Giáo trình Quản trị sản xuất (Phần 2)
Trong nhiều mục tiêu của bố trí mặt bằng, mục tiêu chính cần quan tâm là tối thiểu hóa chi
phí vận chuyển, chi phí sản xuất và tồn trữ nguyên vật liệu trong hệ thống sản xuất.
Có nhiều loại nguyên vật liệu được dùng trong quá trình sản xuất như: nguyên liệu thô, các
chi tiết mua ngoài, nguyên liệu đóng gói, cung cấp bảo trì sửa chữa, phế liệu và chất thải.
Ngoài ra, còn sự đa dạng về hình dáng, màu sắc, kích thước, đặc tính hóa học. Sự đa dạng và
đặc tính của nguyên vật liệu đã được xác định bởi các quyết định trong thiết kế sản phẩm.
Việc bố trí mặt bằng chịu ảnh hưởng trực tiếp các đặc tính tự nhiên của nguyên liệu, như loại
nguyên liệu to lớn, cồng kềnh, chất lỏng, chất rắn, nguyên liệu linh hoạt hay không linh hoạt
trong điều kiện nóng, lạnh, ẩm ướt, ánh sáng, bụi, lửa, sự chấn động.
Một hệ thống vận chuyển nguyên vật liệu là toàn bộ mạng lưới vận chuyển từ khâu tiếp
nhận nguyên vật liệu, tồn trữ trong kho, vận chuyển chúng giữa các bộ phận sản xuất và cuối
cùng là gửi thành phẩm lên xe để phân phối. Do đó thiết kế và bố trí nhà xưởng phải phù hợp
