Environmentally friendly unburnt bricks using raw rice husk and bottom ash as fine aggregates: Physical and mechanical properties
In order to reduce the serious impacts of industrial and agricultural wastes on the environment, raw rice husk
and bottom ash were used as fine aggregates, while fly ash was utilized as a binder material in the production of unburnt building bricks. Two group mixtures were designed with water-to-binder (W/B) ratios of 0.30
and 0.35. The rice husk was used to replace 0%, 3%, 6%, and 9% of bottom ash content by mass. An experimental program was carried out on the brick samples at different ages from 3-day to 28-day to determine the
main physical and mechanical properties of brick, such as unit weight, compressive strength, water absorption,
ultrasonic pulse velocity and thermal conductivity. The microstructure of brick material was captured using
scanning electron microscope technique. The experimental results allow to identify the effects of rice husk,
bottom ash content as well as W/B ratio on the properties of bricks. Brick samples produced in this study had a
proper compressive strength meeting the practice requirement and were classified as Grade M3.5 and 5.0 based
on TCVN 6477:2016. At the use of 9% rice husk, the unit weight and thermal conductivity of bricks were really
low (1.06÷1.08 T/m3 and 0.201÷0.216 W/m.K), they are conformed to be used in temporary construction and
insulation structures.
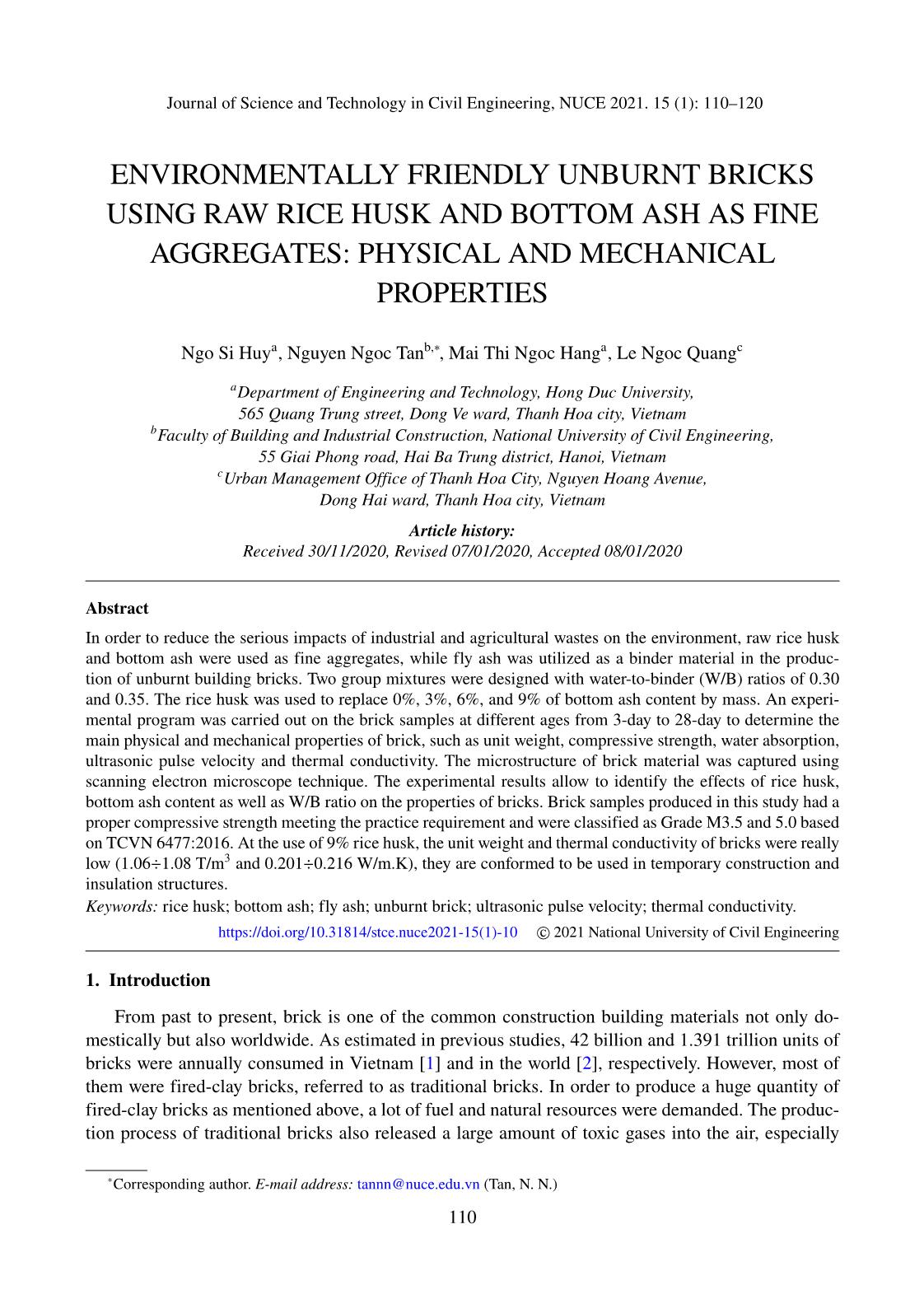
Trang 1
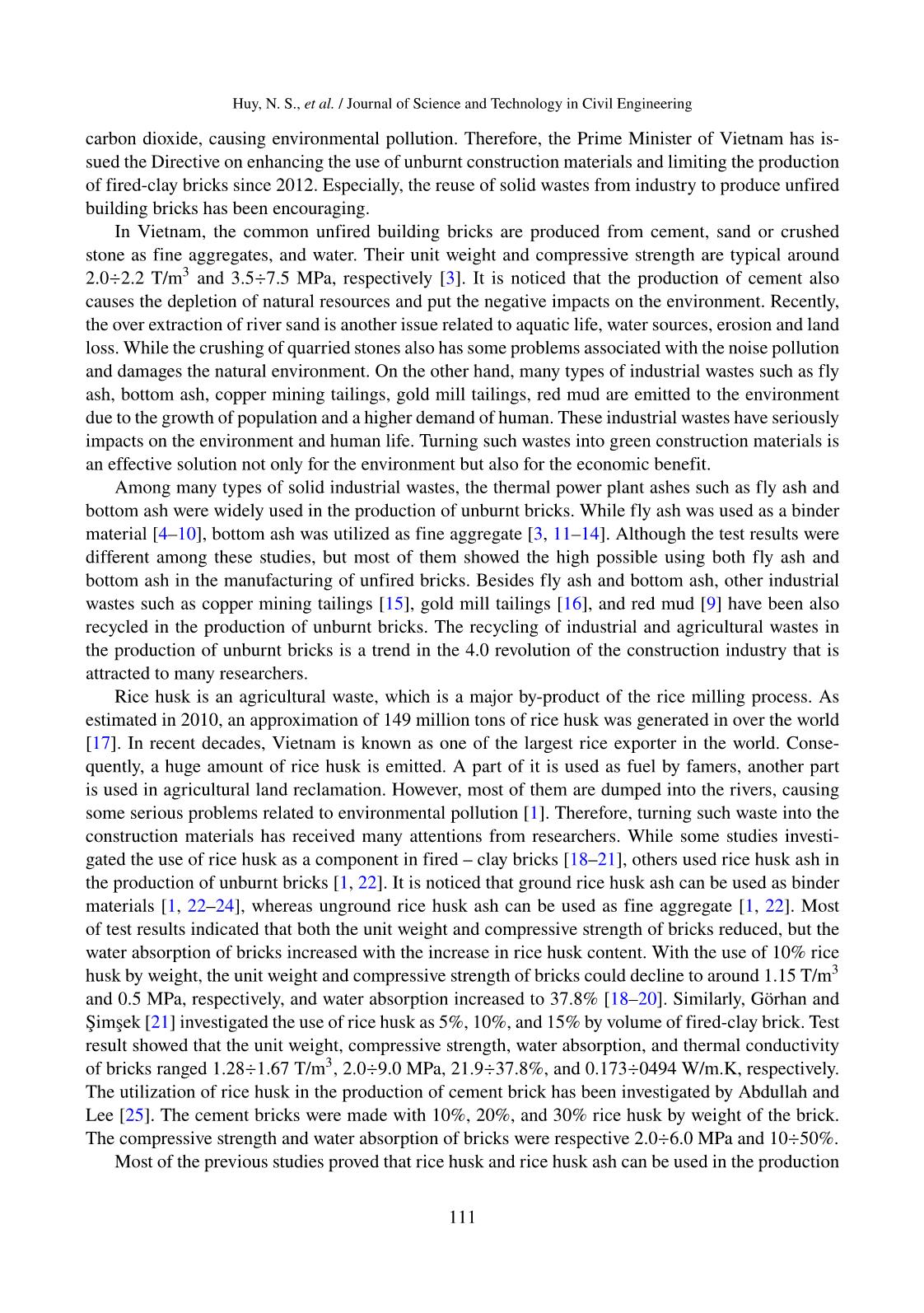
Trang 2
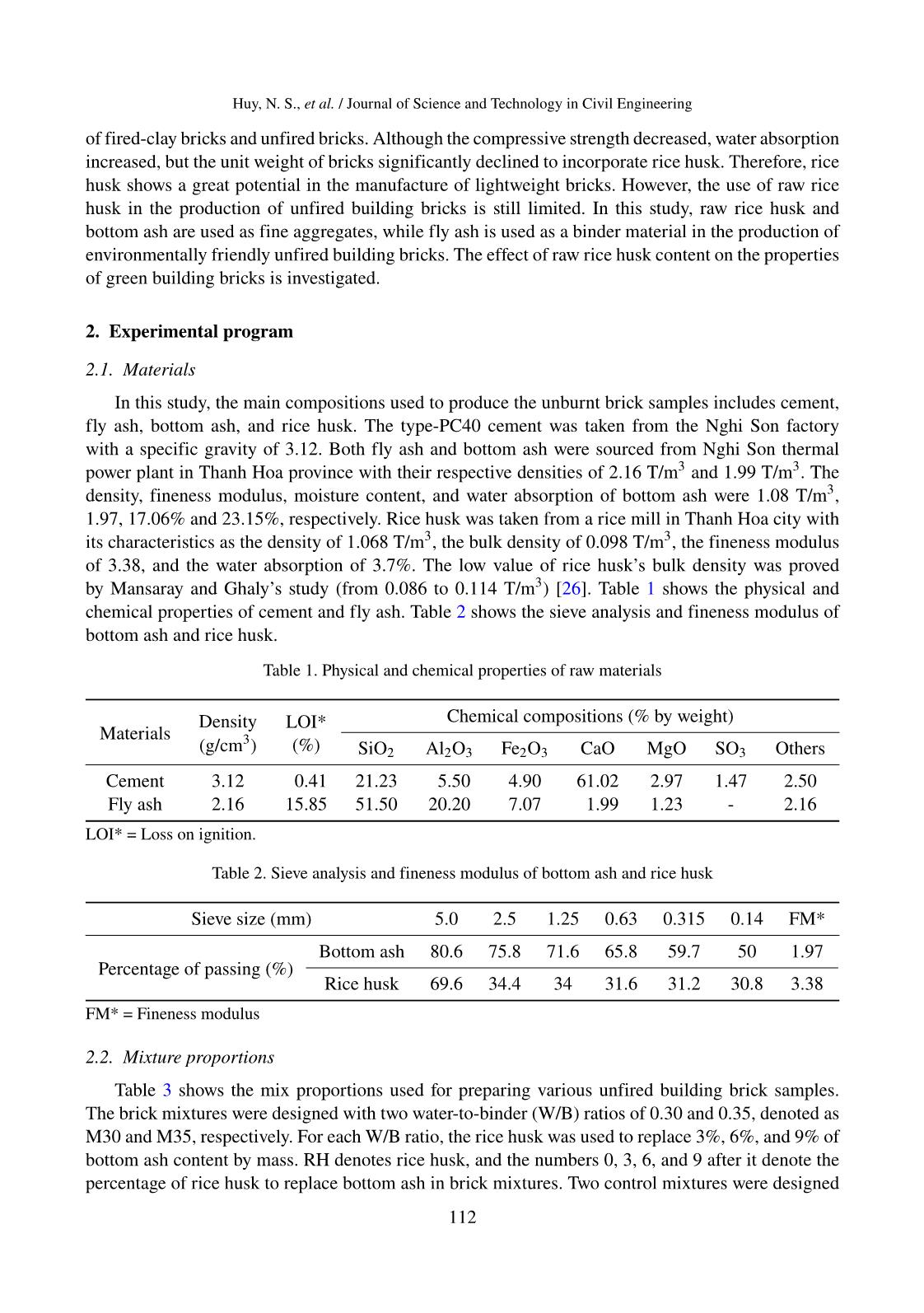
Trang 3
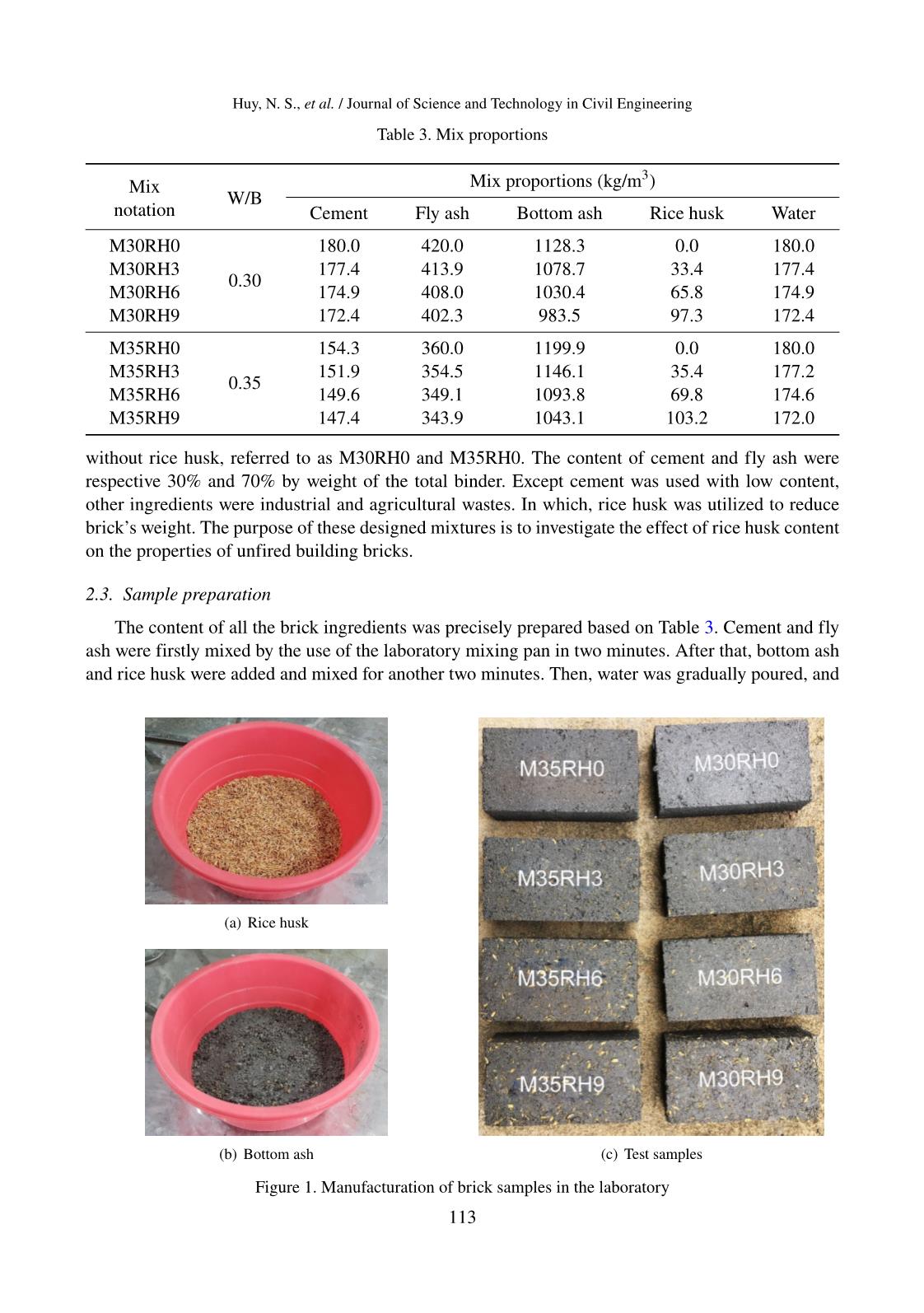
Trang 4
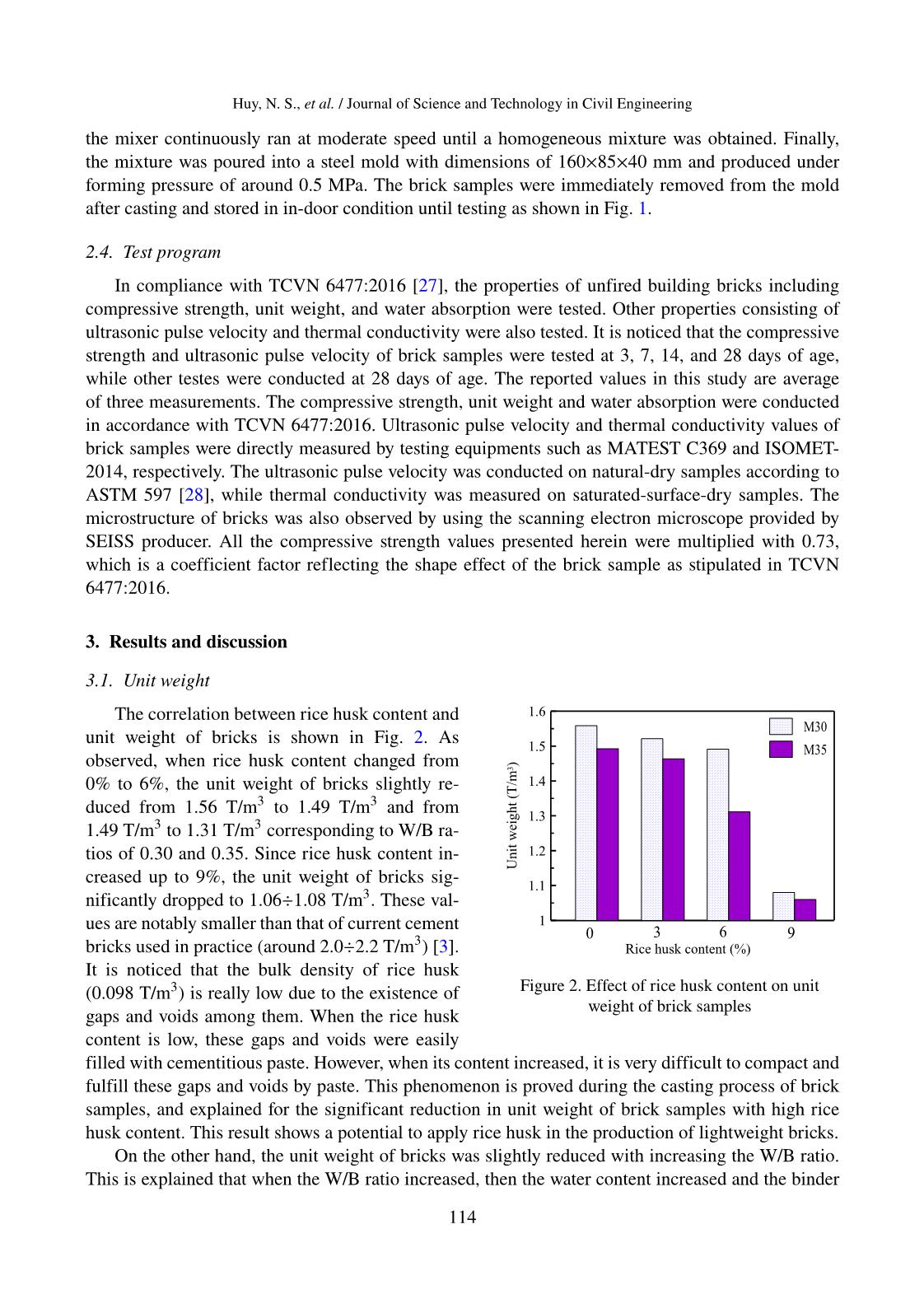
Trang 5
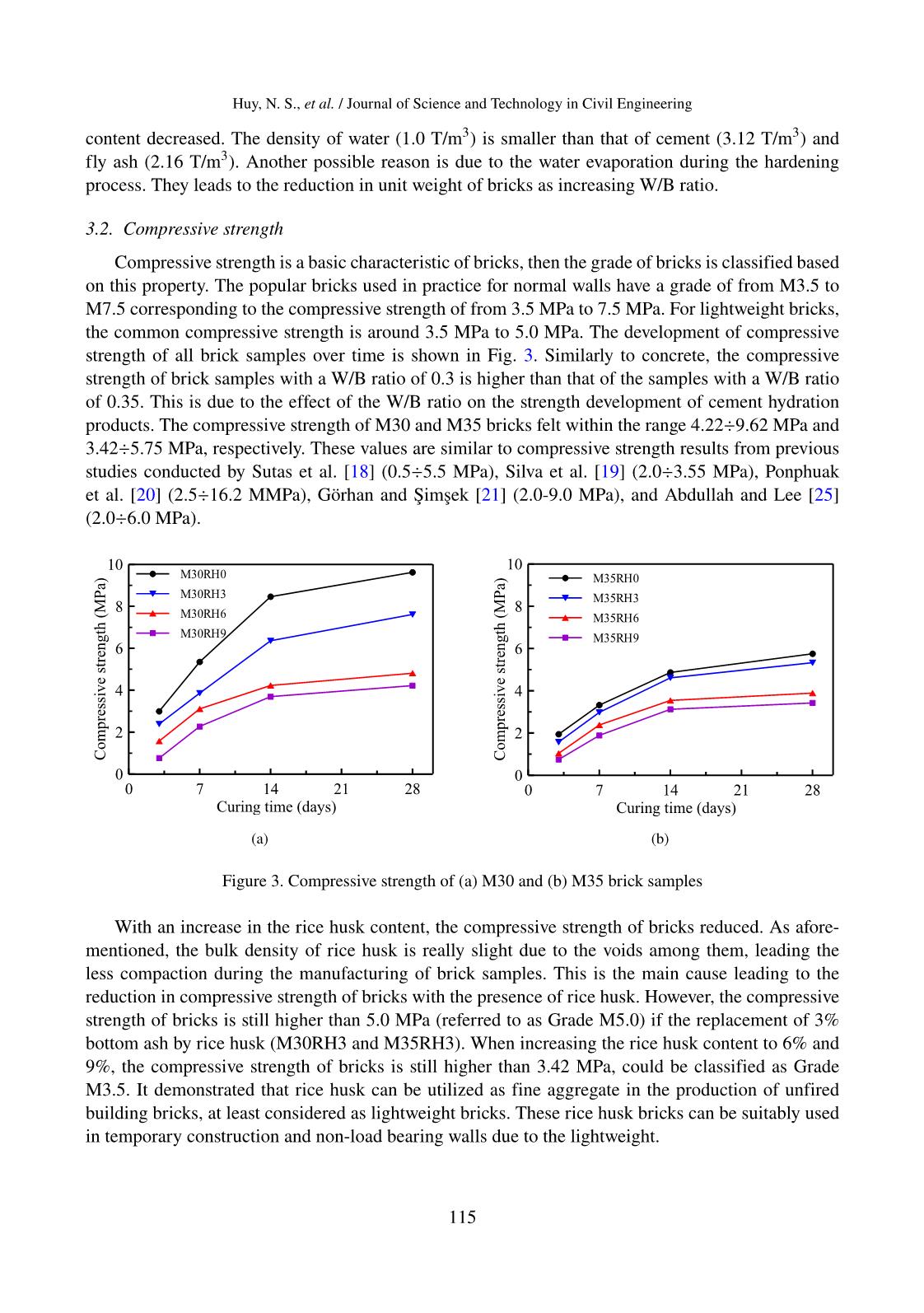
Trang 6
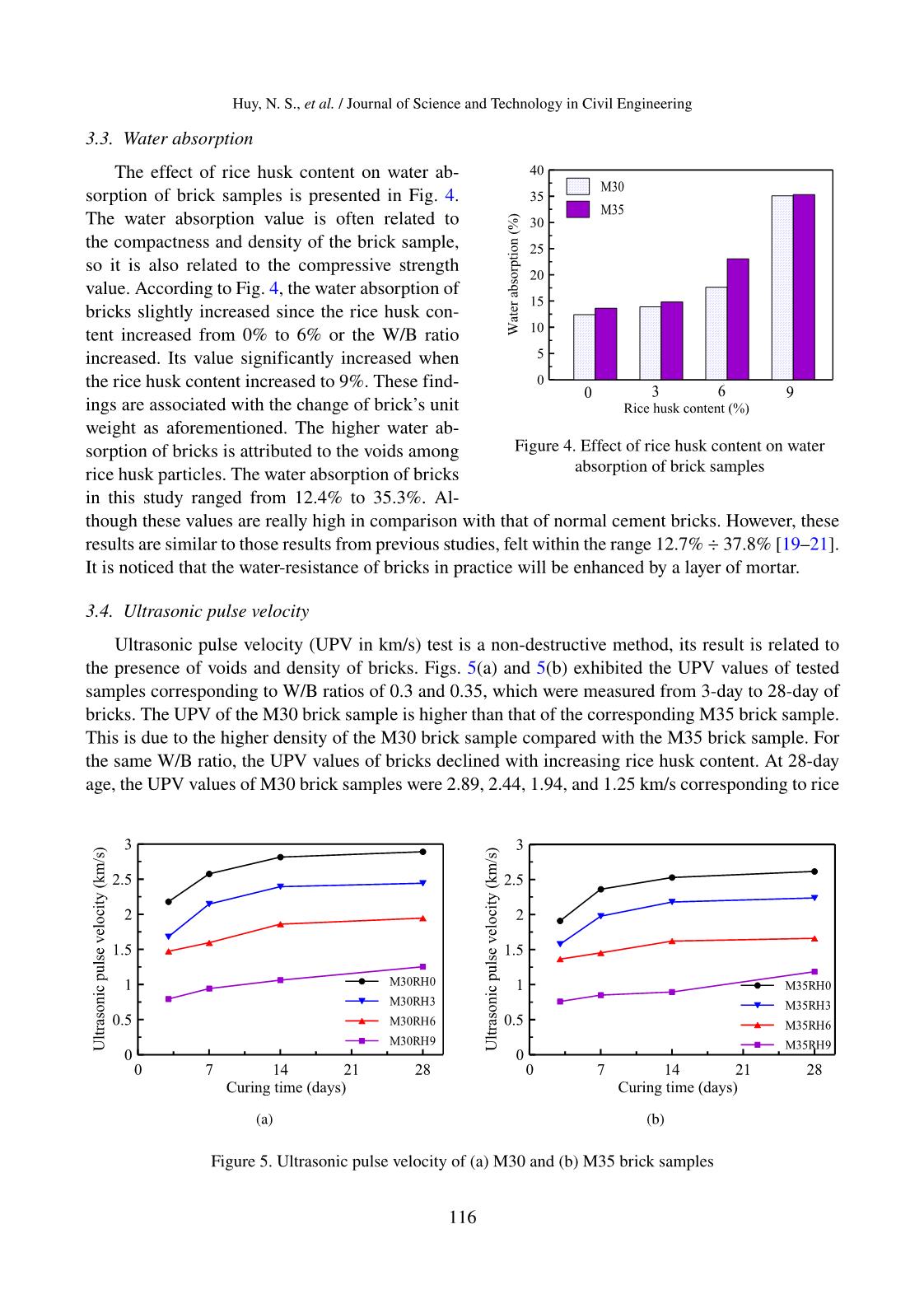
Trang 7
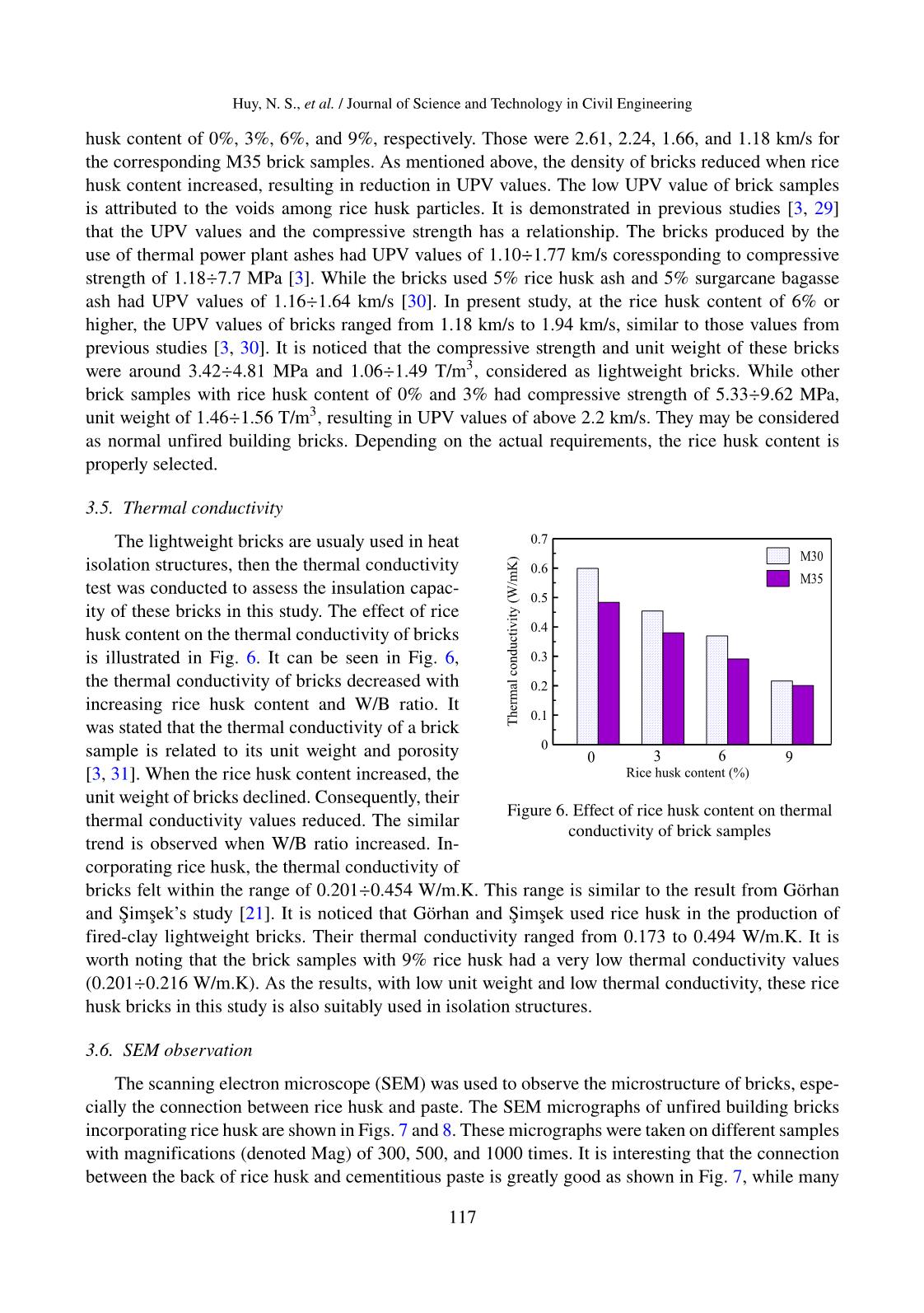
Trang 8
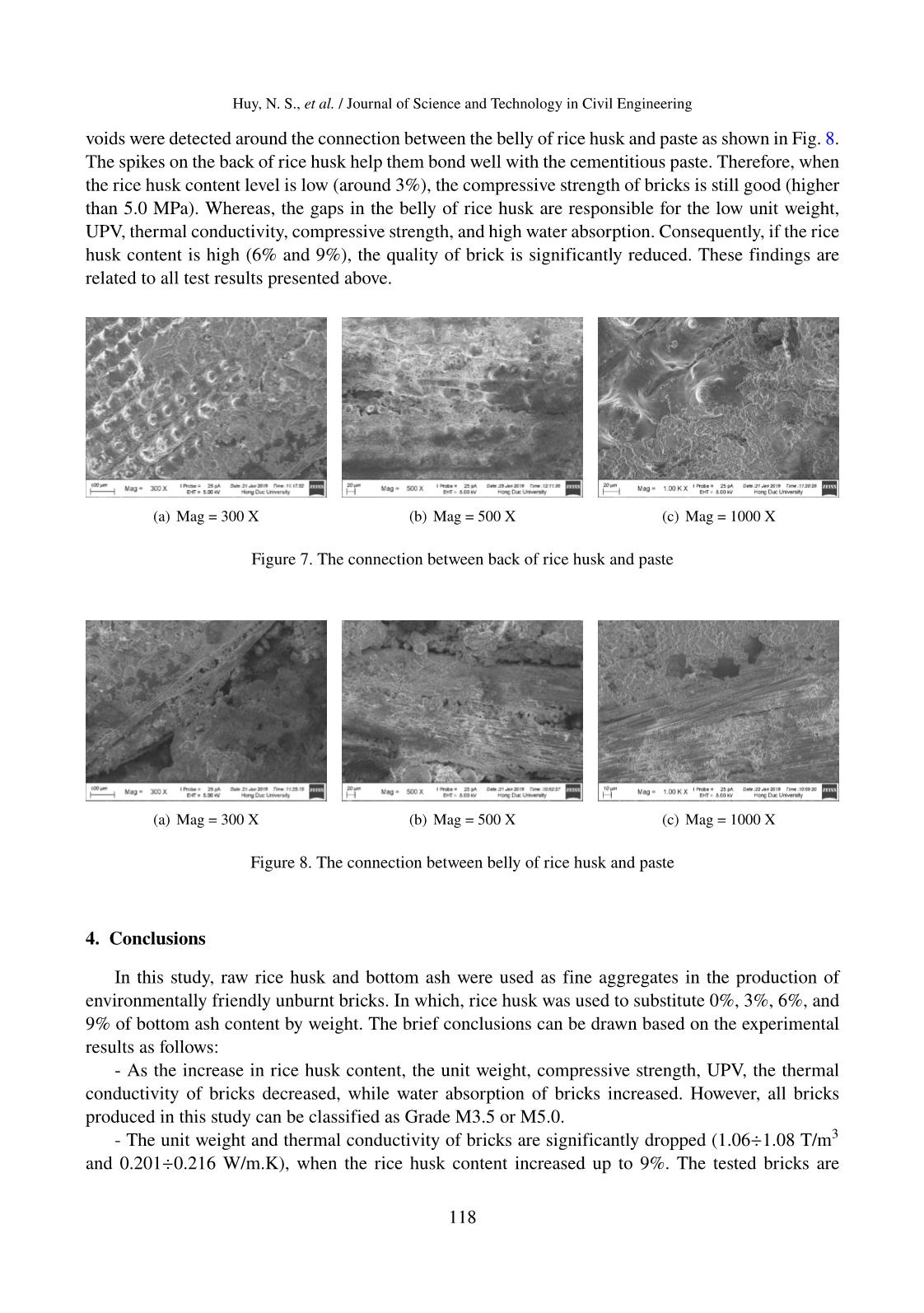
Trang 9
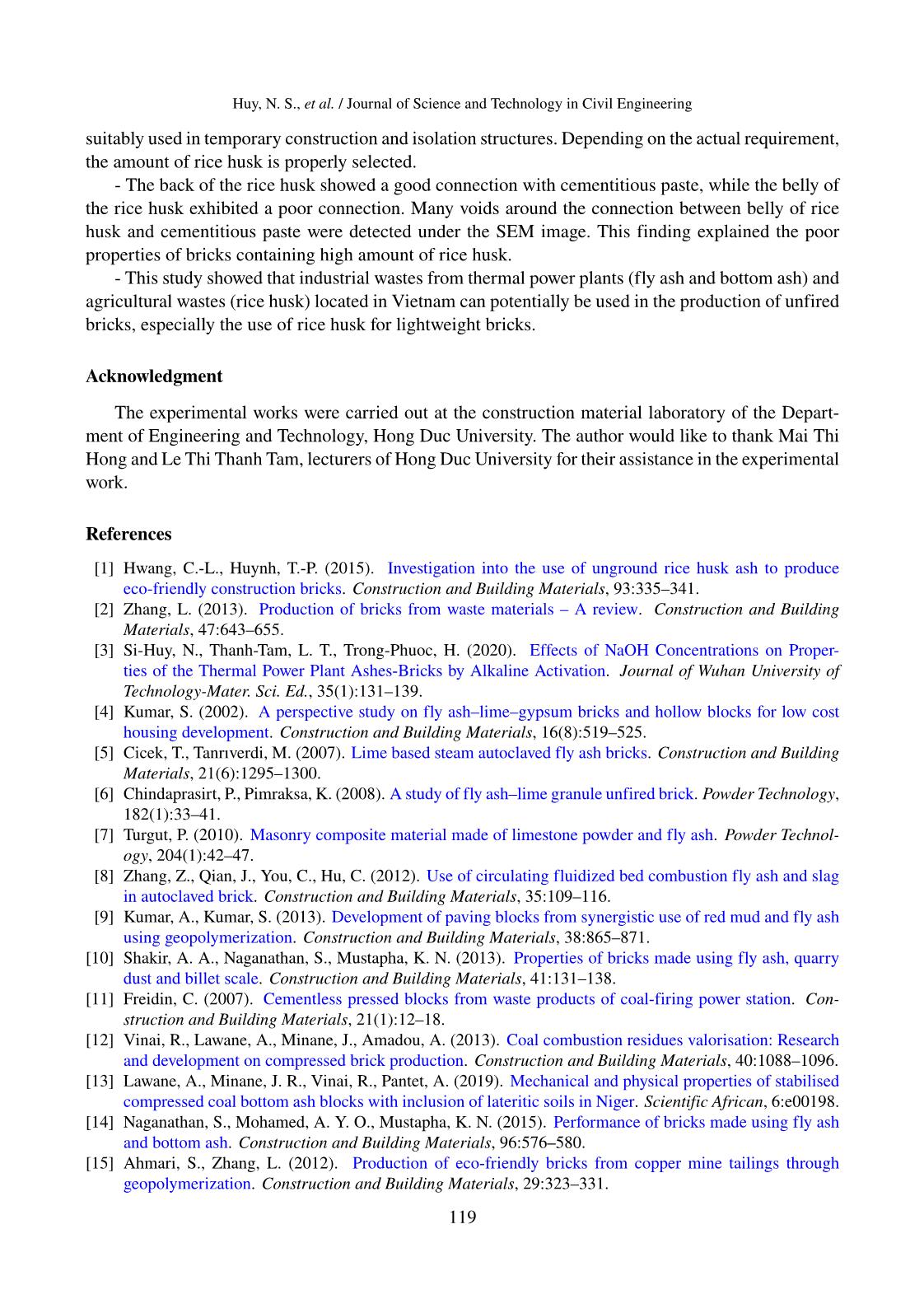
Trang 10
Tải về để xem bản đầy đủ
Tóm tắt nội dung tài liệu: Environmentally friendly unburnt bricks using raw rice husk and bottom ash as fine aggregates: Physical and mechanical properties
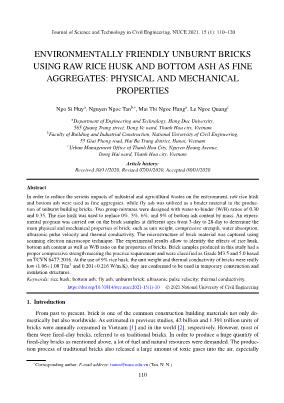
Journal of Science and Technology in Civil Engineering, NUCE 2021. 15 (1): 110–120 ENVIRONMENTALLY FRIENDLY UNBURNT BRICKS USING RAW RICE HUSK AND BOTTOM ASH AS FINE AGGREGATES: PHYSICAL AND MECHANICAL PROPERTIES Ngo Si Huya, Nguyen Ngoc Tanb,∗, Mai Thi Ngoc Hanga, Le Ngoc Quangc aDepartment of Engineering and Technology, Hong Duc University, 565 Quang Trung street, Dong Ve ward, Thanh Hoa city, Vietnam bFaculty of Building and Industrial Construction, National University of Civil Engineering, 55 Giai Phong road, Hai Ba Trung district, Hanoi, Vietnam cUrban