Optimal parameters of linear dynamic vibration absorber for reduction of torsional vibration
The*dynamic vibration absorber (DVA) or tunedmass damper (TMD) is a widely used passive vibration
control device. When a mass-spring system, referred to
as primary system, is subjected to a harmonic excitation
at a constant frequency, its steady-state response can be
suppressed by attaching a secondary mass-spring
system or DVA. This idea was pioneered by Watts in
1883 and Frahm in 1909. However, a DVA consisting
of only a mass and spring has a narrow operation region
and its performance deteriorates significantly when the
exciting frequency varies. The performance robustness
can be improved by using a damped DVA that consists
of a mass, spring, and damper. The key design
parameters of a damped DVA are its tuning parameter
and damping ratio.
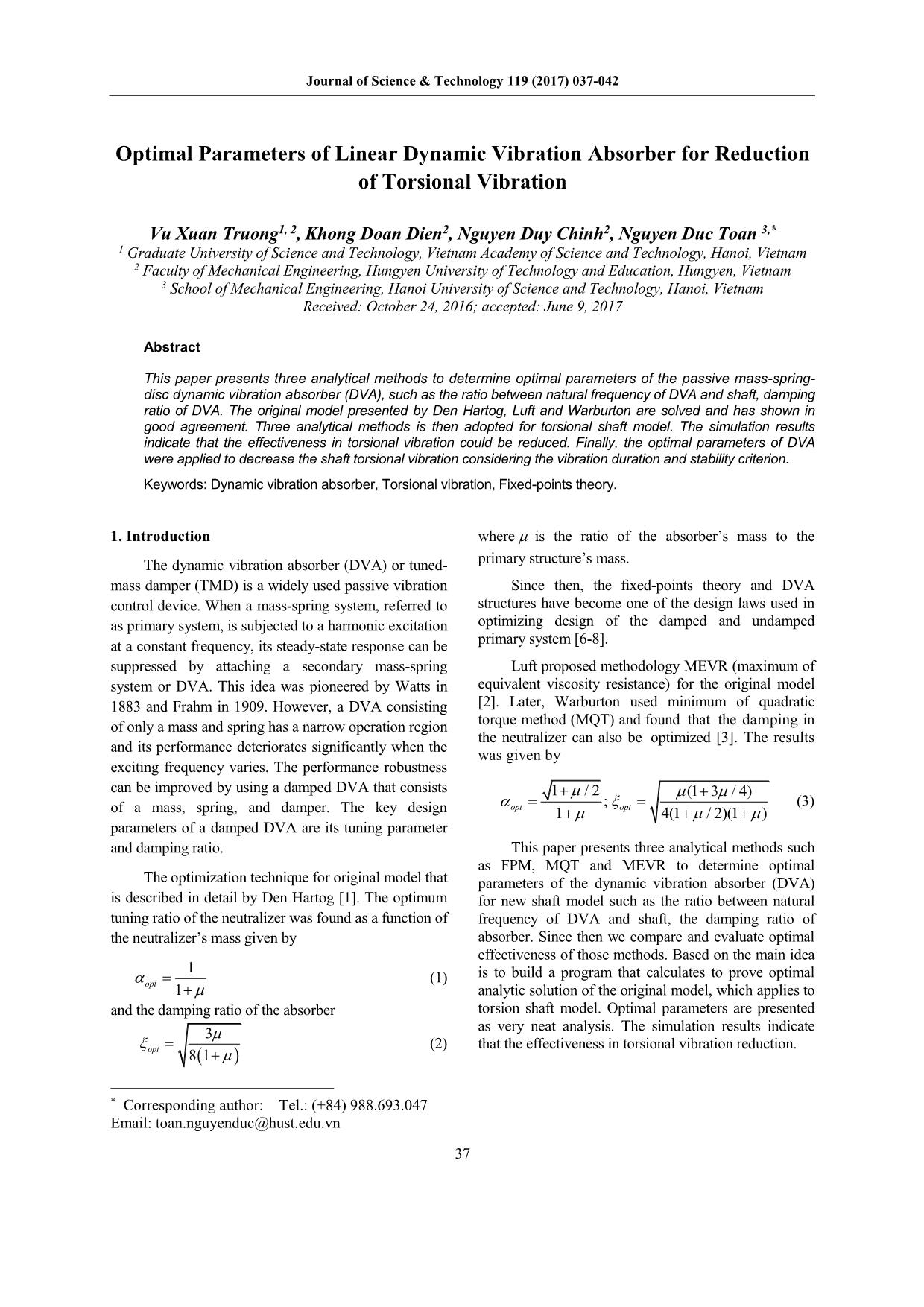
Trang 1
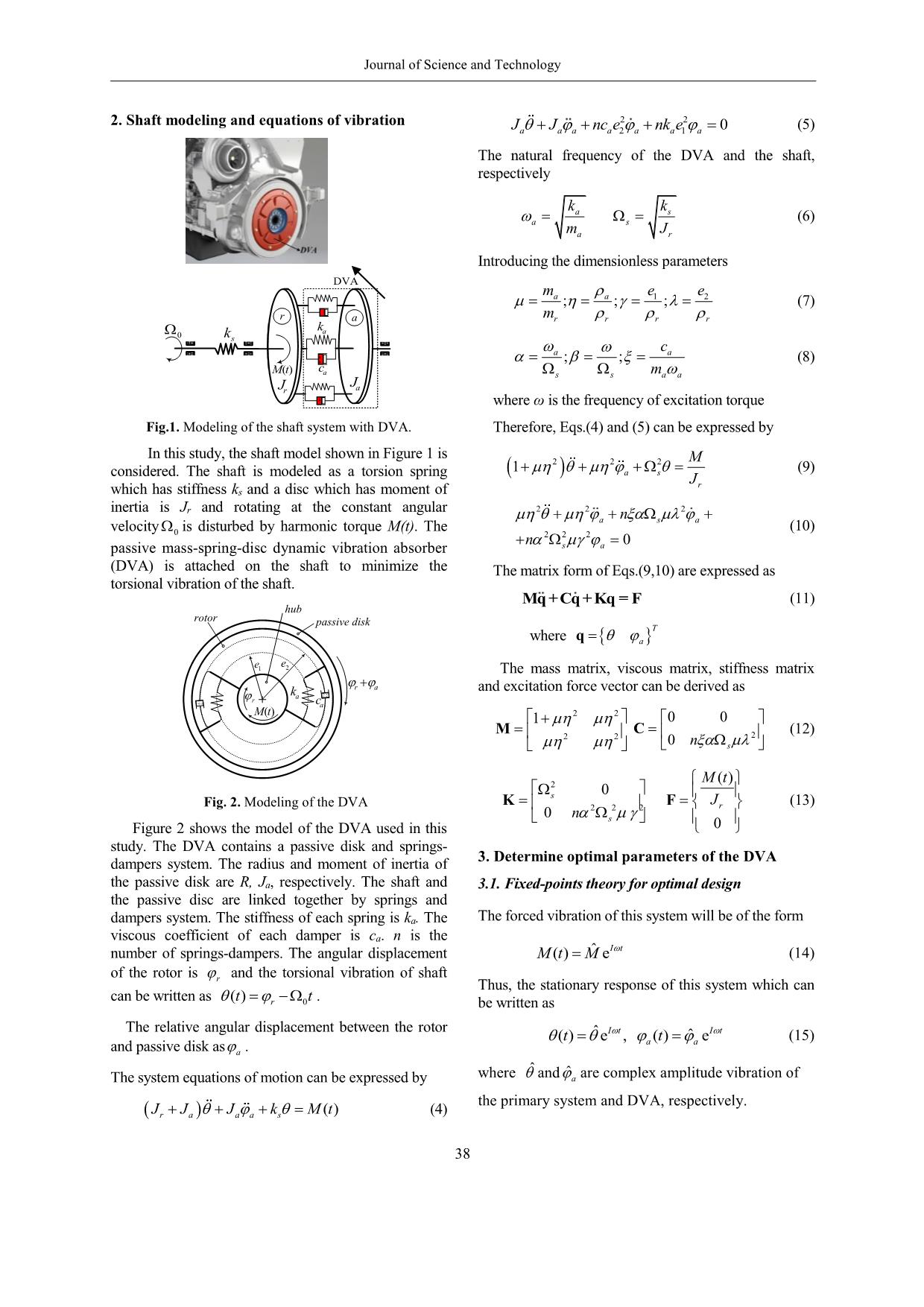
Trang 2
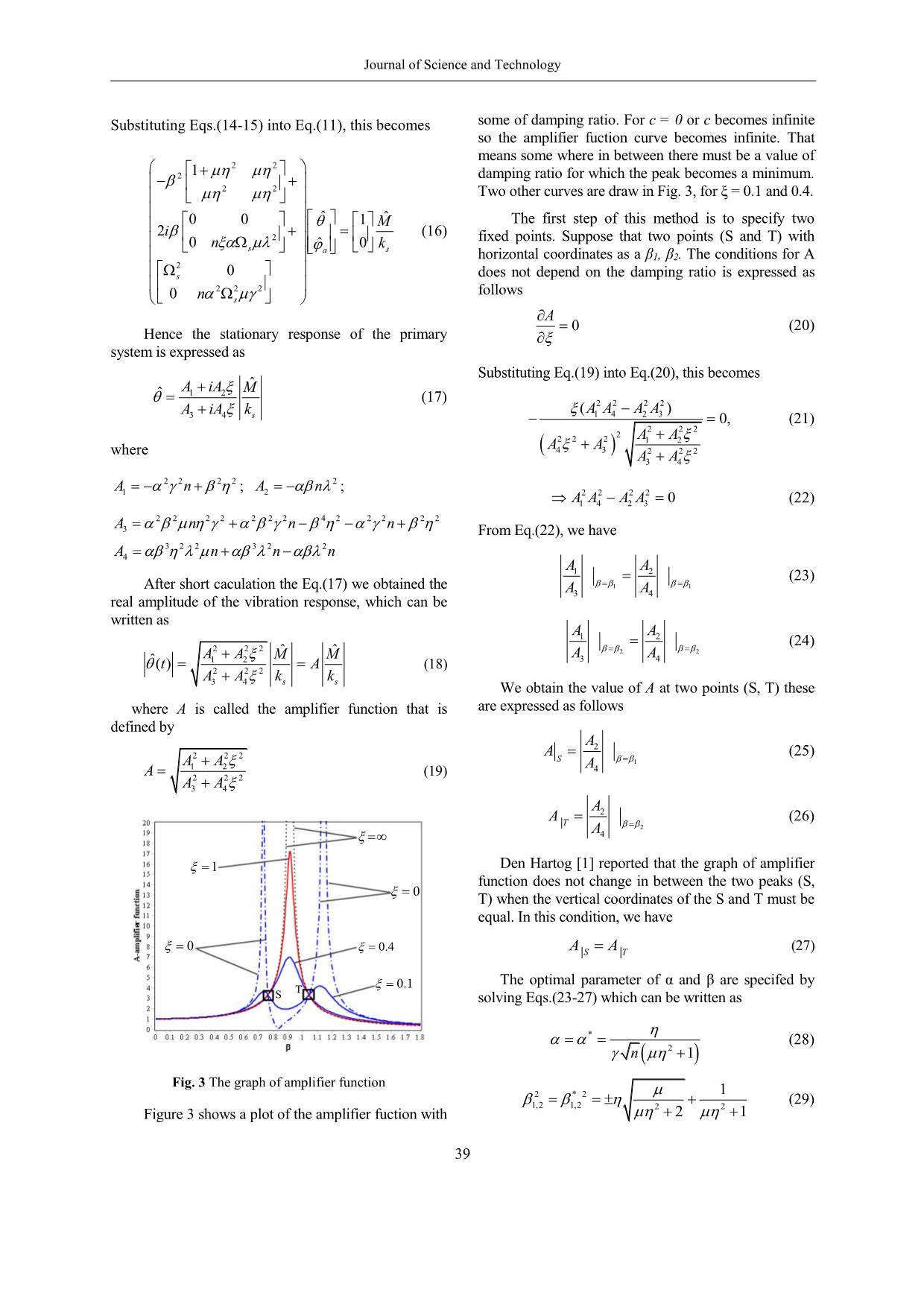
Trang 3
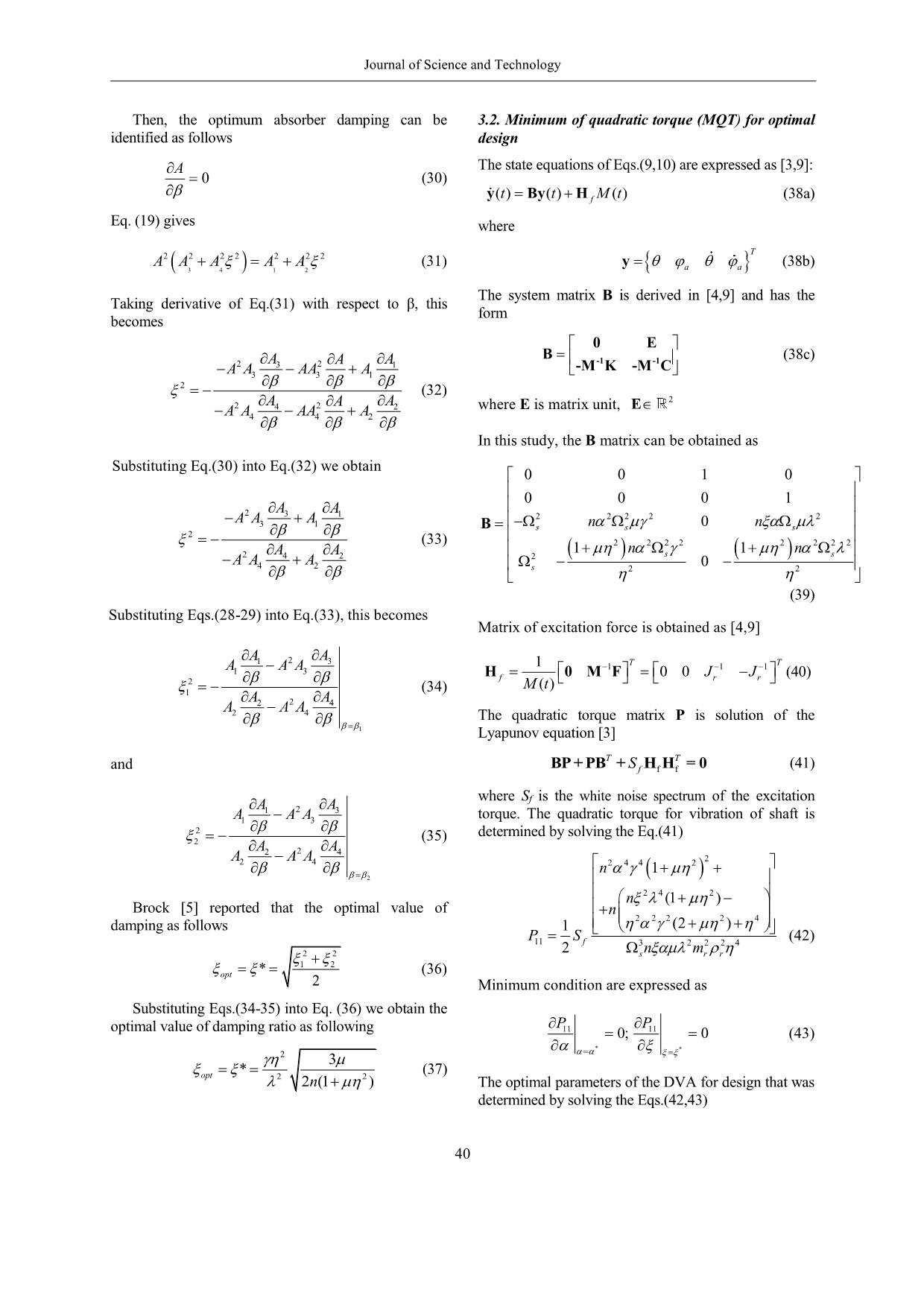
Trang 4
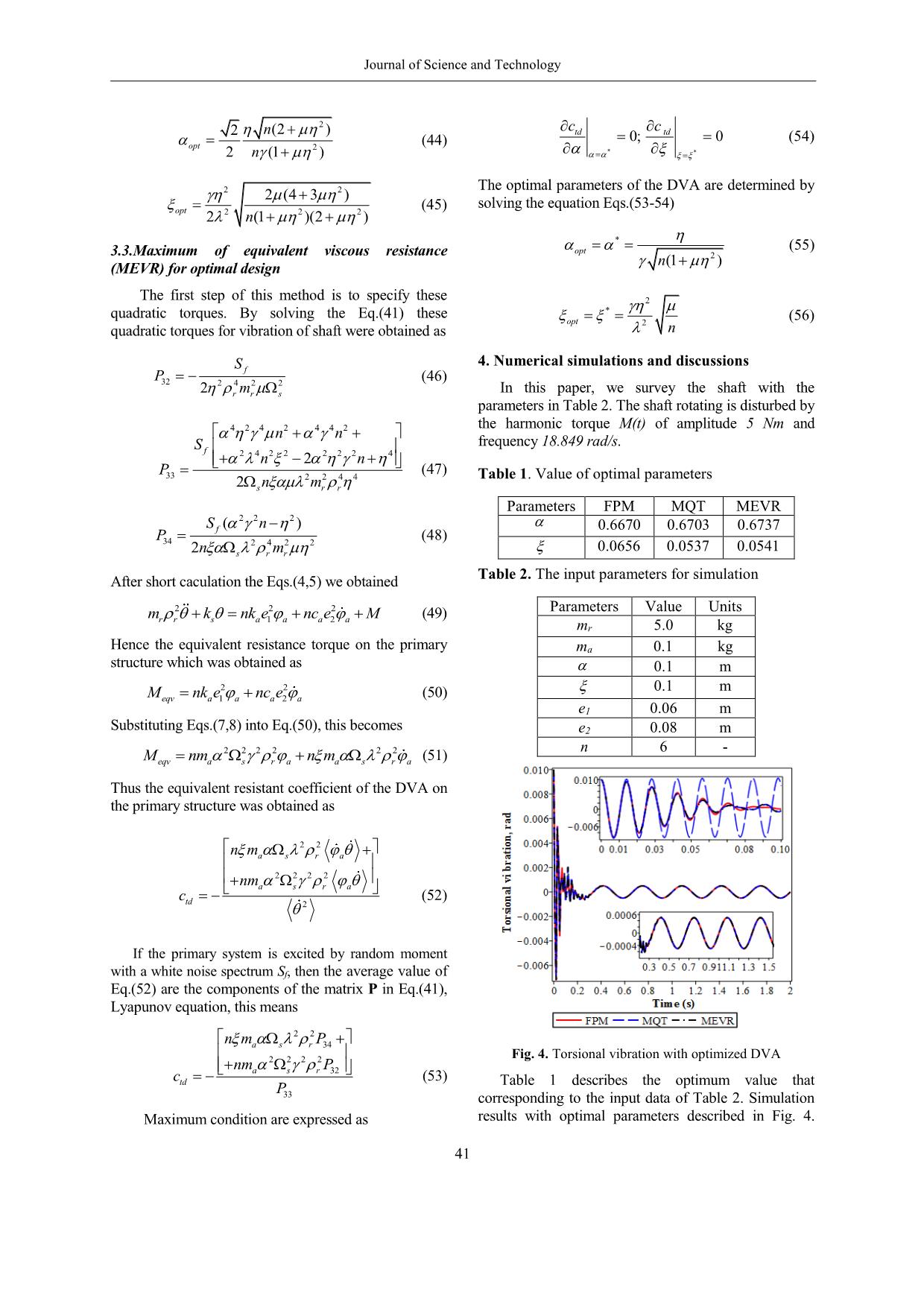
Trang 5
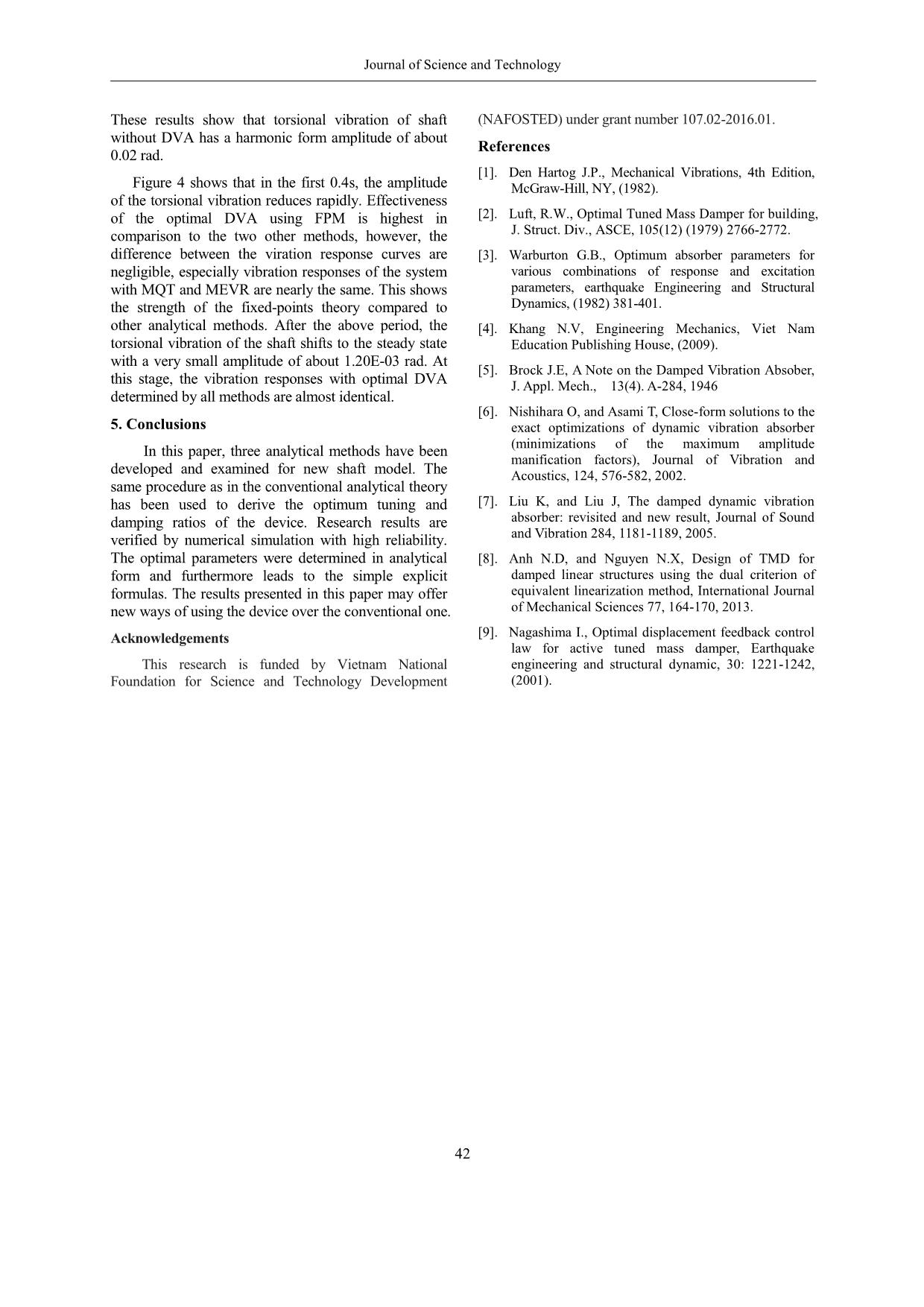
Trang 6
Tóm tắt nội dung tài liệu: Optimal parameters of linear dynamic vibration absorber for reduction of torsional vibration
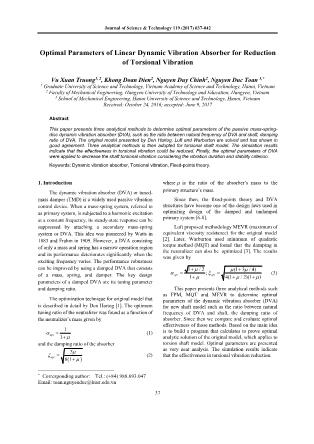
Journal of Science & Technology 119 (2017) 037-042 Optimal Parameters of Linear Dynamic Vibration Absorber for Reduction of Torsional Vibration Vu Xuan Truong1, 2, Khong Doan Dien2, Nguyen Duy Chinh2, Nguyen Duc Toan 3,* 1 Graduate University of Science and Technology, Vietnam Academy of Science and Technology, Hanoi, Vietnam 2 Faculty of Mechanical Engineering, Hungyen University of Technology and Education, Hungyen, Vietnam 3 School of Mechanical Engineering, Hanoi University of Science and Technology, Hanoi, Vietnam Received: October 24, 2016; accepted: June 9, 2017 Abstract This paper presents three analytical