Nâng cao hiệu quả tổ chức xây dựng dự toán hàng tồn kho tại các doanh nghiệp sản xuất Việt Nam trong thời kỳ hội nhập
Tóm tắt
Tổ chức xây dựng dự toán hàng tồn kho là một công cụ quan trọng của nhà quản trị trong
thực hiện chức năng hoạch định và kiểm soát hoạt động của doanh nghiệp. Lập dự toán hàng
tồn kho là hoạt động cần thiết và quan trọng nhằm phác thảo tương lai, giúp doanh nghiệp phát
triển đúng hướng và đưa ra kế hoạch thực hiện phù hợp để đạt được mục tiêu chiến lược. Bài
viết tập trung làm rõ vai trò của tổ chức xây dựng dự toán hàng tồn kho trong các doanh nghiệp
sản xuất, thực trạng xây dựng dự toán hàng tồn kho trong các doanh nghiệp sản xuất ở Việt Nam
hiện nay. Trên cơ sở đó, tác giả đưa ra một số đề xuất hoàn thiện tổ chức xây dựng dự toán hàng
tồn kho nhằm nâng cao hiệu quả quản lý hàng tồn kho của nhà quản trị trong doanh nghiệp.
Từ khóa: dự toán, doanh nghiệp sản xuất, hàng tồn kho, kế toán quản trị, tổ chức.
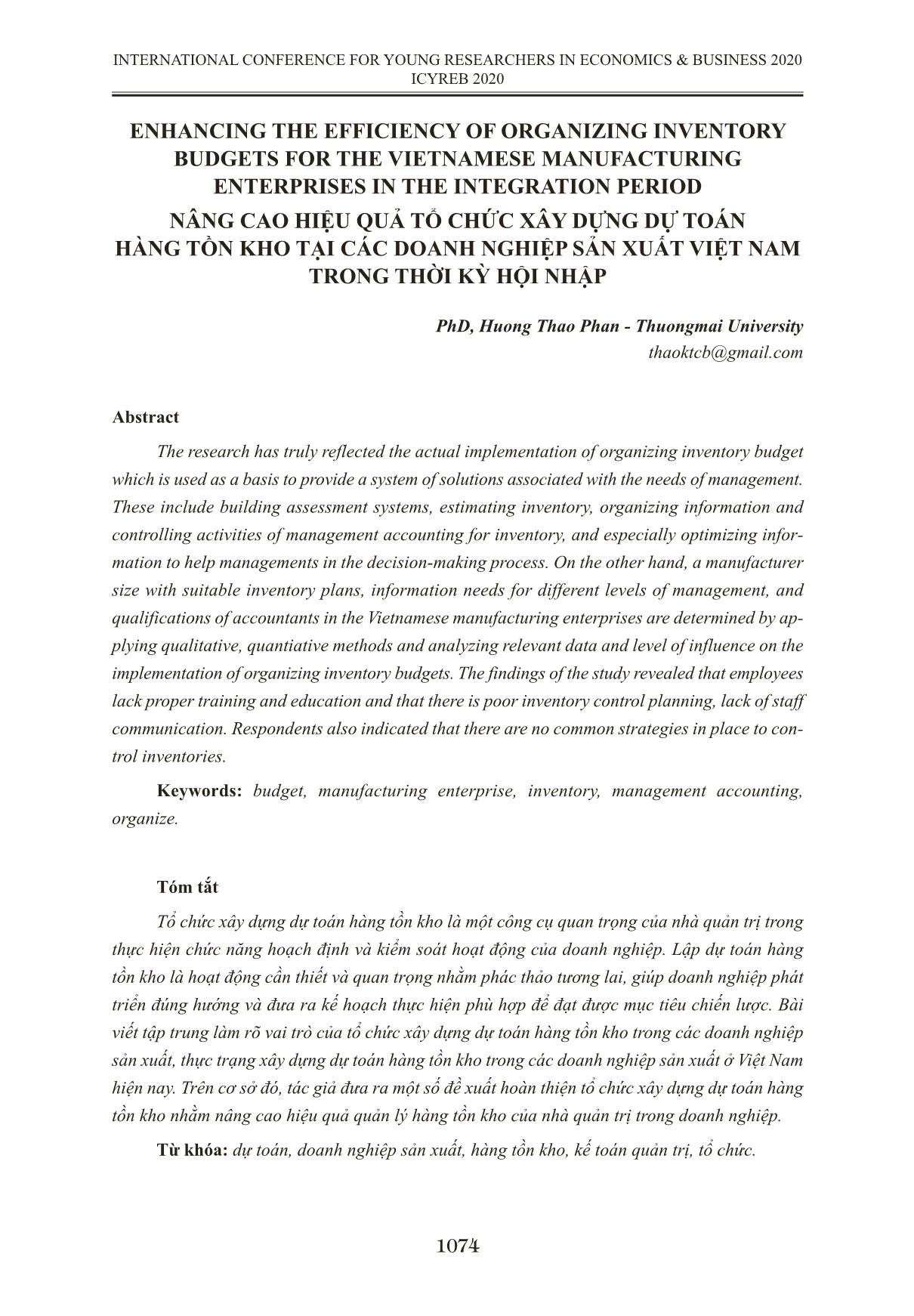
Trang 1
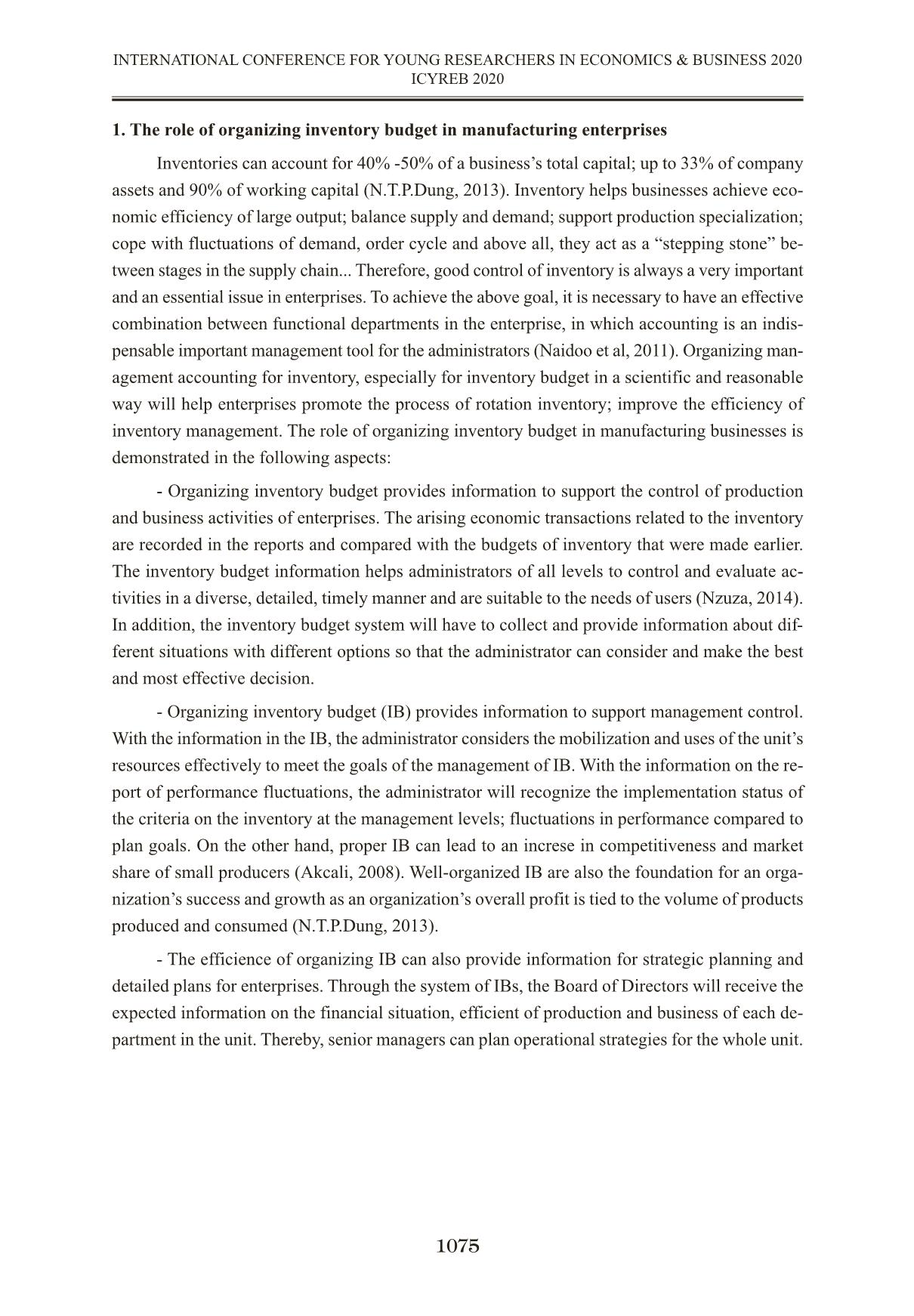
Trang 2
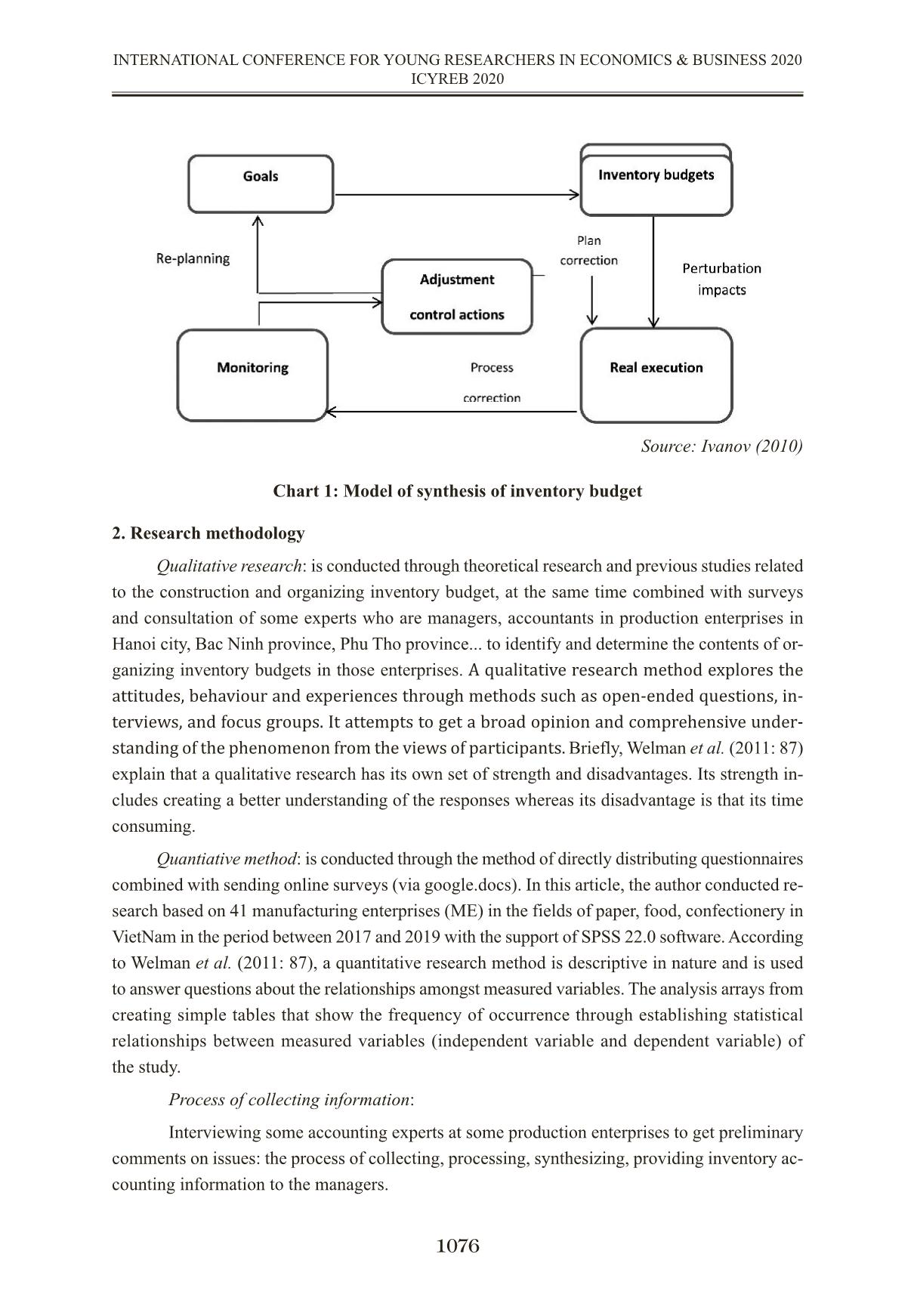
Trang 3
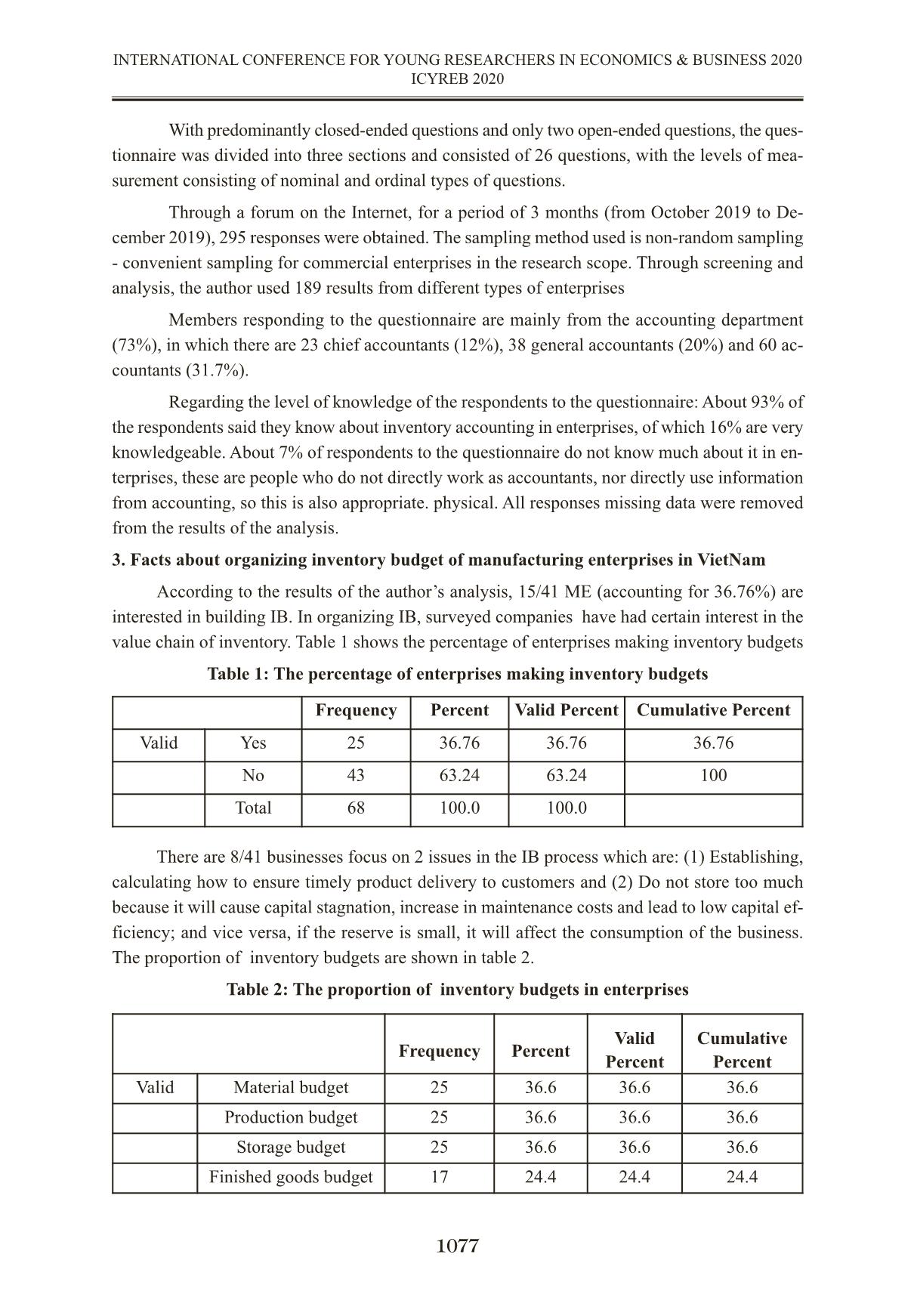
Trang 4
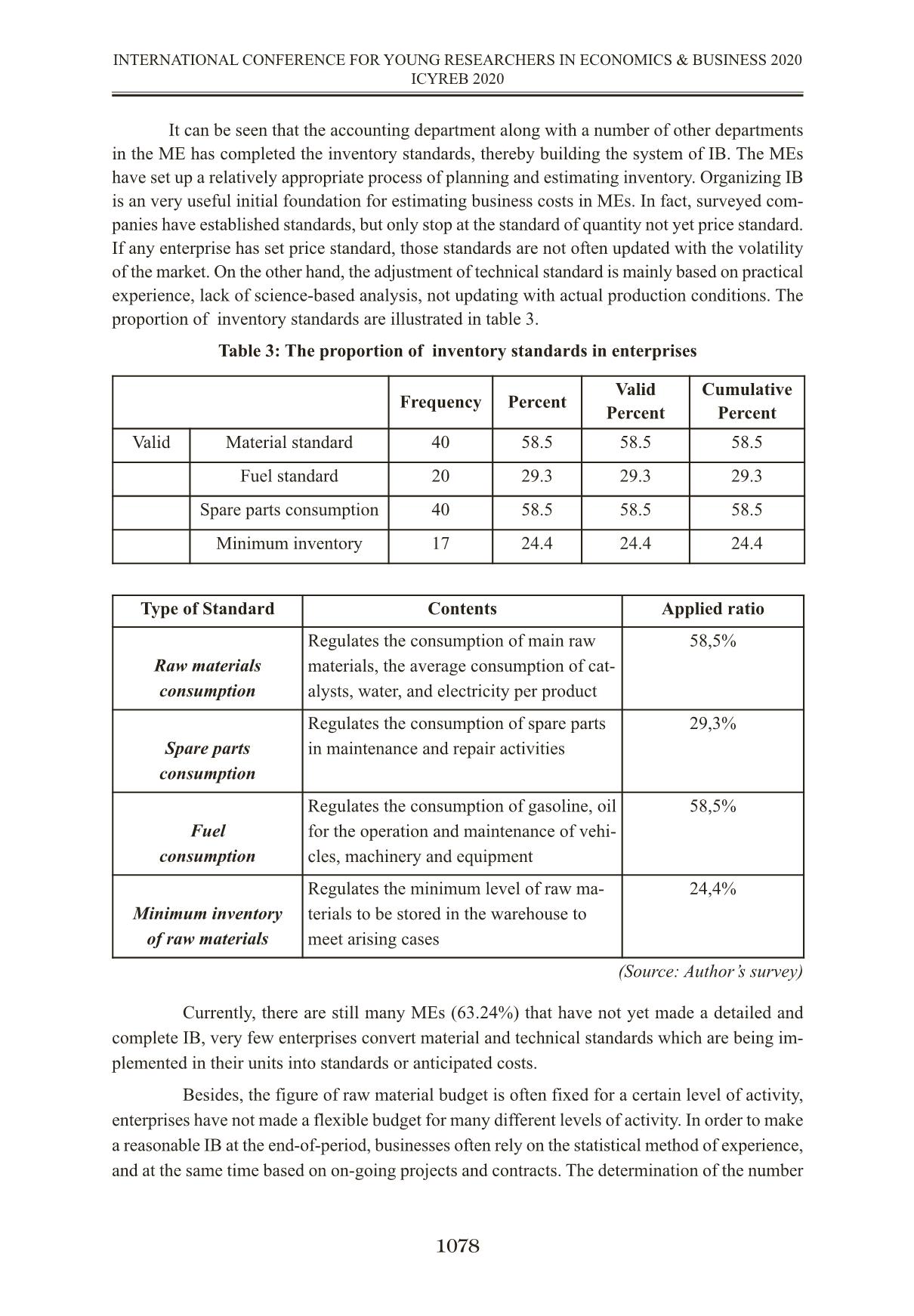
Trang 5
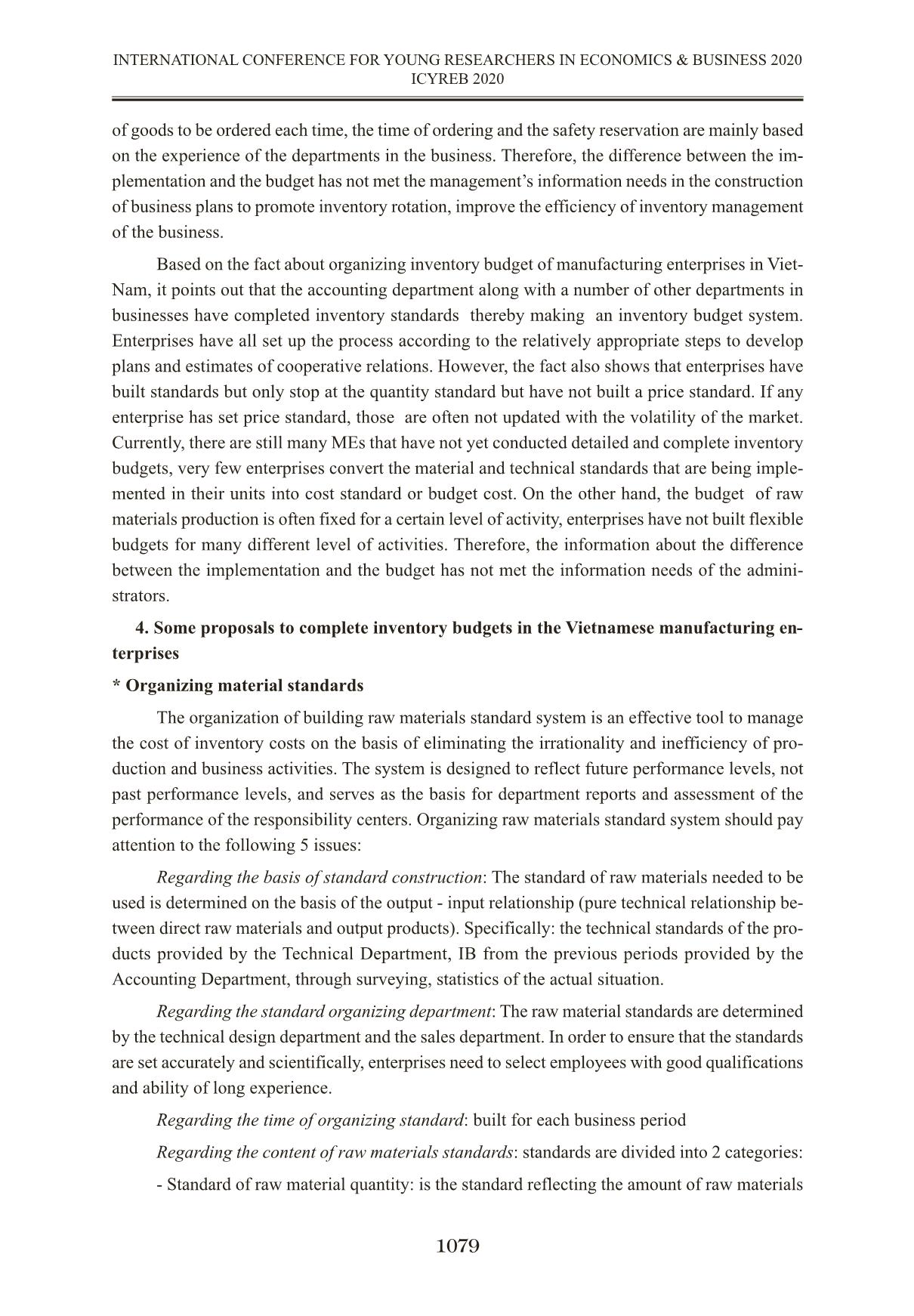
Trang 6
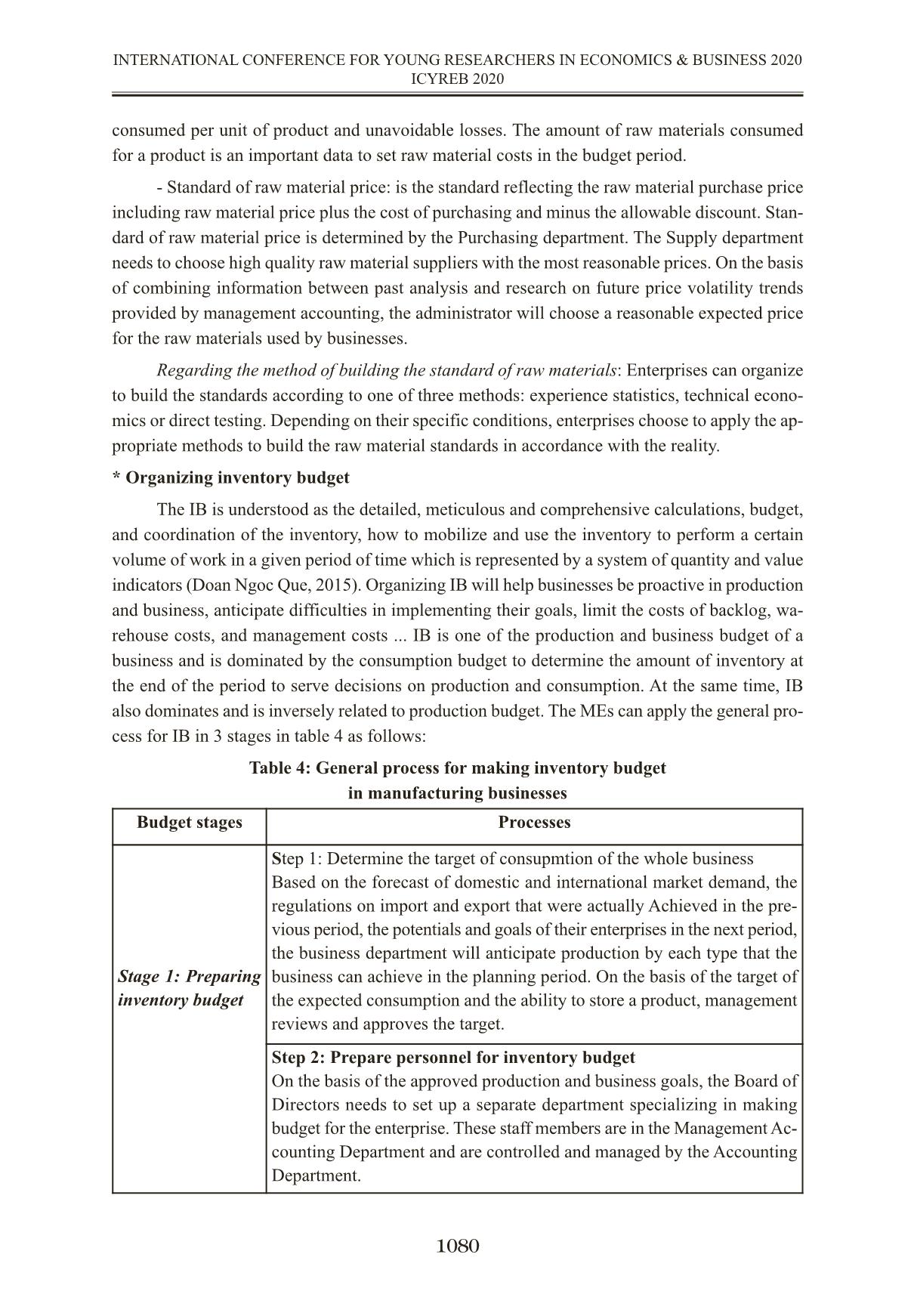
Trang 7
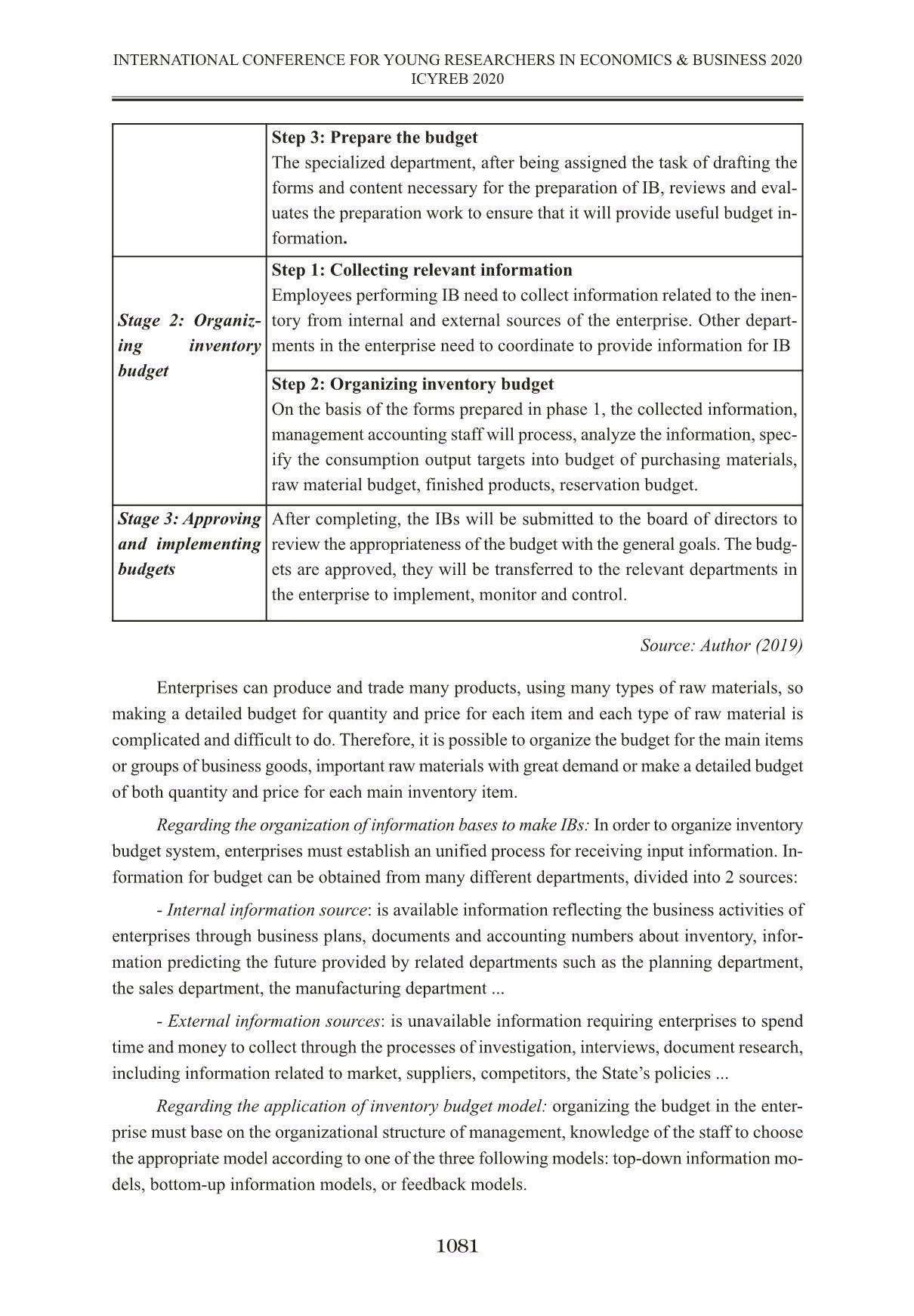
Trang 8
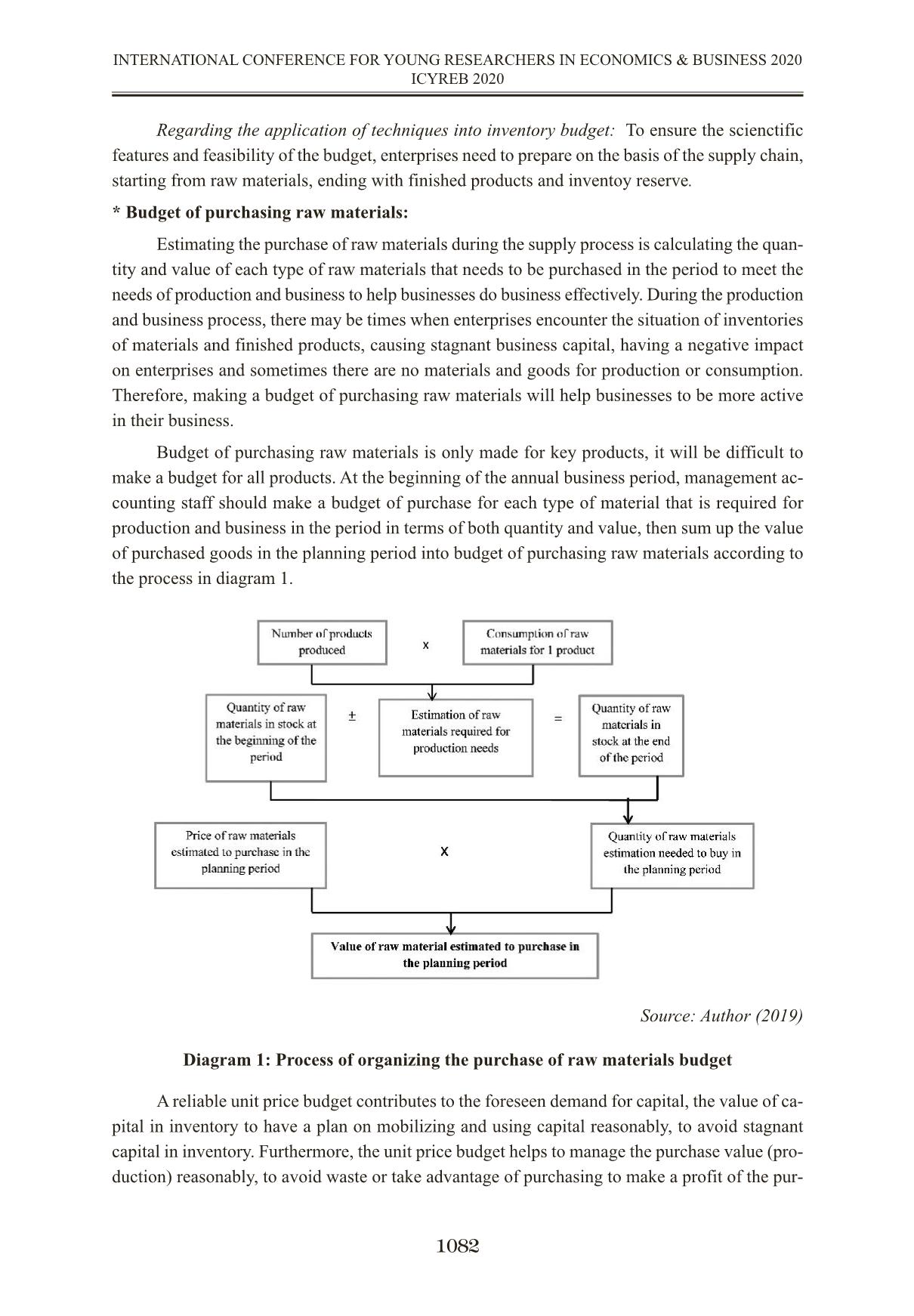
Trang 9
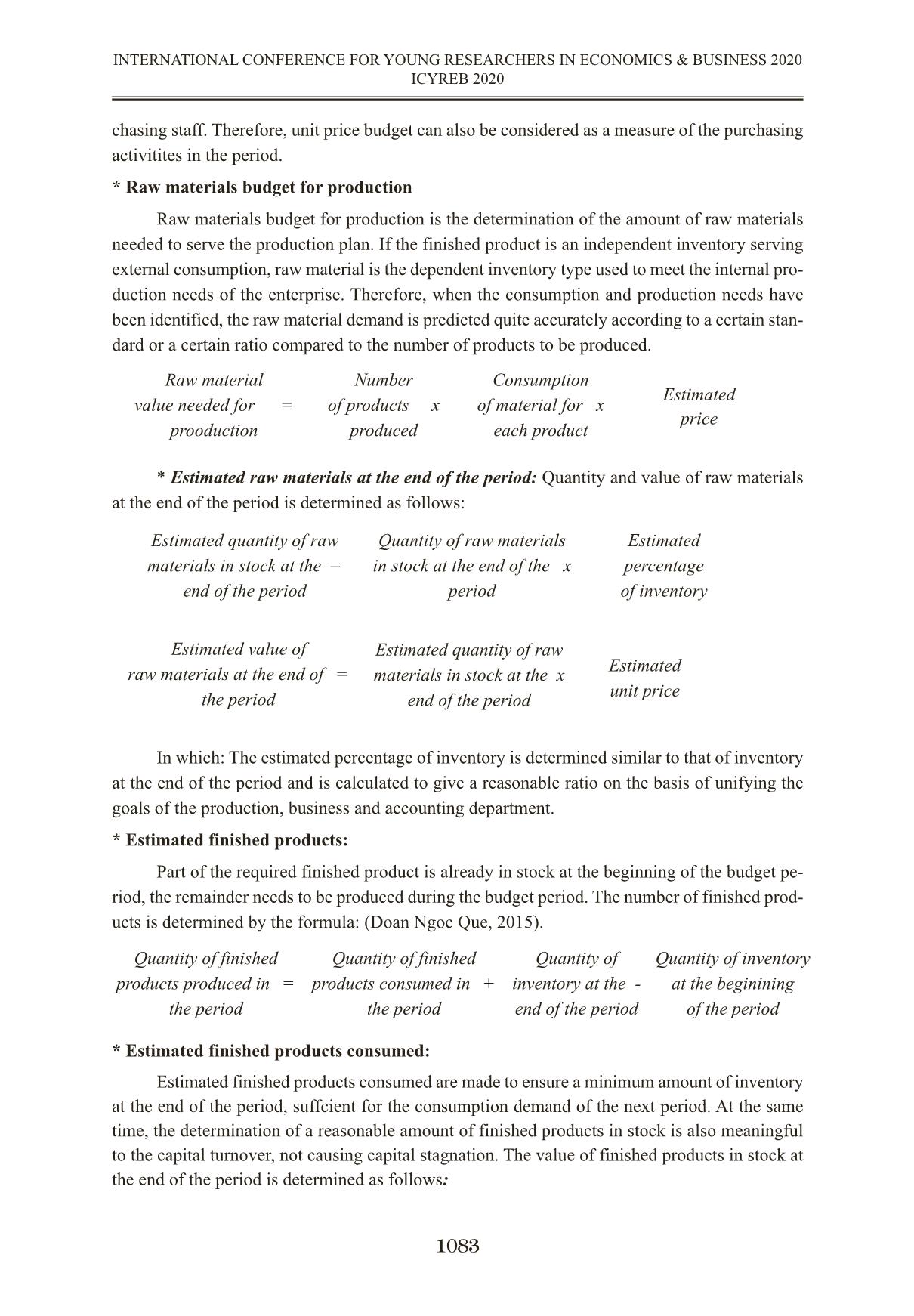
Trang 10
Tải về để xem bản đầy đủ
Tóm tắt nội dung tài liệu: Nâng cao hiệu quả tổ chức xây dựng dự toán hàng tồn kho tại các doanh nghiệp sản xuất Việt Nam trong thời kỳ hội nhập
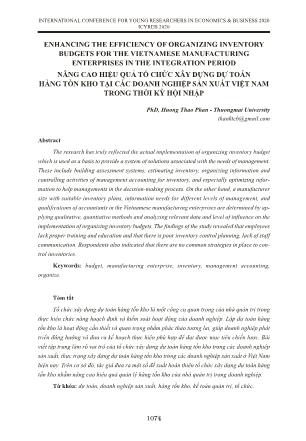
ENHANCING THE EFFICIENCY OF ORGANIZING INVENTORY BUDGETS FOR THE VIETNAMESE MANUFACTURING ENTERPRISES IN THE INTEGRATION PERIOD NÂNG CAO HIỆU QUẢ TỔ CHỨC XÂY DỰNG DỰ TOÁN HÀNG TỒN KHO TẠI CÁC DOANH NGHIỆP SẢN XUẤT VIỆT NAM TRONG THỜI KỲ HỘI NHẬP PhD, Huong Thao Phan - Thuongmai University thaoktcb@gmail.com Abstract The research has truly reflected the actual implementation of organizing inventory budget which is used as a basis to provide a system of solutions associated with the needs of management. These include building assessment systems, estimating inventory, organizing information and controlling activities of management accounting for inventory, and especially optimizing infor- mation to help managements in the decision-making process. On the other hand, a manufacturer size with suitable inventory plans, information needs for different levels of management, and qualifications of accountants in the Vietnamese manufacturing enterprises are determined by ap- plying qualitative, quantiative methods and analyzing