Influence of loop length on microcapsule distribution in cotton interlock knitted fabric
Functional textile using microcapsules has been taken lots of interest all over the world. Along with
microcapsules, the textile substrate contributes important part to the performance of end use products. This
study was to investigate the effect of loop length on the microcapsule distribution in cotton interlock knitted
fabric. Four levels of loop length studied were 2.83, 2.87, 2.96 and 3.05mm. Microcapsules were applied to
fabrics by coating technique. The microcapsule distribution in the treated fabric was expressed by the
average area of microcapsule aggregates on the fabric surface, which was determined by Meander 3.1.2
software of Peacock Media on the SEM images. The results showed an increase of microcapsule aggregate
area in the order of 7537, 8600, 13379 and 16020 µm2 for the loop length of 2.83, 2.87, 2.96 and 3.05 mm,
respectively. This revealed the less even distribution of microcapsules at the higher loop length. The
principle of coating technique, as well as the higher porosity of the fabric at higher loop length, were thought
to account for this trend.
Keywords: loop length, knitted loop model, microcapsule, functional textile.
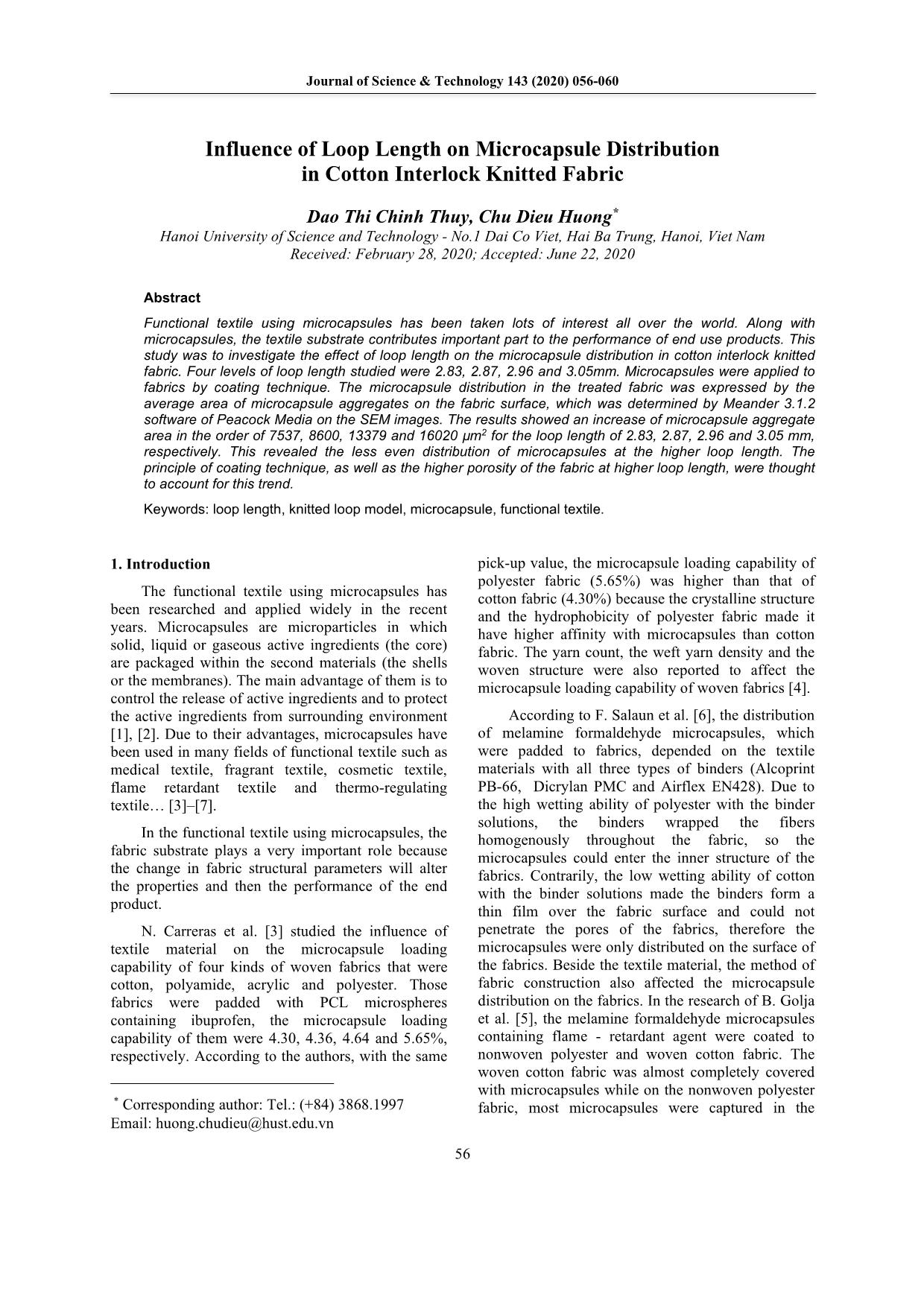
Trang 1
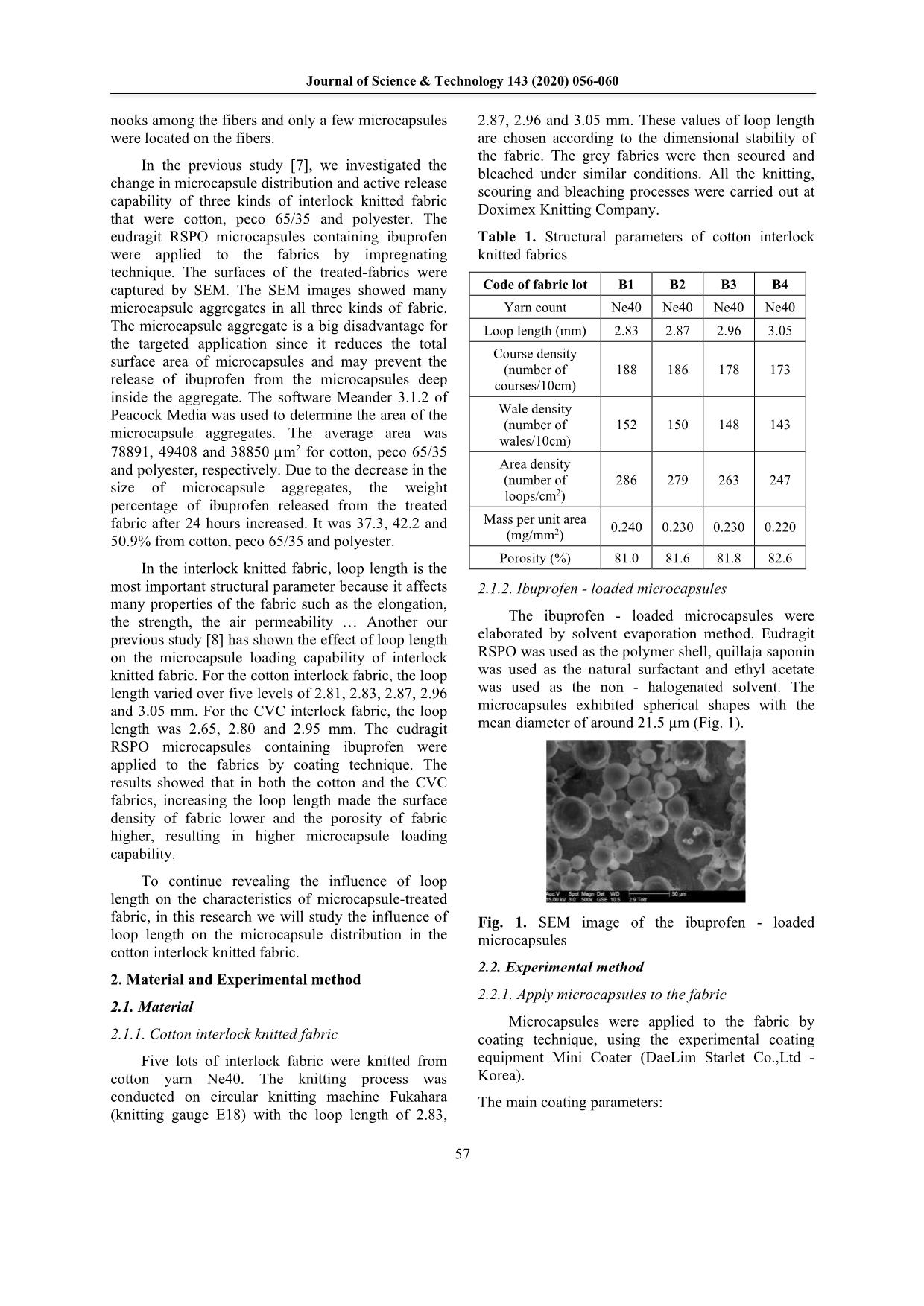
Trang 2
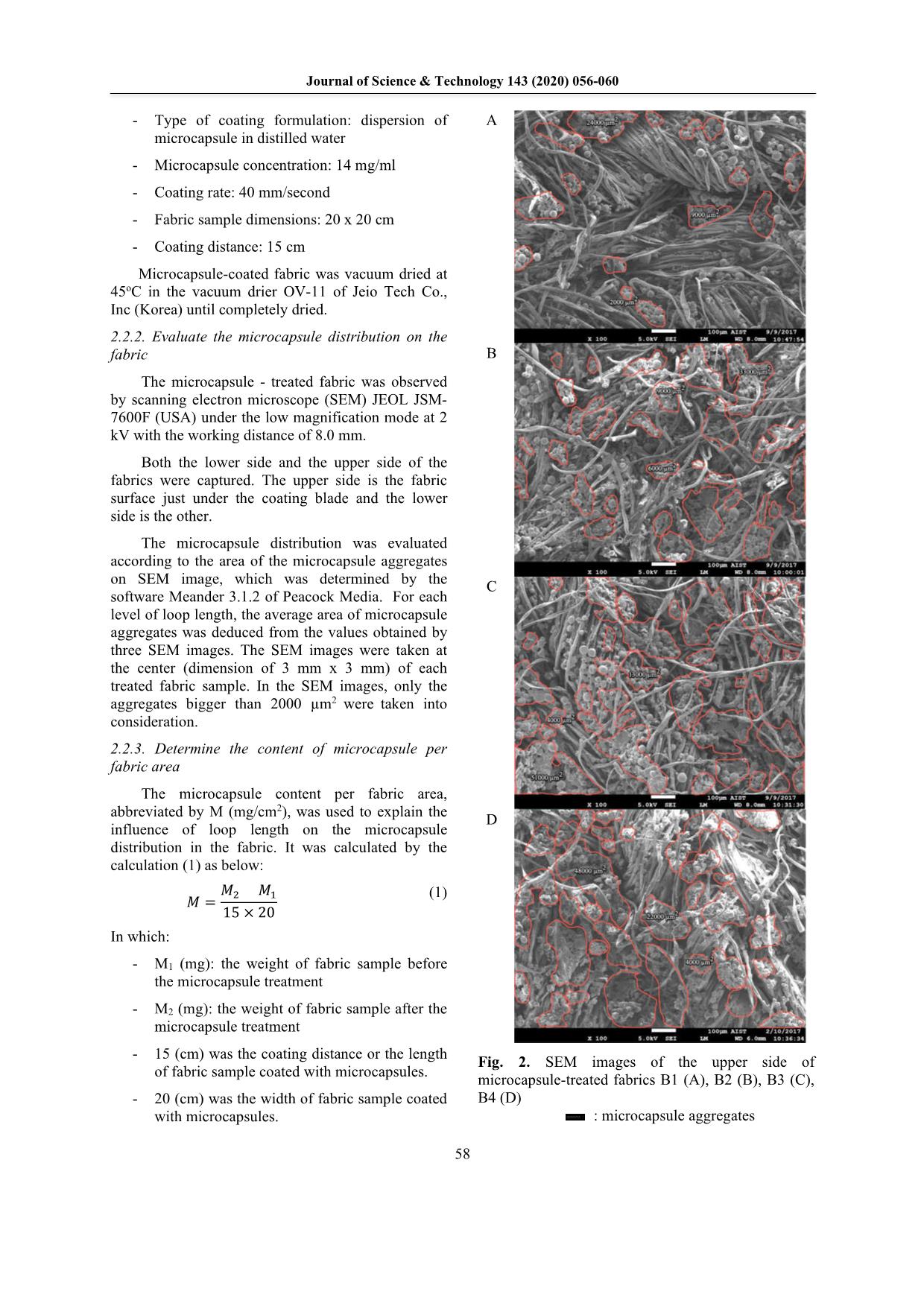
Trang 3
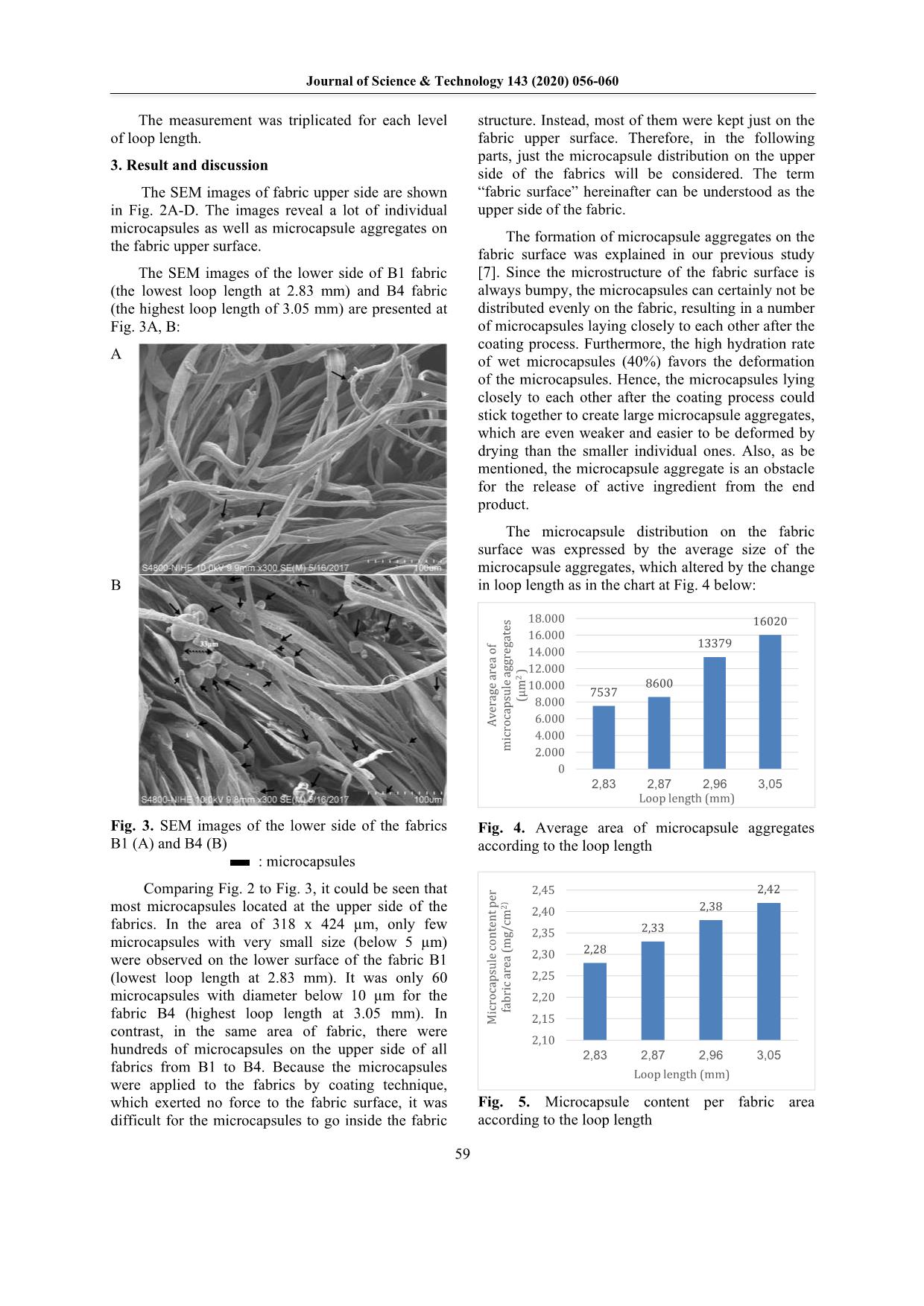
Trang 4
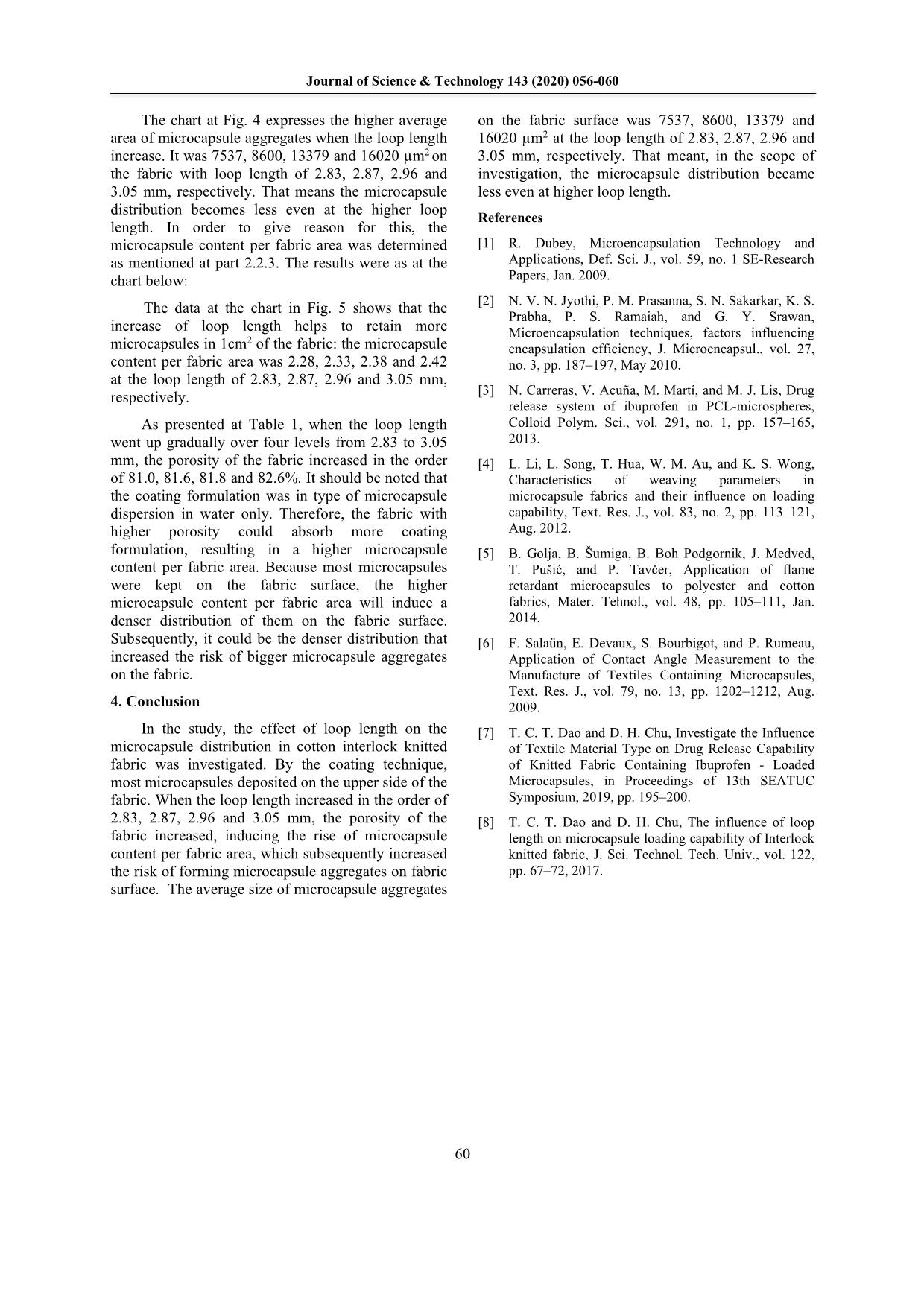
Trang 5
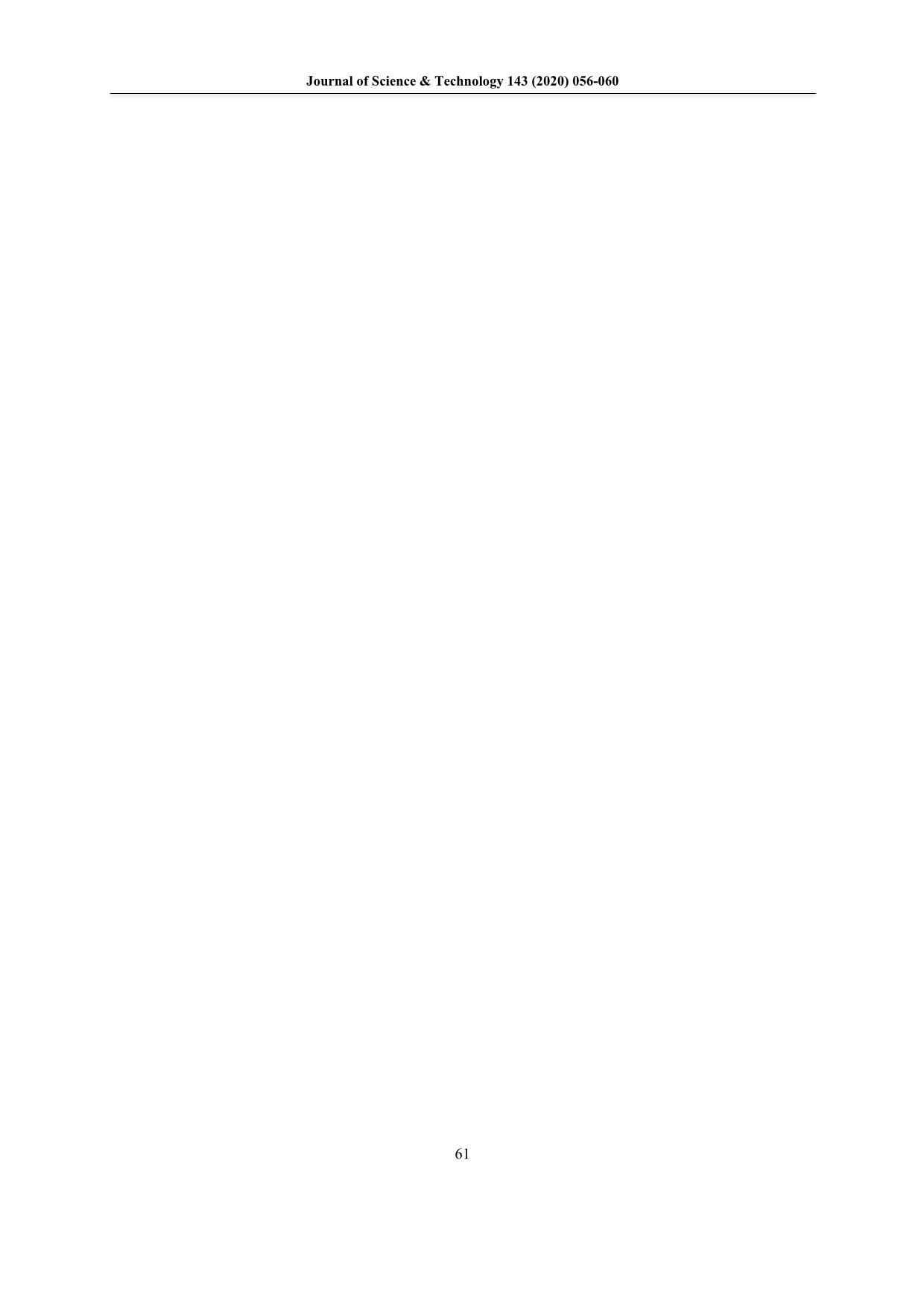
Trang 6
Tóm tắt nội dung tài liệu: Influence of loop length on microcapsule distribution in cotton interlock knitted fabric
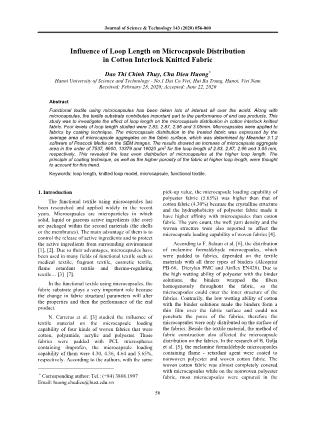
Journal of Science & Technology 143 (2020) 056-060 56 Influence of Loop Length on Microcapsule Distribution in Cotton Interlock Knitted Fabric Dao Thi Chinh Thuy, Chu Dieu Huong* Hanoi University of Science and Technology - No.1 Dai Co Viet, Hai Ba Trung, Hanoi, Viet Nam Received: February 28, 2020; Accepted: June 22, 2020 Abstract Functional textile using microcapsules has been taken lots of interest all over the world. Along with microcapsules, the textile substrate contributes important part to the performance of end use products. This study was to investigate the effect of loop length on the microcapsule distribution in cotton interlock knitted fabric. Four levels of loop length studied