Solving heat transfer problem in ultrasonic welding based on hybrid spline difference method
A Hybrid Spline Difference Method is developed to solve a nonlinear equation of welding problem
in ultrasonic welding. It is shown that the method has a computational procedure as simply as the finite
difference method. In addition, the proposed method can simplify complexity of the traditional spline
method calculation, and increase accuracy of the first and second derivatives of space from O(Tx 2) of
finite difference method to O(Tx 4). According to the calculated temperature distribution in the work pieces,
during the ultrasonic welding process, the proposed method illustrated that not only its precision is greatly
enhanced, but also its concept is very similar to that of the finite difference method. Based on analysis
results, it was concluded that the simple and high-accuracy hybrid spline difference method has a strong
potential to substitute the traditional finite difference method.
Keywords: ultrasonic metal welding, hybrid spline difference method, finite difference method.
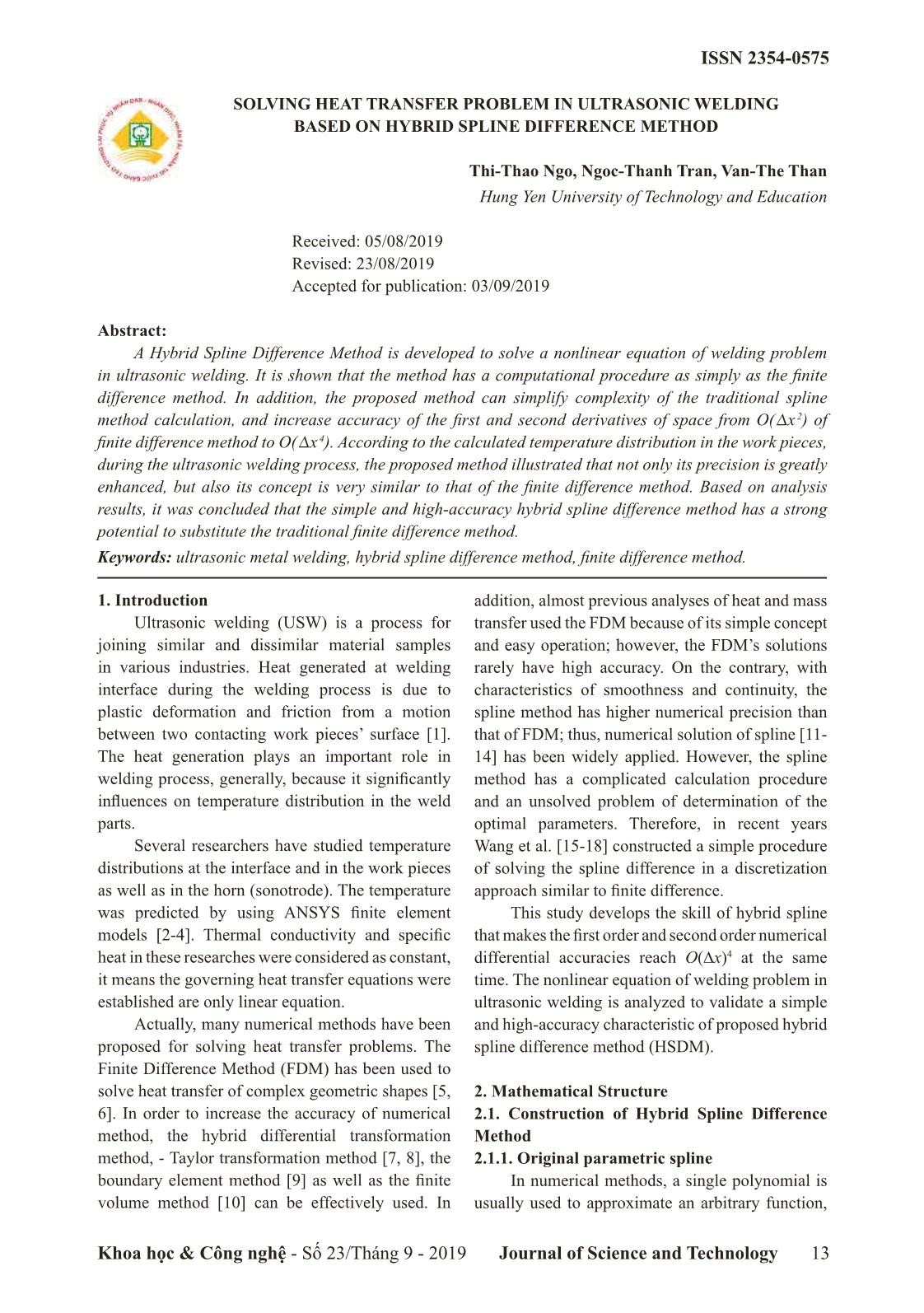
Trang 1
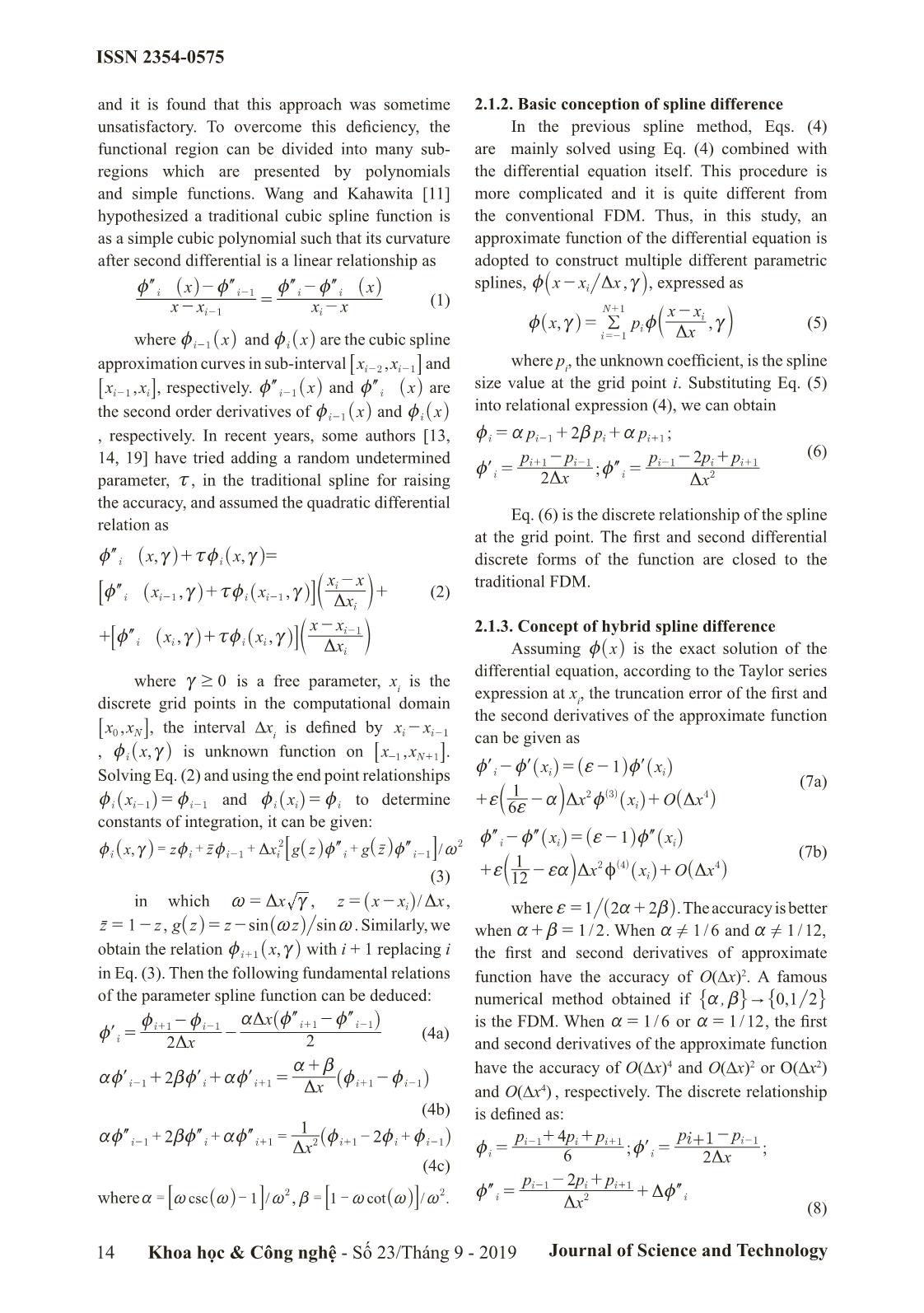
Trang 2
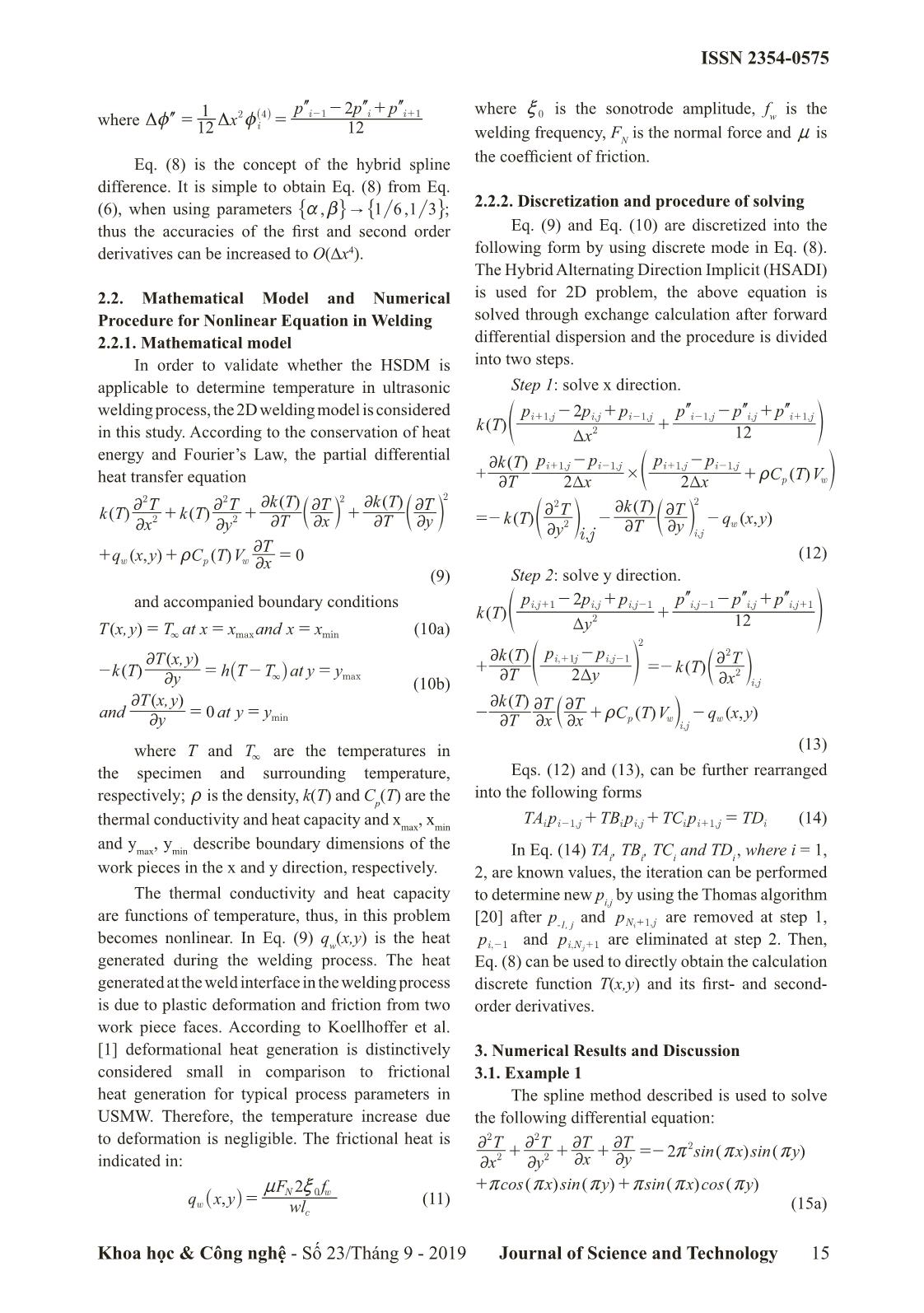
Trang 3
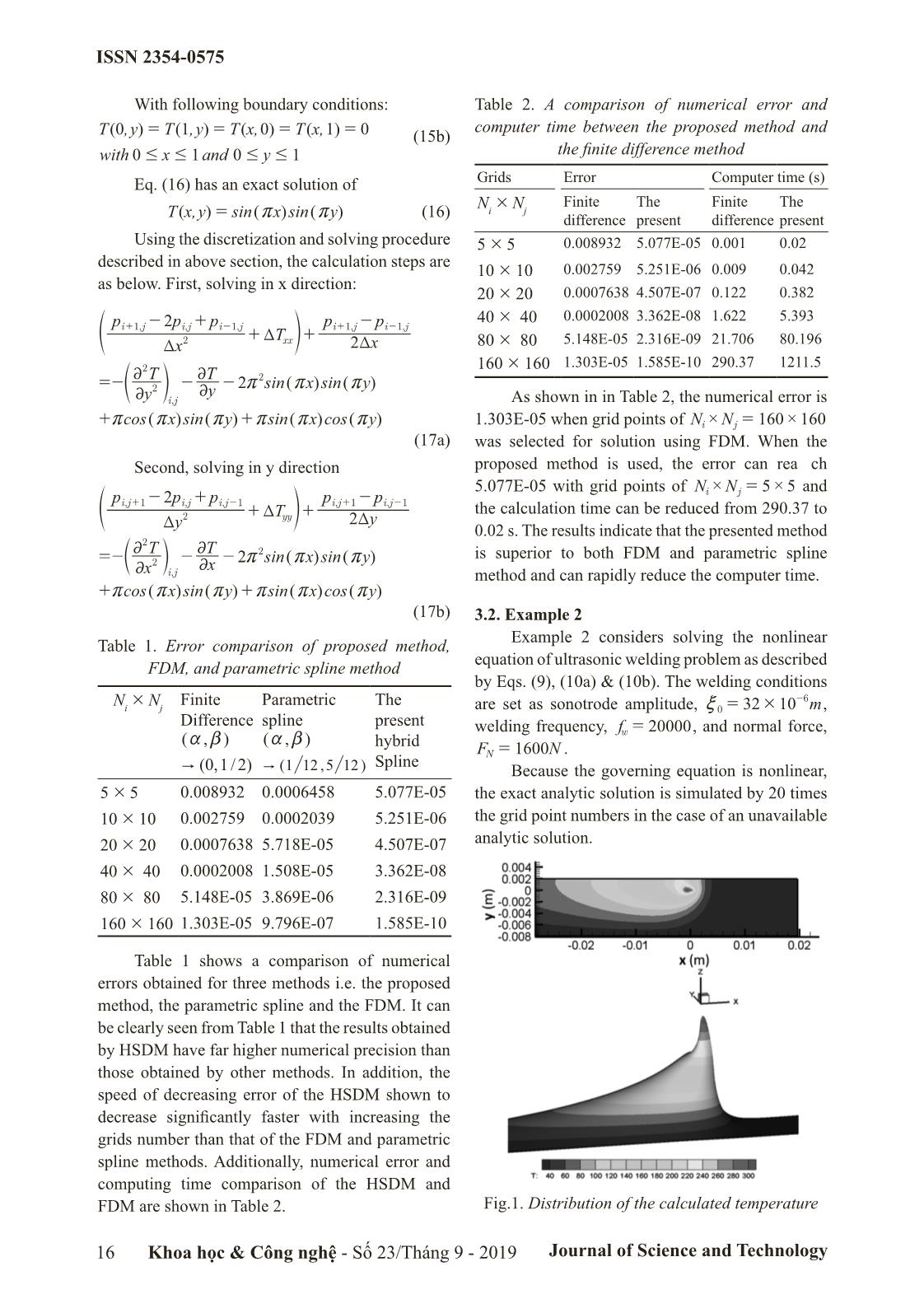
Trang 4
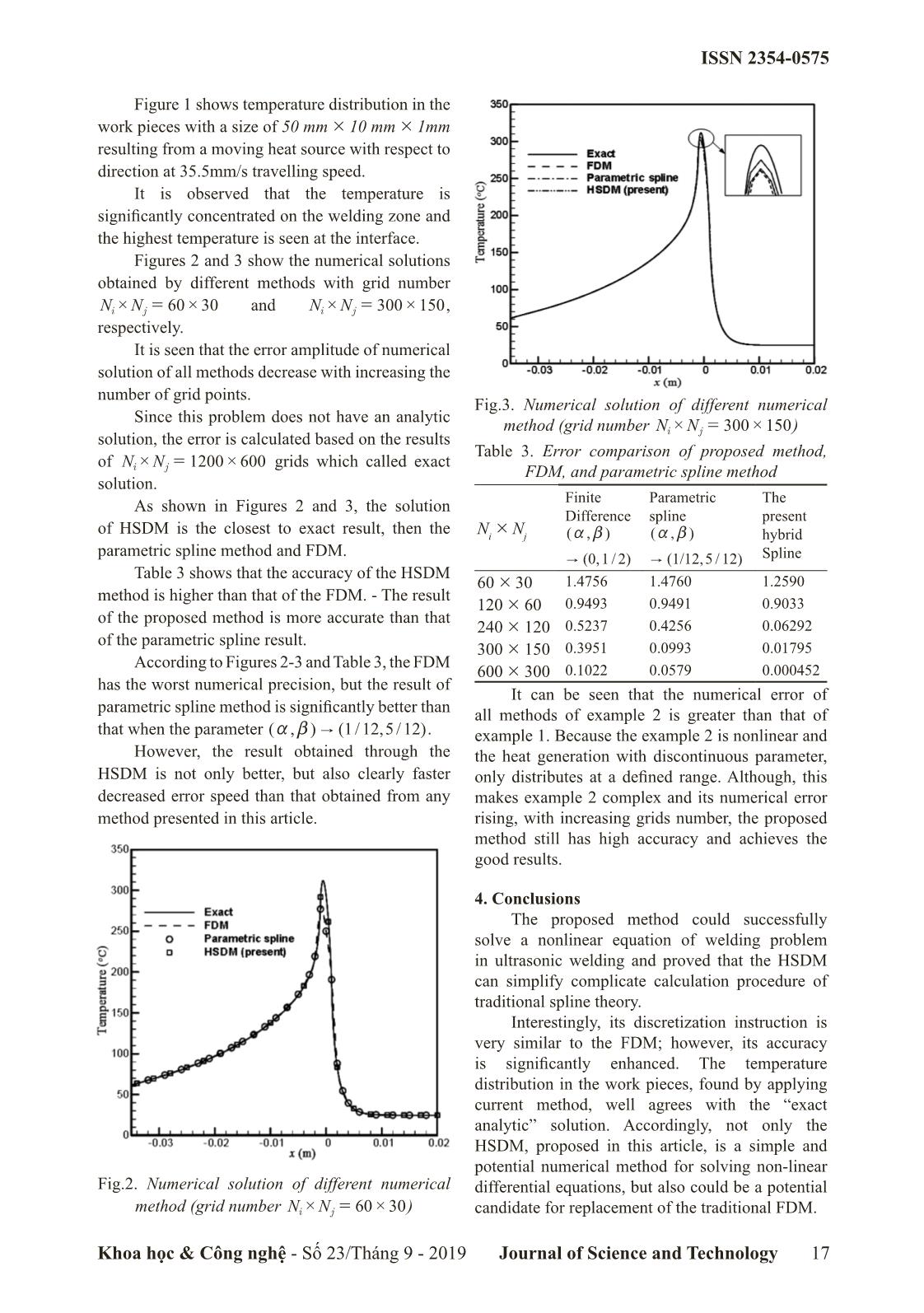
Trang 5
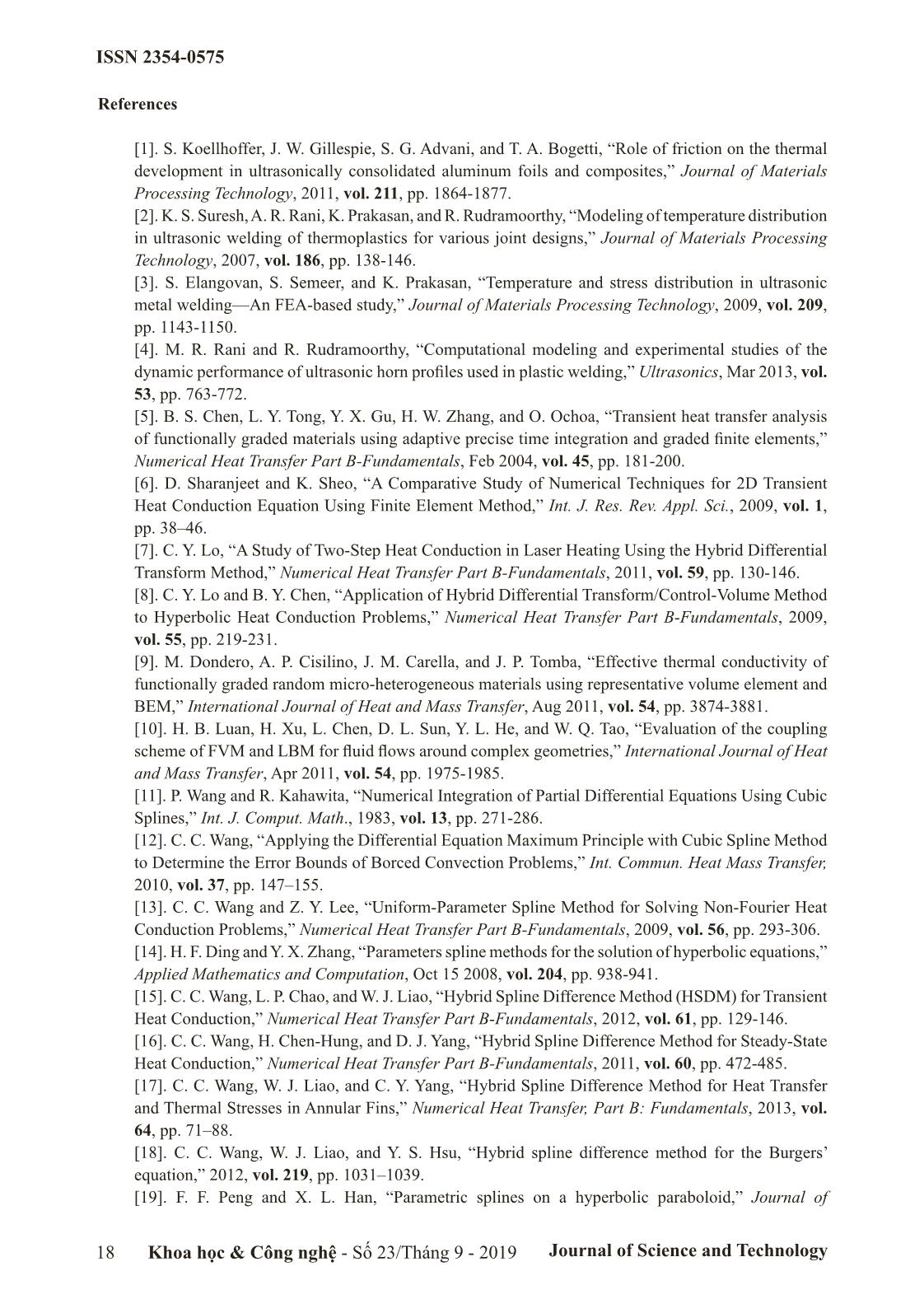
Trang 6
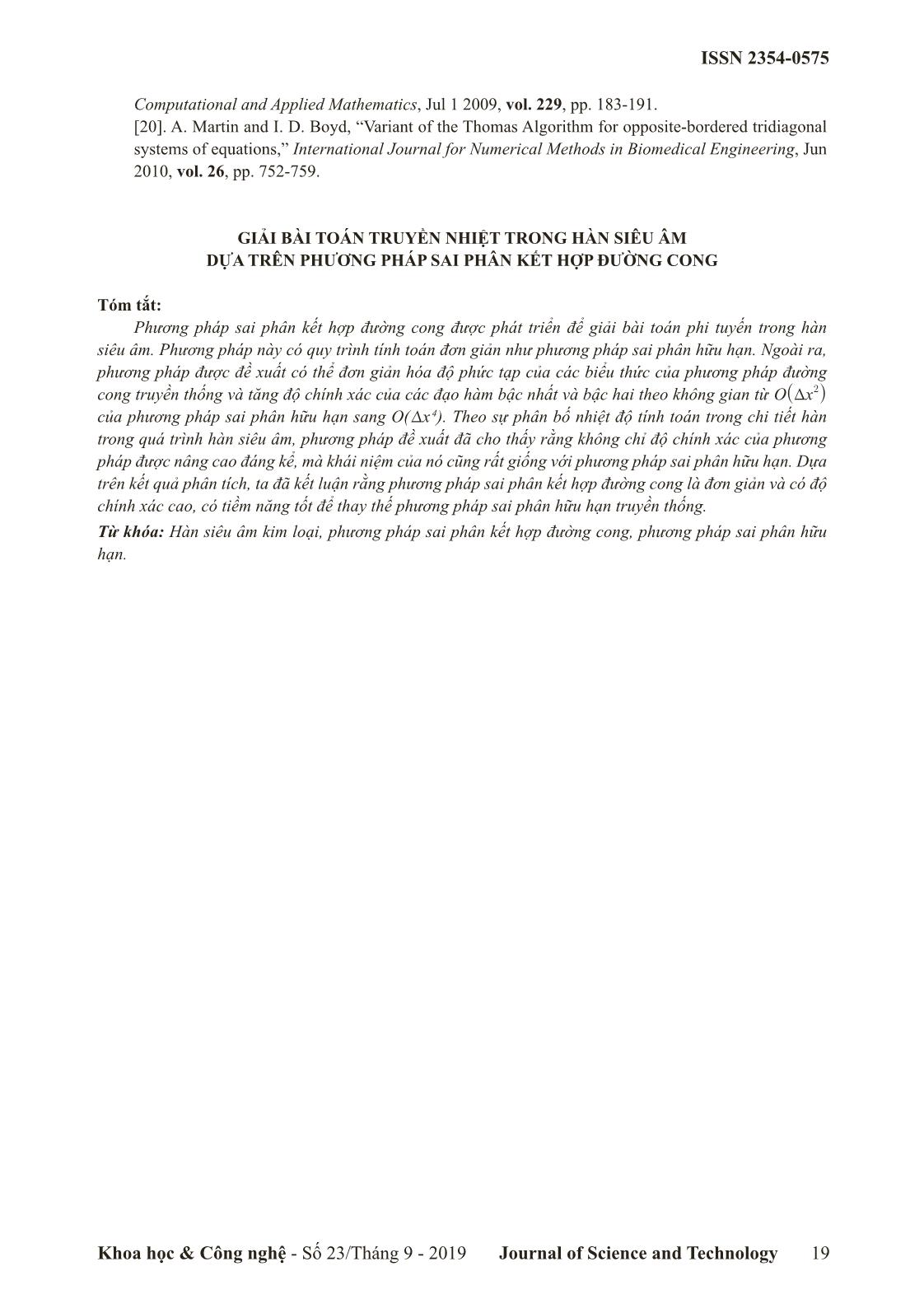
Trang 7
Tóm tắt nội dung tài liệu: Solving heat transfer problem in ultrasonic welding based on hybrid spline difference method
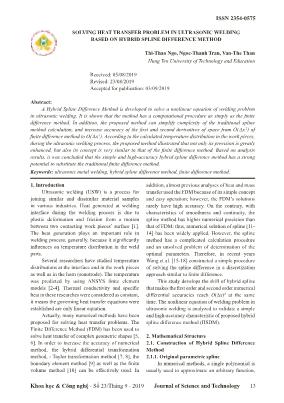
ISSN 2354-0575 SOLVING HEAT TRANSFER PROBLEM IN ULTRASONIC WELDING BASED ON HYBRID SPLINE DIFFERENCE METHOD Thi-Thao Ngo, Ngoc-Thanh Tran, Van-The Than Hung Yen University of Technology and Education Received: 05/08/2019 Revised: 23/08/2019 Accepted for publication: 03/09/2019 Abstract: A Hybrid Spline Difference Method is developed to solve a nonlinear equation of welding problem in ultrasonic welding. It is shown that the method has a computational procedure as simply as the finite difference method. In addition, the proposed method can simplify complexity of the traditional spline method calculation, and increase accuracy of the first and second derivatives of space from O(Tx 2) of finite difference method to O(Tx 4). According to the calculated temperature distribution in the work pieces, during the ultrasonic welding process, the proposed method illustrated that not only its precision is greatly enhanced, but also its concept is very similar to that of the finite difference method. Based on analysis results, it was concluded that the simple and high-accuracy hybrid spline difference method has a strong potential to substitute the traditional finite difference method. Keywords: ultrasonic metal welding, hybrid spline difference method, finite difference method. 