Giáo trình Chế tạo khuôn dập vuốt
I-VỊ TRÍ TÍNH CHẤT MÔ ĐUN:
-Vị trí: Mô đun chế tạo khuôn dập cắt là môn quan trọng trong nội dung đào tạo nghề Nguội chế tạo, mô đun được bố trí sau khi đã học các môn học kỹ thuật cơ sở và một số mô đun: MH16, MH25, 26; MĐ15, 17 .MĐ22.
-Tính chất: Là mô đun chuyên môn nghề bắt buộc.
II-MỤC TIÊU MÔ ĐUN:
Học xong mô đun này, người học có khả năng:
1. Kiến thức:
- Trình bày được kết cấu của chày, cối khuôn dập cắt;
- Trình bày được công nghệ chế tạo chày, cối khuôn dập cắt.
2. Kỹ năng:
- Lập được trình tự công nghệ chế tạo chày và cối cắt hợp lý;
- Lựa chọn, sử dụng thành thạo các dụng cụ gia công nguội dùng trong quá trình chế tạo chày, cối;
- Ứng dụng được các phương pháp gia công nguội để chế tạo chày cối và các chi tiết cơ bản của khuôn dập cắt đạt yêu cầu kỹ thuật.
- Gia công được chày, cối và các chi tiết cơ bản trên máy cắt dây.
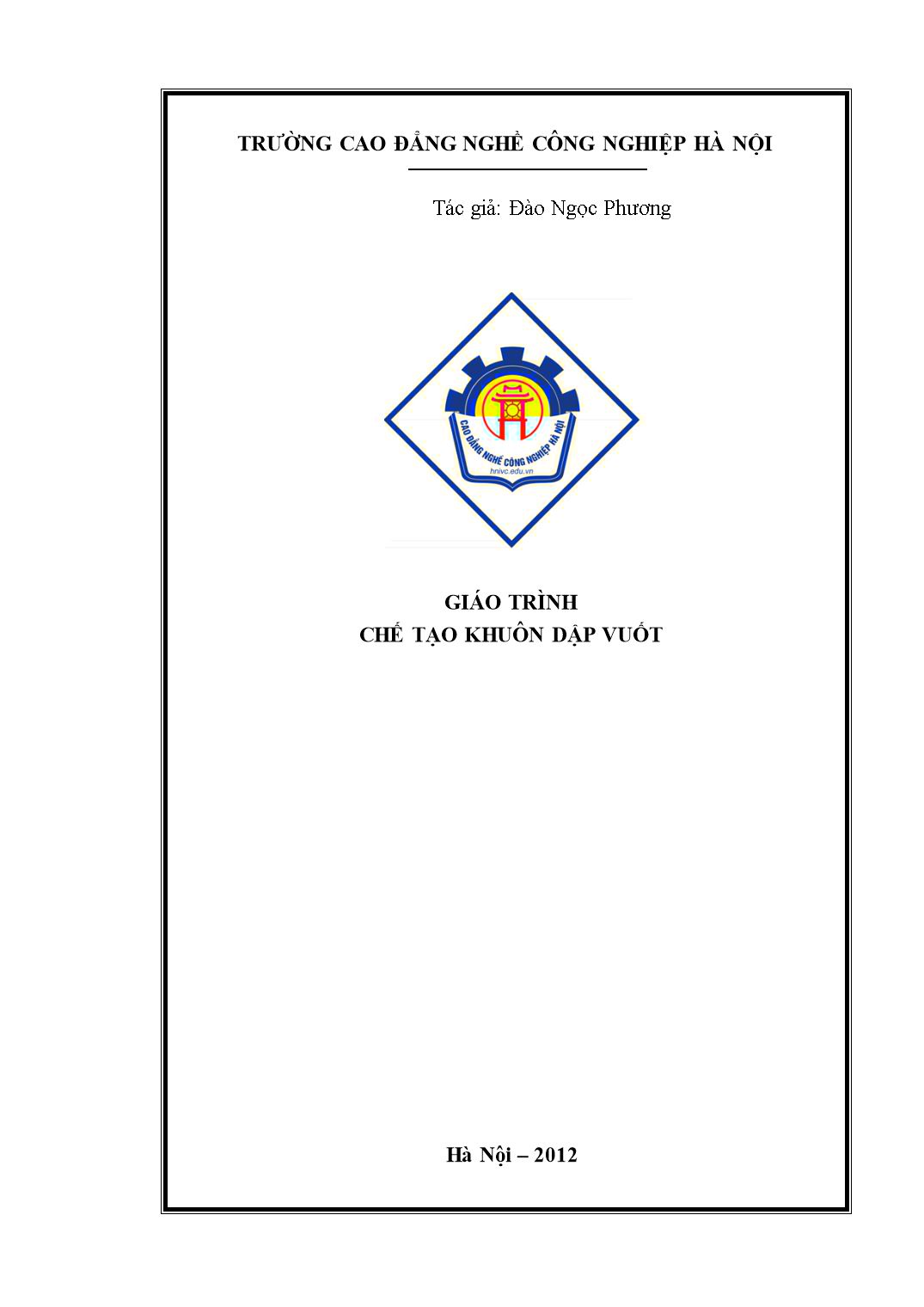
Trang 1
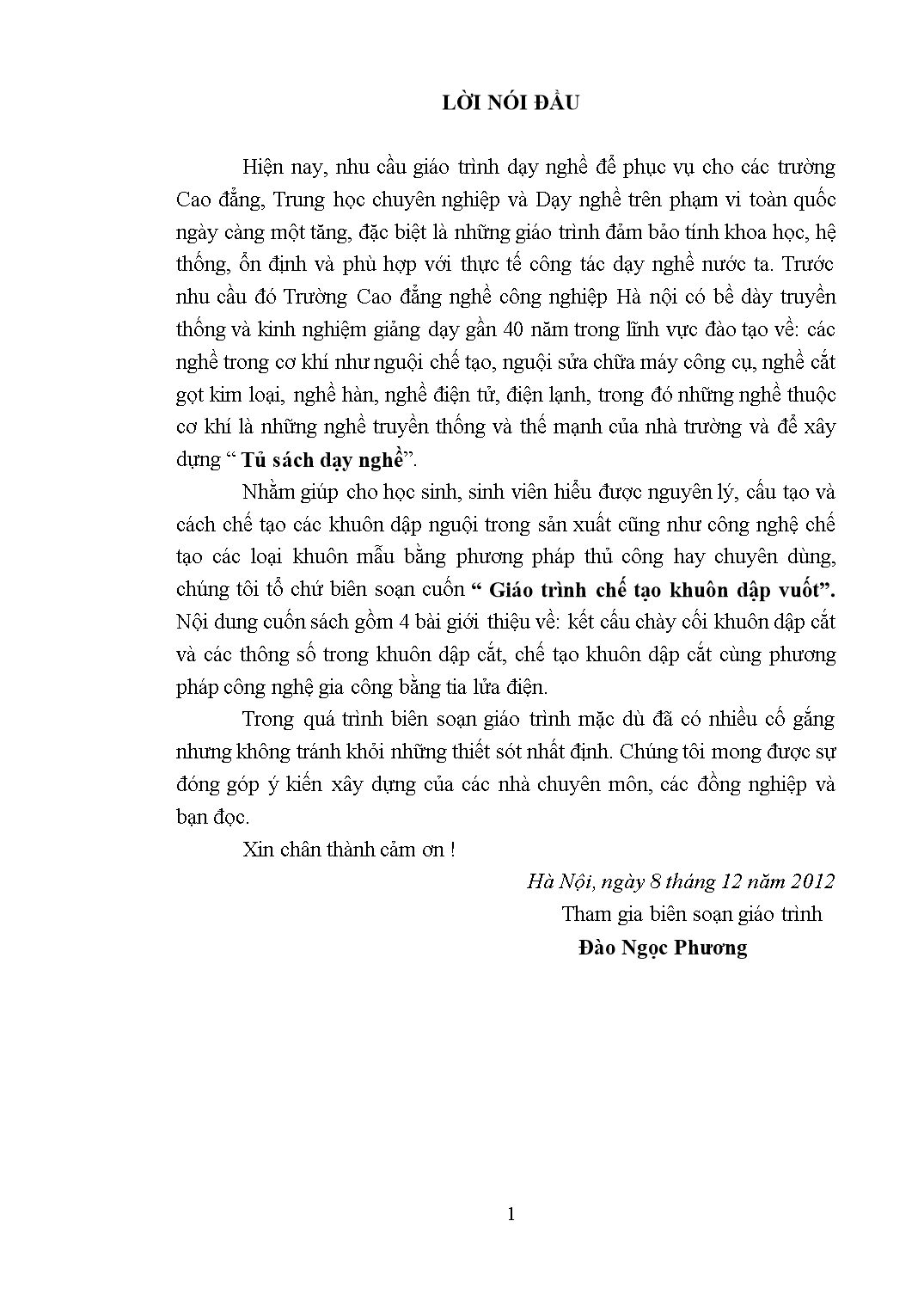
Trang 2
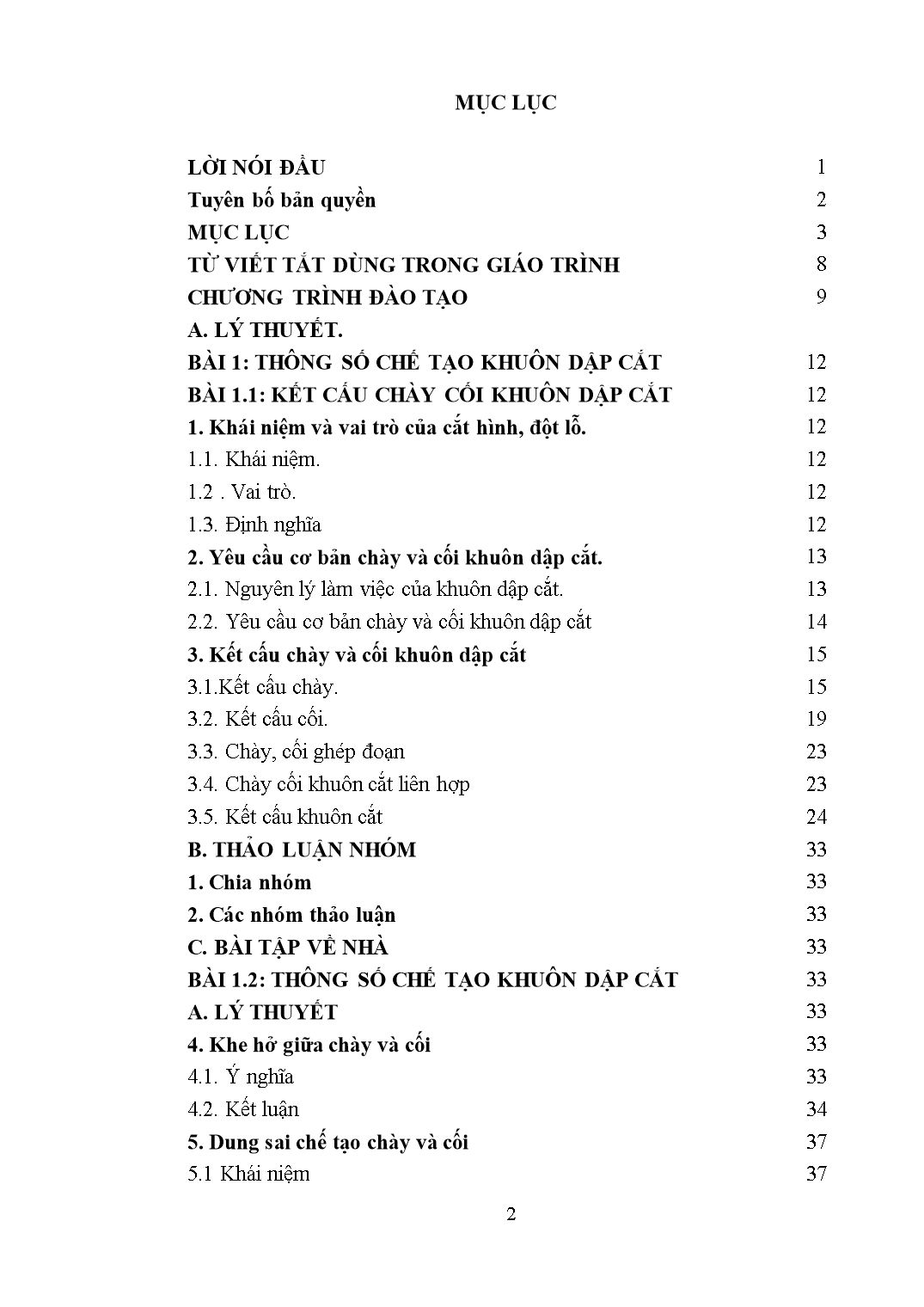
Trang 3
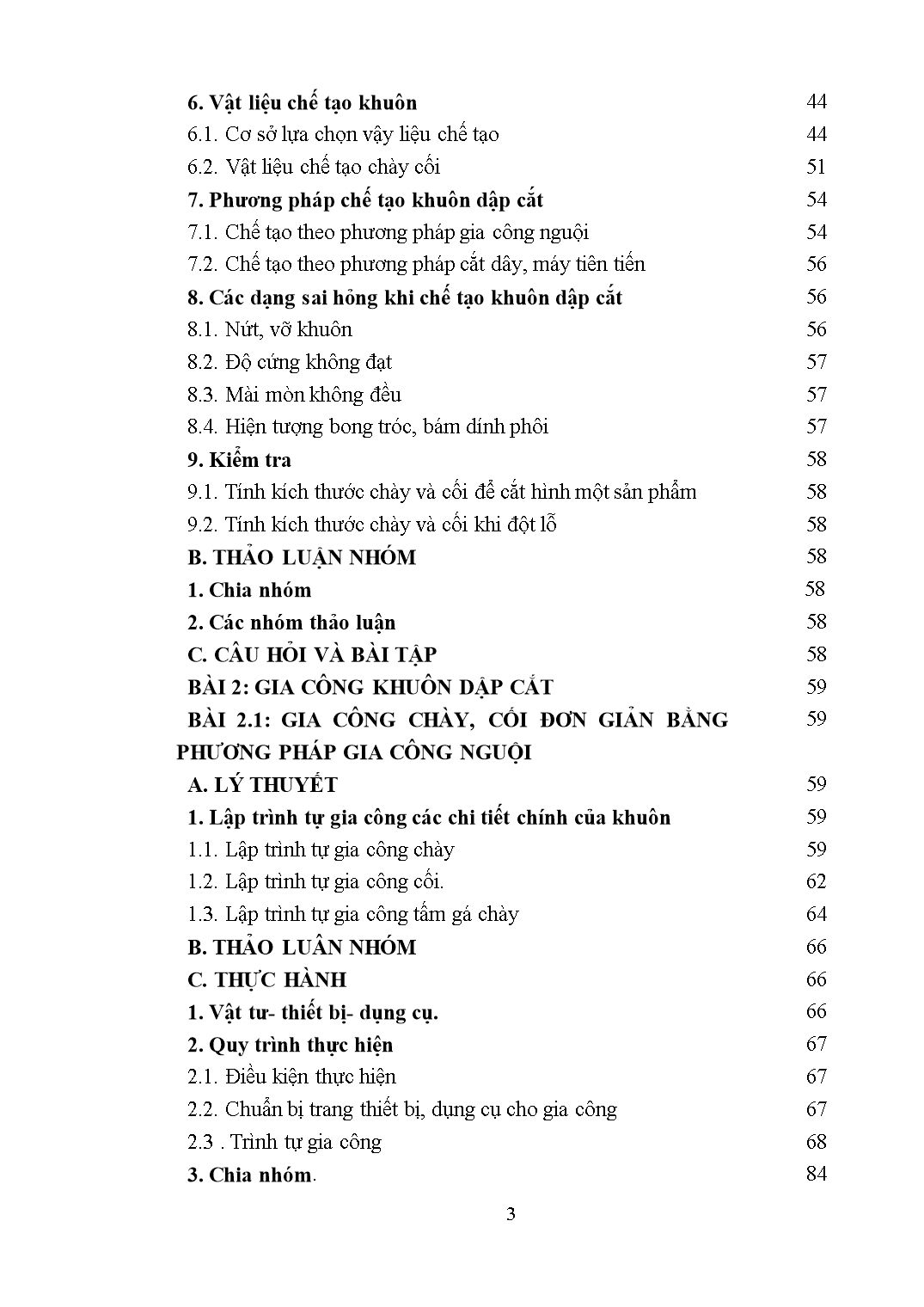
Trang 4
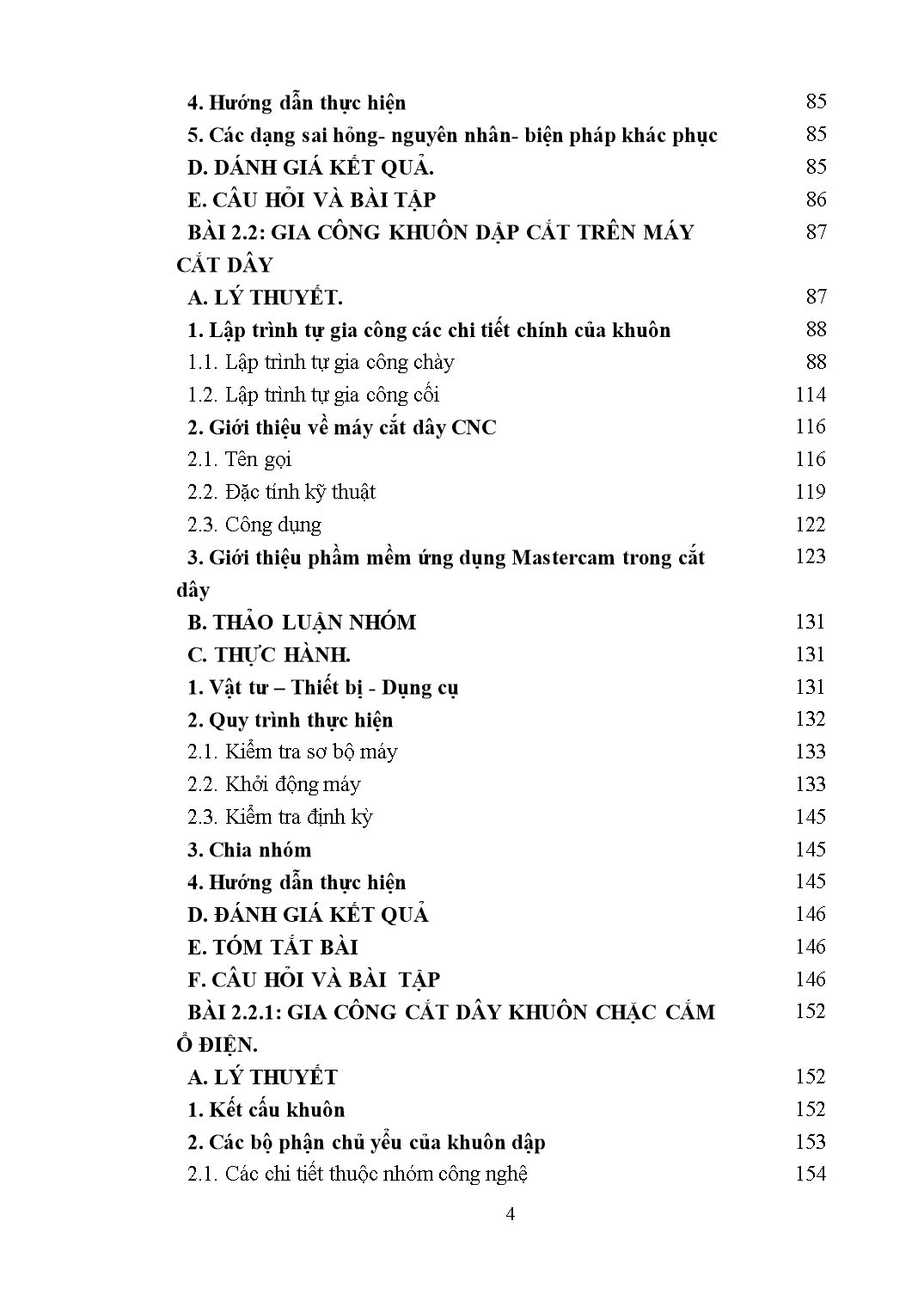
Trang 5
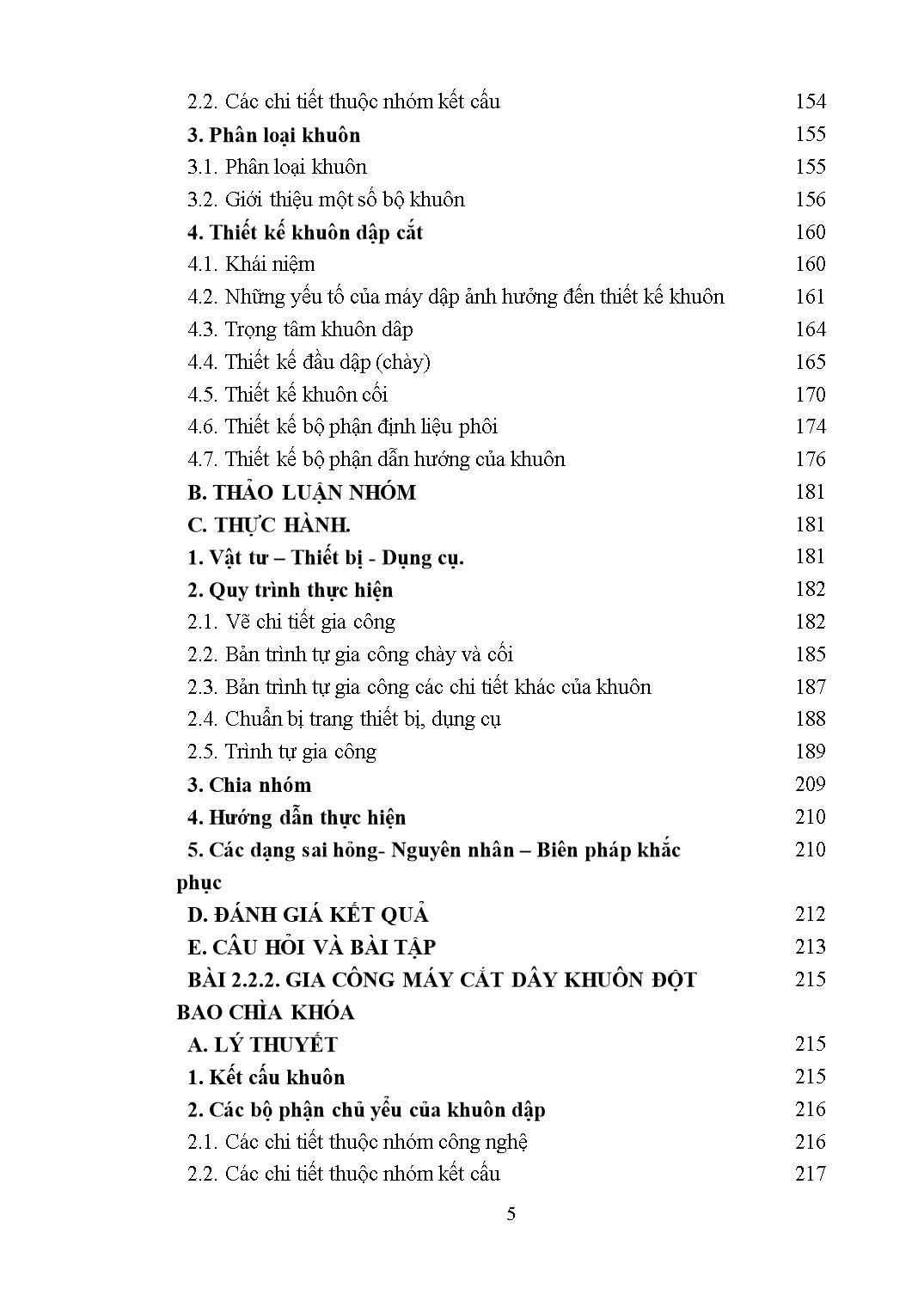
Trang 6
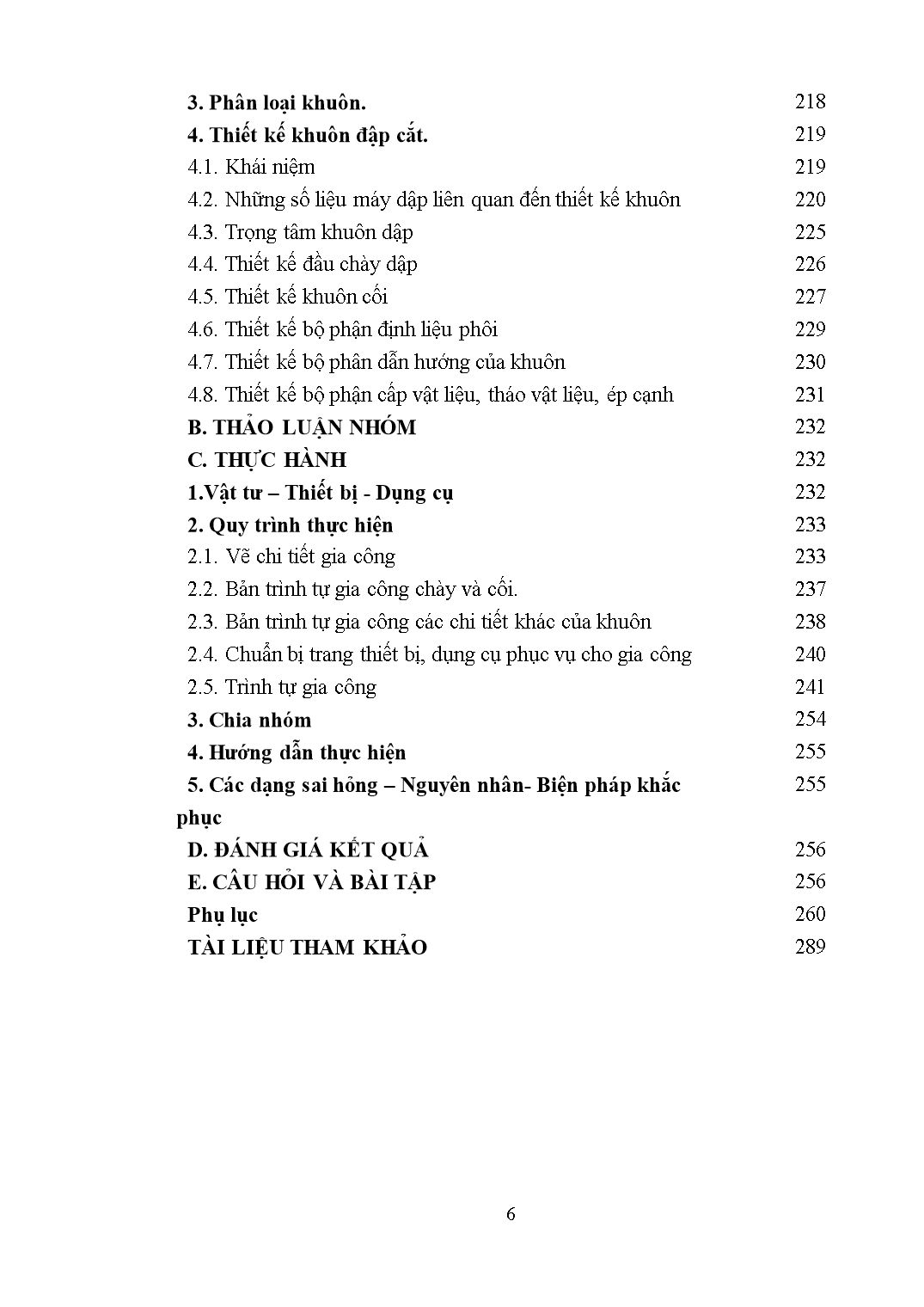
Trang 7
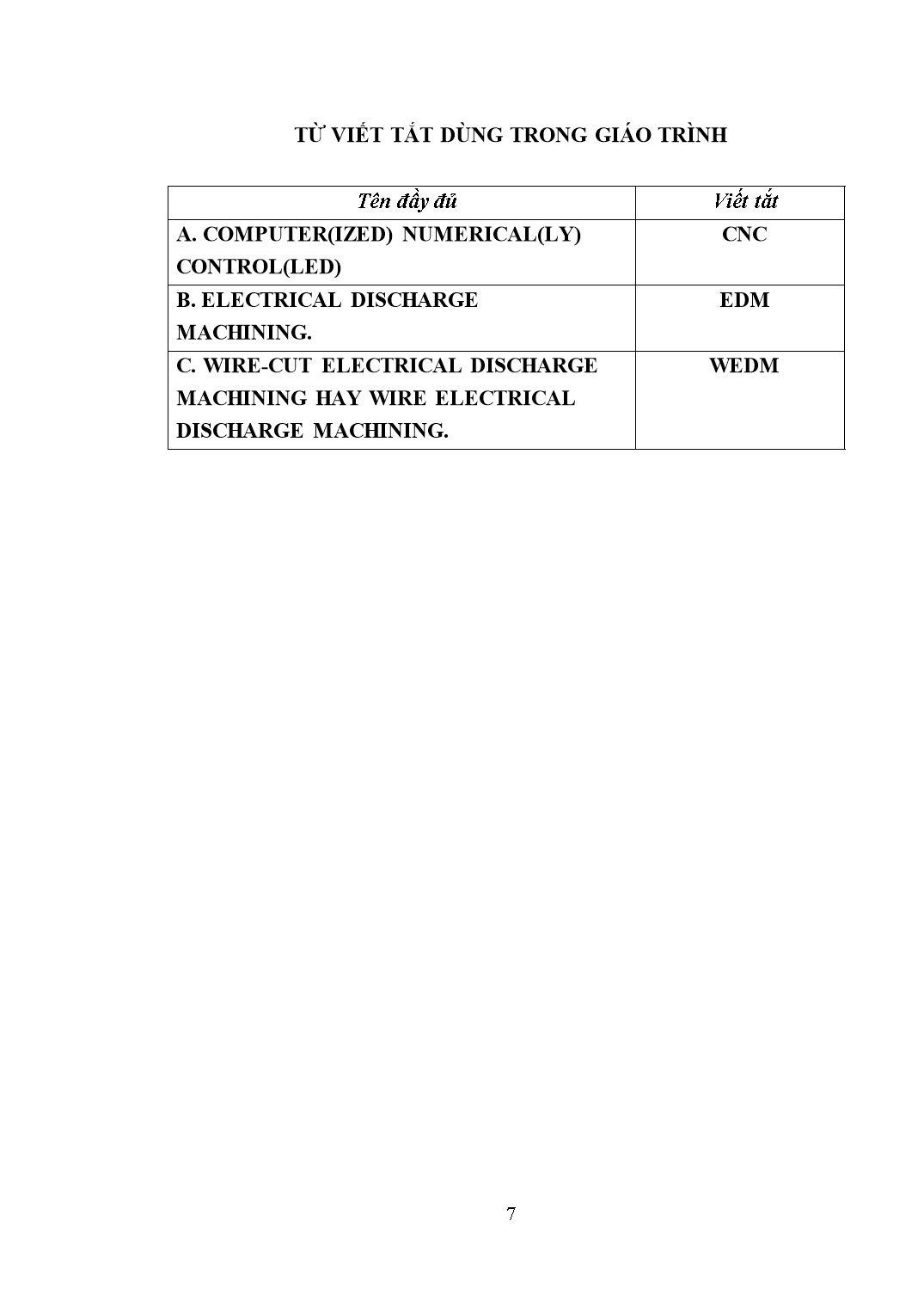
Trang 8
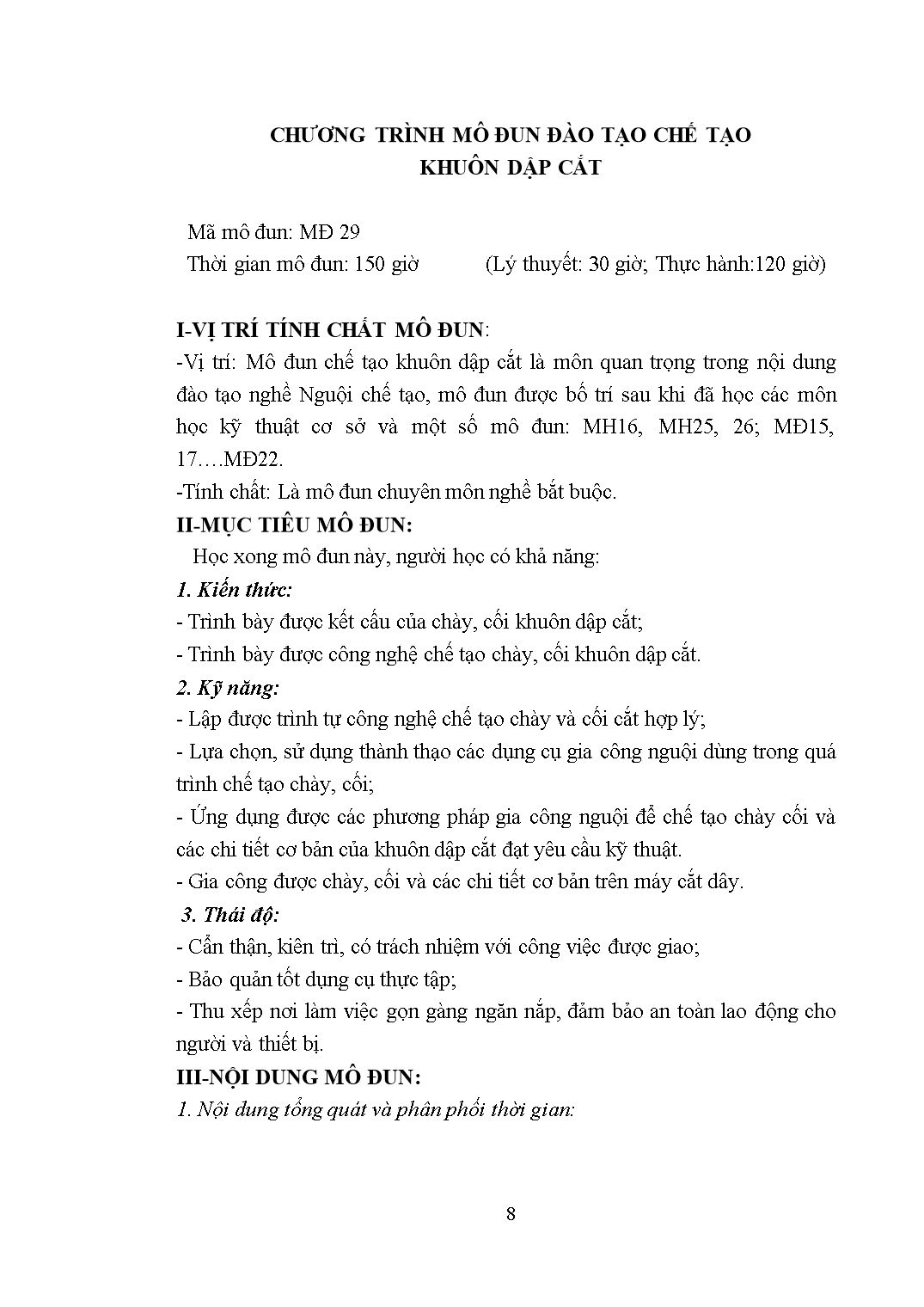
Trang 9
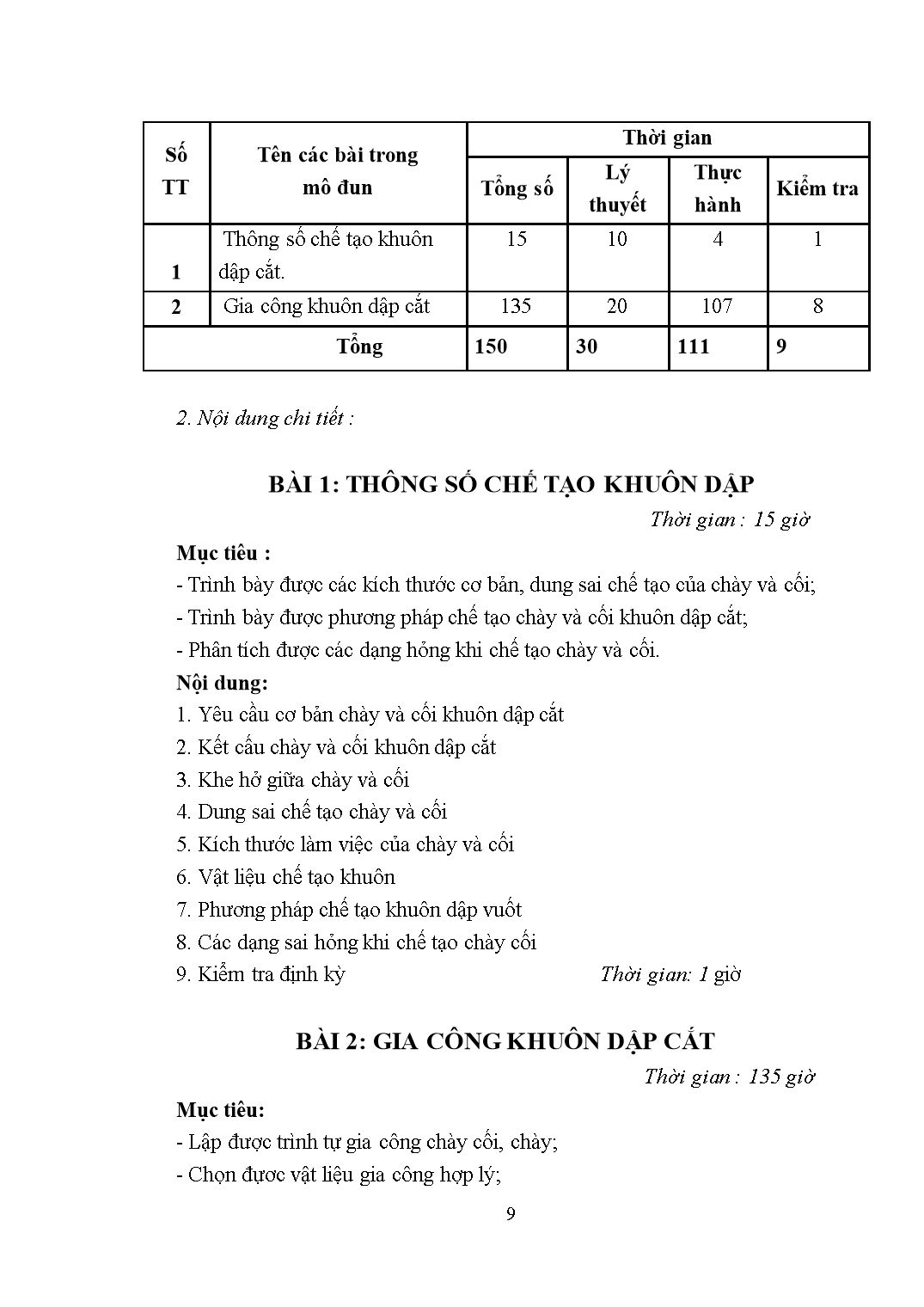
Trang 10
Tải về để xem bản đầy đủ
Tóm tắt nội dung tài liệu: Giáo trình Chế tạo khuôn dập vuốt
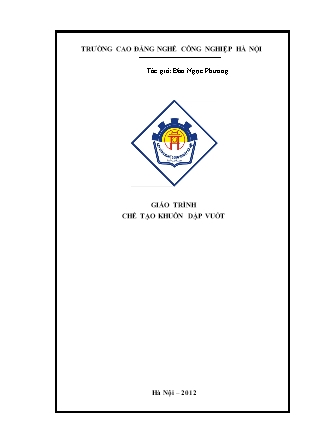
TRƯỜNG CAO ĐẲNG NGHỀ CÔNG NGHIỆP HÀ NỘI Tác giả: Đào Ngọc Phương GIÁO TRÌNH CHẾ TẠO KHUÔN DẬP VUỐT Hà Nội – 2012 LỜI NÓI ĐẦU Hiện nay, nhu cầu giáo trình dạy nghề để phục vụ cho các trường Cao đẳng, Trung học chuyên nghiệp và Dạy nghề trên phạm vi toàn quốc ngày càng một tăng, đặc biệt là những giáo trình đảm bảo tính khoa học, hệ thống, ổn định và phù hợp với thực tế công tác dạy nghề nước ta. Trước nhu cầu đó Trường Cao đẳng nghề công nghiệp Hà nội có bề dày truyền thống và kinh nghiệm giảng dạy gần 40 năm trong lĩnh vực đào tạo về: các nghề trong cơ khí như nguội chế tạo, nguội sửa chữa máy công cụ, nghề cắt gọt kim loại, nghề hàn, nghề điện tử, điện lạnh, trong đó những nghề thuộc cơ khí là những nghề truyền thống và thế mạnh của nhà trường và để xây dựng “ Tủ sách dạy nghề”. Nhằm giúp cho học sinh, sinh viên hiểu được nguyên lý, cấu tạo và cách chế tạo các khuôn dập nguội trong sản xuất cũng như công nghệ chế tạo các loại khuôn mẫu bằng phương pháp thủ công hay chuyên dùng, chúng tôi tổ chứ biên soạn cuốn “ Giáo trình chế tạo khuôn dập vuốt”. Nội dung cuốn sách gồm 4 bài giới thiệu về: kết cấu chày cối khuôn dập