Design and fabrication of a soft robotic gripperfor object picking
Trong bài báo này, tác giả đề xuất một mô hình tay kẹp rô bốt mềm được
làm bằng vật liệu cao su đàn hồi có thể gắp được đồ vật khác nhau. Tay kẹp bao
gồm ba ngón mềm đặt đều nhau trên bề mặt hình nón cụt, ngón được làm bằng
phương pháp đúc và thiết kế của ngón được thừa hưởng từ "Pneunets bending
actuator" của bộ công cụ robot mềm. Bài báo đưa ra các thông số kích thước mô
hình ngón tay mềm, mô phỏng phần tử hữu hạn được thực hiện để xác nhận
thiết kế ngón tay. Ngoài ra, quy trình chế tạo ngón tay mềm được giới thiệu cùng
với mạch dẫn động và mạch điều khiển để thực hiện thao tác đóng - mở kẹp gắp
mềm. Các thí nghiệm được thực hiện để đánh giá độ đàn hồi của ngón tay ở các
áp suất và lực kẹp khác nhau cần thiết để xử lý các vật có kích thước và vật liệu
khác nhau. Thí nghiệm chỉ ra rằng, thiết kế tay kẹp mềm có thể ứng dụng tốt cho
robot gắp vật dạng mềm.
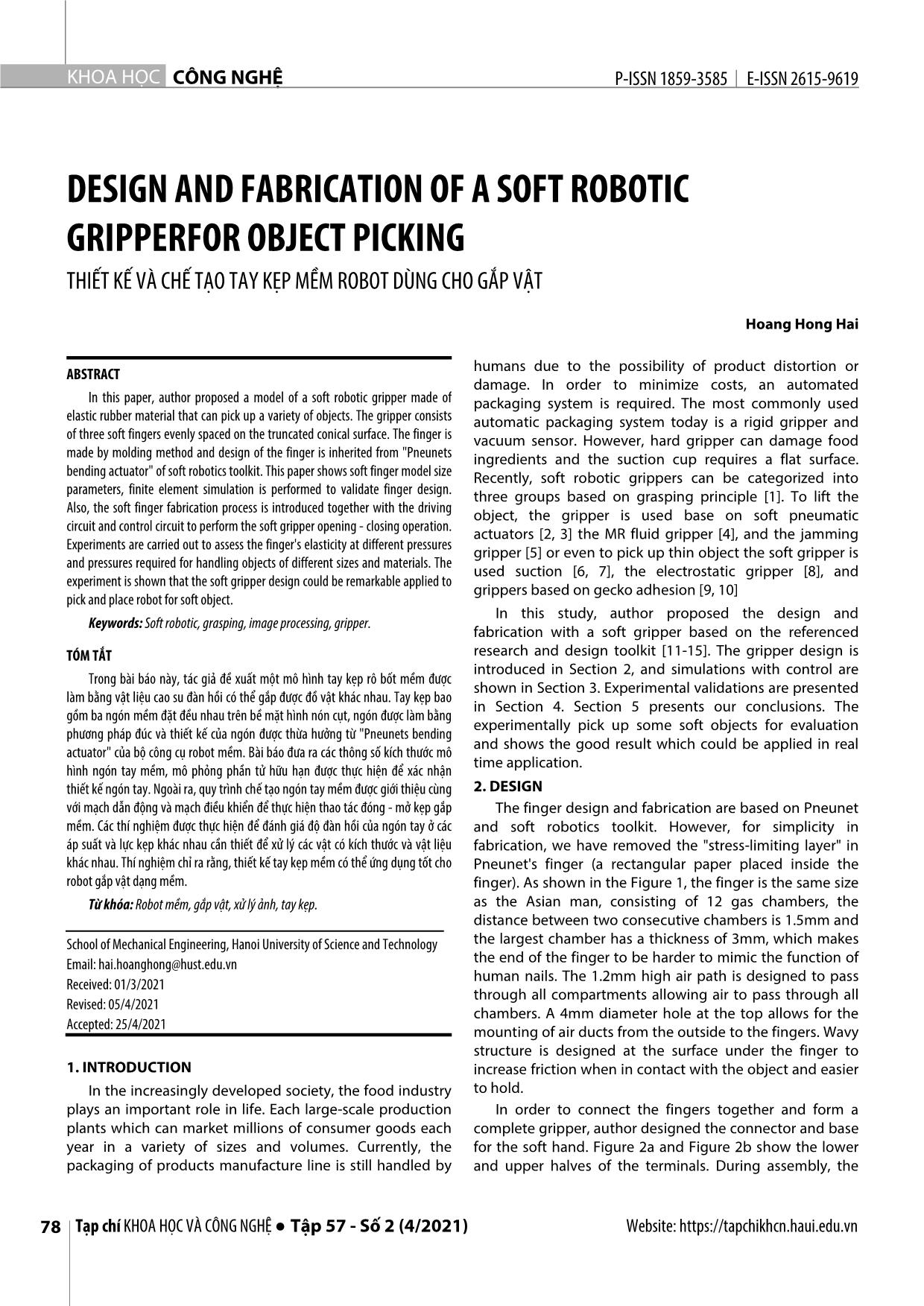
Trang 1
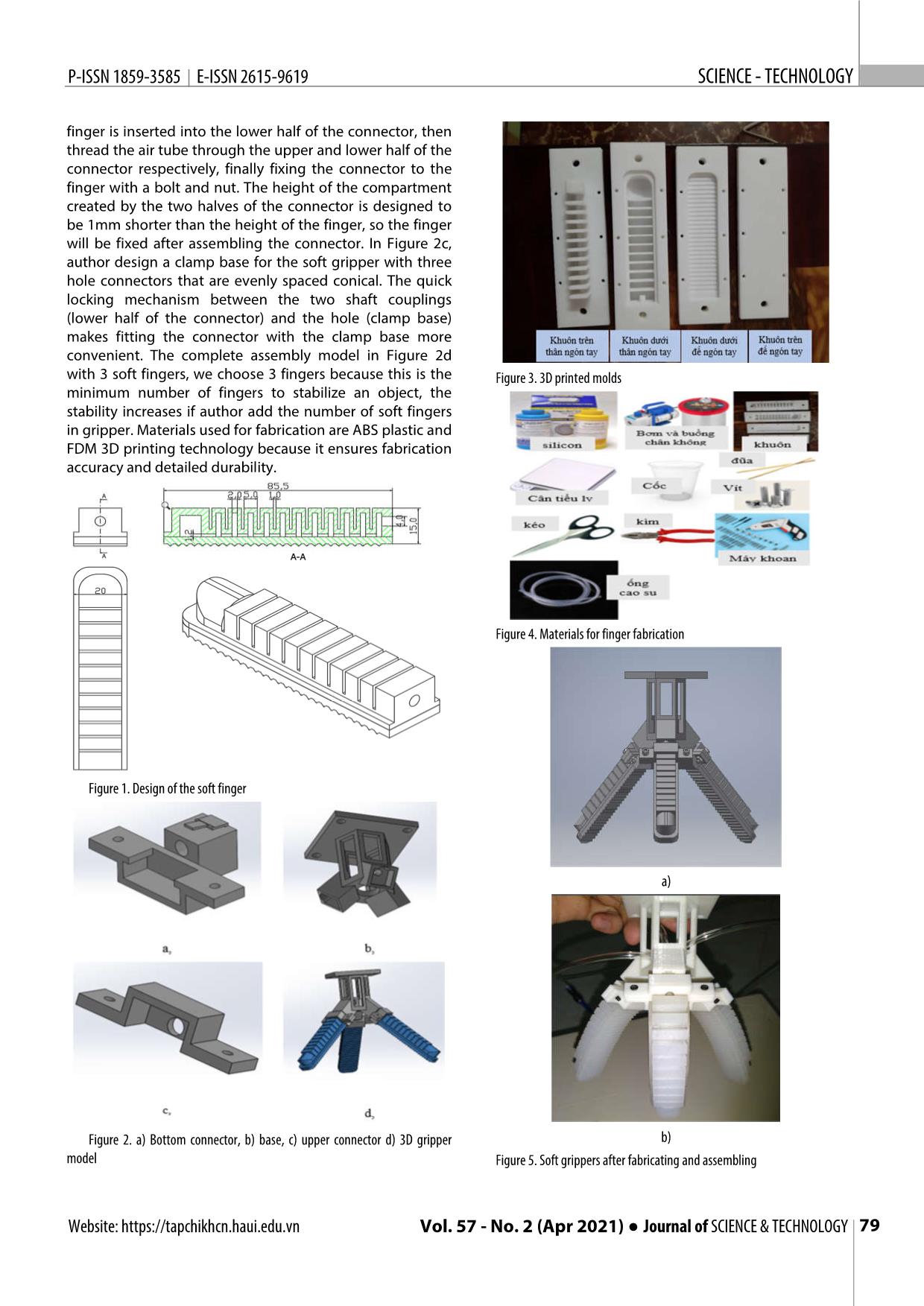
Trang 2
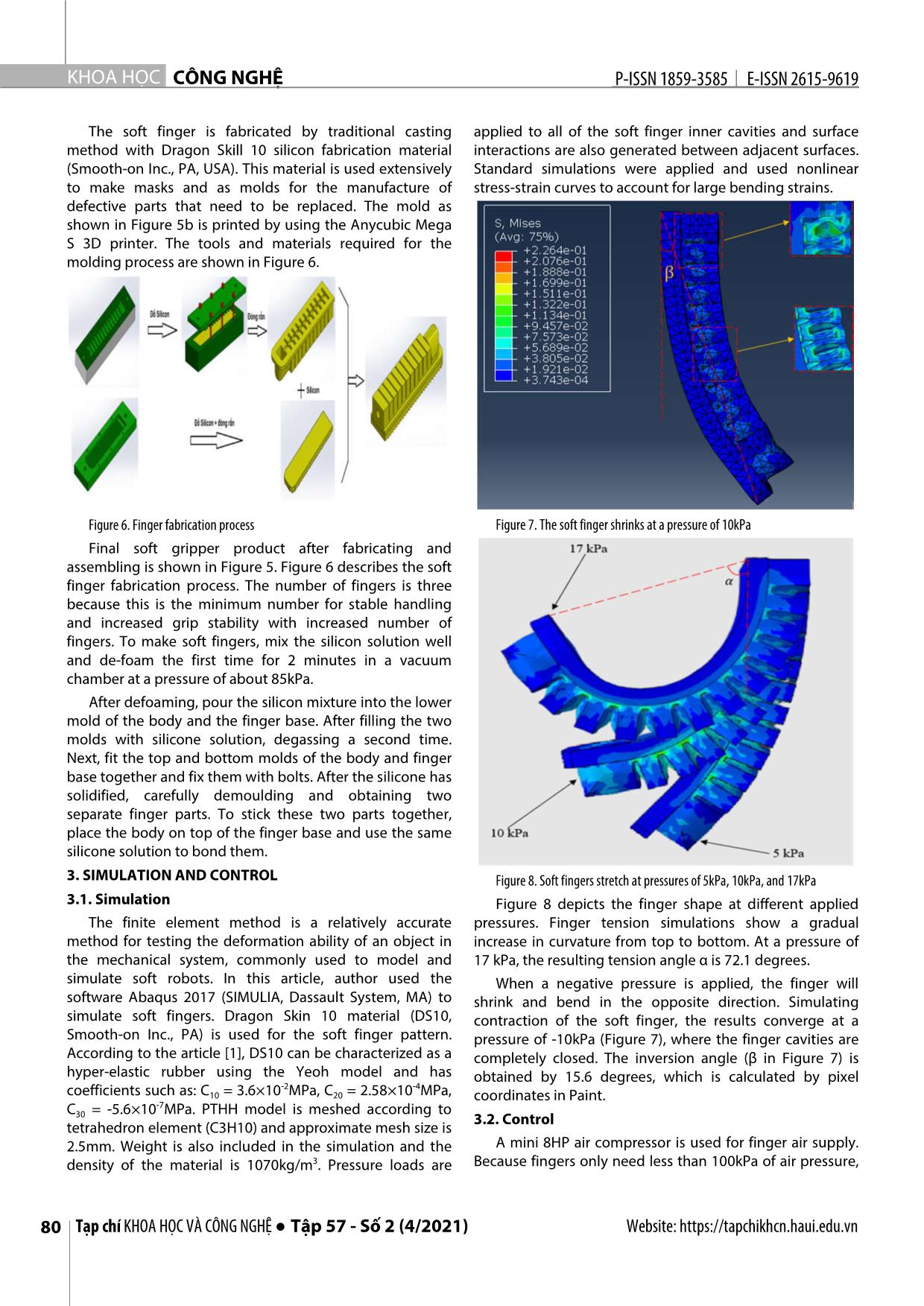
Trang 3
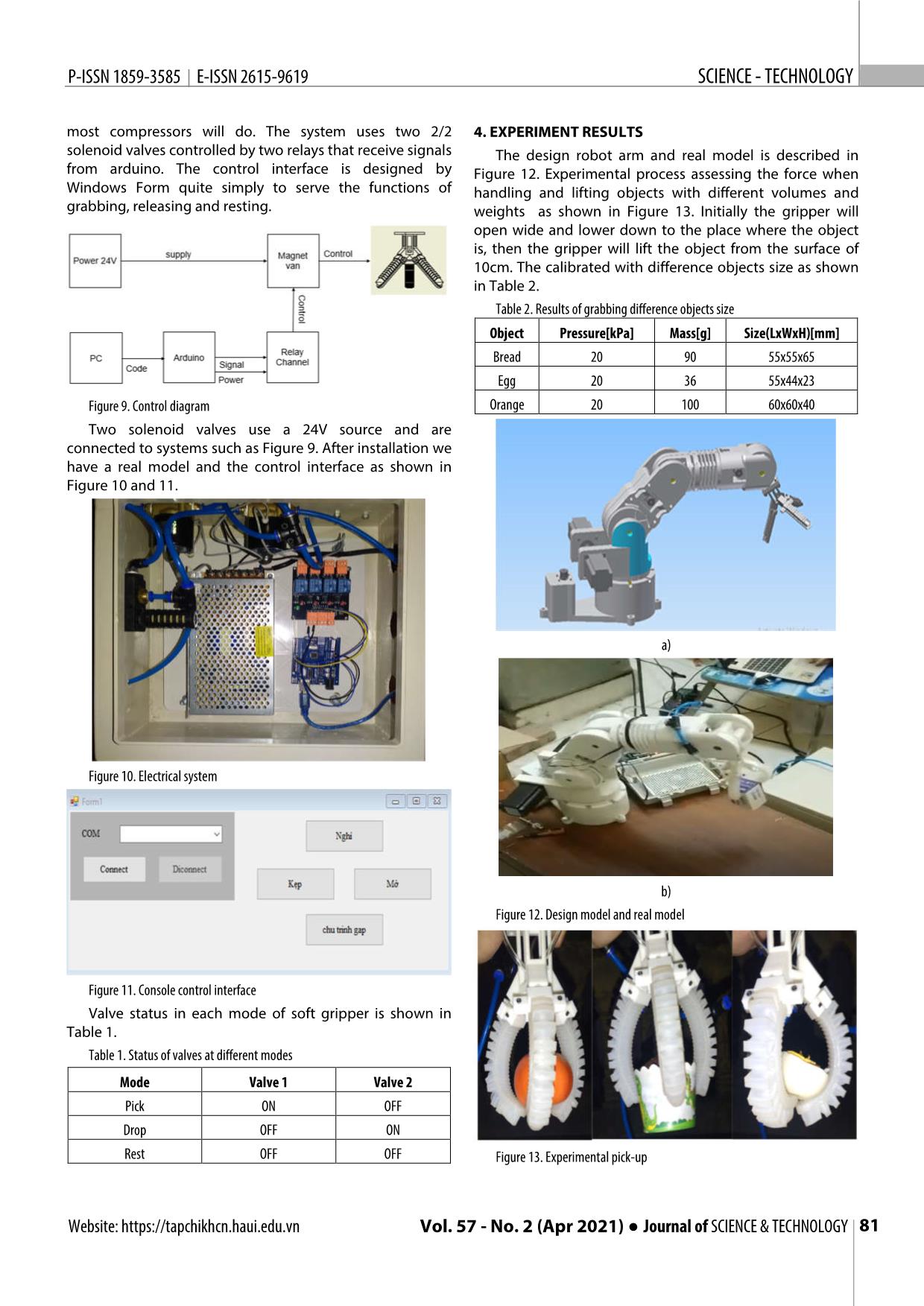
Trang 4
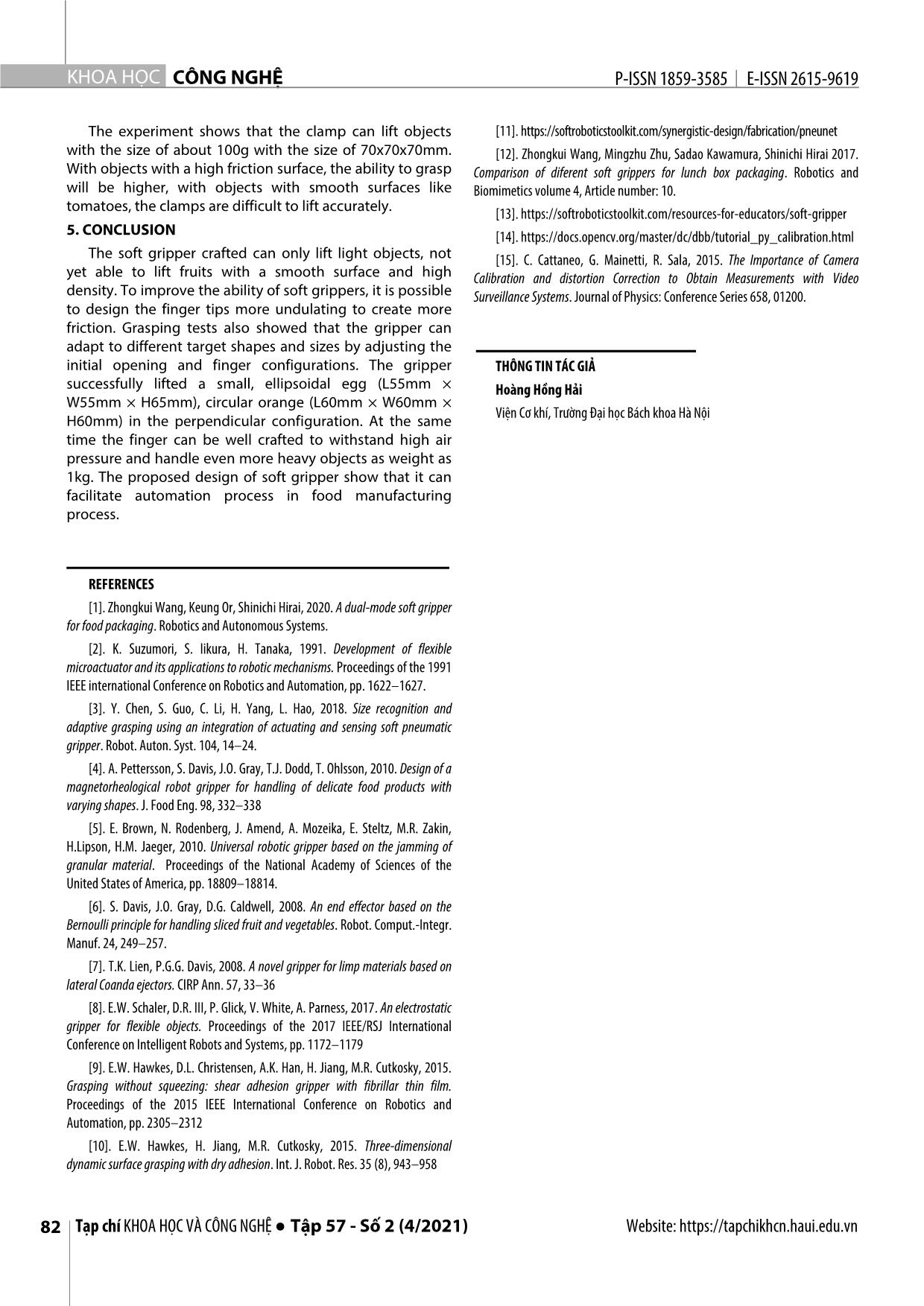
Trang 5
Tóm tắt nội dung tài liệu: Design and fabrication of a soft robotic gripperfor object picking
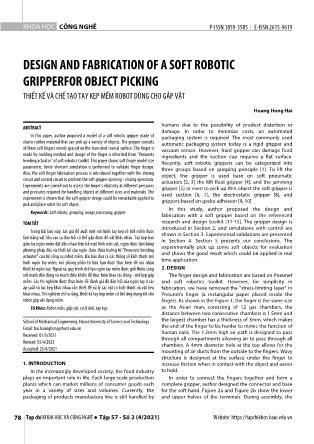
CÔNG NGHỆ Tạp chí KHOA HỌC VÀ CÔNG NGHỆ ● Tập 57 - Số 2 (4/2021) Website: https://tapchikhcn.haui.edu.vn 78 KHOA HỌC P-ISSN 1859-3585 E-ISSN 2615-9619 DESIGN AND FABRICATION OF A SOFT ROBOTIC GRIPPERFOR OBJECT PICKING THIẾT KẾ VÀ CHẾ TẠO TAY KẸP MỀM ROBOT DÙNG CHO GẮP VẬT Hoang Hong Hai ABSTRACT In this paper, author proposed a model of a soft robotic gripper made of elastic rubber material that can pick up a variety of objects. The gripper consists of three soft fingers evenly spaced on the truncated conical surface. The finger is made by molding method and design of the finger is inherited from "Pneunets bending actuator" of soft robotics toolkit. This paper shows soft finger model size parameters, finite element simulation is performed to validate finger