methods to determine optimal parameters of the passive mass-spring- disc dynamic vibration absorber (DVA), such as the ratio between natural frequency of DVA and shaft, damping ratio of DVA. The original model presented by Den Hartog, Luft and Warburton are solved and has shown in good agreement. Three analytical methods is then adopted for torsional shaft model. The simulation results indicate that the effectiveness in torsional vibration could be reduced. Finally, the optimal parameters of DVA were applied to decrease the shaft torsional vibration considering the vibration duration and stability criterion. Keywords: Dynamic vibration absorber, Torsional vibration, Fixed-points theory. 1. Introduction where is the ratio of the absorber’s mass to the The*dynamic vibration absorber (DVA) or tuned- primary structure’s mass. mass damper (TMD) is a widely used passive vibration Since then, the fixed-points theory and DVA control device. When a mass-spring system, referred to structures have become one of the design laws used in as primary system, is subjected to a harmonic excitation optimizing design of the damped and undamped at a constant frequency, its steady-state response can be primary system [6-8]. suppressed by attaching a secondary mass-spring Luft proposed methodology MEVR (maximum of system or DVA. This idea was pioneered by Watts in equivalent viscosity resistance) for the original model 1883 and Frahm in 1909. However, a DVA consisting [2]. Later, Warburton used minimum of quadratic of only a mass and spring has a narrow operation region torque method (MQT) and found that the damping in the neutralizer can also be optimized [3]. The results and its performance deteriorates significantly when the was given by exciting frequency varies. The performance robustness can be improved by using a damped DVA that consists 1/ 2 (13/ 4) ; (3) of a mass, spring, and damper. The key