Advanced compact model and processing circuit for integrated magnetic sensor systems
Abstract: The generalized electric model of the Hall sensor, which is designed
for circuit simulation, is taken into account the features of its design and used for
manufacturing materials. The model of the Hall sensor is implemented in the
language Verilog-A, has a simple structure and allows to accurately describe its
performance characteristics. The equivalent circuit of the sensor is built on the
basis of standard subcomponents and does not use complex equations to describe
the physical processes in its structure. A circuit and topological solution consisting
of Hall sensor, differential amplifier and 10-bit successive approximation register
analog-to-digital converter and other components integrated on a single chip using
the TSMC 0.18 μm CMOS MS/RF 1,8/3,3V PDK design library, allowing to receive
and process data of sensor devices.
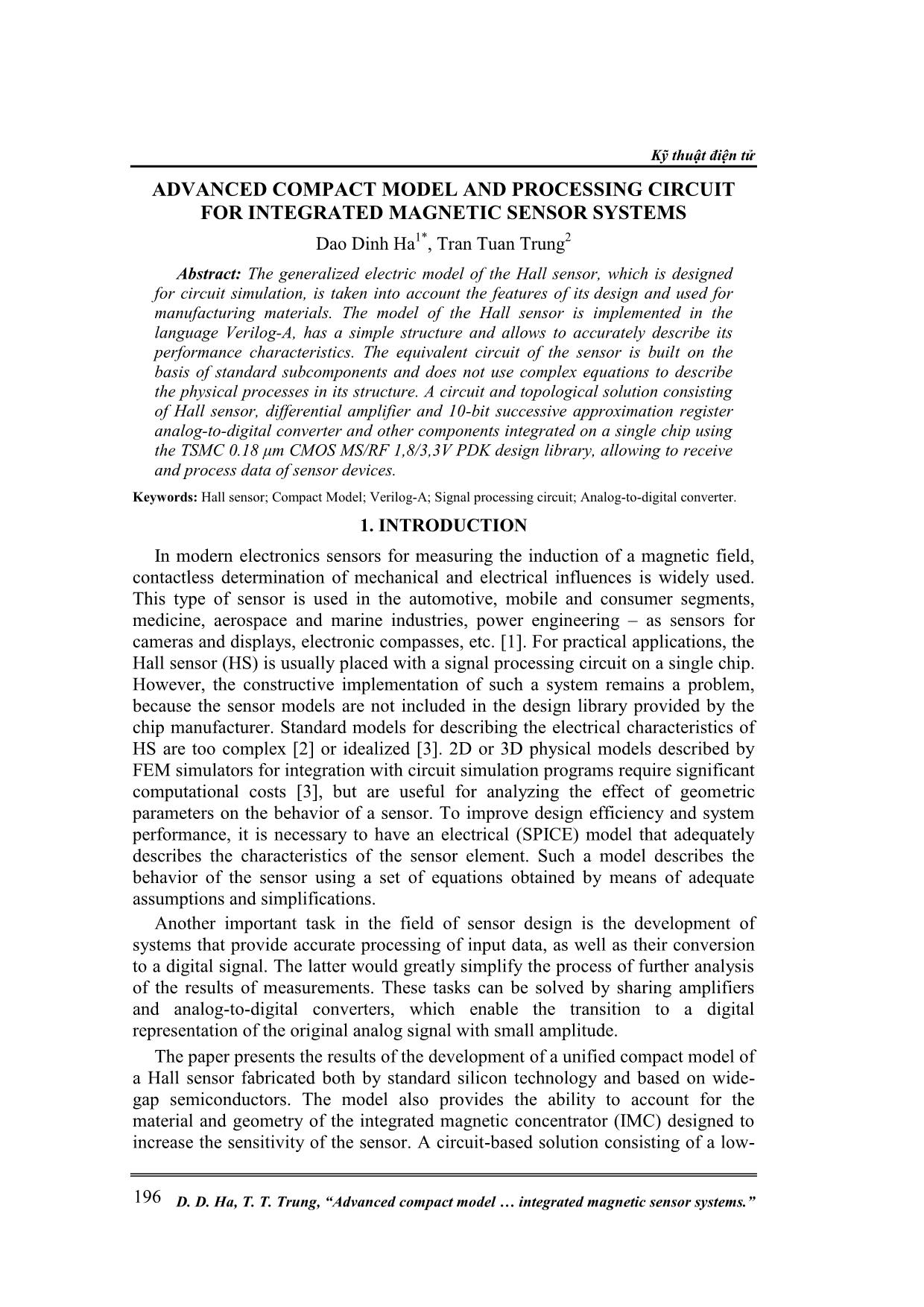
Trang 1
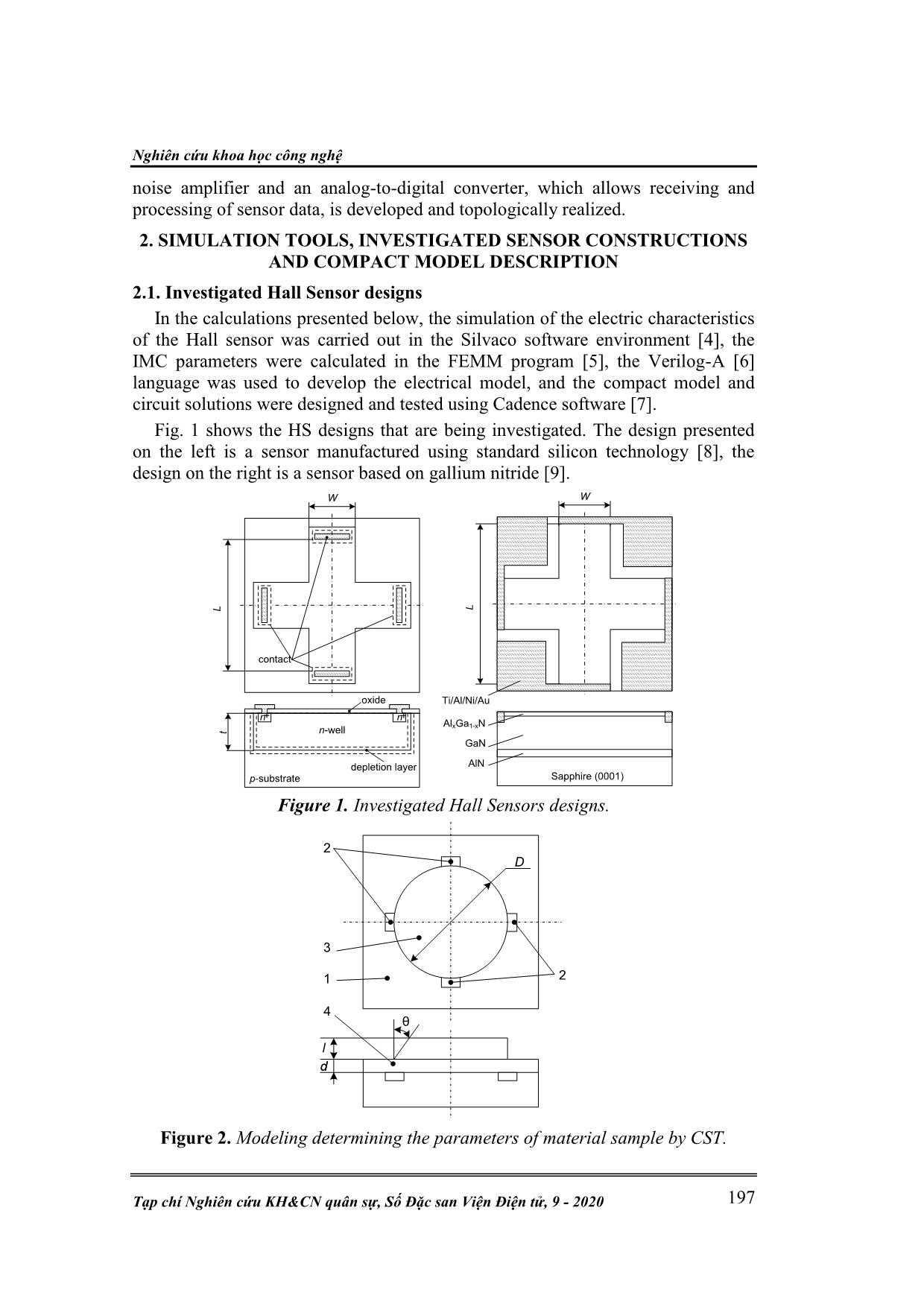
Trang 2
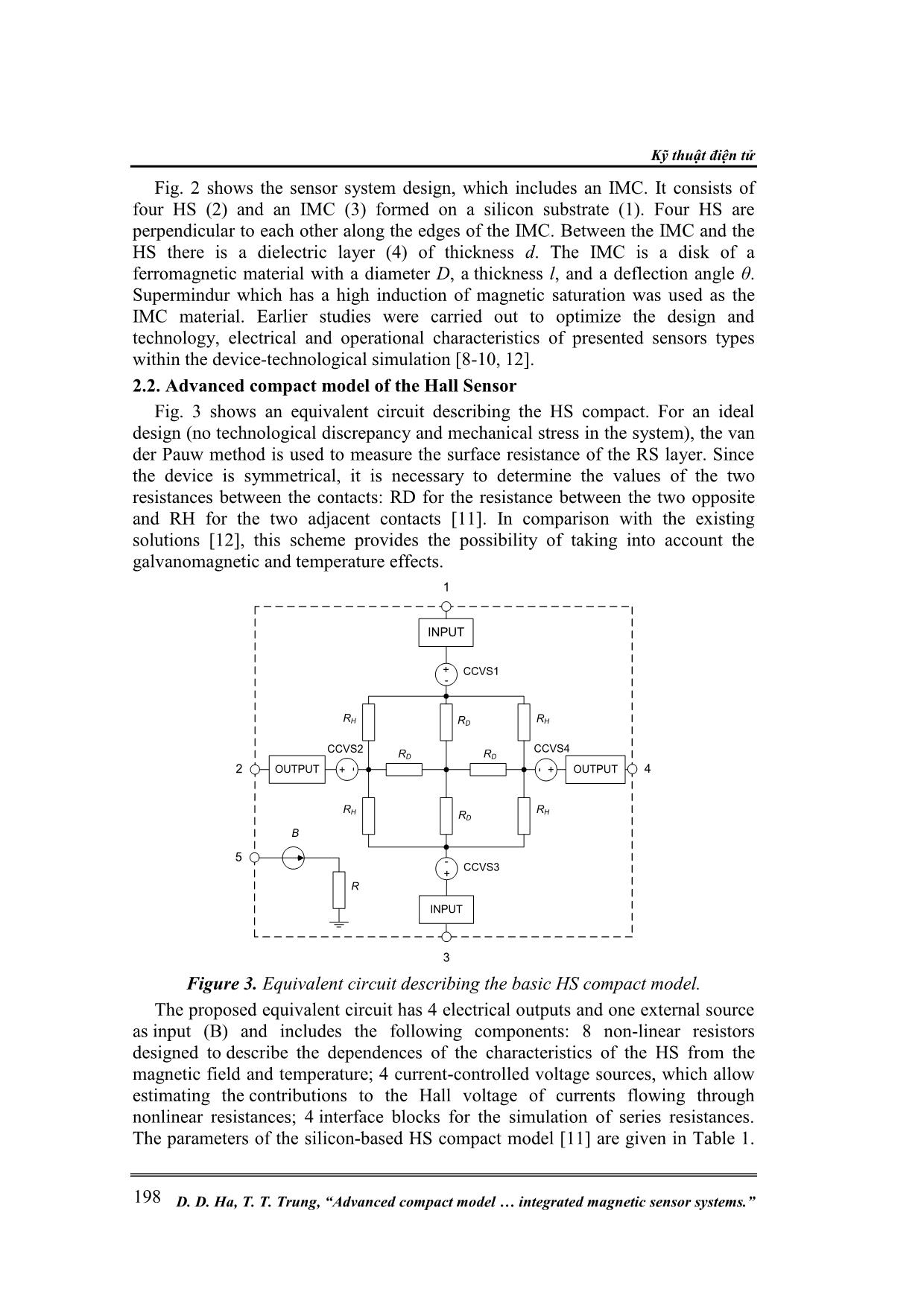
Trang 3
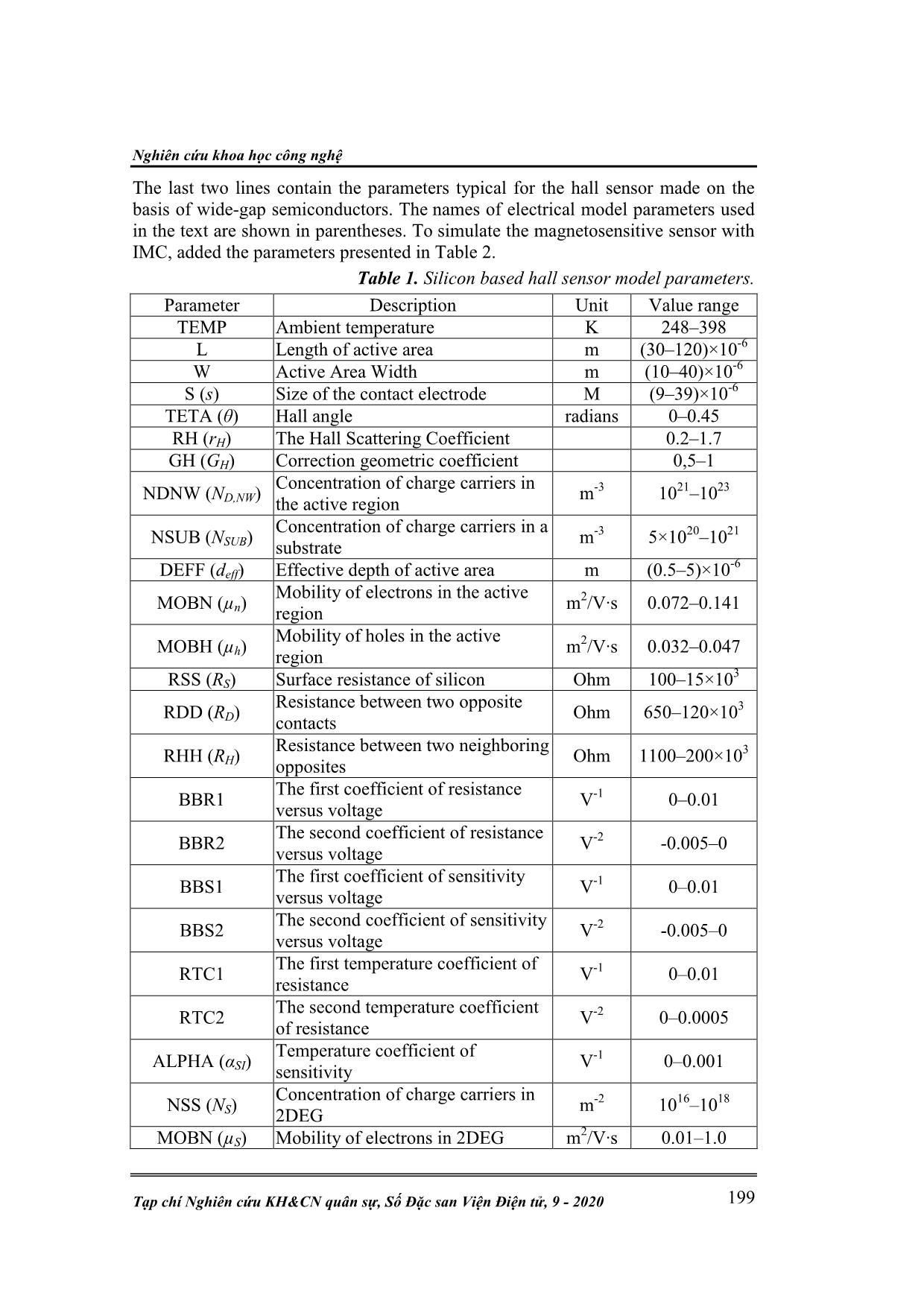
Trang 4
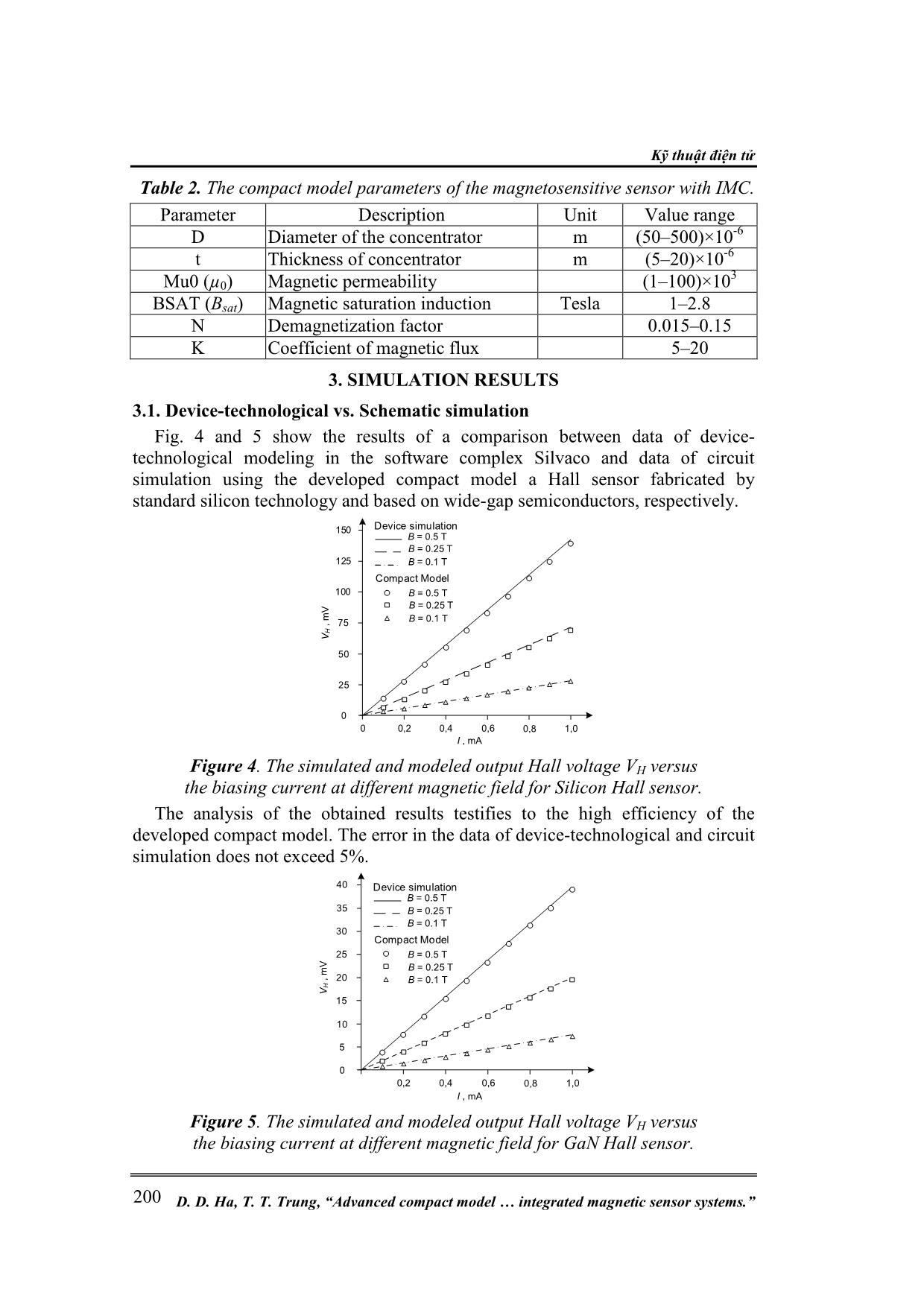
Trang 5
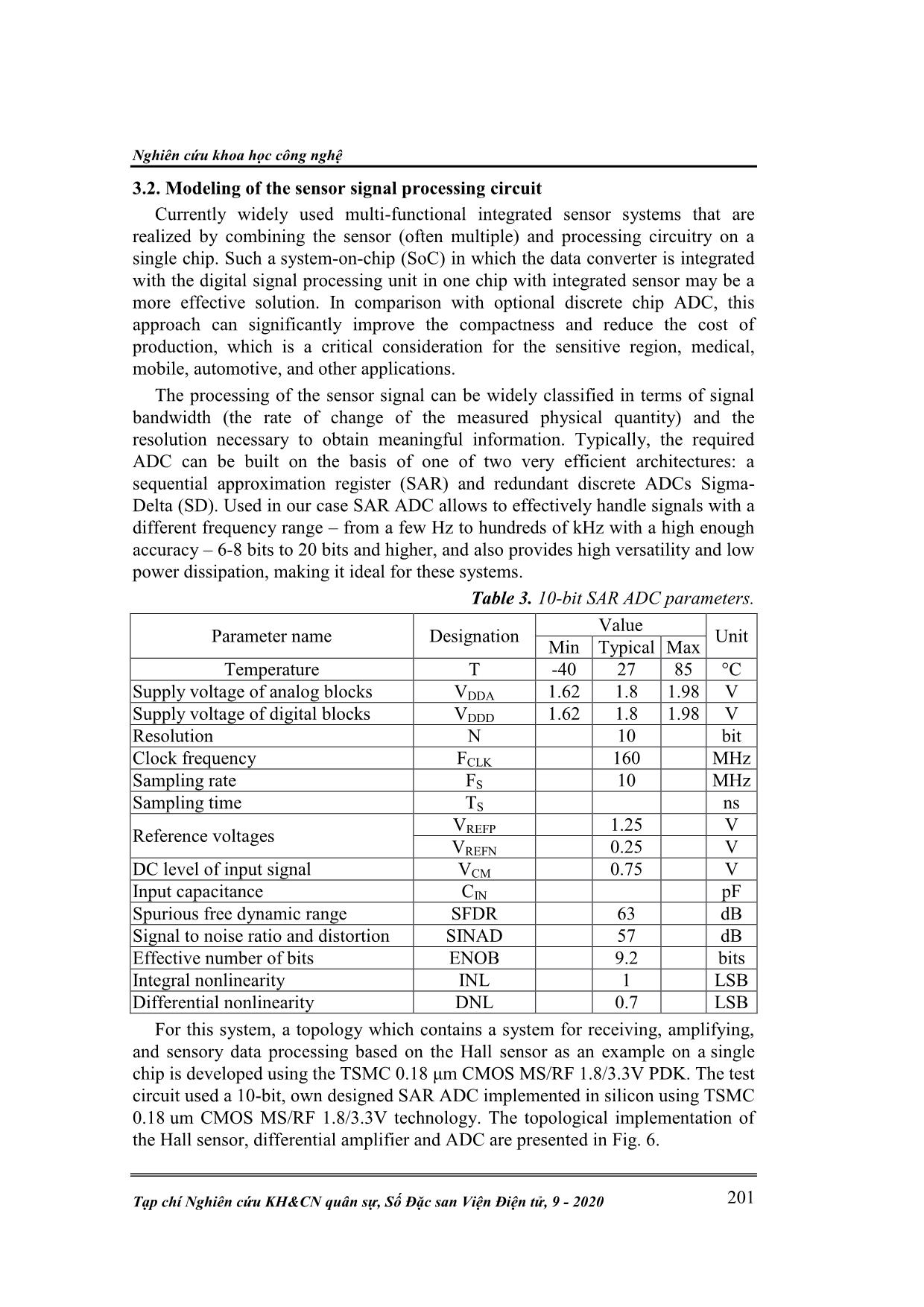
Trang 6
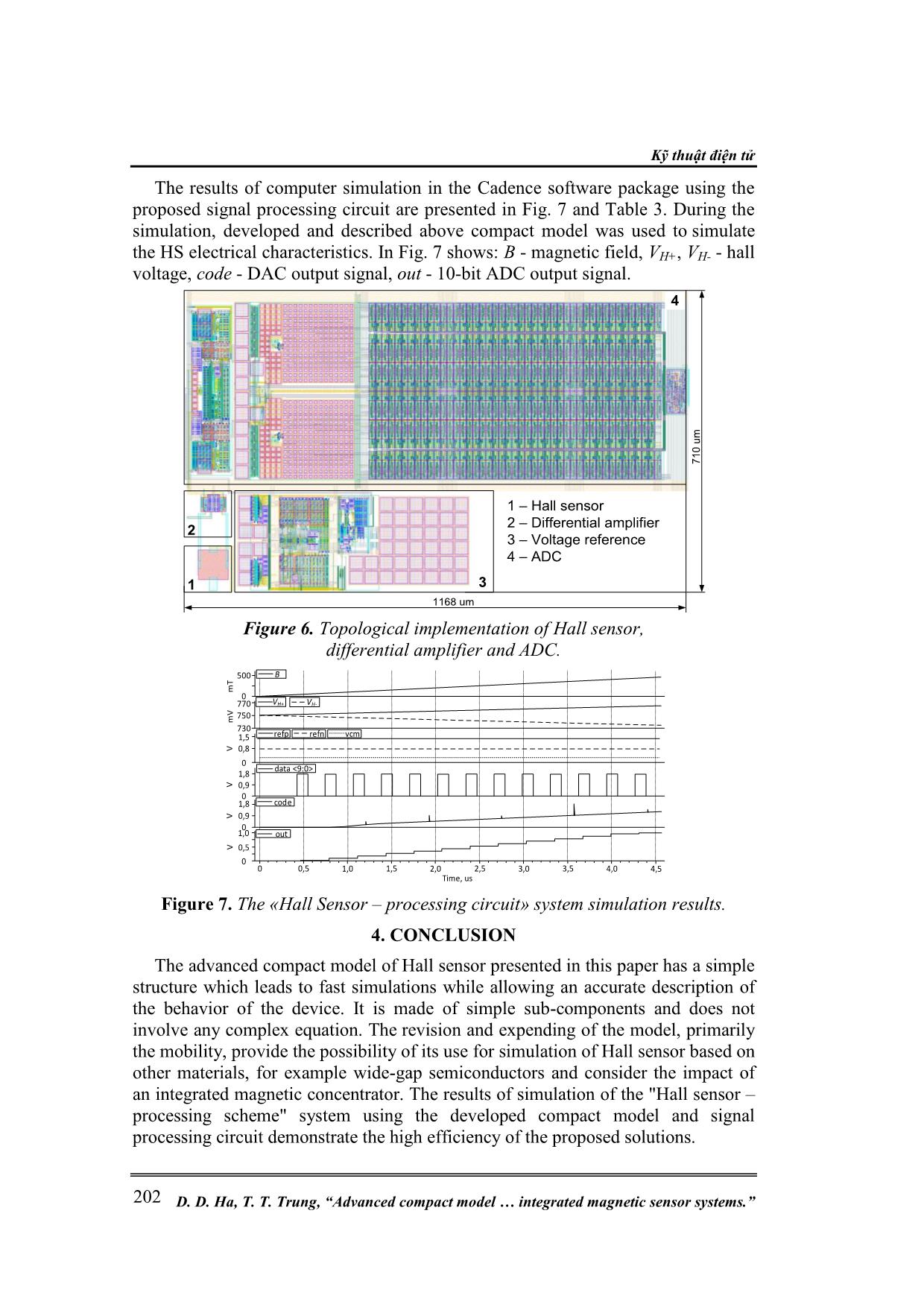
Trang 7
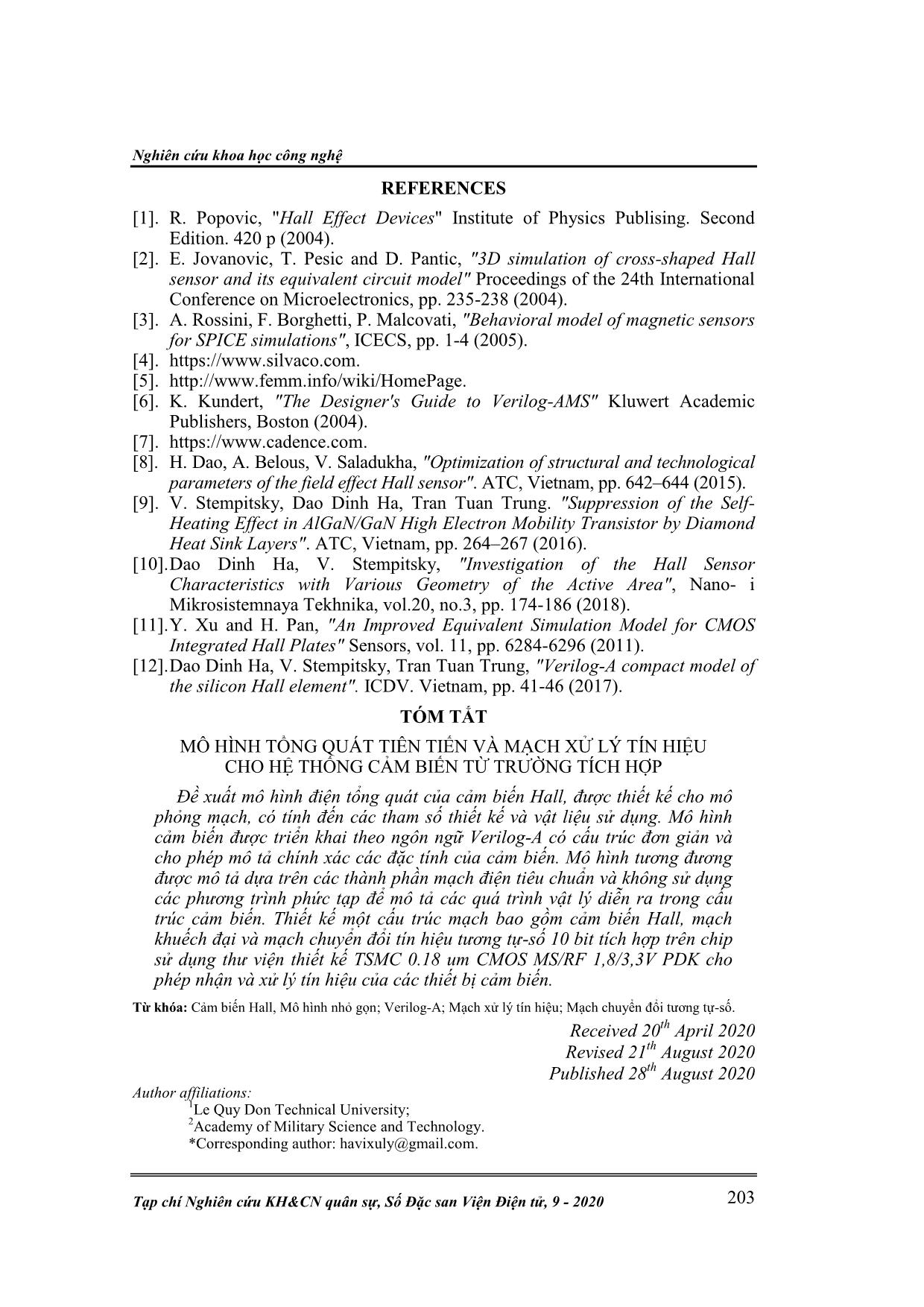
Trang 8
Tóm tắt nội dung tài liệu: Advanced compact model and processing circuit for integrated magnetic sensor systems
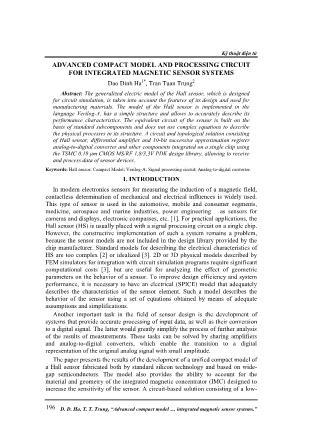
Kỹ thuật điện tử D. D. Ha, T. T. Trung, “Advanced compact model integrated magnetic sensor systems.” 196 ADVANCED COMPACT MODEL AND PROCESSING CIRCUIT FOR INTEGRATED MAGNETIC SENSOR SYSTEMS Dao Dinh Ha 1* , Tran Tuan Trung 2 Abstract: The generalized electric model of the Hall sensor, which is designed for circuit simulation, is taken into account the features of its design and used for manufacturing materials. The model of the Hall sensor is implemented in the language Verilog-A, has a simple structure and allows to accurately describe its performance characteristics. The equivalent circuit of the sensor is built on the basis of standard subcomponents and does not use complex equations to describe the physical processes in its structure. A circuit and topological solution consisting of Hall sensor, differential amplifier and 10-bit successive approximation register analog-to-digital converter and other components integrated on a single chip using the TSMC 0.18 μm CMOS MS/RF 1,8/3,3V PDK design library, allowing to receive and process data of sensor devices. Keywords: Hall sensor; Compact Model; Verilog-A; Signal processing circuit; Analog-to-digital converter. 