Management Office of Thanh Hoa City, Nguyen Hoang Avenue, Dong Hai ward, Thanh Hoa city, Vietnam Article history: Received 30/11/2020, Revised 07/01/2020, Accepted 08/01/2020 Abstract In order to reduce the serious impacts of industrial and agricultural wastes on the environment, raw rice husk and bottom ash were used as fine aggregates, while fly ash was utilized as a binder material in the produc- tion of unburnt building bricks. Two group mixtures were designed with water-to-binder (W/B) ratios of 0.30 and 0.35. The rice husk was used to replace 0%, 3%, 6%, and 9% of bottom ash content by mass. An experi- mental program was carried out on the brick samples at different ages from 3-day to 28-day to determine the main physical and mechanical properties of brick, such as unit weight, compressive strength, water absorption, ultrasonic pulse velocity and thermal conductivity. The microstructure of brick material was captured using scanning electron microscope technique. The experimental results allow to identify the effects of rice husk, bottom ash content as well as W/B ratio on the properties of bricks. Brick samples produced in this study had a proper compressive strength meeting the practice requirement and were classified as Grade M3.5 and 5.0 based on TCVN 6477:2016. At the use of 9% rice husk, the unit weight and thermal conductivity of bricks were really low (1.06÷1.08 T/m3 and 0.201÷0.216 W/m.K), they are conformed to be used in temporary construction and insulation structures. Keywords: rice husk; bottom ash; fly ash; unburnt brick; ultrasonic pulse velocity; thermal conductivity. https://doi.org/10.31814/stce.nuce2021-15(1)-10 © 2021 National University of Civil Engineering 1. Introduction From past to present, brick is one of the common construction building materials not only do- mestically but also worldwide. As estimated in previous studies, 42 billion and 1.391 trillion units of bricks were annually consumed in Vietnam [1] and in the world [2], respectively. However, most of them were fired-clay bricks, referred to as traditional bricks. In order to produce a huge quantity of fired-clay bricks as mentioned above, a lot of fuel and natural resources were demanded. The produc- tion process of traditional bricks also released a large amount of toxic gases into the air, especially ∗Corresponding author. E-mail address: tannn@nuce.edu.vn (Tan, N. N.) 110 Huy, N. S., et al. / Journal of Science and Technology in Civil Engineering carbon dioxide, causing environmental pollution. Therefore, the Prime Minister of Vietnam has is- sued the Directive on enhancing the use of unburnt construction materials and limiting the production of fired-clay bricks since 2012. Especially, the reuse