1. Introduction addition, almost previous analyses of heat and mass Ultrasonic welding (USW) is a process for transfer used the FDM because of its simple concept joining similar and dissimilar material samples and easy operation; however, the FDM’s solutions in various industries. Heat generated at welding rarely have high accuracy. On the contrary, with interface during the welding process is due to characteristics of smoothness and continuity, the plastic deformation and friction from a motion spline method has higher numerical precision than between two contacting work pieces’ surface [1]. that of FDM; thus, numerical solution of spline [11- The heat generation plays an important role in 14] has been widely applied. However, the spline welding process, generally, because it significantly method has a complicated calculation procedure influences on temperature distribution in the weld and an unsolved problem of determination of the parts. optimal parameters. Therefore, in recent years Several researchers have studied temperature Wang et al. [15-18] constructed a simple procedure distributions at the interface and in the work pieces of solving the spline difference in a discretization as well as in the horn (sonotrode). The temperature approach similar to finite difference. was predicted by using ANSYS finite element This study develops the skill of hybrid spline models [2-4]. Thermal conductivity and specific that makes the first order and second order numerical heat in these researches were considered as constant, differential accuracies reach O(∆x)4 at the same it means the governing heat transfer equations were time. The nonlinear equation of welding problem in established are only linear equation. ultrasonic welding is analyzed to validate a simple Actually, many numerical methods have been and high-accuracy characteristic of proposed hybrid proposed for solving heat transfer problems. The spline difference method (HSDM). Finite Difference Method (FDM) has been used to solve heat transfer of complex geometric shapes [5, 2. Mathematical Structure 6]. In order to increase the accuracy of numerical 2.1. Construction of Hybrid Spline Difference method, the hybrid differential transformation Method method, - Taylor transformation method [7, 8], the 2.1.1. Original parametric spline boundary element method [9] as well