1. INTRODUCTION In modern electronics sensors for measuring the induction of a magnetic field, contactless determination of mechanical and electrical influences is widely used. This type of sensor is used in the automotive, mobile and consumer segments, medicine, aerospace and marine industries, power engineering – as sensors for cameras and displays, electronic compasses, etc. [1]. For practical applications, the Hall sensor (HS) is usually placed with a signal processing circuit on a single chip. However, the constructive implementation of such a system remains a problem, because the sensor models are not included in the design library provided by the chip manufacturer. Standard models for describing the electrical characteristics of HS are too complex [2] or idealized [3]. 2D or 3D physical models described by FEM simulators for integration with circuit simulation programs require significant computational costs [3], but are useful for analyzing the effect of geometric parameters on the behavior of a sensor. To improve design efficiency and system performance, it is necessary to have an electrical (SPICE) model that adequately describes the characteristics of the sensor element. Such a model describes the behavior of the sensor using a set of equations obtained by means of adequate assumptions and simplifications. Another important task in the field of sensor design is the development of systems that provide accurate processing of input data, as well as their conversion to a digital signal. The latter would greatly simplify the process of further analysis of the results of measurements. These tasks can be solved by sharing amplifiers and analog-to-digital converters, which enable the transition to a digital representation of the original analog signal with small amplitude. The paper presents the results of the development of a unified compact model of a Hall sensor fabricated both by standard silicon technology and based on wide- gap semiconductors. The model also provides the ability to