of solid wastes from industry to produce unfired building bricks has been encouraging. In Vietnam, the common unfired building bricks are produced from cement, sand or crushed stone as fine aggregates, and water. Their unit weight and compressive strength are typical around 2.0÷2.2 T/m3 and 3.5÷7.5 MPa, respectively [3]. It is noticed that the production of cement also causes the depletion of natural resources and put the negative impacts on the environment. Recently, the over extraction of river sand is another issue related to aquatic life, water sources, erosion and land loss. While the crushing of quarried stones also has some problems associated with the noise pollution and damages the natural environment. On the other hand, many types of industrial wastes such as fly ash, bottom ash, copper mining tailings, gold mill tailings, red mud are emitted to the environment due to the growth of population and a higher demand of human. These industrial wastes have seriously impacts on the environment and human life. Turning such wastes into green construction materials is an effective solution not only for the environment but also for the economic benefit. Among many types of solid industrial wastes, the thermal power plant ashes such as fly ash and bottom ash were widely used in the production of unburnt bricks. While fly ash was used as a binder material [4–10], bottom ash was utilized as fine aggregate [3, 11–14]. Although the test results were different among these studies, but most of them showed the high possible using both fly ash and bottom ash in the manufacturing of unfired bricks. Besides fly ash and botto ... ed in Fig. 6. It can be s en in Fig. 6, the thermal conductivity of bricks decreased with increasing rice husk content and /B ratio. It was stated that the thermal conductivity of a brick sample is related to its unit weight and porosity [3, 31]. When the rice husk content increased, the unit weight of bricks declined. Consequently, their thermal conductivity values reduced. The similar trend is observed when W/B ratio increased. Incorporating rice husk, the thermal conductivity of bricks felt within the range of 0.201÷0.454 W/m.K. This range is similar to the result from Görhan and Şimşek’s study [21]. It is noticed that Görhan and Şimşek used rice husk in the production of fired-clay lightweight bricks. Their thermal conductivity ranged from 0.173 to 0.494 W/m.K. It is worth noting that the brick samples with 9% rice husk had a very low thermal conductivity values (0.201÷0.216 W/m.K). As the results, with low unit weight and low thermal conductivity, these rice husk bricks in this study is also suitably used in isolation structures. 