as the finite In numerical methods, a single polynomial is volume method [10] can be effectively used. In usually used to approximate an arbitrary function, Khoa học & Công nghệ - Số 23/Tháng 9 - 2019 Journal of Science and Technology 13 ISSN 2354-0575 and it is found that this approach was sometime 2.1.2. Basic conception of spline difference unsatisfactory. To overcome this deficiency, the In the previous spline method, Eqs. (4) functional region can be divided into many sub- are mainly solved using Eq. (4) combined with regions which are presented by polynomials the differential equation itself. This procedure is and simple functions. Wang and Kahawita [11] more complicated and it is quite different from hypothesized a traditional cubic spline function is the conventional FDM. Thus, in this study, an as a simple cubic polynomial such that its curvature approximate function of the differential equation is after second differential is a linear relationship as adopted to construct multiple different parametric zzmmx - zzmm- x splines, zcxx- i Dx , , expressed as ii__ii-1 = ii `j - - (1) N+1 xxi-1 xxi xx- i zcxp,,= / i zc (5) where z x and z x are the cubic spline _ i i =-1 b Dx l i-1 _i i _i approximation curves i ... M is into two steps. applicable to determine temperature in ultrasonic Step 1: solve x direction. 2 welding process, the 2D welding model is considered ppij+-11,,-+ij ppij,,mmij-+11-+ppij,,mij kT() + in this study. According to the conservation of heat f Tx2 12 p energy and Fourier’s Law, the partial differential 2kT()ppij+-11,,--ij ppij+-11,,ij + # + t () heat transfer equation 2T 22TTx e x CTpwV o 2 2 2T 222T 2kT()2T 2kT()2T 2 2 () 2 kT() ++kT() + ()2 T kT 2T (,) 2x2 2y2 2T 2x 2T d 2y n =-kT 2 --2 2 qxw y b l e 2y oij, T d y nij, 2 ++(,)(t ) T = 0 (12) qxwpyCTVw 2x (9) Step 2: solve y direction. 2 and accompanied boundary conditions ppij,,+-11-+ij ppij,,mmij-+11-+ppij,,mij kT() + () f Ty2 12 p Tx,yT==3 at xxmaxmand xx= in (10a) 2 () 2 2 () 2kT ppij,,+-11- ij 2 T () Tx,y + =-kT() -=kT hT-=Ta3 ty ymax 2T f 2Ty p 2 2y _i (10b) d 2x nij, 2 () 2 () Tx,y 0 kT 2T 2T () (,) and ==at yymin -+tCTpwVq- w xy 2y 2T 2x b 2x lij, (13) where T and T3 are the temperatures in the specimen and surrounding temperature, Eqs. (12) and (13), can be further rearranged into the following forms respectively; t is the density, k(T) and Cp(T) are the ++ = (14) thermal conductivity and heat capacity and xmax, xmin TAiipT-+11,,jiBpij TCiipT,jiD and ymax, ymin describe boundary dimensions of the In Eq. (14) TAi, TBi, TCi and TDi , where i = 1, work pieces in the x and y direction, respectively. 