High flame retardant performance of SiO2-TiO2 sol coated on polyester/cotton fabrics
Abstract: SiO2 and TiO2 sols were successfully synthesized by using sodium silicate and titanium
chloride as Si and Ti sources. SiO2-TiO2 sol coated polyester/cotton fabric was fabricated by deepcoating method and using SiO2, TiO2 sols as coating materials. SiO2-TiO2 coated fabric were
characterized by XRD, FTIR, TGA, SEM and EDX. From SEM image, it showed the SiO2, TiO2
particles of 20-30 nm which well deposited on fabric surface. TGA result revealed the significant
improvement of thermal resistance and stability of SiO2-TiO2 coated fabric as compared to those
of uncoated fabric. Flame retardant performance of SiO2-TiO2 coated fabrics was much better than
that of uncoated fabric. Thus, SiO2-TiO2 coated fabric SiO2-TiO2 content of 26wt% showed the
UL-94 classification of V-0 and LOI value of 30.3 were obtained. Moreover, mechanical property
(tear strength) of SiO2-TiO2 coated fabrics were also improved.
Keywords: nano silica, titanium dioxide, polyester/cotton fabrics, flame retardant
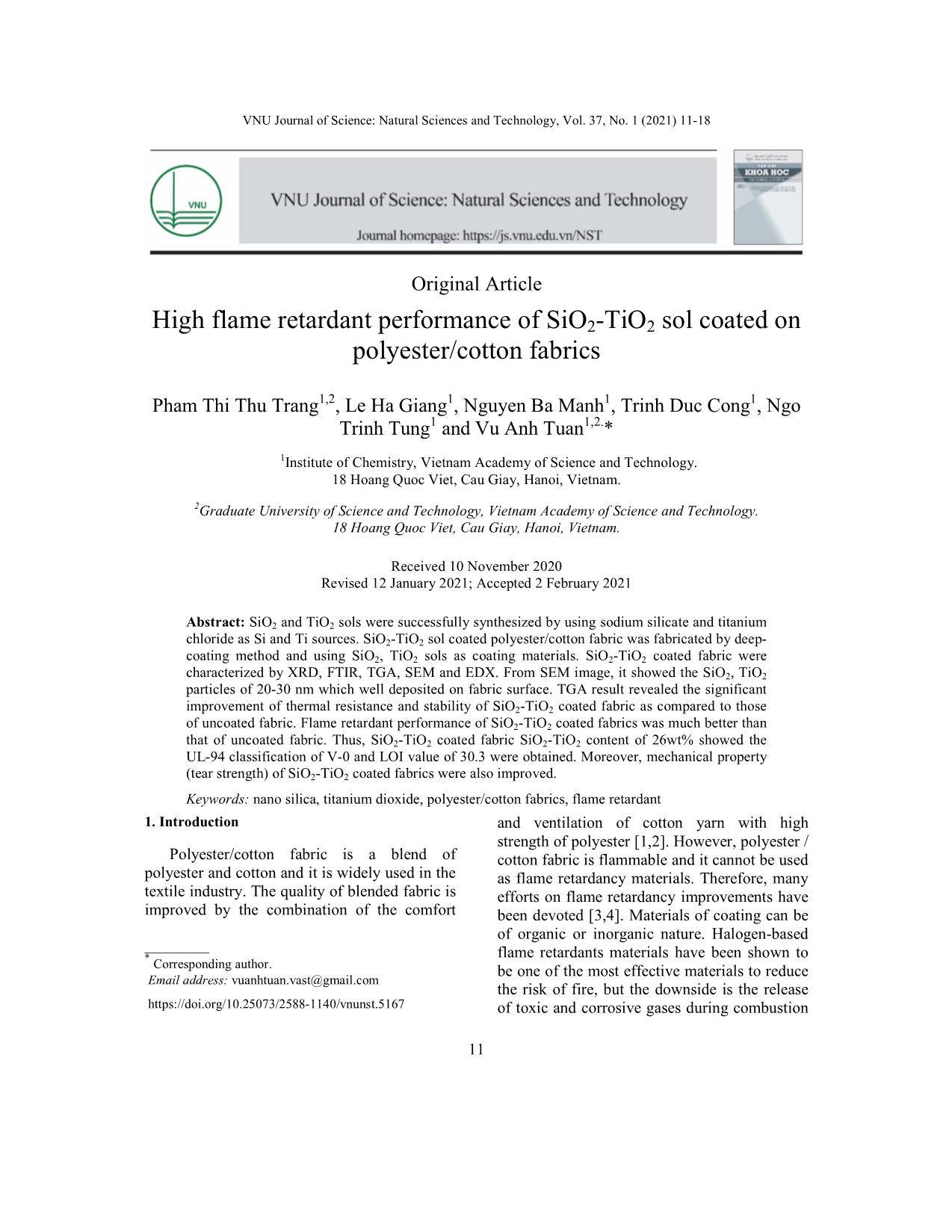
Trang 1
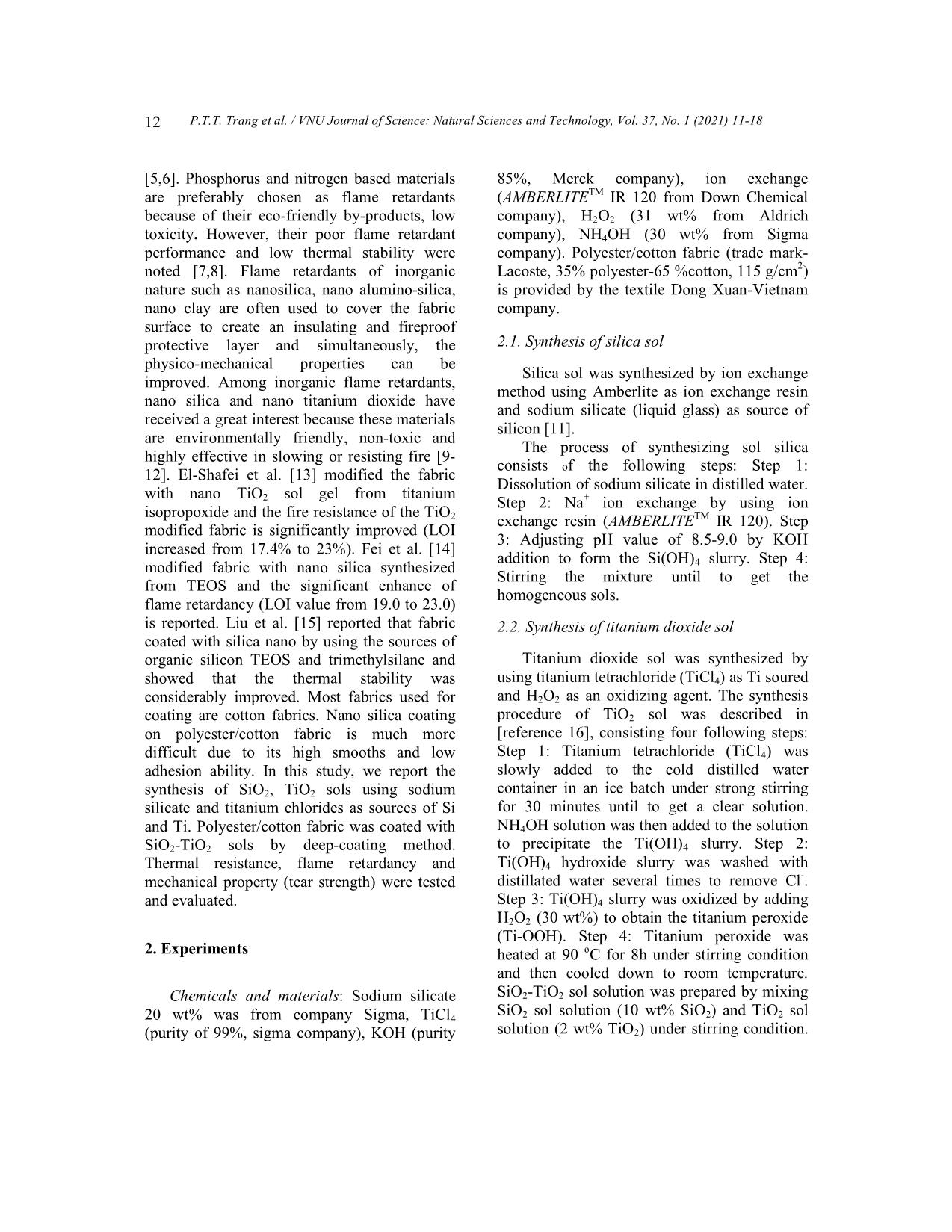
Trang 2
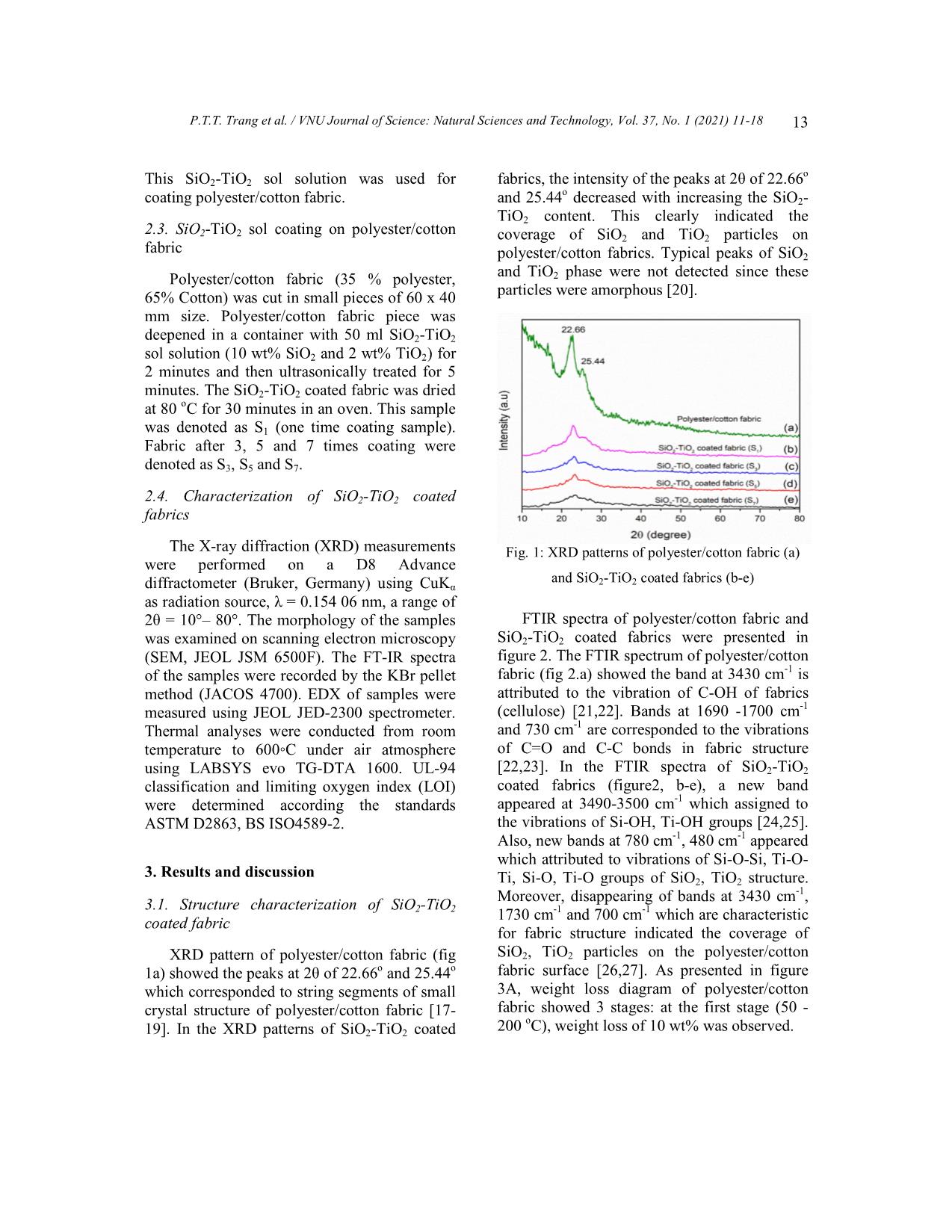
Trang 3
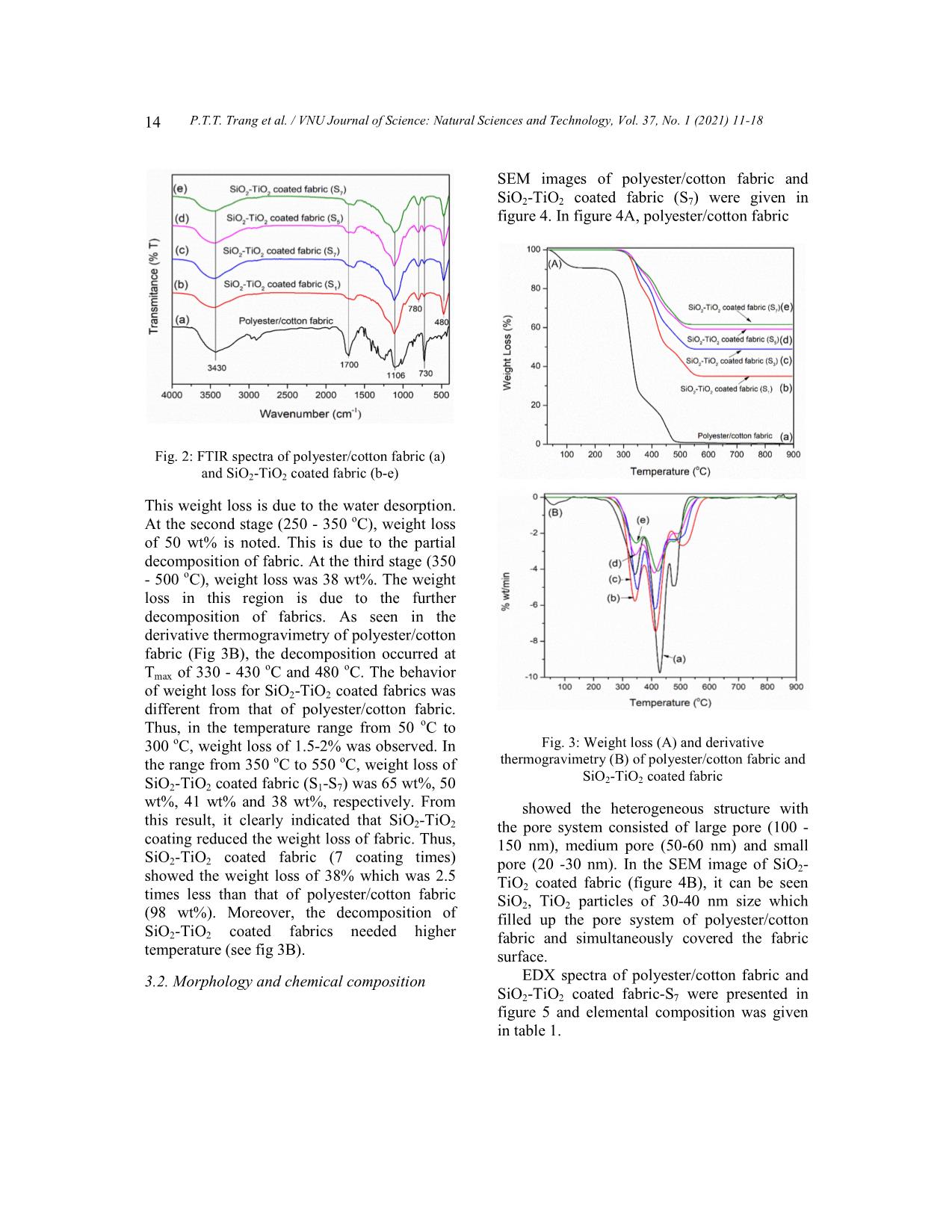
Trang 4
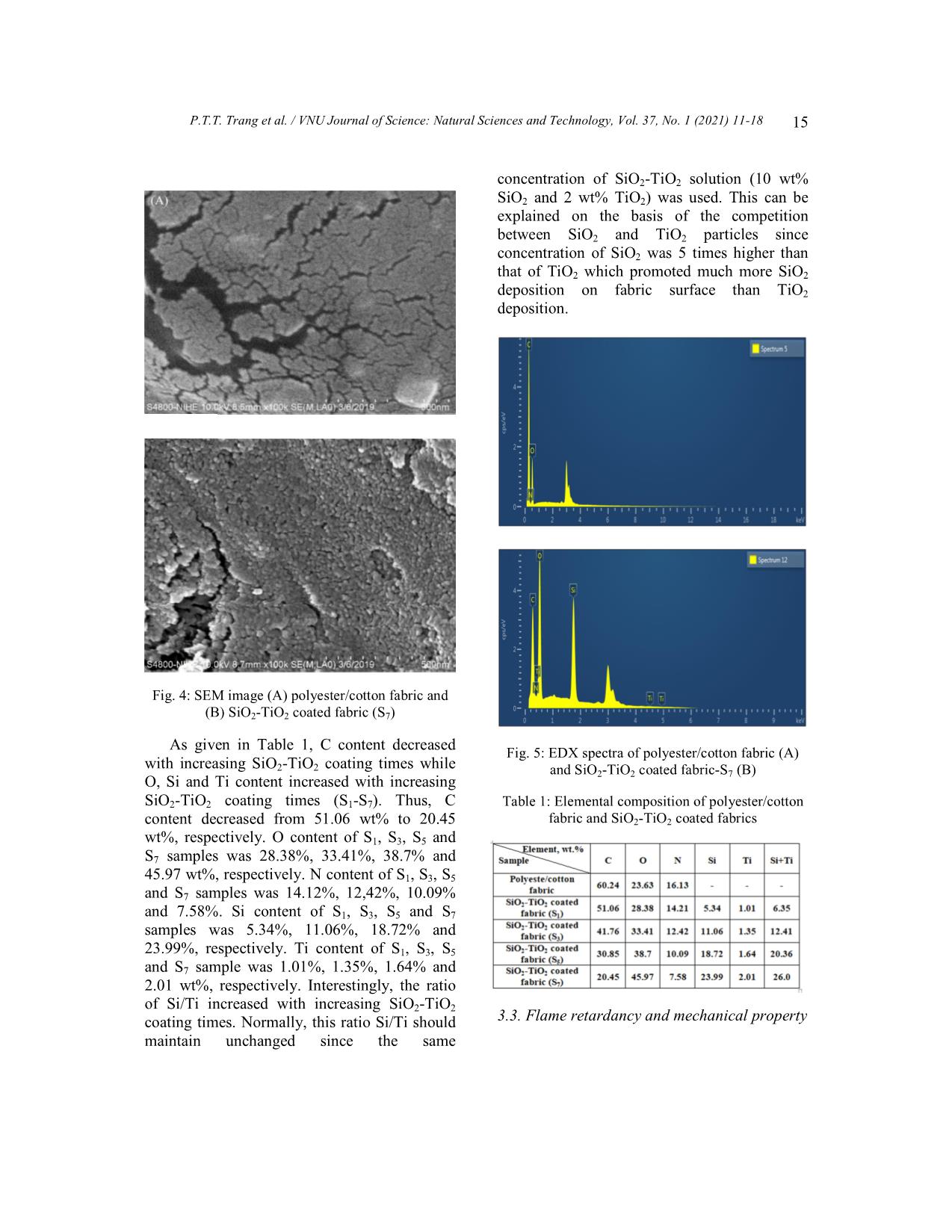
Trang 5
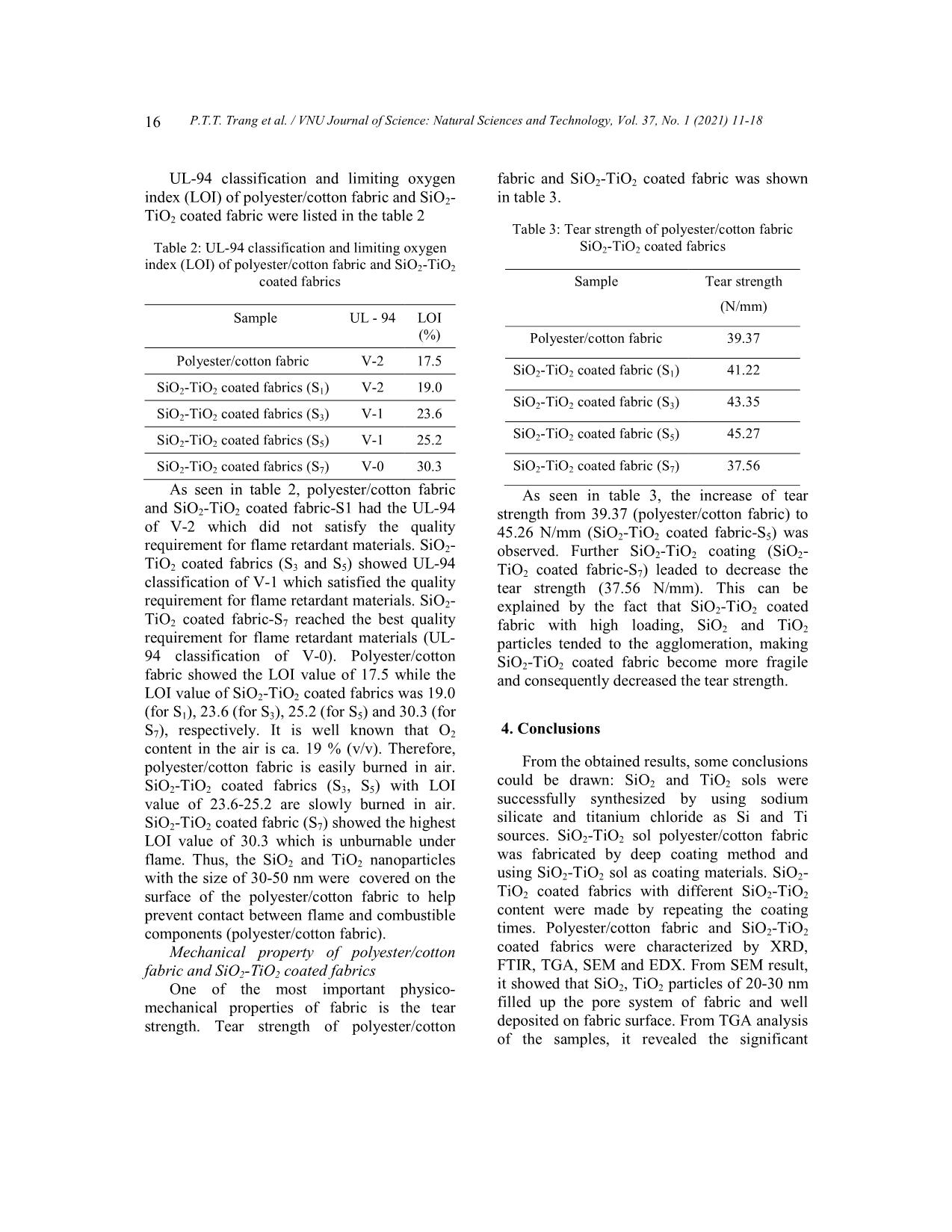
Trang 6
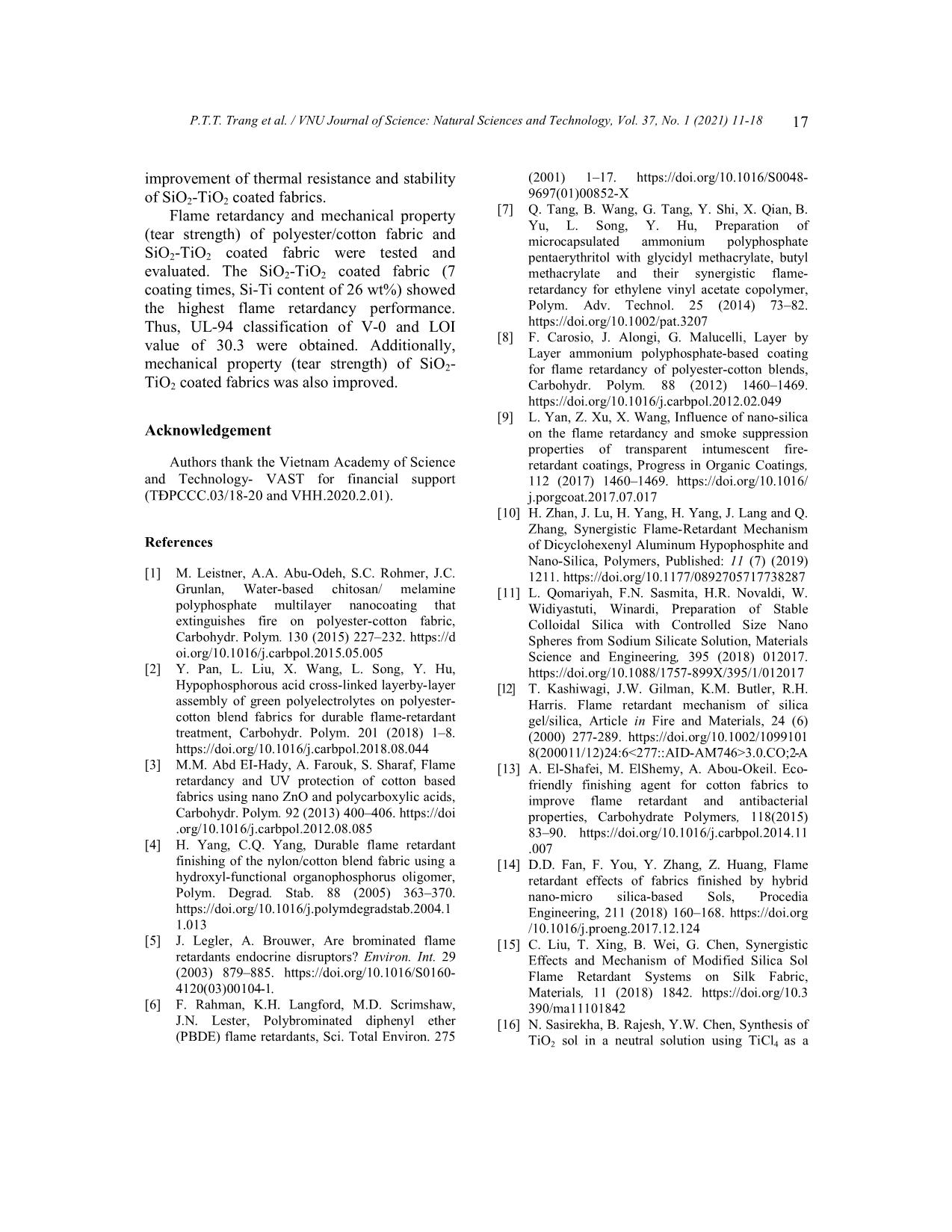
Trang 7
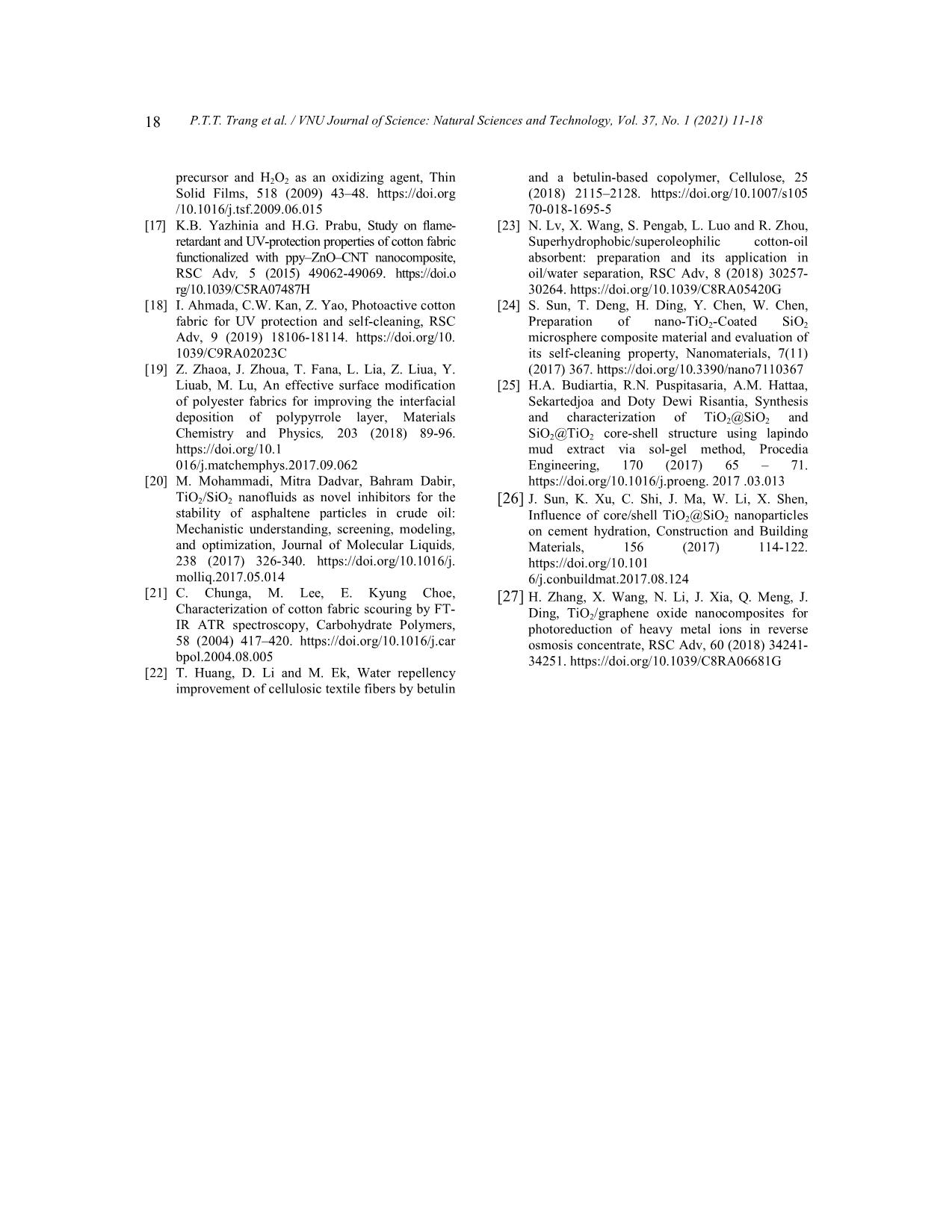
Trang 8
Tóm tắt nội dung tài liệu: High flame retardant performance of SiO2-TiO2 sol coated on polyester/cotton fabrics
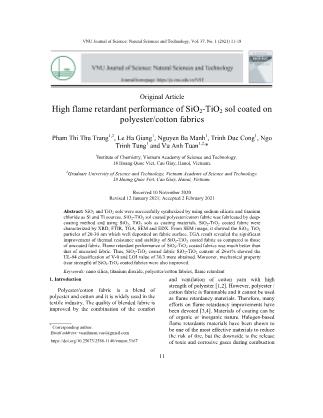
VNU Journal of Science: Natural Sciences and Technology, Vol. 37, No. 1 (2021) 11-18 Original Article High flame retardant performance of SiO2-TiO2 sol coated on polyester/cotton fabrics Pham Thi Thu Trang1,2, Le Ha Giang1, Nguyen Ba Manh1, Trinh Duc Cong1, Ngo Trinh Tung1 and Vu Anh Tuan1,2.* 1Institute of Chemistry, Vietnam Academy of Science and Technology. 18 Hoang Quoc Viet, Cau Giay, Hanoi, Vietnam. 2Graduate University of Science and Technology, Vietnam Academy of Science and Technology. 18 Hoang Quoc Viet, Cau Giay, Hanoi, Vietnam. Received 10 November 2020 Revised 12 January 2021; Accepted 2 February 2021 Abstract: SiO2 and TiO2 sols were successfully synthesized by using sodium silicate and titanium chloride as Si and Ti sources. SiO2-TiO2 sol coated polyester/cotton fabric was fabricated by deep- coating method and using SiO2, TiO2 sols as coating materials. SiO2-TiO2 coated fabric were characterized by XRD, FTIR, TGA, SEM and EDX. From SEM image, it showed the