relevant data and level of influence on the implementation of organizing inventory budgets. The findings of the study revealed that employees lack proper training and education and that there is poor inventory control planning, lack of staff communication. Respondents also indicated that there are no common strategies in place to con- trol inventories. Keywords: budget, manufacturing enterprise, inventory, management accounting, organize. Tóm tắt Tổ chức xây dựng dự toán hàng tồn kho là một công cụ quan trọng của nhà quản trị trong thực hiện chức năng hoạch định và kiểm soát hoạt động của doanh nghiệp. Lập dự toán hàng tồn kho là hoạt động cần thiết và quan trọng nhằm phác thảo tương lai, giúp doanh nghiệp phát triển đúng hướng và đưa ra kế hoạch thực hiện phù hợp để đạt được mục tiêu chiến lược. Bài viết tập trung làm rõ vai trò của tổ chức xây dựng dự toán hàng tồn kho trong các doanh nghiệp sản xuất, thực trạng xây dựng dự toán hàng tồn kho trong các doanh nghiệp sản xuất ở Việt Nam hiện nay. Trên cơ sở đó, tác giả đưa ra một số đề xuất hoàn thiện tổ chức xây dựng dự toán hàng tồn kho nhằm nâng cao hiệu quả quản lý hàng tồn kho của nhà quản trị trong doanh nghiệp. Từ khóa: dự toán, doanh nghiệp sản xuất, hàng tồn kho, kế toán quản trị, tổ chức. 1074 INTERNATIONAL CONFERENCE FOR YOUNG RESEARCHERS IN ECONOMICS & BUSINESS 2020 ICYREB 2020 1. The role of organizing inventory budget in manufacturing enterprises Inventories can account for 40% -50% of a business’s total capital; up to 33% of company assets and 90% of working capital (N.T.P.Dung, 2013). Inventory helps businesses achieve eco- nomic efficiency of large output; balance supply and demand; support production specialization; cope with fluctuations of demand, order cycle and above all, they act as a “stepping stone” be- tween stages in the supply chain... Therefore, good control of inventory is always a very important and an essential issue in enterprises. To achieve the above goal, it is necessary to have an effective combination between functional departments in the enterprise, in which accounting is an indis- pensable important management tool for the administrators (Naidoo et al, 2011). Organizing man- agement accounting for inventory, especially for inventory budget in a scientific and reasonable way will help enterprises promote the process of rotation inventory; improve the efficiency of inventory management. The role of organizing inventory budget in manufacturing businesses is demonstrated in the following aspects: - Organizing inventory budget provides information to support the control of production and business activities of enterprises. The arising