Paper sheets made from sugarcane bagasse and lemongrass by-products: Synthesis and properties
Plastic single-use packaging is one of the largest contributors to plastic pollution in Vietnam as well as in many
other countries. Alternative materials, especially materials derived from natural and renewable sources, should be
developed to solve this global issue. In this study, we aimed to investigate the synthesis and properties of packaging
paper sheets from sugarcane bagasse and lemongrass by-products. The delignification of the biomass was
implemented at different NaOH/biomass ratios and hydrolysis times while the paper making process was studied at
various sugarcane bagasse/lemongrass ratios and different amounts of glycerol and starch additives. The obtained
paper sheets were then tested for their mechanic properties and water absorption through ASTM (American Society
for Testing and Materials) procedures, and the biodegradability by scanning electron microscopy (SEM). The results
showed that the paper sheets at the optimized conditions had low thickness (0.3mm), density (0.4 g cm-3), and water
absorption but high tensile strength (19 N mm-2) and flexural modulus (17 N). These properties and their
biodegradability suggest that the paper sheets could potentially be used in packaging.
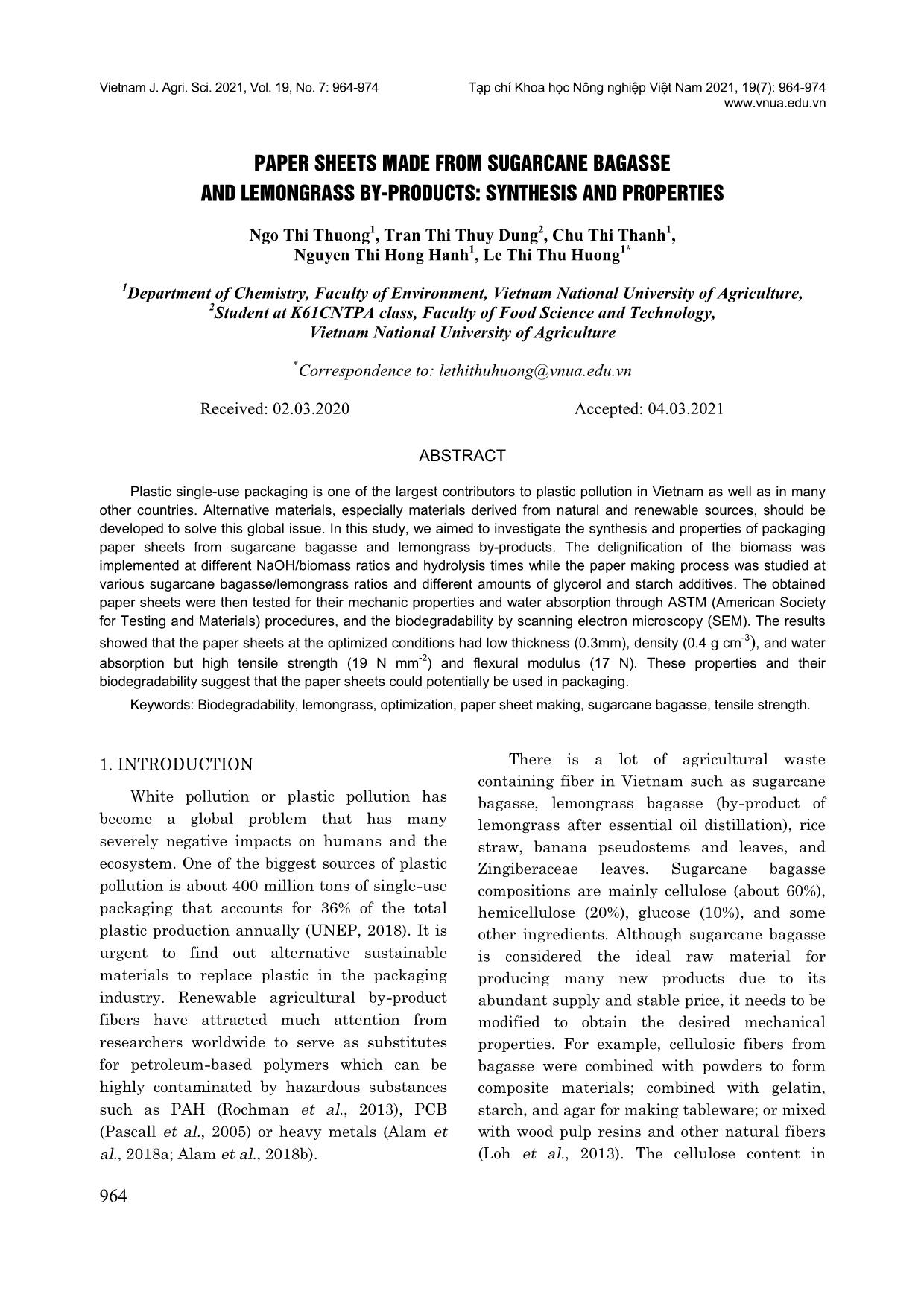
Trang 1
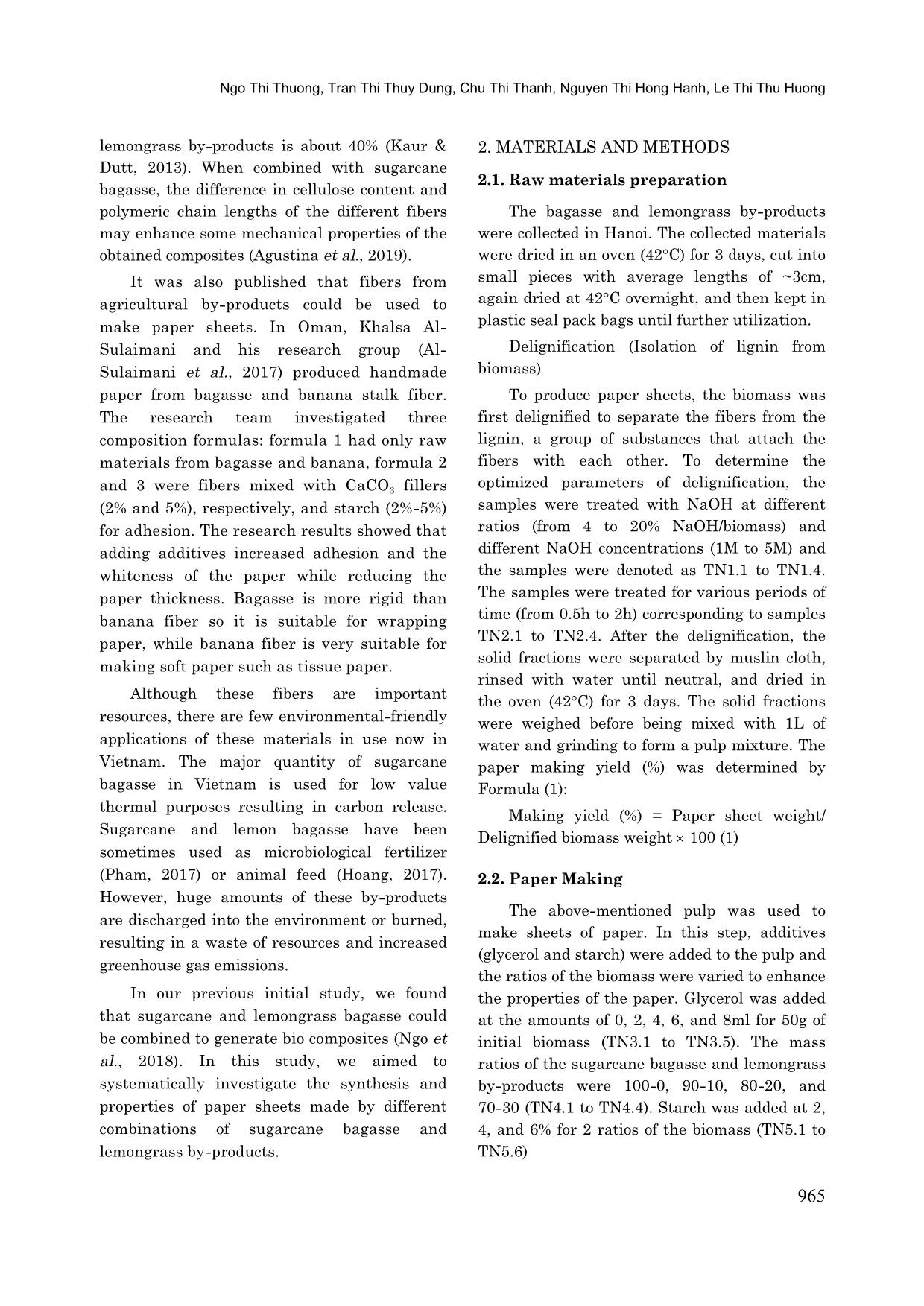
Trang 2
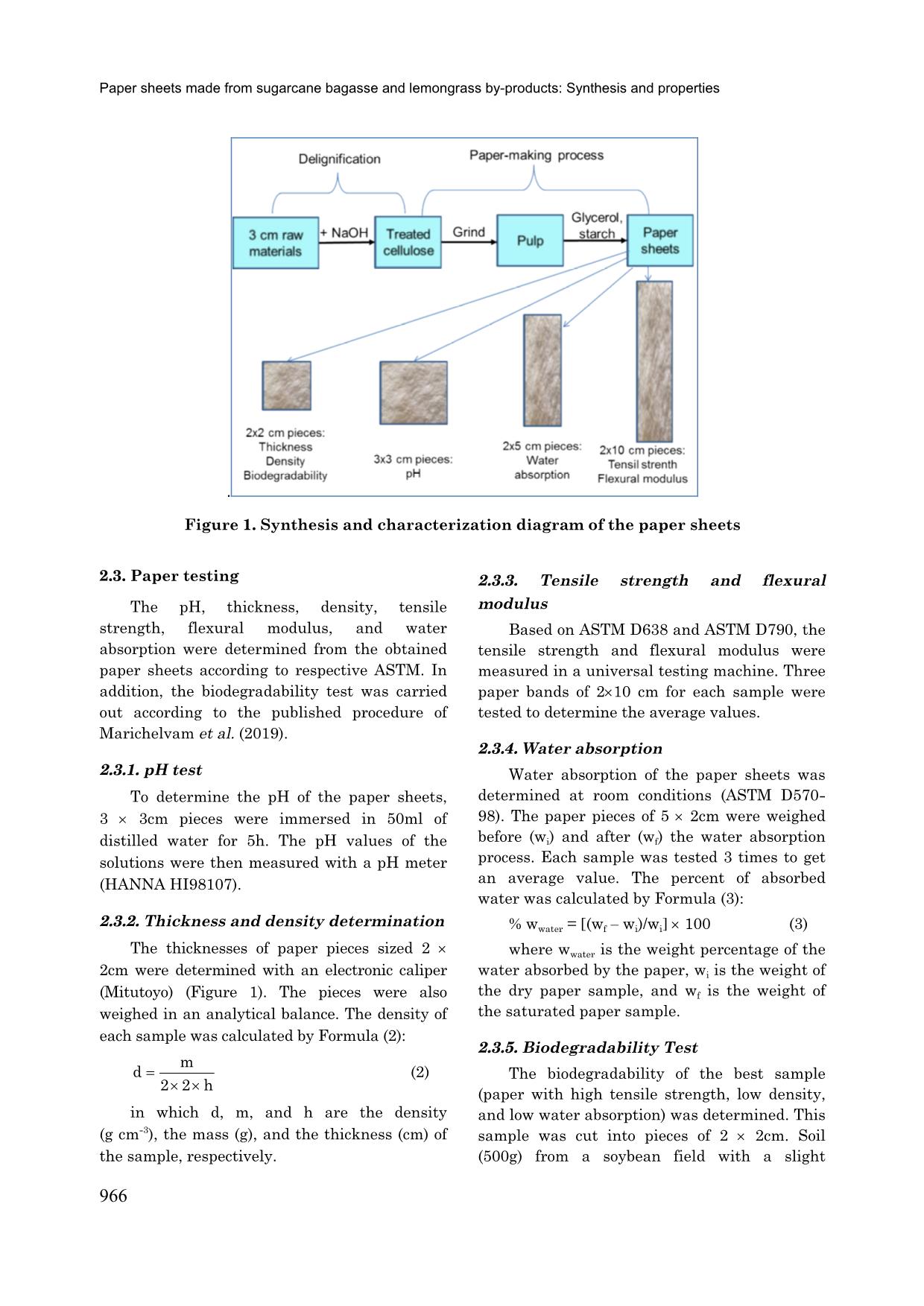
Trang 3
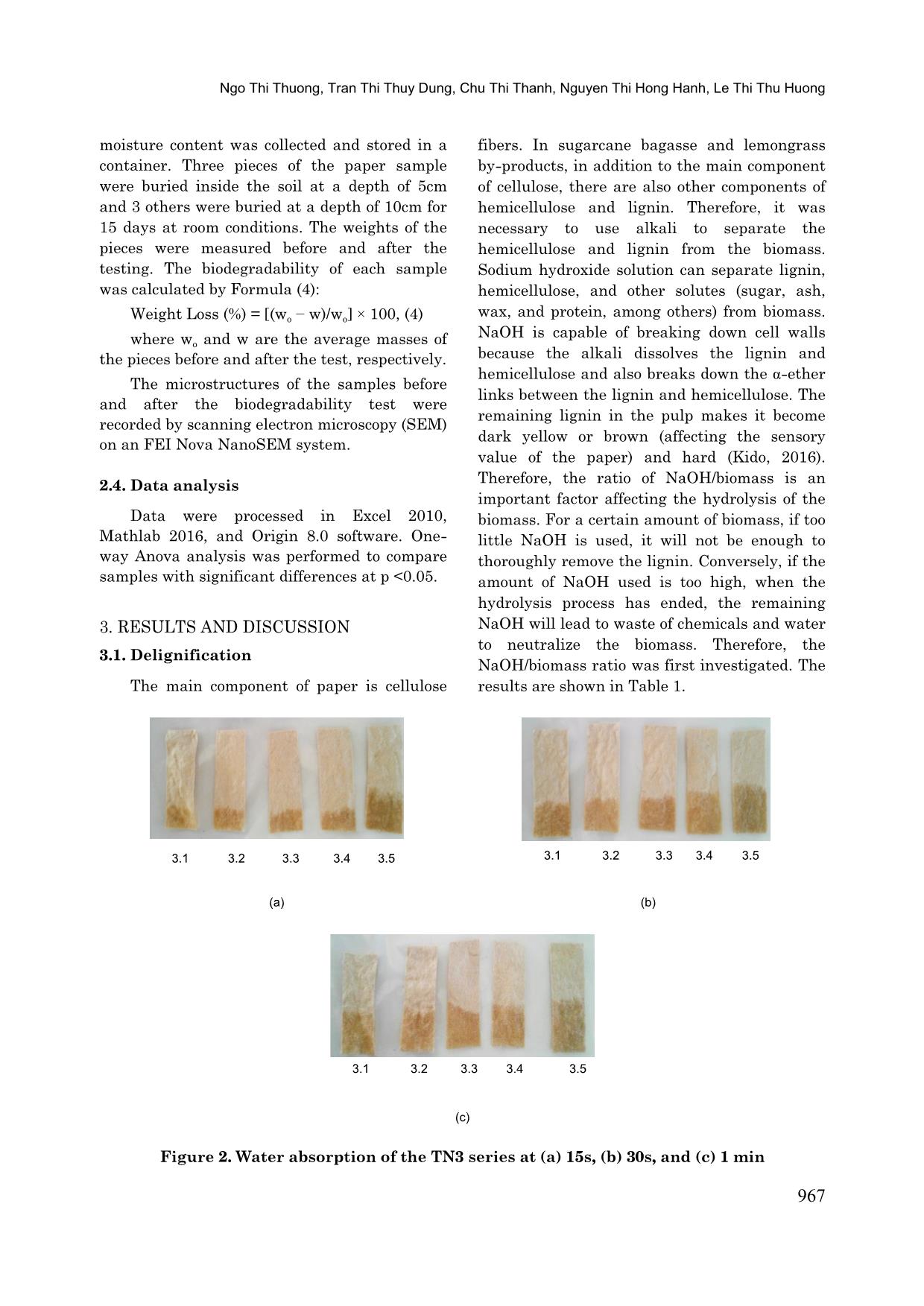
Trang 4
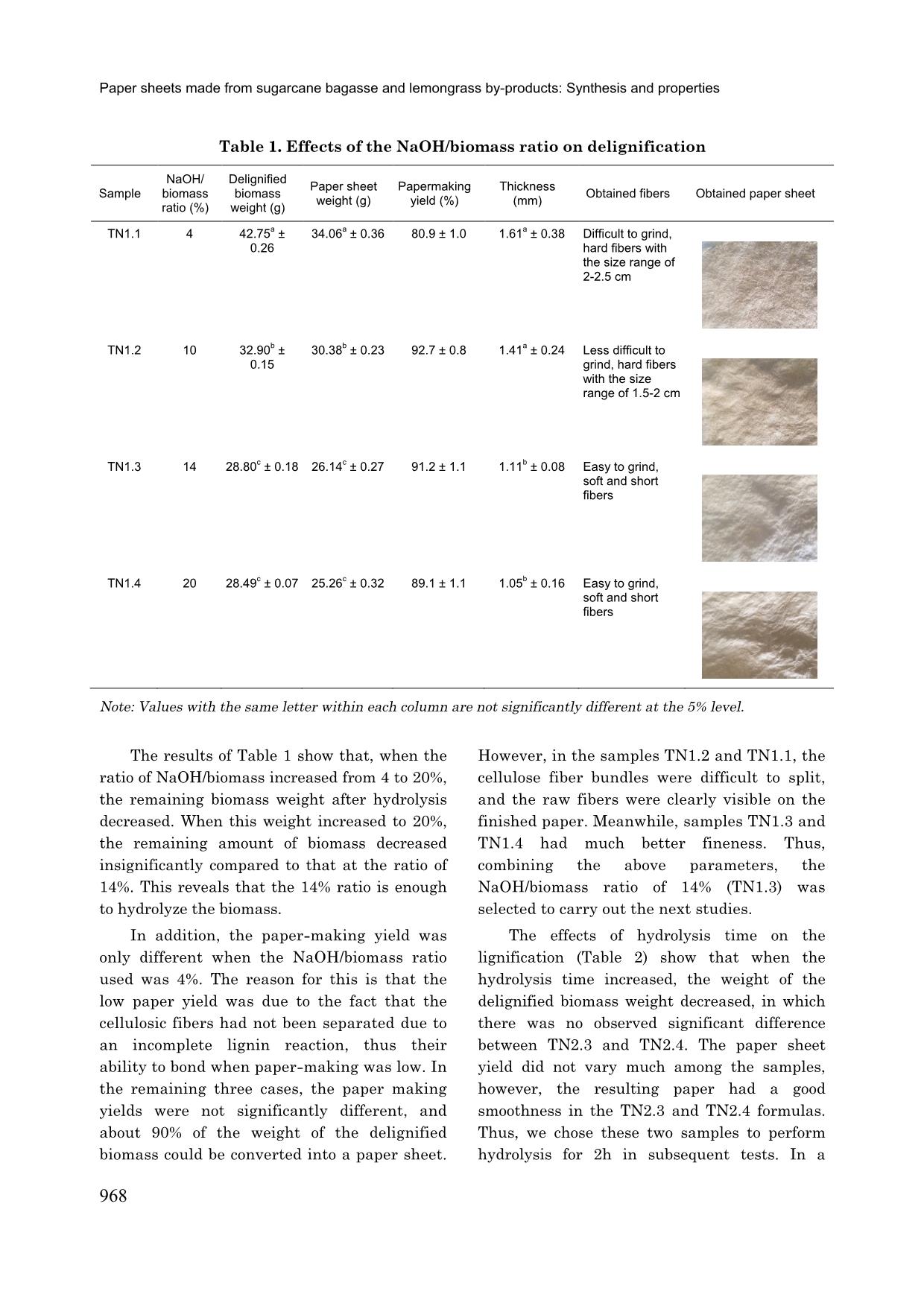
Trang 5
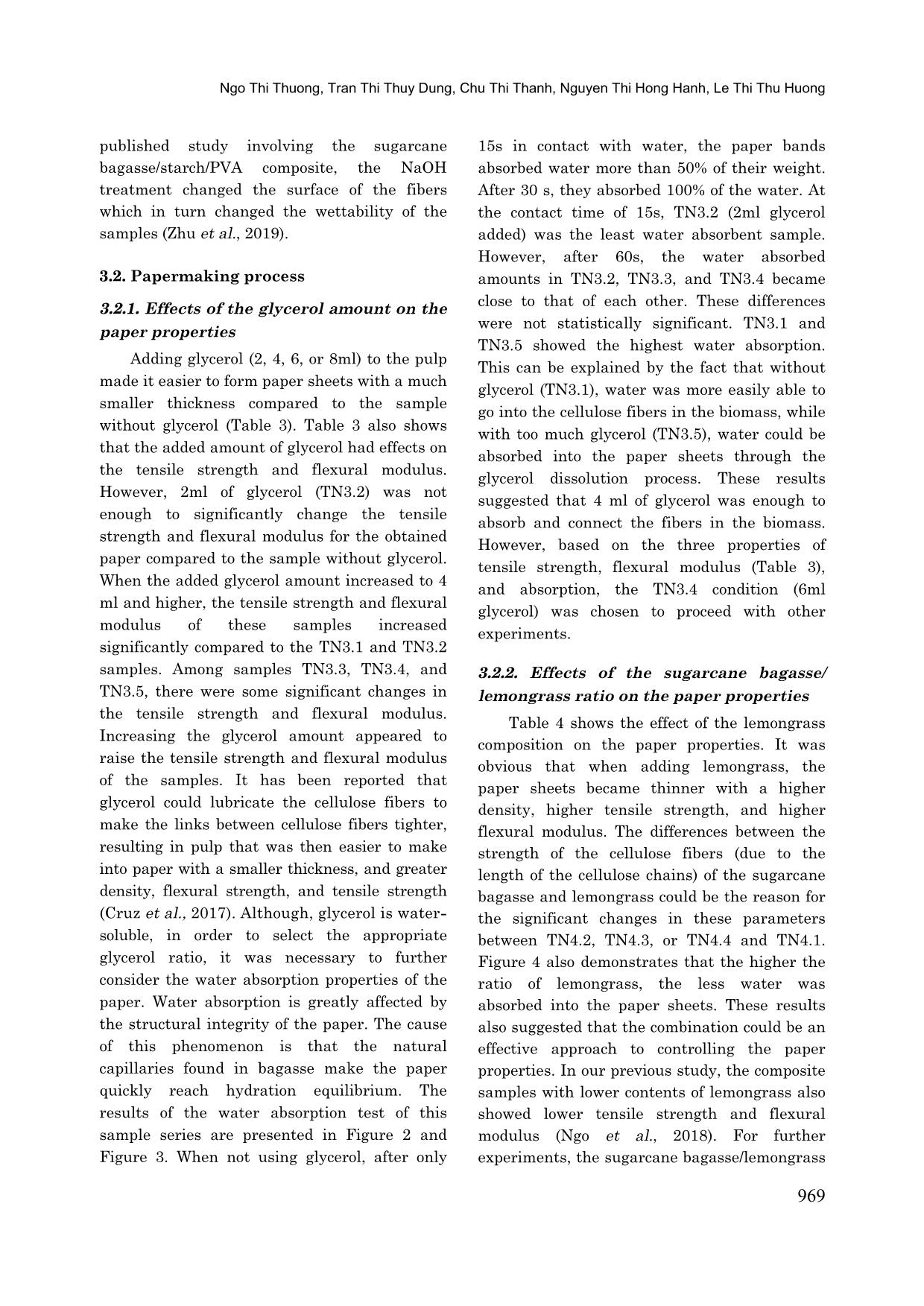
Trang 6
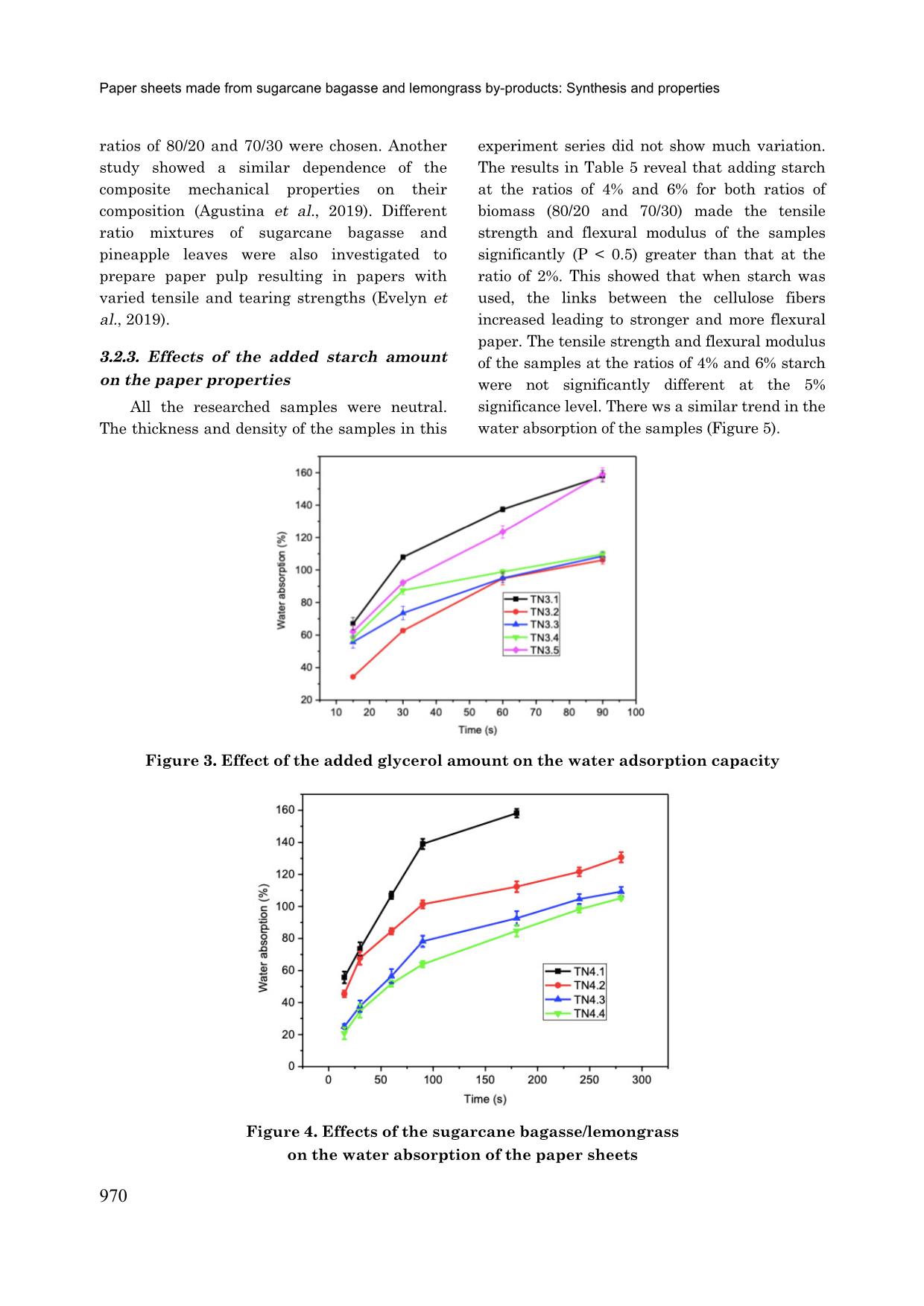
Trang 7
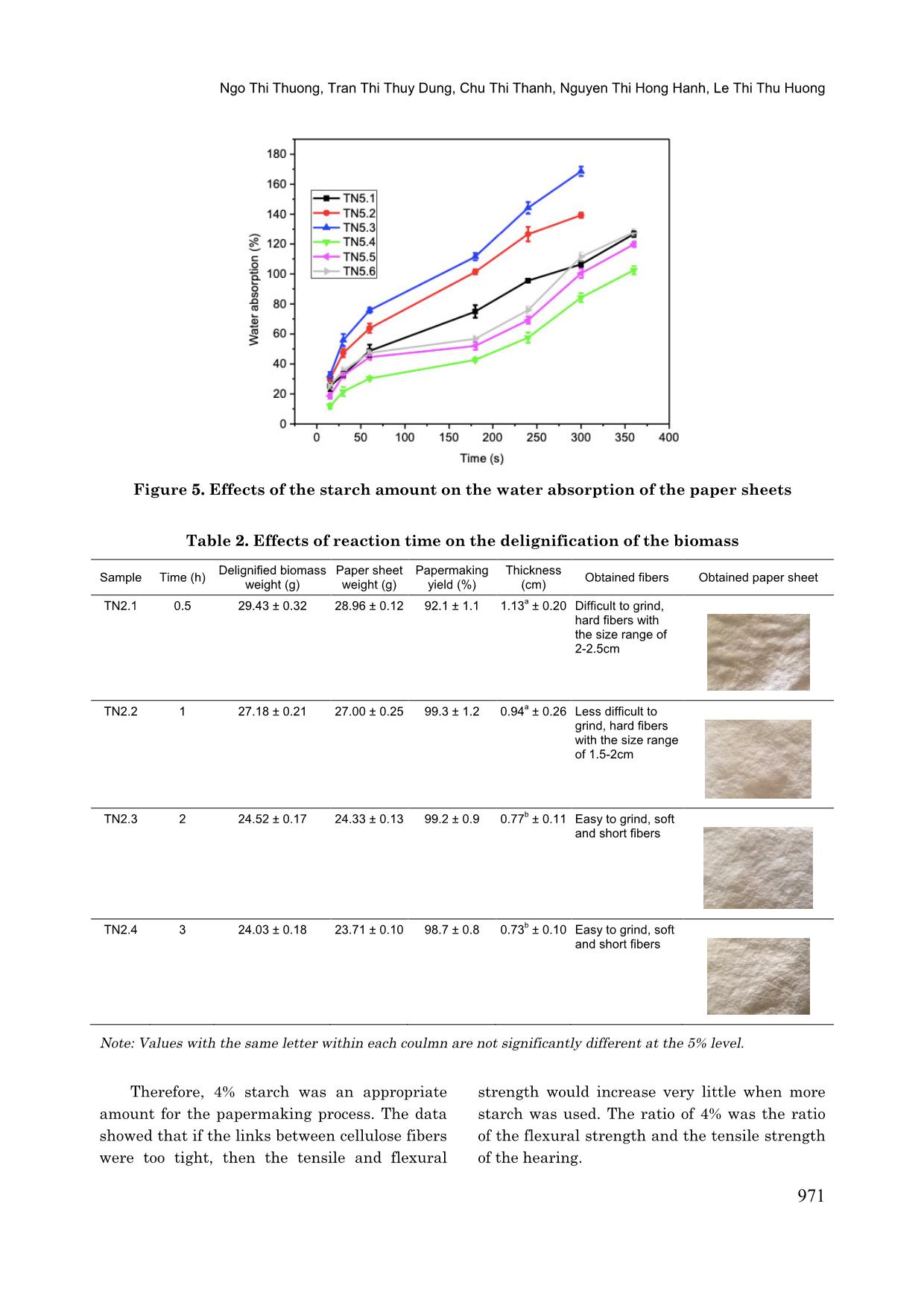
Trang 8
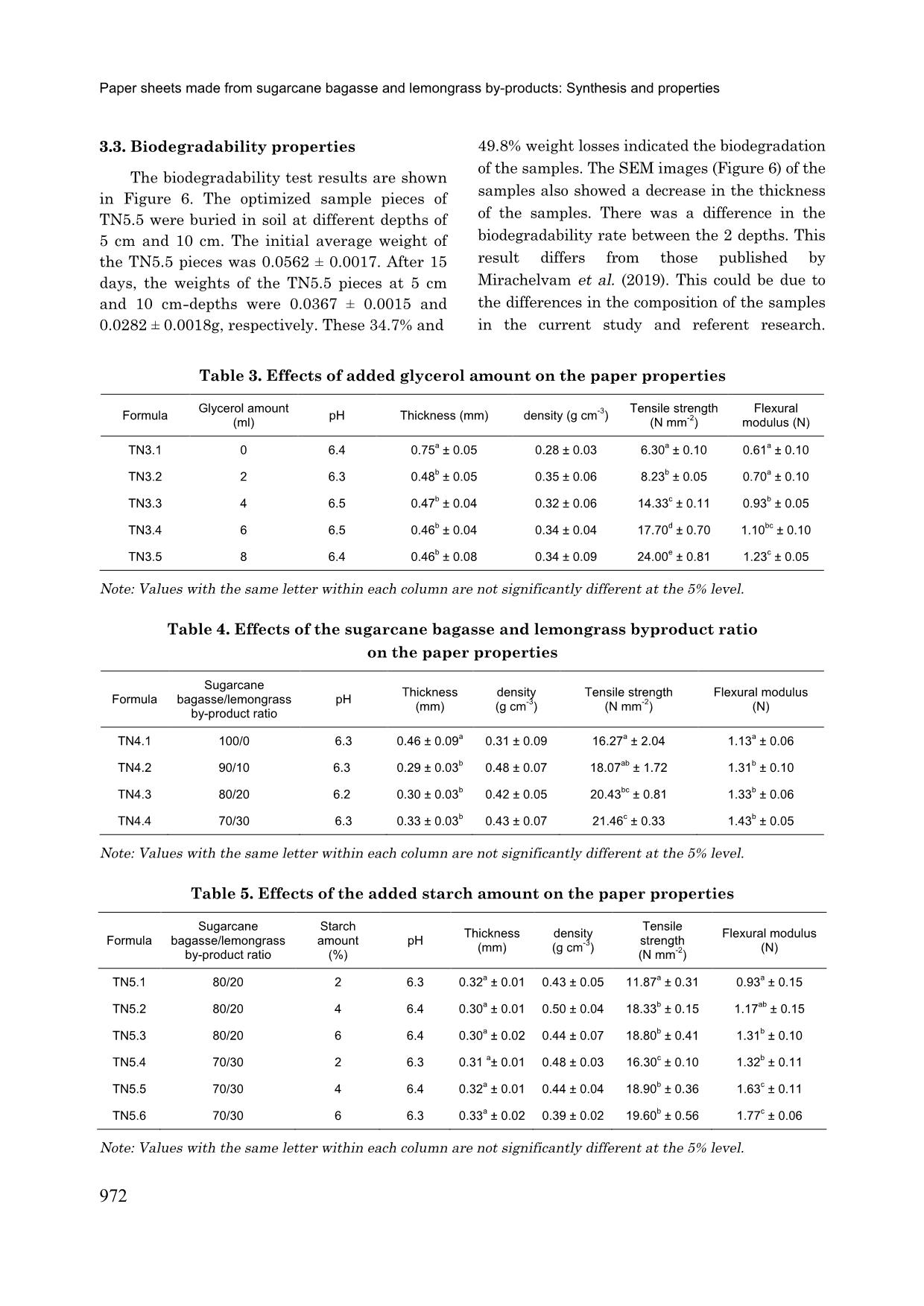
Trang 9
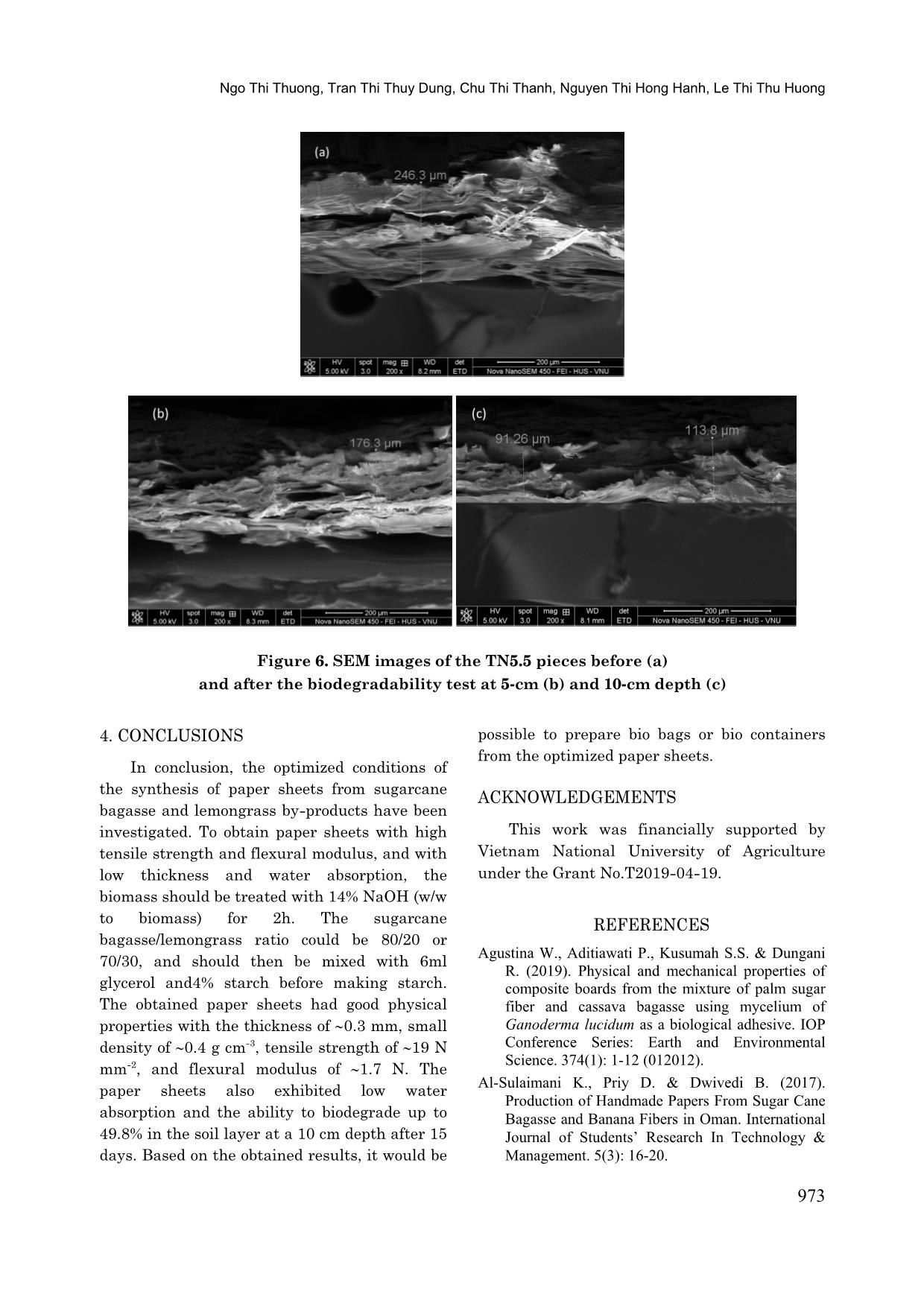
Trang 10
Tải về để xem bản đầy đủ
Tóm tắt nội dung tài liệu: Paper sheets made from sugarcane bagasse and lemongrass by-products: Synthesis and properties
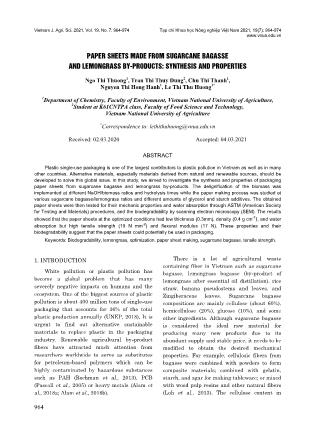
Vietnam J. Agri. Sci. 2021, Vol. 19, No. 7: 964-974 Tạp chí Khoa học Nông nghiệp Việt Nam 2021, 19(7): 964-974 www.vnua.edu.vn 964 PAPER SHEETS MADE FROM SUGARCANE BAGASSE AND LEMONGRASS BY-PRODUCTS: SYNTHESIS AND PROPERTIES Ngo Thi Thuong1, Tran Thi Thuy Dung2, Chu Thi Thanh1, Nguyen Thi Hong Hanh1, Le Thi Thu Huong1* 1Department of Chemistry, Faculty of Environment, Vietnam National University of Agriculture, 2Student at K61CNTPA class, Faculty of Food Science and Technology, Vietnam National University of Agriculture *Correspondence to: lethithuhuong@vnua.edu.vn Received: 02.03.2020 Accepted: 04.03.2021 ABSTRACT Plastic single-use