Giáo trình Đồ gá trên máy công cụ
Trong quá trình sản xuất của ngành cơ khí chế tạo máy, toàn bộ các phụ tùng kèm theo máy gia công để giúp cho máy đó thực hiện có hiệu quả quá trình công nghệ gia công các đối tượng sản xuất, đều được gọi là các trang bị công nghệ.
Như vậy trang bị công nghệ nói chung bao gồm các loại đồ gá trên máy cắt, đồ gá lắp ráp, đồ gá kiểm tra, các dụng cụ cắt, các dụng cụ phụ, các cơ cấu cấp phôi, tháo phôi, đồ gá gia công nóng, .
Theo kết cấu và công dụng, trang bị công nghệ được phân thành hai loại: trang bị công nghệ vạn năng và trang bị công nghệ chuyên dùng. Đặc điểm của trang bị công nghệ vạn năng là không phụ thuộc vào đối tượng gia công nhất định và được sử dụng chủ yếu vào dạng sản xuất đơn chiếc và loạt nhỏ.
Trang bị công nghệ chuyên dùng có kết cấu và tính năng của nó phụ thuộc vào một hoặc một nhóm đối tượng gia công nhất định, nó được dùng chủ yếu trong sản xuất hàng khối và loạt lớn, cá biệt trong sản xuất nhỏ và đơn chiếc yêu cầu có độ chính xác cao hoặc đối với những chi tiết bắt buộc phải dùng đồ gá chuyên dùng mới gia công được.
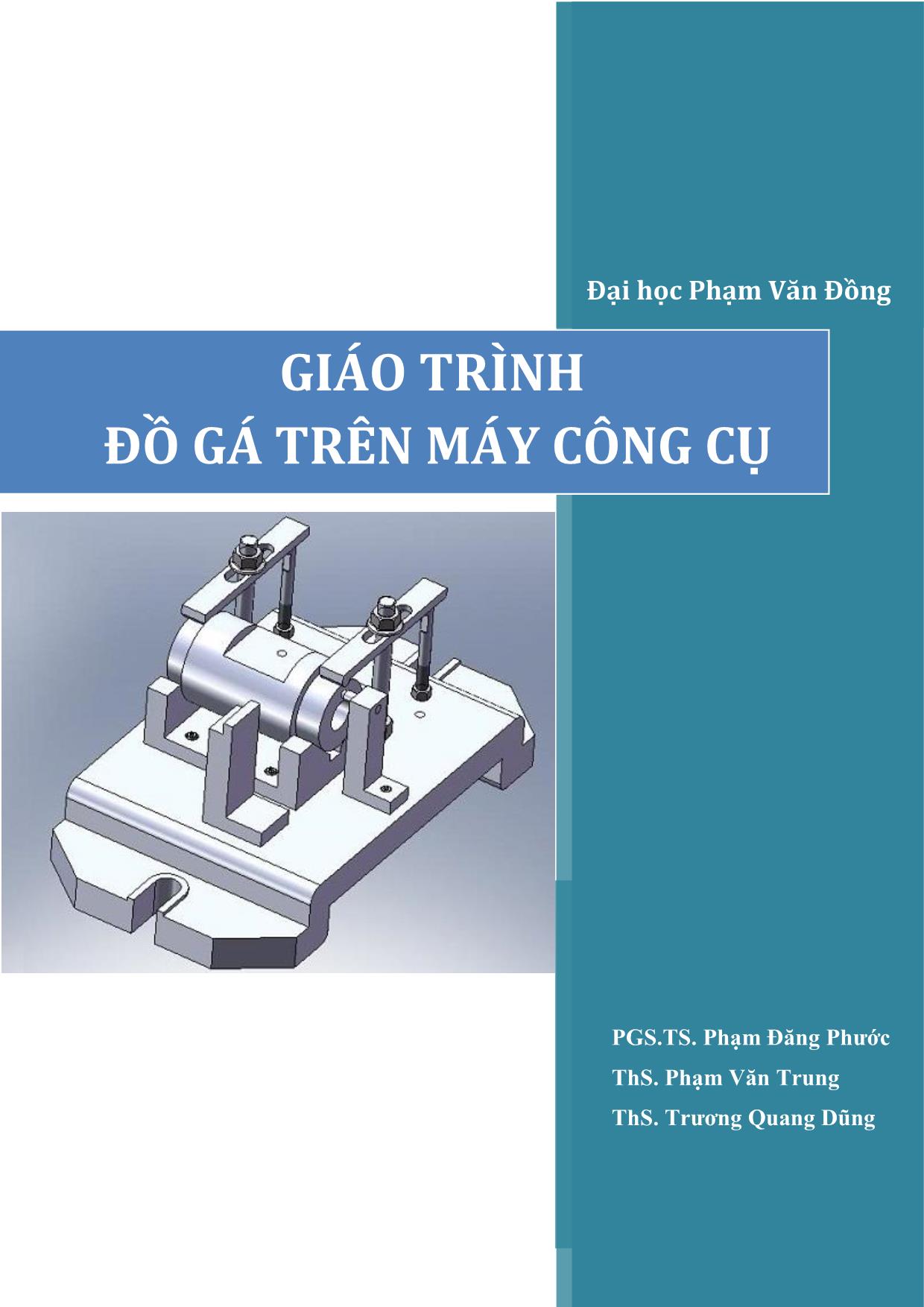
Trang 1
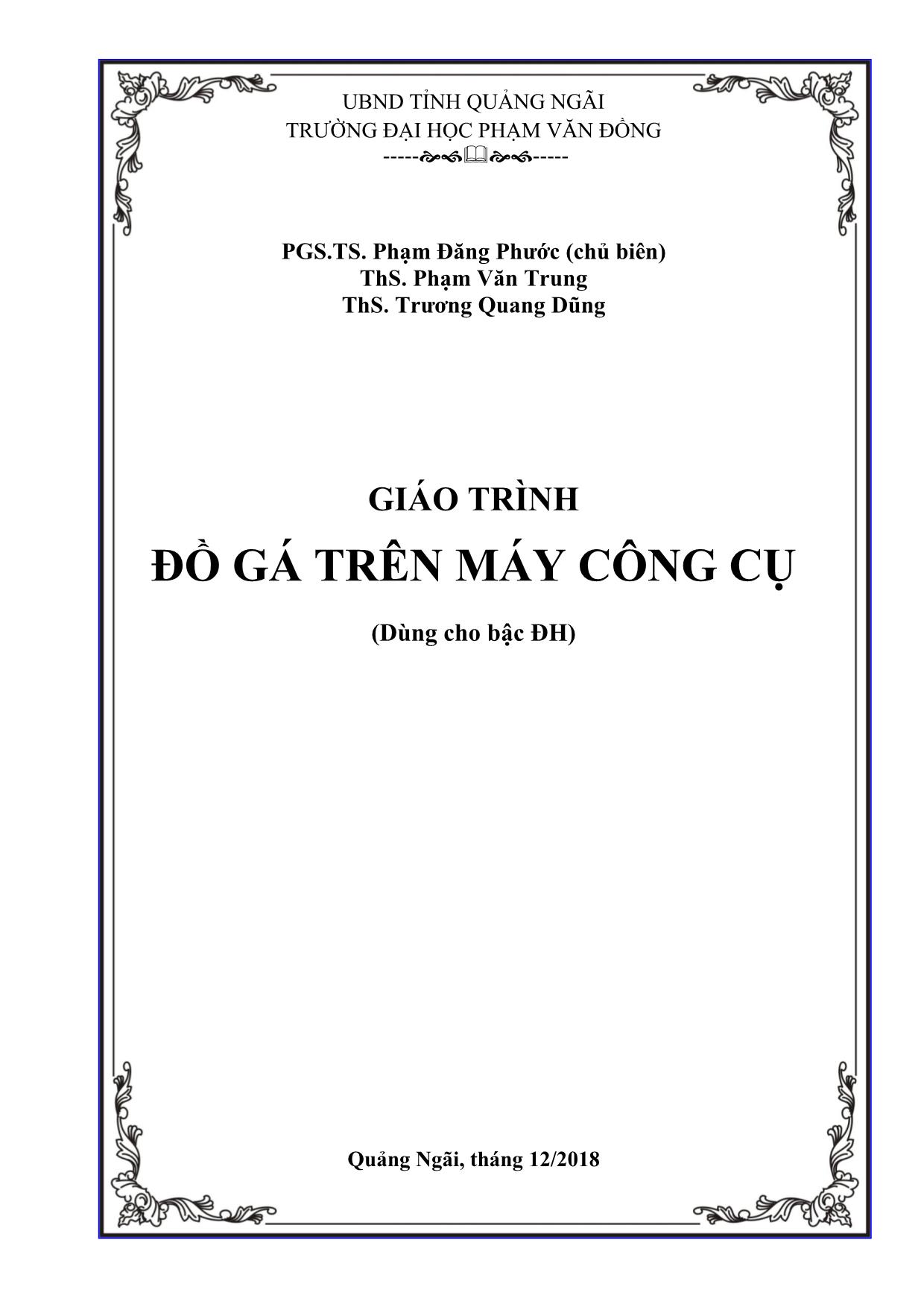
Trang 2
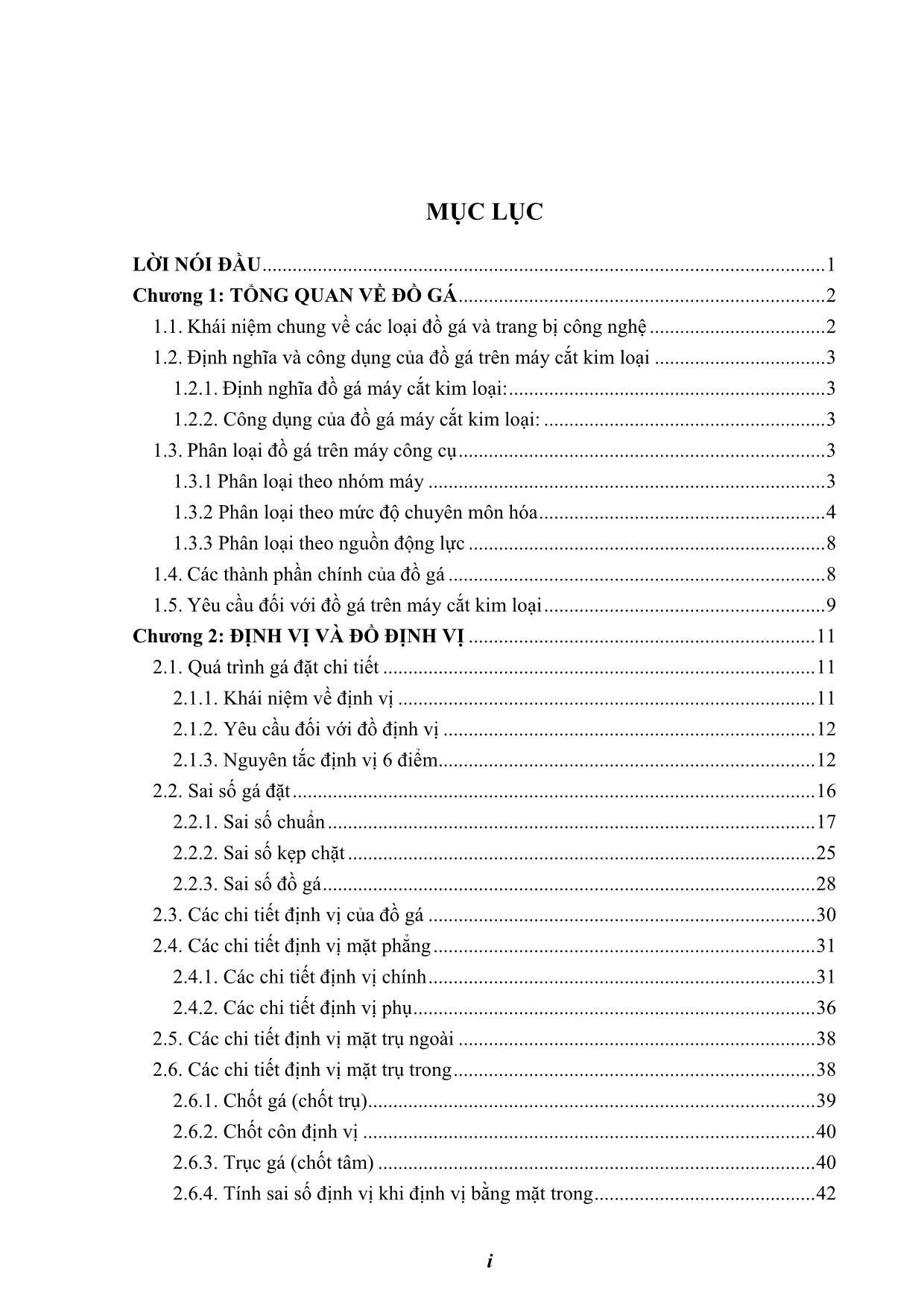
Trang 3
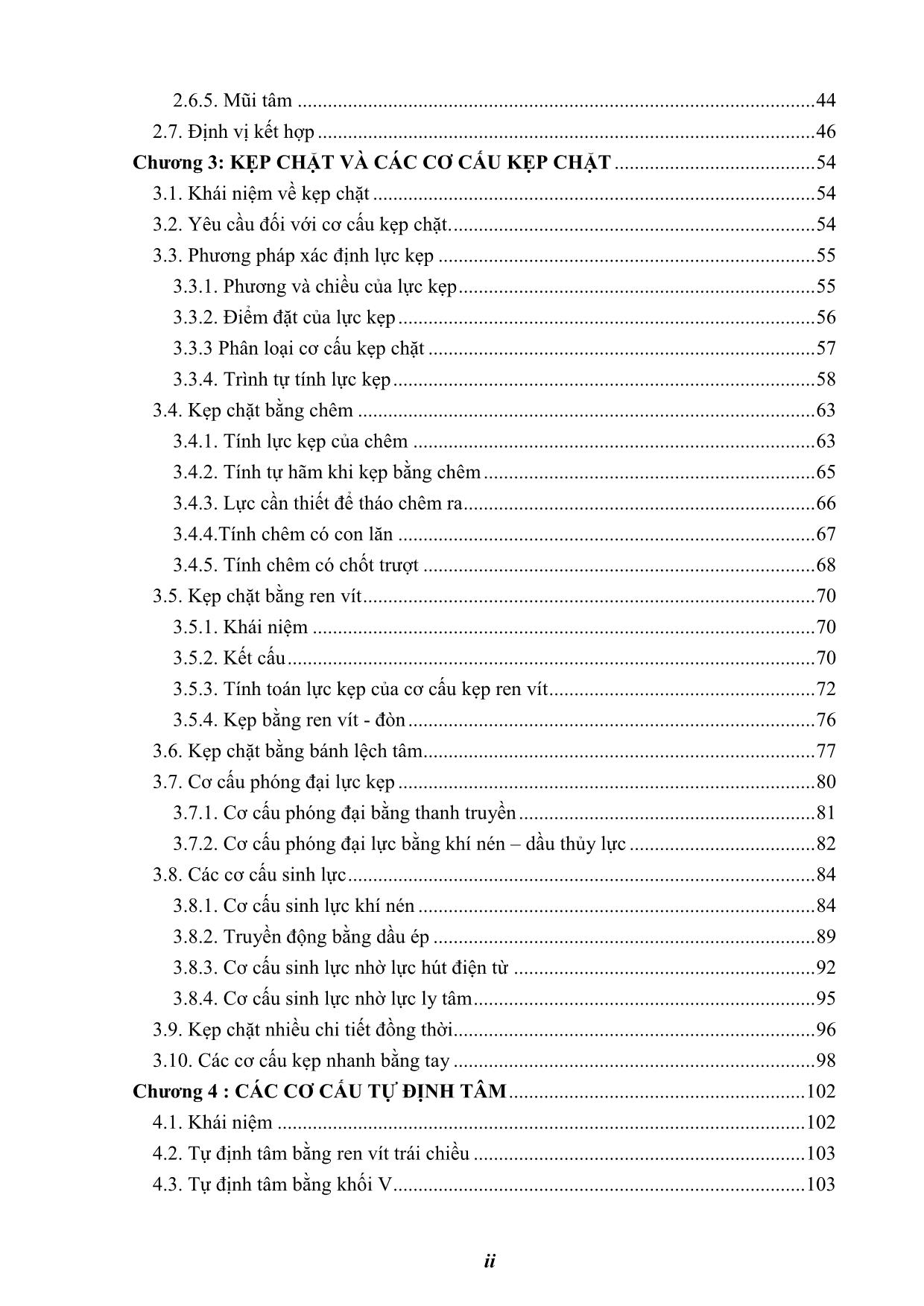
Trang 4
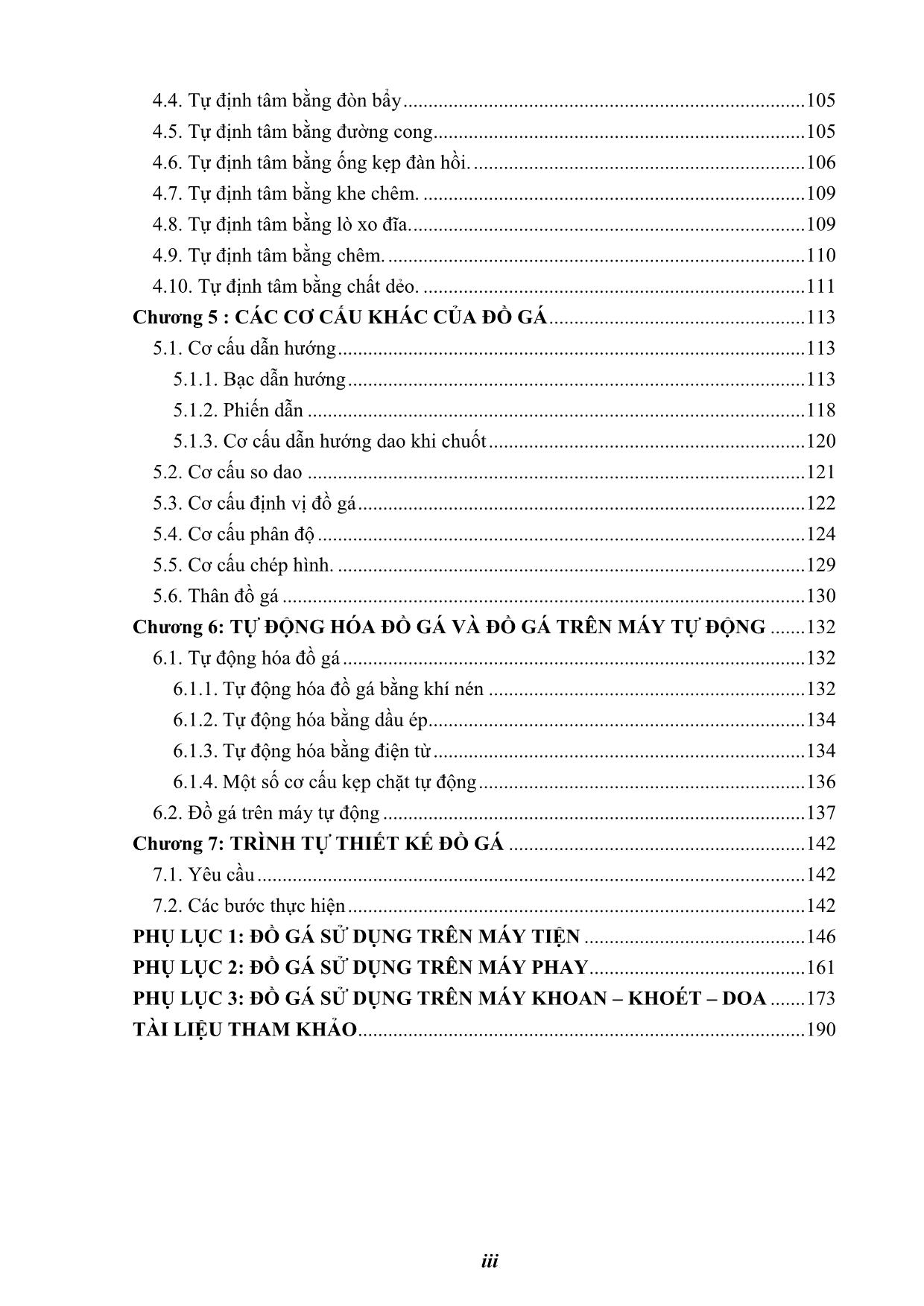
Trang 5
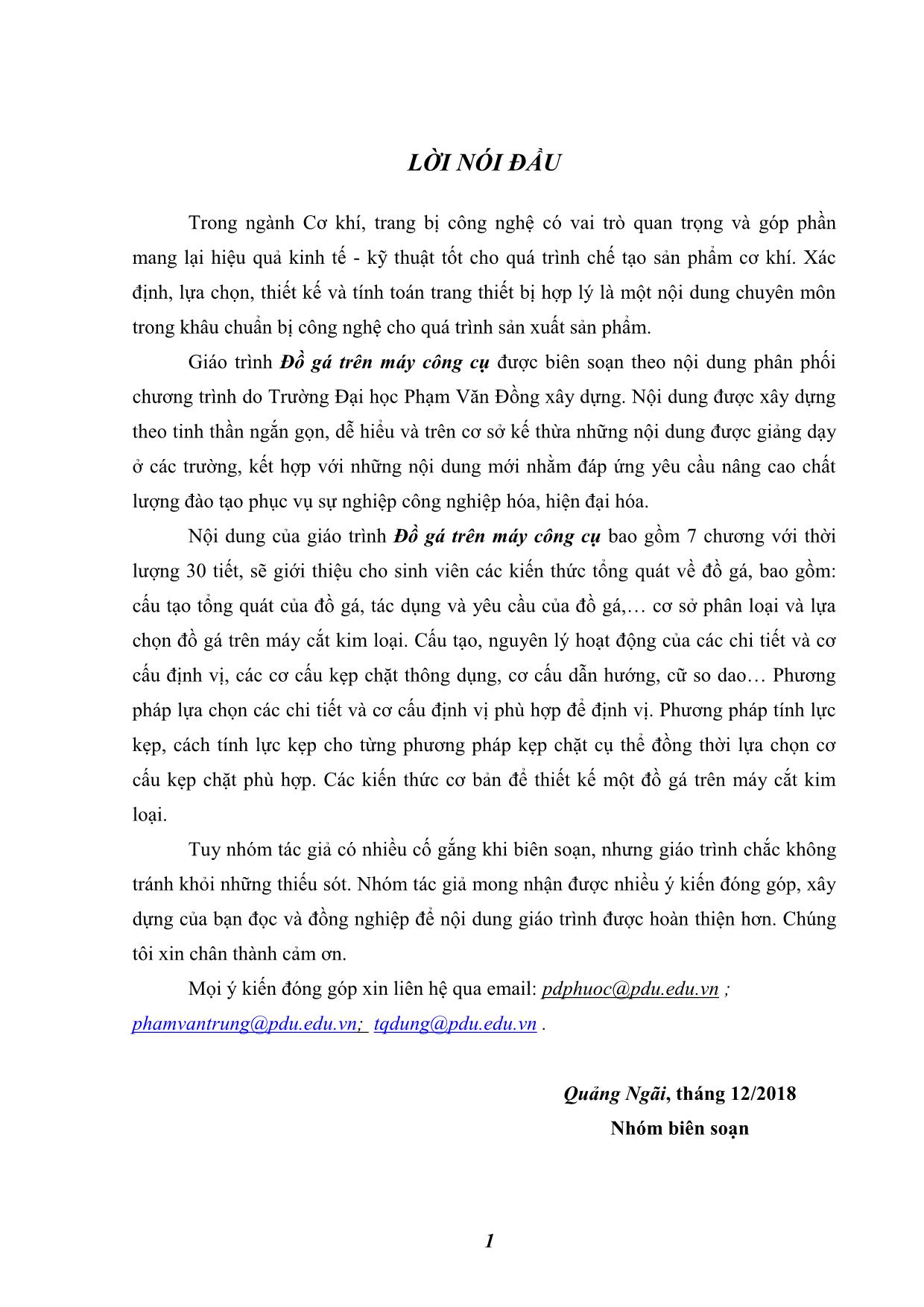
Trang 6
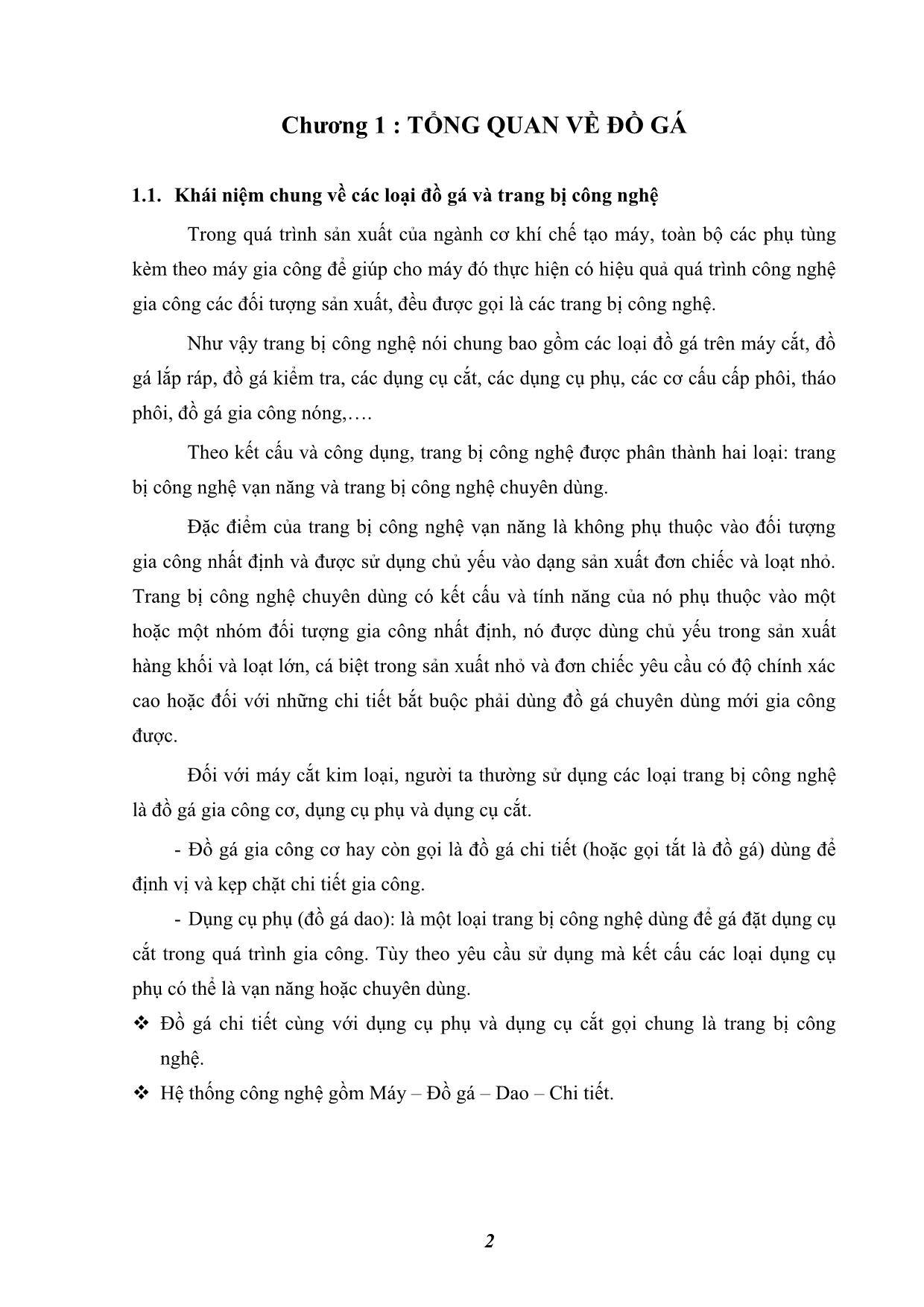
Trang 7
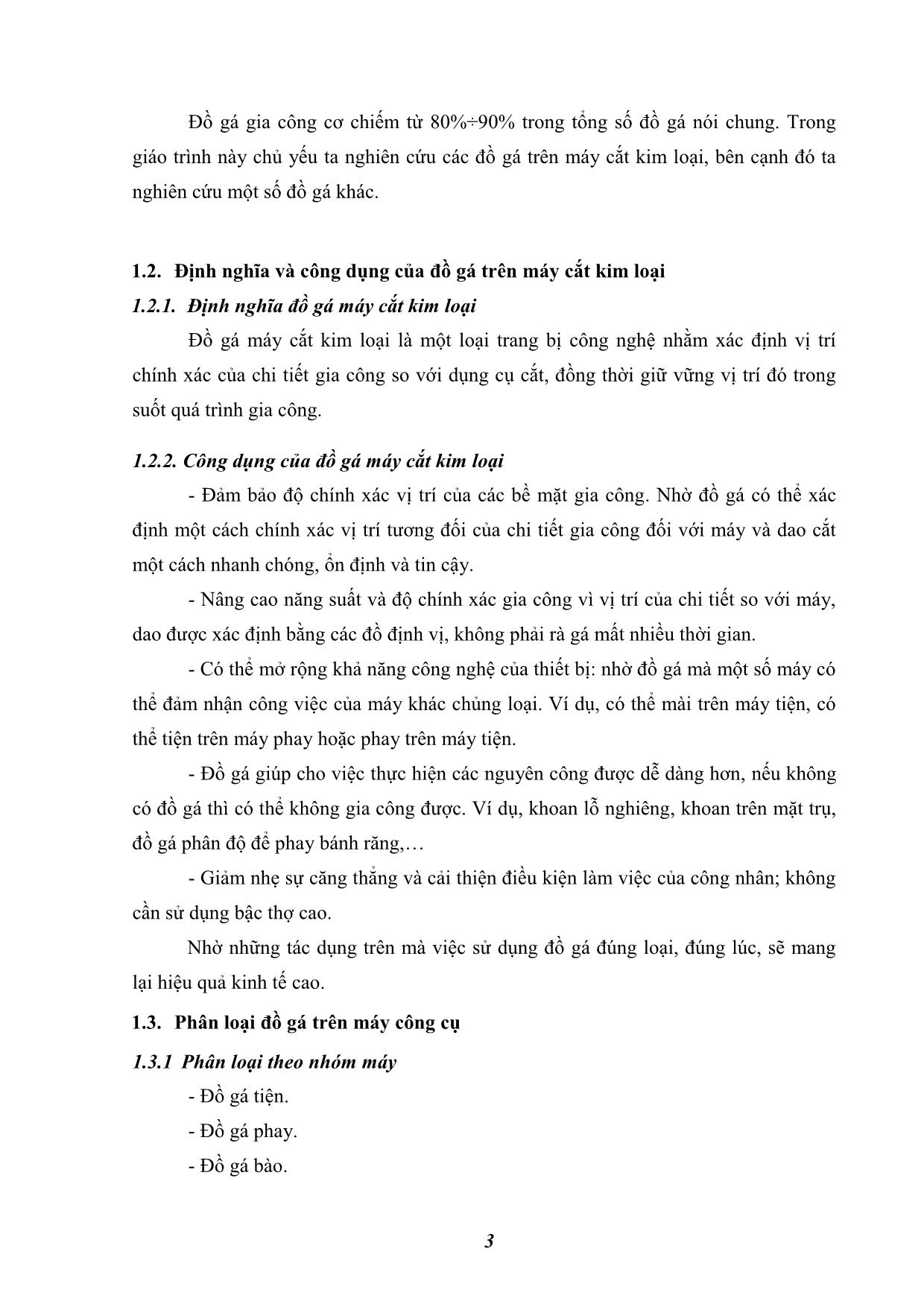
Trang 8
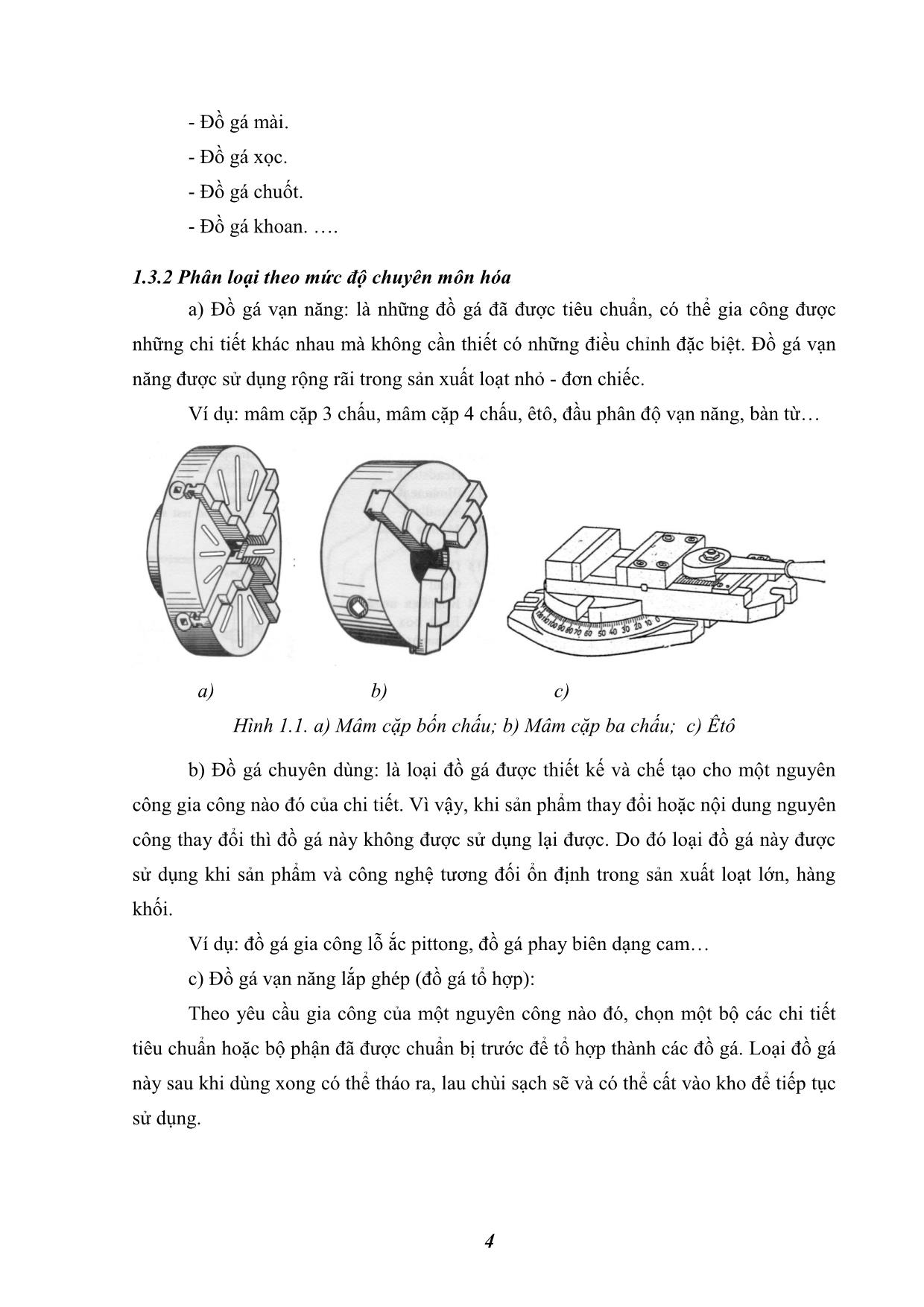
Trang 9
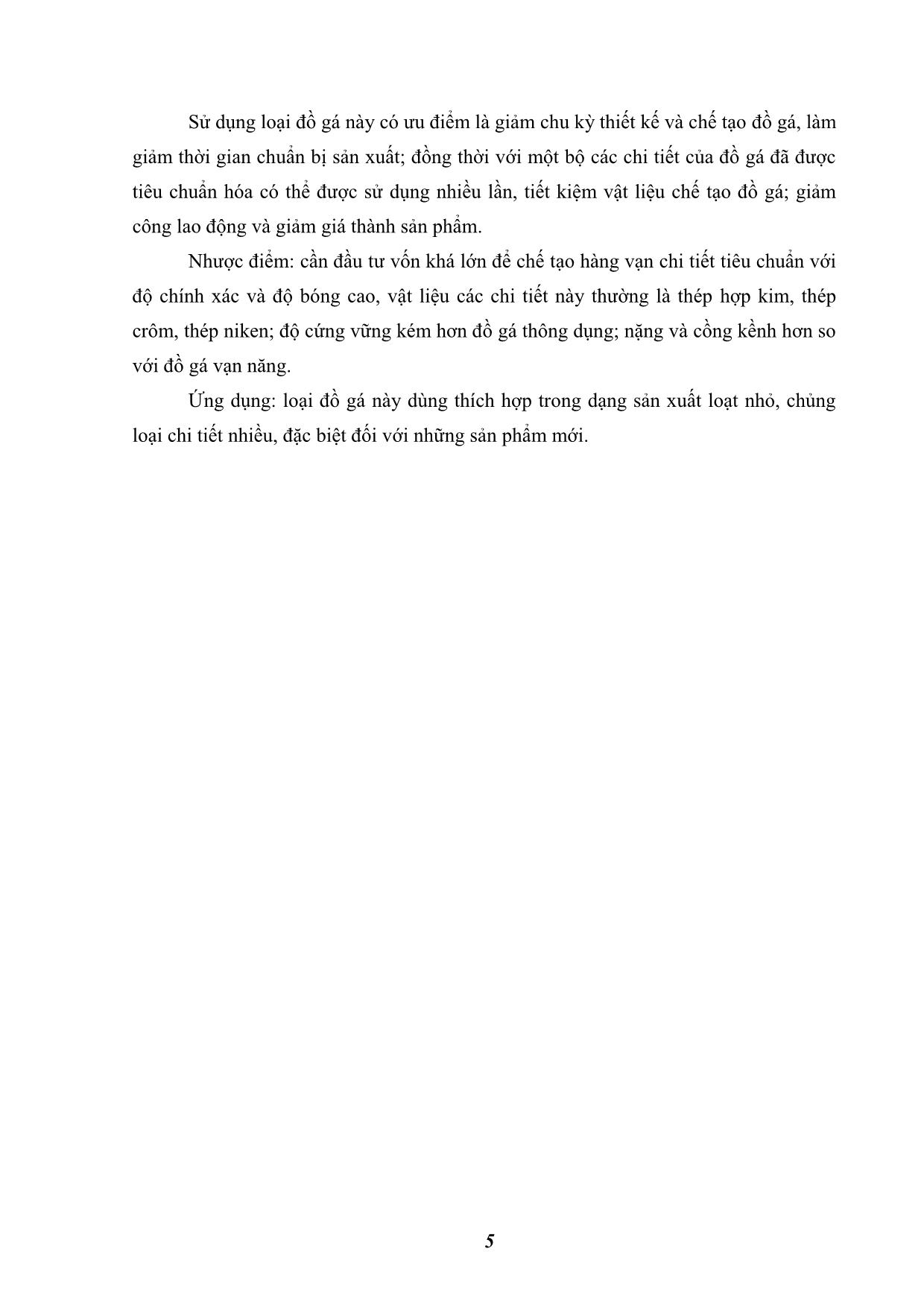
Trang 10
Tải về để xem bản đầy đủ
Tóm tắt nội dung tài liệu: Giáo trình Đồ gá trên máy công cụ
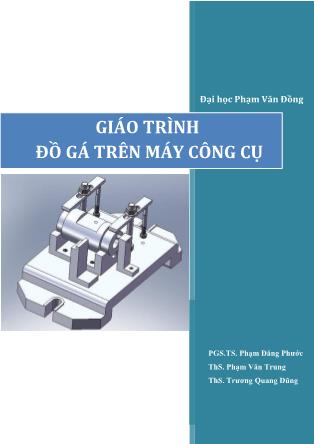
Đại học Phạm Văn Đồng PGS.TS. Phạm Đăng Phước ThS. Phạm Văn Trung ThS. Trương Quang Dũng 5/2017 GIÁO TRÌNH ĐỒ GÁ TRÊN MÁY CÔNG CỤ U N T N QUẢN N TRƯỜN ĐẠ ỌC P ẠM VĂN ĐỒN ---------- PGS.TS. Phạm Đăng Phước (chủ biên) ThS. Phạm Văn Trung ThS. Trương Quang Dũng GIÁO TRÌNH ĐỒ GÁ TRÊN MÁY CÔNG CỤ (Dùng cho bậc ĐH) Quảng Ngãi, tháng 12/2018 i MỤC LỤC LỜI NÓI ĐẦU ................................................................................................................ 1 Chương 1: TỔNG QUAN VỀ ĐỒ GÁ ......................................................................... 2 1.1. Khái niệm chung về các loại đồ gá và trang bị công nghệ ................................... 2 1.2. Định nghĩa và công dụng của đồ gá trên máy cắt kim loại .................................. 3 1.2.1. Định nghĩa đồ gá máy cắt kim loại: ............................................................... 