economic transactions related to the inventory are recorded in the reports and compared with the budgets of inventory that were made earlier. The inventory budget information helps administrators of all levels to control and evaluate ac- tivities in a diverse, detailed, timely manner and are suitable to the needs of users (Nzuza, 2014). In addition, the inventory budget system will have to collect and provide information about dif- ferent situations with different options so that the administrator can consider and make the best and most effective decision. - Organizing inventory budget (IB) provides information to support management control. With the information in the IB, the administrator considers the mobilization and uses of the unit’s resources effectively to meet the goals of the management of IB. With the information on the re- port of performance fluctuations, the administrator will recognize the implementation status of the criteria on the inventory at the management levels; fluctuations in performance compared to plan goals. On the other hand, proper IB can lead to an increse in competitiveness and market share of small producers (Akcali, 2008). Well-organized IB are also the foundation for an orga- nizat ... terial price is determined by the Purchasing department. The Supply department needs to choose high quality raw material suppliers with the most reasonable prices. On the basis of combining information between past analysis and research on future price volatility trends provided by management accounting, the administrator will choose a reasonable expected price for the raw materials used by businesses. Regarding the method of building the standard of raw materials: Enterprises can organize to build the standards according to one of three methods: experience statistics, technical econo- mics or direct testing. Depending on their specific conditions, enterprises choose to apply the ap- propriate methods to build the raw material standards in accordance with the reality. * Organizing inventory budget The IB is understood as the detailed, meticulous and comprehensive calculations, budget, and coordination of the inventory, how to mobilize and use the inventory to perform a certain volume of work in a given period of time which is represented by a system of quantity and value indicators (Doan Ngoc Que, 2015). Organizing IB will help businesses be proactive in production and business, anticipate difficulties in implementing their goals, limit the costs of backlog, wa- rehouse costs, and management costs ... IB is one of the production and business budget of a business and is dominated by the consumption budget to