0 7 14 21 28 Curing time (days) 0 0.5 1 1.5 2 2.5 3 U ltr as on ic p ul se v el oc ity (k m /s ) M30RH0 M30RH3 M30RH6 M30RH9 0 7 14 21 28 Curing time (days) 0 0.5 1 1.5 2 2.5 3 U ltr as on ic p ul se v el oc ity (k m /s ) M35RH0 M35RH3 M35RH6 M35RH9 (b) Figure 5. Ultrasonic pulse velocity of (a) 30 and (b) M35 brick samples 116 Huy, N. S., et al. / Journal of Science and Technology in Civil Engineering husk content of 0%, 3%, 6%, and 9%, respectively. Those were 2.61, 2.24, 1.66, and 1.18 km/s for the corresponding M35 brick samples. As mentioned above, the density of bricks reduced when rice husk content increased, resulting in reduction in UPV values. The low UPV value of brick samples is attributed to the voids among rice husk particles. It is demonstrated in previous studies [3, 29] that the UPV values and the compressive strength has a relationship. The bricks produced by the use of thermal power plant ashes had UPV values of 1.10÷1.77 km/s coressponding to compressive strength of 1.18÷7.7 MPa [3]. While the bricks used 5% rice husk ash and 5% surgarcane bagasse ash had UPV values of 1.16÷1.64 km/s [30]. In present study, at the rice husk content of 6% or higher, the UPV values of bricks ranged from 1.18 km/s to 1.94 km/s, similar to those values from previous studies [3, 30]. It is noticed that the compressive strength and unit weight of these bricks were around 3.42÷4.81 MPa and 1.06÷1.49 T/m3, considered as lightweight bricks. While other brick samples with rice husk content of 0% and 3% had compressive strength of 5.33÷9.62 MPa, unit weight of 1.46÷1.56 T/m3, resulting in UPV values of above 2.2 km/s. They may be considered as normal unfired building bricks. Depending on the actual requirements, the rice husk content is properly selected. 3.5. Thermal conductivity Journal of Science and Technology in Civil Engineering NUCE 2021 Figure 6. Effect of rice husk content on thermal conductivity of brick samples 3.6. SEM observation The scanning electron microscope (SEM) was used to observe the microstructure of bricks, especially the connection between rice husk and paste. The SEM micrographs of unfired building bricks incorporating rice husk are shown in Figs. 7 and 8. These micrographs were taken on different samples with magnifications (denoted Mag) of 300, 500, and 1000 times. It is interesting that the connection between the back of rice husk and cementitious paste is greatly good as shown in Fig. 7, while many voids were detected around the connection between the belly of rice husk and paste as shown in Fig. 8. The spikes on the back of rice husk help them bond well with the cementitious paste. Therefore, when the rice husk content level is low (around 3%), the compressive strength of bricks is still good (higher