packaging is one of the largest contributors to plastic pollution in Vietnam as well as in many other countries. Alternative materials, especially materials derived from natural and renewable sources, should be developed to solve this global issue. In this study, we aimed to investigate the synthesis and properties of packaging paper sheets from sugarcane bagasse and lemongrass by-products. The delignification of the biomass was implemented at different NaOH/biomass ratios and hydrolysis times while the paper making process was studied at various sugarcane bagasse/lemongrass ratios and different amounts of glycerol and starch additives. The obtained paper sheets were then tested for their mechanic properties and water absorption through ASTM (American Society for Testing and Materials) procedures, and the biodegradability by scanning electron microscopy (SEM). The results showed that the paper sheets at the optimized conditions had low thickness (0.3mm), density (0.4 g cm-3), and water absorption but high tensile strength (19 N mm-2) and flexural modulus (17 N). These properties and their biodegradability suggest that the paper sheets could potentially be used in packaging. Keywords: Biodegradability, lemongrass, optimization, paper sheet making, sugarcane bagasse, tensile strength. 1. INTRODUCTION White pollution or plastic pollution has become a global problem that has many severely negative impacts on humans and the ecosystem. One of the biggest sources of plastic pollution is about 400 million tons of single-use packaging that accounts for 36% of the total plastic production annually (UNEP, 2018). It is urgent to find out alternative sustainable materials to replace plastic in the packaging industry. Renewable agricultural by-product fibers have attracted much attention from researchers worldwide to serve as substitutes for petroleum-based polymers which can be highly contaminated by hazardous substances such as PAH (Rochman et al., 2013), PCB (Pascall et al., 2005) or heavy metals (Alam et al., 2018a; Alam et al., 2018b). There is a lot of agricultural waste containing fiber in Vietnam such as sugarcane bagasse, lemongrass bagasse (by-product of lemongrass after essential oil distillation), rice straw, banana pseudostems and leaves, and Zingiberaceae leaves. Sugarcane bagasse compositions are mainly cellulose (about 60%), hemicellulose (20%), glucose (10%), and some other ingredients. Although sugarcane bagasse is considered the ideal raw material for producing many new products due to its abundant supply and stable price, it needs to be modified to obtain the desired mechanical