Chế tạo lớp phủ cứng tin bằng phương pháp hồ quang Catot, ứng dụng trên khuôn đúc áp lực hợp kim nhôm để sản xuất chi tiết vòng ôm
Trong khuôn đúc áp lực hợp kim nhôm, các chi tiết chốt tạo lỗ cho sản phẩm có tốc độ hỏng nhanh gấp 10 lần khuôn. Tác động của vận tốc dòng chảy lớn, nhiệt độ kim loại lỏng và áp lực đúc cao là các nguyên nhân chính gây phá huỷ bề mặt chốt như xói mòn, dính bám nhôm. Các tác động này làm giảm chất lượng vật
đúc và tăng chi phí sản xuất đúc. Lớp phủ cứng trên cơ sở nitrit có tác dụng bảo vệ bề mặt thép khuôn chống lại xói mòn, dính bám nhôm và hạn chế mỏi nhiệt. Bài báo trình bày công nghệ chế tạo lớp phủ TiN lên nền khuôn từ thép SKD61 bằng phương pháp hồ quang catot. Kết quả đạt được lớp phủ TiN có chiều dày 1,52 µm, hợp thức xấp xỉ 1:1; số lượng hạt macro kích thước rất lớn (915 µm) trên bề mặt ít. Khi sử
dụng chi tiết khuôn đúc áp lực có phủ TiN để đúc chi tiết máy từ hợp kim nhôm dụng lõi/ chốt khuôn không phủ TiN. Lớp phủ TiN chế tạo được có độ cứng cao, hệ số ma sát nhỏ, giảm dính bám nhôm và có khả năng làm việc ở 7000C trong điều kiện sản xuất.
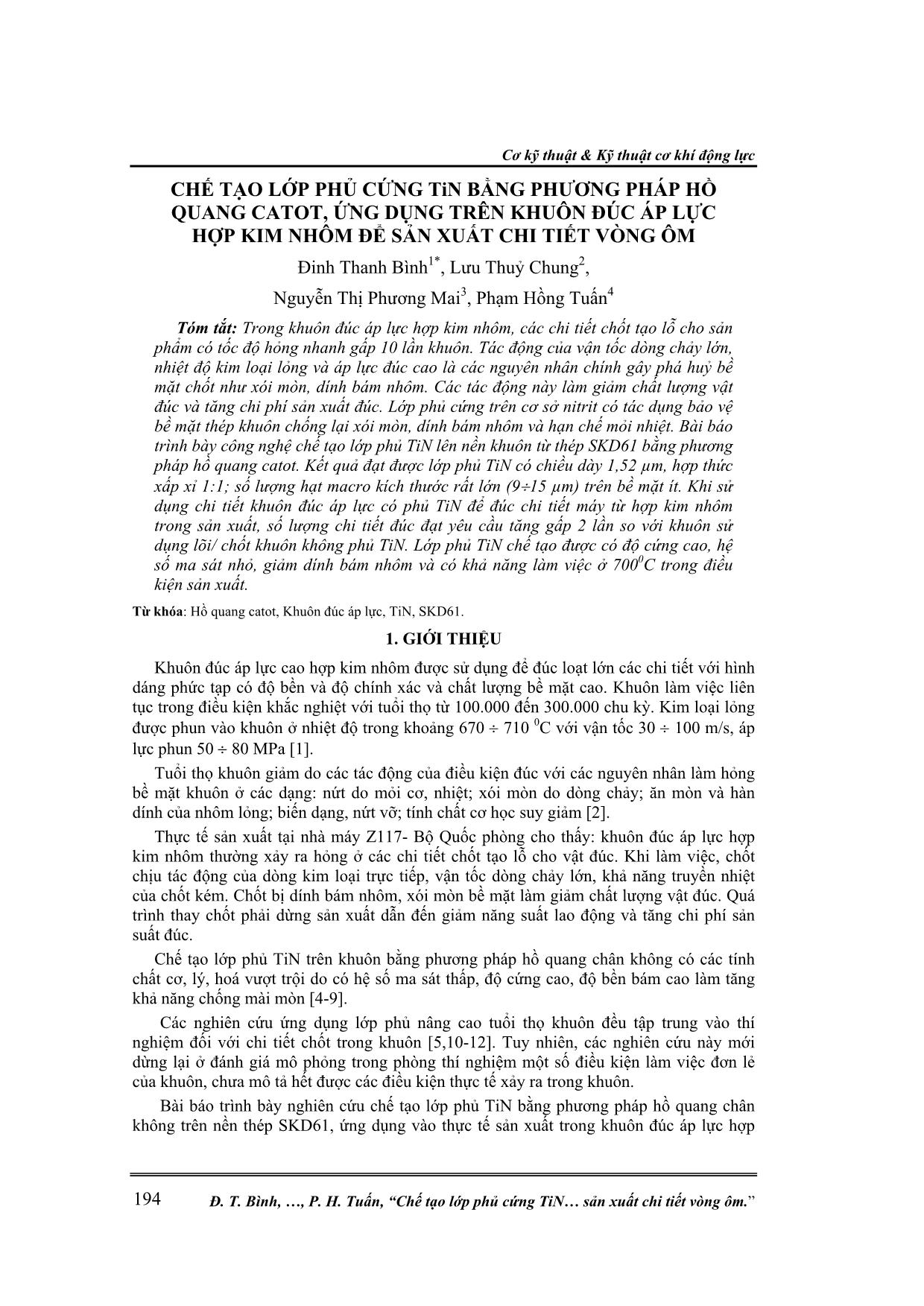
Trang 1
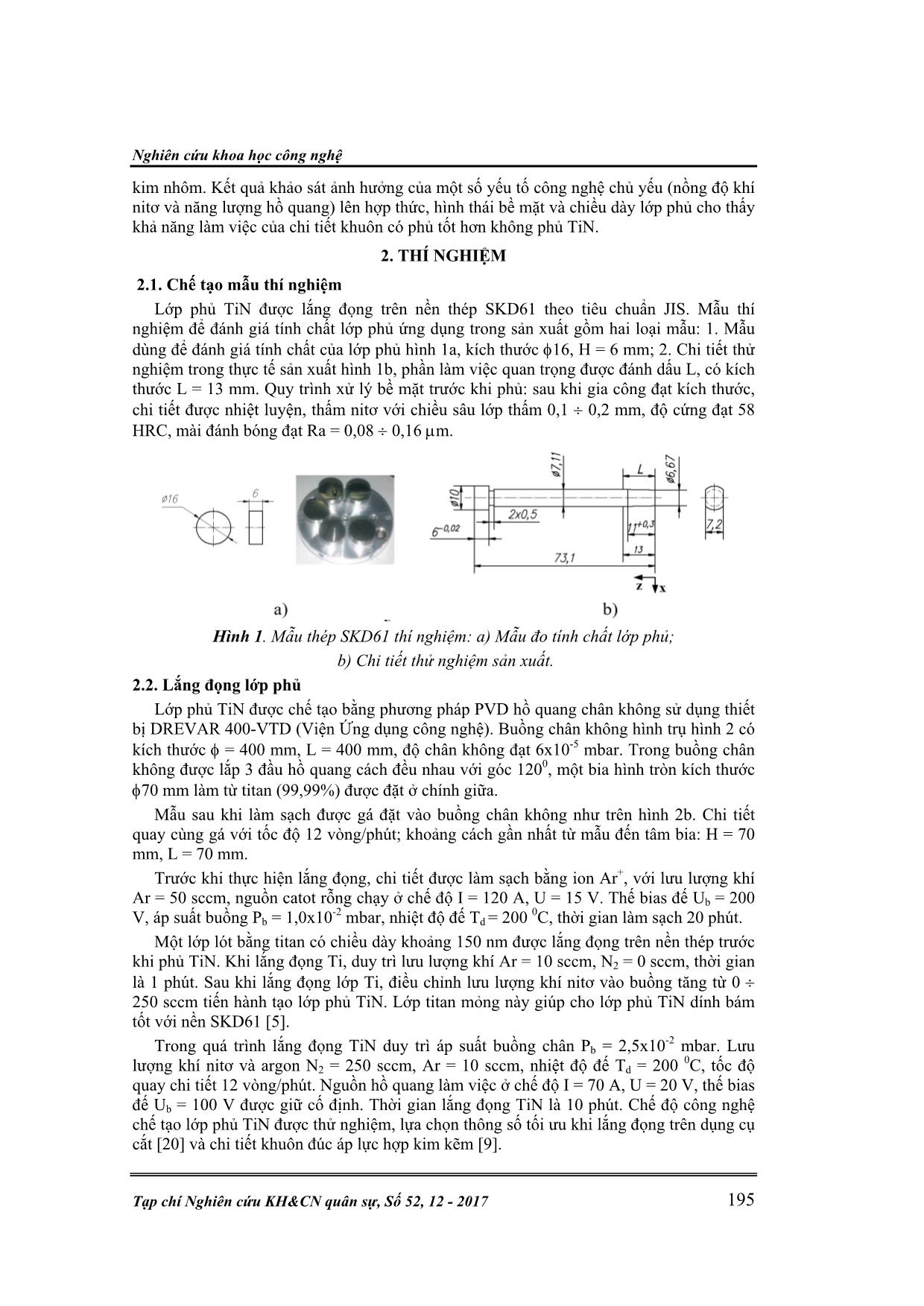
Trang 2
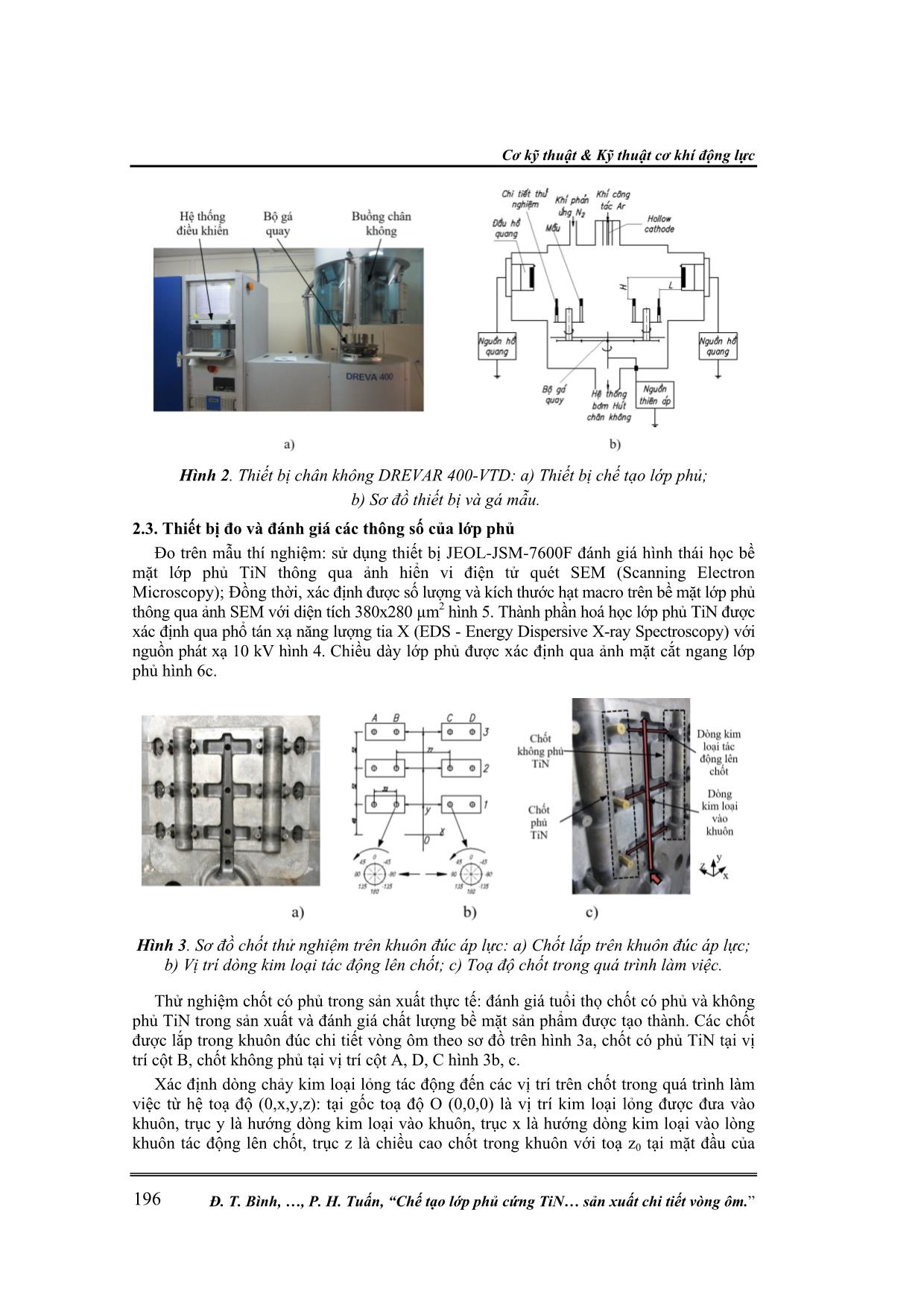
Trang 3
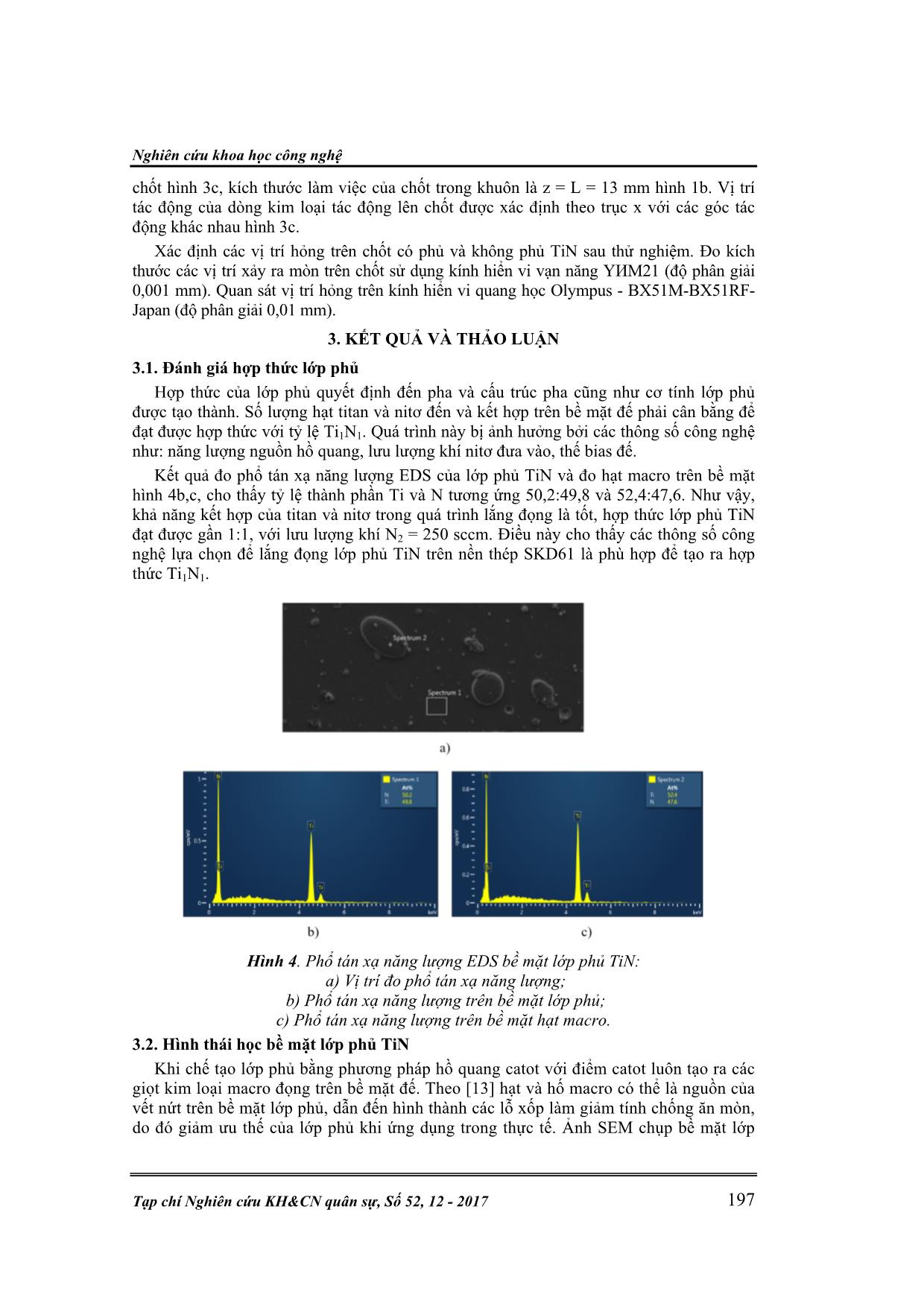
Trang 4
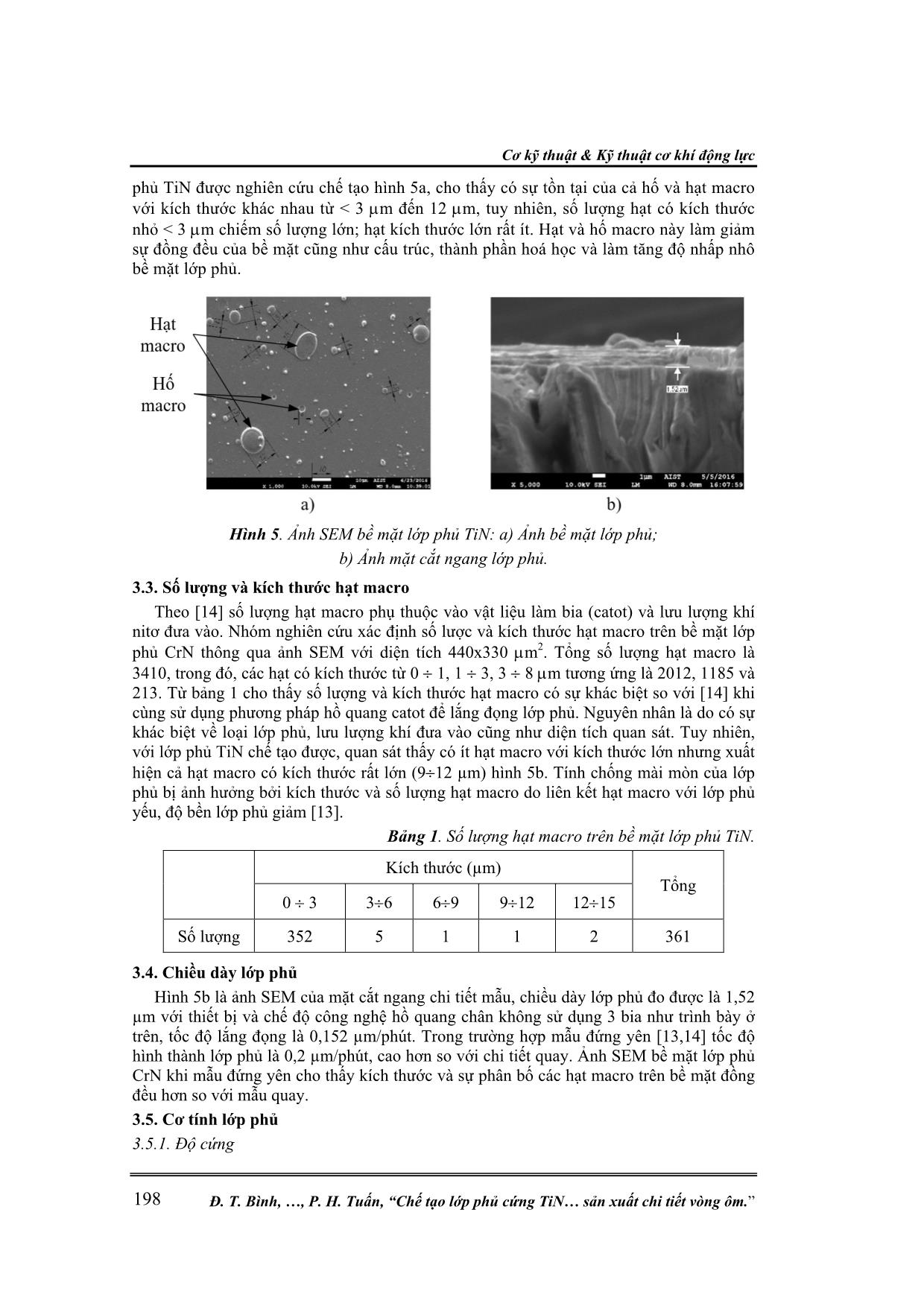
Trang 5
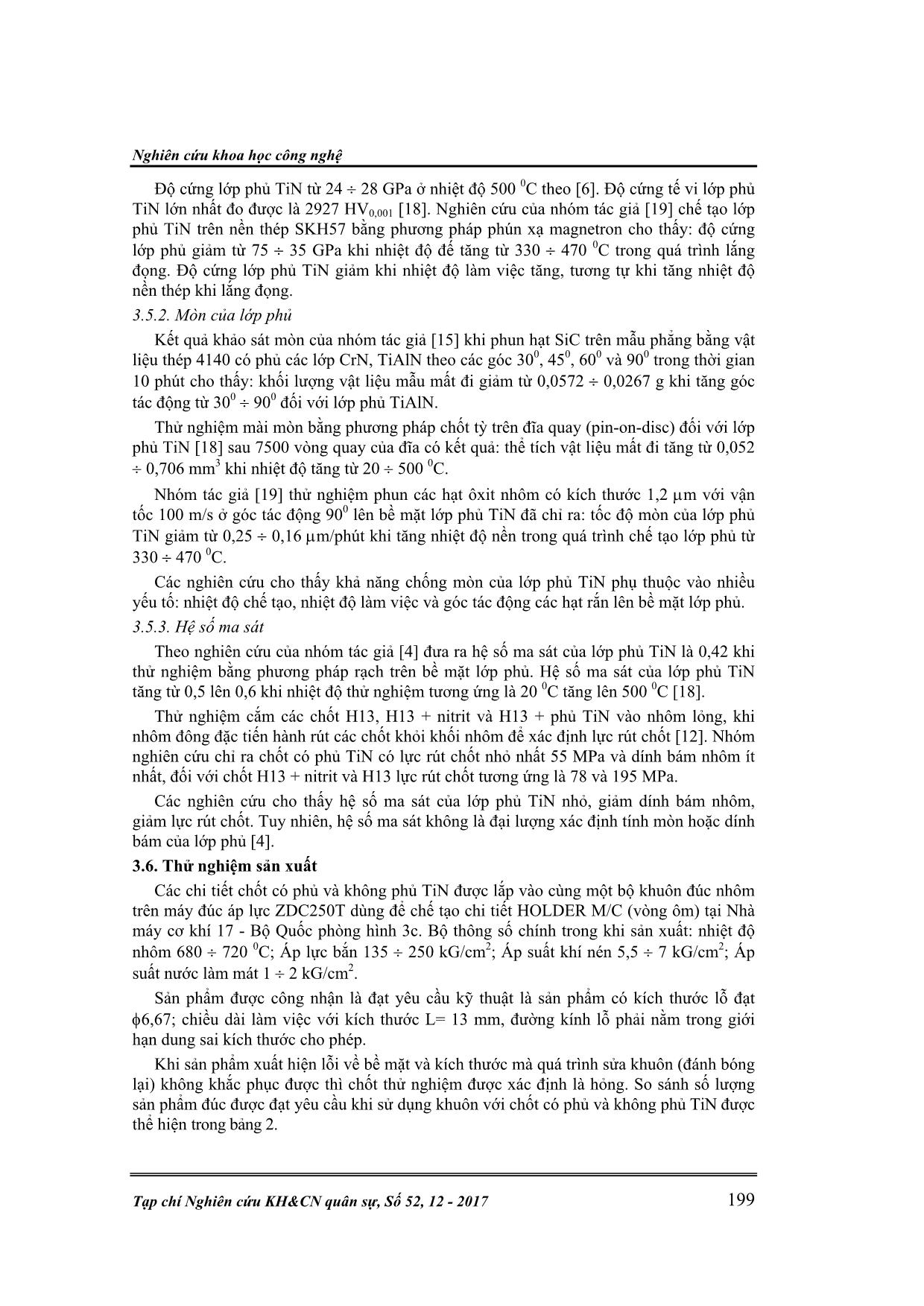
Trang 6
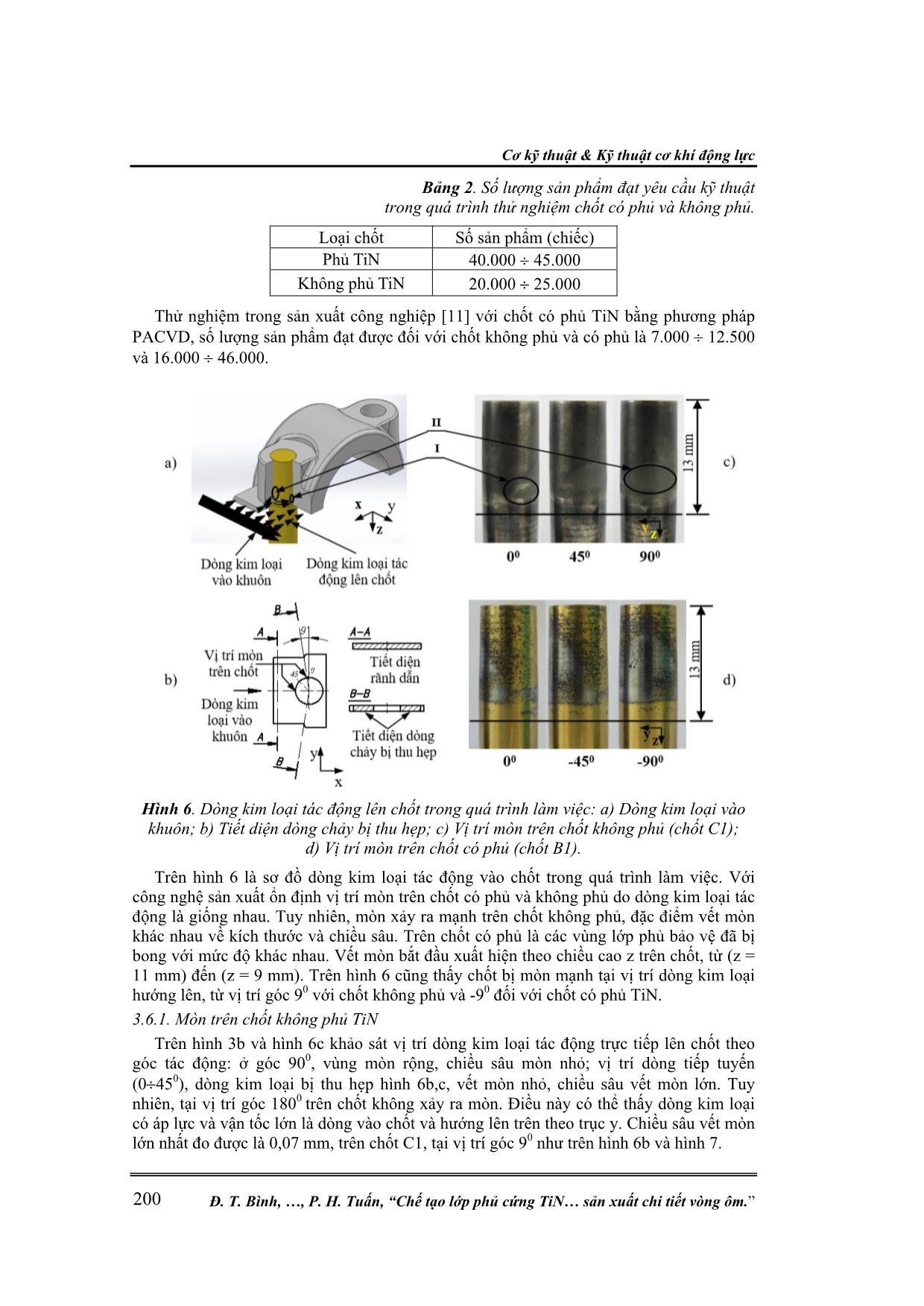
Trang 7
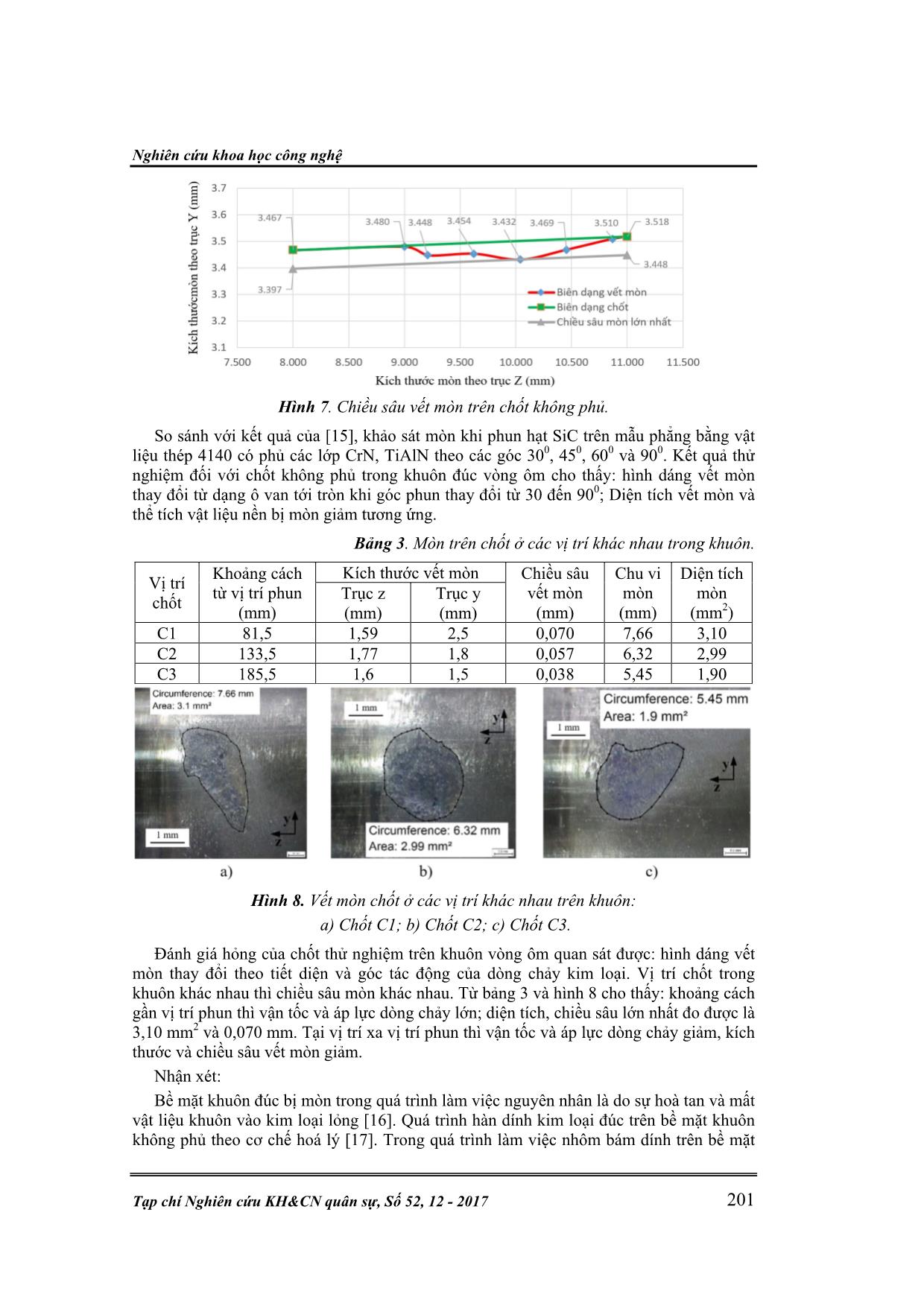
Trang 8

Trang 9
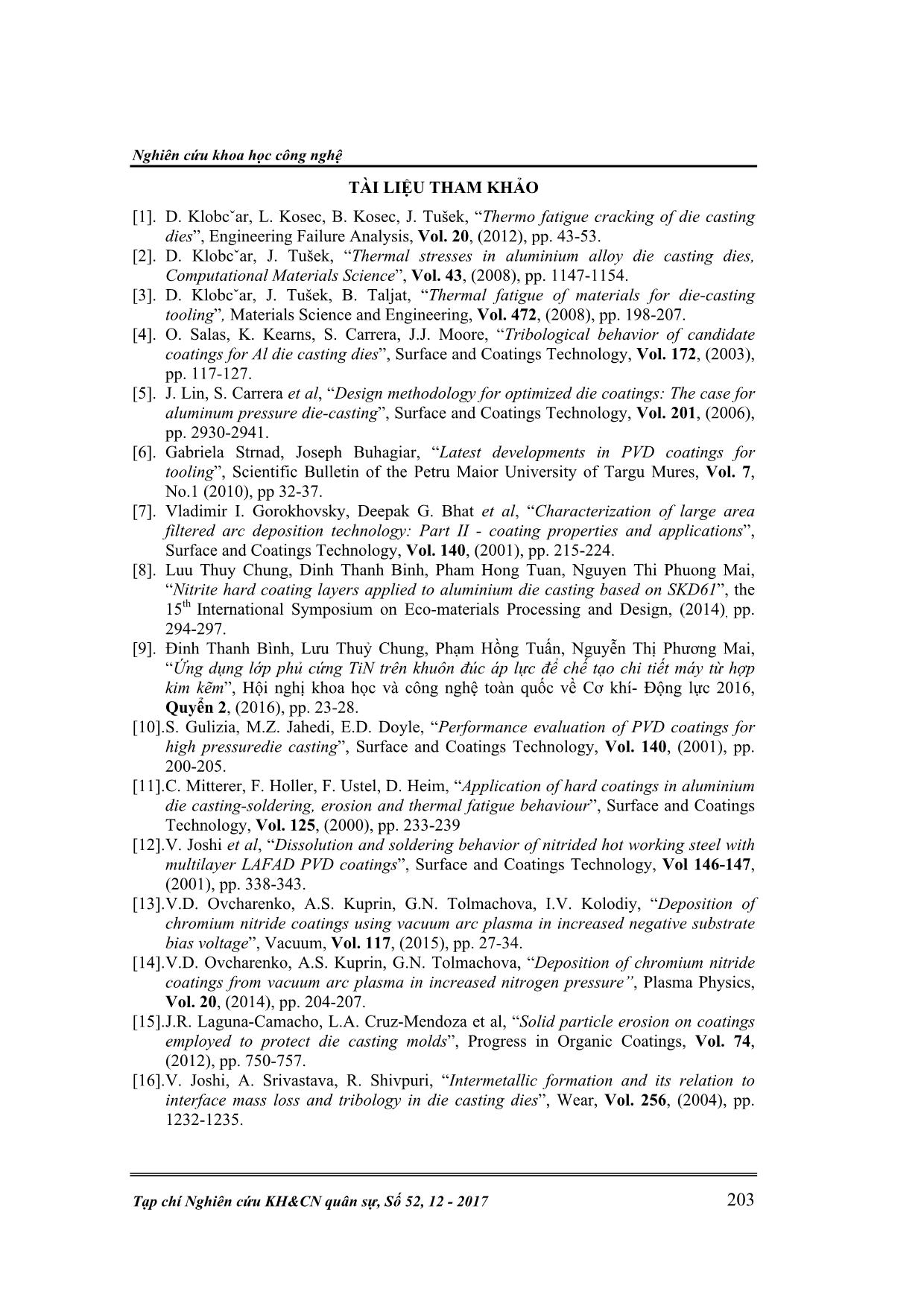
Trang 10
Tải về để xem bản đầy đủ
Tóm tắt nội dung tài liệu: Chế tạo lớp phủ cứng tin bằng phương pháp hồ quang Catot, ứng dụng trên khuôn đúc áp lực hợp kim nhôm để sản xuất chi tiết vòng ôm
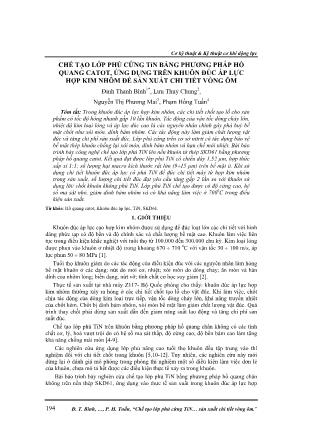
Cơ kỹ thuật & Kỹ thuật cơ khí động lực Đ. T. Bình, , P. H. Tuấn, “Chế tạo lớp phủ cứng TiN sản xuất chi tiết vòng ôm.” 194 CHẾ TẠO LỚP PHỦ CỨNG TiN BẰNG PHƯƠNG PHÁP HỒ QUANG CATOT, ỨNG DỤNG TRÊN KHUÔN ĐÚC ÁP LỰC HỢP KIM NHÔM ĐỂ SẢN XUẤT CHI TIẾT VÒNG ÔM Đinh Thanh Bình1*, Lưu Thuỷ Chung2, Nguyễn Thị Phương Mai3, Phạm Hồng Tuấn4 Tóm tắt: Trong khuôn đúc áp lực hợp kim nhôm, các chi tiết chốt tạo lỗ cho sản phẩm có tốc độ hỏng nhanh gấp 10 lần khuôn. Tác động của vận tốc dòng chảy lớn, nhiệt độ kim loại lỏng và áp lực đúc cao là các nguyên nhân chính gây phá huỷ bề mặt chốt như xói mòn, dính bám nhôm. Các tác động này làm giảm chất lượng vật đúc và tăng chi phí sản xuất đúc. Lớp phủ cứng trên cơ sở nitrit có tác dụng bảo vệ bề mặt thép khuôn chống lại xói mòn, dính bám nhôm và hạn chế mỏi nhiệt. Bài báo trình bày công nghệ chế tạo lớp phủ TiN lên nền khuôn từ thép SKD61 