Effects of knit structure on the dimensional and physical properties of winter outerwear knitted fabrics
Knit fabrics provide outstanding comfort
qualities and have long been preferred as
fabrics in many kinds of clothing. Since
knit fabrics are produced on different
machines with different knit stitches and
conditions to create different patterns and
fabric types, we expect them to have different qualities [1]. The commercial design of knitted garments is a process that
shares many important characteristics
with other types of aesthetic design and
engineering [2]. Although many CAD
systems are commercially available for
the artistic design of fabrics, none is
commercially available for the engineering design of fabrics to meet their end use
performance requirements [3].
In apparel design and garment manufacturing, fabric characteristics are usually dictated by a specified end-use.
Understanding the relationship between
the fabric end-use and fabric properties
becomes fundamental for classification,
selection, search, and purchase control
of apparel fabrics [4]. Tactile (hand) and
appearance properties are very important in all classes of fabrics [5]. Appearance retention is directly related to the
longevity and serviceability of fabrics.
A fabric may loose its aesthetic appeal
due to wear, which is a combined effect
of several factors like abrasion, repeated
laundering, the application of forces in
dry and wet states etc. arising from everyday use and service. Surface abrasion
is considered perhaps the most important
of these factors, and so it has become
routine in fabric testing [6]. The effects
of various knit structures on the abrasion
strength have been analysed by a lot of
researchers [7 - 9].
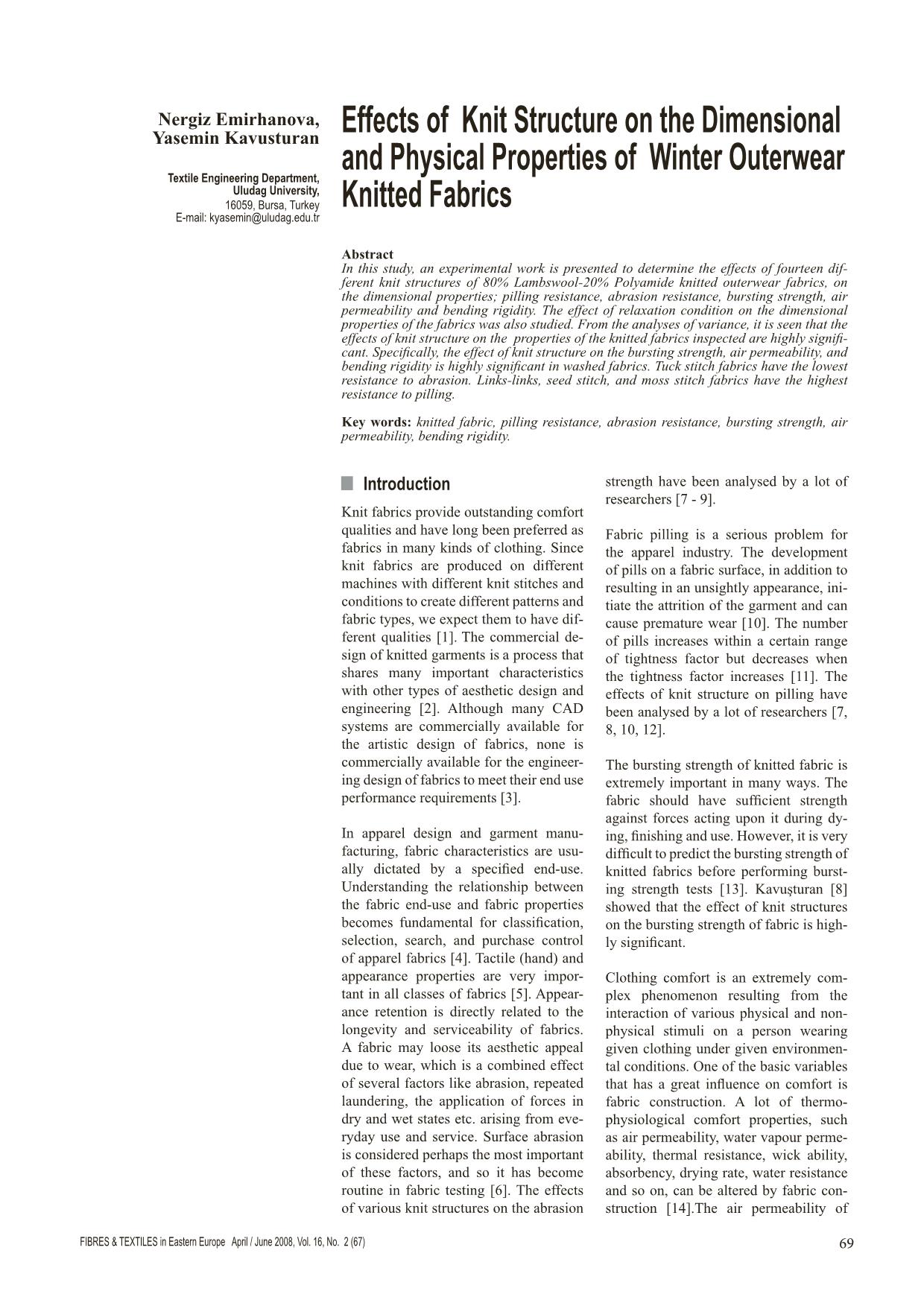
Trang 1
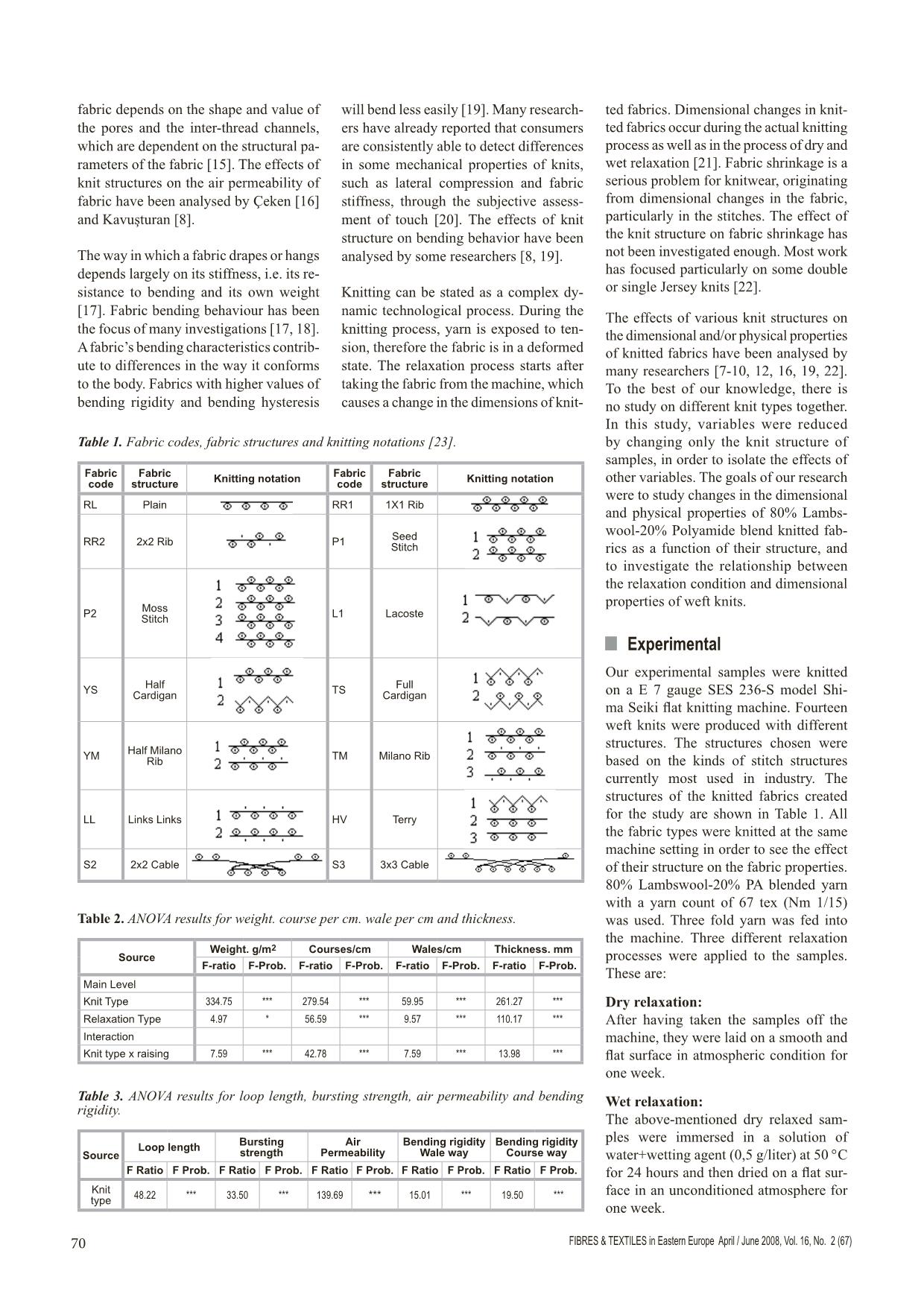
Trang 2
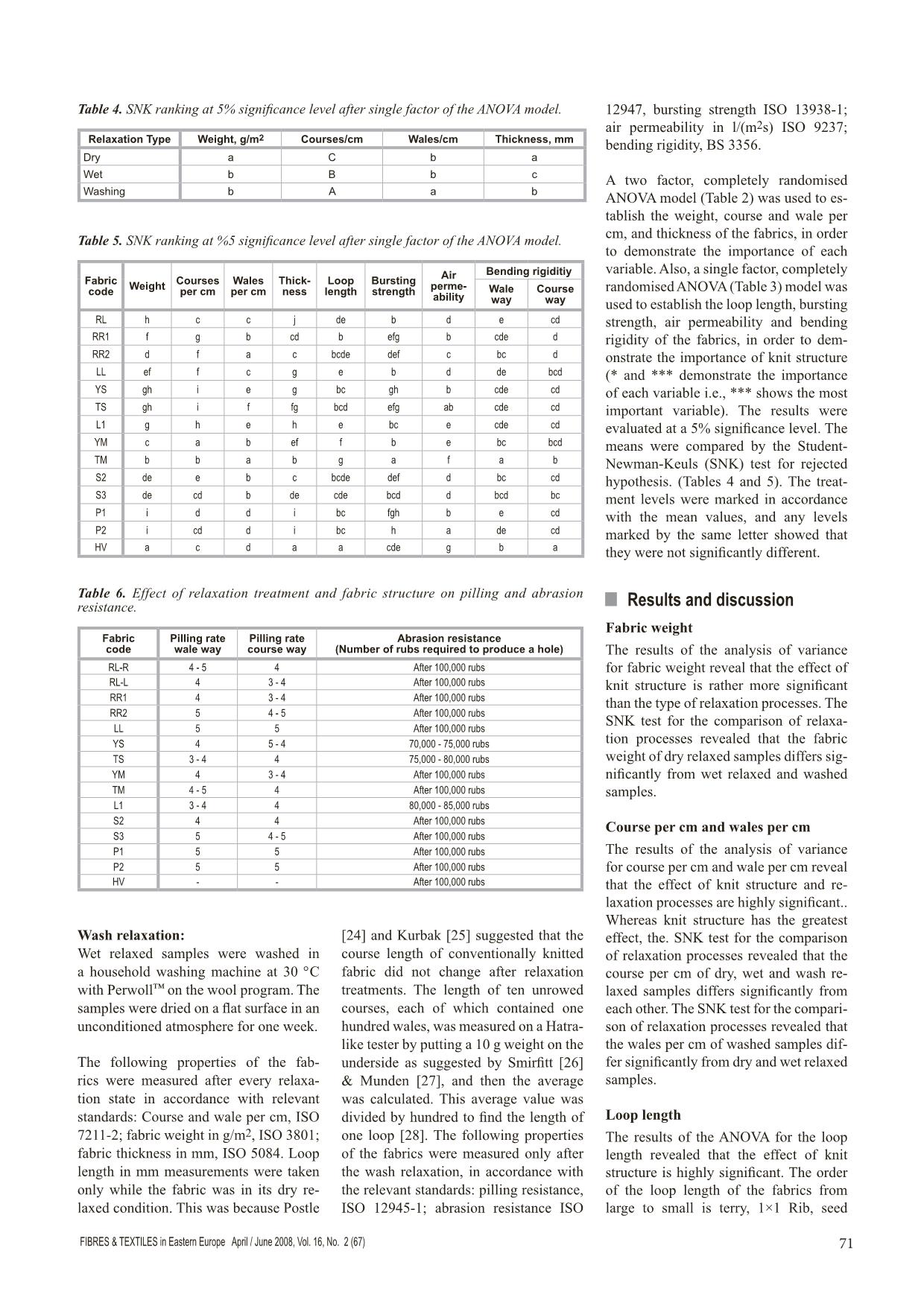
Trang 3
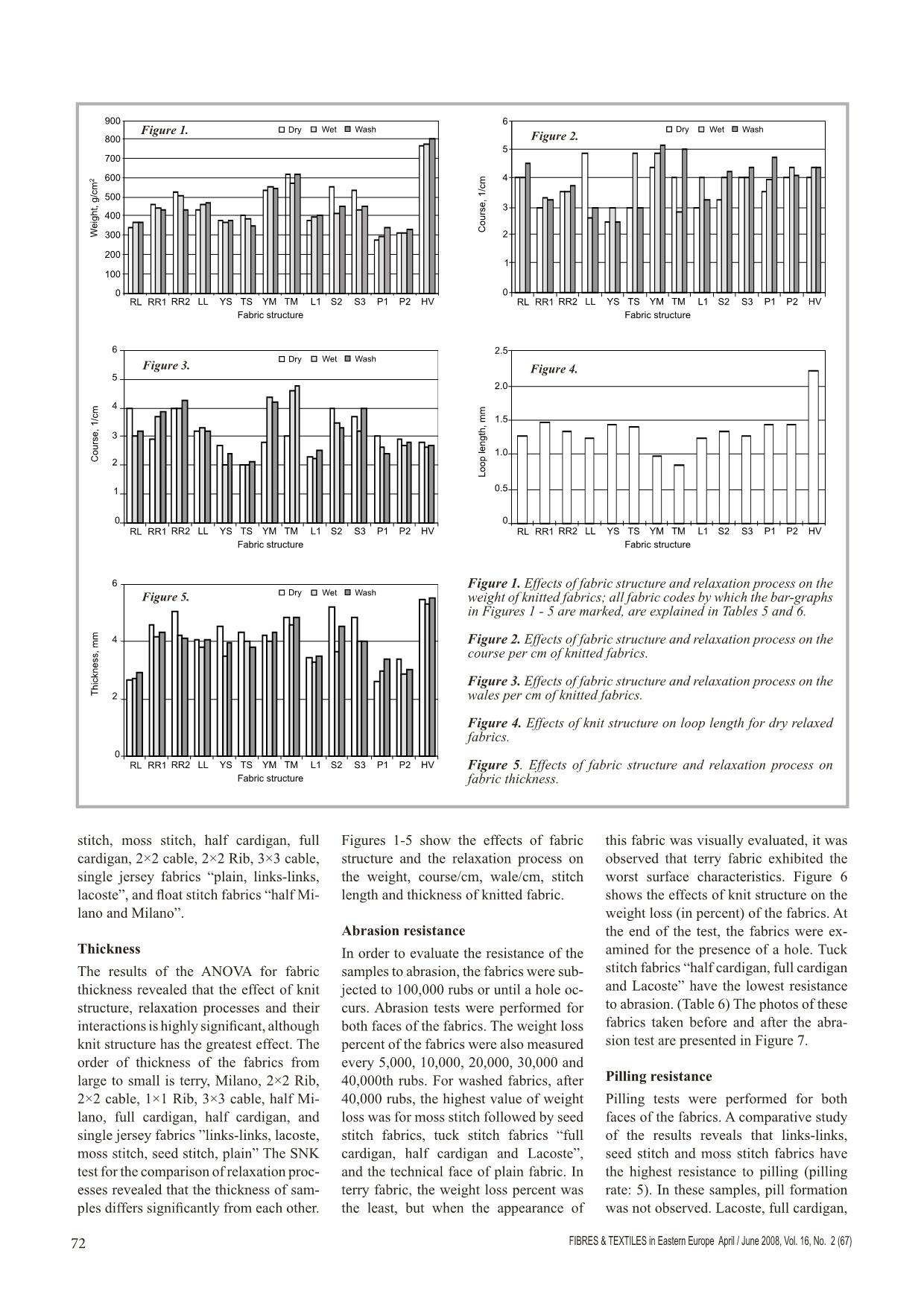
Trang 4
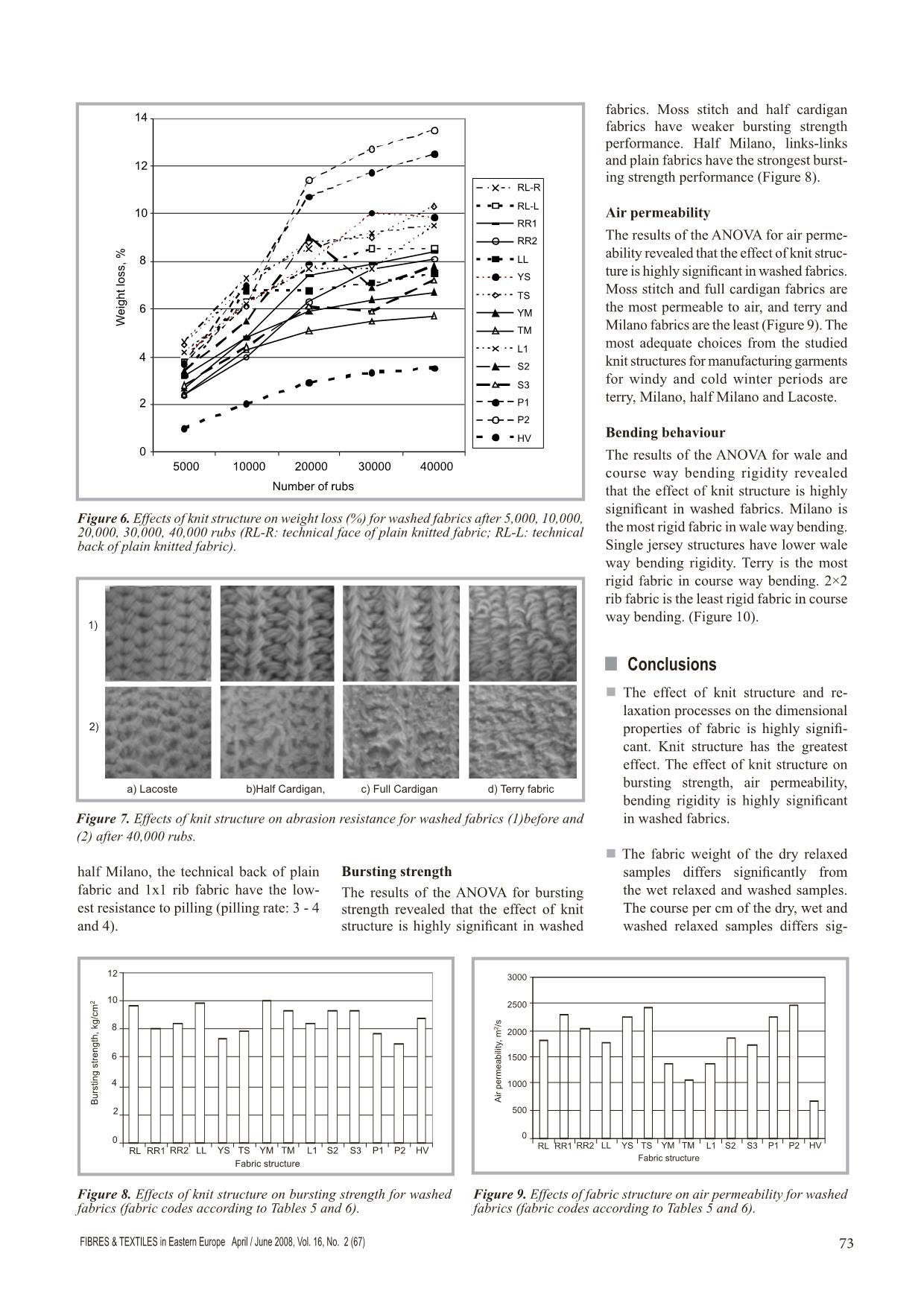
Trang 5
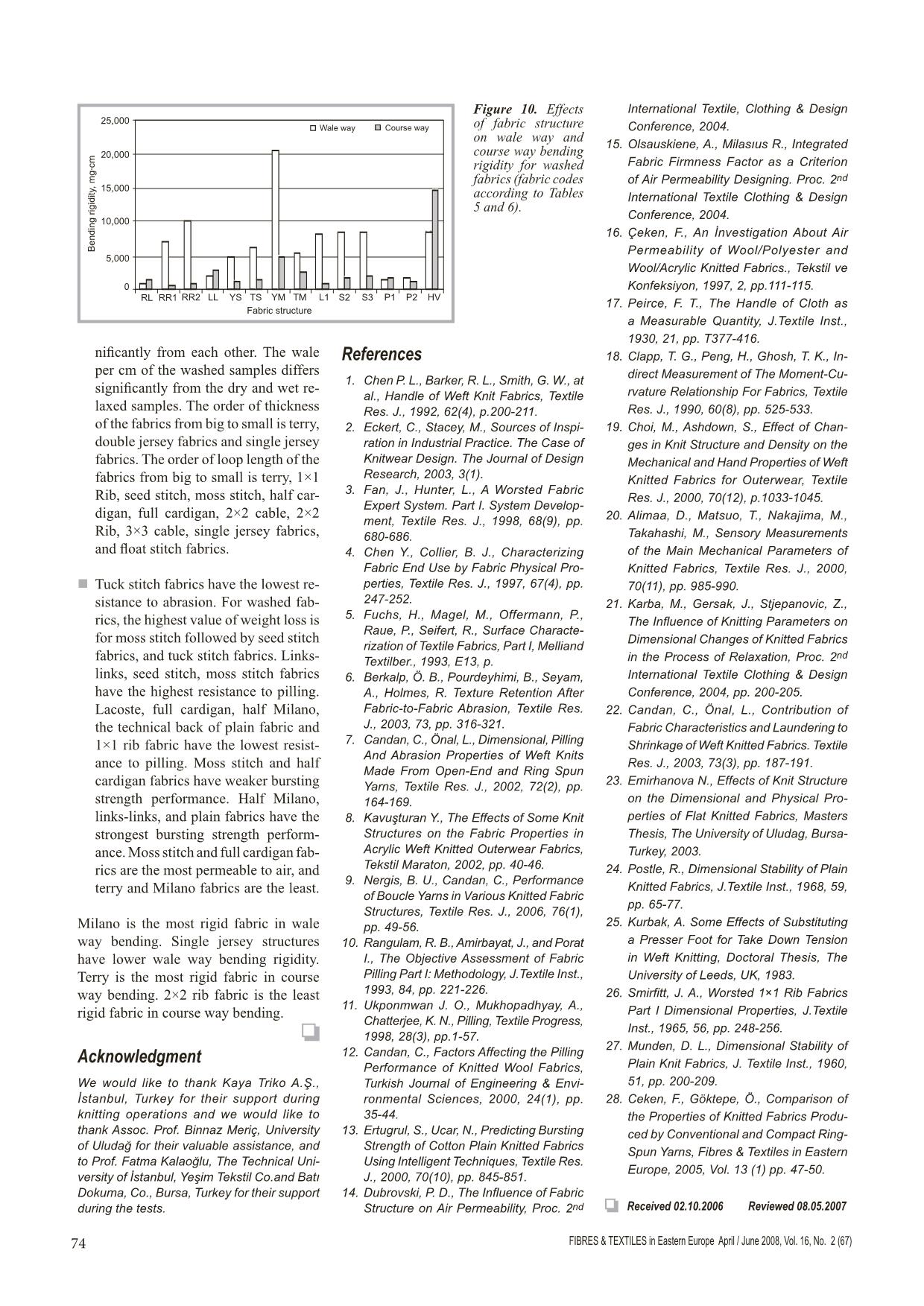
Trang 6
Tóm tắt nội dung tài liệu: Effects of knit structure on the dimensional and physical properties of winter outerwear knitted fabrics
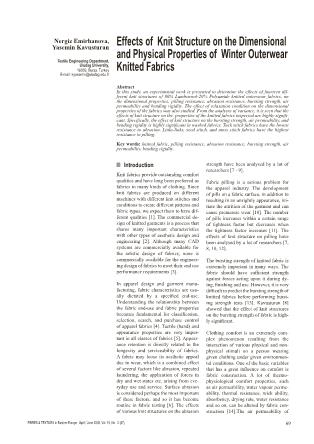
69FIBRES & TEXTILES in Eastern Europe April / June 2008, Vol. 16, No. 2 (67) n Introduction Knit fabrics provide outstanding comfort qualities and have long been preferred as fabrics in many kinds of clothing. Since knit fabrics are produced on different machines with different knit stitches and conditions to create different patterns and fabric types, we expect them to have dif- ferent qualities [1]. The commercial de- sign of knitted garments is a process that shares many