Lower bound of performance index of anti - sway control of a pendulum using on-off damping radial spring - damper
Residual sway vibration of a pendulum is often met in pendulum-type structures
such as ropeway gondola, crane, floating structures (e.g., ships or tension leg platforms)
or spacecraft. The anti-sway control problem of a single pendulum is often approached
by regulating the movement of the fulcrum point, which can be referred, for example, in
a numerous studies on anti-sway control of crane [1].
However, this paper does not consider the approach of moving the fulcrum point.
In some recent studies, we have introduced the approach of radial spring-damper to reduce the sway motion [2, 3]. It works in the principle of nonlinear Coriolis damping [4].
Without adaptability and flexibility, the passive damping, however, has some shortcomings. For example, the too small passive damping can not prevent the resonance motion
but the too large passive damping reduces the damper motion and dissipation energy.
The on-off damping is the simplest way to improve the adaptability of the damping. The
device producing on-off damping is much cheaper and easier to control than the one
producing continuous state damping [5]. The on-off damping, as a method of vibration
control, has been studied widely from the point of view of both control strategies and
implemented devices, see for example [6–9] and references therein.
The on-off damping strategies have been developed extensively but all the studied
controllers are inapplicable to the problem in this paper because the damper’s radial
force is not codirectional with the sway motion. The novelty in this paper is a clear
derivation of the lower bound of performance index of an on-off damping radial springdamper incorporating to a simple pendulum. This lower bound gives a useful analytical
benchmark to evaluate any other practical controller.
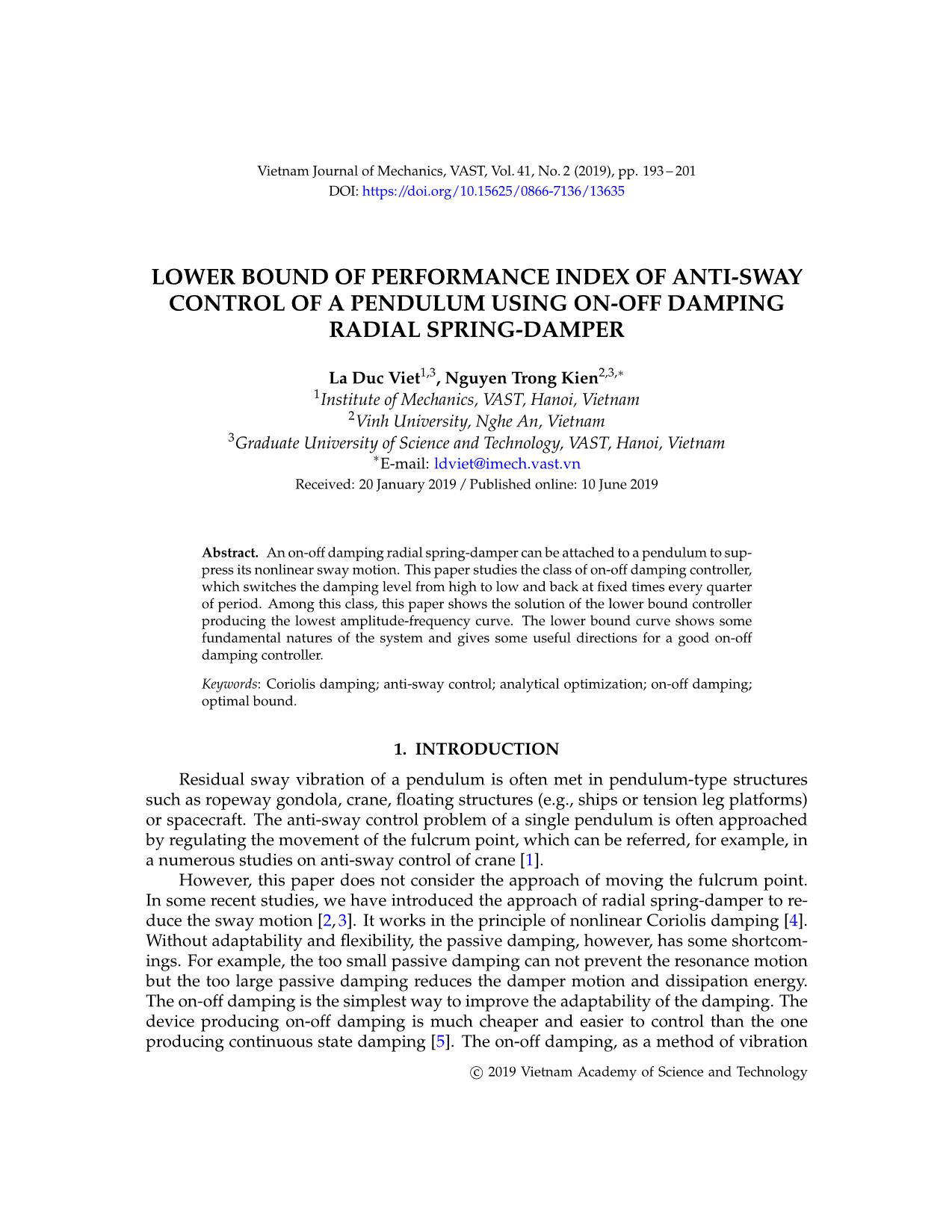
Trang 1
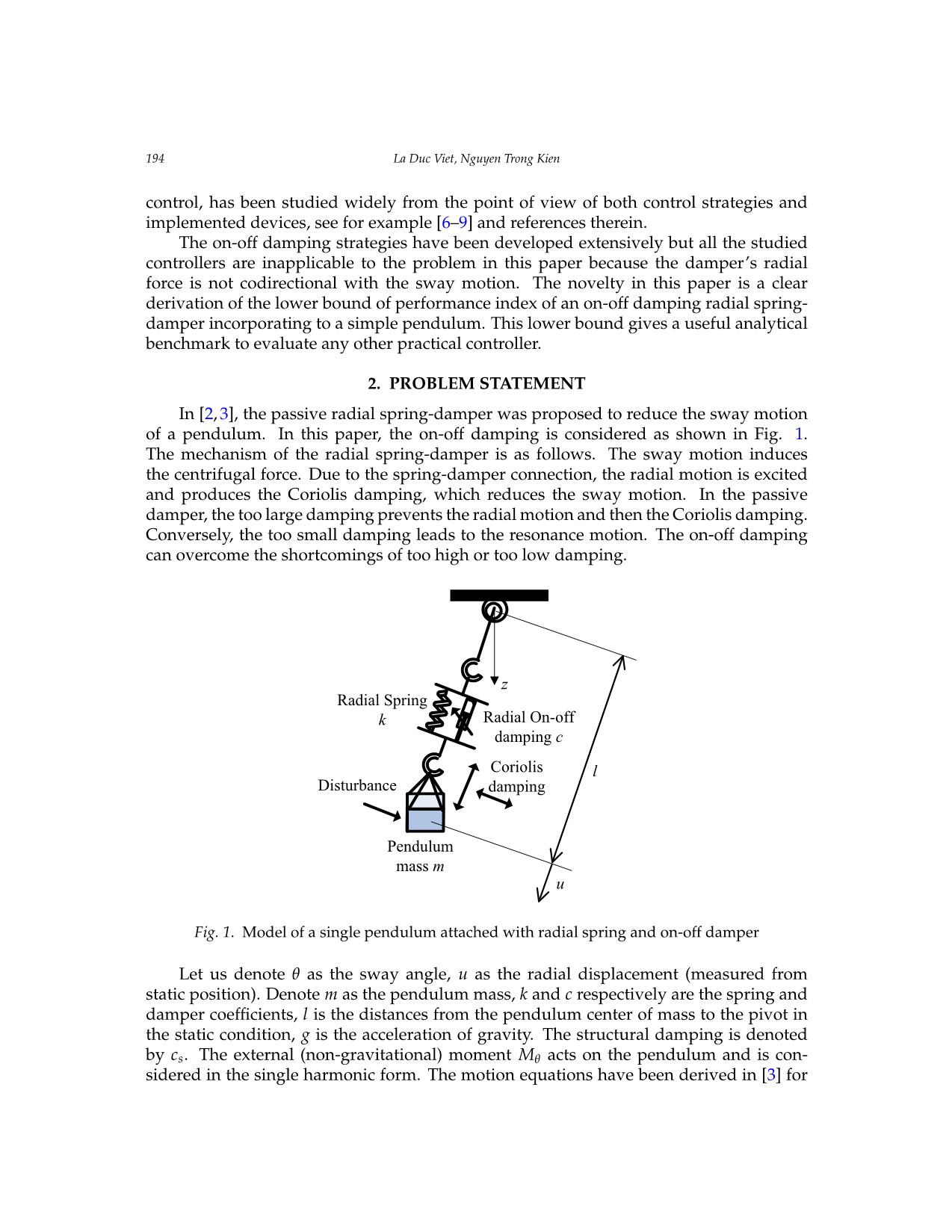
Trang 2
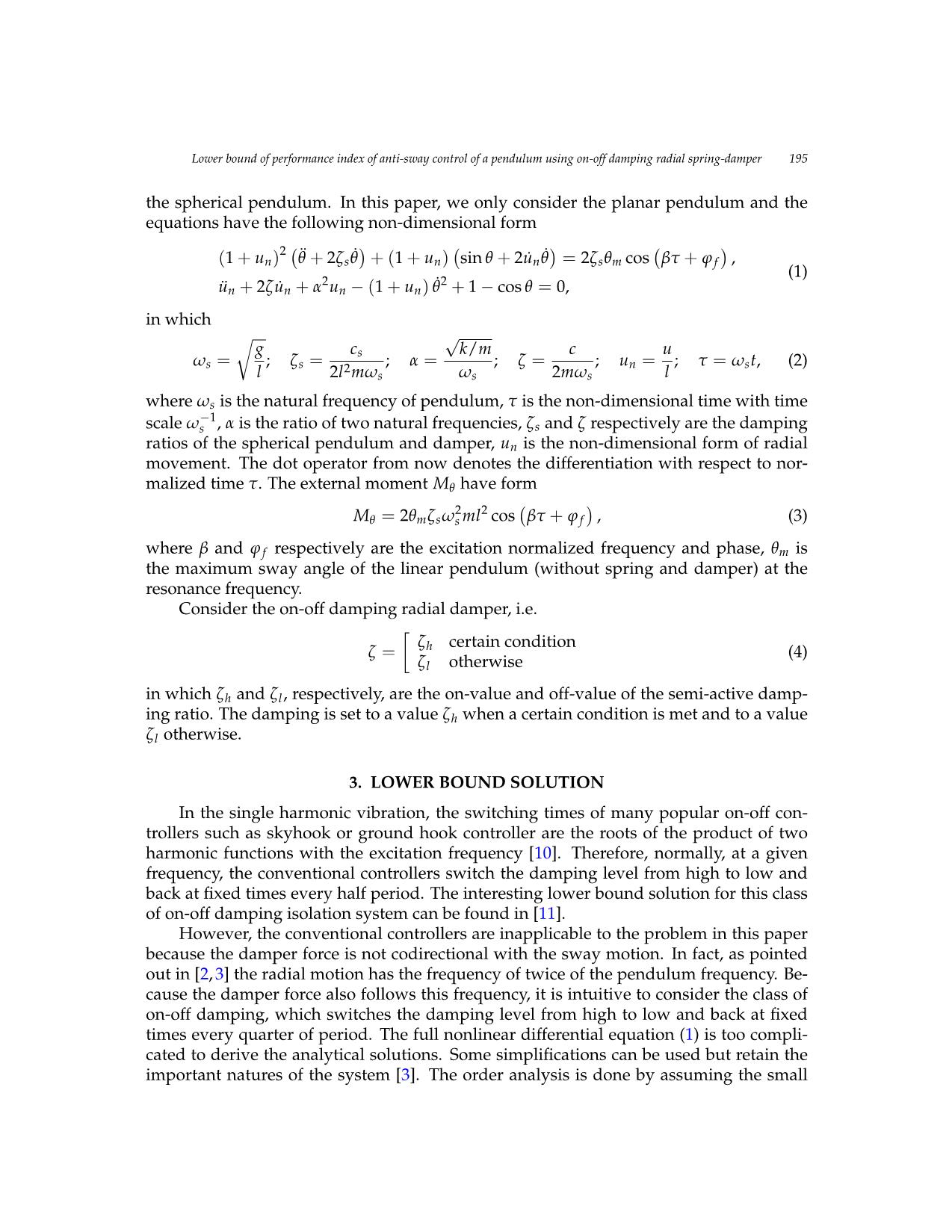
Trang 3
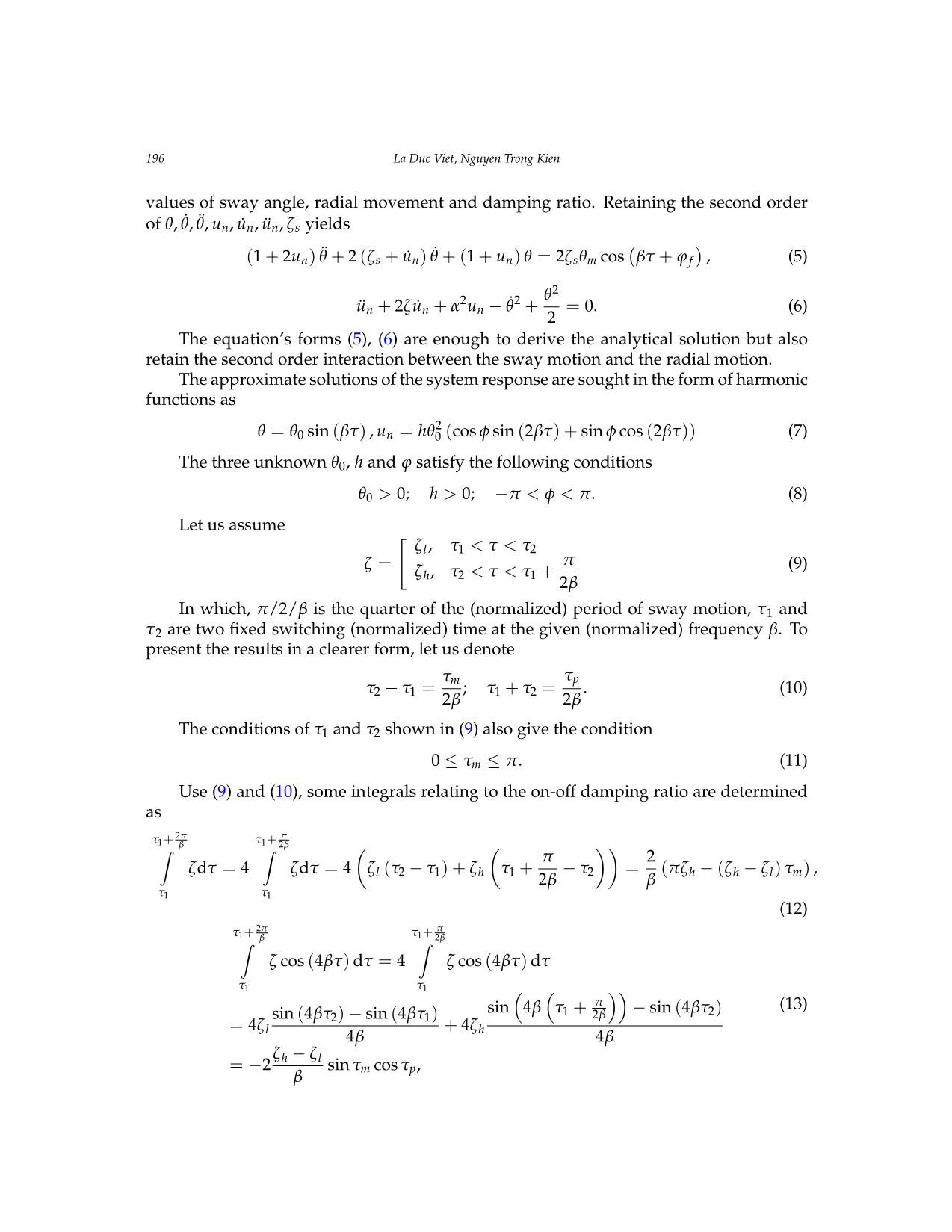
Trang 4
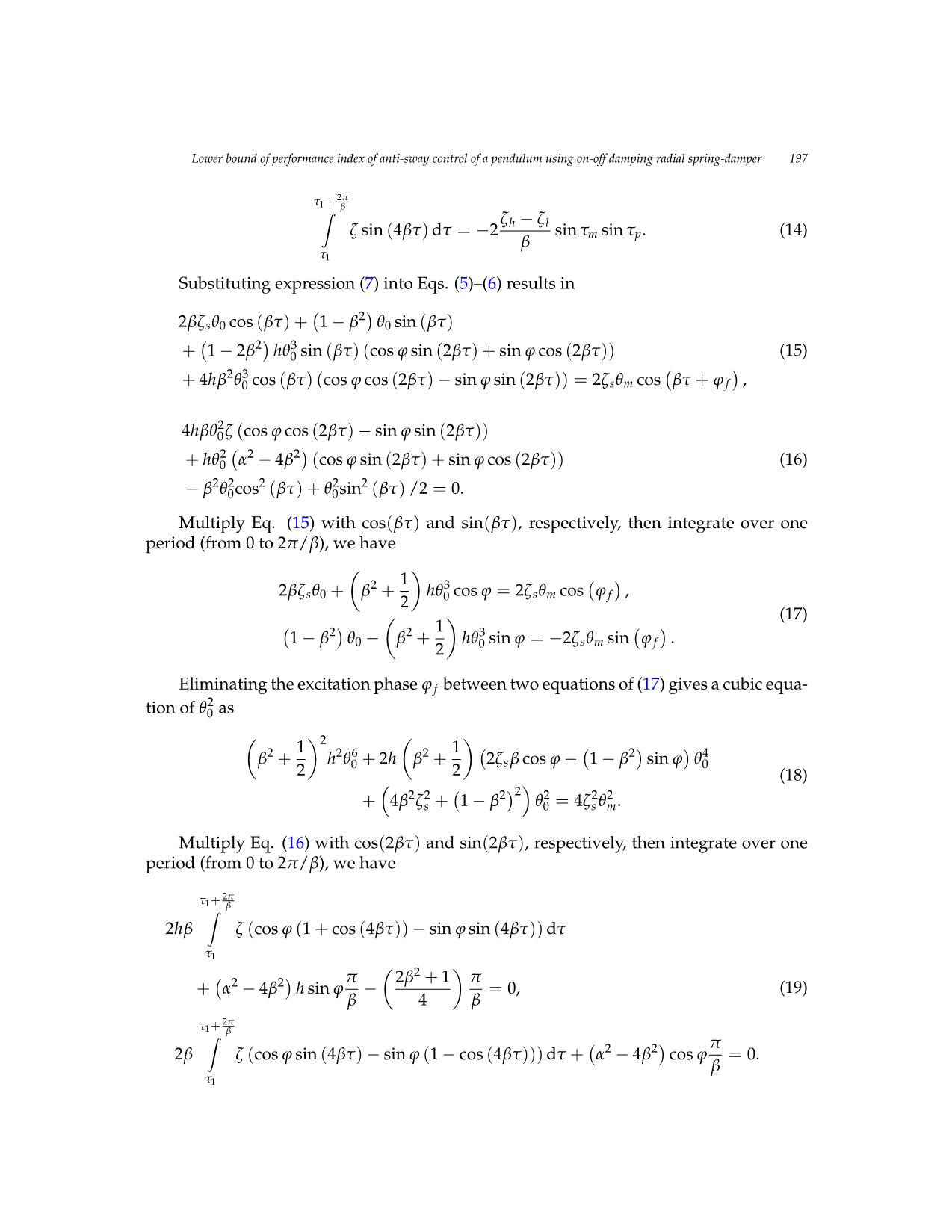
Trang 5
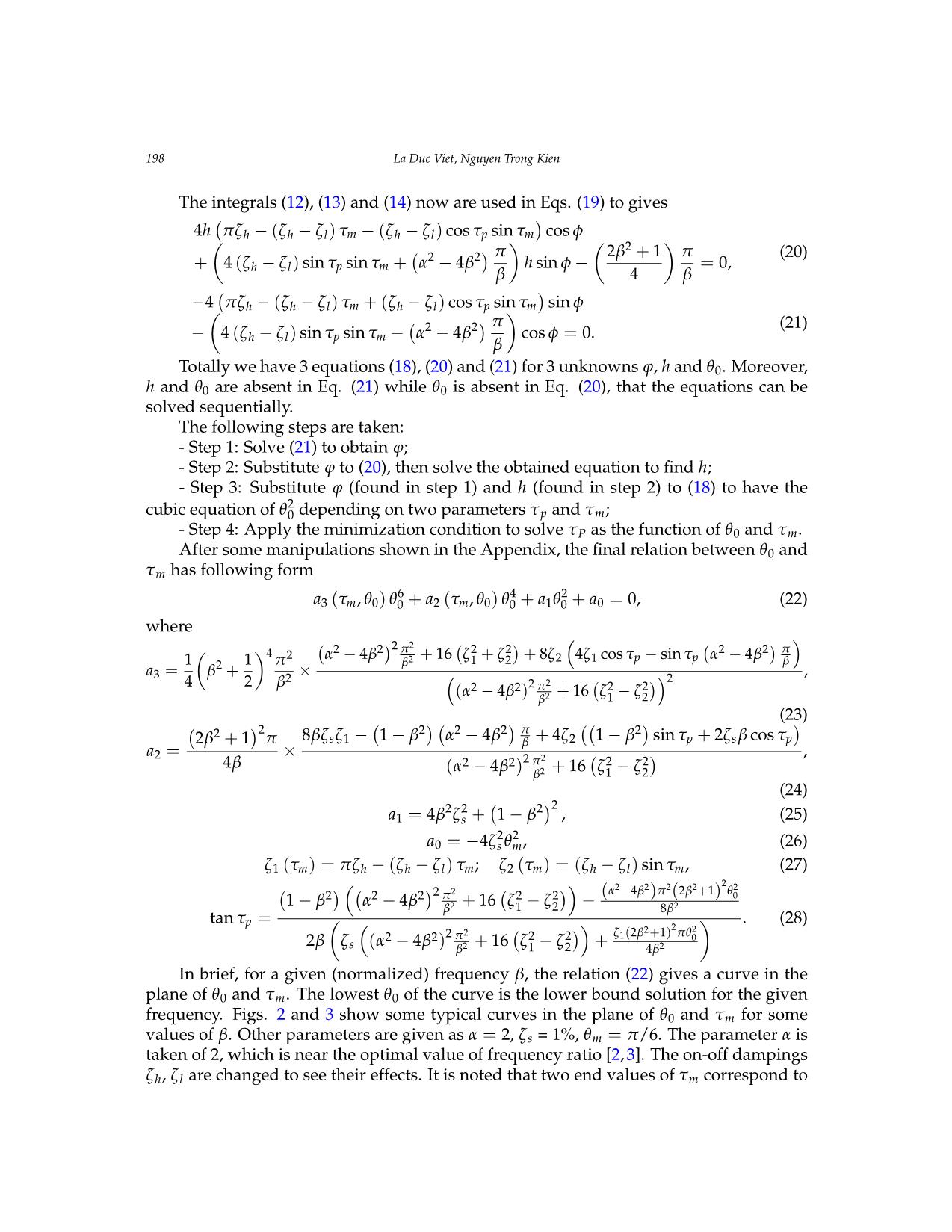
Trang 6
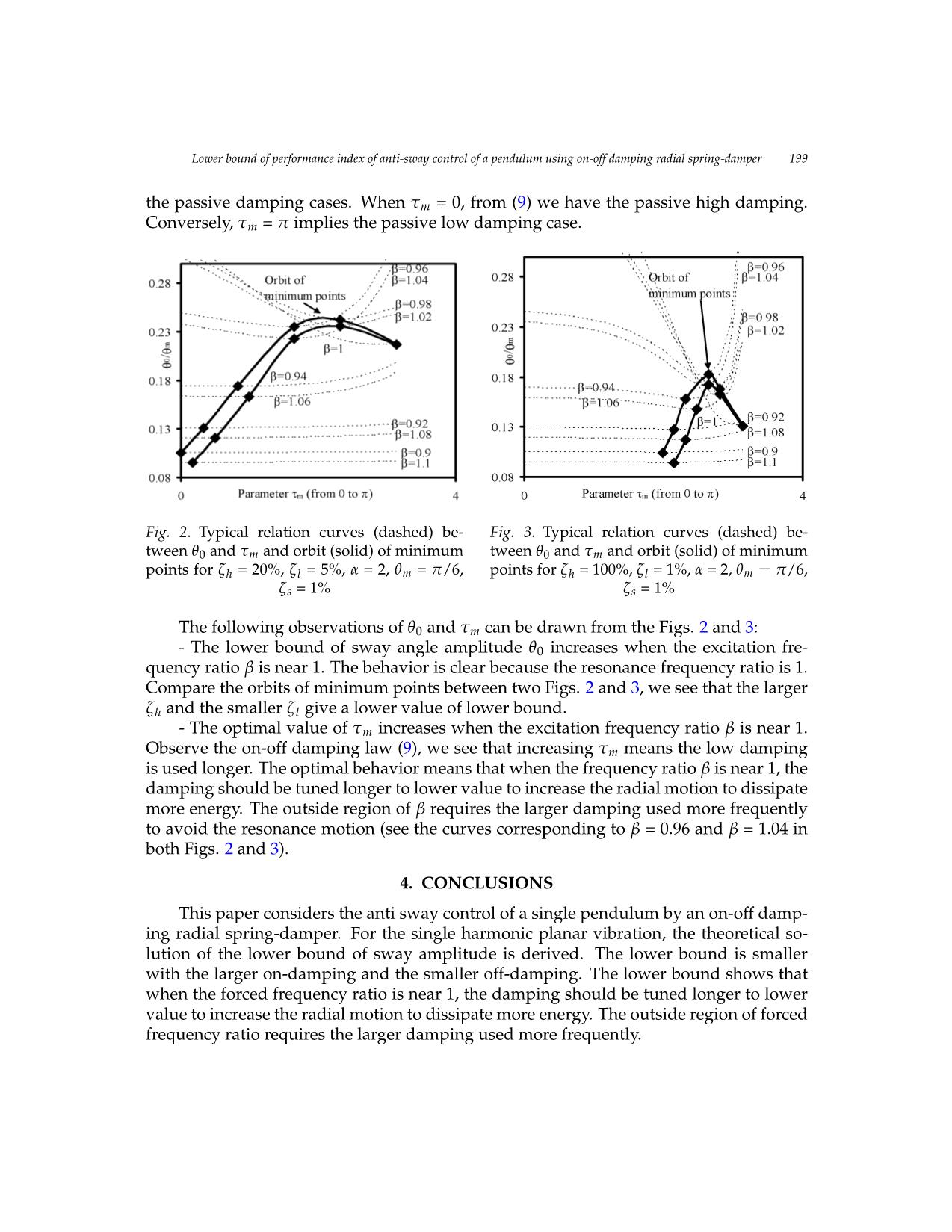
Trang 7
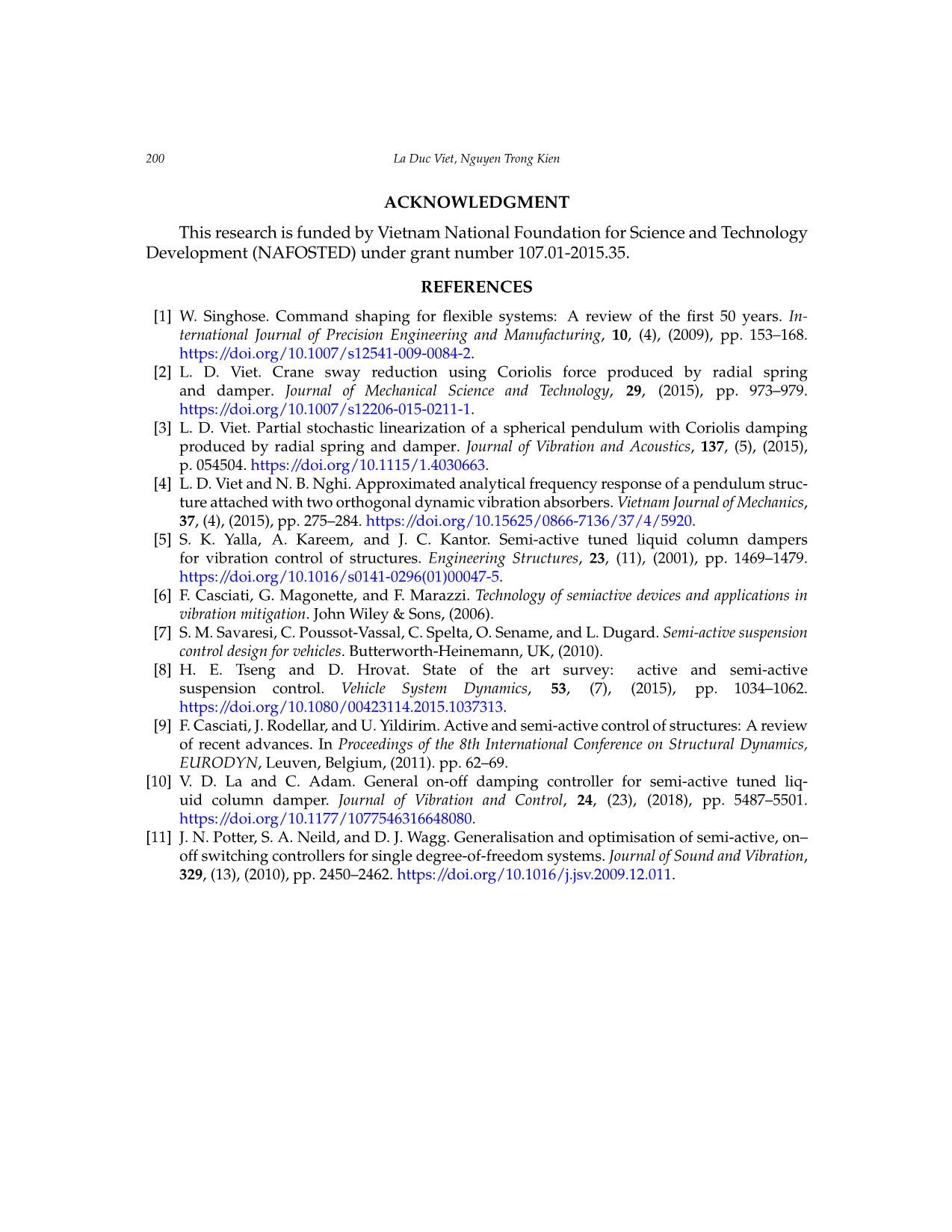
Trang 8
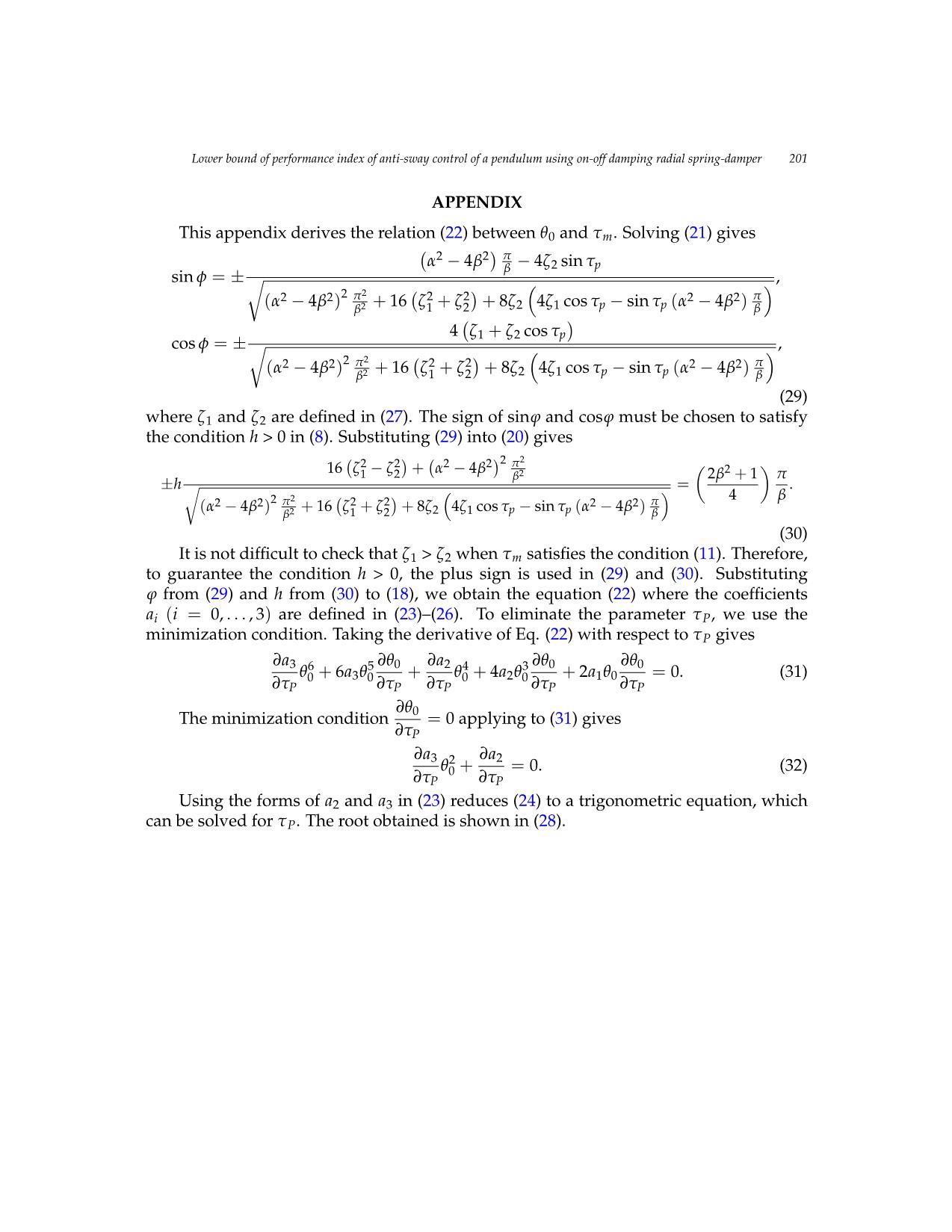
Trang 9
Tóm tắt nội dung tài liệu: Lower bound of performance index of anti - sway control of a pendulum using on-off damping radial spring - damper
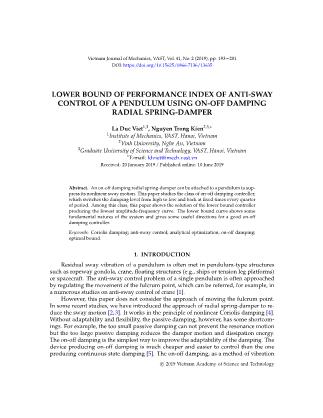