properties. For example, cellulosic fibers from bagasse were combined with powders to form composite materials; combined with gelatin, starch, and agar for making tableware; or mixed with wood pulp resins and other natural fibers (Loh et al., 2013). The cellulose content in Ngo Thi Thuong, Tran Thi Thuy Dung, Chu Thi Thanh, Nguyen Thi Hong Hanh, Le Thi Thu Huong 965 lemongrass by-products is about 40% (Kaur & Dutt, 2013). When combined with sugarcane bagasse, the difference in cellulose content and polymeric chain lengths of the different fibers may enhance some mechanical properties of the obtained composites (Agustina et al., 2019). It was also published that fibers from agricultural by-products could be used to make paper sheets. In Oman, Khalsa Al- Sulaimani and his research group (Al- Sulaimani et al., 2017) produced handmade paper from bagasse and banana stalk fiber. The research team investigated three composition formulas: formula 1 had only raw materials from bagasse and banana, formula 2 and 3 were fibers mixed with CaCO3 fillers (2% and 5%), respectively, and starch (2%-5%) for adhesion. The research results showed that adding additives increased adhesion and the whiteness of the paper while reducing the paper thickness. Bagasse is more rigid than banana fiber so it is suitable for wrapping paper, while banana fiber is very suitable for making soft paper such as tissue paper. Although these fibers are important resources, there are few environmental-friendly applications of these materials in use now in Vietnam. ... sier to make into paper with a smaller thickness, and greater density, flexural strength, and tensile strength (Cruz et al., 2017). Although, glycerol is water- soluble, in order to select the appropriate glycerol ratio, it was necessary to further consider the water absorption properties of the paper. Water absorption is greatly affected by the structural integrity of the paper. The cause of this phenomenon is that the natural capillaries found in bagasse make the paper quickly reach hydration equilibrium. The results of the water absorption test of this sample series are presented in Figure 2 and Figure 3. When not using glycerol, after only 15s in contact with water, the paper bands absorbed water more than 50% of their weight. After 30 s, they absorbed 100% of the water. At the contact time of 15s, TN3.2 (2ml glycerol added) was the least water absorbent sample. However, after 60s, the water absorbed amounts in TN3.2, TN3.3, and TN3.4 became close to that of each other. These differences were not statistically significant. TN3.1 and TN3.5 showed the highest water