cắt và các thông số trong khuôn dập cắt, chế tạo khuôn dập cắt cùng phương pháp công nghệ gia công bằng tia lửa điện. Trong quá trình biên soạn giáo trình mặc dù đã có nhiều cố gắng nhưng không tránh khỏi những thiết sót nhất định. Chúng tôi mong được sự đóng góp ý kiến xây dựng của các nhà chuyên môn, các đồng nghiệp và bạn đọc. Xin chân thành cảm ơn ! Hà Nội, ngày 8 tháng 12 năm 2012 Tham gia biên soạn giáo trình Đào Ngọc Phương MỤC LỤC LỜI NÓI ĐẦU 1 Tuyên bố bản quyền 2 MỤC LỤC 3 TỪ VIẾT TẮT DÙNG TRONG GIÁO TRÌNH 8 CHƯƠNG TRÌNH ĐÀO TẠO 9 A. LÝ THUYẾT. BÀI 1: THÔNG SỐ CHẾ TẠO KHUÔN DẬP CẮT 12 BÀI 1.1: KẾT CẤU CHÀY CỐI KHUÔN DẬP CẮT 12 1. Khái niệm và vai trò của cắt hình, đột lỗ. 12 1.1. Khái niệm. 12 1.2 . Vai trò. 12 1.3. Định nghĩa 12 2. Yêu cầu cơ bản chày và cối khuôn dập cắt. 13 2.1. Nguyên lý làm việc của khuôn dập cắt. 13 2.2. Yêu cầu cơ bản chày và cối khuôn dập cắt 14 3. Kết cấu chày và cối khuôn dập cắt 15 3.1.Kết cấu chày. 15 3.2. Kết cấu cối. 19 3.3. Chày, cối ghép đoạn 23 3.4. Chày cối khuôn cắt liên hợp 23 3.5. Kết cấu khuôn cắt 24 B. THẢO LUẬN NHÓM 33 1. Chia nhóm 33 2. Các nhóm thảo luận 33 C. BÀI TẬP VỀ NHÀ 33 BÀI 1.2: THÔNG SỐ CHẾ TẠO KHUÔN DẬP CẮT 33 A. LÝ THUYẾT 33 4. Khe hở giữa chày và cối 33 4.1. Ý nghĩa 33 4.2. Kết luận 34 5. Dung sai chế tạo chày và cối 37 5.1 Khái niệm 37 6. Vật liệu chế tạo khuôn 44 6.1. Cơ sở lựa chọn vậy liệu chế tạo 44 6.2. Vật liệu chế tạo chày cối 51 7. Phương pháp chế tạo khuôn dập cắt 54 7.1. Chế tạo theo phương pháp gia công nguội 54 7.2. Chế tạo theo phương pháp cắt dây, máy tiên tiến 56 8. Các dạng sai hỏng khi chế tạo khuôn dập cắt 56 8.1. Nứt, vỡ khuôn 56 8.2. Độ cứng không đạt 57 8.3. Mài mòn không đều 57 8.4. Hiện tượng bong tróc, bám dính phôi 57 9. Kiểm tra 58 9.1. Tính kích thước chày và cối để cắt hình một sản phẩm 58 9.2. Tính kích thước chày và cối khi đột lỗ 58 B. THẢO LUẬN NHÓM 58 1. Chia nhóm 58 2. Các nhóm thảo luận 58 C. CÂU HỎI VÀ BÀI TẬP 58 BÀI 2: GIA CÔNG KHUÔN DẬP CẮT 59 BÀI 2.1: GIA CÔNG CHÀY, CỐI ĐƠN GIẢN BẰNG PHƯƠNG PHÁP GIA CÔNG NGUỘI 59 A. LÝ THUYẾT 59 1. Lập trình tự gia công các chi tiết chính của khuôn 59 1.1. Lập trình tự gia công chày 59 1.2. Lập trình tự gia công cối. 62 1.3. Lập trình tự gia công tấm gá chày 64 B. THẢO LUÂN NHÓM 66 C. THỰC HÀNH 66 1. Vật tư- thiết bị- dụng cụ. 66 2. Quy trình thực hiện 67 2.1. Điều kiện thực hiện 67 2.2. Chuẩn bị trang thiết bị, dụng cụ cho gia công 67 2.3 . Trình tự gia công 68 3. Chia nhóm. 84 4. Hướng dẫn thực hiện 85 5. Các dạng sai hỏng- nguyên nhân- biện pháp khác phục 85 D. DÁNH GIÁ KẾT QUẢ. 85 E. CÂU HỎI VÀ BÀI TẬP 86 BÀI 2.2: GIA CÔNG KHUÔN DẬP CẮT TRÊN MÁY CẮT DÂY 87 A. LÝ THUYẾT. 