design. Also, the soft finger fabrication process is introduced together with the driving circuit and control circuit to perform the soft gripper opening - closing operation. Experiments are carried out to assess the finger's elasticity at different pressures and pressures required for handling objects of different sizes and materials. The experiment is shown that the soft gripper design could be remarkable applied to pick and place robot for soft object. Keywords: Soft robotic, grasping, image processing, gripper. TÓM TẮT Trong bài báo này, tác giả đề xuất một mô hình tay kẹp rô bốt mềm được làm bằng vật liệu cao su đàn hồi có thể gắp được đồ vật khác nhau. Tay kẹp bao gồm ba ngón mềm đặt đều nhau trên bề mặt hình nón cụt, ngón được làm bằng phương pháp đúc và thiết kế của ngón được thừa hưởng từ "Pneunets bending actuator" của bộ công cụ robot mềm. Bài báo đưa ra các thông số kích thước mô hình ngón tay mềm, mô phỏng phần tử hữu hạn được thực hiện để xác nhận thiết kế ngón tay. Ngoài ra, quy trình chế tạo ngón tay mềm được giới thiệu cùng với mạch dẫn động và mạch điều khiển để thực hiện thao tác đóng - mở kẹp gắp mềm. Các thí nghiệm được thực hiện để đánh giá độ đàn hồi của ngón tay ở các áp suất và lực kẹp khác nhau cần thiết để xử lý các vật có kích thước và vật liệu khác nhau. Thí nghiệm chỉ ra rằng, thiết kế tay kẹp mềm có thể ứng dụng tốt cho robot gắp vật dạng mềm. Từ khóa: Robot mềm, gắp vật, xử lý ảnh, tay kẹp. School of Mechanical Engineering, Hanoi University of Science and Technology Email: hai.hoanghong@hust.edu.vn Received: 01/3/2021 Revised: 05/4/2021 Accepted: 25/4/2021 1. INTRODUCTION In the increasingly developed society, the food industry plays an important role in life. Each large-scale production plants which can market millions of consumer goods each year in a variety of sizes and volumes. Currently, the packaging of products manufacture line is still handled by humans due to the possibility of product distortion or damage. In order to minimize costs, an automated packaging system is required. The most commonly used automatic