2, are known values, the iteration can be performed The thermal conductivity and heat capacity to determine new pi,j by using the Thomas algorithm are functions of temperature, thus, in this problem [20] after p-1, j and pNji +1, are removed at step 1, becomes nonlinear. In Eq. (9) qw(x,y) is the heat pi,-1 and piN, j +1 are eliminated at step 2. Then, generated during the welding process. The heat Eq. (8) can be used to directly obtain the calculation generated at the weld interface in the welding process discrete function T(x,y) and its first- and second- is due to plastic deformation and friction from two order derivatives. work piece faces. According to Koellhoffer et al. [1] deformational heat generation is distinctively 3. Numerical Results and Discussion considered small in comparison to frictional 3.1. Example 1 heat generation for typical process parameters in The spline method described is used to solve USMW. Therefore, the temperature increase due the following differential equation: 2 2 to deformation is negligible. The frictional heat is 2 T 2 T 2T 2T 2 +++=- 2rrsinx()siny()r indicated in: 2x2 2y2 2x 2y 2 ++rrcosx()siny()rrsinx()rrcosy() , npFfNw0 qxw y = (11) _i wlc (15a) Khoa học & Công nghệ - Số 23/Tháng 9 - 2019 Journal of Science and Technology 15 ISSN 2354-0575 With following boundary conditions: Table 2. A comparison of numerical error and ()01() ()01()0 computer time between the proposed method and Ty,,====Ty Tx,,Tx (15b) with 01##x and 01##y the finite difference method Eq. (16) has an exact solution of Grids Error Computer time (s) N # N Finite The Finite The ()= ()rr() i j Tx,ysin xsin y (16) difference present difference present Using the discretization and solving procedure 5 # 5 0.008932 5.077E-05 0.001 0.02 described in above section, the calculation steps are 10 # 10 0.002759 5.251E-06 0.009 0.042 as below. First, solving in x direction: 20 # 20 0.0007638 4.507E-07 0.122 0.382 2 # 0.0002008 3.362E-08 1.622 5.393 ppij+-11,,-+ij pij,,ppij+-11- ij, 40 40 ++TT f Tx2 xx p 2Tx 80 # 80 5.148E-05 2.316E-09 21.706 80.196 # 1.303E-05 1.585E-10 290.37 1211.5 22 2 160 160 =- T --T 2rr2 ()()r 2 2y sinxsiny e 2y oij, As shown in in Table 2, the numerical error is ()() () () 160 160 ++rrcosxsinyrrsinxrrcosy 1.303E-05 when grid points of NNij##= (17a) was selected for solution using FDM. When the Second, solving in y direction proposed method is used, the error can rea ch ## 2 5.077E-05 with grid points of NNij= 5 5 and ppij,,+-11-+ij pij,,ppij+-11- ij, ++TT the calculation time can be reduced from 290.37 to f Ty2 yy p 2Ty 0.02 s. The results indicate