determine the amount of inventory at the end of the period to serve decisions on production and consumption. At the same time, IB also dominates and is inversely related to production budget. The MEs can apply the general pro- cess for IB in 3 stages in table 4 as follows: Table 4: General process for making inventory budget in manufacturing businesses 1080 INTERNATIONAL CONFERENCE FOR YOUNG RESEARCHERS IN ECONOMICS & BUSINESS 2020 ICYREB 2020 Budget stages Processes Stage 1: Preparing inventory budget Step 1: Determine the target of consupmtion of the whole business Based on the forecast of domestic and international market demand, the regulations on import and export that were actually Achieved in the pre- vious period, the potentials and goals of their enterprises in the next period, the business department will anticipate production by each type that the business can achieve in the planning period. On the basis of the target of the expected consumption and the ability to store a product, management reviews and approves the target. Step 2: Prepare personnel for inventory budget On the basis of the approved production and business goals, the Board of Directors needs to set up a separate department specializing in making budget for the enterprise. These staff members are in the Management Ac- counting Department and are controlled and managed by the Accounting Department. Source: Author (2019) Enterprises can produce and trade many products, using many types of raw materials, so making a detailed budget for quantity and price for each item and each type of raw material is complicated and difficult to do. Therefore, it is possible to organize the budget for the main items or groups of business goods, important raw materials with great demand or make a detailed budget of both quantity and price for each main inventory item. Regarding the organization of information bases to make IBs: In order to organize inventory budget system, enterprises must establish an unified process for receiving input information. In- formation for budget can be obtained from many different departments, divided into 2 sources: - Internal information source: is available information reflecting the business activities of enterprises through business plans, documents and accounting numbers about inventory, infor- mation predicting the future provided by related departments such as the planning department, the sales department, the manufacturing department ... - External information sources: is unavailable information requiring enterprises to spend time and money to collect through the processes of investigation, interviews, document research, including