packaging system today is a rigid gripper and vacuum sensor. However, hard gripper can damage food ingredients and the suction cup requires a flat surface. Recently, soft robotic grippers can be categorized into three groups based on grasping principle [1]. To lift the object, the gripper is used base on soft pneumatic actuators [2, 3] the MR fluid gripper [4], and the jamming gripper [5] or even to pick up thin object the soft gripper is used suction [6, 7], the electrostatic gripper [8], and grippers based on gecko adhesion [9, 10] In this study, author proposed the design and fabrication with a soft gripper based on the referenced research and design toolkit [11-15]. The gripper design is introduced in Section 2, and simulations with control are shown in Section 3. Experimental validations are presented in Section 4. Section 5 presents our conclusions. The experimentally pick up some soft objects for evaluation and shows the good result which could be applied in real time application. 2. DESIGN The finger design and fabrication are based on Pneunet and soft robotics toolkit. However, for simplicity in fabrication, we have removed the "stress-limiting layer" in Pneunet's finger (a rectangular paper placed inside the finger). As shown in the Figure 1, the finger is the same size as the Asian man, consisting of 12 gas chambers, the distance between two consecutive chambers is 1.5mm and the largest chamber has a thickness of 3mm, which makes the end of the finger to be harder to mimic the function of human nails. The 1.2mm high air path is designed to pass through all compartments allowing air to pass through all chambers. A 4mm diameter hole at the top allows for the mounting of air ducts from the outside to the fingers. Wavy structure is designed at the surface under the finger to increase friction when in contact with the object and easier to hold. In order to connect the fingers together and form a complete gripper, author designed the connector and base for the soft hand. Figure 2a and Figure 2b show the lower and upper halves of the terminals. During