bằng phương pháp hồ quang catot. Kết quả đạt được lớp phủ TiN có chiều dày 1,52 µm, hợp thức xấp xỉ 1:1; số lượng hạt macro kích thước rất lớn (915 µm) trên bề mặt ít. Khi sử dụng chi tiết khuôn đúc áp lực có phủ TiN để đúc chi tiết máy từ hợp kim nhôm trong sản xuất, số lượng chi tiết đúc đạt yêu cầu tăng gấp 2 lần so với khuôn sử dụng lõi/ chốt khuôn không phủ TiN. Lớp phủ TiN chế tạo được có độ cứng cao, hệ số ma sát nhỏ, giảm dính bám nhôm và có khả năng làm việc ở 7000C trong điều kiện sản xuất. Từ khóa: Hồ quang catot, Khuôn đúc áp lực, TiN, SKD61. 1. GIỚI THIỆU Khuôn đúc áp lực cao hợp kim nhôm được sử dụng để đúc loạt lớn các chi tiết với hình dáng phức tạp có độ bền và độ chính xác và chất lượng bề mặt cao. Khuôn làm việc liên tục trong điều kiện khắc nghiệt với tuổi thọ từ 100.000 đến 300.000 chu kỳ. Kim loại lỏng được phun vào khuôn ở nhiệt độ trong khoảng 670 710 0C với vận tốc 30 100 m/s, áp lực phun 50 80 MPa [1]. Tuổi thọ khuôn giảm do các tác động của điều kiện đúc với các nguyên nhân làm hỏng bề mặt khuôn ở các dạng: nứt do mỏi cơ, nhiệt; xói mòn do dòng chảy; ăn mòn và hàn dính của nhôm lỏng; biến dạng, nứt vỡ; tính chất cơ học suy giảm [2]. Thực tế sản xuất tại nhà máy Z117- Bộ Quốc phòng cho thấy: khuôn đúc áp lực hợp kim nhôm thường xảy ra hỏng ở các chi tiết chốt tạo lỗ cho vật đúc. Khi làm việc, chốt chịu tác động của dòng kim loại trực tiếp, vận tốc dòng chảy lớn, khả năng truyền nhiệt của chốt kém. Chốt bị dính bám nhôm, xói mòn bề mặt làm giảm chất lượng vật đúc. Quá trình thay chốt phải dừng sản xuất dẫn đến giảm năng suất lao động và tăng chi phí sản suất đúc. Chế tạo lớp phủ TiN trên khuôn bằng phương pháp hồ quang chân không có các tính chất cơ, lý, hoá vượt trội do có hệ số ma sát thấp, độ cứng cao, độ bền bám cao làm tăng khả năng chống mài mòn [4-9]. Các nghiên cứu ứng dụng lớp phủ nâng cao tuổi thọ khuôn đều tập trung vào thí nghiệm đối với chi tiết chốt trong khuôn [5,10-12]. Tuy nhiên, các nghiên cứu này mới dừng lại ở đánh giá mô phỏng trong phòng thí nghiệm một số điều kiện làm việc đơn lẻ của khuôn, chưa mô tả hết được các điều kiện thực tế xảy ra trong khuôn. Bài báo trình bày nghiên cứu chế tạo lớp phủ TiN bằng phương pháp hồ quang chân không trên nền thép SKD61, ứng dụng vào thực tế sản xuất trong khuôn đúc áp lực hợp Nghiên cứu khoa học công nghệ Tạp chí Nghiên cứu KH&CN quân sự, Số 52, 12 - 2017 195 kim nhôm. Kết quả khảo sát ảnh hưởng của một số yếu tố công nghệ chủ yếu (nồng độ khí nitơ và năng lượng hồ quang) lên hợp thức, hình thái bề mặt và chiều dày lớp phủ cho thấy khả năng làm việc của chi tiết khuôn có phủ tốt hơn không phủ TiN. 2. THÍ NGHIỆM 2.1. Chế