information related to market, suppliers, competitors, the State’s policies ... Regarding the application of inventory budget model: organizing the budget in the enter- prise must base on the organizational structure of management, knowledge of the staff to choose the appropriate model according to one of the three following models: top-down information mo- dels, bottom-up information models, or feedback models. 1081 INTERNATIONAL CONFERENCE FOR YOUNG RESEARCHERS IN ECONOMICS & BUSINESS 2020 ICYREB 2020 Step 3: Prepare the budget The specialized department, after being assigned the task of drafting the forms and content necessary for the preparation of IB, reviews and eval- uates the preparation work to ensure that it will provide useful budget in- formation. Stage 2: Organiz- ing inventory budget Step 1: Collecting relevant information Employees performing IB need to collect information related to the inen- tory from internal and external sources of the enterprise. Other depart- ments in the enterprise need to coordinate to provide information for IB Step 2: Organizing inventory budget On the basis of the forms prepared in phase 1, the collected information, management accounting staff will process, analyze the information, spec- ify the consumption output targets into budget of purchasing materials, raw material budget, finished products, reservation budget. Stage 3: Approving and implementing budgets After completing, the IBs will be submitted to the board of directors to review the appropriateness of the budget with the general goals. The budg- ets are approved, they will be transferred to the relevant departments in the enterprise to implement, monitor and control. Regarding the application of techniques into inventory budget: To ensure the scienctific features and feasibility of the budget, enterprises need to prepare on the basis of the supply chain, starting from raw materials, ending with finished products and inventoy reserve. * Budget of purchasing raw materials: Estimating the purchase of raw materials during the supply process is calculating the quan- tity and value of each type of raw materials that needs to be purchased in the period to meet the needs of production and business to help businesses do business effectively. During the production and business process, there may be times when enterprises encounter the situation of inventories of materials and finished products, causing stagnant business capital, having a negative impact on enterprises and sometimes there are no materials and goods for production or consumption. Therefore, making a budget of purchasing raw materials will help businesses to be more active