that the presented method 2 2 T 2T 2 =- --2rrsinx()siny()r is superior to both FDM and parametric spline 2 2 2x d x nij, method and can rapidly reduce the computer time. ++rrcosx()siny()rrsinx()rrcosy() (17b) 3.2. Example 2 Example 2 considers solving the nonlinear Table 1. Error comparison of proposed method, equation of ultrasonic welding problem as described FDM, and parametric spline method by Eqs. (9), (10a) & (10b). The welding conditions # 32 10-6 Ni Nj Finite Parametric The are set as sonotrode amplitude, p0 = # m, Difference spline present = 20000 (,) (,) welding frequency, fw , and normal force, ab ab hybrid 1600 FNN = . " (,01/)2 " (,112512 ) Spline Because the governing equation is nonlinear, 5 # 5 0.008932 0.0006458 5.077E-05 the exact analytic solution is simulated by 20 times 10 # 10 0.002759 0.0002039 5.251E-06 the grid point numbers in the case of an unavailable 20 # 20 0.0007638 5.718E-05 4.507E-07 analytic solution. 40 # 40 0.0002008 1.508E-05 3.362E-08 80 # 80 5.148E-05 3.869E-06 2.316E-09 160 # 160 1.303E-05 9.796E-07 1.585E-10 Table 1 shows a comparison of numerical errors obtained for three methods i.e. the proposed method, the parametric spline and the FDM. It can be clearly seen from Table 1 that the results obtained by HSDM have far higher numerical precision than those obtained by other methods. In addition, the speed of decreasing error of the HSDM shown to decrease significantly faster with increasing the grids number than that of the FDM and parametric spline methods. Additionally, numerical error and computing time comparison of the HSDM and FDM are shown in Table 2. Fig.1. Distribution of the calculated temperature 16 Khoa học & Công nghệ - Số 23/Tháng 9 - 2019 Journal of Science and Technology ISSN 2354-0575 Figure 1 shows temperature distribution in the work pieces with a size of 50 mm # 10 mm # 1mm resulting from a moving heat source with respect to direction at 35.5mm/s travelling speed. It is observed that the temperature is significantly concentrated on the welding zone and the highest temperature is seen at the interface. Figures 2 and 3 show the numerical solutions obtained by different methods with grid number 60 30 300 150 NNij##= and NNij##= , respectively. It is seen that the error amplitude of numerical solution of all methods decrease with increasing the number of grid points. Fig.3. Numerical solution of different numerical Since this problem does not have an analytic 300 150 method (grid number NNij##= ) solution, the error is calculated based on the results Table 3. Error comparison of proposed method, of NN##= 1200 600 grids