3 1.2.2. Công dụng của đồ gá máy cắt kim loại: ........................................................ 3 1.3. Phân loại đồ gá trên máy công cụ ......................................................................... 3 1.3.1 Phân loại theo nhóm máy ............................................................................... 3 1.3.2 Phân loại theo mức độ chuyên môn hóa ......................................................... 4 1.3.3 Phân loại theo nguồn động lực ....................................................................... 8 1.4. Các thành phần chính của đồ gá ........................................................................... 8 1.5. Yêu cầu đối với đồ gá trên máy cắt kim loại ........................................................ 9 Chương 2: ĐỊNH VỊ VÀ ĐỒ ĐỊNH VỊ ..................................................................... 11 2.1. Quá trình gá đặt chi tiết ...................................................................................... 11 2.1.1. Khái niệm về định vị ................................................................................... 11 2.1.2. Yêu cầu đối với đồ định vị .......................................................................... 12 2.1.3. Nguyên tắc định vị 6 điểm........................................................................... 12 2.2. Sai số gá đặt ........................................................................................................ 16 2.2.1. Sai số chuẩn ................................................................................................. 17 2.2.2. Sai số kẹp chặt ............................................................................................. 25 2.2.3. Sai số đồ gá .................................................................................................. 28 2.3. Các chi tiết định vị của đồ gá ............................................................................. 30 2.4. Các chi tiết định vị mặt phẳng ............................................................................ 31 2.4.1. Các chi tiết định vị chính ............................................................................. 31 2.4.2. Các chi tiết định vị phụ ................................................................................ 36 2.5. Các chi tiết định vị mặt trụ ngoài ....................................................................... 38 2.6. Các chi tiết định vị mặt trụ trong ........................................................................ 38 2.6.1. Chốt gá (chốt trụ) ......................................................................................... 