account for the material and geometry of the integrated magnetic concentrator (IMC) designed to increase the sensitivity of the sensor. A circuit-based solution consisting of a low- Nghiên cứu khoa học công nghệ Tạp chí Nghiên cứu KH&CN quân sự, Số Đặc san Viện Điện tử, 9 - 2020 197 noise amplifier and an analog-to-digital converter, which allows receiving and processing of sensor data, is developed and topologically realized. 2. SIMULATION TOOLS, INVESTIGATED SENSOR CONSTRUCTIONS AND COMPACT MODEL DESCRIPTION 2.1. Investigated Hall Sensor designs In the calculations presented below, the simulation of the electric characteristics of the Hall sensor was carried out in the Silvaco software environment [4], the IMC parameters were calculated in the FEMM program [5], the Verilog-A [6] language was used to develop the electrical model, and the compact model and circuit solutions were designed and tested using Cadence software [7]. Fig. 1 shows the HS designs that are being investigated. The design presented on the left is a sensor manufactured using standard silicon technology [8], the design on the right is a sensor based on gallium nitride [9]. L W Sapphire (0001) contact AlxGa1-xN GaN AlN Ti/Al/Ni/Au L W n-well depletion layer p-substrate contact n+ n+ oxide t Figure 1. Investigated Hall Sensors designs. 1 2 2 3 θ l d D 4 Figure 2. Modeling determining the parameters of material sample by CST. Kỹ thuật điện tử D. D. Ha, T. T. Trung, “Advanced compact model integrated magnetic sensor systems.” 198 Fig. 2 shows the sensor system design, which includes an IMC. It consists of four HS (2) and an IMC (3) formed on a silicon substrate (1). Four HS are perpendicular to each other along the edges of the IMC. Between the IMC and the HS there is a dielectric layer (4) of thickness d. The IMC is a disk of a ferromagnetic material with a diameter D, a thickness l, and a deflection angle θ. Supermindur which has a high induction of magnetic saturation was used as the IMC material. Earlier studies were carried out to optimize the design and technology, electrical and operational characteristics of presented sensors types within the device-technological simulation [8-10, 12]. 