which called exact ij FDM, and parametric spline method solution. Finite Parametric The As shown in Figures 2 and 3, the solution Difference spline present of HSDM is the closest to exact result, then the N # N (,ab) (,ab) i j hybrid parametric spline method and FDM. " (,01/)2 " (,1/12 51/)2 Spline Table 3 shows that the accuracy of the HSDM 60 # 30 1.4756 1.4760 1.2590 method is higher than that of the FDM. - The result 120 # 60 0.9493 0.9491 0.9033 of the proposed method is more accurate than that 240 # 120 0.5237 0.4256 0.06292 of the parametric spline result. 300 # 150 0.3951 0.0993 0.01795 According to Figures 2-3 and Table 3, the FDM 600 # 300 0.1022 0.0579 0.000452 has the worst numerical precision, but the result of It can be seen that the numerical error of parametric spline method is significantly better than all methods of example 2 is greater than that of (,)(" 11/,25/)12 that when the parameter ab . example 1. Because the example 2 is nonlinear and However, the result obtained through the the heat generation with discontinuous parameter, HSDM is not only better, but also clearly faster only distributes at a defined range. Although, this decreased error speed than that obtained from any makes example 2 complex and its numerical error method presented in this article. rising, with increasing grids number, the proposed method still has high accuracy and achieves the good results. 4. Conclusions The proposed method could successfully solve a nonlinear equation of welding problem in ultrasonic welding and proved that the HSDM can simplify complicate calculation procedure of traditional spline theory. Interestingly, its discretization instruction is very similar to the FDM; however, its accuracy is significantly enhanced. The temperature distribution in the work pieces, found by applying current method, well agrees with the “exact analytic” solution. Accordingly, not only the HSDM, proposed in this article, is a simple and potential numerical method for solving non-linear Fig.2. Numerical solution of different numerical differential equations, but also could be a potential ##60 30 method (grid number NNij= ) candidate for replacement of the traditional FDM. Khoa học & Công nghệ - Số 23/Tháng 9 - 2019 Journal of Science and Technology 17 ISSN 2354-0575 References [1]. S. Koellhoffer, J. W. Gillespie, S. G. Advani, and T. A. Bogetti, “Role of friction on the thermal development in ultrasonically consolidated aluminum foils and composites,” Journal of Materials Processing Technology, 2011, vol. 211, pp. 1864-1877. [2]. K. S. Suresh, A. R. Rani, K. Prakasan, and