39 2.6.2. Chốt côn định vị .......................................................................................... 40 2.6.3. Trục gá (chốt tâm) ....................................................................................... 40 2.6.4. Tính sai số định vị khi định vị bằng mặt trong ............................................ 42 ii 2.6.5. Mũi tâm ....................................................................................................... 44 2.7. Định vị kết hợp ................................................................................................... 46 Chương 3: KẸP CHẶT VÀ CÁC CƠ CẤU KẸP CHẶT ........................................ 54 3.1. Khái niệm về kẹp chặt ........................................................................................ 54 3.2. Yêu cầu đối với cơ cấu kẹp chặt. ........................................................................ 54 3.3. Phương pháp xác định lực kẹp ........................................................................... 55 3.3.1. Phương và chiều của lực kẹp ....................................................................... 55 3.3.2. Điểm đặt của lực kẹp ................................................................................... 56 3.3.3 Phân loại cơ cấu kẹp chặt ........................................................................... ... m việc). - Ít rò khí, thể tích bé, giá thành rẻ hơn xilanh - pittong. - Ít tốn hơi ép hơn. Nhược điểm của xilanh màng là: hành trình ngắn nên chỉ dùng cho chi tiết gia công nhỏ. Thường hành trình của cán không quá 1/3 đường kính màng. Tính lực kẹp của pittong – xilanh màng: iện tích làm việc của màng là hình tròn đường kính . Nhưng áp lực hơi ép tác dụng lên diện tích có đường kính d (đĩa kim loại đỡ) sẽ truyền toàn bộ lên cán và có giá trị: 2 1 . 4 Q d p (3.58) Áp lực hơi ép tác dụng lên diện tích vành khăn ( -d) sẽ không truyền được toàn bộ lên cán, mà một phần lực tác dụng lên vỏ xilanh vì màng bị kẹp giữa hai vỏ. Càng gần vỏ bao nhiêu thì áp lực tác dụng lên màng và đĩa càng ít bấy nhiêu. Xét một phân bố hình vành khăn cách tâm một đoạn là ρ (giữa d và ) và có bề rộng (ρ+dρ) Áp lực khí nén tác dụng lên diện tích hình vành khăn 2 .d sẽ truyền lên cán theo tỷ lệ: R R r (3.59) Với 2 d r ; 2 D R Hình 3.30 89 o đó lực truyền lên cán pittong trên cả diện tích hình vành khăn: 2 . .2 . . R r R Q p d R r (3.60) 2 2 3 3 2 2 2 3 p R r R r Q R R r (3.61) 2 22 2 3 p Q R Rr r (3.62) Vậy tổng lực truyền lên cán (kể cả diện tích có đường kính d) là: Q = Q1 + Q2 – q (3.63) 2 2 12 p Q D Dd d