assembly, the P-ISSN 1859-3585 E-ISSN 2615-9619 SCIENCE - TECHNOLOGY Website: https://tapchikhcn.haui.edu.vn Vol. 57 - No. 2 (Apr 2021) ● Journal of SCIENCE & TECHNOLOGY 79 finger is inserted into the lower half of the connector, then thread the air tube through the upper and lower half of the connector respectively, finally fixing the connector to the finger with a bolt and nut. The height of the compartment created by the two halves of the connector is designed to be 1mm shorter than the height of the finger, so the finger will be fixed after assembling the connector. In Figure 2c, author design a clamp base for the soft gripper with three hole connectors that are evenly spaced conical. The quick locking mechanism between the two shaft couplings (lower half of the connector) and the hole (clamp base) makes fitting the connector with the clamp base more convenient. The complete assembly model in Figure 2d with 3 soft fingers, we choose 3 fingers because this is the minimum number of fingers to stabilize an object, the stability increases if author add the number of soft fingers in gripper. Materials used for fabrication are ABS plastic and FDM 3D printing technology because it ensures fabrication accuracy and detailed durability. Figure 1. Design of the soft finger Figure 2. a) Bottom connector, b) base, c) upper connector d) 3D gripper model Figure 3. 3D printed molds Figure 4. Materials for finger fabrication a) b) Figure 5. Soft grippers after fabricating and assembling CÔNG NGHỆ Tạp chí KHOA HỌC VÀ CÔNG NGHỆ ● Tập 57 - Số 2 (4/2021) Website: https://tapchikhcn.haui.edu.vn 80 KHOA HỌC P-ISSN 1859-3585 E-ISSN 2615-9619 The soft finger is fabricated by traditional casting method with Dragon Skill 10 silicon fabrication material (Smooth-on Inc., PA, USA). This material is used extensively to make masks and as molds for the manufacture of defective parts that need to be replaced. The mold as shown in Figure 5b is printed by using the Anycubic Mega S 3D printer. The tools and materials required for the molding process are shown in Figure 6. Figure 