SiO2, TiO2 particles of 20-30 nm which well deposited on fabric surface. TGA result revealed the significant improvement of thermal resistance and stability of SiO2-TiO2 coated fabric as compared to those of uncoated fabric. Flame retardant performance of SiO2-TiO2 coated fabrics was much better than that of uncoated fabric. Thus, SiO2-TiO2 coated fabric SiO2-TiO2 content of 26wt% showed the UL-94 classification of V-0 and LOI value of 30.3 were obtained. Moreover, mechanical property (tear strength) of SiO2-TiO2 coated fabrics were also improved. Keywords: nano silica, titanium dioxide, polyester/cotton fabrics, flame retardant 1. Introduction* and ventilation of cotton yarn with high strength of polyester [1,2]. However, polyester / Polyester/cotton fabric is a blend of cotton fabric is flammable and it cannot be used polyester and cotton and it is widely used in the as flame retardancy materials. Therefore, many textile industry. The quality of blended fabric is efforts on flame retardancy improvements have improved by the combination of the comfort been devoted [3,4]. Materials of coating can be of organic or inorganic nature. Halogen-based ________ * flame retardants materials have been shown to Corresponding author. be one of the most effective materials to reduce Email address: vuanhtuan.vast@gmail.com the risk of fire, but the downside is the release https://doi.org/10.25073/2588-1140/vnunst.5167 of toxic and corrosive gases during combustion 11 12 P.T.T. Trang et al. / VNU Journal of Science: Natural Sciences and Technology, Vol. 37, No. 1 (2021) 11-18 [5,6]. Phosphorus and nitrogen based materials 85%, Merck company), ion exchange are preferably chosen as flame retardants (AMBERLITETM IR 120 from Down Chemical because of their eco-friendly by-products, low company), H2O2 (31 wt% from Aldrich toxicity. However, their poor flame retardant company), NH4OH (30 wt% from Sigma performance and low thermal stability were company). Polyester/cotton fabric (trade mark- noted [7,8]. Flame retardants of inorganic Lacoste, 35% polyester-65 %cotton, 115 g/cm2) nature such as nanosilica, nano alumino-silica, is provided by the textile Dong Xuan-Vietnam nano clay are often used to cover the fabric company. surface to create an insulating and fireproof protective layer and simultaneously, the 2.1. Synthesis of silica sol physico-mechanical properties can be Silica sol was synthesized by ion exchange improved. Among inorganic flame retardants, method using Amberlite as ion exchange resin nano silica and nano titanium dioxide have and sodium silicate (liquid glass) as source of received