tạo mẫu thí nghiệm Lớp phủ TiN được lắng đọng trên nền thép SKD61 theo tiêu chuẩn JIS. Mẫu thí nghiệm để đánh giá tính chất lớp phủ ứng dụng trong sản xuất gồm hai loại mẫu: 1. Mẫu dùng để đánh giá tính chất của lớp phủ hình 1a, kích thước 16, H = 6 mm; 2. Chi tiết thử nghiệm trong thực tế sản xuất hình 1b, phần làm việc quan trọng được đánh dấu L, có kích thước L = 13 mm. Quy trình xử lý bề mặt trước khi phủ: sau khi gia công đạt kích thước, chi tiết được nhiệt luyện, thấm nitơ với chiều sâu lớp thấm 0,1 0,2 mm, độ cứng đạt 58 HRC, mài đánh bóng đạt Ra = 0,08 0,16 m. Hình 1. Mẫu thép SKD61 thí nghiệm: a) Mẫu đo tính chất lớp phủ; b) Chi tiết thử nghiệm sản xuất. 2.2. Lắng đọng lớp phủ Lớp phủ TiN được chế tạo bằng phương pháp PVD hồ quang chân không sử dụng thiết bị DREVAR 400-VTD (Viện Ứng dụng công nghệ). Buồng chân không hình trụ hình 2 có kích thước = 400 mm, L = 400 mm, độ chân không đạt 6x10-5 mbar. Trong buồng chân không được lắp 3 đầu hồ quang cách đều nhau với góc 1200, một bia hình tròn kích thước 70 mm làm từ titan (99,99%) được đặt ở chính giữa. Mẫu sau khi làm sạch được gá đặt vào buồng chân không như trên hình 2b. Chi tiết quay cùng gá với tốc độ 12 vòng/phút; khoảng cách gần nhất từ mẫu đến tâm bia: H = 70 mm, L = 70 mm. Trước khi thực hiện lắng đọng, chi tiết được làm sạ ... chốt [12]. Nhóm nghiên cứu chỉ ra chốt có phủ TiN có lực rút chốt nhỏ nhất 55 MPa và dính bám nhôm ít nhất, đối với chốt H13 + nitrit và H13 lực rút chốt tương ứng là 78 và 195 MPa. Các nghiên cứu cho thấy hệ số ma sát của lớp phủ TiN nhỏ, giảm dính bám nhôm, giảm lực rút chốt. Tuy nhiên, hệ số ma sát không là đại lượng xác định tính mòn hoặc dính bám của lớp phủ [4]. 3.6. Thử nghiệm sản xuất Các chi tiết chốt có phủ và không phủ TiN được lắp vào cùng một bộ khuôn đúc nhôm trên máy đúc áp lực ZDC250T dùng để chế tạo chi tiết HOLDER M/C (vòng ôm) tại Nhà máy cơ khí 17 - Bộ Quốc phòng hình 3c. Bộ thông số chính trong khi sản xuất: nhiệt độ nhôm 680 720 0C; Áp lực bắn 135 250 kG/cm2; Áp suất khí nén 5,5 7 kG/cm2; Áp suất nước làm mát 1 2 kG/cm2. Sản phẩm được công nhận là đạt yêu cầu kỹ thuật là sản phẩm có kích thước lỗ đạt 6,67; chiều dài làm việc với kích thước L= 13 mm, đường kính lỗ phải nằm trong giới hạn dung sai kích thước cho phép. Khi sản phẩm xuất hiện lỗi về bề mặt và kích thước mà quá trình sửa khuôn (đánh bóng lại) không khắc phục được thì chốt thử nghiệm được xác định là hỏng. So sánh số lượng sản phẩm đúc được đạt yêu cầu khi sử dụng khuôn với chốt có phủ và không phủ TiN được thể hiện trong bảng 2. Cơ kỹ thuật & Kỹ thuật cơ khí động lực Đ. T. Bình, , P. H. Tuấn, “Chế tạo lớp phủ cứng TiN sản xuất chi