were 2.83, 2.87, 2.96 and 3.05mm. Microcapsules were applied to fabrics by coating technique. The microcapsule distribution in the treated fabric was expressed by the average area of microcapsule aggregates on the fabric surface, which was determined by Meander 3.1.2 software of Peacock Media on the SEM images. The results showed an increase of microcapsule aggregate area in the order of 7537, 8600, 13379 and 16020 µm2 for the loop length of 2.83, 2.87, 2.96 and 3.05 mm, respectively. This revealed the less even distribution of microcapsules at the higher loop length. The principle of coating technique, as well as the higher porosity of the fabric at higher loop length, were thought to account for this trend. Keywords: loop length, knitted loop model, microcapsule, functional textile. 1. Introduction The functional textile using microcapsules has been researched and applied widely in the recent years. Microcapsules are microparticles in which solid, liquid or gaseous active ingredients (the core) are packaged within the second materials (the shells or the membranes). The main advantage of them is to control the release of active ingredients and to protect the active ingredients from surrounding environment [1], [2]. Due to their advantages, microcapsules have been used in many fields of functional textile such as medical textile, fragrant textile, cosmetic textile, flame retardant textile and thermo-regulating textile [3]–[7]. In the functional textile using microcapsules, the fabric substrate plays a very important role because the change in fabric structural parameters will alter the properties and then the performance of the end product. N. Carreras et al. [3] studied the influence of textile material on the microcapsule loading capability of four kinds of woven fabrics that were cotton, polyamide, acrylic and polyester. Those fabrics were padded with PCL microspheres containing ibuprofen, the microcapsule loading capability of them were 4.30, 4.36, 4.64 and 5.65%, respectively. According to the authors, with the same * Corresponding author: Tel.: (+84) 3868.1997 Email: huong.chudieu@hust.edu.vn pick-up value, the microcapsule loading capability of polyester fabric (5.65%) was higher than that of cotton fabric (4.30%) because the crystalline structure and the hydrophobicity of polyester fabric made it have higher affinity with microcapsules than cotton