Numerical modelization of the oil film pressure for a hydrodynamic tilting - pad thrust bearing
Tilting pad thrust bearings are used in rotary
machineries, allow for the thrust load operation at the
average of rotation and support a heavy load.
Hydrodynamic thrust bearing based on hydrodynamic
lubrication.
In 2012, D. V. Srikanth et. al. [1] studied a large
tilting pad thrust bearing angular stiffness. In 2014,
Najar and Harmain [2] performed a numerical study on
pressure profiles in the hydrodynamic thrust bearing.
Annan Guo et.al [3] experiment static and dynamic
characteristics of tilting pad thrust bearing in the same
year. In 2018, Mostefa K. et al. [4] analyzed the effect
of dimple geometries on textured tilting pad thrust
bearing using a finite difference method.
In Vietnam, studies about hydrodynamic tilting
pad bearing are few. Most recently, Hai T.T.T et al [5]
compared a numerical calculation of a hydrodynamic
fixed pad thrust bearing with experiment results.
Besides Dung Le Anh et al. [6] perform a numerical
modelization of oil film pressure in hydrodynamic
journal bearing under a steady load.
This research analyzes the pressure and oil film
thickness of a pivot tilting pad thrust bearing at
hydrodynamic lubrication.
2. Thrust bearing and the equations
2.1. Tilting pad thrust bearing
*Corresponding author: Tel.: (+84) 978263926
Email: hai.tranthithanh@hust.edu.vn
Fig.1 shows the diagram of a pad in pivot tilting
pad thrust bearing. Here, the pad is placed onto a pivot
that is eccentric from the middle of the pad, to form the
oil wedge as hydrodynamic theory. The pressure in the
wedge generates the force onto the pad surface making
the pad to tilt at an angle respected to the r-axis and the
θ -axis. r and θ are two directions of polar
coordinates. The inner and outer radius of the pad are
r1 and r2, θ pad is the pad angle, θ p and rp are the
position of the pivot, hp is the film thickness at pivot
location, αr and αθ are the inclinations of the pad
along the radial and circumferential direction, ω is