in their business. Budget of purchasing raw materials is only made for key products, it will be difficult to make a budget for all products. At the beginning of the annual business period, management ac- counting staff should make a budget of purchase for each type of material that is required for production and business in the period in terms of both quantity and value, then sum up the value of purchased goods in the planning period into budget of purchasing raw materials according to the process in diagram 1. Source: Author (2019) Diagram 1: Process of organizing the purchase of raw materials budget A reliable unit price budget contributes to the foreseen demand for capital, the value of ca- pital in inventory to have a plan on mobilizing and using capital reasonably, to avoid stagnant capital in inventory. Furthermore, the unit price budget helps to manage the purchase value (pro- duction) reasonably, to avoid waste or take advantage of purchasing to make a profit of the pur- 1082 INTERNATIONAL CONFERENCE FOR YOUNG RESEARCHERS IN ECONOMICS & BUSINESS 2020 ICYREB 2020 chasing staff. Therefore, unit price budget can also be considered as a measure of the purchasing activitites in the period. * Raw materials budget for production Raw materials budget for production is the determination of the amount of raw materials needed to serve the production plan. If the finished product is an independent inventory serving external consumption, raw material is the dependent inventory type used to meet the internal pro- duction needs of the enterprise. Therefore, when the consumption and production needs have been identified, the raw material demand is predicted quite accurately according to a certain stan- dard or a certain ratio compared to the number of products to be produced. * Estimated raw materials at the end of the period: Quantity and value of raw materials at the end of the period is determined as follows: In which: The estimated percentage of inventory is determined similar to that of inventory at the end of the period and is calculated to give a reasonable ratio on the basis of unifying the goals of the production, business and accounting department. * Estimated finished products: Part of the required finished product is already in stock at the beginning of the budget pe- riod, the remainder needs to be produced during the budget period. The number of finished prod- ucts is determined by the formula: (Doan Ngoc Que, 2015). * Estimated finished products consumed: Estimated finished products consumed are made to ensure a minimum amount of inventory at the end of the period, suffcient for the consumption demand of the next