fabric. The yarn count, the weft yarn density and the woven structure were also reported to affect the microcapsule loading capability of woven fabrics [4]. According to F. Salaun et al. [6], the distribution of melamine formaldehyde microcapsules, which were padded to fabrics, depended on the textile materials with all three types of binders (Alcoprint PB-66, Dicrylan PMC and Airflex EN428). Due to the high wetting ability of polyester with the binder solutions, the binders wrapped the fibers homogenously throughout the fabric, so the microcapsules could enter the inner structure of the fabrics. Contrarily, the low wetting ability of cotton with the binder solutions made the binders form a thin film over the fabric surface and could not penetrate the pores of the fabrics, therefore the microcapsules were only distributed on the surface of the fabrics. Beside the textile material, the method of fabric construction also affected the microcapsule distribution on the fabrics. In the research of B. Golja et al. [5], the melamine formaldehyde microcapsules containing flame - retardant agent were coated to nonwoven polyester and woven cotton fabric. The woven cotton fabric was almost completely covered with microcapsules while on the nonwoven polyester fabric, most microcapsules were captured in the Journal of Science & Technology 143 (2020) 056-060 57 nooks among the fibers and only a few microcapsules were located on the fibers. In the previous study [7], we investigated the change in microcapsule distribution and active release capability of three kinds of interlock knitted fabric that were cotton, peco 65/35 and polyester. The eudragit RSPO microcapsules containing ibuprofen were applied to the fabrics by impregnating technique. The surfaces of the treated-fabrics were captured by SEM. The SEM images showed many microcapsule aggregates in all three kinds of fabric. The microcapsule aggregate is a big disadvantage for the targeted application since it reduces the total surface area of microcapsules and may prevent the release of ibuprofen from the microcapsules deep inside the aggregate. The software Meander 3.1.2 of Peacock Media was used to determine the area of the microcapsule aggregates. The average area was 78891, 49408 and 38850 m2 for cotton, peco 65/35 and polyester, respectively. Due to the decrease in the size of microcapsule aggregates, the weight