design optopt 14(1/ 2)(1) parameters of a damped DVA are its tuning parameter and damping ratio. This paper presents three analytical methods such as FPM, MQT and MEVR to determine optimal The optimization technique for original model that parameters of the dynamic vibration absorber (DVA) is described in detail by Den Hartog [1]. The optimum for new shaft model such as the ratio between natural tuning ratio of the neutralizer was found as a function of frequency of DVA and shaft, the damping ratio of the neutralizer’s mass given by absorber. Since then we compare and evaluate optimal effectiveness of those methods. Based on the main idea 1 (1) is to build a program that calculates to prove optimal opt 1 analytic solution of the original model, which applies to and the damping ratio of the absorber torsion shaft model. Optimal parameters are presented 3 as very neat analysis. The simulation results indicate (2) that the effectiveness in torsional vibration reduction. opt 81 * Corresponding author: Tel.: (+84) 988.693.047 Email: toan.nguyenduc@hust.edu.vn 37 Journal of Science and Technology 2. Shaft modeling and equations of vibration 22 JJncenkeaaaaaaa 210 (5) The natural frequency of the DVA and the shaft, respectively ka ks a s (6) ma Jr Introducing the dimensionless parameters DVA m ee aa;;; 12 (7) r a mrrrr ka 0 ks c aa;; (8) c Mt() a ssaa m J Jr a where ω is the frequency of excitation torque Fig.1. Modeling of the shaft system with DVA. Therefore, Eqs.(4) and (5) can be expressed by In this study, the shaft model shown in Figure 1 is 222 M considered. The shaft is modeled as a torsion spring 1 as (9) Jr which has stiffness ks and a disc which has moment of inertia is Jr and rotating at the constant angular 222 n velocity is disturbed by harmonic torque M(t). The asa (10) 0 n 222 0 passive mass-spring-disc dynamic vibration absorber sa (DVA) is attached on the shaft to minimize the The matrix form of Eqs.