6. Finger fabrication process Final soft gripper product after fabricating and assembling is shown in Figure 5. Figure 6 describes the soft finger fabrication process. The number of fingers is three because this is the minimum number for stable handling and increased grip stability with increased number of fingers. To make soft fingers, mix the silicon solution well and de-foam the first time for 2 minutes in a vacuum chamber at a pressure of about 85kPa. After defoaming, pour the silicon mixture into the lower mold of the body and the finger base. After filling the two molds with silicone solution, degassing a second time. Next, fit the top and bottom molds of the body and finger base together and fix them with bolts. After the silicone has solidified, carefully demoulding and obtaining two separate finger parts. To stick these two parts together, place the body on top of the finger base and use the same silicone solution to bond them. 3. SIMULATION AND CONTROL 3.1. Simulation The finite element method is a relatively accurate method for testing the deformation ability of an object in the mechanical system, commonly used to model and simulate soft robots. In this article, author used the software Abaqus 2017 (SIMULIA, Dassault System, MA) to simulate soft fingers. Dragon Skin 10 material (DS10, Smooth-on Inc., PA) is used for the soft finger pattern. According to the article [1], DS10 can be characterized as a hyper-elastic rubber using the Yeoh model and has coefficients such as: C10 = 3.6×10-2MPa, C20 = 2.58×10-4MPa, C30 = -5.6×10-7MPa. PTHH model is meshed according to tetrahedron element (C3H10) and approximate mesh size is 2.5mm. Weight is also included in the simulation and the density of the material is 1070kg/m3. Pressure loads are applied to all of the soft finger inner cavities and surface interactions are also generated between adjacent surfaces. Standard simulations were applied and used nonlinear stress-strain curves to account for large bending strains. Figure 7. The soft finger shrinks at a pressure of 10kPa Figure 8. Soft fingers stretch