Vietnam Journal of Mechanics, VAST, Vol.41, No. 2 (2019), pp. 193 – 201 DOI: https://doi.org/10.15625/0866-7136/13635 LOWER BOUND OF PERFORMANCE INDEX OF ANTI-SWAY CONTROL OF A PENDULUM USING ON-OFF DAMPING RADIAL SPRING-DAMPER La Duc Viet1,3, Nguyen Trong Kien2,3,∗ 1Institute of Mechanics, VAST, Hanoi, Vietnam 2Vinh University, Nghe An, Vietnam 3Graduate University of Science and Technology, VAST, Hanoi, Vietnam ∗E-mail: ldviet@imech.vast.vn Received: 20 January 2019 / Published online: 10 June 2019 Abstract. An on-off damping radial spring-damper can be attached to a pendulum to sup- press its nonlinear sway motion. This paper studies the class of on-off damping controller, which switches the damping level from high to low and back at fixed times every quarter of period. Among this class, this paper shows the solution of the lower bound controller producing the lowest amplitude-frequency curve. The lower bound curve shows some fundamental natures of the system and gives some useful directions for a good on-off damping controller. Keywords: Coriolis damping; anti-sway control; analytical optimization; on-off damping; optimal bound. 1. INTRODUCTION Residual sway vibration of a pendulum is often met in pendulum-type structures such as ropeway gondola, crane, floating structures (e.g., ships or tension leg platforms) or spacecraft. The anti-sway control problem of a single pendulum is often approached by regulating the movement of the fulcrum point, which can be referred, for example, in a numerous studies on anti-sway control of crane [1]. However, this paper does not consider the approach of moving the fulcrum point. In some recent studies, we have introduced the approach of radial spring-damper to re- duce the sway motion [2,3]. It works in the principle of nonlinear Coriolis damping [4]. Without adaptability and flexibility, the passive damping, however, has some shortcom- ings. For example, the too small passive damping can not prevent the resonance motion but the too large passive damping reduces the damper motion and dissipation energy. The on-off damping is the simplest way to improve the adaptability of the damping. The device producing on-off damping is much cheaper and easier to control than the one producing continuous state damping [5]. The on-off damping, as a method of vibration c 2019 Vietnam Academy of Science and Technology 194 La Duc Viet, Nguyen Trong Kien control, has been studied widely from the point of view of both control strategies and implemented devices, see for example [6–9] and references therein. The on-off damping strategies have been developed extensively but all the studied controllers are inapplicable to the problem in this paper because the damper’s radial force is not codirectional with the sway motion. The novelty in this paper is a clear derivation of the lower bound of performance index of an on-off damping radial spring- damper incorporating to a simple pendulum. This lower bound gives a useful analytical benchmark to evaluate any other practical controller. 