important characteristics with other types of aesthetic design and engineering [2]. Although many CAD systems are commercially available for the artistic design of fabrics, none is commercially available for the engineer- ing design of fabrics to meet their end use performance requirements [3]. In apparel design and garment manu- facturing, fabric characteristics are usu- ally dictated by a specified end-use. Understanding the relationship between the fabric end-use and fabric properties becomes fundamental for classification, selection, search, and purchase control of apparel fabrics [4]. Tactile (hand) and appearance properties are very impor- tant in all classes of fabrics [5]. Appear- ance retention is directly related to the longevity and serviceability of fabrics. A fabric may loose its aesthetic appeal due to wear, which is a combined effect of several factors like abrasion, repeated laundering, the application of forces in dry and wet states etc. arising from eve- ryday use and service. Surface abrasion is considered perhaps the most important of these factors, and so it has become routine in fabric testing [6]. The effects of various knit structures on the abrasion strength have been analysed by a lot of researchers [7 - 9]. Fabric pilling is a serious problem for the apparel industry. The development of pills on a fabric surface, in addition to resulting in an unsightly appearance, ini- tiate the attrition of the garment and can cause premature wear [10]. The number of pills increases within a certain range of tightness factor but decreases when the tightness factor increases [11]. The effects of knit structure on pilling have been analysed by a lot of researchers [7, 8, 10, 12]. The bursting strength of knitted fabric is extremely important in many ways. The fabric should have sufficient strength against forces acting upon it during dy- ing, finishing and use. However, it is very difficult to predict the bursting strength of knitted fabrics before performing burst- ing strength tests [13]. Kavuşturan [8] showed that the effect of knit structures on the bursting strength of fabric is high- ly significant. Clothing comfort is an extremely com- plex phenomenon resulting from the interaction of various physical and non- physical stimuli on a person wearing given clothing under given environmen- tal conditions. One of the basic variables that has a great influence on comfort is fabric construction. A lot of thermo- physiological comfort properties, such as air permeability, water vapour perme- ability, thermal resistance, wick ability, absorbency, drying rate, water resistance and so on, can be altered by fabric con- struction [14].The air permeability of Effects of Knit Structure on the Dimensional and Physical Properties of Winter Outerwear Knitted Fabrics Nergiz Emirhanova, Yasemin Kavusturan Textile Engineering Department, Uludag University, 16059, Bursa, Turkey E-mail: kyasemin@uludag.edu.tr Abstract In this study, an experimental work is presented to determine the effects of fourteen dif- ferent knit structures of 80% Lambswool-20% Polyamide knitted outerwear fabrics, on the dimensional properties; pilling resistance, abrasion resistance, bursting strength, air permeability and bending rigidity. The effect of relaxation condition on the dimensional properties of the fabrics was also studied. From the analyses of variance, it is seen that the effects of knit structure on the properties of the knitted fabrics inspected are highly signifi- cant. Specifically, the effect of knit structure on the bursting strength, air permeability, and bending rigidity is highly significant in washed fabrics. Tuck stitch fabrics have the lowest resistance to abrasion. Links-links, seed stitch, and moss stitch fabrics have the highest resistance to pilling. Key words: knitted fabric, pilling resistance, abrasion resistance, bursting strength, air permeability, bending rigidity. FIBRES & TEXTILES in Eastern Europe April / June 2008, Vol. 16, No. 2 (67)70 fabric depends on the shape and value of the pores and the inter-thread channels, which are dependent on the structural pa- rameters of the fabric [15]. The effects of knit structures on the air permeability of fabric have been analysed by Çeken [16] and Kavuşturan [8]. The way in which a fabric drapes or hangs ... ses. The SNK test for the comparison of relaxa- tion processes revealed that the fabric weight of dry relaxed samples differs sig- nificantly from wet relaxed and washed samples. Course per cm and wales per cm The results of the analysis of variance for course per cm and wale per cm reveal that the effect of knit structure and re- laxation processes are highly significant.. Whereas knit structure has the greatest effect, the. SNK test for the comparison of relaxation processes revealed that the course per cm of dry, wet and wash re- laxed samples differs significantly from each other. The SNK test for the compari- son of relaxation processes revealed that the wales per cm of washed samples dif- fer significantly from dry and wet relaxed samples. Loop length The results of the ANOVA for the loop length revealed that the effect of knit structure is highly significant. The order of the loop length of the fabrics from large to small is terry, 1×1 Rib, seed Table 4. SNK ranking at 5% significance level after