(9,10) are expressed as torsional vibration of the shaft. Mq +Cq +Kq = F (11) hub rotor passive disk T where q a e e 1 2 The mass matrix, viscous matrix, stiffness matrix ra and excitation force vector can be derived as ka r ca Mt() 1 22 00 C M 22 2 (12) 0 n s Mt() 2 0 s J Fig. 2. Modeling of the DVA K 2 2 2 F r (13) 0 n s Figure 2 shows the model of the DVA used in this 0 study. The DVA contains a passive disk and springs- dampers system. The radius and moment of inertia of 3. Determine optimal parameters of the DVA the passive disk are R, Ja, respectively. The shaft and 3.1. Fixed-points theory for optimal design the passive disc are linked together by springs and dampers system. The stiffness of each spring is ka. The The forced vibration of this system will be of the form viscous coefficient of each damper is ca. n is the ˆ It number of springs-dampers. The angular displacement M( t ) M e (14) of the rotor is and the torsional vibration of shaft r Thus, the stationary response of this system which can can be written as ()tt . r 0 be written as The relative angular displacement between the rotor ˆ I t I t (tt ) e , aa ( ) ˆ e (15) and passive disk as a . ˆ ˆ The system equations of motion can be expressed by where and a are complex amplitude vibration of the primary system and DVA, respectively. Jr J a J a a k s M() t (4) 38 Journal of Science and Technology Substituting Eqs.(14-15) into Eq.(11), this becomes some of damping ratio. For c = 0 or c becomes infinite so the amplifier fuction curve becomes infinite. That means some where in between there must be a value of 22 2 1 damping ratio for which the peak becomes a minimum. 22 Two other curves are draw in Fig. 3, for ξ = 0.1 and 0.4. 