the angular velocity of the collar.
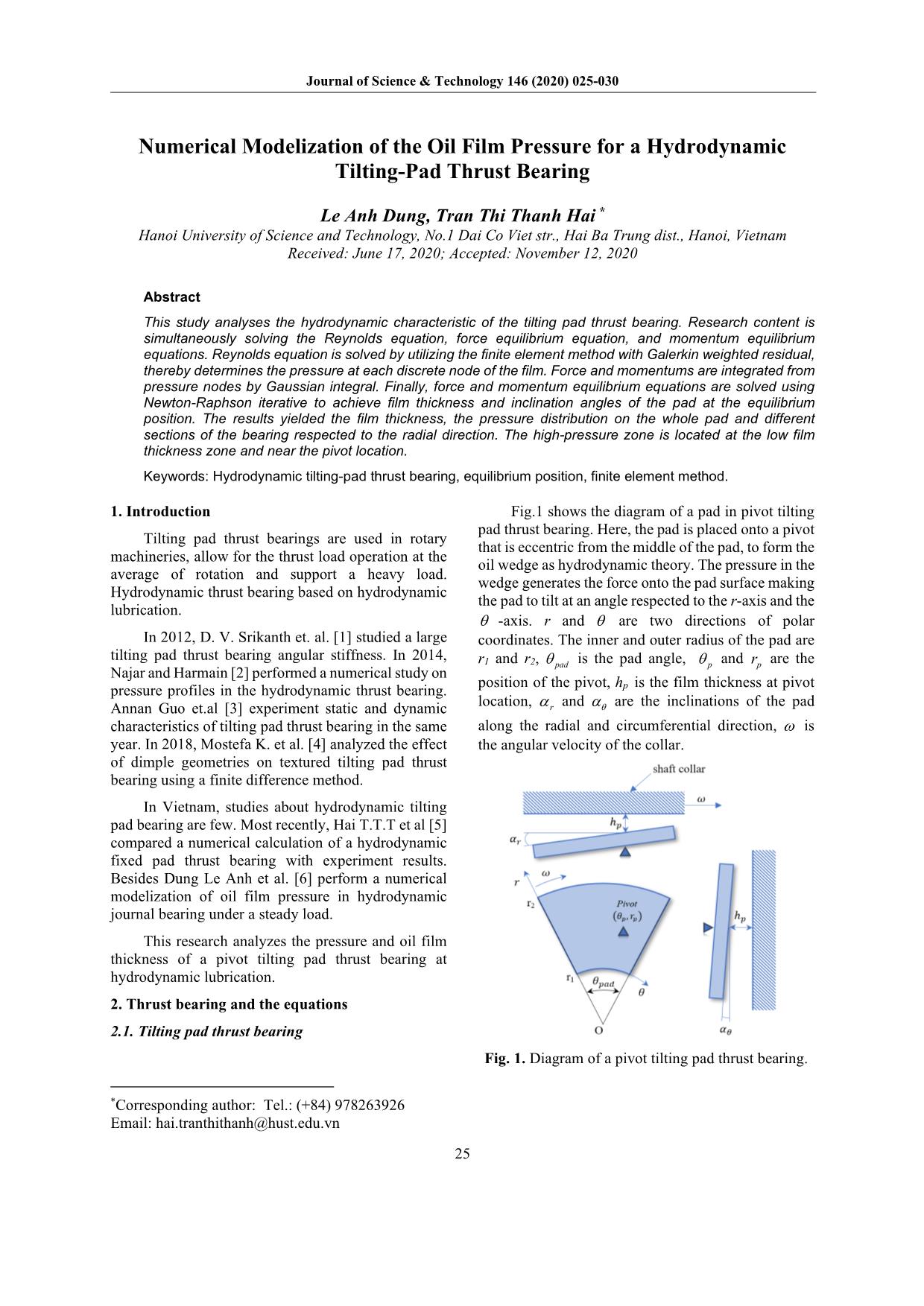
Trang 1
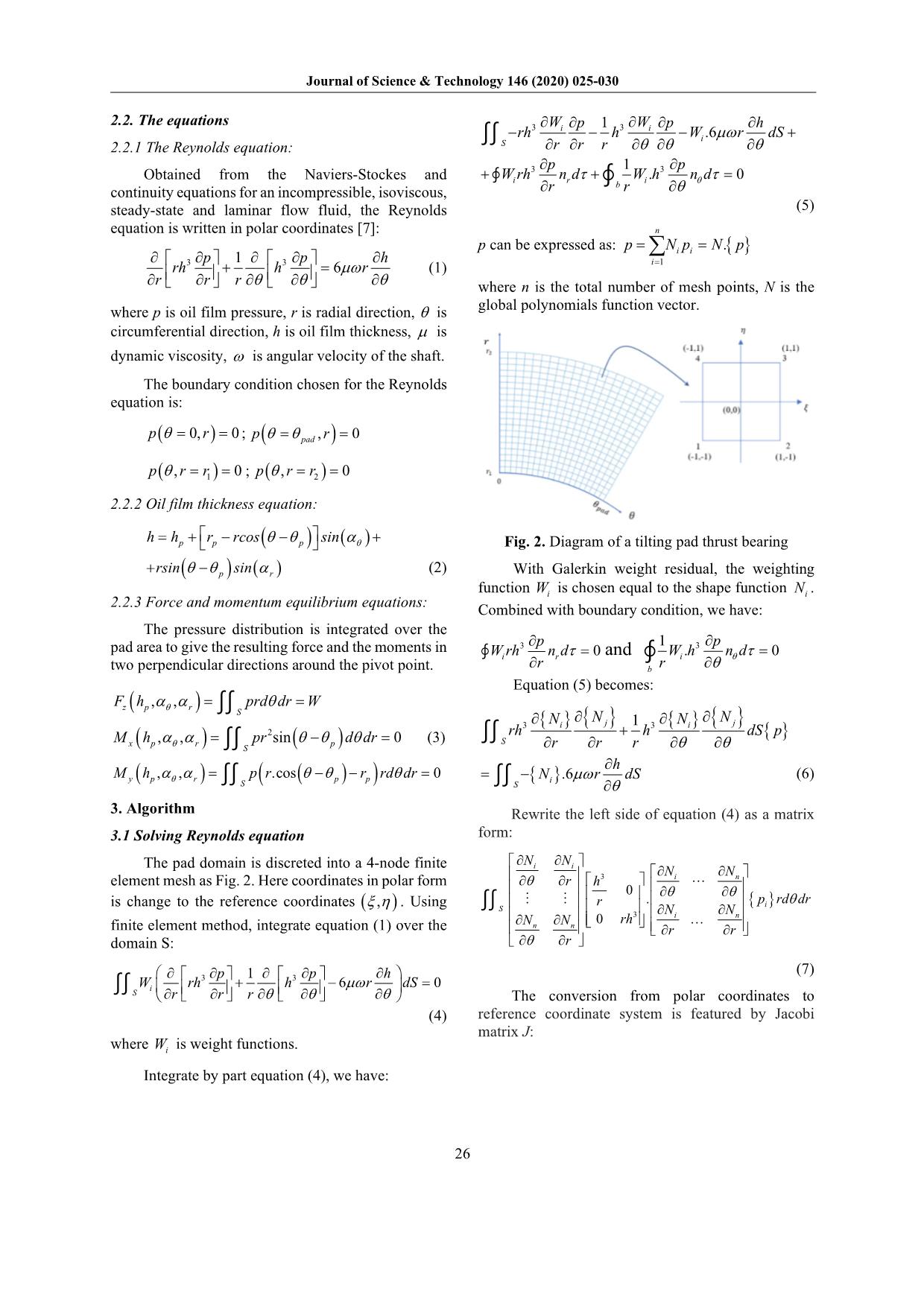
Trang 2
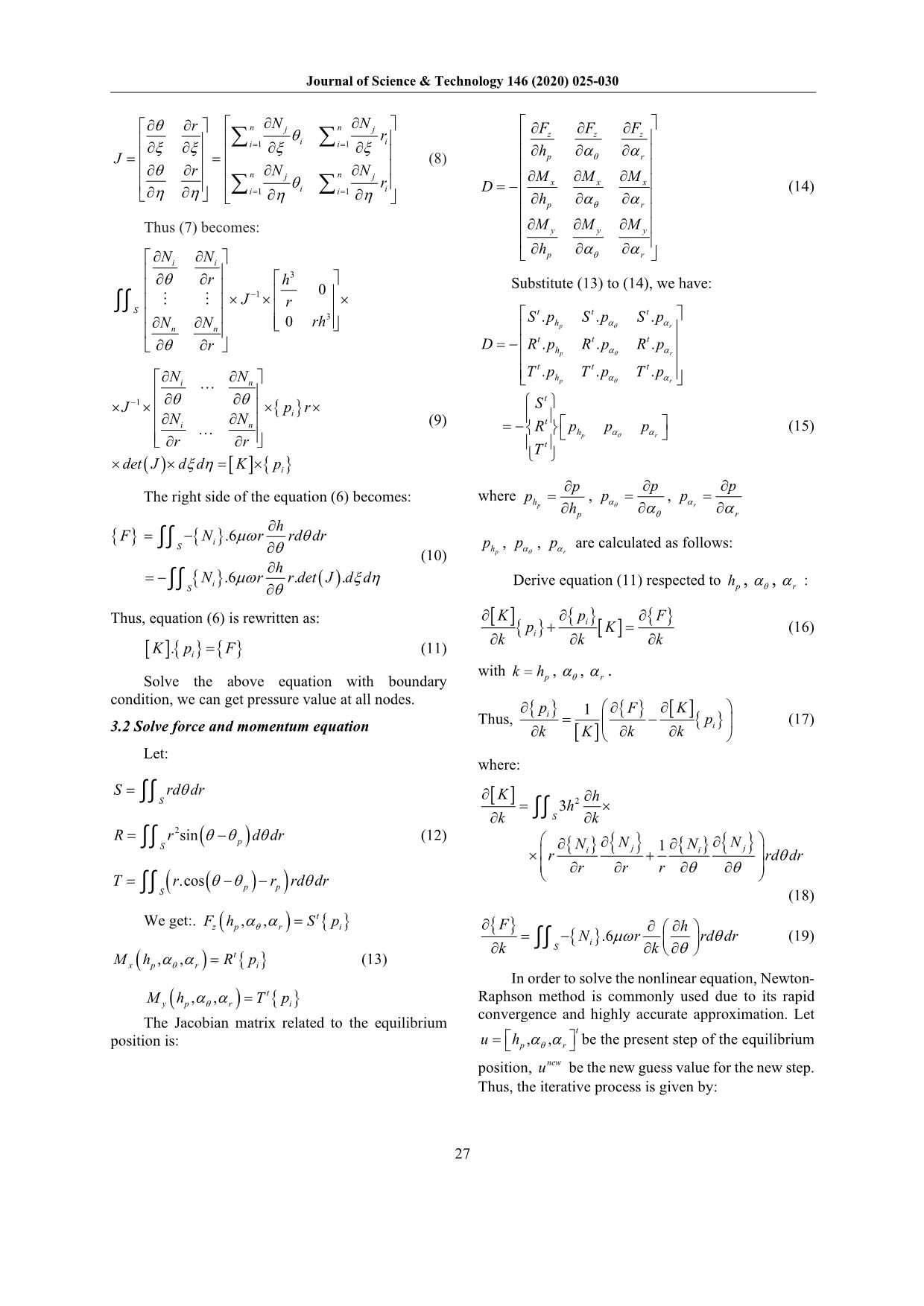
Trang 3
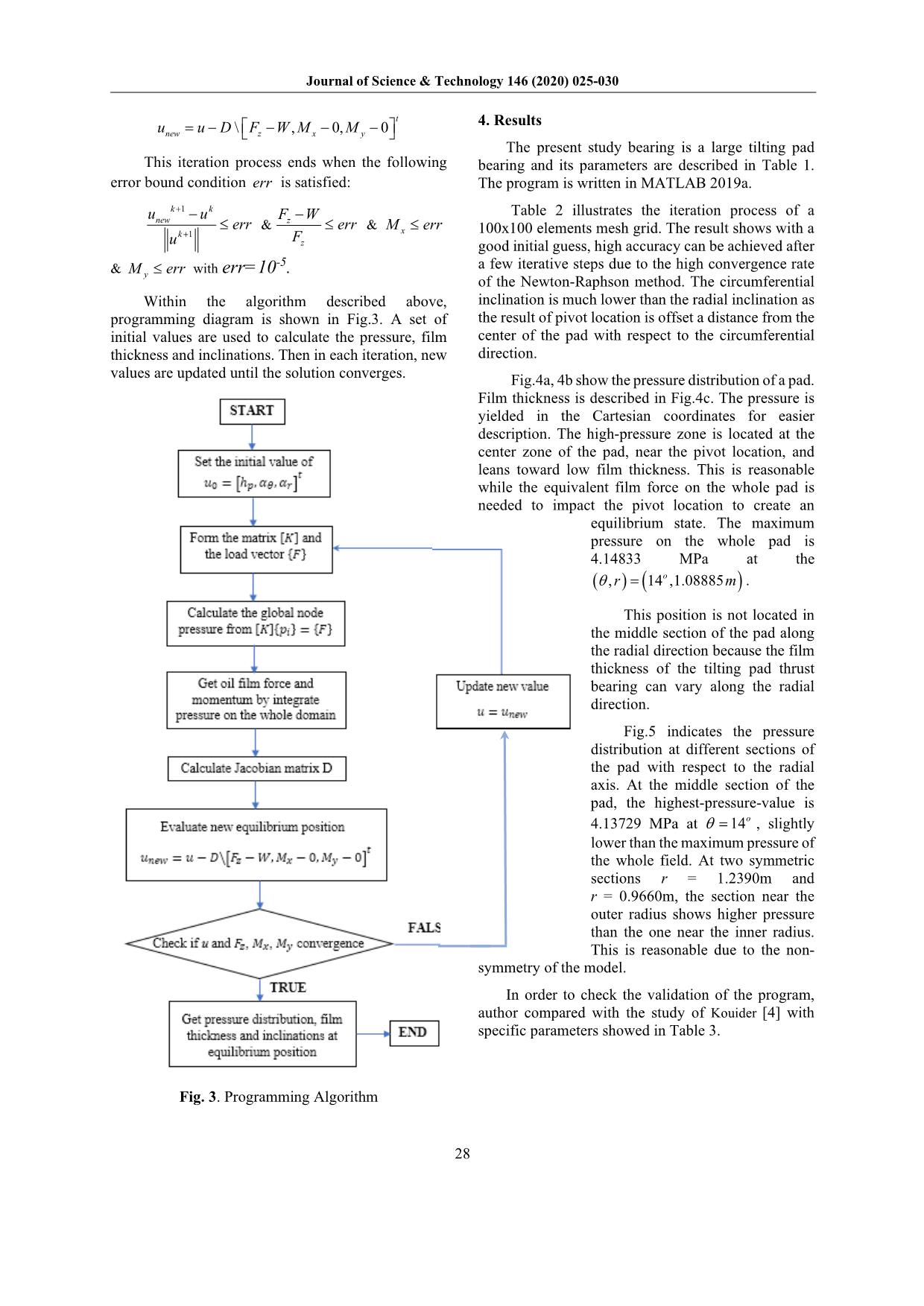
Trang 4
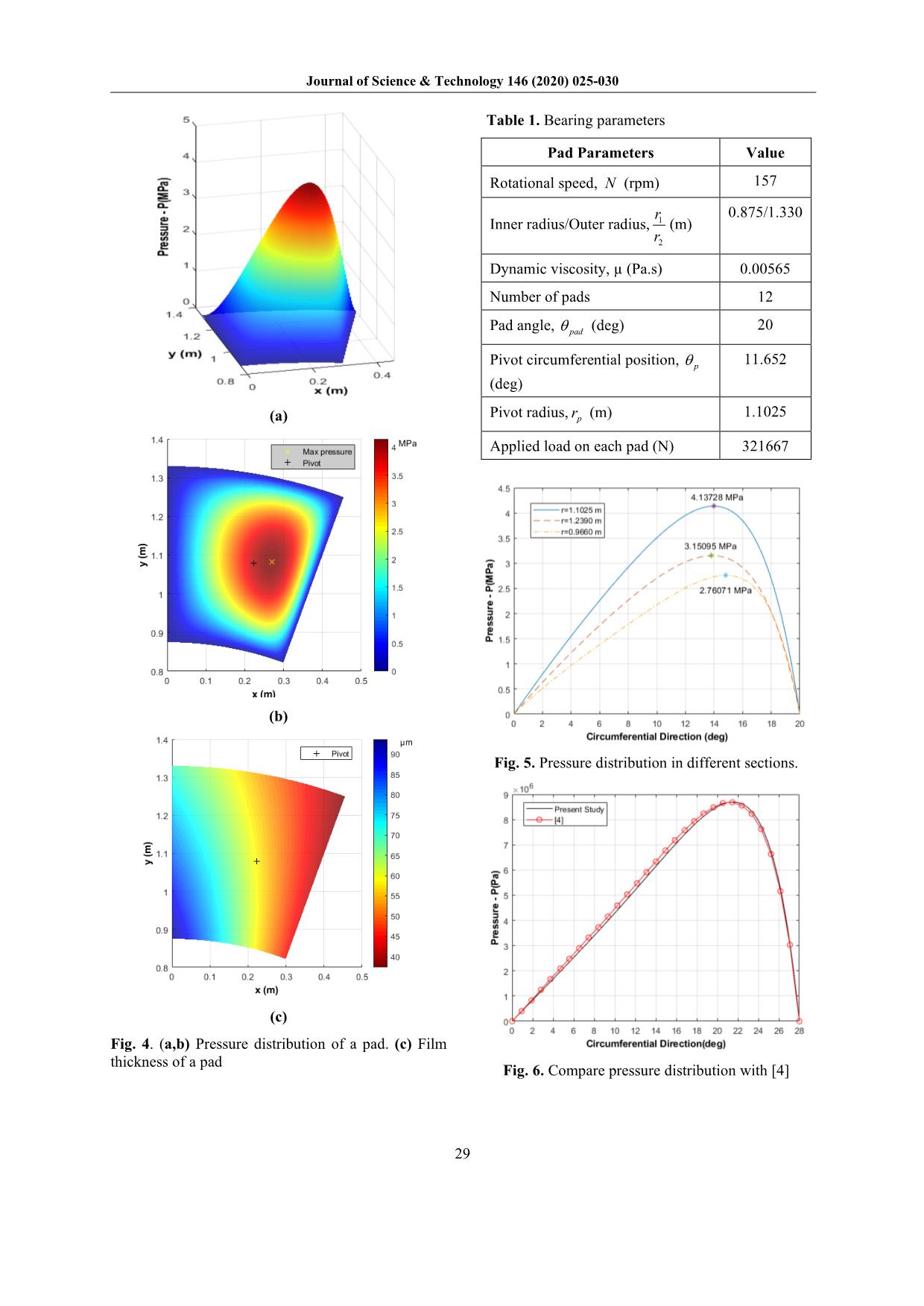
Trang 5
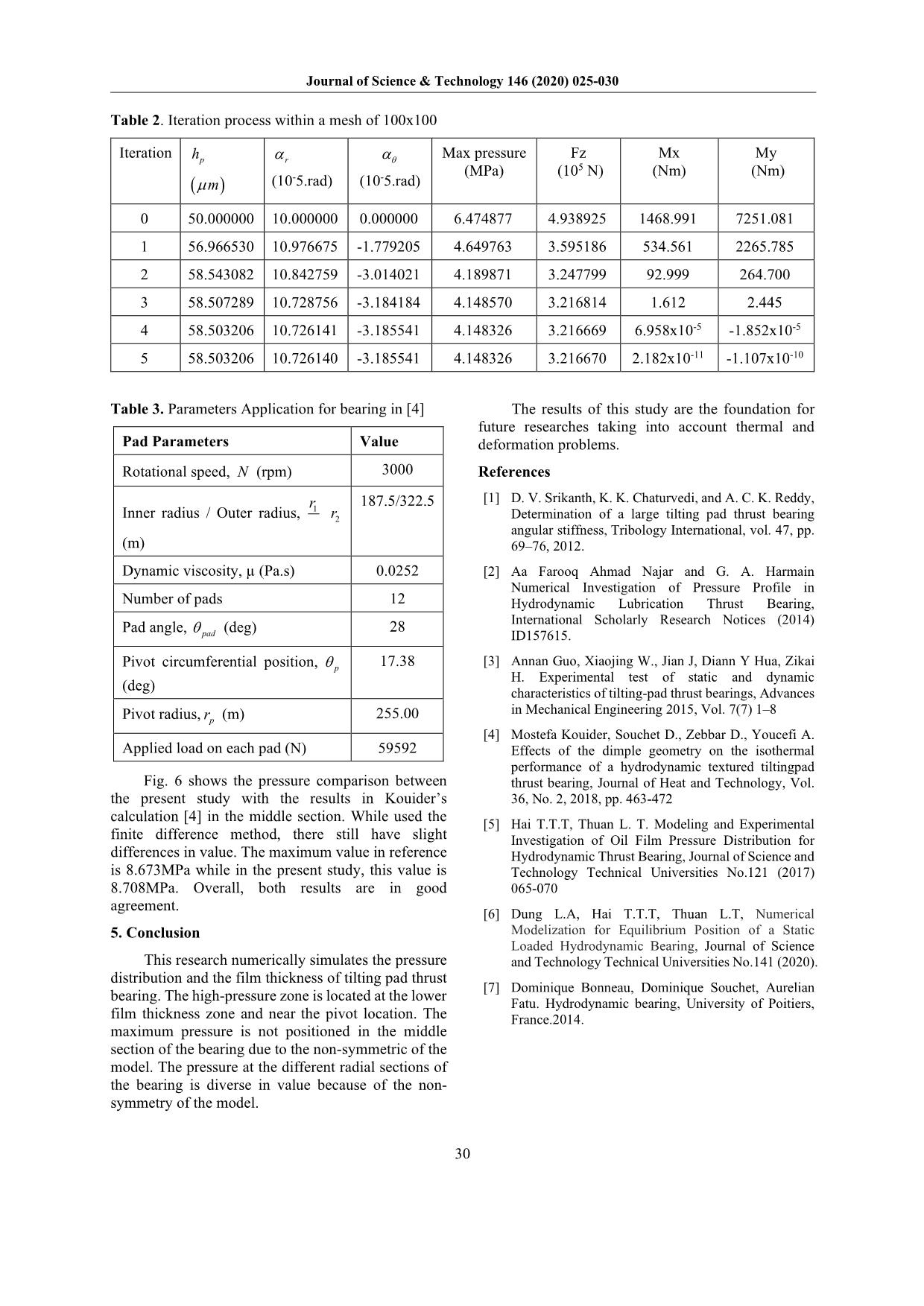
Trang 6
Tóm tắt nội dung tài liệu: Numerical modelization of the oil film pressure for a hydrodynamic tilting - pad thrust bearing
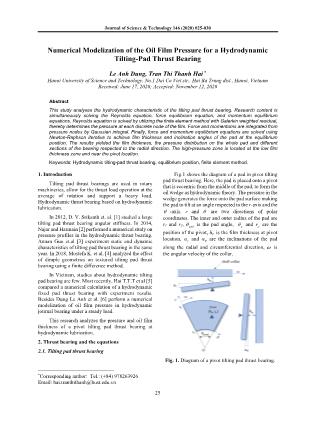
Journal of Science & Technology 146 (2020) 025-030 Numerical Modelization of the Oil Film Pressure for a Hydrodynamic Tilting-Pad Thrust Bearing Le Anh Dung, Tran Thi Thanh Hai * Hanoi University of Science and Technology, No.1 Dai Co Viet str., Hai Ba Trung dist., Hanoi, Vietnam Received: June 17, 2020; Accepted: November 12, 2020 Abstract This study analyses the hydrodynamic characteristic of the tilting pad thrust bearing. Research content is simultaneously solving the Reynolds equation, force equilibrium equation, and momentum equilibrium equations. Reynolds equation is solved by utilizing the finite element method with Galerkin weighted residual, thereby determines the pressure at each discrete node of the film. Force and momentums are integrated from pressure nodes by Gaussian integral. Finally, force and momentum equilibrium equations are solved using Newton-Raphson iterative to achieve film thickness and inclination angles of the pad at the equilibrium position. The results yielded the film thickness, the pressure distribution on the whole pad and different sections of the bearing respected to the radial direction. The high-pressure zone is located at the low film thickness zone and near the pivot location. Keywords: Hydrodynamic tilting-pad thrust bearing, equilibrium position, finite element method. 