percentage of ibuprofen released from the treated fabric after 24 hours increased. It was 37.3, 42.2 and 50.9% from cotton, peco 65/35 and polyester. In the interlock knitted fabric, loop length is the most important structural parameter because it affects many properties of the fabric such as the elongation, the strength, the air permeability Another our previous study [8] has shown the effect of loop length on the microcapsule loading capability of interlock knitted fabric. For the cotton interlock fabric, the loop length varied over five levels of 2.81, 2.83, 2.87, 2.96 and 3.05 mm. For the CVC interlock fabric, the loop length was 2.65, 2.80 and 2.95 mm. The eudragit RSPO microcapsules containing ibuprofen were applied to the fabrics by coating technique. The results showed that in both the cotton and the CVC fabrics, increasing the loop length made the surface density of fabric lower and the porosity of fabric higher, resulting in higher microcapsule loading capability. To continue revealing the influence of loop length on the characteristics of microcapsule-treated fabric, in this research we will study the influence of loop length on the microcapsule distribution in the cotton interlock knitted fabric. 2. Material and Experimental method 2.1. Material 2.1.1. Cotton interlock knitted fabric Five lots of interlock fabric were knitted from cotton yarn Ne40. The knitting process was conducted on circular knitting machine Fukahara (knitting gauge E18) with the loop length of 2.83, 2.87, 2.96 and 3.05 mm. These values of loop length are chosen according to the dimensional stability of the fabric. The grey fabrics were then scoured and bleached under similar conditions. All the knitting, scouring and bleaching processes were carried out at Doximex Knitting Company. Table 1. Structural parameters of cotton interlock knitted fabrics Code of fabric lot B1 B2 B3 B4 Yarn count Ne40 Ne40 Ne40 Ne40 Loop length (mm) 2.83 2.87 2.96 3.05 Course density (number of courses/10cm) 188 186 178 173 Wale density (number of wales/10cm) 152 150 148 143 Area density (number of loops/cm2) 286 279 263 247 Mass per unit area (mg/mm2) 0.240 0.230 0.230 0.220 Porosity (%) 81.0 81.6 81.8 82.6 2.1.2. Ibuprofen - loaded microcapsules The ibuprofen - loaded microcapsules were elaborated by solvent evaporation method. Eudragit RSPO was used as the polymer shell, quillaja saponin was used