2. PROBLEM STATEMENT In [2,3], the passive radial spring-damper was proposed to reduce the sway motion of a pendulum. In this paper, the on-off damping is considered as shown in Fig.1. The mechanism of the radial spring-damper is as follows. The sway motion induces the centrifugal force. Due to the spring-damper connection, the radial motion is excited andradial produces spring-damper the is Coriolis as follows. damping, The sway motion which induces reduces the centrifugal the sway force. motion. Due to Inthe thespring passive- damper,damper connection, the too large the radial damping motion preventsis excited and the produces radial motionthe Coriolis and damping, then the which Coriolis reduces damping. the Conversely,sway motion. In the the too passive small damper, damping the too leads large todamping the resonance prevents the motion. radial motion The on-offand then damping the canCoriolis overcome damping. the Conversely, shortcomings the too of small too high damping or too leads low to thedamping. resonance motion. The on-off damping can overcome the shortcomings of too high or too low damping. z Radial Spring k Radial On-off damping c Coriolis l Disturbance damping Pendulum mass m u Figure 1. Model of a single pendulum attached with radial spring and on-off damper Fig. 1. Model of a single pendulum attached with radial spring and on-off damper Let us denote q as the sway angle, u as the radial displacement (measured from static position). Denote m as the pendulum mass, k and c respectively are the spring and damper coefficients, l is the distancesLet from us denote the penduluθ asm center the sway of mass angle, to the pivotu as in the the radialstatic condition displacement, g is the acceleration (measured of from static position). Denote m as the pendulum mass, k and c respectively are t ... n + α un − (1 + un) θ˙ + 1 − cos θ = 0, in which √ r g c k/m c u = = s = = = = ωs ; ζs 2 ; α ; ζ ; un ; τ ωst, (2) l 2l mωs ωs 2mωs l where ωs is the natural frequency of pendulum, τ is the non-dimensional time with time −1 scale ωs , α is the ratio of two natural frequencies, ζs and ζ respectively are the damping ratios of the spherical pendulum and damper, un is the non-dimensional form of radial movement. The dot operator from now denotes the differentiation with respect to nor- malized time τ. The external moment Mθ have form 2 2 Mθ = 2θmζsωs ml cos βτ + ϕ f , (3) where β and ϕ f respectively are the excitation normalized frequency and phase, θm is the maximum sway angle of the linear pendulum (without spring and damper) at the resonance frequency. Consider the on-off damping radial damper, i.e. ζ certain condition ζ = h (4) ζl otherwise in which ζh and ζl, respectively, are the on-value and off-value of the semi-active damp- ing ratio. The damping is set to a value ζh when a certain condition is met and to a value ζl otherwise. 