at pressures of 5kPa, 10kPa, and 17kPa Figure 8 depicts the finger shape at different applied pressures. Finger tension simulations show a gradual increase in curvature from top to bottom. At a pressure of 17 kPa, the resulting tension angle α is 72.1 degrees. When a negative pressure is applied, the finger will shrink and bend in the opposite direction. Simulating contraction of the soft finger, the results converge at a pressure of -10kPa (Figure 7), where the finger cavities are completely closed. The inversion angle (β in Figure 7) is obtained by 15.6 degrees, which is calculated by pixel coordinates in Paint. 3.2. Control A mini 8HP air compressor is used for finger air supply. Because fingers only need less than 100kPa of air pressure, P-ISSN 1859-3585 E-ISSN 2615-9619 SCIENCE - TECHNOLOGY Website: https://tapchikhcn.haui.edu.vn Vol. 57 - No. 2 (Apr 2021) ● Journal of SCIENCE & TECHNOLOGY 81 most compressors will do. The system uses two 2/2 solenoid valves controlled by two relays that receive signals from arduino. The control interface is designed by Windows Form quite simply to serve the functions of grabbing, releasing and resting. Figure 9. Control diagram Two solenoid valves use a 24V source and are connected to systems such as Figure 9. After installation we have a real model and the control interface as shown in Figure 10 and 11. Figure 10. Electrical system Figure 11. Console control interface Valve status in each mode of soft gripper is shown in Table 1. Table 1. Status of valves at different modes Mode Valve 1 Valve 2 Pick ON OFF Drop OFF ON Rest OFF OFF 4. EXPERIMENT RESULTS The design robot arm and real model is described in Figure 12. Experimental process assessing the force when handling and lifting objects with different volumes and weights as shown in Figure 13. Initially the gripper will open wide and lower down to the place where the object is, then the gripper will lift the object from the surface of 10cm. The calibrated with difference objects size as shown in Table 2. Table 2. Results of grabbing difference objects size