period. At the same time, the determination of a reasonable amount of finished products in stock is also meaningful to the capital turnover, not causing capital stagnation. The value of finished products in stock at the end of the period is determined as follows: 1083 INTERNATIONAL CONFERENCE FOR YOUNG RESEARCHERS IN ECONOMICS & BUSINESS 2020 ICYREB 2020 Raw material value needed for = prooduction Estimated quantity of raw materials in stock at the = end of the period Estimated value of raw materials at the end of = the period Quantity of finished products produced in = the period Quantity of finished products consumed in + the period Quantity of inventory at the - end of the period Quantity of inventory at the beginining of the period Estimated quantity of raw materials in stock at the x end of the period Estimated unit price Quantity of raw materials in stock at the end of the x period Estimated percentage of inventory Number of products x produced Consumption of material for x each product Estimated price * Determine the safe inventory level The establishment of a safe inventory level will help ME to avoid unexpected demands that enterprises did not anticipate. For example, the regulation of 10% of the average inventory for a kind finished product in the same period last year will help businesses promptly respond to unusual demands for such products. Regulation of inventory level should be based on the fol- lowing criteria: physical and chemical characteristics of inventory, demand for materials used in the previous year, expected analysis report of consumption. The safety inventory level is deter- mined by the following formula: Organizing inventory budget is a content of management accounting in enterprises in order to provide information about inventory for each enterprise to perform the function of managing consumption factors for activities, to help the administrators develop plans, control and evaluate performance as well as make reasonable decisions. In many MEs in Vietnam, in recent years, al- though awareness of the importance of IB has been raised, many enterprises still have not really paid attention to this issue. Therefore, managers in enterprises need to change their perception of the role of inventory budget in business management soon. Traditional and experienced manage- ment thinking should be replaced by modern management accounting methods, thus adding and updating new knowledge to improve the efficiency of inventory management in enterprises. REFERENCES 1. Akcali, E. and Bayindir, Z. P. (2008), ‘Analyzing the effects of inventory cost setting rules in a disassembly and recovery environment’, International journal of production research. 