1. Introduction1 Fig.1 shows the diagram of a pad in pivot tilting pad thrust bearing. Here, the pad is placed onto a pivot Tilting pad thrust bearings are used in rotary that is eccentric from the middle of the pad, to form the machineries, allow for the thrust load operation at the oil wedge as hydrodynamic theory. The pressure in the average of rotation and support a heavy load. wedge generates the force onto the pad surface making Hydrodynamic thrust bearing based on hydrodynamic the pad to tilt at an angle respected to the r-axis and the lubrication. θ -axis. r and θ are two directions of polar In 2012, D. V. Srikanth et. al. [1] studied a large coordinates. The inner and outer radius of the pad are tilting pad thrust bearing angular stiffness. In 2014, r1 and r2, θ pad is the pad angle, θ p and rp are the Najar and Harmain [2] performed a numerical study on position of the pivot, hp is the film thickness at pivot pressure profiles in the hydrodynamic thrust bearing. location, α and α are the inclinations of the pad Annan Guo et.al [3] experiment static and dynamic r θ characteristics of tilting pad thrust bearing in the same along the radial and circumferential direction, ω is year. In 2018, Mostefa K. et al. [4] analyzed the effect the angular velocity of the collar. of dimple geometries on textured tilting pad thrust bearing using a finite difference method. In Vietnam, studies about hydrodynamic tilting pad bearing are few. Most recently, Hai T.T.T et al [5] compared a numerical calculation of a hydrodynamic fixed pad thrust bearing with experiment results. Besides Dung Le Anh et al. [6] perform a numerical modelization of oil film pressure in hydrodynamic journal bearing under a steady load. This research analyzes the pressure and oil film thickness of a pivot tilting pad thrust bearing at hydrodynamic lubrication. 2. Thrust bearing and the equations 2.1. Tilting pad thrust bearing Fig. 1. Diagram of a pivot tilting pad thrust bearing. *Corresponding author: Tel.: (+84) 978263926 Email: hai.tranthithanh@hust.edu.vn 25 Journal of Science & Technology 146 (2020) 025-030 2.2. The equations 33∂∂WWii∂∂∂pph1 ∬ −−rh h − Wi .6µω r dS + 2.2.1 The Reynolds equation: S ∂∂rrr ∂∂θθ ∂ θ 33∂∂pp1 Obtained from the Naviers-Stockes and ++∮Wir rh n dττ W i.0 h nθ d = ∮b continuity equations for an incompressible, isoviscous, ∂∂rrθ steady-state and laminar flow fluid, the Reynolds (5) equation is written in polar coordinates [7]: n = = p can be expressed as: p∑ Npii N.