single factor of the ANOVA model. Relaxation Type Weight, g/m2 Courses/cm Wales/cm Thickness, mm Dry a C b a Wet b B b c Washing b A a b Table 5. SNK ranking at %5 significance level after single factor of the ANOVA model. Fabric code Weight Courses per cm Wales per cm Thick- ness Loop length Bursting strength Air perme- ability Bending rigiditiy Wale way Course way RL h c c j de b d e cd RR1 f g b cd b efg b cde d RR2 d f a c bcde def c bc d LL ef f c g e b d de bcd YS gh i e g bc gh b cde cd TS gh i f fg bcd efg ab cde cd L1 g h e h e bc e cde cd YM c a b ef f b e bc bcd TM b b a b g a f a b S2 de e b c bcde def d bc cd S3 de cd b de cde bcd d bcd bc P1 i d d i bc fgh b e cd P2 i cd d i bc h a de cd HV a c d a a cde g b a Table 6. Effect of relaxation treatment and fabric structure on pilling and abrasion resistance. Fabric code Pilling rate wale way Pilling rate course way Abrasion resistance (Number of rubs required to produce a hole) RL-R 4 - 5 4 After 100,000 rubs RL-L 4 3 - 4 After 100,000 rubs RR1 4 3 - 4 After 100,000 rubs RR2 5 4 - 5 After 100,000 rubs LL 5 5 After 100,000 rubs YS 4 5 - 4 70,000 - 75,000 rubs TS 3 - 4 4 75,000 - 80,000 rubs YM 4 3 - 4 After 100,000 rubs TM 4 - 5 4 After 100,000 rubs L1 3 - 4 4 80,000 - 85,000 rubs S2 4 4 After 100,000 rubs S3 5 4 - 5 After 100,000 rubs P1 5 5 After 100,000 rubs P2 5 5 After 100,000 rubs HV - - After 100,000 rubs FIBRES & TEXTILES in Eastern Europe April / June 2008, Vol. 16, No. 2 (67)72 stitch, moss stitch, half cardigan, full cardigan, 2×2 cable, 2×2 Rib, 3×3 cable, single jersey fabrics “plain, links-links, lacoste”, and float stitch fabrics “half Mi- lano and Milano”. Thickness The results of the ANOVA for fabric thickness revealed that the effect of knit structure, relaxation processes and their interactions is highly significant, although knit structure has the greatest effect. The order of thickness of the fabrics from large to small is terry, Milano, 2×2 Rib, 2×2 cable, 1×1 Rib, 3×3 cable, half Mi- lano, full cardigan, half cardigan, and single jersey fabrics ”links-links, lacoste, moss stitch, seed stitch, plain” The SNK test for the comparison of relaxation proc- esses revealed that the thickness of sam- ples differs significantly from each other. Figures 1-5 show the effects of fabric structure and the relaxation process on the weight, course/cm, wale/cm, stitch length and thickness of knitted fabric. Abrasion resistance In order to evaluate the resistance of the samples to abrasion, the fabrics were sub- jected to 100,000 rubs or until a hole oc- curs. Abrasion tests were performed for both faces of the fabrics. The weight loss percent of the fabrics were also