absorption. This can be explained by the fact that without glycerol (TN3.1), water was more easily able to go into the cellulose fibers in the biomass, while with too much glycerol (TN3.5), water could be absorbed into the paper sheets through the glycerol dissolution process. These results suggested that 4 ml of glycerol was enough to absorb and connect the fibers in the biomass. However, based on the three properties of tensile strength, flexural modulus (Table 3), and absorption, the TN3.4 condition (6ml glycerol) was chosen to proceed with other experiments. 3.2.2. Effects of the sugarcane bagasse/ lemongrass ratio on the paper properties Table 4 shows the effect of the lemongrass composition on the paper properties. It was obvious that when adding lemongrass, the paper sheets became thinner with a higher density, higher tensile strength, and higher flexural modulus. The differences between the strength of the cellulose fibers (due to the length of the cellulose chains) of the sugarcane bagasse and lemongrass could be the reason for the significant changes in these parameters between TN4.2, TN4.3, or TN4.4 and TN4.1. Figure 4 also demonstrates that the higher the ratio of lemongrass, the less water was absorbed into the paper sheets. These results also suggested that the combination could be an effective approach to controlling the paper properties. In our previous study, the composite samples with lower contents of lemongrass also showed lower tensile strength and flexural modulus (Ngo et al., 2018). For further experiments, the sugarcane bagasse/lemongrass Paper sheets made from sugarcane bagasse and lemongrass by-products: Synthesis and properties 970 ratios of 80/20 and 70/30 were chosen. Another study showed a similar dependence of the composite mechanical properties on their composition (Agustina et al., 2019). Different ratio mixtures of sugarcane bagasse and pineapple leaves were also investigated to prepare paper pulp resulting in papers with varied tensile and tearing strengths (Evelyn et al., 2019). 3.2.3. Effects of the added starch amount on the paper properties All the researched samples were neutral. The thickness and density of the samples in this experiment series did not show much variation. The results in Table 5 reveal that adding starch at the ratios of 4% and 6% for both ratios of biomass (80/20 and 70/30) made the tensile strength and flexural modulus of the samples significantly (P < 0.5) greater than that at the ratio of 2%. This showed that when starch was used, the links between the cellulose fibers increased leading to stronger and more flexural