as the natural surfactant and ethyl acetate was used as the non - halogenated solvent. The microcapsules exhibited spherical shapes with the mean diameter of around 21.5 µm (Fig. 1). Fig. 1. SEM image of the ibuprofen - loaded microcapsules 2.2. Experimental method 2.2.1. Apply microcapsules to the fabric Microcapsules were applied to the fabric by coating technique, using the experimental coating equipment Mini Coater (DaeLim Starlet Co.,Ltd - Korea). The main coating parameters: Journal of Science & Technology 143 (2020) 056-060 58 - Type of coating formulation: dispersion of microcapsule in distilled water - Microcapsule concentration: 14 mg/ml - Coating rate: 40 mm/second - Fabric sample dimensions: 20 x 20 cm - Coating distance: 15 cm Microcapsule-coated fabric was vacuum dried at 45oC in the vacuum drier OV-11 of Jeio Tech Co., Inc (Korea) until completely dried. 2.2.2. Evaluate the microcapsule distribution on the fabric The microcapsule - treated fabric was observed by scanning electron microscope (SEM) JEOL JSM- 7600F (USA) under the low magnification mode at 2 kV with the working distance of 8.0 mm. Both the lower side and the upper side of the fabrics were captured. The upper side is the fabric surface just under the coating blade and the lower side is the other. The microcapsule distribution was evaluated according to the area of the microcapsule aggregates on SEM image, which was determined by the software Meander 3.1.2 of Peacock Media. For each level of loop length, the average area of microcapsule aggregates was deduced from the values obtained by three SEM images. The SEM images were taken at the center (dimension of 3 mm x 3 mm) of each treated fabric sample. In the SEM images, only the aggregates bigger than 2000 µm2 were taken into consideration. 2.2.3. Determine the content of microcapsule per fabric area The microcapsule content per fabric area, abbreviated by M (mg/cm2), was used to explain the influence of loop length on the microcapsule distribution in the fabric. It was calculated by the calculation (1) as below: = 15 × 20 (1) In which: - M1 (mg): the weight of fabric sample before the microcapsule treatment - M2 (mg): the weight of fabric sample after the microcapsule treatment - 15 (cm) was the coating distance or the length of fabric sample coated with microcapsules. - 20 (cm) was the width of fabric sample coated with microcapsules. A B C D Fig. 2. SEM images of the upper side of microcapsule-treated fabrics B1 (A), B2 (B), B3 (C), B4 (D) : microcapsule aggregates Journal of Science & Technology 143 (2020) 056-060 59 The measurement was triplicated for each level of loop length. 