a great interest because these materials silicon [11]. are environmentally friendly, non-toxic and The process of synthesizing sol silica highly effective in slowing or resisting fire [9- consists of the following steps: Step 1: 12]. El-Shafei et al. [13] modified the fabric Dissolution of sodium silicate in distilled water. with nano TiO sol gel from titanium 2 Step 2: Na+ ion exchange by using ion isopropoxide and the fire resistance of the TiO 2 exchange resin (AMBERLITETM IR 120). Step modified fabric is significantly improved (LOI 3: Adjusting pH value of 8.5-9.0 by KOH increased from 17.4% to 23%). Fei et al. [14] addition to form the Si(OH) slurry. Step 4: modified fabric with nano silica synthesized 4 Stirring the mixture until to get the from TEOS and the significant enhance of homogeneous sols. flame retardancy (LOI value from 19.0 to 23.0) is reported. Liu et al. [15] reported that fabric 2.2. Synthesis of titanium dioxide sol coated with silica nano by using the sources of organic silicon TEOS and trimethylsilane and Titanium dioxide sol was synthesized by showed that the thermal stability was using titanium tetrachloride (TiCl4) as Ti soured considerably imp ... 0 - o 19]. In the XRD patterns of SiO2-TiO2 coated 200 C), weight loss of 10 wt% was observed. 14 P.T.T. Trang et al. / VNU Journal of Science: Natural Sciences and Technology, Vol. 37, No. 1 (2021) 11-18 SEM images of polyester/cotton fabric and SiO2-TiO2 coated fabric (S7) were given in figure 4. In figure 4A, polyester/cotton fabric Fig. 2: FTIR spectra of polyester/cotton fabric (a) and SiO2-TiO2 coated fabric (b-e) This weight loss is due to the water desorption. At the second stage (250 - 350 oC), weight loss of 50 wt% is noted. This is due to the partial decomposition of fabric. At the third stage (350 - 500 oC), weight loss was 38 wt%. The weight loss in this region is due to the further decomposition of fabrics. As seen in the derivative thermogravimetry of polyester/cotton fabric (Fig 3B), the decomposition occurred at o o Tmax of 330 - 430 C and 480 C. The behavior of weight loss for SiO2-TiO2 coated fabrics was different from that of polyester/cotton fabric. Thus, in the temperature range from 50 oC to 300 oC, weight loss of 1.5-2% was observed. In Fig. 3: Weight loss (A) and derivative the range from 350 oC to 550 oC, weight loss of thermogravimetry (B) of polyester/cotton fabric and SiO2-TiO2 coated fabric SiO2-TiO2 coated fabric (S1-S7) was 65 wt%, 50 wt%, 41 wt% and 38 wt%, respectively. From showed the heterogeneous structure with this result, it clearly indicated that SiO2-TiO2 the