tiết vòng ôm.” 200 Bảng 2. Số lượng sản phẩm đạt yêu cầu kỹ thuật trong quá trình thử nghiệm chốt có phủ và không phủ. Loại chốt Số sản phẩm (chiếc) Phủ TiN 40.000 45.000 Không phủ TiN 20.000 25.000 Thử nghiệm trong sản xuất công nghiệp [11] với chốt có phủ TiN bằng phương pháp PACVD, số lượng sản phẩm đạt được đối với chốt không phủ và có phủ là 7.000 12.500 và 16.000 46.000. Hình 6. Dòng kim loại tác động lên chốt trong quá trình làm việc: a) Dòng kim loại vào khuôn; b) Tiết diện dòng chảy bị thu hẹp; c) Vị trí mòn trên chốt không phủ (chốt C1); d) Vị trí mòn trên chốt có phủ (chốt B1). Trên hình 6 là sơ đồ dòng kim loại tác động vào chốt trong quá trình làm việc. Với công nghệ sản xuất ổn định vị trí mòn trên chốt có phủ và không phủ do dòng kim loại tác động là giống nhau. Tuy nhiên, mòn xảy ra mạnh trên chốt không phủ, đặc điểm vết mòn khác nhau về kích thước và chiều sâu. Trên chốt có phủ là các vùng lớp phủ bảo vệ đã bị bong với mức độ khác nhau. Vết mòn bắt đầu xuất hiện theo chiều cao z trên chốt, từ (z = 11 mm) đến (z = 9 mm). Trên hình 6 cũng thấy chốt bị mòn mạnh tại vị trí dòng kim loại hướng lên, từ vị trí góc 90 với chốt không phủ và -90 đối với chốt có phủ TiN. 3.6.1. Mòn trên chốt không phủ TiN Trên hình 3b và hình 6c khảo sát vị trí dòng kim loại tác động trực tiếp lên chốt theo góc tác động: ở góc 900, vùng mòn rộng, chiều sâu mòn nhỏ; vị trí dòng tiếp tuyến (0450), dòng kim loại bị thu hẹp hình 6b,c, vết mòn nhỏ, chiều sâu vết mòn lớn. Tuy nhiên, tại vị trí góc 1800 trên chốt không xảy ra mòn. Điều này có thể thấy dòng kim loại có áp lực và vận tốc lớn là dòng vào chốt và hướng lên trên theo trục y. Chiều sâu vết mòn lớn nhất đo được là 0,07 mm, trên chốt C1, tại vị trí góc 90 như trên hình 6b và hình 7. Nghiên cứu khoa học công nghệ Tạp chí Nghiên cứu KH&CN quân sự, Số 52, 12 - 2017 201 Hình 7. Chiều sâu vết mòn trên chốt không phủ. So sánh với kết quả của [15], khảo sát mòn khi phun hạt SiC trên mẫu phẳng bằng vật liệu thép 4140 có phủ các lớp CrN, TiAlN theo các góc 300, 450, 600 và 900. Kết quả thử nghiệm đối với chốt không phủ trong khuôn đúc vòng ôm cho thấy: hình dáng vết mòn thay đổi từ dạng ô van tới tròn khi góc phun thay đổi từ 30 đến 900; Diện tích vết mòn và thể tích vật liệu nền bị mòn giảm tương ứng. Bảng 3. Mòn trên chốt ở các vị trí khác nhau trong khuôn. Vị trí chốt Khoảng cách từ vị trí phun (mm) Kích thước vết mòn Chiều sâu vết mòn (mm) Chu vi mòn (mm) Diện tích mòn (mm2) Trục z (mm) Trục y (mm) C1 81,5 1,59 2,5 0,070 7,66 3,10 C2 133,5 1,77 1,8 0,057 6,32 2,99 C3 185,5 1,6 1,5 0,038 5,45 1,90 Hình 8. Vết mòn chốt ở các vị trí khác nhau trên khuôn: a) Chốt C1; b) Chốt