2.2. Advanced compact model of the Hall Sensor Fig. 3 shows an equivalent circuit describing the HS compact. For an ideal design (no technological discrepancy and mechanical stress in the system), the van der Pauw method is used to measure the surface resistance of the RS layer. Since the device is symmetrical, it is necessary to determine the values of the two resistances between the contacts: RD for the resistance between the two opposite and RH for the two adjacent contacts [11]. In comparison with the existing solutions [12], this scheme provides the possibility of taking into account the galvanomagnetic and temperature effects. INPUT CCVS1 CCVS4 CCVS3 CCVS2 RH RD - + - + - + -+ INPUT OUTPUTOUTPUT RD RD RD RH RH RH 2 1 4 3 5 B R Figure 3. Equivalent circuit describing the basic HS compact model. The proposed equivalent circuit has 4 electrical outputs and one external source as input (B) and includes the following components: 8 non-linear resistors designed to describe the dependences of the characteristics of the HS from the magnetic field and temperature; 4 current-controlled voltage sources, which allow estimating the contributions to the Hall voltage of currents flowing through nonlinear resistances; 4 interface blocks for the simulation of series resistances. The parameters of the silicon-based HS compact model [11] are given in Table 1. Nghiên cứu khoa học công nghệ Tạp chí Nghiên cứu KH&CN quân sự, Số Đặc san Viện Điện tử, 9 - 2020 199 The last two lines contain the parameters typical for the hall sensor made on the basis of wide-gap semiconductors. The names of electrical model parameters used in the text are shown in parentheses. To simulate the magnetosensitive sensor with IMC, added the parameters presented in Table 2. Table 1. Silicon based hall sensor model parameters. Parameter Description Unit Value range TEMP Ambient temperature K 248–398 L Length of active area m (30–120)×10-6 W Active Area Width m (10–40)×10-6 S (s) Size of the contact electrode M (9–39)×10-6 TETA (θ) Hall angle radians 0–0.45 RH (rH) The Hall Scattering Coefficient 0.2–1.7 GH (GH) Correction geometric coefficient 0,5–1 NDNW (ND,NW) Concentration of charge carriers in the active region m -3 10 21–1023 NSUB (NSUB) Concentration of charge carriers in a substrate m -3 5×10 20–1021 DEFF (deff) Effective depth of active area m (0.5–5)×10 -6 MOBN (µn) Mobility of electrons in the active region m 2/V∙s 0.072–0.141 MOBH (µh) Mobility of holes in the active region