pore system consisted of large pore (100 - coating reduced the weight loss of fabric. Thus, 150 nm), medium pore (50-60 nm) and small SiO2-TiO2 coated fabric (7 coating times) pore (20 -30 nm). In the SEM image of SiO2- showed the weight loss of 38% which was 2.5 TiO coated fabric (figure 4B), it can be seen times less than that of polyester/cotton fabric 2 SiO2, TiO2 particles of 30-40 nm size which (98 wt%). Moreover, the decomposition of filled up the pore system of polyester/cotton SiO2-TiO2 coated fabrics needed higher fabric and simultaneously covered the fabric temperature (see fig 3B). surface. 3.2. Morphology and chemical composition EDX spectra of polyester/cotton fabric and SiO2-TiO2 coated fabric-S7 were presented in figure 5 and elemental composition was given in table 1. P.T.T. Trang et al. / VNU Journal of Science: Natural Sciences and Technology, Vol. 37, No. 1 (2021) 11-18 15 concentration of SiO2-TiO2 solution (10 wt% SiO2 and 2 wt% TiO2) was used. This can be explained on the basis of the competition between SiO2 and TiO2 particles since concentration of SiO2 was 5 times higher than that of TiO2 which promoted much more SiO2 deposition on fabric surface than TiO2 deposition. (B) Fig. 4: SEM image (A) polyester/cotton fabric and (B) SiO2-TiO2 coated fabric (S7) As given in Table 1, C content decreased Fig. 5: EDX spectra of polyester/cotton fabric (A) with increasing SiO2-TiO2 coating times while and SiO -TiO coated fabric-S (B) O, Si and Ti content increased with increasing 2 2 7 SiO2-TiO2 coating times (S1-S7). Thus, C Table 1: Elemental composition of polyester/cotton content decreased from 51.06 wt% to 20.45 fabric and SiO2-TiO2 coated fabrics wt%, respectively. O content of S1, S3, S5 and S7 samples was 28.38%, 33.41%, 38.7% and 45.97 wt%, respectively. N content of S1, S3, S5 and S7 samples was 14.12%, 12,42%, 10.09% and 7.58%. Si content of S1, S3, S5 and S7 samples was 5.34%, 11.06%, 18.72% and 23.99%, respectively. Ti content of S1, S3, S5 and S7 sample was 1.01%, 1.35%, 1.64% and 2.01 wt%, respectively. Interestingly, the ratio of Si/Ti increased with increasing SiO2-TiO2 coating times. Normally, this ratio Si/Ti should 3.3. Flame retardancy and mechanical property maintain unchanged since the same 16 P.T.T. Trang et al. / VNU Journal of Science: Natural Sciences and Technology, Vol. 37, No. 1 (2021) 11-18 UL-94 classification and limiting oxygen fabric and SiO2-TiO2 coated fabric was shown index (LOI) of polyester/cotton fabric and SiO2- in table 3. TiO2 coated fabric were listed in the table 2 Table 3: Tear strength of polyester/cotton fabric