C2; c) Chốt C3. Đánh giá hỏng của chốt thử nghiệm trên khuôn vòng ôm quan sát được: hình dáng vết mòn thay đổi theo tiết diện và góc tác động của dòng chảy kim loại. Vị trí chốt trong khuôn khác nhau thì chiều sâu mòn khác nhau. Từ bảng 3 và hình 8 cho thấy: khoảng cách gần vị trí phun thì vận tốc và áp lực dòng chảy lớn; diện tích, chiều sâu lớn nhất đo được là 3,10 mm2 và 0,070 mm. Tại vị trí xa vị trí phun thì vận tốc và áp lực dòng chảy giảm, kích thước và chiều sâu vết mòn giảm. Nhận xét: Bề mặt khuôn đúc bị mòn trong quá trình làm việc nguyên nhân là do sự hoà tan và mất vật liệu khuôn vào kim loại lỏng [16]. Quá trình hàn dính kim loại đúc trên bề mặt khuôn không phủ theo cơ chế hoá lý [17]. Trong quá trình làm việc nhôm bám dính trên bề mặt Cơ kỹ thuật & Kỹ thuật cơ khí động lực Đ. T. Bình, , P. H. Tuấn, “Chế tạo lớp phủ cứng TiN sản xuất chi tiết vòng ôm.” 202 chốt, các lớp mỏng hình thành liên kim với vật liệu nền. Lớp dính bám ảnh hưởng xấu đến độ bóng bề mặt vật đúc hoặc gây xước bề mặt. Lớp dính bám phát triển đến chiều dày nhất định dưới tác động của dòng chảy trong khuôn bong ra khỏi bề mặt khuôn kéo theo một lớp kim loại nền. Qua nhiều chu kỳ đúc, quá trình mất vật liệu trên bề mặt chốt gây hụt kích thước lỗ dẫn đến vật đúc không đạt yêu cầu kỹ thuật. Kết quả nhận được so sánh với kết quả của [15] cho thấy vết mòn dài ở vị trí tác động của dòng kim loại phun vào bề mặt khuôn có góc nhỏ hơn 450, tại vị trí tiết diện dòng chảy bị thu hẹp. Bề mặt chốt trong thử nghiệm chịu tác động của dòng chảy kim loại nhôm ít gây mòn tại vị trí kim loại phun trực tiếp. Mòn trên bề mặt chốt không có lớp phủ do tác động tổng hợp của dòng chảy, dính bám kim loại nhôm lỏng tạo liên kim với nền và lớp liên kim bong ra khỏi bề mặt khuôn. 3.6.2. Mòn trên chốt có phủ TiN Khi có lớp phủ TiN, kim loại nhôm nóng chảy trên bề mặt lớp phủ, thay vì chảy trực tiếp trên bề mặt khuôn bằng thép SKD61. Cơ chế phá huỷ lớp phủ trên bề mặt khuôn là do quá trình hình thành, phát triển và tạo các điểm vỡ cục bộ trên bề mặt lớp phủ. Các nguyên nhân ảnh hưởng như quá trình tạo lớp phủ, tác động cơ học, hoá học của kim loại lỏng, chu kỳ nhiệt của khuôn trong quá trình đúc chi tiết [5]. Mòn trên chốt có phủ bị ảnh hưởng bởi khả năng làm việc, bảo vệ của lớp phủ, khả năng dính bám của lớp phủ với nền. Đánh giá mòn trên chốt có phủ TiN được quan sát sau thử nghiệm sản xuất trên khuôn vòng ôm. Lớp phủ TiN bong mạnh và chủ yếu ở góc tác động trực tiếp 900 hình 6d. Vùng bong rộng có thể quan sát thấy các nhấp nhô bề mặt chốt do quá trình gia công đánh bóng chốt trước khi phủ. Các góc tác động nhỏ vùng bong nhỏ hơn và không xuất hiện