87 1. Lập trình tự gia công các chi tiết chính của khuôn 88 1.1. Lập trình tự gia công chày 88 1.2. Lập trình tự gia công cối 114 2. Giới thiệu về máy cắt dây CNC 116 2.1. Tên gọi 116 2.2. Đặc tính kỹ thuật 119 2.3. Công dụng 122 3. Giới thiệu phầm mềm ứng dụng Mastercam trong cắt dây 123 B. THẢO LUẬN NHÓM 131 C. THỰC HÀNH. 131 1. Vật tư – Thiết bị - Dụng cụ 131 2. Quy trình thực hiện 132 2.1. Kiểm tra sơ bộ máy 133 2.2. Khởi động máy 133 2.3. Kiểm tra định kỳ 145 3. Chia nhóm 145 4. Hướng dẫn thực hiện 145 D. ĐÁNH GIÁ KẾT QUẢ 146 E. TÓM TẮT BÀI 146 F. CÂU HỎI VÀ BÀI TẬP 146 BÀI 2.2.1: GIA CÔNG CẮT DÂY KHUÔN CHẶC CẮM Ổ ĐIỆN. 152 A. LÝ THUYẾT 152 1. Kết cấu khuôn 152 2. Các bộ phận chủ yểu của khuôn dập 153 2.1. Các chi tiết thuộc nhóm công nghệ 154 2.2. Các chi tiết thuộc nhóm kết cấu 154 3. Phân loại khuôn 155 3.1. Phân loại khuôn 155 3.2. Giới thiệu một số bộ khuôn 156 4. Thiết kế khuôn dập cắt 160 4.1. Khái niệm 160 4.2. Những yếu tố của máy dập ảnh hưởng đến thiết kế khuôn 161 4.3. Trọng tâm khuôn dâp 164 4.4. Thiết kế đầu dập (chày) 165 4.5. Thiết kế khuôn cối 170 4.6. Thiết kế bộ phận định liệu phôi 174 4.7. Thiết kế bộ phận dẫn hướng của khuôn 176 B ... trong những phương pháp chuẩn bị bề mặt kim loại tốt nhất trước khi sơn phủ. Ngoài ra, màng phốt phát hoá chuyển hoá bề mặt kim loại thành một lớp bề mặt mới không còn tính dẫn điện và tính kim loại, có khả năng chống ăn mòn. Nhờ các tính chất đó người ta tạo ra công nghệ phốt phát hoá để sử dụng trong các nhà máy xử lý bề mặt kim loại. Quy trình phốt phát hoá cổ điển là nhúng từ 10 phút đến vài giờ trong dung dịch nhiệt độ cao (600-900C). Dung dịch phốt phát hoá hiện đại có chứa các chất phụ gia làm tăng tốc độ quá trình, hạ thấp nhiệt độ xuống 350C và vận hành bằng cách phun hoặc phun – nhúng liên hợp. Dung dịch phốt phát hoá hiện đại thường có thành phần phức tạp, nhưng bao giờ cũng có ba thành phần chính sau: axit phốtphoric tự do, muối kim loại đihyđrôphotphat và chất tăng tốc. Phản ứng xảy ra trong quá trình phốt phát hoá rất phức tạp: Me(H2PO4) → Me2+ + 2H2PO4- H2PO4- = H+ + HPO42- HPO42- = H+ + PO43- Trong đó: Me là Fe, Zn, Mn. Khi thép nhúng vào dung dịch phốt phát hoá sẽ hình thành các vùng anốt và catốt xen kẽ nhau. Tại vùng anốt sắt bị xâm thực tan vào dung dịch Fe → Fe2+ + 2e, vùng catốt hyđrô thoát ra 2H+ + 2e → 2H → H2. Kết quả là lớp dung dịch sát vật gia công giàu ion Fe2+, HPO42- , PO43- cùng kết hợp với nhau thành các hợp chất không tan FeHPO4 và Fe3(PO4)2 kết tinh thành màng phốt phát. Trong màng không chỉ có muối sắt mà còn có cả muối mangan hay kẽm. Thành phần kim loại nền, cách gia công bề