m 2/V∙s 0.032–0.047 RSS (RS) Surface resistance of silicon Ohm 100–15×10 3 RDD (RD) Resistance between two opposite contacts Ohm 650–120×103 RHH (RH) Resistance between two neighboring opposites Ohm 1100–200×103 BBR1 The first coefficient of resistance versus voltage V -1 0–0.01 BBR2 The second coefficient of resistance versus voltage V -2 -0.005–0 BBS1 The first coefficient of sensitivity versus voltage V -1 0–0.01 BBS2 The second coefficient of sensitivity versus voltage V -2 -0.005–0 RTC1 The first temperature coefficient of resistance V -1 0–0.01 RTC2 The second temperature coefficient of resistance V -2 0–0.0005 ALPHA (αSI) Temperature coefficient of sensitivity V -1 0–0.001 NSS (NS) Concentration of charge carriers in 2DEG m -2 10 16–1018 MOBN (µS) Mobility of electrons in 2DEG m 2/V∙s 0.01–1.0 Kỹ thuật điện tử D. D. Ha, T. T. Trung, “Advanced compact model integrated magnetic sensor systems.” 200 Table 2. The compact model parameters of the magnetosensitive sensor with IMC. Parameter Description Unit Value range D Diameter of the concentrator m (50–500)×10-6 t Thickness of concentrator m (5–20)×10-6 Mu0 (µ0) Magnetic permeability (1–100)×10 3 BSAT (Bsat) Magnetic saturation induction Tesla 1–2.8 N Demagnetization factor 0.015–0.15 K Coefficient of magnetic flux 5–20 3. SIMULATION RESULTS 3.1. Device-technological vs. Schematic simulation Fig. 4 and 5 show the results of a comparison between data of device- technological modeling in the software complex Silvaco and data of circuit simulation using the developed compact model a Hall sensor fabricated by standard silicon technology and based on wide-gap semiconductors, respectively. 0 0,2 0,4 0,6 0,8 1,0 150 125 100 75 50 25 0 I , mA V H , m V Device simulation B = 0.25 T B = 0.1 T B = 0.5 T Compact Model B = 0.25 T B = 0.1 T B = 0.5 T Figure 4. The simulated and modeled output Hall voltage VH versus the biasing current at different magnetic field for Silicon Hall sensor. The analysis of the obtained results testifies to the high efficiency of the developed compact model. The error in the data of device-technological and circuit simulation does not exceed 5%. 