vết mòn sâu như chốt không phủ. Cũng tương tự như các chốt không phủ, kích thước vết mòn giảm khi vị trí chốt xa vị trí phun kim loại vào khuôn. Điều này có thể thấy lớp phủ chống dính bám nhôm lỏng tốt, đồng thời giảm ma sát giữa lớp phủ và kim loại vật đúc giúp quá trình rút chốt khỏi vật đúc dễ dàng. Ngoài sự bong tróc do tác động trực tiếp của dòng kim loại, lớp phủ còn bị hỏng trong quá trình làm việc do ứng suất trong xuất hiện khi nung nóng và làm nguội khuôn gây ra các vết nứt tế vi, các vết nứt này phát triển và kim loại đúc điền đầy vết nứt. Khi tăng số lần phun khuôn, kim loại đúc tiếp xúc với kim loại nền hình thành liên kim. Kết hợp với ứng suất sau một số quá trình làm việc lớp phủ mất khả năng dính bám và bong ra khỏi bề mặt khuôn, được nhắc đến trong [5]. Điều này phù hợp với kết quả quan sát trên chốt được phủ TiN sử dụng trong thử nghiệm sản xuất tại nhà máy Z117 - Bộ Quốc phòng. Các nghiên cứu về vị trí mòn, quy luật mòn, ảnh hưởng của dòng chảy là cơ sở xác định dòng chảy trong khuôn, hướng tác động, vị trí chịu tác động lớn nhất, từ đó ứng dụng lớp phủ TiN trên các chi tiết có xu hướng xảy ra hỏng lớn nhất nhằm nâng cao tuổi thọ và năng suất cũng như chất lượng vật đúc. 4. KẾT LUẬN Lớp phủ TiN trên chi tiết khuôn đúc áp lực hợp kim nhôm chế tạo bằng phương pháp hồ quang chân không trên thiết bị DREVAR 400-VTD đạt được: hợp thức của lớp phủ TiN xấp xỉ 1:1 đồng đều trên toàn bộ bề mặt, chiều dày lớp phủ 1,52 µm. Số lượng hạt macro có kích thước lớn trên bề mặt ít nhưng nhưng vẫn còn hạt macro kích thước rất lớn (912 µm). Với chi tiết khuôn có phủ TiN, số lượng chi tiết đúc được đạt yêu cầu kỹ thuật tăng gấp 2 lần so với chi tiết khuôn không phủ TiN. Chốt không phủ TiN bị xói mòn mạnh ở vị trí dòng kim loại bị thu hẹp, góc tác động nhỏ hơn 450. Chốt có phủ TiN bị bong mạnh ở vị trí dòng kim loại tác động trực tiếp (900); lớp phủ TiN có khả năng làm việc ở nhiệt độ 700 0C, chống dính tốt và ma sát với nhôm nhỏ. Nghiên cứu khoa học công nghệ Tạp chí Nghiên cứu KH&CN quân sự, Số 52, 12 - 2017 203 TÀI LIỆU THAM KHẢO [1]. D. Klobcˇar, L. Kosec, B. Kosec, J. Tušek, “Thermo fatigue cracking of die casting dies”, Engineering Failure Analysis, Vol. 20, (2012), pp. 43-53. [2]. D. Klobcˇar, J. Tušek, “Thermal stresses in aluminium alloy die casting dies, Computational Materials Science”, Vol. 43, (2008), pp. 1147-1154. [3]. D. Klobcˇar, J. Tušek, B. Taljat, “Thermal fatigue of materials for die-casting tooling”, Materials Science and Engineering, Vol. 472, (2008), pp. 198-207. [4]. O. Salas, K. Kearns, S. Carrera, J.J. Moore, “Tribological behavior of candidate coatings for Al die casting dies”, Surface