Table 2: UL-94 classification and limiting oxygen SiO2-TiO2 coated fabrics index (LOI) of polyester/cotton fabric and SiO2-TiO2 coated fabrics Sample Tear strength (N/mm) Sample UL - 94 LOI (%) Polyester/cotton fabric 39.37 Polyester/cotton fabric V-2 17.5 SiO2-TiO2 coated fabric (S1) 41.22 SiO2-TiO2 coated fabrics (S1) V-2 19.0 SiO2-TiO2 coated fabric (S3) 43.35 SiO2-TiO2 coated fabrics (S3) V-1 23.6 SiO2-TiO2 coated fabric (S5) 45.27 SiO2-TiO2 coated fabrics (S5) V-1 25.2 SiO2-TiO2 coated fabrics (S7) V-0 30.3 SiO2-TiO2 coated fabric (S7) 37.56 As seen in table 2, polyester/cotton fabric As seen in table 3, the increase of tear and SiO2-TiO2 coated fabric-S1 had the UL-94 strength from 39.37 (polyester/cotton fabric) to of V-2 which did not satisfy the quality 45.26 N/mm (SiO2-TiO2 coated fabric-S5) was requirement for flame retardant materials. SiO2- observed. Further SiO2-TiO2 coating (SiO2- TiO2 coated fabrics (S3 and S5) showed UL-94 TiO2 coated fabric-S7) leaded to decrease the classification of V-1 which satisfied the quality tear strength (37.56 N/mm). This can be requirement for flame retardant materials. SiO2- explained by the fact that SiO2-TiO2 coated TiO2 coated fabric-S7 reached the best quality fabric with high loading, SiO2 and TiO2 requirement for flame retardant materials (UL- particles tended to the agglomeration, making 94 classification of V-0). Polyester/cotton SiO2-TiO2 coated fabric become more fragile fabric showed the LOI value of 17.5 while the and consequently decreased the tear strength. LOI value of SiO2-TiO2 coated fabrics was 19.0 (for S1), 23.6 (for S3), 25.2 (for S5) and 30.3 (for S7), respectively. It is well known that O2 4. Conclusions content in the air is ca. 19 % (v/v). Therefore, polyester/cotton fabric is easily burned in air. From the obtained results, some conclusions could be drawn: SiO2 and TiO2 sols were SiO2-TiO2 coated fabrics (S3, S5) with LOI value of 23.6-25.2 are slowly burned in air. successfully synthesized by using sodium silicate and titanium chloride as Si and Ti SiO2-TiO2 coated fabric (S7) showed the highest LOI value of 30.3 which is unburnable under sources. SiO2-TiO2 sol polyester/cotton fabric was fabricated by deep coating method and flame. Thus, the SiO2 and TiO2 nanoparticles with the size of 30-50 nm were covered on the using SiO2-TiO2 sol as coating materials. SiO2- surface of the polyester/cotton fabric to help TiO2 coated fabrics with different SiO2-TiO2 prevent contact between flame and combustible content were made by repeating the coating components (polyester/cotton fabric). times. Polyester/cotton