2. Dimitrios P. Koumanakos (2004), ‘The effect of inventory management accounting on firm performance’, Thesis of doctor, University of Patras, Greece House. 3. Doan Ngoc Que (2015), ‘Management Accounting Text book’, HochiMinh Economic Publish 4. Ivanov (2010), ‘An adaptive framework for aligning (re)planning decisions on supply chain strategy, design, tactics, and operations’, International journal of production research, 48(13): 4010. 5. Jonsson, P. and Mattsson, S.A.(2008), ‘Inventory management practices and their implications on perceived planning performance’, International journal of production research, 46(7): 1788-1789. 1084 INTERNATIONAL CONFERENCE FOR YOUNG RESEARCHERS IN ECONOMICS & BUSINESS 2020 ICYREB 2020 Value of finished products in stock at the end of the = period Safety inventory level = Expected demand for product consumption in the x next period Estimated percentage of inventory Number of finished products in stock at the = end of the period Product price per unit 6. Konstantopoulos, Nikolaos, Bekiaris, Michail G, Zounta, Stella (2007), ‘A Dynamic Simulation Model of the Inventories Management Accounting Information Systems (MAIS)’, AIP Conference Proceedings, Vol. 963 Issue 2. 7. Mayanja MK và Vander Poll HM (2011), ‘Management accounting: An instrument for implementing effective corporate governance’, African Journal of Business Management Vol. 5(30) 8. Merchant (2017), ‘Management Control Systems: Performance Measurement, Evalua- tion and Incentives’, Pitman Publishing 9. Mohammaditabar, D., Hassan, G. S. and O’Brien, C. (2012), ‘Inventory control system design by integrating inventory classification and policy selection’, International journal of pro- duction economics, 140(2): 655. 10. Naidoo, V. & Wu, T. (2011), ‘Marketing strategy implementation in higher education: A mixed approach for model development and testing’, Journal of marketing management. 11. Nguyen Thi Phuong Dung (2013), ‘The evaluation of Management accounting practices in VietNam: empirical evidience from VietNamese food and beverage enterprises’, Thesis of doc- tor, Tohoku University. 12. Nzuza (2013), ‘Factors affecting the success of inventory control in the Stores Division of the eThekwini Municipality, Durban: a case study’, Thesis of doctor, Durban University of Technology Durban, South Africa. 13. Welman, C, Kruger, F. and Mitchell, B. (2011), ‘Research methodology’, 3rd ed. Cape Town: Oxford University Press South Africa. 1085 INTERNATIONAL CONFERENCE FOR YOUNG RESEARCHERS IN ECONOMICS & BUSINESS 2020 ICYREB 2020
File đính kèm:
nang_cao_hieu_qua_to_chuc_xay_dung_du_toan_hang_ton_kho_tai.pdf