00 ˆ 1 Mˆ The first step of this method is to specify two 2i (16) 0 n 2 0 fixed points. Suppose that two points (S and T) with s ˆa ks horizontal coordinates as a β1, β2. The conditions for A 2 s 0 does not depend on the damping ratio is expressed as 222 follows 0 n s A 0 (20) Hence the stationary response of the primary system is expressed as Substituting Eq.(19) into Eq.(20), this becomes A iA Mˆ ˆ 12 (17) A iA k ()AAAA2222 34s 1423 0, (21) 222 2 AA AA222 12 where 43 222 AA34 2 2 2 2 2 An1 ; An2 ; 2222 AAAA1423 0 (22) Annn 2222222422222 3 From Eq.(22), we have 322322 Annn4 AA 12 (23) After short caculation the Eq.(17) we obtained the 11 AA34 real amplitude of the vibration response, which can be written as AA 12 (24) AA222 MMˆˆ AA 22 ˆ()tA 12 (18) 34 AA222 kk 34 ss We obtain the value of A at two points (S, T) these where A is called the amplifier function that is are expressed as follows defined by A2 222 A (25) AA S 1 12 A4 A 222 (19) AA34 A2 A T (26) A 2 4 1 Den Hartog [1] reported that the graph of amplifier function does not change in between the two peaks (S, 0 T) when the vertical coordinates of the S and T must be equal. In this condition, we have 0 0.4 AAST (27) The optimal parameter of α and β are specifed by T 0.1 S solving Eqs.(23-27) which can be written as * (28) n 2 1 Fig. 3 The graph of amplifier function 2 * 2 1 1,2 1,2 22 (29) Figure 3 shows a plot of the amplifier fuction with 21 39 Journal of Science and Technology Then, the optimum absorber damping can be 3.2. Minimum of quadratic torque (MQT) for optimal identified as follows design A The state equations of Eqs.(9,10) are expressed as [3,9]: 0 (30) yByH()()()ttMt f (38a) Eq. (19) gives where T AAAAA2 2 2 2 2 2 2 (31) y (38b) 3 4 1 2 aa The system matrix B is derived in [4,9] and has the Taking derivative of Eq.(31) with respect to β, this form becomes 0E A A A B -1-1 (38c) A22 A3 AA A 1 -MK-MC 3 3 1 2 (32) AAA 2 A22 A42 AA A where E is matrix unit, E 4 4 2 In this study, the B matrix can be obtained as Substituting Eq.(30) into Eq.