3. Result and discussion The SEM images of fabric upper side are shown in Fig. 2A-D. The images reveal a lot of individual microcapsules as well as microcapsule aggregates on the fabric upper surface. The SEM images of the lower side of B1 fabric (the lowest loop length at 2.83 mm) and B4 fabric (the highest loop length of 3.05 mm) are presented at Fig. 3A, B: A B Fig. 3. SEM images of the lower side of the fabrics B1 (A) and B4 (B) : microcapsules Comparing Fig. 2 to Fig. 3, it could be seen that most microcapsules located at the upper side of the fabrics. In the area of 318 x 424 µm, only few microcapsules with very small size (below 5 µm) were observed on the lower surface of the fabric B1 (lowest loop length at 2.83 mm). It was only 60 microcapsules with diameter below 10 µm for the fabric B4 (highest loop length at 3.05 mm). In contrast, in the same area of fabric, there were hundreds of microcapsules on the upper side of all fabrics from B1 to B4. Because the microcapsules were applied to the fabrics by coating technique, which exerted no force to the fabric surface, it was difficult for the microcapsules to go inside the fabric structure. Instead, most of them were kept just on the fabric upper surface. Therefore, in the following parts, just the microcapsule distribution on the upper side of the fabrics will be considered. The term “fabric surface” hereinafter can be understood as the upper side of the fabric. The formation of microcapsule aggregates on the fabric surface was explained in our previous study [7]. Since the microstructure of the fabric surface is always bumpy, the microcapsules can certainly not be distributed evenly on the fabric, resulting in a number of microcapsules laying closely to each other after the coating process. Furthermore, the high hydration rate of wet microcapsules (40%) favors the deformation of the microcapsules. Hence, the microcapsules lying closely to each other after the coating process could stick together to create large microcapsule aggregates, which are even weaker and easier to be deformed by drying than the smaller individual ones. Also, as be mentioned, the