mặt trước khi phốt phát hoá, thành phần dung dịch và chế độ phốt phát hoá đều ảnh hưởng thành phần và tính chất màng. Chất lượng lớp phốt phát trên thép được xác định bằng trọng lượng của màng trên một đơn vị diện tích. Phốt phát hoá kim loại gồm các loại: phốt phát hoá thường, phốt phát hoá nhanh và phốt phát hoá nguội. Phốt phát hoá thường: Để thu được màng phốt phát phải dùng muối đihyđrôphotphát của các kim loại: Mn, Fe, Zn, Cd. Ở Nga hay dùng chế phẩm Majef chính là hỗn hợp các muối đihyđrôphotphát của sắt và mangan: Fe(H2PO4)2, Mn(H2PO4)2.H2O, MnHPO4 và có thành phần hoá học: 2,4-2,5% Fe, 14% Mn, 45-52% phot phát, 1% SO42-, CaO vết, Cl- vết và 1-2% H2O. Quá trình phốt phát hoá hiệu quả nhất trong dung dịch chứa 30-33g/l chế phẩm Majef ở nhiệt độ 960 - 980C. Ở nhiệt độ thấp hơn sẽ sinh ra cấu trúc tinh thể, còn ở nhiệt độ cao hơn sẽ sinh ra nhiều cặn bã trong dung dịch. Thời gian phốt phát hoá được xác định bằng thời điểm ngừng thoát khí hyđrô, tuy nhiên nên kéo dài thêm 5-10 phút nữa Màng tạo từ dung dịch muối Majef có độ bám cao, đạt chiều dày từ 7-50μm và xốp. Lớp phủ có điện trở cao và chịu nhiệt tốt Để màng có tinh thể nhỏ, tính bảo vệ cao nên dùng dung dịch có nồng độ Majef đặc (100-200g/l) và tiến hành ở nhiệt độ thấp 800- 850C Đối với thép hợp kim cao nên dùng dung dịch có 30-32 g/l muối Majef, 10-12 g/l BaCl2, nhiệt độ 98-1000C, thời gian 40-60phút Nhược điểm của phốt phát hoá trong dung dịch Majef là: thời gian lâu, nhiệt độ cao, khoảng nhiệt độ làm việc hẹp, khí hyđrô thoát ra mạnh, làm nền thấm nhiều hyđrô, cơ tính giảm. Vì vậy nếu giảm được sự thấm hyđrô sẽ rút ngắn được thời gian phốt phát hoá. Phốt phát hoá nhanh: Thành phần dung dịch và chế độ phốt phát hoá nhanh như sau: Majef 30-40 g/l 30-40g/l Zn(NO3)2.6H2O 50-65 g/l 50-70 g/l NaF 2-5 g/l - H3PO4 - 0,1 -1,0 g/l NaNO3 - 4-5 g/l Nhiệt độ 45-650C 92-960C Thời gian 8-15phút 8-10phút Phốt phát hoá nhanh được dùng khá rộng rãi trong công nghiệp vì không có những nhược điểm như phốt phát hoá thường ở trên. Dung dịch phốt phát hoá nhanh cho màng tương đối mỏng và độ bền ăn mòn thấp Phốt phát hóa nguội: Cách này không phải đun nóng dung dịch, nhưng màng tương đối mỏng. Phốt phát hoá nguội có thể dùng muối Majef hay muối kẽm đihyđrôphốtphát. NaF và NaNO2 là chất hoạt hoá cho quá trình. Khi tăng nhiệt độ dung dịch sẽ được màng tinh thể nhỏ mịn. Thành phần dung dịch và chế độ phốt phát hoá nhanh như sau: Majef 25-30 g/l - - - Zn(H2PO4)2 - 60-70 g/l 100 g/l - ZnO - - - 18-21g/l Zn(NO3)2.6H2O 35-40g/l 80-100 g/l - - NaF 5-10 g/l - 6 - H3PO4 - - - 80-85 g/l NaNO3 - 0,3-1,0 g/l 2 1-2 g/l Thời gian 40phút 15-25phút 30-40phút 