paper. The tensile strength and flexural modulus of the samples at the ratios of 4% and 6% starch were not significantly different at the 5% significance level. There ws a similar trend in the water absorption of the samples (Figure 5). Figure 3. Effect of the added glycerol amount on the water adsorption capacity Figure 4. Effects of the sugarcane bagasse/lemongrass on the water absorption of the paper sheets Ngo Thi Thuong, Tran Thi Thuy Dung, Chu Thi Thanh, Nguyen Thi Hong Hanh, Le Thi Thu Huong 971 Figure 5. Effects of the starch amount on the water absorption of the paper sheets Table 2. Effects of reaction time on the delignification of the biomass Sample Time (h) Delignified biomass weight (g) Paper sheet weight (g) Papermaking yield (%) Thickness (cm) Obtained fibers Obtained paper sheet TN2.1 0.5 29.43 ± 0.32 28.96 ± 0.12 92.1 ± 1.1 1.13 a ± 0.20 Difficult to grind, hard fibers with the size range of 2-2.5cm TN2.2 1 27.18 ± 0.21 27.00 ± 0.25 99.3 ± 1.2 0.94 a ± 0.26 Less difficult to grind, hard fibers with the size range of 1.5-2cm TN2.3 2 24.52 ± 0.17 24.33 ± 0.13 99.2 ± 0.9 0.77 b ± 0.11 Easy to grind, soft and short fibers TN2.4 3 24.03 ± 0.18 23.71 ± 0.10 98.7 ± 0.8 0.73 b ± 0.10 Easy to grind, soft and short fibers Note: Values with the same letter within each coulmn are not significantly different at the 5% level. Therefore, 4% starch was an appropriate amount for the papermaking process. The data showed that if the links between cellulose fibers were too tight, then the tensile and flexural strength would increase very little when more starch was used. The ratio of 4% was the ratio of the flexural strength and the tensile strength of the hearing. Paper sheets made from sugarcane bagasse and lemongrass by-products: Synthesis and properties 972 3.3. Biodegradability properties The biodegradability test results are shown in Figure 6. The optimized sample pieces of TN5.5 were buried in soil at different depths of 5 cm and 10 cm. The initial average weight of the TN5.5 pieces was 0.0562 ± 0.0017. After 15 days, the weights of the TN5.5 pieces at 5 cm and 10 cm-depths were 0.0367 ± 0.0015 and 0.0282 ± 0.0018g, respectively. These 34.7% and 49.8% weight losses indicated the biodegradation of the samples. The SEM images (Figure 6) of the samples also showed a decrease in the thickness of the samples. There was a difference in the biodegradability rate between the 2 depths. This result differs from those published by Mirachelvam et al. (2019). This could be due to the differences in the composition of the samples in the current study and referent research. Table 3. Effects of