than 5.0 MPa). Whereas, the gaps in the belly of rice husk are responsible for the low unit weight, UPV, thermal conductivity, compressive strength, and high water absorption. Consequently, if the rice husk content is high (6% and 9%), the quality of brick is significantly reduced. These findings are related to all test results presented above. (a) Mag = 300 X (b) Mag = 500 X (c) Mag = 1000 X Figure 7. The connection between back of rice husk and paste Rice husk content (%) 0 0.1 0.2 0.3 0.4 0.5 0.6 0.7 Th er m al c on du ct iv ity (W /m K ) M30 M35 0 3 6 9 Figure 6. Effect of rice husk content on thermal conductivity of brick samples The lightweight bricks are usualy used in heat isolation structures, then the thermal conductivity test was conducted to assess the insulation capac- ity of these bricks in this study. The effect of rice husk content on the thermal conductivity of bricks is illustrated in Fig. 6. It can be seen in Fig. 6, the thermal conductivity of bricks decreased with increasing rice husk content and W/B ratio. It was stated that the thermal conductivity of a brick sample is related to its unit weight and porosity [3, 31]. When the rice husk content increased, the unit weight of bricks declined. Consequently, their thermal conductivity values reduced. The similar trend is observed when W/B ratio increased. In- corporating rice husk, the thermal conductivity of bricks felt within the range of 0.201÷0.454 W/m.K. This range is similar to the result from Go¨rhan and S¸ims¸ek’s study [21]. It is noticed that Go¨rhan and S¸ims¸ek used ri e husk in the production of fired-clay lightweight bricks. Their thermal conductivity ranged from 0.173 to 0.494 W/m.K. It is worth noting that the brick samples with 9% rice husk had a very low thermal conductivity values (0.201÷0.216 W/m.K). As the results, with low unit weight and low thermal conductivity, these rice husk bricks in this study is also suitably used in isolation structures. 3.6. SEM observation The scanning electron microscope (SEM) was us d to obser the micr structure of bricks, espe- cially the connection between rice husk and paste. The SEM micrographs of unfired building bricks incorporating rice husk are shown in Figs. 7 and 8. These micrographs were taken on different samples with magnifications (denoted Mag) of 300, 500, and 1000 times. It is interesting that the connection between the back of rice husk and cementitious paste is greatly good as shown in Fig. 7, while many 117 Huy, N. S., et al. / Journal of Science and Technology in Civil Engineering voids were detected around the connection between the belly of rice husk and paste as shown in Fig. 8. The spikes on the back of rice husk help them bond well with the