15-20phút Quy trình xử lý phốt phát hóa: + Tẩy dầu, tẩy nhờn. + Rửa qua nước lạnh khoảng ½ - 1 phút + Nhúng vào bể dung dịch axit oxalic khoảng 10÷30 giây. Bể dung dịch này chứa 0,073 kg axit oxalic trong một gallon nước (4 lít). Axit mạnh nên duy trì ở 30 point ( point: là số ml của 0,1N dung dịch NaOH chuẩn độ 10ml, phenolphthalein là chất chỉ thị) và kiểm tra định kỳ nửa tháng 1 lần. Bể nên được rửa sạch khi có xuất hiện bùn đặc, cặn bám dính vào chi tiết đang được xử lý. + Rửa qua nước lạnh khoảng ½ - 1 phút + Rửa qua nước ấm khoảng ½ - 1 phút. Bể rửa nên duy trì nhiệt độ khoảng 65-800C, và điều chỉnh nước ấm từ khi bị nhiễm bẩn. + Xử lý phốt phát hóa ở 800C trong 4 phút. Thiết bị dùng là MIL-C 490A. Làm loãng nước xấp xỉ 1,3 kg/l. Duy trì ở 30 point* theo phân tích thống kê hàng ngày. + Rửa qua nước lạnh trong 1 phút. + Rửa qua nước ấm trong 1 phút (điều kiện bể rửa như trên) + Sấy khô. + Cất giữ chi tiết cẩn thận cho đến khi đưa vào lò thấm nitơ. Nhận thấy với ba phương pháp dùng để phốt phát hoá thì đều tạo ra màng xốp rất thích hợp cho giai đoạn thấm nitơ tiếp theo cho thép. Màng xốp sẽ tạo điều kiện thuận lợi cho các nguyên tử nitơ khuếch tán vào trong nền thép được tốt hơn như vậy độ cứng hay khả năng chống mài mòn của thép cũng sẽ cao hơn. Vậy ta đã giải quyết được khâu nhiệt luyện cho phôi cối đạt độ cứng 58-60HRC, Sau khi ta nhiệt luyện xong cần mài lại để đạt độ phẳng để chuẩn bị gia công các nguyên công tiếp theo. b. Tính toán các thông số quá trình nhiệt luyện khuôn đột dập - Vật liệu làm khuôn: CD80A - Khối lượng khuôn: 3,2 kg - Khối lượng riêng: 7,8 g/cm3 - Nhiệt dung riêng C (kJ/kgđộ) Bảng 2.7 T°C 20 400 800 C 0,460 0,536 0,686 - Hệ số dẫn nhiệt λ (kJ/m.h.K) Bảng 2.8 T°C 20 400 600 1000 λ 154,9 125,6 118,8 83,7 - Kích thước chi tiết: Hình 2.230: Kích thước phôi. Tính toán thời gian tôi Sơ đồ nung và giữ nhiệt trong lò tôi Nhiệt độ °C 790 Nước + NaOH 10% Thời gian Hinh 2.231.Sơ đồ nung và giữ nhiệt trong lò tôi - Chọn lò giếng RJ2 60-9 của Trung Quốc Công suất : 60kW Kích thước buồng lò : ɸ800 x 1000 Nhiệt độ làm việc tối đa : 950°C - Tính nhiệt độ trung bình của vật nung theo công thức 1.3.5[1] : (2.26) Trong đó T2tb: là nhiệt độ trung bình của vật nung T2đ: Nhiệt độ ban đầu của vật nung(oK) T2c: Nhiệt độ cuối giai đoạn của vật nung(oK) T2đ= 25+273= 298oK T2c= 790+273= 1063oK → T2tb = 895 °K = 622°C Tra bảng 1.5.1 [1] xác định được : Hệ số dẫn nhiệt l (ở nhiệt độ 622°C) = 107,23 kJ/m.h.K =29,78 W/m.K Nhiệt dung riêng C (ở nhiệt độ 622°C) = 0.5927 kJ/kg.