{ p} ∂ ∂p 1 ∂∂ ph ∂ = rh33+=h 6µωr (1) i 1 ∂ ∂ ∂∂θθ ∂ θ r rr where n is the total number of mesh points, N is the where p is oil film pressure, r is radial direction, θ is global polynomials function vector. circumferential direction, h is oil film thickness, µ is dynamic viscosity, ω is angular velocity of the shaft. The boundary condition chosen for the Reynolds equation is: pr(θ =0,) = 0 ; pr(θθ=pad ,0) = p(θ,0 rr=1 ) = ; p(θ,0 rr=2 ) = 2.2.2 Oil film thickness equation: =+−θθ − α + h hpp r rcos( p) sin( θ ) Fig. 2. Diagram of a tilting pad thrust bearing +−rsin(θθpr) sin( α) (2) With Galerkin weight residual, the weighting function Wi is chosen equal to the shape function Ni . 2.2.3 Force and momentum equilibrium equations: Combined with boundary condition, we have: The pressure distribution is integrated over the ∂ ∂ pad area to give the resulting force and the moments in 3 p 1 3 p ∮Wir rh n dτ = 0 and ∮ Whi .0 ndθ τ = two perpendicular directions around the pivot point. ∂r b r ∂θ Equation (5) becomes: Fzp h ,,ααθ r= prd θ dr= W ( ) ∬S ∂∂∂∂NN 33{NNii} { jj} 1 { } { } 2 ∬ rh + h dS{ p} Mxp h ,,ααθ r= pr sin θθ −=pd θ dr 0 (3) S ( ) ∬S ( ) ∂∂r rr ∂∂θθ ∂ αα =θθ −− θ = h Myp( h ,,θ r) ∬ p( r.cos( p) r p) rd dr 0 =∬ −{Ni }.6µω r dS (6) S S ∂θ 3. Algorithm Rewrite the left side of equation (4) as a matrix 3.1 Solving Reynolds equation form: The pad domain is discreted into a 4-node finite ∂∂NNii 3 ∂∂NNin element mesh as Fig. 2. Here coordinates in polar form ∂∂θ r h 0 ∂∂θθ is change to the reference coordinates ξη, . Using ∬ r .