0,2 0,4 0,6 0,8 1,0 40 35 30 25 10 5 0 I , mA V H , m V 20 Device simulation B = 0.1 T B = 0.5 T Compact Model B = 0.1 T B = 0.5 T B = 0.25 T B = 0.25 T 15 Figure 5. The simulated and modeled output Hall voltage VH versus the biasing current at different magnetic field for GaN Hall sensor. Nghiên cứu khoa học công nghệ Tạp chí Nghiên cứu KH&CN quân sự, Số Đặc san Viện Điện tử, 9 - 2020 201 3.2. Modeling of the sensor signal processing circuit Currently widely used multi-functional integrated sensor systems that are realized by combining the sensor (often multiple) and processing circuitry on a single chip. Such a system-on-chip (SoC) in which the data converter is integrated with the digital signal processing unit in one chip with integrated sensor may be a more effective solution. In comparison with optional discrete chip ADC, this approach can significantly improve the compactness and reduce the cost of production, which is a critical consideration for the sensitive region, medical, mobile, automotive, and other applications. The processing of the sensor signal can be widely classified in terms of signal bandwidth (the rate of change of the measured physical quantity) and the resolution necessary to obtain meaningful information. Typically, the required ADC can be built on the basis of one of two very efficient architectures: a sequential approximation register (SAR) and redundant discrete ADCs Sigma- Delta (SD). Used in our case SAR ADC allows to effectively handle signals with a different frequency range – from a few Hz to hundreds of kHz with a high enough accuracy – 6-8 bits to 20 bits and higher, and also provides high versatility and low power dissipation, making it ideal for these systems. Table 3. 10-bit SAR ADC parameters. Parameter name Designation Value Unit Min Typical Max Temperature T -40 27 85 °C Supply voltage of analog blocks VDDA 1.62 1.8 1.98 V Supply voltage of digital blocks VDDD 1.62 1.8 1.98 V Resolution N 10 bit Clock frequency FCLK 160 MHz Sampling rate FS 10 MHz Sampling time TS ns Reference voltages VREFP 1.25 V VREFN 0.25 V DC level of input signal VCM 0.75 V Input capacitance CIN pF Spurious free dynamic range SFDR 63 dB Signal to noise ratio and distortion SINAD 57 dB Effective number of bits ENOB 9.2 bits Integral nonlinearity INL 1 LSB Differential nonlinearity DNL 0.7 LSB For this system, a topology which contains a system for receiving, amplifying, and sensory data processing based on the Hall sensor as an example on a single chip is developed using the