R. Rudramoorthy, “Modeling of temperature distribution in ultrasonic welding of thermoplastics for various joint designs,” Journal of Materials Processing Technology, 2007, vol. 186, pp. 138-146. [3]. S. Elangovan, S. Semeer, and K. Prakasan, “Temperature and stress distribution in ultrasonic metal welding—An FEA-based study,” Journal of Materials Processing Technology, 2009, vol. 209, pp. 1143-1150. [4]. M. R. Rani and R. Rudramoorthy, “Computational modeling and experimental studies of the dynamic performance of ultrasonic horn profiles used in plastic welding,”Ultrasonics , Mar 2013, vol. 53, pp. 763-772. [5]. B. S. Chen, L. Y. Tong, Y. X. Gu, H. W. Zhang, and O. Ochoa, “Transient heat transfer analysis of functionally graded materials using adaptive precise time integration and graded finite elements,” Numerical Heat Transfer Part B-Fundamentals, Feb 2004, vol. 45, pp. 181-200. [6]. D. Sharanjeet and K. Sheo, “A Comparative Study of Numerical Techniques for 2D Transient Heat Conduction Equation Using Finite Element Method,” Int. J. Res. Rev. Appl. Sci., 2009, vol. 1, pp. 38–46. [7]. C. Y. Lo, “A Study of Two-Step Heat Conduction in Laser Heating Using the Hybrid Differential Transform Method,” Numerical Heat Transfer Part B-Fundamentals, 2011, vol. 59, pp. 130-146. [8]. C. Y. Lo and B. Y. Chen, “Application of Hybrid Differential Transform/Control-Volume Method to Hyperbolic Heat Conduction Problems,” Numerical Heat Transfer Part B-Fundamentals, 2009, vol. 55, pp. 219-231. [9]. M. Dondero, A. P. Cisilino, J. M. Carella, and J. P. Tomba, “Effective thermal conductivity of functionally graded random micro-heterogeneous materials using representative volume element and BEM,” International Journal of Heat and Mass Transfer, Aug 2011, vol. 54, pp. 3874-3881. [10]. H. B. Luan, H. Xu, L. Chen, D. L. Sun, Y. L. He, and W. Q. Tao, “Evaluation of the coupling scheme of FVM and LBM for fluid flows around complex geometries,”International Journal of Heat and Mass Transfer, Apr 2011, vol. 54, pp. 1975-1985. [11]. P. Wang and R. Kahawita, “Numerical Integration of Partial Differential Equations Using Cubic Splines,” Int. J. Comput. Math., 1983, vol. 13, pp. 271-286. [12]. C. C. Wang, “Applying the Differential Equation Maximum Principle with Cubic Spline Method to Determine the Error Bounds of Borced Convection Problems,” Int. Commun. Heat Mass Transfer, 2010, vol. 37, pp. 147–155. [13]. C. C. Wang and Z. Y. Lee, “Uniform-Parameter Spline Method for Solving Non-Fourier Heat Conduction Problems,” Numerical Heat Transfer Part B-Fundamentals, 2009, vol. 56, pp. 293-306. [14]. H. F. Ding and