{ pi } rdθ dr ( ) S ∂∂ 3 NNin ∂∂NN0 rh finite element method, integrate equation (1) over the nn ∂∂rr domain S: ∂∂θ r ∂ ∂p 1 ∂ ∂ ph ∂ (7) 33+−=µω ∬ W i rh h60 r dS S ∂r ∂ rr ∂∂θθ ∂ θ The conversion from polar coordinates to (4) reference coordinate system is featured by Jacobi matrix J: where Wi is weight functions. Integrate by part equation (4), we have: 26 Journal of Science & Technology 146 (2020) 025-030 ∂∂θ r nn∂∂NNjj ∂∂∂ θ FFFzzz ∑∑= ii= r ∂∂ξξii11 ∂ ξ ∂ ξ ∂∂∂h αα J = = (8) prθ ∂∂θ ∂ ∂ rNnnjj N ∂∂∂ θ r MMMxxx ∑∑ii=11ii= D = − (14) ∂∂ηη∂∂ηη ∂∂∂h αα prθ Thus (7) becomes: ∂∂∂MMMyyy ∂∂∂αα hprθ ∂∂NNii ∂∂θ 3 r h Substitute (13) to (14), we have: −1 0 ∬ ××J r × S ttt 3 Sp... Spαα Sp ∂∂NN 0 rh hprθ nn ttt ∂∂θ r D= − Rp...h Rpαα Rp prθ ttt Tp...h Tpαα Tp ∂∂NNin prθ − ∂∂θθ t ××J1 ×pr × S { i } ∂∂NNin (9) t = − Rp pαα p (15) hprθ ∂∂rr t T ×det( J) ×=× dξη d[ K] { pi } ∂p ∂p ∂p where p = , p = , p = The right side of the equation (6) becomes: hp αθ αr ∂hp ∂αθ ∂αr ∂h {F} = −{ Ni }.6µω r rd θ dr ∬S p , p , p are calculated as follows: ∂θ hp αθ αr (10) ∂h = −∬ { Ni }.6µω r r . det( J) . dξ d η Derive equation (11) respected to h , α , α : S ∂θ p θ r Thus, equation (6) is rewritten as: ∂[K ] ∂∂{ pFi } { } { pK} +=[ ] (16) ∂∂∂kkki [Kp].{ i } = { F} (11) with kh= , α , α . Solve the above equation with boundary p θ r condition, we can get pressure value at all nodes. ∂∂{ pF} 1 { } ∂[K ] Thus, i = − p (17) 3.2 Solve force and momentum equation { i } ∂kKk[ ] ∂∂ k Let: where: = θ S∬ rd dr ∂[K ] ∂h S = 3h2 × ∬S ∂∂kk 2 R=∬ r sin (θθ− p )d θ dr (12) S ∂∂{NN} ∂∂{NNjj} 1 { } { } ×+r iirdθ dr ∂∂ ∂∂θθ r rr T=∬ ( r.cos(θθ −−pp) r) rd θ dr S (18) αα = t We get:. Fhzp( ,,θ r) S{ p i} ∂{F} ∂∂h = −{Ni }.6µω r rdθ dr (19) ∬S t ∂kk∂∂θ Mhxp( ,,ααθ r) = Rp{ i} (13) In order to solve the nonlinear equation, Newton- t Mhyp( ,,ααθ r) = Tp{ i} Raphson method is commonly used due to its rapid convergence and highly accurate approximation. Let The Jacobian matrix related to the equilibrium t = αα position is: uhpr, θ , be the present step of the equilibrium position, unew be the new guess value for the new step. Thus, the iterative process is given by: 27 Journal of Science & Technology 146 (2020) 025-030 t =−− −− 4. Results unew u D\ Fz WM ,x 0, M y 0 The present study bearing is a large tilting pad This iteration process