q (3.64) Trong đó: p – áp suất hơi ép D – đường kính lớn của xilanh d – đường kính đĩa q – lực chống lại của lò xo 3.8.2. Truyền động bằng dầu ép ầu ép cũng là một hình thức truyền động hay dùng trong đồ gá tuy có ít hơn hơi ép. ầu thủy lực có áp suất cao hơn khí nén nhiều (tới 60÷70 atm), lại ít bị nén, đàn tính kém nên dùng cho các chi tiết gia công to và nặng có lực cắt lớn rất thích hợp. ầu ép có những nhược điểm sau: vận tốc làm việc bé, để duy trì áp suất làm việc cần có nhiều phần tử kèm theo máy nên vốn đầu tư lớn. Nếu trên máy cắt kim loại có hệ thống bơm dầu thì có thể tách ra một nhánh làm nguồn cấp. Sơ đồ làm việc của một cơ cấu dầu ép như hình 3.31. Hình 3.31. Sơ đồ hệ thống dầu ép 1- Bơm thủy lực 2- Bể chứa dầu 3- Van phân phối 4- Xilanh thủy lực 5- Van tràn 90 ệ thống trang bị cần thiết để sử dụng cơ cấu sinh lực bằng dầu ép gồm: Động cơ – bơm thủy lực, thệ thống đường ống, bể chứa dầu, thiết bị điều khiển, xilanh công tác Xilanh công tác được chia thành hai loại: loại cố định và loại quay. Xilanh cố định có hai loại: loại tác động một chiều (hình 3.32) và loại tác động hai chiều (hình 3.33). Xilanh quay (xilanh chuyển động) được chia thành hai loại: loại cánh và loại pittong. Hình 3.32. Các xilanh thủy lực tác dụng một chiều a) Loại đẩy; b) Loại kéo 1. Ống dẫn dầu; 2. Pittong; 3. Lò xo; 4. Cán pittong Nguyên lý làm việc của loại xilanh tác động một chiều như sau: dầu đi theo ống 1 vào buồng A của xilanh và đẩy pittong 2 cùng cán 4 về phía bên phải của loại đẩy (hình 3.32a) và về phía bên trái của loại kéo (hình 3.32b). Khi tháo lỏng chi tiết thì lò xo 3 đẩy pittong 2 cùng cán 4 về phía bên trái của loại đẩy và về phía bên phải của loại kéo. Hình 3.33. Xilanh thủy lực tác động hai chiều 1. Cán pittong; 2. Pittong 91 Với xilanh tác động hai chiều (hình 3.33) dầu thủy lực được bơm vào cả hai buồng trái và phải của xilanh và đẩy pittong 2 cùng cán 1 về hai phía khi kẹp chặt và khi tháo lỏng chi tiết gia công. Lực Q ở cán pittong của xilanh một chiều (hình 3.32) được xác định như sau: - Loại đẩy: 2 . . 4 D Q p q (3.65) - Loại kéo: 2 2( ) . . 4 D d Q p q (3.66) Lực Q ở cán pittong của xilanh hai chiều (hình 3.33) được xác định như sau: - Khi dầu bơm vào buồng không có cán pittong: 2 . . 4 t D Q p (3.67) - Khi dầu bơm vào buồng có cán pittong: 2 2( ) . . 4 p D d Q p (3.68) Trong đó: D – đường kính xilanh. d – đường kính cán pittong. p – áp suất của dầu tác dụng lên pittong. q – lực cản của lò xo. η – hiệu suất của xilanh, η = 0,85÷0,9. Năng suất (lít/phút) V của máy bơm: 1 . 1000. . . Q L V t p (lít/phút) (3.69) Trong đó: Q – lực ở cán pittong (k ). L – chiều dài hành trình làm việc của pittong (cm). t – thời gian của hành trình làm việc của pittong (phút) p – áp suất của dầu (Mpa hoặc k /cm2). 92 η1 – hiệu suất thể tích của hệ thống thủy lực (do không kín khít), η1=0,85. Khi biết áp suất của dầu là p, lực kẹp là Q, ta có thể tính diện tích F của pittong theo công thức: 2 4 D Q F p Suy ra đường kính của pittong: 4. 4. 1,13 . F Q Q D p p (3.70) Thời gian t (phút) cho cán pittong chuyển động một hành trình được xác định theo công thức: 2 3 . 4.10 . D L t V (3.71) Công suất cho cơ cấu dẫn động của bơm được xác định theo công thức: 2 . 612. V p N (kW) (3.72) Ở đây: V – năng suất của máy bơm (lít/phút) p – áp suất của dầu (Mpa hoặc k /cm2) η2 – hiệu suất của máy bơm, η2 = 0,85. 3.8.3. Cơ cấu sinh lực nhờ lực hút điện từ Nguyên lý làm việc: Loại cơ cấu này thường dùng để kẹp chặt trực tiếp các chi tiết phẳng, mỏng. Nó có ưu điểm rất lớn là không gây biến dạng chi tiết như các cơ cấu kẹp chặt khác, không cản trở quá trình cắt. Có thể dùng từ vĩnh cửu hay điện từ. Từ vĩnh cửu ít được dùng vì lực kẹp hạn chế và sau một thời gian từ trường yếu vì nhiệt độ hoặc thay đổi hoặc vì xung lực. Còn điện từ được dùng nhiều hơn, nhất là trên máy mài hoặc đôi khi trên máy phay, máy khoan để gia công các chi tiết phức tạp. Sơ đồ của khối điện từ như hình 3.34 93 Hình 3.34a. Sơ đồ khối điện từ ồm cuộn dây 6 cuốn quanh lõi 2, lớp cách từ 5 ngăn cách với lõi 4 với tấm dẫn 3 để đại đa số đường sức sau khi thông qua chi tiết có thể về tấm dẫn từ 3, chứ không từ lõi 4 qua tấm dẫn từ 3 chuyển về vỏ 1 làm từ thông yếu đi. Khi dòng điện một chiều qua cuộn dây 6, chi tiết 7 sẽ được hút chặt xuống tấm dẫn từ 3. Sự phân bố lõi tùy thuộc theo kết cấu chi tiết (phân bố hình bầu dục, phân bố ngang, phân bố dọc, phân bố hình sao). Chú ý: Điện từ phải dùng dòng điện một chiều. Chất cách từ thường dùng đồng, nhôm hoặc hợp kim babit. Trình tự tính toán: 1- Xác định lực hút của bàn từ để giữ chặt chi tiết dưới tác dụng của lực cắt: F = T.f = k.Px (3.73) . x k T P f (3.74) Trong đó: f – hệ số ma sát giữa chi tiết gia công và bàn từ (f=0,1÷0,15); k – hệ số an toàn; Px – lực cắt. 2- Xác định số cặp cực: bằng 2n, tùy theo kích thước và hình dáng của chi tiết (với bàn từ có chiều dài 300 ÷900, thì bước phân bố các cực n lấy từ 35÷50mm). Cũng có thể xác định bằng phương pháp tính toán để khoảng cách giữa hai cực bằng hai lần bề dày của lõi từ, khi đó lực sinh ra ở mỗi cặp cực là: ' 2 T T n (N) (3.75) 1- Vỏ 2- Lõi từ 3- Tấm dẫn từ 4- Lõi 5- Lớp cách từ 6- Cuộn dây 7- Chi tiết Hình 3.34b 94 3- Tính diện tích mặt cắt của cực từ (Q). ' 6 2 25. .10T Q B (cm 2 ) (3.76) Trong đó: Q – diện tích cực từ (cm2) T’ – lực hút của mỗi cặp từ (N) B – cường độ cảm ứng từ của vật liệu lõi, tra theo bảng 3-1. 