(32) we obtain 0010 0001 A A AAA2 3 1 22222 31 B sss nn 0 2 (33) 22222222 2 AA 11 nnss AAA 42 2 42 s 220 (39) Substituting Eqs.(28-29) into Eq.(33), this becomes Matrix of excitation force is obtained as [4,9] A1 2 A3 1 111 TT AA13 A H0Mfrr F 00JJ(40) 2 (34) Mt () 1 AA AA A24 2 24 The quadratic torque matrix P is solution of the 1 Lyapunov equation [3] TT and BP + PB+HS H=f ff 0 (41) where Sf is the white noise spectrum of the excitation A1 2 A3 AA13 A torque. The quadratic torque for vibration of shaft is 2 determined by solving the Eq.(41) 2 (35) AA242 AA A 2 24 2 4 42 n 1 2 n2 42(1) Brock [5] reported that the optimal value of n 2 2 224 damping as follows 1 (2) PS11 f 32 2 2 4 (42) 22 2 srnm r 12 opt * (36) 2 Minimum condition are expressed as Substituting Eqs.(34-35) into Eq. (36) we obtain the PP optimal value of damping ratio as following 1111 0;0 (43) * * 2 3 * (37) opt 222n (1) The optimal parameters of the DVA for design that was determined by solving the Eqs.(42,43) 40 Journal of Science and Technology 2 cc 2 n(2) td 0; td 0 (54) opt 2 (44) 2 n(1) * * The optimal parameters of the DVA are determined by 222(43) (45) solving the equation Eqs.(53 -54 ) opt 2(1)(2)222 n * 3.3.Maximum of equivalent viscous resistance opt (55) n(1) 2 (MEVR) for optimal design The first step of this method is to specify these 2 quadratic torques. By solving the Eq.(41) these * opt 2 (56) quadratic torques for vibration of shaft were obtained as n 4. Numerical simulations and discussions S f P32 2 4 2 2 (46) 2 rm r s In this paper, we survey the shaft with the parameters in Table 2. The shaft rotating is disturbed by the harmonic torque M(t) of amplitude 5 Nm and 4 2 4 nn 2 4 4 2 S frequency 18.849 rad/s. f 2 4 2 2 2 2 2 4 nn 2 P33 2 2 4 4 (47) Table 1 . Value of optim al parameters 2snm r r Parameters FPM MQT MEVR 222 Snf () 0.6670 0.6703 0.6737 P34 2422 (48) 2nm srr 0.0656 0.0537 0.0541 After short caculation the Eqs.