ends when the following bearing and its parameters are described in Table 1. error bound condition err is satisfied: The program is written in MATLAB 2019a. kk+1 Table 2 illustrates the iteration process of a uunew − FWz − ≤ err & ≤ err & Mx ≤ err 100x100 elements mesh grid. The result shows with a k +1 F u z good initial guess, high accuracy can be achieved after -5 a few iterative steps due to the high convergence rate & My ≤ err with err=10 . of the Newton-Raphson method. The circumferential Within the algorithm described above, inclination is much lower than the radial inclination as programming diagram is shown in Fig.3. A set of the result of pivot location is offset a distance from the initial values are used to calculate the pressure, film center of the pad with respect to the circumferential thickness and inclinations. Then in each iteration, new direction. values are updated until the solution converges. Fig.4a, 4b show the pressure distribution of a pad. Film thickness is described in Fig.4c. The pressure is yielded in the Cartesian coordinates for easier description. The high-pressure zone is located at the center zone of the pad, near the pivot location, and leans toward low film thickness. This is reasonable while the equivalent film force on the whole pad is needed to impact the pivot location to create an equilibrium state. The maximum pressure on the whole pad is 4.14833 MPa at the (θ,rm) = ( 14o ,1.08885 ) . This position is not located in the middle section of the pad along the radial direction because the film thickness of the tilting pad thrust bearing can vary along the radial direction. Fig.5 indicates the pressure distribution at different sections of the pad with respect to the radial axis. At the middle section of the pad, the highest-pressure-value is 4.13729 MPa at θ = 14o , slightly lower than the maximum pressure of the whole field. At two symmetric sections r = 1.2390m and r = 0.9660m, the section near the outer radius shows higher pressure than the one near the inner radius. This is