added glycerol amount on the paper properties Formula Glycerol amount (ml) pH Thickness (mm) density (g cm -3 ) Tensile strength (N mm -2 ) Flexural modulus (N) TN3.1 0 6.4 0.75 a ± 0.05 0.28 ± 0.03 6.30 a ± 0.10 0.61 a ± 0.10 TN3.2 2 6.3 0.48 b ± 0.05 0.35 ± 0.06 8.23 b ± 0.05 0.70 a ± 0.10 TN3.3 4 6.5 0.47 b ± 0.04 0.32 ± 0.06 14.33 c ± 0.11 0.93 b ± 0.05 TN3.4 6 6.5 0.46 b ± 0.04 0.34 ± 0.04 17.70 d ± 0.70 1.10 bc ± 0.10 TN3.5 8 6.4 0.46 b ± 0.08 0.34 ± 0.09 24.00 e ± 0.81 1.23 c ± 0.05 Note: Values with the same letter within each column are not significantly different at the 5% level. Table 4. Effects of the sugarcane bagasse and lemongrass byproduct ratio on the paper properties Formula Sugarcane bagasse/lemongrass by-product ratio pH Thickness (mm) density (g cm -3 ) Tensile strength (N mm -2 ) Flexural modulus (N) TN4.1 100/0 6.3 0.46 ± 0.09 a 0.31 ± 0.09 16.27 a ± 2.04 1.13 a ± 0.06 TN4.2 90/10 6.3 0.29 ± 0.03 b 0.48 ± 0.07 18.07 ab ± 1.72 1.31 b ± 0.10 TN4.3 80/20 6.2 0.30 ± 0.03 b 0.42 ± 0.05 20.43 bc ± 0.81 1.33 b ± 0.06 TN4.4 70/30 6.3 0.33 ± 0.03 b 0.43 ± 0.07 21.46 c ± 0.33 1.43 b ± 0.05 Note: Values with the same letter within each column are not significantly different at the 5% level. Table 5. Effects of the added starch amount on the paper properties Formula Sugarcane bagasse/lemongrass by-product ratio Starch amount (%) pH Thickness (mm) density (g cm -3 ) Tensile strength (N mm -2 ) Flexural modulus (N) TN5.1 80/20 2 6.3 0.32 a ± 0.01 0.43 ± 0.05 11.87 a ± 0.31 0.93 a ± 0.15 TN5.2 80/20 4 6.4 0.30 a ± 0.01 0.50 ± 0.04 18.33 b ± 0.15 1.17 ab ± 0.15 TN5.3 80/20 6 6.4 0.30 a ± 0.02 0.44 ± 0.07 18.80 b ± 0.41 1.31 b ± 0.10 TN5.4 70/30 2 6.3 0.31 a ± 0.01 0.48 ± 0.03 16.30 c ± 0.10 1.32 b ± 0.11 TN5.5 70/30 4 6.4 0.32 a ± 0.01 0.44 ± 0.04 18.90 b ± 0.36 1.63 c ± 0.11 TN5.6 70/30 6 6.3 0.33 a ± 0.02 0.39 ± 0.02 19.60 b ± 0.56 1.77 c ± 0.06 Note: Values with the same letter within each column are not significantly different at the 5% level. Ngo Thi Thuong, Tran Thi Thuy Dung, Chu Thi Thanh, Nguyen Thi Hong Hanh, Le Thi Thu Huong 973 Figure 6. SEM images of the TN5.5 pieces before (a) and after the biodegradability test at 5-cm (b) and 10-cm depth (c) 4. CONCLUSIONS In conclusion, the optimized conditions of the synthesis of paper sheets from sugarcane bagasse and lemongrass by-products have been investigated. To obtain paper sheets with high tensile strength and flexural modulus, and with low thickness and water absorption, the biomass should be treated with 14% NaOH (w/w to biomass) for 2h. The sugarcane bagasse/lemongrass ratio could be 80/20 or 70/30, and should then be