(4,5) we obtained Table 2. The input parameters for simulation 222 Parameters Value Units mknkrrsaaaa enc eM 12 (49) mr 5.0 kg Hence the equivalent resistance torque on the primary ma 0.1 kg structure which was obtained as 0.1 m 22 0.1 m Mnkeqvaaaa enc e 12 (50) e1 0.06 m Substituting Eqs.(7,8) into Eq.(50), this becomes e2 0.08 m 22 2222 n 6 - Mnmneqvasraasra m (51) Thus the equivalent resistant coefficient of the DVA on the primary structure was obtained as nm 22 a s r a nm 2 2 2 2 a s r a ctd (52) 2 If the primary system is excited by random moment with a white noise spectrum Sf, then the average value of Eq.(52) are the components of the matrix P in Eq.(41), Lyapunov equation, this means 22 n ma s r P34 2 2 2 2 Fig. 4. Torsional vibration with optimized DVA nma s r P32 ctd (53) Table 1 describes the optimum value that P 33 corresponding to the input data of Table 2. Simulation Maximum condition are expressed as results with optimal parameters described in Fig. 4. 41 Journal of Science and Technology These results show that torsional vibration of shaft (NAFOSTED) under grant number 107.02-2016.01. without DVA has a harmonic form amplitude of about References 0.02 rad. [1]. Den Hartog J.P., Mechanical Vibrations, 4th Edition, Figure 4 shows that in the first 0.4s, the amplitude McGraw-Hill, NY, (1982). of the torsional vibration reduces rapidly. Effectiveness of the optimal DVA using FPM is highest in [2]. Luft, R.W., Optimal Tuned Mass Damper for building, comparison to the two other methods, however, the J. Struct. Div., ASCE, 105(12) (1979) 2766-2772. difference between the viration response curves are [3]. Warburton G.B., Optimum absorber parameters for negligible, especially vibration responses of the system various combinations of response and excitation with MQT and MEVR are nearly the same. This shows parameters, earthquake Engineering and Structural the strength of the fixed-points theory compared to Dynamics, (1982) 