3. LOWER BOUND SOLUTION In the single harmonic vibration, the switching times of many popular on-off con- trollers such as skyhook or ground hook controller are the roots of the product of two harmonic functions with the excitation frequency [10]. Therefore, normally, at a given frequency, the conventional controllers switch the damping level from high to low and back at fixed times every half period. The interesting lower bound solution for this class of on-off damping isolation system can be found in [11]. However, the conventional controllers are inapplicable to the problem in this paper because the damper force is not codirectional with the sway motion. In fact, as pointed out in [2,3] the radial motion has the frequency of twice of the pendulum frequency. Be- cause the damper force also follows this frequency, it is intuitive to consider the class of on-off damping, which switches the damping level from high to low and back at fixed times every quarter of period. The full nonlinear differential equation (1) is too compli- cated to derive the analytical solutions. Some simplifications can be used but retain the important natures of the system [3]. The order analysis is done by assuming the small 196 La Duc Viet, Nguyen Trong Kien values of sway angle, radial movement and damping ratio. Retaining the second order of θ, θ˙, θ¨, un, u˙ n, u¨n, ζs yields (1 + 2un) θ¨ + 2 (ζs + u˙ n) θ˙ + (1 + un) θ = 2ζsθm cos βτ + ϕ f , (5) θ2 u¨ + 2ζu˙ + α2u − θ˙2 + = 0. (6) n n n 2 The equation’s forms (5), (6) are enough to derive the analytical solution but also retain the second order interaction between the sway motion and the radial motion. The approximate solutions of the system response are sought in the form of harmonic functions as 2 θ = θ0 sin (βτ) , un = hθ0 (cos φ sin (2βτ) + sin φ cos (2βτ)) (7) The three unknown θ0, h and ϕ satisfy the following conditions θ0 > 0; h > 0; −π < φ < π. (8) Let us assume " ζl, τ1 < τ < τ2 = π ζ ζ , τ < τ < τ + (9) h 2 1 2β In which, π/2/β is the quarter of the (normalized) period of sway motion, τ1 and τ2 are two fixed switching (normalized) time at the given (normalized) frequency β. To present the results in a clearer form, let us denote τ τp τ − τ = m ; τ + τ = . (10) 2 1 2β 1 2 2β The conditions of τ1 and τ2 shown in (9) also give the condition 0 ≤ τm ≤ π. (11) Use (9) and (10), some integrals relating