measured every 5,000, 10,000, 20,000, 30,000 and 40,000th rubs. For washed fabrics, after 40,000 rubs, the highest value of weight loss was for moss stitch followed by seed stitch fabrics, tuck stitch fabrics “full cardigan, half cardigan and Lacoste”, and the technical face of plain fabric. In terry fabric, the weight loss percent was the least, but when the appearance of this fabric was visually evaluated, it was observed that terry fabric exhibited the worst surface characteristics. Figure 6 shows the effects of knit structure on the weight loss (in percent) of the fabrics. At the end of the test, the fabrics were ex- amined for the presence of a hole. Tuck stitch fabrics “half cardigan, full cardigan and Lacoste” have the lowest resistance to abrasion. (Table 6) The photos of these fabrics taken before and after the abra- sion test are presented in Figure 7. Pilling resistance Pilling tests were performed for both faces of the fabrics. A comparative study of the results reveals that links-links, seed stitch and moss stitch fabrics have the highest resistance to pilling (pilling rate: 5). In these samples, pill formation was not observed. Lacoste, full cardigan, Figure 1. Effects of fabric structure and relaxation process on the weight of knitted fabrics; all fabric codes by which the bar-graphs in Figures 1 - 5 are marked, are explained in Tables 5 and 6. Figure 2. Effects of fabric structure and relaxation process on the course per cm of knitted fabrics. Figure 3. Effects of fabric structure and relaxation process on the wales per cm of knitted fabrics. Figure 4. Effects of knit structure on loop length for dry relaxed fabrics. Figure 5. Effects of fabric structure and relaxation process on fabric thickness. Figure 1. Figure 2. Figure 3. Figure 4. Figure 5. 73FIBRES & TEXTILES in Eastern Europe April / June 2008, Vol. 16, No. 2 (67) fabrics. Moss stitch and half cardigan fabrics have weaker bursting strength performance. Half Milano, links-links and plain fabrics have the strongest burst- ing strength performance (Figure 8). Air permeability The results of the ANOVA for air perme- ability revealed that the effect of knit struc- ture is highly significant in washed fabrics. Moss stitch and full cardigan fabrics are the most permeable to air, and terry and Milano fabrics are the least (Figure 9). The most adequate choices from the studied knit structures for manufacturing garments for windy and cold winter periods are terry, Milano, half Milano and Lacoste. Bending behaviour The results of the ANOVA for wale and course way bending rigidity revealed that the effect of knit structure is highly significant in washed fabrics. Milano is the most rigid fabric in wale way bending. Single jersey structures have lower wale way bending rigidity. Terry is the most rigid fabric in course way bending. 