microcapsule aggregate is an obstacle for the release of active ingredient from the end product. The microcapsule distribution on the fabric surface was expressed by the average size of the microcapsule aggregates, which altered by the change in loop length as in the chart at Fig. 4 below: Fig. 4. Average area of microcapsule aggregates according to the loop length Fig. 5. Microcapsule content per fabric area according to the loop length 7537 8600 13379 16020 0 2.000 4.000 6.000 8.000 10.000 12.000 14.000 16.000 18.000 2,83 2,87 2,96 3,05 A v er ag e ar ea o f m ic ro ca p su le a gg re ga te s (µ m 2 ) Loop length (mm) 2,28 2,33 2,38 2,42 2,10 2,15 2,20 2,25 2,30 2,35 2,40 2,45 2,83 2,87 2,96 3,05 M ic ro ca p su le c o n te n t p er fa b ri c ar ea ( m g/ cm 2 ) Loop length (mm) Journal of Science & Technology 143 (2020) 056-060 60 The chart at Fig. 4 expresses the higher average area of microcapsule aggregates when the loop length increase. It was 7537, 8600, 13379 and 16020 µm2 on the fabric with loop length of 2.83, 2.87, 2.96 and 3.05 mm, respectively. That means the microcapsule distribution becomes less even at the higher loop length. In order to give reason for this, the microcapsule content per fabric area was determined as mentioned at part 2.2.3. The results were as at the chart below: The data at the chart in Fig. 5 shows that the increase of loop length helps to retain more microcapsules in 1cm2 of the fabric: the microcapsule content per fabric area was 2.28, 2.33, 2.38 and 2.42 at the loop length of 2.83, 2.87, 2.96 and 3.05 mm, respectively. As presented at Table 1, when the loop length went up gradually over four levels from 2.83 to 3.05 mm, the porosity of the fabric increased in the order of 81.0, 81.6, 81.8 and 82.6%. It should be noted that the coating formulation was in type of microcapsule dispersion in water only. Therefore, the fabric with higher porosity could absorb more coating formulation, resulting in a higher microcapsule content per fabric area. Because most microcapsules were kept on the fabric surface, the higher microcapsule content per fabric area will induce a denser distribution of them on the fabric surface. Subsequently, it could be the denser distribution that increased the risk of bigger microcapsule aggregates on the fabric. 