to the on-off damping ratio are determined as 2π π τ1+ β τ1+ 2β Z Z π 2 ζdτ = 4 ζdτ = 4 ζ (τ − τ ) + ζ τ + − τ = (πζ − (ζ − ζ ) τ ) , l 2 1 h 1 2β 2 β h h l m τ1 τ1 (12) 2π π τ1+ β τ1+ 2β Z Z ζ cos (4βτ) dτ = 4 ζ cos (4βτ) dτ τ τ 1 1 + π − ( ) (13) sin (4βτ ) − sin (4βτ ) sin 4β τ1 2β sin 4βτ2 = 4ζ 2 1 + 4ζ l 4β h 4β ζ − ζ = −2 h l sin τ cos τ , β m p Lower bound of performance index of anti-sway control of a pendulum using on-off damping radial spring-damper 197 2π τ1+ β Z ζ − ζ ζ sin (4βτ) dτ = −2 h l sin τ sin τ . (14) β m p τ1 Substituting expression (7) into Eqs. (5)–(6) results in 2 2βζsθ0 cos (βτ) + 1 − β θ0 sin (βτ) 2 3 + 1 − 2β hθ0 sin (βτ)(cos ϕ sin (2βτ) + sin ϕ cos (2βτ)) (15) 2 3 + 4hβ θ0 cos (βτ)(cos ϕ cos (2βτ) − sin ϕ sin (2βτ)) = 2ζsθm cos βτ + ϕ f , 2 4hβθ0ζ (cos ϕ cos (2βτ) − sin ϕ sin (2βτ)) 2 2 2 + hθ0 α − 4β (cos ϕ sin (2βτ) + sin ϕ cos (2βτ)) (16) 2 2 2 2 2 − β θ0cos (βτ) + θ0sin (βτ) /2 = 0. Multiply Eq. (15) with cos(βτ) and sin(βτ), respectively, then integrate over one period (from 0 to 2π/β), we have 1 2βζ θ + β2 + hθ3 cos ϕ = 2ζ θ cos ϕ , s 0 2 0 s m f (17) 1 1 − β2 θ − β2 + hθ3 sin ϕ = −2ζ θ sin ϕ . 0 2 0 s m f Eliminating the excitation phase ϕ f between two equations of (17) gives a cubic equa- 2 tion of θ0 as 2 2 1 2 6 2 1 2 4 β + h θ0 + 2h β + 2ζsβ cos ϕ − 1 − β sin ϕ θ0 2 2 (18) 2 2 22 2 2 2 + 4β ζs + 1 − β θ0 = 4ζs θm. Multiply Eq. (16) with cos(2βτ) and sin(2βτ), respectively, then integrate over one period (from 0 to 2π/β), we have 2π τ1+ β Z 2hβ ζ (cos ϕ (1 + cos (4βτ)) − sin ϕ sin (4βτ)) dτ τ1 π 2β2 + 1 π + α2 − 4β2 h sin ϕ − = 0, (19) β 4 β 2π τ1+ β Z π 2β ζ (cos ϕ sin (4βτ) − sin ϕ (1 − cos (4βτ))) dτ + α2 − 4β2 cos ϕ = 0. β τ1 198 La Duc Viet, Nguyen Trong Kien The integrals (12), (13) and (14) now are used in Eqs. (19) to gives 4h πζh − (ζh − ζl) τm − (ζh − ζl) cos τp sin τm cos φ π 2β2 + 1 π (20) + 4 (ζ − ζ ) sin τ sin τ + α2 − 4β2 h sin φ − = 0, h l p m β 4 β −4 πζh − (ζh − ζl) τm + (ζh − ζl) cos τp sin τm sin φ π (21) − 4 (ζ − ζ ) sin τ sin τ − α2 − 4β2 cos φ = 0. h l p m β Totally we have 3 equations (18), (20) and (21) for 3 unknowns ϕ, h and θ0. Moreover, h and θ0 are absent in Eq. (21) while θ0 is absent in Eq. (20), that the equations can be solved sequentially. The following steps are taken: - Step 1: Solve (21) to obtain ϕ; - Step 2: Substitute ϕ to (20), then solve the obtained equation to find h; - Step 3: Substitute ϕ (found in step 1) and h (found in step 2) to (18) to have the 2 cubic equation of θ0 depending on two parameters τp and τm; - Step 4: Apply the minimization condition to solve τP as the function of θ0 and τm. After some manipulations shown in the Appendix, the final relation between θ0 and τm has