2×2 rib fabric is the least rigid fabric in course way bending. (Figure 10). n Conclusions n The effect of knit structure and re- laxation processes on the dimensional properties of fabric is highly signifi- cant. Knit structure has the greatest effect. The effect of knit structure on bursting strength, air permeability, bending rigidity is highly significant in washed fabrics. n The fabric weight of the dry relaxed samples differs significantly from the wet relaxed and washed samples. The course per cm of the dry, wet and washed relaxed samples differs sig- Figure 6. Effects of knit structure on weight loss (%) for washed fabrics after 5,000, 10,000, 20,000, 30,000, 40,000 rubs (RL-R: technical face of plain knitted fabric; RL-L: technical back of plain knitted fabric). a) Lacoste b)Half Cardigan, c) Full Cardigan d) Terry fabric 1) 2) Figure 7. Effects of knit structure on abrasion resistance for washed fabrics (1)before and (2) after 40,000 rubs. Figure 8. Effects of knit structure on bursting strength for washed fabrics (fabric codes according to Tables 5 and 6). Figure 9. Effects of fabric structure on air permeability for washed fabrics (fabric codes according to Tables 5 and 6). half Milano, the technical back of plain fabric and 1x1 rib fabric have the low- est resistance to pilling (pilling rate: 3 - 4 and 4). Bursting strength The results of the ANOVA for bursting strength revealed that the effect of knit structure is highly significant in washed FIBRES & TEXTILES in Eastern Europe April / June 2008, Vol. 16, No. 2 (67)74 nificantly from each other. The wale per cm of the washed samples differs significantly from the dry and wet re- laxed samples. The order of thickness of the fabrics from big to small is terry, double jersey fabrics and single jersey fabrics. The order of loop length of the fabrics from big to small is terry, 1×1 Rib, seed stitch, moss stitch, half car- digan, full cardigan, 2×2 cable, 2×2 Rib, 3×3 cable, single jersey fabrics, and float stitch fabrics. n Tuck stitch fabrics have the lowest re- sistance to abrasion. For washed fab- rics, the highest value of weight loss is for moss stitch followed by seed stitch fabrics, and tuck stitch fabrics. Links- links, seed stitch, moss stitch fabrics have the highest resistance to pilling. Lacoste, full cardigan, half Milano, the technical back of plain fabric and 1×1 rib fabric have the lowest resist- ance to pilling. Moss stitch and half cardigan fabrics have weaker bursting strength performance. Half Milano, links-links, and plain fabrics have the strongest bursting strength perform- ance. Moss stitch and full cardigan fab- rics are the most permeable to air, and terry and Milano fabrics are the least. Milano is the most rigid fabric in wale way bending. Single jersey structures have lower wale way bending rigidity. Terry is the most rigid fabric in course way bending. 