Object Pressure[kPa] Mass[g] Size(LxWxH)[mm] Bread 20 90 55x55x65 Egg 20 36 55x44x23 Orange 20 100 60x60x40 a) b) Figure 12. Design model and real model Figure 13. Experimental pick-up CÔNG NGHỆ Tạp chí KHOA HỌC VÀ CÔNG NGHỆ ● Tập 57 - Số 2 (4/2021) Website: https://tapchikhcn.haui.edu.vn 82 KHOA HỌC P-ISSN 1859-3585 E-ISSN 2615-9619 The experiment shows that the clamp can lift objects with the size of about 100g with the size of 70x70x70mm. With objects with a high friction surface, the ability to grasp will be higher, with objects with smooth surfaces like tomatoes, the clamps are difficult to lift accurately. 5. CONCLUSION The soft gripper crafted can only lift light objects, not yet able to lift fruits with a smooth surface and high density. To improve the ability of soft grippers, it is possible to design the finger tips more undulating to create more friction. Grasping tests also showed that the gripper can adapt to different target shapes and sizes by adjusting the initial opening and finger configurations. The gripper successfully lifted a small, ellipsoidal egg (L55mm × W55mm × H65mm), circular orange (L60mm × W60mm × H60mm) in the perpendicular configuration. At the same time the finger can be well crafted to withstand high air pressure and handle even more heavy objects as weight as 1kg. The proposed design of soft gripper show that it can facilitate automation process in food manufacturing process. REFERENCES [1]. Zhongkui Wang, Keung Or, Shinichi Hirai, 2020. A dual-mode soft gripper for food packaging. Robotics and Autonomous Systems. [2]. K. Suzumori, S. Iikura, H. Tanaka, 1991. Development of flexible microactuator and its applications to robotic mechanisms. Proceedings of the 1991 IEEE international Conference on Robotics and Automation, pp. 1622–1627. [3]. Y. Chen, S. Guo, C. Li, H. Yang, L. Hao, 2018. Size recognition and adaptive grasping using an integration of actuating and sensing soft pneumatic gripper. Robot. Auton. Syst. 104, 14–24. [4]. A. Pettersson, S. Davis, J.O. Gray, T.J. Dodd, T. Ohlsson, 2010. Design of a magnetorheological