độ Tra theo hình 1.3.1[1] xác định được hệ số truyền nhiệt ở nhiệt độ 622°C : a = 95 W/m2K Hệ số Bi theo 1.4.2[1] : (2.27) → Bi = 0,07 < 0,25 → vật nung là vật mỏng. - Công suất hữu ích của lò theo công thức 1.4.1[1]: (2.28) h : Hệ số sử dụng hữu ích của lò, h = 0,7¸0,8 Ntk : công suất thiết kế của lò, Ntk = 60 kW - Số chi tiết trong 1 mẻ để sử dụng hết công suất hữu ích của lò theo 1.5.11[1]: (2.27) k: hệ số tỷ lệ giữa nhiệt độ đạt được ở giai đoạn đầu và nhiệt độ nung cuối cùng cần đạt , k = 0,85 ¸ 0,95 ® chọn k = 0.9 - Chọn số chi tiết trong 1 mẻ là 90 cái. - Khối lượng chi tiết trong 1 mẻ là : Mct = 90.3,2 = 288 (Kg) + F : diện tích bề mặt nung một chi tiết : F = 2.0,059.0,1 + 2.0,059.0,07 + 2.0,07.0,1 = 0,03406 (m) - Do nung vật ở mọi phía nên chiều dày vật nung được xác định là : S= 1/2 chiều dày = 22 (mm) = 0,022 m * Đồ gá : Thiết kế đồ gá gồm 5 tầng gá, mỗi tầng gá hình tròn có kích thước600x600. Gá được chia làm 5 tầng, mỗi tầng được đặt 18 chi tiết. Trên mỗi tầng của đồ gá có đục 90 lỗ nhỏ đường kính 25 mm có tác dụng dẫn nhiệt từ dưới lên.Gá mỗi tầng dày 5 mm, có 4 thanh trụ đường kính 10 mm cao 600 mm hàn các tầng gá để liên kết các tầng với nhau. Mỗi tầng hàn 1 dây thép đường kính 5mm dài 1,88m (khi quấn tròn được hình tròn đường kính 600mm) bao quanh để đỡ 4 trụ và chi tiết đặt bên trong. 600 Chi tiết Hình 2.232 : Hình dạng đồ gá 5 tầng Theo bảng 1.4.1[1] hệ số sắp xếp kx = 2,2. - Khối lượng của gá : - Khối lượng 1 mẻ xếp là : Mmẻ = Mgá + Mct = 49,43 + 288 =337,43(Kg) (2.28) - Diện tích hấp thụ nhiệt của mỗi gá : - Diện tích hấp thụ nhiệt của chi tiết : Fct = n.F = 90.0,03406 = 3,0654 m2 → Fm = Fct + 5.Fgá = 3,0654 + 5.0,48 = 5,4654 m2 - Kiểm tra điều kiện: Công suất nung để nhiệt độ lò không thay đổi trong toàn bộ quá trình nung: (2.29) Chọn hệ số hữu dụng h = 0,8. Ta thấy Nkt > Ntk nên quá trình nung đến 790oC trong lò tôi phải trải qua 2 giai đoạn: + Giai đoạn 1: Nhiệt độ lò thay đổi - Khi kết thúc giai đoạn 1 nhiệt độ chi tiết đạt nhiệt độ t’2 (2.30) - Thời gian nung giai đoạn 1: (2.31) + Giai đoạn 2: nhiệt độ lò không thay đổi (2.32) Thời gian nung t1 = (tnung1 + tnung2).kx= (3813 + 756).2,2 = 10051,8 s =167 phút=2,79 h. * Tính toán thời gian giữ nhiệt quá trình tôi: Áp dụng công thức 1.9.4[1]: S : chiều dày trung bình của vật nung : S = 22 mm Các hệ số A,b được xác định theo bảng 1.9.3[1]: A=0, b=1 → = 0 + 1.22 = 22 phút. Quá trình làm nguội trong môi trường (nước + 10%NaOH) 20-25°C với tốc độ nguội tới hạn là 1200°C Thời gian làm nguội: - Tính nhiệt độ trung bình của vật nung 1.3.5 [1] : (2.33) Trong đó: T2tb : Nhiệt độ trung bình của vật nung T2d : Nhiệt độ ban đầu của vật nung (0K), T2d = 790 + 273 = 10630K T2c: Nhiệt độ cuối giai đoạn của vật nung(0K), T2c= (25 + 15) + 273 = 3130K t1 : Nhiệt độ của nước, t1= 250C Thay giá trị vào công thức trên ta có: → T2tb = 8950K = 6220C Dựa vào đồ thị (1.3.1 [1]) suy ra: là hệ số truyền nhiệt cho nước + NaOH ở 6220C : W/m2K - Tra bảng 2.18 và tính toán xác định được: Hệ số dẫn nhiệt l = 55 (W/moK) Nhiệt dung riêng c = 0,1675 (kJ/kg.