2×2 rib fabric is the least rigid fabric in course way bending. Acknowledgment We would like to thank Kaya Triko A.Ş., İstanbul, Turkey for their support during knitting operations and we would like to thank Assoc. Prof. Binnaz Meriç, University of Uludağ for their valuable assistance, and to Prof. Fatma Kalaoğlu, The Technical Uni- versity of İstanbul, Yeşim Tekstil Co.and Batı Dokuma, Co., Bursa, Turkey for their support during the tests. References 1. Chen P. L., Barker, R. L., Smith, G. W., at al., Handle of Weft Knit Fabrics, Textile Res. J., 1992, 62(4), p.200-211. 2. Eckert, C., Stacey, M., Sources of Inspi- ration in Industrial Practice. The Case of Knitwear Design. The Journal of Design Research, 2003, 3(1). 3. Fan, J., Hunter, L., A Worsted Fabric Expert System. Part I. System Develop- ment, Textile Res. J., 1998, 68(9), pp. 680-686. 4. Chen Y., Collier, B. J., Characterizing Fabric End Use by Fabric Physical Pro- perties, Textile Res. J., 1997, 67(4), pp. 247-252. 5. Fuchs, H., Magel, M., Offermann, P., Raue, P., Seifert, R., Surface Characte- rization of Textile Fabrics, Part I, Melliand Textilber., 1993, E13, p. 6. Berkalp, Ö. B., Pourdeyhimi, B., Seyam, A., Holmes, R. Texture Retention After Fabric-to-Fabric Abrasion, Textile Res. J., 2003, 73, pp. 316-321. 7. Candan, C., Önal, L., Dimensional, Pilling And Abrasion Properties of Weft Knits Made From Open-End and Ring Spun Yarns, Textile Res. J., 2002, 72(2), pp. 164-169. 8. Kavuşturan Y., The Effects of Some Knit Structures on the Fabric Properties in Acrylic Weft Knitted Outerwear Fabrics, Tekstil Maraton, 2002, pp. 40-46. 9. Nergis, B. U., Candan, C., Performance of Boucle Yarns in Various Knitted Fabric Structures, Textile Res. J., 2006, 76(1), pp. 49-56. 10. Rangulam, R. B., Amirbayat, J., and Porat I., The Objective Assessment of Fabric Pilling Part I: Methodology, J.Textile Inst., 1993, 84, pp. 221-226. 11. Ukponmwan J. O., Mukhopadhyay, A., Chatterjee, K. N., Pilling, Textile Progress, 1998, 28(3), pp.1-57. 12. Candan, C., Factors Affecting the Pilling Performance of Knitted Wool Fabrics, Turkish Journal of Engineering & Envi- ronmental Sciences, 2000, 24(1), pp. 35-44. 13. Ertugrul, S., Ucar, N., Predicting Bursting Strength of Cotton Plain Knitted Fabrics Using Intelligent Techniques, Textile Res. J., 2000, 70(10), pp. 845-851. 