and Coatings Technology, Vol. 172, (2003), pp. 117-127. [5]. J. Lin, S. Carrera et al, “Design methodology for optimized die coatings: The case for aluminum pressure die-casting”, Surface and Coatings Technology, Vol. 201, (2006), pp. 2930-2941. [6]. Gabriela Strnad, Joseph Buhagiar, “Latest developments in PVD coatings for tooling”, Scientific Bulletin of the Petru Maior University of Targu Mures, Vol. 7, No.1 (2010), pp 32-37. [7]. Vladimir I. Gorokhovsky, Deepak G. Bhat et al, “Characterization of large area filtered arc deposition technology: Part II - coating properties and applications”, Surface and Coatings Technology, Vol. 140, (2001), pp. 215-224. [8]. Luu Thuy Chung, Dinh Thanh Binh, Pham Hong Tuan, Nguyen Thi Phuong Mai, “Nitrite hard coating layers applied to aluminium die casting based on SKD61”, the 15th International Symposium on Eco-materials Processing and Design, (2014), pp. 294-297. [9]. Đinh Thanh Bình, Lưu Thuỷ Chung, Phạm Hồng Tuấn, Nguyễn Thị Phương Mai, “Ứng dụng lớp phủ cứng TiN trên khuôn đúc áp lực để chế tạo chi tiết máy từ hợp kim kẽm”, Hội nghị khoa học và công nghệ toàn quốc về Cơ khí- Động lực 2016, Quyển 2, (2016), pp. 23-28. [10]. S. Gulizia, M.Z. Jahedi, E.D. Doyle, “Performance evaluation of PVD coatings for high pressuredie casting”, Surface and Coatings Technology, Vol. 140, (2001), pp. 200-205. [11]. C. Mitterer, F. Holler, F. Ustel, D. Heim, “Application of hard coatings in aluminium die casting-soldering, erosion and thermal fatigue behaviour”, Surface and Coatings Technology, Vol. 125, (2000), pp. 233-239 [12]. V. Joshi et al, “Dissolution and soldering behavior of nitrided hot working steel with multilayer LAFAD PVD coatings”, Surface and Coatings Technology, Vol 146-147, (2001), pp. 338-343. [13]. V.D. Ovcharenko, A.S. Kuprin, G.N. Tolmachova, I.V. Kolodiy, “Deposition of chromium nitride coatings using vacuum arc plasma in increased negative substrate bias voltage”, Vacuum, Vol. 117, (2015), pp. 27-34. [14]. V.D. Ovcharenko, A.S. Kuprin, G.N. Tolmachova, “Deposition of chromium nitride coatings from vacuum arc plasma in increased nitrogen pressure”, Plasma Physics, Vol. 20, (2014), pp. 204-207. [15]. J.R. Laguna-Camacho, L.A. Cruz-Mendoza et al, “Solid particle erosion on coatings employed to protect die casting molds”, Progress in Organic Coatings, Vol. 74, (2012), pp. 750-757. [16]. V. Joshi, A. Srivastava, R. Shivpuri, “Intermetallic formation and its relation to interface mass loss and tribology in die casting dies”, Wear, Vol. 256, (2004), pp. 1232-1235. Cơ kỹ thuật & Kỹ thuật cơ khí động lực Đ. T. Bình, , P. H. Tuấn, “Chế tạo lớp phủ cứng TiN sản