mixed with 6ml glycerol and4% starch before making starch. The obtained paper sheets had good physical properties with the thickness of 0.3 mm, small density of 0.4 g cm-3, tensile strength of 19 N mm-2, and flexural modulus of 1.7 N. The paper sheets also exhibited low water absorption and the ability to biodegrade up to 49.8% in the soil layer at a 10 cm depth after 15 days. Based on the obtained results, it would be possible to prepare bio bags or bio containers from the optimized paper sheets. ACKNOWLEDGEMENTS This work was financially supported by Vietnam National University of Agriculture under the Grant No.T2019-04-19. REFERENCES Agustina W., Aditiawati P., Kusumah S.S. & Dungani R. (2019). Physical and mechanical properties of composite boards from the mixture of palm sugar fiber and cassava bagasse using mycelium of Ganoderma lucidum as a biological adhesive. IOP Conference Series: Earth and Environmental Science. 374(1): 1-12 (012012). Al-Sulaimani K., Priy D. & Dwivedi B. (2017). Production of Handmade Papers From Sugar Cane Bagasse and Banana Fibers in Oman. International Journal of Students’ Research In Technology & Management. 5(3): 16-20. Paper sheets made from sugarcane bagasse and lemongrass by-products: Synthesis and properties 974 Alam O., Billah M. & Yajie D. (2018). Characteristics of plastic bags and their potential environmental hazards. Resources, Conservation and Recycling. 132: 121-129. Alam O., Wang S. & Lu W. (2018). Heavy metals dispersion during thermal treatment of plastic bags and its recovery. Journal of Environmental Management. 212: 367-374. Anggraeni N.I., Hidayat I.W., Rachman S.D. & Ersanda (2018). Bioactivity of essential oil from lemongrass (Cymbopogon citratus Stapf) as antioxidant agent. AIP Conference Proceedings. 1927: 1-5 (030007). Cruz T., Delia R. T. B. & Raúl S. (2017). Influence of Proportion and Size of Sugarcane Bagasse Fiber on the Properties of Sweet Potato Starch Foams. IOP Conference Series: Materials Science and Engineering. 225:1-8 (012180). Ekpenyong C.E. & Akpan E.E. (2017). Use of Cymbopogon citratus essential oil in food preservation: Recent advances and future perspectives. Critical Reviews in Food Science and Nutrition. 57(12): 2541-2559. Evelyn Komalasari, Adegustias R.A., Margaretha E. A. & Simanjuntak M.S. (2019). Production and Characterization of Paper from Pineapple Leaves and Sugarcane Bagasse Pulp. Journal of Physics: Conference Series. 