14. Dubrovski, P. D., The Influence of Fabric Structure on Air Permeability, Proc. 2nd International Textile, Clothing & Design Conference, 2004. 15. Olsauskiene, A., Milasıus R., Integrated Fabric Firmness Factor as a Criterion of Air Permeability Designing. Proc. 2nd International Textile Clothing & Design Conference, 2004. 16. Çeken, F., An İnvestigation About Air Permeability of Wool/Polyester and Wool/Acrylic Knitted Fabrics., Tekstil ve Konfeksiyon, 1997, 2, pp.111-115. 17. Peirce, F. T., The Handle of Cloth as a Measurable Quantity, J.Textile Inst., 1930, 21, pp. T377-416. 18. Clapp, T. G., Peng, H., Ghosh, T. K., In- direct Measurement of The Moment-Cu- rvature Relationship For Fabrics, Textile Res. J., 1990, 60(8), pp. 525-533. 19. Choi, M., Ashdown, S., Effect of Chan- ges in Knit Structure and Density on the Mechanical and Hand Properties of Weft Knitted Fabrics for Outerwear, Textile Res. J., 2000, 70(12), p.1033-1045. 20. Alimaa, D., Matsuo, T., Nakajima, M., Takahashi, M., Sensory Measurements of the Main Mechanical Parameters of Knitted Fabrics, Textile Res. J., 2000, 70(11), pp. 985-990. 21. Karba, M., Gersak, J., Stjepanovic, Z., The Influence of Knitting Parameters on Dimensional Changes of Knitted Fabrics in the Process of Relaxation, Proc. 2nd International Textile Clothing & Design Conference, 2004, pp. 200-205. 22. Candan, C., Önal, L., Contribution of Fabric Characteristics and Laundering to Shrinkage of Weft Knitted Fabrics. Textile Res. J., 2003, 73(3), pp. 187-191. 23. Emirhanova N., Effects of Knit Structure on the Dimensional and Physical Pro- perties of Flat Knitted Fabrics, Masters Thesis, The University of Uludag, Bursa- Turkey, 2003. 24. Postle, R., Dimensional Stability of Plain Knitted Fabrics, J.Textile Inst., 1968, 59, pp. 65-77. 25. Kurbak, A. Some Effects of Substituting a Presser Foot for Take Down Tension in Weft Knitting, Doctoral Thesis, The University of Leeds, UK, 1983. 26. Smirfitt, J. A., Worsted 1×1 Rib Fabrics Part I Dimensional Properties, J.Textile Inst., 1965, 56, pp. 248-256. 27. Munden, D. L., Dimensional Stability of Plain Knit Fabrics, J. Textile Inst., 1960, 51, pp. 200-209. 28. Ceken, F., Göktepe, Ö., Comparison of the Properties of Knitted Fabrics Produ- ced by Conventional and Compact Ring- Spun Yarns, Fibres & Textiles in Eastern Europe, 2005, Vol. 13 (1) pp. 47-50. Received 02.10.2006 Reviewed 08.05.2007 Figure 10. Effects of fabric structure on wale way and course way bending rigidity for washed fabrics (fabric codes according to Tables 5 and 6).
File đính kèm:
effects_of_knit_structure_on_the_dimensional_and_physical_pr.pdf