381-401. other analytical methods. After the above period, the [4]. Khang N.V, Engineering Mechanics, Viet Nam torsional vibration of the shaft shifts to the steady state Education Publishing House, (2009). with a very small amplitude of about 1.20E-03 rad. At [5]. Brock J.E, A Note on the Damped Vibration Absober, this stage, the vibration responses with optimal DVA J. Appl. Mech., 13(4). A-284, 1946 determined by all methods are almost identical. [6]. Nishihara O, and Asami T, Close-form solutions to the 5. Conclusions exact optimizations of dynamic vibration absorber In this paper, three analytical methods have been (minimizations of the maximum amplitude manification factors), Journal of Vibration and developed and examined for new shaft model. The Acoustics, 124, 576-582, 2002. same procedure as in the conventional analytical theory has been used to derive the optimum tuning and [7]. Liu K, and Liu J, The damped dynamic vibration damping ratios of the device. Research results are absorber: revisited and new result, Journal of Sound verified by numerical simulation with high reliability. and Vibration 284, 1181-1189, 2005. The optimal parameters were determined in analytical [8]. Anh N.D, and Nguyen N.X, Design of TMD for form and furthermore leads to the simple explicit damped linear structures using the dual criterion of formulas. The results presented in this paper may offer equivalent linearization method, International Journal new ways of using the device over the conventional one. of Mechanical Sciences 77, 164-170, 2013. Acknowledgements [9]. Nagashima I., Optimal displacement feedback control law for active tuned mass damper, Earthquake This research is funded by Vietnam National engineering and structural dynamic, 30: 1221-1242, Foundation for Science and Technology Development (2001). 42
File đính kèm:
optimal_parameters_of_linear_dynamic_vibration_absorber_for.pdf