cementitious paste. Therefore, when the rice husk content level is low (around 3%), the compressive strength of bricks is still good (higher than 5.0 MPa). Whereas, the gaps in the belly of rice husk are responsible for the low unit weight, UPV, thermal conductivity, compressive strength, and high water absorption. Consequently, if the rice husk content is high (6% and 9%), the quality of brick is significantly reduced. These findings are related to all test results presented above. (a) Mag = 300 X (b) Mag = 500 X (c) Mag = 1000 X Figure 7. The connection between back of rice husk and paste (a) Mag = 300 X (b) Mag = 500 X (c) Mag = 1000 X Figure 8. The connection between belly of rice husk and paste 4. Conclusions In this study, raw rice husk and bottom ash were used as fine aggregates in the production of environmentally friendly unburnt bricks. In which, rice husk was used to substitute 0%, 3%, 6%, and 9% of bottom ash content by weight. The brief conclusions can be drawn based on the experimental results as follows: - As the increase in rice husk content, the unit weight, compressive strength, UPV, the thermal conductivity of bricks decreased, while water absorption of bricks increased. However, all bricks produced in this study can be classified as Grade M3.5 or M5.0. - The unit weight and thermal conductivity of bricks are significantly dropped (1.06÷1.08 T/m3 and 0.201÷0.216 W/m.K), when the rice husk content increased up to 9%. The tested bricks are 118 Huy, N. S., et al. / Journal of Science and Technology in Civil Engineering suitably used in temporary construction and isolation structures. Depending on the actual requirement, the amount of rice husk is properly selected. - The back of the rice husk showed a good connection with cementitious paste, while the belly of the rice husk exhibited a poor connection. Many voids around the connection between belly of rice husk and cementitious paste were detected under the SEM image. This finding explained the poor properties of bricks containing high amount of rice husk. - This study showed that industrial wastes from thermal power plants (fly ash and bottom ash) and agricultural wastes (rice husk) located in Vietnam can potentially be used in the production of unfired bricks, especially the use of rice husk for lightweight bricks. Acknowledgment The experimental works were carried out at the construction material laboratory of the Depart- ment of Engineering and Technology, Hong Duc University. The author would like to thank Mai Thi Hong and Le Thi Thanh Tam, lecturers of Hong Duc University for their assistance in the experimental work. References [1] Hwang, C.-L., Huynh, T.