4- Xác định từ trở chung theo công thức: ' 1. ' . n i i i i ll S Q Q (3.77) Trong đó: l1, l2,, ln – chiều dài của mỗi đoạn tính từ trở (cm). μi – hệ số dẫn từ của vật liệu trên đoạn thứ i, tra theo bảng 3-1. Q’i – diện tích của mặt cắt đoạn thứ i (cm 2 ). (3.78) 5- Xác định tổng từ thông (giả thiết hao phí 30%): Φ = 0,7. .Q Bảng 3-1 Trị số cường độ cảm ứng từ và hệ số dẫn từ μ 6- Tính số ampe-vòng của cuộn dây: . 0,4. S I (3.79) Trong đó: I – cường độ dòng điện (A). ω – số vòng của cuộn dây. Φ – Tổng từ thông (Φ= .Q). 7- Xác định đường kính dây dẫn của cuộn dây: 95 4. . I d q (mm) (3.80) Trong đó: q – mật độ dòng điện cho phép 2 (3 5) A q mm Cơ cấu sinh lực bằng điện từ, so với các cơ cấu sinh lực khác, có những ưu điểm sau: lực tác dụng nhanh, không làm hỏng bề mặt kẹp chặt của chi tiết ở những nguyên công cuối, lực kẹp phân bố đều trên mặt tiếp xúc, có thể kẹp chặt nhiều chi tiết nhỏ cùng một lúc, sử dụng thuận tiện, không cần nhiều các trang bị phụ. Nhược điểm cơ bản của diện từ là: lực kẹp không lớn so với các cơ cấu cơ khí khác, không kẹp được các chi tiết làm bằng vật liệu không dẫn từ, có khả năng gây ra sự cố khi nguồn năng lượng cung cấp cho các cuộn dây điện từ bị mất điện đột ngột. 3.8.4. Cơ cấu sinh lực nhờ lực ly tâm Hình 3.35. Cơ cấu sinh lực do xuất hiện lực ly tâm 1 - Bi trượt; 2 - Vỏ đỡ; 3 - Bích cố định; 4 - Mặt bích; 5 - Trục rút. Cơ cấu sinh lực nhờ lực ly tâm thường được sử dụng khi chi tiết gia công cần có chuyển động quay tròn như khi tiện trục, trong trường hợp này đồ để gá đặt cũng phải quay tròn. Trên hình 3.35 là một loại cơ cấu sinh lực nhờ lực ly tâm. Trục rút 5 bắt chặt với bích 4. Một vật nặng hoặc bi 1 nằm giữa mặt côn của vỏ 2 và mặt bích 4. Khi đồ gá quay, do xuất hiện lực ly tâm, bi 1 bị văng ra nhưng một phía tỳ vào mặt côn nên đẩy bích 4 về phía trái kéo theo trục 5 trượt trong lỗ của vỏ 2 và tạo ra lực kéo Q tác dụng vào cơ cấu kẹp. Khi ngừng quay, bi 1 tụt vào nhờ lực đẩy của lò xo thông qua bích 4 đẩy trục 5 về phía phải, tác dụng vào cơ cấu kẹp để tháo lỏng chi tiết đã gia công xong và gá phôi mới vào cơ cấu kẹp. 96 Ngoài các cơ cấu sinh lực trên thì trong đồ gá người ta còn dùng kẹp bằng chất dẻo, lực chân không, cơ cấu sinh lực kẹp nhờ chuyển động tiến dao (phiến dẫn khoan), cơ cấu sinh lực khi có lực cắt, 3.9. Kẹp chặt nhiều chi tiết đồng thời Để nâng cao năng suất lao động trong những trường hợp có thể cần gia công nhiều chi tiết cùng