xuất chi tiết vòng ôm.” 204 [17]. Hanliang Zhu, Jingjie Guo, Jun Jia, “Experimental study and theoretical analysis on die solderingin aluminum die casting”, Journal of Materials Processing Technology, Vol. 123, (2002), pp. 229-235. [18]. M. Polok-Rubiniec, L.A. Dobrzański, K. Lukaszkowicz, M. Adamiak, “Comparison of the structure, properties and wear resistance of the TiN PVD coatings” Journal of Achievements in Materials and Manufacturing Engineering, Vol. 27, (2008), pp. 87- 90. [19]. Y. Iwai et al, “Evaluation of erosive wear resistance of TiN coatings by a slurry jet impact test”, Wear, Vol. 261, (2006), pp. 112-118. [20]. Nguyễn Thành Hợp, Đinh Thanh Bình, Nguyễn Thị Phương Mai, Phạm Hồng Tuấn, “Chế tạo lớp phủ cứng TiN, ZrN, TiCN trên dụng cụ cắt và chi tiết khuôn mẫu bằng công nghệ hồ quang chân không”, Hội nghị khoa học - công nghệ toàn quốc về cơ khí lần thứ IV, Quyển 2, (2015), pp. 607-613. ABSTRACT DEPOSITED THE TiN HARD COATING BY VACUUM CATHODE ARC, USING FOR ALUMINUM DIE-CASTING OF HOLDER M/C COMPONENT In the aluminum alloy die cast mold, the pins for creating holes in the product have a failure speed 10 times faster than that of the mold. The effects of high flow velocities, liquid metal temperatures and high molding pressures are the main causes of surface damage such as erosion, adhesion to aluminum. These effects reduce the quality of the castings and increase the cost of molding. Nitrile-based hard coatings protect the steel surface against erosion, aluminum adhesion and reduce thermal fatigue. This paper presents the technology of manufacture TiN coating on the SKD61 steel mold base by vacuum cathode arc method. Results obtained was the TiN coating with a thickness of 1.52 μm, congruence approximate 1: 1; The number of very large macro particles (915 μm) on the surface is low. When using TiN coated die castings for casting machine parts from aluminum alloy for production, the required number of molded parts is doubled compared to TiN coated cores/latches. TiN coatings were made of high hardness, low coefficient of friction, reduced adhesion to aluminum and capable of working at 7000C under production conditions. Keywords: Cathodic arc, Aluminium die casting, TiN, SKD61. Nhận bài ngày 08 tháng 6 năm 2017 Hoàn thiện ngày 01 tháng 8 năm 2017 Chấp nhận đăng ngày 20 tháng 12 năm 2017 Địa chỉ: 1 Khoa Dạy nghề, Cao đẳng Công nghiệp quốc phòng; 2 Khoa Cơ khí, Đại học Sư phạm Kỹ thuật Vinh; 3 Viện Cơ khí, Đại học Bách khoa Hà Nội; 4 Trung tâm Quang điện tử, Viện Ứng dụng Công nghệ. * E-mail: thanhbinh2183@gmail.com.
File đính kèm:
che_tao_lop_phu_cung_tin_bang_phuong_phap_ho_quang_catot_ung.pdf