following form 6 4 2 a3 (τm, θ0) θ0 + a2 (τm, θ0) θ0 + a1θ0 + a0 = 0, (22) where 2 π2 π 4 2 2 − 2 + 2 + 2 + − 2 − 2 1 1 π α 4β β2 16 ζ1 ζ2 8ζ2 4ζ1 cos τp sin τp α 4β β a = β2 + × , 3 2 2 4 2 β ( 2 − 2)2 π2 + 2 − 2 α 4β β2 16 ζ1 ζ2 (23) 2 2 2 2 2 π 2 2β + 1 π 8βζsζ1 − 1 − β α − 4β β + 4ζ2 1 − β sin τp + 2ζsβ cos τp a2 = × , 4β ( 2 − 2)2 π2 + 2 − 2 α 4β β2 16 ζ1 ζ2 (24) 2 2 22 a1 = 4β ζs + 1 − β , (25) 2 2 a0 = −4ζs θm, (26) ζ1 (τm) = πζh − (ζh − ζl) τm; ζ2 (τm) = (ζh − ζl) sin τm, (27) 2 2 2 (α2−4β2)π2(2β2+1) θ2 − 2 2 − 2 π + 2 − 2 − 0 1 β α 4β β2 16 ζ1 ζ2 8β2 tan τ = . (28) p 2 2 ζ (2β2+1) πθ2 ( 2 − 2)2 π + 2 − 2 + 1 0 2β ζs α 4β β2 16 ζ1 ζ2 4β2 In brief, for a given (normalized) frequency β, the relation (22) gives a curve in the plane of θ0 and τm. The lowest θ0 of the curve is the lower bound solution for the given frequency. Figs.2 and3 show some typical curves in the plane of θ0 and τm for some values of β. Other parameters are given as α = 2, ζs = 1%, θm = π/6. The parameter α is taken of 2, which is near the optimal value of frequency ratio [2,3]. The on-off dampings ζh, ζl are changed to see their effects. It is noted that two end values of τm correspond to Lower bound of performance index of anti-sway control of a pendulum using on-off damping radial spring-damper 199 the passive damping cases. When τm = 0, from (9) we have the passive high damping. Conversely, τ = π implies the passive lowFigure damping 2: Typical relati case.on curves (dashed) between q0 and tm and orbit (solid) of minimum m points for zh=20%, zl=5%, a=2, qm=p/6, zs=1% Figure 2: Typical relation curves (dashed) between q0 and tm and orbit (solid) ofFigure minimum 3: Typical relation curves (dashed) between q0 and tm and orbit (solid) of minimum Fig. 2points. Typical for zh=20%, relation zl=5%, a=2, curves qm=p/6, zs=1% (dashed) be- Fig. 3points. Typical for zh=100%, relation zl=1%, a=2, curves qm=p/6, zs (dashed)=1% be- tween θ0 and τm and orbit (solid) of minimumThe followingtween observationsθ0 and of q0 andτm tmand can be orbit drawn (solid)from the Figs. of minimum2 and 3: points for ζh = 20%, ζl = 5%, α = 2, θm = π/6, points for ζh = 100%, ζl = 1%, α = 2, θm = π/6, ζs = 1% ζs = 1% The following observations of θ0 and τm can be drawn from the Figs.2 and3: - The lower bound of sway angle amplitude θ0 increases when the excitation fre- quency ratio β is near 1. The behavior is clear because the resonance frequency ratio is 1. Compare the orbits of minimum points between two Figs.2 and3, we see that the larger ζh and the smaller ζl give a lower value of lower bound. - The optimal value of τm increases when the excitation frequency ratio β is near 1. Observe the on-off damping law (9), we see that increasing τm means the low damping is used longer. The optimal behavior means that when the frequency ratio β is near 1, the damping should be tuned longer to lower value to increase the radial motion to dissipate more energy. The outside region of β requires the larger damping used more frequently Figure 3: Typical relation curves (dashed) between q0 and tm and orbit (solid) of minimum to avoidpoints for the zh=100%, resonance zl=1%, a=2, motion qm=p/6, zs=1% (see the curves corresponding to β = 0.96 and β = 1.04 in The followingboth observations Figs. of2 q and0 and t3m ).can be drawn from the Figs. 2 and 3: 4. CONCLUSIONS This paper considers the anti sway control of a single pendulum by an on-off damp- ing radial spring-damper. For the single harmonic planar vibration, the theoretical so- lution of the lower bound of sway amplitude is derived. The lower bound is smaller with the larger on-damping and the smaller off-damping. The lower bound shows that when the forced frequency ratio is near 1, the damping should be tuned longer to lower value to increase the radial motion to dissipate more energy. The outside region of forced frequency ratio requires the larger damping used more frequently. 200 La Duc Viet, Nguyen Trong Kien ACKNOWLEDGMENT This research is funded by Vietnam National Foundation for Science and Technology Development (NAFOSTED) under grant number 107.01-2015.35. REFERENCES [1] W. Singhose. Command shaping for flexible systems: A review of the first 50 years. In- ternational Journal of Precision Engineering and Manufacturing, 10, (4), (2009), pp. 153–168. https://doi.org/10.1007/s12541-009-0084-2. [2] L. D. Viet. Crane sway reduction using Coriolis force produced by radial spring and damper. Journal of Mechanical Science and Technology, 29, (2015), pp. 973–979. https://doi.org/10.1007/s12206-015-0211-1. [3] L. D. Viet. Partial stochastic linearization of a spherical pendulum with Coriolis damping produced by radial spring and damper. Journal of Vibration and Acoustics, 137, (5), (2015), p. 054504. https://doi.org/10.1115/1.4030663. [4] L. D. Viet and N. B. Nghi. Approximated analytical frequency response of a pendulum struc- ture attached with two orthogonal dynamic vibration absorbers. Vietnam Journal of Mechanics, 37, (4), (2015), pp. 275–284. https://doi.org/10.15625/0866-7136/37/4/5920. [5] S. K. Yalla, A. Kareem, and J. C. Kantor. Semi-active tuned liquid column dampers for vibration control of structures. Engineering Structures, 23, (11), (2001), pp. 1469–1479. https://doi.org/10.1016/s0141-0296(01)00047-5. [6] F. Casciati, G. Magonette, and F. Marazzi. Technology of semiactive devices and applications in vibration mitigation. John