Control. IEEE Transactions on Industrial Electronics. 2011;58(7):2915–2925. Available from: https:// doi.org/10.1109/TIE.2010.2070779. 11. Espi-Huerta JM, Santamaria EJDG, et al. Design of the L- LC Resonant Inverter for Induction Heating Based on Its Equivalent SRI. IEEE Transactions on Industrial Electronics. 2007;54(6):3178–3187. Available from: https://doi.org/10. 1109/TIE.2007.905928. 12. Wheeler HA. Simple Inductance Formulas for Radio Coils. Proceedings of the Institute of Radio Engineers. 1928;16(10):1398–1400. Available from: https://doi.org/10. 1109/JRPROC.1928.221309. 745 Tạp chí Phát triển Khoa học và Công nghệ – Kĩ thuật và Công nghệ, 4(1):738-746 Open Access Full Text Article Bài Nghiên cứu 1Khoa Điện – Điện tử, Trường Cao đẳng Kỹ thuật Cao Thắng, Hồ Chí Minh, Việt Nam 2Khoa Điện - Điện tử, Trường Đại học Bách khoa, ĐHQG-HCM, Việt Nam Liên hệ Ngô Phi Thường, Khoa Điện – Điện tử, Trường Cao đẳng Kỹ thuật Cao Thắng, Hồ Chí Minh, Việt Nam Email: ngophithuongbk@gmail.com Lịch sử Ngày nhận: 27-7-2020 Ngày chấp nhận: 22-3-2021 Ngày đăng: 31-3-2021 DOI : 10.32508/stdjet.v4i1.751 Bản quyền © ĐHQG Tp.HCM. Đây là bài báo công bố mở được phát hành theo các điều khoản của the Creative Commons Attribution 4.0 International license. Quy trình thiết kế bộ nghịch lưu LLC với phân tích định lượng về công suất truyền Ngô Phi Thường1,*, Nguyễn Quang Nam2 Use your smartphone to scan this QR code and download this article TÓM TẮT Gia nhiệt bằng đốt nóng cảm ứng đã là một quy trình tiên tiến cho các ứng dụng tôi trong công nghiệp, nhằm tăng độ cứng của vật liệu đến một độ thấm sâu cho phép, với những ưu điểm như hiệu suất chuyển đổi năng lượng cao, sạch, an toàn và đặc biệt là khả năng làm nóng từng phần cho chi tiết cần tôi. Trong quá trình này, thông thường một cuộn dây L sẽ được sử dụng với hình dạng và kích thước phù hợp với vật liệu cần gia nhiệt, sự phù hợp giữa kích thước cuộn dây L và vật liệu tôi có ảnh hưởng lớn đến hiệu suất đốt nóng cũng như hoạt động của bộ biến đổi công suất vì sẽ ảnh hưởng đến khoảng hở không khí của hệ thống chuyển đổi năng lượng điện-từ-nhiệt. Mặc dù đốt nóng cảm ứng đã thu hút mạnh mẽ sự quan tâm trong những năm gần đây, nhưng việc thiết kế điện cảm trongmạch cộng hưởng cho các yêu cầu cụ thể vẫn ít được xem xét. Cụ thể, vẫn cần có một quy trình thiết kế sử dụng công suất yêu cầu và kích thước của cuộn đốt làm đầu vào, trong thực tế. Trong bài báo này, nguyên lý hoạt động của một mạch cộng hưởng LLC dùng cho đốt nóng cảm ứng sẽ được giải thích, từ đómột phân tích định lượng về công suất truyền đến cuộn đốt sẽ được thực hiện để giúp thiết kế mạch cộng hưởng. Một quy trình thiết kế mạch LLC sẽ được đề xuất, sử dụng các kết quả từ phân tích định lượng về công suất và có xét đến các ràng buộc vật lý của cuộn đốt. Ngoài ra, một kỹ thuật đơn giản để giám sát trạng thái chuyển mạch mềm của các khóa công suất trong mạch nghịch lưu cộng hưởng, dựa trên việc theo dõi lệch pha giữa điện áp của tụ điện cộng hưởng và điện áp mạch cộng hưởng, cũng được đề xuất. Tính khả thi của quy trình thiết kế và giải thuật theo dõi pha đề xuất sẽ đượcminh họa và kiểm chứng thông qua mô phỏng và một mạch thực nghiệm đốt nóng cảm ứng LLC 2 kW, 100 kHz cho ứng dụng tôi vật liệu thép rỗng ruột đường kính 4 cm. Từ khoá: Nghịch lưu cộng hưởng, Truyền năng lượng cảm ứng, Chuyển mạch với điện áp bằng không Trích dẫn bài báo này: Thường N P, Nam N Q. Quy trình thiết kế bộ nghịch lưu LLC với phân tích định lượng về công suất truyền. Sci. Tech. Dev. J. - Eng. Tech.; 4(1):738-746. 746
File đính kèm:
llc_inverter_design_procedure_for_induction_heating_with_qua.pdf