độ) - Hệ số Bi 1.4.2 [1] : Bi = 0,2536 > 0.25 ® Vật nung là vật dày - Thời gian làm nguội (s) = 1,6(phút) (2.34) Trong đó: a: Hệ số truyền nhiệt độ (m2/s) (2.35) F0: chỉ tiêu F0. Từ biểu đồ Burin [3] tính toán theo nhiệt độ bề mặt cho chi tiết dạng khối với Bi = 0,2536 và xác định được F0 = 8,5 : Chỉ tiêu nhiệt độ . (2.36) -Thời gian làm nguội tính đến ảnh hưởng của chi tiết: (phút) (2.37) Tổng kết quy trình tôi : Nhiệt độ °C 790 Nước +NaOH 10% 2,79h 22 phút Thời gian Hình 2.233: Sơ đồ quy trình tôi Tính toán thời gian ram Sơ đồ nung và giữ nhiệt trong lò ram nhiệt độ 200 Thời gian Hình 2.234 : Sơ đồ nung và giữ nhiệt trong lò ram - Chọn lò ram Liên Xô loại πA-32-1 : + công suất 30kW + Kích thước 500 x 650 mm, + Nhiệt độ làm việc tối đa 650°C Tính toán thời gian nung đến nhiệt độ ram - Tính nhiệt độ trung bình của vật nung 1.3.5[1]: (2.38) Trong đó T2tb: là nhiệt độ trung bình của vật nung T2đ: Nhiệt độ ban đầu của vật nung(oK) T2c: Nhiệt độ cuối giai đoạn của vật nung(oK) T2đ = 25 + 273 = 298 °K T2c = 200 + 273 = 473°K Từ đó ta có T2tb= 4120K= 139oC - Tra bảng 1.5.1 [1] xác định được :Hệ số dẫn nhiệt l = 40,487 W/mK Nhiệt dung riêng C = 0,484 kJ/kg.độ - Tra theo hình 1.3.1[1] xác định được hệ số truyền nhiệt a = 25 W/m2K - Chỉ tiêu Bi tính theo công thức 1.4.2[1] : → vật nung là vật mỏng. - Công suất hữu ích của lò 1.4.1[1] : Nh == =16000 (W) (2.39) h : Hệ số sử dụng hữu ích của lò, h = 0,7¸0,8 Ntk : công suất thiết kế của lò, Ntk = 30 kW - Số chi tiết trong 1 mẻ để sử dụng hết công suất hữu ích của lò theo 1.5.11[1]: (2.40) + k: hệ số tỷ lệ giữa nhiệt độ đạt được ở giai đoạn đầu và nhiệt độ nung cuối cùng cần đạt , k = 0,85 ¸ 0,95 ® chọn k = 0.9 + F là diện tích nung của một chi tiết: F = 2.0,059.0,1 + 2.0,059.0,07 + 2.0,07.0,1 = 0,03406 (m) - Chọn số chi tiết trong 1 mẻ là 90 cái. * Đồ gá : Chọn đồ gá gồm 4 tầng kích thước 450x480 mm, mỗi tầng dày 5mm. Trên mỗi tầng đục 60 lỗ nhỏ đường kính 25 mm có tác dụng dẫn nhiệt từ dưới lên.Thiết kế 4 thanh trụ đường kính 10 mm cao 480 mm hàn các tầng gá để liên kết các tầng với nhau.Mỗi tầng hàn 1 dây thép đường kính 5mm dài 1,414m (khi quấn tròn được hình tròn đường kính 450mm) bao quanh để đỡ 4 trụ và chi tiết đặt bên trong.3 tầng dưới ta đặt khít tầm 23 chi tiết, tầng trên cùng đặt 21 chi tiết. Hình 2.235 : Hình dáng mô tả đồ gá 4 tầng - Khối lượng của gá : -Khối lượng mẻ xếp : Mmẻ = Mct + Mgá = 288 + 26,8 =314,8 Kg (2.41) Hình 2.236 : Hình dáng mô tả đồ gá - Diện tích hấp thụ nhiệt của mỗi gá : - Diện tích hấp thụ nhiệt của chi tiết : Fct = n.F = 90.0,03406 = 3,0654 m2 → Fm = Fct + 4.Fgá = 3,0654 + 4.0,266 = 4,1294 m2 - Kiểm tra điều kiện: Công suất nung để nhiệt độ lò không thay đổi trong toàn bộ quá trình nung: (2.42) Chọn hệ số hữu dụng h = 0,8. Ta thấy Nkt > Ntk nên quá trình nung đến 200oC trong lò ram phải trải qua 2 giai đoạn: + Giai đoạn 1: Nhiệt độ lò thay đổi - Khi kết thúc giai đoạn 1 nhiệt độ chi tiết đạt nhiệt độ t’2 (2.43) - Thời gian nung giai đoạn 1: (2.44) + Giai đoạn 2: nhiệt độ lò không thay đổi (2.45) Thời gian nung t1 = = (tn1 + tn2).kx= (286 + 4045).1,4 = 6063,4 s = 101 phút (2.46) = 1,68 giờ. Thời gian giữ nhiệt khi ram Áp dụng công thức 1.9.4[1]: (2.47) S : chiều dày trung bình của vật nung : S = 22 mm Các hệ số A,b được xác định theo bảng 1.9.3[1] với nhiệt độ ram 200°C: A=120, b=1 → = 120 + 1.22 = 142 phút = 2,36 giờ. Nhiệt độ 200 1,68h 2,36h thời gian Hình 2.237: Sơ đồ quy trình ram Sau khi ta nhiệt luyện xong cần mài lại để đạt độ phẳng để chuẩn bị gia công các nguyên công tiếp theo. TÀI LIỆU THAM KHẢO - Công nghệ dập nguội – Lê Nhương (Hiệu đính) - Nhà xuất bản khoa học kỹ thuật - Năm 1974. - Sổ tay dập nguội - dịch Nguyễn Giảng – Lê Nhương hiệu đính- Nhà xuất bản khoa học kỹ thuật - Năm 1972. - Giáo trình kỹ thuật dập nguội –Tổ môn: Nhiệt luyện- Rèn dập biên soan- Trường Trung cấp Cơ điện- Hà nội. - Sổ tay thiết kế khuôn dập tấm-V.L MARTRENCO, L.I RUDMAN (Vũ khúc Nhã biên dịch) – Nhà xuất bản Hải Phòng - Năm 2005. - Hỏi và đáp về Dập tấm và cán kéo kim loại – Đỗ hữu Nhơn, Nguyễn ngọc Giao, Nguyễn mậu Đằng.-Nhà xuất bản khoa học kỹ thuật – Năm 2001. - MISUMI (standard components for press dieds) – Năm 2007 - Gia công tia lửa điện –Tác giả PGS.TS Vũ hoài Ân - Nhà xuất bản khoa học kỹ thuật – Năm 2005. - Thực hành nguội N.I MakienKo – Nhà xuất bản Maxcơva. - Công nghệ trên máy CNC - Tác giả PGS.TS Trần Văn Địch - Nhà xuất bản KHKT - 2000. - Máy công cụ CNC - Tạ Duy Liêm - Nhà xuất bản KHKT - 1999. - Nhập môn CNC - Trung tâm IMI. - Phần mềm TopSolid 2007 (Full license) - Miller (Pháp) 5. Ghi chú: Mục 2 là gia công trên máy cắt dây, có thể trang thiết bị phục vụ cho thực tập cắt dây một số trường không có. Vì vậy có thể sử dụng các phần mềm cho học viên thực tập chế tạo khuôn dập cắt trên các máy ảo để hình thành kỹ năng cơ bản, sau đó cho học viên xuống các cơ sở kinh doanh hoặc các công ty có máy cắt dây thực tập thực tế. Như vậy mới đảm bảo mục tiêu của mô đun.
File đính kèm:
giao_trinh_che_tao_khuon_dap_vuot.doc