-P. (2015). Investigation into the use of unground rice husk ash to produce eco-friendly construction bricks. Construction and Building Materials, 93:335–341. [2] Zhang, L. (2013). Production of bricks from waste materials – A review. Construction and Building Materials, 47:643–655. [3] Si-Huy, N., Thanh-Tam, L. T., Trong-Phuoc, H. (2020). Effects of NaOH Concentrations on Proper- ties of the Thermal Power Plant Ashes-Bricks by Alkaline Activation. Journal of Wuhan University of Technology-Mater. Sci. Ed., 35(1):131–139. [4] Kumar, S. (2002). A perspective study on fly ash–lime–gypsum bricks and hollow blocks for low cost housing development. Construction and Building Materials, 16(8):519–525. [5] Cicek, T., Tanrıverdi, M. (2007). Lime based steam autoclaved fly ash bricks. Construction and Building Materials, 21(6):1295–1300. [6] Chindaprasirt, P., Pimraksa, K. (2008). A study of fly ash–lime granule unfired brick. Powder Technology, 182(1):33–41. [7] Turgut, P. (2010). Masonry composite material made of limestone powder and fly ash. Powder Technol- ogy, 204(1):42–47. [8] Zhang, Z., Qian, J., You, C., Hu, C. (2012). Use of circulating fluidized bed combustion fly ash and slag in autoclaved brick. Construction and Building Materials, 35:109–116. [9] Kumar, A., Kumar, S. (2013). Development of paving blocks from synergistic use of red mud and fly ash using geopolymerization. Construction and Building Materials, 38:865–871. [10] Shakir, A. A., Naganathan, S., Mustapha, K. N. (2013). Properties of bricks made using fly ash, quarry dust and billet scale. Construction and Building Materials, 41:131–138. [11] Freidin, C. (2007). Cementless pressed blocks from waste products of coal-firing power station. Con- struction and Building Materials, 21(1):12–18. [12] Vinai, R., Lawane, A., Minane, J., Amadou, A. (2013). Coal combustion residues valorisation: Research and development on compressed brick production. Construction and Building Materials, 40:1088–1096. [13] Lawane, A., Minane, J. R., Vinai, R., Pantet, A. (2019). Mechanical and physical properties of stabilised compressed coal bottom ash blocks with inclusion of lateritic soils in Niger. Scientific African, 6:e00198. [14] Naganathan, S., Mohamed, A. Y. O., Mustapha, K. N. (2015). Performance of bricks made using fly ash and bottom ash. Construction and Building Materials, 96:576–580. [15] Ahmari, S., Zhang, L. (2012). Production of eco-friendly bricks from copper mine tailings through geopolymerization. Construction and Building Materials, 29:323–331. 