fabric and SiO2-TiO2 Mechanical property of polyester/cotton coated fabrics were characterized by XRD, FTIR, TGA, SEM and EDX. From SEM result, fabric and SiO2-TiO2 coated fabrics One of the most important physico- it showed that SiO2, TiO2 particles of 20-30 nm mechanical properties of fabric is the tear filled up the pore system of fabric and well strength. Tear strength of polyester/cotton deposited on fabric surface. From TGA analysis of the samples, it revealed the significant P.T.T. Trang et al. / VNU Journal of Science: Natural Sciences and Technology, Vol. 37, No. 1 (2021) 11-18 17 improvement of thermal resistance and stability (2001) 1–17. https://doi.org/10.1016/S0048- 9697(01)00852-X of SiO2-TiO2 coated fabrics. Flame retardancy and mechanical property [7] Q. Tang, B. Wang, G. Tang, Y. Shi, X. Qian, B. Yu, L. Song, Y. Hu, Preparation of (tear strength) of polyester/cotton fabric and microcapsulated ammonium polyphosphate SiO2-TiO2 coated fabric were tested and pentaerythritol with glycidyl methacrylate, butyl evaluated. The SiO2-TiO2 coated fabric (7 methacrylate and their synergistic flame- coating times, Si-Ti content of 26 wt%) showed retardancy for ethylene vinyl acetate copolymer, the highest flame retardancy performance. Polym. Adv. Technol. 25 (2014) 73–82. Thus, UL-94 classification of V-0 and LOI https://doi.org/10.1002/pat.3207 [8] F. Carosio, J. Alongi, G. Malucelli, Layer by value of 30.3 were obtained. Additionally, Layer ammonium polyphosphate-based coating mechanical property (tear strength) of SiO2- for flame retardancy of polyester-cotton blends, TiO2 coated fabrics was also improved. Carbohydr. Polym. 88 (2012) 1460–1469. https://doi.org/10.1016/j.carbpol.2012.02.049 [9] L. Yan, Z. Xu, X. Wang, Influence of nano-silica Acknowledgement on the flame retardancy and smoke suppression properties of transparent intumescent fire- Authors thank the Vietnam Academy of Science retardant coatings, Progress in Organic Coatings, and Technology- VAST for financial support 112 (2017) 1460–1469. https://doi.org/10.1016/ (TĐPCCC.03/18-20 and VHH.2020.2.01). j.porgcoat.2017.07.017 [10] H. Zhan, J. Lu, H. Yang, H. Yang, J. Lang and Q. Zhang, Synergistic Flame-Retardant Mechanism References of Dicyclohexenyl Aluminum Hypophosphite and Nano-Silica, Polymers, Published: 11 (7) (2019) [1] M. Leistner, A.A. Abu-Odeh, S.C. Rohmer, J.C. 1211. https://doi.org/10.1177/0892705717738287 Grunlan, Water-based chitosan/ melamine [11] L. Qomariyah, F.N. Sasmita, H.R. Novaldi, W. polyphosphate multilayer nanocoating that Widiyastuti, Winardi, Preparation of Stable extinguishes fire on polyester-cotton fabric, Colloidal Silica with Controlled Size Nano Carbohydr. Polym. 