robot gripper for handling of delicate food products with varying shapes. J. Food Eng. 98, 332–338 [5]. E. Brown, N. Rodenberg, J. Amend, A. Mozeika, E. Steltz, M.R. Zakin, H.Lipson, H.M. Jaeger, 2010. Universal robotic gripper based on the jamming of granular material. Proceedings of the National Academy of Sciences of the United States of America, pp. 18809–18814. [6]. S. Davis, J.O. Gray, D.G. Caldwell, 2008. An end effector based on the Bernoulli principle for handling sliced fruit and vegetables. Robot. Comput.-Integr. Manuf. 24, 249–257. [7]. T.K. Lien, P.G.G. Davis, 2008. A novel gripper for limp materials based on lateral Coanda ejectors. CIRP Ann. 57, 33–36 [8]. E.W. Schaler, D.R. III, P. Glick, V. White, A. Parness, 2017. An electrostatic gripper for flexible objects. Proceedings of the 2017 IEEE/RSJ International Conference on Intelligent Robots and Systems, pp. 1172–1179 [9]. E.W. Hawkes, D.L. Christensen, A.K. Han, H. Jiang, M.R. Cutkosky, 2015. Grasping without squeezing: shear adhesion gripper with fibrillar thin film. Proceedings of the 2015 IEEE International Conference on Robotics and Automation, pp. 2305–2312 [10]. E.W. Hawkes, H. Jiang, M.R. Cutkosky, 2015. Three-dimensional dynamic surface grasping with dry adhesion. Int. J. Robot. Res. 35 (8), 943–958 [11]. https://softroboticstoolkit.com/synergistic-design/fabrication/pneunet [12]. Zhongkui Wang, Mingzhu Zhu, Sadao Kawamura, Shinichi Hirai 2017. Comparison of diferent soft grippers for lunch box packaging. Robotics and Biomimetics volume 4, Article number: 10. [13]. https://softroboticstoolkit.com/resources-for-educators/soft-gripper [14]. https://docs.opencv.org/master/dc/dbb/tutorial_py_calibration.html [15]. C. Cattaneo, G. Mainetti, R. Sala, 2015. The Importance of Camera Calibration and distortion Correction to Obtain Measurements with Video Surveillance Systems. Journal of Physics: Conference Series 658, 01200. THÔNG TIN TÁC GIẢ Hoàng Hồng Hải Viện Cơ khí, Trường Đại học Bách khoa Hà Nội
File đính kèm:
design_and_fabrication_of_a_soft_robotic_gripperfor_object_p.pdf