Y. X. Zhang, “Parameters spline methods for the solution of hyperbolic equations,” Applied Mathematics and Computation, Oct 15 2008, vol. 204, pp. 938-941. [15]. C. C. Wang, L. P. Chao, and W. J. Liao, “Hybrid Spline Difference Method (HSDM) for Transient Heat Conduction,” Numerical Heat Transfer Part B-Fundamentals, 2012, vol. 61, pp. 129-146. [16]. C. C. Wang, H. Chen-Hung, and D. J. Yang, “Hybrid Spline Difference Method for Steady-State Heat Conduction,” Numerical Heat Transfer Part B-Fundamentals, 2011, vol. 60, pp. 472-485. [17]. C. C. Wang, W. J. Liao, and C. Y. Yang, “Hybrid Spline Difference Method for Heat Transfer and Thermal Stresses in Annular Fins,” Numerical Heat Transfer, Part B: Fundamentals, 2013, vol. 64, pp. 71–88. [18]. C. C. Wang, W. J. Liao, and Y. S. Hsu, “Hybrid spline difference method for the Burgers’ equation,” 2012, vol. 219, pp. 1031–1039. [19]. F. F. Peng and X. L. Han, “Parametric splines on a hyperbolic paraboloid,” Journal of 18 Khoa học & Công nghệ - Số 23/Tháng 9 - 2019 Journal of Science and Technology ISSN 2354-0575 Computational and Applied Mathematics, Jul 1 2009, vol. 229, pp. 183-191. [20]. A. Martin and I. D. Boyd, “Variant of the Thomas Algorithm for opposite-bordered tridiagonal systems of equations,” International Journal for Numerical Methods in Biomedical Engineering, Jun 2010, vol. 26, pp. 752-759. GIẢI BÀI TOÁN TRUYỀN NHIỆT TRONG HÀN SIÊU ÂM DỰA TRÊN PHƯƠNG PHÁP SAI PHÂN KẾT HỢP ĐƯỜNG CONG Tóm tắt: Phương pháp sai phân kết hợp đường cong được phát triển để giải bài toán phi tuyến trong hàn siêu âm. Phương pháp này có quy trình tính toán đơn giản như phương pháp sai phân hữu hạn. Ngoài ra, phương pháp được đề xuất có thể đơn giản hóa độ phức tạp của các biểu thức của phương pháp đường cong truyền thống và tăng độ chính xác của các đạo hàm bậc nhất và bậc hai theo không gian từ OxT 2 _i của phương pháp sai phân hữu hạn sang O(Tx 4). Theo sự phân bố nhiệt độ tính toán trong chi tiết hàn trong quá trình hàn siêu âm, phương pháp đề xuất đã cho thấy rằng không chỉ độ chính xác của phương pháp được nâng cao đáng kể, mà khái niệm của nó cũng rất giống với phương pháp sai phân hữu hạn. Dựa trên kết quả phân tích, ta đã kết luận rằng phương pháp sai phân kết hợp đường cong là đơn giản và có độ chính xác cao, có tiềm năng tốt để thay thế phương pháp sai phân hữu hạn truyền thống. Từ khóa: Hàn siêu âm kim loại, phương pháp sai phân kết hợp đường cong, phương pháp sai phân hữu hạn. Khoa học & Công nghệ - Số 23/Tháng 9 - 2019 Journal of Science and Technology 19
File đính kèm:
solving_heat_transfer_problem_in_ultrasonic_welding_based_on.pdf