130 (2015) 227–232. https://d Spheres from Sodium Silicate Solution, Materials oi.org/10.1016/j.carbpol.2015.05.005 Science and Engineering, 395 (2018) 012017. [2] Y. Pan, L. Liu, X. Wang, L. Song, Y. Hu, https://doi.org/10.1088/1757-899X/395/1/012017 Hypophosphorous acid cross-linked layerby-layer [12] T. Kashiwagi, J.W. Gilman, K.M. Butler, R.H. assembly of green polyelectrolytes on polyester- Harris. Flame retardant mechanism of silica cotton blend fabrics for durable flame-retardant gel/silica, Article in Fire and Materials, 24 (6) treatment, Carbohydr. Polym. 201 (2018) 1–8. (2000) 277-289. https://doi.org/10.1002/1099101 https://doi.org/10.1016/j.carbpol.2018.08.044 8(200011/12)24:63.0.CO;2-A [3] M.M. Abd EI-Hady, A. Farouk, S. Sharaf, Flame [13] A. El-Shafei, M. ElShemy, A. Abou-Okeil. Eco- retardancy and UV protection of cotton based friendly finishing agent for cotton fabrics to fabrics using nano ZnO and polycarboxylic acids, improve flame retardant and antibacterial Carbohydr. Polym. 92 (2013) 400–406. https://doi properties, Carbohydrate Polymers, 118(2015) .org/10.1016/j.carbpol.2012.08.085 83–90. https://doi.org/10.1016/j.carbpol.2014.11 [4] H. Yang, C.Q. Yang, Durable flame retardant .007 finishing of the nylon/cotton blend fabric using a [14] D.D. Fan, F. You, Y. Zhang, Z. Huang, Flame hydroxyl-functional organophosphorus oligomer, retardant effects of fabrics finished by hybrid Polym. Degrad. Stab. 88 (2005) 363–370. nano-micro silica-based Sols, Procedia https://doi.org/10.1016/j.polymdegradstab.2004.1 Engineering, 211 (2018) 160–168. https://doi.org 1.013 /10.1016/j.proeng.2017.12.124 [5] J. Legler, A. Brouwer, Are brominated flame [15] C. Liu, T. Xing, B. Wei, G. Chen, Synergistic retardants endocrine disruptors? Environ. Int. 29 Effects and Mechanism of Modified Silica Sol (2003) 879–885. https://doi.org/10.1016/S0160- Flame Retardant Systems on Silk Fabric, 4120(03)00104-1. Materials, 11 (2018) 1842. https://doi.org/10.3 [6] F. Rahman, K.H. Langford, M.D. Scrimshaw, 390/ma11101842 J.N. Lester, Polybrominated diphenyl ether [16] N. Sasirekha, B. Rajesh, Y.W. Chen, Synthesis of (PBDE) flame retardants, Sci. Total Environ. 