TSMC 0.18 μm CMOS MS/RF 1.8/3.3V PDK. The test circuit used a 10-bit, own designed SAR ADC implemented in silicon using TSMC 0.18 um CMOS MS/RF 1.8/3.3V technology. The topological implementation of the Hall sensor, differential amplifier and ADC are presented in Fig. 6. Kỹ thuật điện tử D. D. Ha, T. T. Trung, “Advanced compact model integrated magnetic sensor systems.” 202 The results of computer simulation in the Cadence software package using the proposed signal processing circuit are presented in Fig. 7 and Table 3. During the simulation, developed and described above compact model was used to simulate the HS electrical characteristics. In Fig. 7 shows: B - magnetic field, VH+, VH- - hall voltage, code - DAC output signal, out - 10-bit ADC output signal. 1 – Hall sensor 2 – Differential amplifier 3 – Voltage reference 4 – ADC 4 31 2 1168 um 7 1 0 u m Figure 6. Topological implementation of Hall sensor, differential amplifier and ADC. 0 500 0 В m T 1,8 0,9V 730 770 750 VH+ VH- m V 0 1,5 0,8 refp refn vcm V data 1,8 0 0,9 code V 0,5 0 out V 1,00,50 2,01,5 3,02,5 4,03,5 4,5 1,0 Time, us Figure 7. The «Hall Sensor – processing circuit» system simulation results. 4. CONCLUSION The advanced compact model of Hall sensor presented in this paper has a simple structure which leads to fast simulations while allowing an accurate description of the behavior of the device. It is made of simple sub-components and does not involve any complex equation. The revision and expending of the model, primarily the mobility, provide the possibility of its use for simulation of Hall sensor based on other materials, for example wide-gap semiconductors and consider the impact of an integrated magnetic concentrator. The results of simulation of the "Hall sensor – processing scheme" system using the developed compact model and signal processing circuit demonstrate the high efficiency of the proposed solutions. Nghiên cứu khoa học công nghệ Tạp chí Nghiên cứu KH&CN quân sự, Số Đặc san Viện Điện tử, 9 - 2020 203 REFERENCES [1]. R. Popovic, "Hall Effect Devices" Institute of Physics Publising. Second Edition. 