Wiley & Sons, (2006). [7] S. M. Savaresi, C. Poussot-Vassal, C. Spelta, O. Sename, and L. Dugard. Semi-active suspension control design for vehicles. Butterworth-Heinemann, UK, (2010). [8] H. E. Tseng and D. Hrovat. State of the art survey: active and semi-active suspension control. Vehicle System Dynamics, 53, (7), (2015), pp. 1034–1062. https://doi.org/10.1080/00423114.2015.1037313. [9] F. Casciati, J. Rodellar, and U. Yildirim. Active and semi-active control of structures: A review of recent advances. In Proceedings of the 8th International Conference on Structural Dynamics, EURODYN, Leuven, Belgium, (2011). pp. 62–69. [10] V. D. La and C. Adam. General on-off damping controller for semi-active tuned liq- uid column damper. Journal of Vibration and Control, 24, (23), (2018), pp. 5487–5501. https://doi.org/10.1177/1077546316648080. [11] J. N. Potter, S. A. Neild, and D. J. Wagg. Generalisation and optimisation of semi-active, on– off switching controllers for single degree-of-freedom systems. Journal of Sound and Vibration, 329, (13), (2010), pp. 2450–2462. https://doi.org/10.1016/j.jsv.2009.12.011. Lower bound of performance index of anti-sway control of a pendulum using on-off damping radial spring-damper 201 APPENDIX This appendix derives the relation (22) between θ0 and τm. Solving (21) gives 2 2 π α − 4β β − 4ζ2 sin τp sin φ = ± , r ( 2 − 2)2 π2 + 2 + 2 + − ( 2 − 2) π α 4β β2 16 ζ1 ζ2 8ζ2 4ζ1 cos τp sin τp α 4β β 4 ζ1 + ζ2 cos τp cos φ = ± , r ( 2 − 2)2 π2 + 2 + 2 + − ( 2 − 2) π α 4β β2 16 ζ1 ζ2 8ζ2 4ζ1 cos τp sin τp α 4β β (29) where ζ1 and ζ2 are defined in (27). The sign of sinϕ and cosϕ must be chosen to satisfy the condition h > 0 in (8). Substituting (29) into (20) gives 2 π2 2 − 2 + 2 − 2 2 16 ζ1 ζ2 α 4β β2 2β + 1 π ±h = . r 4 β ( 2 − 2)2 π2 + 2 + 2 + − ( 2 − 2) π α 4β β2 16 ζ1 ζ2 8ζ2 4ζ1 cos τp sin τp α 4β β (30) It is not difficult to check that ζ1 > ζ2 when τm satisfies the condition (11). Therefore, to guarantee the condition h > 0, the plus sign is used in (29) and (30). Substituting ϕ from (29) and h from (30) to (18), we obtain the equation (22) where the coefficients ai (i = 0, . . . , 3) are defined in (23)–(26). To eliminate the parameter τP, we use the minimization condition. Taking the derivative of Eq. (22) with respect to τP gives ∂a3 6 5 ∂θ0 ∂a2 4 3 ∂θ0 ∂θ0 θ0 + 6a3θ0 + θ0 + 4a2θ0 + 2a1θ0 = 0. (31) ∂τP ∂τP ∂τP ∂τP ∂τP ∂θ The minimization condition 0 = 0 applying to (31) gives ∂τP ∂a3 2 ∂a2 θ0 + = 0. (32) ∂τP ∂τP Using the forms of a2 and a3 in (23) reduces (24) to a trigonometric equation, which can be solved for τP. The root obtained is shown in (28).
File đính kèm:
lower_bound_of_performance_index_of_anti_sway_control_of_a_p.pdf