275 TiO2 sol in a neutral solution using TiCl4 as a 18 P.T.T. Trang et al. / VNU Journal of Science: Natural Sciences and Technology, Vol. 37, No. 1 (2021) 11-18 precursor and H2O2 as an oxidizing agent, Thin and a betulin-based copolymer, Cellulose, 25 Solid Films, 518 (2009) 43–48. https://doi.org (2018) 2115–2128. https://doi.org/10.1007/s105 /10.1016/j.tsf.2009.06.015 70-018-1695-5 [17] K.B. Yazhinia and H.G. Prabu, Study on flame- [23] N. Lv, X. Wang, S. Pengab, L. Luo and R. Zhou, retardant and UV-protection properties of cotton fabric Superhydrophobic/superoleophilic cotton-oil functionalized with ppy–ZnO–CNT nanocomposite, absorbent: preparation and its application in RSC Adv, 5 (2015) 49062-49069. https://doi.o oil/water separation, RSC Adv, 8 (2018) 30257- rg/10.1039/C5RA07487H 30264. https://doi.org/10.1039/C8RA05420G [18] I. Ahmada, C.W. Kan, Z. Yao, Photoactive cotton [24] S. Sun, T. Deng, H. Ding, Y. Chen, W. Chen, fabric for UV protection and self-cleaning, RSC Preparation of nano-TiO2-Coated SiO2 Adv, 9 (2019) 18106-18114. https://doi.org/10. microsphere composite material and evaluation of 1039/C9RA02023C its self-cleaning property, Nanomaterials, 7(11) [19] Z. Zhaoa, J. Zhoua, T. Fana, L. Lia, Z. Liua, Y. (2017) 367. https://doi.org/10.3390/nano7110367 Liuab, M. Lu, An effective surface modification [25] H.A. Budiartia, R.N. Puspitasaria, A.M. Hattaa, of polyester fabrics for improving the interfacial Sekartedjoa and Doty Dewi Risantia, Synthesis deposition of polypyrrole layer, Materials and characterization of TiO2@SiO2 and Chemistry and Physics, 203 (2018) 89-96. SiO2@TiO2 core-shell structure using lapindo https://doi.org/10.1 mud extract via sol-gel method, Procedia 016/j.matchemphys.2017.09.062 Engineering, 170 (2017) 65 – 71. [20] M. Mohammadi, Mitra Dadvar, Bahram Dabir, https://doi.org/10.1016/j.proeng. 2017 .03.013 TiO2/SiO2 nanofluids as novel inhibitors for the [26] J. Sun, K. Xu, C. Shi, J. Ma, W. Li, X. Shen, stability of asphaltene particles in crude oil: Influence of core/shell TiO2@SiO2 nanoparticles Mechanistic understanding, screening, modeling, on cement hydration, Construction and Building and optimization, Journal of Molecular Liquids, Materials, 156 (2017) 114-122. 238 (2017) 326-340. https://doi.org/10.1016/j. https://doi.org/10.101 molliq.2017.05.014 6/j.conbuildmat.2017.08.124 [21] C. Chunga, M. Lee, E. Kyung Choe, [27] H. Zhang, X. Wang, N. Li, J. Xia, Q. Meng, J. Characterization of cotton fabric scouring by FT- Ding, TiO2/graphene oxide nanocomposites for IR ATR spectroscopy, Carbohydrate Polymers, photoreduction of heavy metal ions in reverse 58 (2004) 417–420. https://doi.org/10.1016/j.car osmosis concentrate, RSC Adv, 60 (2018) 34241- bpol.2004.08.005 34251. https://doi.org/10.1039/C8RA06681G [22] T. Huang, D. Li and M. Ek, Water repellency improvement of cellulosic textile fibers by betulin
File đính kèm:
high_flame_retardant_performance_of_sio2_tio2_sol_coated_on.pdf