một lúc (nhất là đối với các chi tiết nhỏ, mặt gia công đơn giản). Việc kẹp nhiều chi tiết đồng thời có một ý nghĩa rất lớn trong kết cấu đồ gá. Theo chiều của lực kẹp có thể phân loại như sau: a) Kẹp liên tục: lực kẹp bằng nhau, truyền từ chi tiết này sang chi tiết khác theo cùng một chiều. Hình 3.36. Cơ cấu kẹp liên tục b) Kẹp song song: lực kẹp phân bố đều nhau trên nhiều chi tiết theo cùng một hướng song song nhau. Hình 3.37. Cơ cấu kẹp có lực kẹp song song c) Lực kẹp ngược chiều nhau: lực kẹp phân bố lên hai chi tiết hoặc hai nhóm chi tiết song song nhưng ngược chiều nhau. 97 Hình 3.38. Cơ cấu kẹp có lực kẹp song song ngược chiều d) Lực kẹp giao nhau: chiều lực kẹp giao nhau thành một góc. e) Kẹp tổ hợp: đồng thời ứng dụng hai hoặc nhiều kiểu trên. Hình 3.39. Cơ cấu kẹp tổ hợp Chú ý: Khi kẹp liên tục do dung sai của bề mặt định vị của chi tiết không bằng nhau nên cơ cấu kẹp sẽ dồn các chitiết theo chiều lực kẹp, nên sai số tích lũy sẽ cộng dồn càng nhiều ở các chi tiết sau. Vì thế dùng cơ cấu loại này chỉ nên cho trường hợp kích thước khởi xuất thẳng góc với chiều lực kẹp, nghĩa là bề mặt gia công song song với chiều lực kẹp. Khi kẹp song song do dung sai của các chi tiết nên miếng kẹp cứng sẽ không thể kẹp tất cả các chi tiết. o đó chỉ nên sử dụng miếng kẹp tự lựa. 98 3.10. Các cơ cấu kẹp nhanh bằng tay Ren vít là một loại kẹp tốn nhiều thời gian để quay, ảnh hưởng đến năng suất lao động và tiêu tốn sức lao động, vì thế khi kẹp bằng ren vít cần nghiên cứu sao cho nhanh. Hình 3.40 là một cơ cấu kẹp nhanh bằng tay. Nguyên lý làm việc của cơ cấu như sau: khi quay tay quay 2 (đầu quay là một đai ốc) nhờ ren vít mà đòn 1 tiến sang trái để kẹp chặt chi tiết. Vít định vị 4 được cắm vào rãnh của đòn kẹp 1 để chống xoay (đảm bảo cho đòn 1 tiến sang trái). Khi tháo thì tiến hành hạ khối đệm 3 xuống và rút đòn kẹp 1 về phía sau (về bên phải). Để kẹp chặt chi tiết tiếp theo, sau khi định vị chi tiết ta đẩy đòn kẹp 1 về bên trái cho tiếp xúc chi tiết gia công, sau đó nâng khối đệm 3 lên và quay tay quay 2 khoảng nửa vòng là có thể kẹp chặt được chi tiết. Hình 3.40. Cơ cấu kẹp nhanh bằng tay 1. Đòn kẹp; 2. Tay quay; 3. Khối đệm; 4. Vít định vị 99 CÂU HỎI ÔN TẬP 1) Mục đích của kẹp chặt khi gá đặt chi tiết? 2) Cơ cấu kẹp chặt cần đạt được những yêu cầu nào? 3) Phương và điểm đặt cần đạt yêu cầu gì? Tại sao? 4) Tại sao kẹp chặt bằng chêm lại tự hãm được? 5) Nguyên tắc kẹp bằng bánh lệch tâm? Cách tính lực kẹp và điều kiện tự hãm của lệch tâm tròn? 6) Cơ cấu phóng đại lực kẹp nhằm mục đích gì? 7) Ưu – khuyết điểm của kẹp bằng hơi ép? 8) Căn cứ vào những yếu