119 Huy, N. S., et al. / Journal of Science and Technology in Civil Engineering [16] Roy, S., Adhikari, G. R., Gupta, R. N. (2007). Use of gold mill tailings in making bricks: a feasibility study. Waste Management & Research, 25(5):475–482. [17] Khan, R., Jabbar, A., Ahmad, I., Khan, W., Khan, A. N., Mirza, J. (2012). Reduction in environmental problems using rice-husk ash in concrete. Construction and Building Materials, 30:360–365. [18] Sutas, J., Mana, A., Pitak, L. (2012). Effect of Rice Husk and Rice Husk Ash to Properties of Bricks. Procedia Engineering, 32:1061–1067. [19] Silva, G. S. D., Perera, B. (2018). Effect of waste rice husk ash (RHA) on structural, thermal and acoustic properties of fired clay bricks. Journal of Building Engineering, 18:252–259. [20] Phonphuak, N., Saengthong, C., Srisuwan, A. (2019). Physical and mechanical properties of fired clay bricks with rice husk waste addition as construction materials. Materials Today: Proceedings, 17:1668– 1674. [21] Go¨rhan, G., S¸ims¸ek, O. (2013). Porous clay bricks manufactured with rice husks. Construction and Building Materials, 40:390–396. [22] Hwang, C.-L., Huynh, T.-P., Risdianto, Y. (2016). An application of blended fly ash and residual rice husk ash for producing green building bricks. Journal of the Chinese Institute of Engineers, 39(7):850–858. [23] An, V. V. T. (2017). Alkali silica reaction in ultra-high performance concrete containing rice husk ash. Journal of Science and Technology in Civil Engineering (STCE) - NUCE, 11(6):104–110. [24] Phuoc, H. T., Hung, V. V., Tuan, B. L. A., Giang, P. H. H. (2020). Development of a cementless eco- binder as an alternative to traditional Portland cement in construction activities. Journal of Science and Technology in Civil Engineering (STCE) - NUCE, 14(3):40–52. [25] Abdullah, A., Lee, C. (2017). Effect of Treatments on Properties of Cement-fiber Bricks Utilizing Rice Husk, Corncob and Coconut Coir. Procedia Engineering, 180:1266–1273. [26] Mansaray, K. G., Ghaly, A. E. (1997). Physical and Thermochemical Properties of Rice Husk. Energy Sources, 19(9):989–1004. [27] TCVN 6477:2016. Concrete bricks. Ministry of Science and Technology, Vietnam. [28] ASTM C597 (2016). Standard tets method for pulse velocity through concrete. American Society of Testing Materials. [29] Bogas, J. A., Gomes, M. G., Gomes, A. (2013). Compressive strength evaluation of structural lightweight concrete by non-destructive ultrasonic pulse velocity method. Ultrasonics, 53(5):962–972. [30] Kazmi, S. M. S., Abbas, S., Munir, M. J., Khitab, A. (2016). Exploratory study on the effect of waste rice husk and sugarcane bagasse ashes in burnt clay bricks. Journal of Building Engineering, 7:372–378. [31] Sutcu, M., Akkurt, S. (2009). The use of recycled paper processing residues in making porous brick with reduced thermal conductivity. Ceramics International, 35(7):2625–2631. 120
File đính kèm:
environmentally_friendly_unburnt_bricks_using_raw_rice_husk.pdf