1351: 1-6 (012117). Hoang P. (2017). Raising shrimp with bagasse powder. Retrieved from https://thanhnien.vn/tai-chinh-kinh- doanh/nuoi-tom-bang-bot-ba-mia-849324.html (in Vietnamese) on December 30, 2019. Kaur H. & Dutt D. (2013). Anatomical, morphological and chemical characterization of lignocellulosic by-products of lemon and sofia grasses obtained after recuperation of essential oils by steam distillation. Cellulose Chemistry and Technology. 47(1-2): 83-94. Kido H. (2016). Sample Preparation Techniques for Soil, Plant, and Animal Samples. In Sample Preparation Techniques for Soil, Plant, and Animal Samples. Springer protocols handbooks. pp. 117-123. Loh Y.R., Sujan D., Rahman M.E. & Das C.A. (2013). Sugarcane bagasse - The future composite material: A literature review. Resources, Conservation and Recycling. 75: 14-22. Marichelvam M.K., Jawaid M. & Asim M. (2019). Corn and rice starch-based bio-plastics as alternative packaging materials. Fibers. 7(4): 1-14. Mirghani M. E. S., Liyana Y. & Parveen, J. (2012). Bioactivity analysis of lemongrass (Cymbopogan citratus) essential oil. International Food Research Journal. 19(2): 569-575. Ngo T.T., Chu T.T., Nguyen N.K., Phung T.V. & Le T. T.H. (2018). Synthesis and characteristic of composites made of lemongrass byproduct and sugarcane bagasse. Journal of Agriculture and Rural Development. 12: 89-94. Pascall M.A., Zabik M.E., Zabik M.J. & Hernandez R.J. (2005). Uptake of polychlorinated biphenyls (PCBs) from an aqueous medium by polyethylene, polyvinyl chloride, and polystyrene films. Journal of Agricultural and Food Chemistry. 53(1): 164-169. Pham H. (2017). Technology of collecting lemongrass essential oil in Vietnam for the first time by 65- year-old scientist. Retrieved from https://vnexpress.net/tin-tuc/khoa-hoc/trong-nuoc/ cong-nghe-thu-tinh-dau-sa-lan-dau-o-viet-nam-cua -nha-khoa-hoc-65-tuoi-3586834-p2.html (in Vietnamese) on December 30, 2019. Rochman C.M., Manzano C., Hentschel B.T., Simonich S.L.M. & Hoh E. (2013). Polystyrene plastic: A source and sink for polycyclic aromatic hydrocarbons in the marine environment. Environmental Science and Technology. 47(24): 13976-13984. Terumi I. A., Batista T. J. & Freitas Schwan-Estrada K. R. (2013). Cymbopogon citratus essential oil bioactivity and the induction of enzymes related to the pathogenesis of Alternaria solani on tomato plants. Idesia (Arica). 31(4): 11-17. UNEP (2018). Single-use plastics: a roadmap to sustainability. International Journal of Social Science and Economic Research. Zhu J., Xiong J., Hu X. & Wang B. (2019). Mechanical Properties and Wettability of Bagasse-reinforced Composite. Journal Wuhan University of Technology, Materials Science Edition. 34(2): 312-316.
File đính kèm:
paper_sheets_made_from_sugarcane_bagasse_and_lemongrass_by_p.pdf