reasonable due to the non- symmetry of the model. In order to check the validation of the program, author compared with the study of Kouider [4] with specific parameters showed in Table 3. Fig. 3. Programming Algorithm 28 Journal of Science & Technology 146 (2020) 025-030 Table 1. Bearing parameters Pad Parameters Value Rotational speed, N (rpm) 157 r 0.875/1.330 Inner radius/Outer radius, 1 (m) r2 Dynamic viscosity, µ (Pa.s) 0.00565 Number of pads 12 Pad angle, θ pad (deg) 20 Pivot circumferential position, θ p 11.652 (deg) (a) Pivot radius, rp (m) 1.1025 Applied load on each pad (N) 321667 (b) Fig. 5. Pressure distribution in different sections. (c) Fig. 4. (a,b) Pressure distribution of a pad. (c) Film thickness of a pad Fig. 6. Compare pressure distribution with [4] 29 Journal of Science & Technology 146 (2020) 025-030 Table 2. Iteration process within a mesh of 100x100 Iteration hp αr αθ Max pressure Fz Mx My 5 - - (MPa) (10 N) (Nm) (Nm) (µm) (10 5.rad) (10 5.rad) 0 50.000000 10.000000 0.000000 6.474877 4.938925 1468.991 7251.081 1 56.966530 10.976675 -1.779205 4.649763 3.595186 534.561 2265.785 2 58.543082 10.842759 -3.014021 4.189871 3.247799 92.999 264.700 3 58.507289 10.728756 -3.184184 4.148570 3.216814 1.612 2.445 4 58.503206 10.726141 -3.185541 4.148326 3.216669 6.958x10-5 -1.852x10-5 5 58.503206 10.726140 -3.185541 4.148326 3.216670 2.182x10-11 -1.107x10-10 Table 3. Parameters Application for bearing in [4] The results of this study are the foundation for future researches taking into account thermal and Pad Parameters Value deformation problems. Rotational speed, N (rpm) 3000 References [1] D. V. Srikanth, K. K. Chaturvedi, and A. C. K. Reddy, r1 187.5/322.5 Inner radius / Outer radius, r2 Determination of a large tilting pad thrust bearing angular stiffness, Tribology International, vol. 47, pp. (m) 69–76, 2012. Dynamic viscosity, µ (Pa.s) 0.0252 [2] Aa Farooq Ahmad Najar and G. A. Harmain Numerical Investigation of Pressure Profile in Number of pads 12 Hydrodynamic Lubrication Thrust Bearing, Pad angle, θ (deg) 28 International Scholarly Research Notices (2014) pad ID157615. Pivot circumferential position, θ p 17.38 [3] Annan Guo, Xiaojing W., Jian J, Diann Y Hua, Zikai H. Experimental test of static and dynamic (deg) characteristics of tilting-pad thrust bearings, Advances in Mechanical Engineering 2015, Vol. 7(7) 1–8 Pivot radius, rp (m) 255.00 [4] Mostefa Kouider, Souchet D., Zebbar D., Youcefi A. Applied load on each pad (N) 59592 Effects of the dimple geometry on the isothermal performance of a hydrodynamic textured tiltingpad Fig. 6 shows the pressure comparison between thrust bearing, Journal of Heat and Technology, Vol. the present study with the results in Kouider’s 36, No. 2, 2018, pp. 463-472 calculation [4] in the middle section. While used the [5] Hai T.T.T, Thuan L. T. Modeling and Experimental finite difference method, there still have slight Investigation of Oil Film Pressure Distribution for differences in value. The maximum value in reference Hydrodynamic Thrust Bearing, Journal of Science and is 8.673MPa while in the present study, this value is Technology Technical Universities No.121 (2017) 8.708MPa. Overall, both results are in good 065-070 agreement. [6] Dung L.A, Hai T.T.T, Thuan L.T, Numerical 5. Conclusion Modelization for Equilibrium Position of a Static Loaded Hydrodynamic Bearing, Journal of Science This research numerically simulates the pressure and Technology Technical Universities No.141 (2020). distribution and the film thickness of tilting pad thrust [7] Dominique Bonneau, Dominique Souchet, Aurelian bearing. The high-pressure zone is located at the lower Fatu. Hydrodynamic bearing, University of Poitiers, film thickness zone and near the pivot location. The France.2014. maximum pressure is not positioned in the middle section of the bearing due to the non-symmetric of the model. The pressure at the different radial sections of the bearing is diverse in value because of the non- symmetry of the model. 30
File đính kèm:
numerical_modelization_of_the_oil_film_pressure_for_a_hydrod.pdf