tố nào để chọn hình thức kẹp hợp lý cho đồ gá? 9) Tính lực kẹp W khi khoan lỗ trên chi tiết, sơ đồ định vị, kẹp chặt như hình vẽ. Lực cắt gây moment xoắn Mx= 0,8 K .m, bỏ qua lực chiều trục P0. iết hệ số ma sát tại các chỗ tiếp xúc là f = 0,1. Đường kính = 60mm; óc khối V là = 120 0 . Hình 3.41 10) Cần bào vát một phần của chi tiết trục bậc, đạt kích thước h. Chi tiết được định vị ở phần trụ nhỏ có đường kính d, trên khối V, có góc V là α. Kẹp chặt bằng Xy lanh- Pittong khí nén. iết lực cắt là Pc; hệ số ma sát tại các chỗ tiếp xúc là f; áp lực của khí nén là p; lực nén của lò xo là q. Tính đường kính của Pittong để tạo ra lực kẹp W theo yêu cầu Hình 3.42 ình chiếu bằng D P0 M W W D W d h p P D 100 11) Cần bào vát một phần của chi tiết trục bậc, đạt kích thước h. Chi tiết được định vị ở phần trụ nhỏ có đường kính d, trên khối V, có góc V là α. Kẹp chặt bằng Xy lanh khí nén phối hợp với tay đòn; có các kích thước như hình vẽ. iết lực cắt là Pc; hệ số ma sát tại các chỗ tiếp xúc là f; áp lực khí nén là p; lực lò xo là q. Tính đường kính của Pittong để tạo lực kẹp theo yêu cầu. Hình 3.43 12) Tính lực Q theo sơ đồ định vị và kẹp chặt như hình vẽ để gia công mặt M. iết: Lực cắt là Pc; tay đòn có chiều dài L1, L2; góc chêm là α; góc khối V bằng 90 0 ; góc ma sát tại các chỗ tiếp xúc là φ; tỉ lệ đường kính của con lăn và đường kính chốt là d/ = 1/2. iệu suất cơ cấu tay đòn là η, hệ số an toàn là K. Hình 3.44 13) Hình 3.45 ia công đồng thời hai chi tiết đạt kích thước (hình 3.45). Chi tiết được định vị trên khối V có góc V là α. Kẹp chặt bằng ren vít phối hợp với tay đòn; có các kích thước L2 L1 Pc Q H W D M P P W W Q H D L L p Q L W Pc d h L2 W D 101 như hình vẽ. iết lực cắt là Pc; hệ số ma sát tại các chỗ tiếp xúc là f; hiệu suất của cơ cấu kẹp là η. Tính lực Q của cơ cấu ren vít để tạo ra lực kẹp W theo yêu cầu. 14) Tính lực tác dụng Q cần thiết để kẹp chặt chi tiết được định vị trên khối V, có góc V là α (hình 3.46). - iết: Lực cắt Pc ; hệ số ma sát trượt tại các chỗ tiếp xúc là f; chiều dài tay đòn: l1 và l2; đường kính chi tiết là ; kích thước mặt gia công là h; hiệu suất của cơ cấu kẹp là η. Hình 3.46 15) Tính đường kính của Pittông để tạo lực kẹp chặt chi tiết khi gia công mặt M, được định vị, kẹp chặt như hình 3.47. - iết: Lực cắt Pc ; hệ số ma sát tại các chỗ tiếp xúc là f; chiều dài tay đòn: l1 và l2; đường kính chi tiết là ct; kích thước gia công là h; lực lò xo là q; áp lực khí nén là p. hiệu suất của cơ cấu kẹp là η. l1 l2 Q Pc W h D l1 l2 Pc h p M Hình 3.47
File đính kèm:
giao_trinh_do_ga_tren_may_cong_cu.pdf
giaotrinh_dogap2_2842_558254.pdf