4. Conclusion In the study, the effect of loop length on the microcapsule distribution in cotton interlock knitted fabric was investigated. By the coating technique, most microcapsules deposited on the upper side of the fabric. When the loop length increased in the order of 2.83, 2.87, 2.96 and 3.05 mm, the porosity of the fabric increased, inducing the rise of microcapsule content per fabric area, which subsequently increased the risk of forming microcapsule aggregates on fabric surface. The average size of microcapsule aggregates on the fabric surface was 7537, 8600, 13379 and 16020 µm2 at the loop length of 2.83, 2.87, 2.96 and 3.05 mm, respectively. That meant, in the scope of investigation, the microcapsule distribution became less even at higher loop length. References [1] R. Dubey, Microencapsulation Technology and Applications, Def. Sci. J., vol. 59, no. 1 SE-Research Papers, Jan. 2009. [2] N. V. N. Jyothi, P. M. Prasanna, S. N. Sakarkar, K. S. Prabha, P. S. Ramaiah, and G. Y. Srawan, Microencapsulation techniques, factors influencing encapsulation efficiency, J. Microencapsul., vol. 27, no. 3, pp. 187–197, May 2010. [3] N. Carreras, V. Acuña, M. Martí, and M. J. Lis, Drug release system of ibuprofen in PCL-microspheres, Colloid Polym. Sci., vol. 291, no. 1, pp. 157–165, 2013. [4] L. Li, L. Song, T. Hua, W. M. Au, and K. S. Wong, Characteristics of weaving parameters in microcapsule fabrics and their influence on loading capability, Text. Res. J., vol. 83, no. 2, pp. 113–121, Aug. 2012. [5] B. Golja, B. Šumiga, B. Boh Podgornik, J. Medved, T. Pušić, and P. Tavčer, Application of flame retardant microcapsules to polyester and cotton fabrics, Mater. Tehnol., vol. 48, pp. 105–111, Jan. 2014. [6] F. Salaün, E. Devaux, S. Bourbigot, and P. Rumeau, Application of Contact Angle Measurement to the Manufacture of Textiles Containing Microcapsules, Text. Res. J., vol. 79, no. 13, pp. 1202–1212, Aug. 2009. [7] T. C. T. Dao and D. H. Chu, Investigate the Influence of Textile Material Type on Drug Release Capability of Knitted Fabric Containing Ibuprofen - Loaded Microcapsules, in Proceedings of 13th SEATUC Symposium, 2019, pp. 195–200. [8] T. C. T. Dao and D. H. Chu, The influence of loop length on microcapsule loading capability of Interlock knitted fabric, J. Sci. Technol. Tech. Univ., vol. 122, pp. 67–72, 2017. Journal of Science & Technology 143 (2020) 056-060 61
File đính kèm:
influence_of_loop_length_on_microcapsule_distribution_in_cot.pdf