420 p (2004). [2]. E. Jovanovic, T. Pesic and D. Pantic, "3D simulation of cross-shaped Hall sensor and its equivalent circuit model" Proceedings of the 24th International Conference on Microelectronics, pp. 235-238 (2004). [3]. A. Rossini, F. Borghetti, P. Malcovati, "Behavioral model of magnetic sensors for SPICE simulations", ICECS, pp. 1-4 (2005). [4]. https://www.silvaco.com. [5]. [6]. K. Kundert, "The Designer's Guide to Verilog-AMS" Kluwert Academic Publishers, Boston (2004). [7]. https://www.cadence.com. [8]. H. Dao, A. Belous, V. Saladukha, "Optimization of structural and technological parameters of the field effect Hall sensor". ATC, Vietnam, pp. 642–644 (2015). [9]. V. Stempitsky, Dao Dinh Ha, Tran Tuan Trung. "Suppression of the Self- Heating Effect in AlGaN/GaN High Electron Mobility Transistor by Diamond Heat Sink Layers". ATC, Vietnam, pp. 264–267 (2016). [10]. Dao Dinh Ha, V. Stempitsky, "Investigation of the Hall Sensor Characteristics with Various Geometry of the Active Area", Nano- i Mikrosistemnaya Tekhnika, vol.20, no.3, pp. 174-186 (2018). [11]. Y. Xu and H. Pan, "An Improved Equivalent Simulation Model for CMOS Integrated Hall Plates" Sensors, vol. 11, pp. 6284-6296 (2011). [12]. Dao Dinh Ha, V. Stempitsky, Tran Tuan Trung, "Verilog-A compact model of the silicon Hall element". ICDV. Vietnam, pp. 41-46 (2017). TÓM TẮT MÔ HÌNH TỔNG QUÁT TIÊN TIẾN VÀ MẠCH XỬ LÝ TÍN HIỆU CHO HỆ THỐNG CẢM BIẾN TỪ TRƯỜNG TÍCH HỢP Đề xuất mô hình điện tổng quát của cảm biến Hall, được thiết kế cho mô phỏng mạch, có tính đến các tham số thiết kế và vật liệu sử dụng. Mô hình cảm biến được triển khai theo ngôn ngữ Verilog-A có cấu trúc đơn giản và cho phép mô tả chính xác các đặc tính của cảm biến. Mô hình tương đương được mô tả dựa trên các thành phần mạch điện tiêu chuẩn và không sử dụng các phương trình phức tạp để mô tả các quá trình vật lý diễn ra trong cấu trúc cảm biến. Thiết kế một cấu trúc mạch bao gồm cảm biến Hall, mạch khuếch đại và mạch chuyển đổi tín hiệu tương tự-số 10 bit tích hợp trên chip sử dụng thư viện thiết kế TSMC 0.18 um CMOS MS/RF 1,8/3,3V PDK cho phép nhận và xử lý tín hiệu của các thiết bị cảm biến. Từ khóa: Cảm biến Hall, Mô hình nhỏ gọn; Verilog-A; Mạch xử lý tín hiệu; Mạch chuyển đổi tương tự-số. Received 20 th April 2020 Revised 21 th August 2020 Published 28 th August 2020 Author affiliations: 1 Le Quy Don Technical University; 2 Academy of Military Science and Technology. *Corresponding author: havixuly@gmail.com.
File đính kèm:
advanced_compact_model_and_processing_circuit_for_integrated.pdf