với thiết kế hệ thống vận chuyển. Ví dụ: nếu muốn sử dụng băng tải trên cao thì nhà xưởng
phải đủ vững chắc hoặc nếu dùng xe nâng hàng thì lối đi phải đủ rộng, mức chịu tải của sàn
nhà thích hợp.
Các nguyên tắc vận chuyển nguyên vật liệu.
− Tối thiểu hóa việc vận chuyển nguyên vật liệu đến bộ phận sản xuất.
− Các qui trình sản xuất liên quan được sắp xếp sao cho thuận lợi dòng cung cấp nguyên
liệu.
− Nên thiết kế và định vị các thiết bị vận chuyển, lựa chọn nơi tồn trữ nguyên liệu sao cho
giảm tối đa sự nổ lực của công nhân: cúi xuống, với tay, đi lại.
− Tối thiểu hóa số lần vận chuyển của từng loại nguyên liệu
− Sự linh hoạt của hệ thống cho phép các tình huống bất thường: thiết bị vận chuyển
nguyên liệu hỏng, thay đổi công nghệ sản xuất, mở rộng năng lực sản xuất.
− Các thiết bị vận chuyển phải sử dụng hết trọng tải của nó
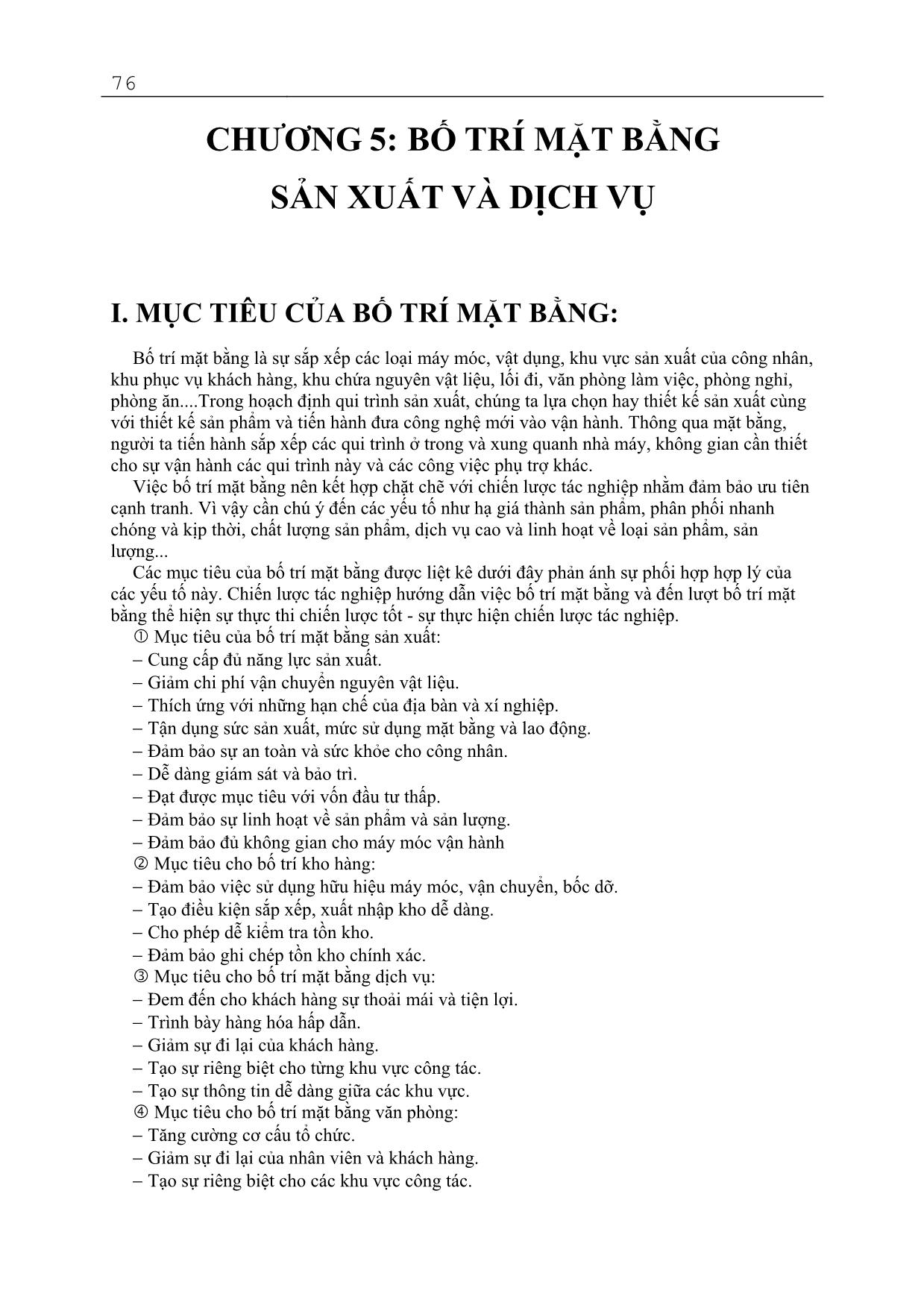
Trang 1
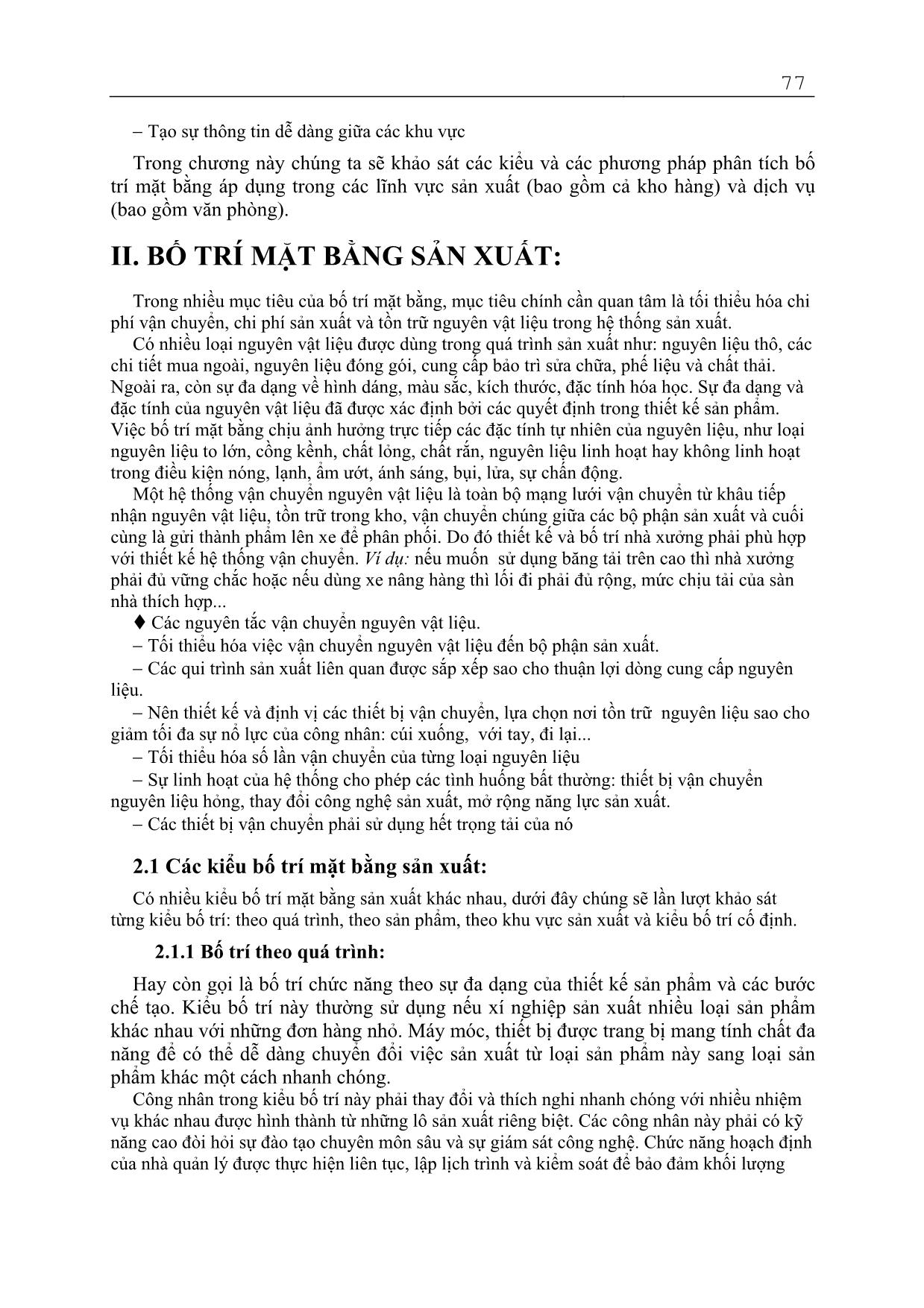
Trang 2
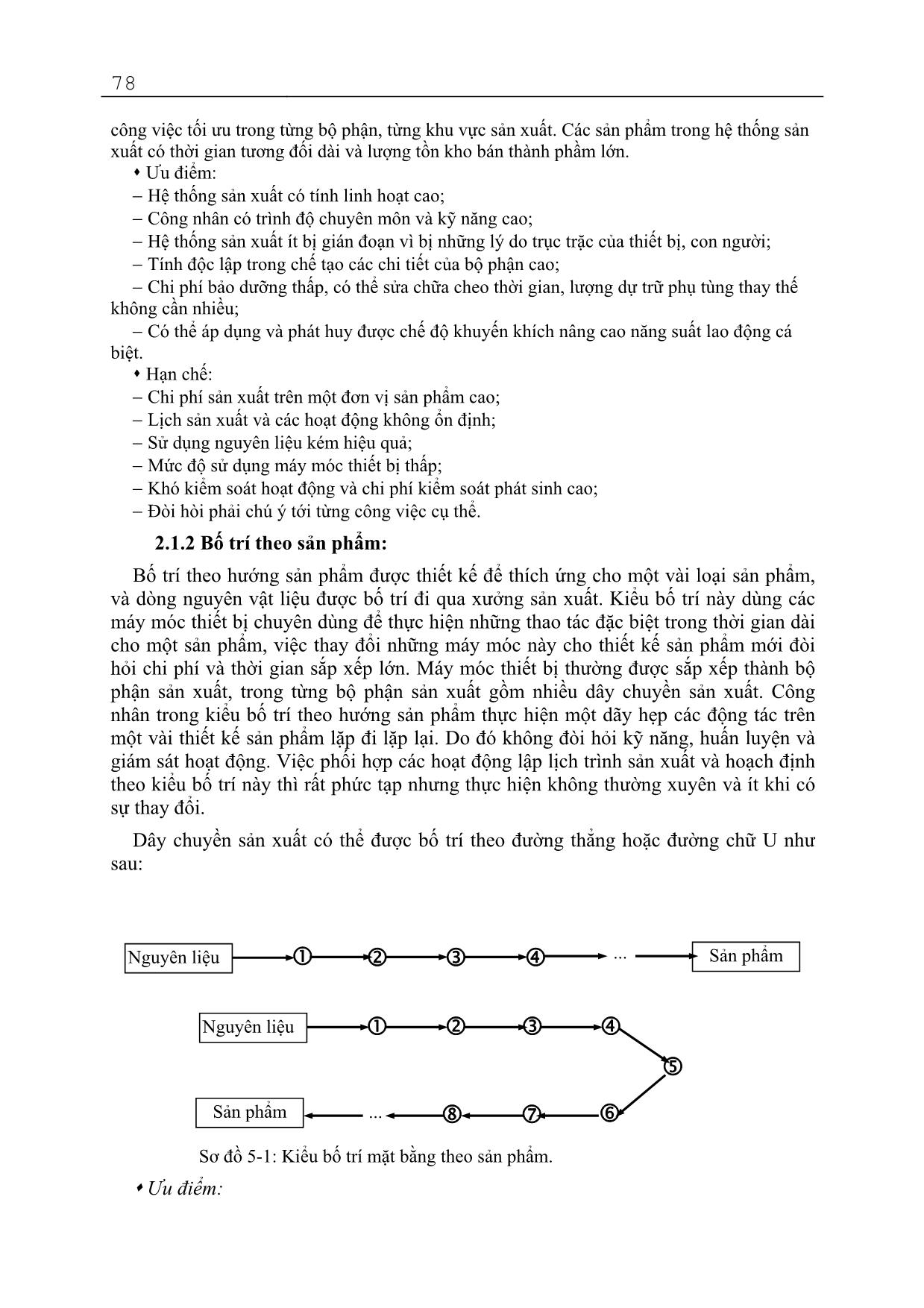
Trang 3
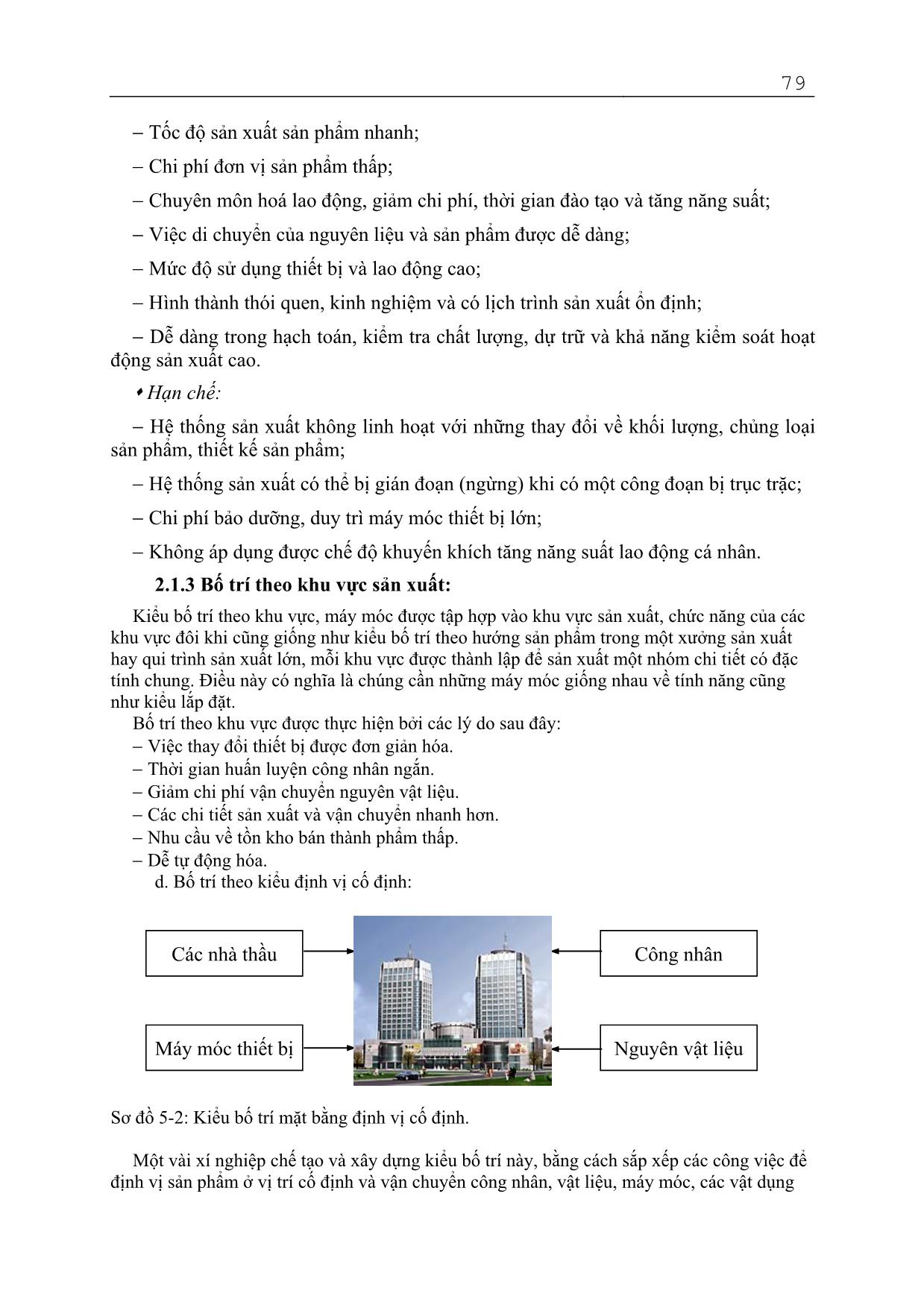
Trang 4
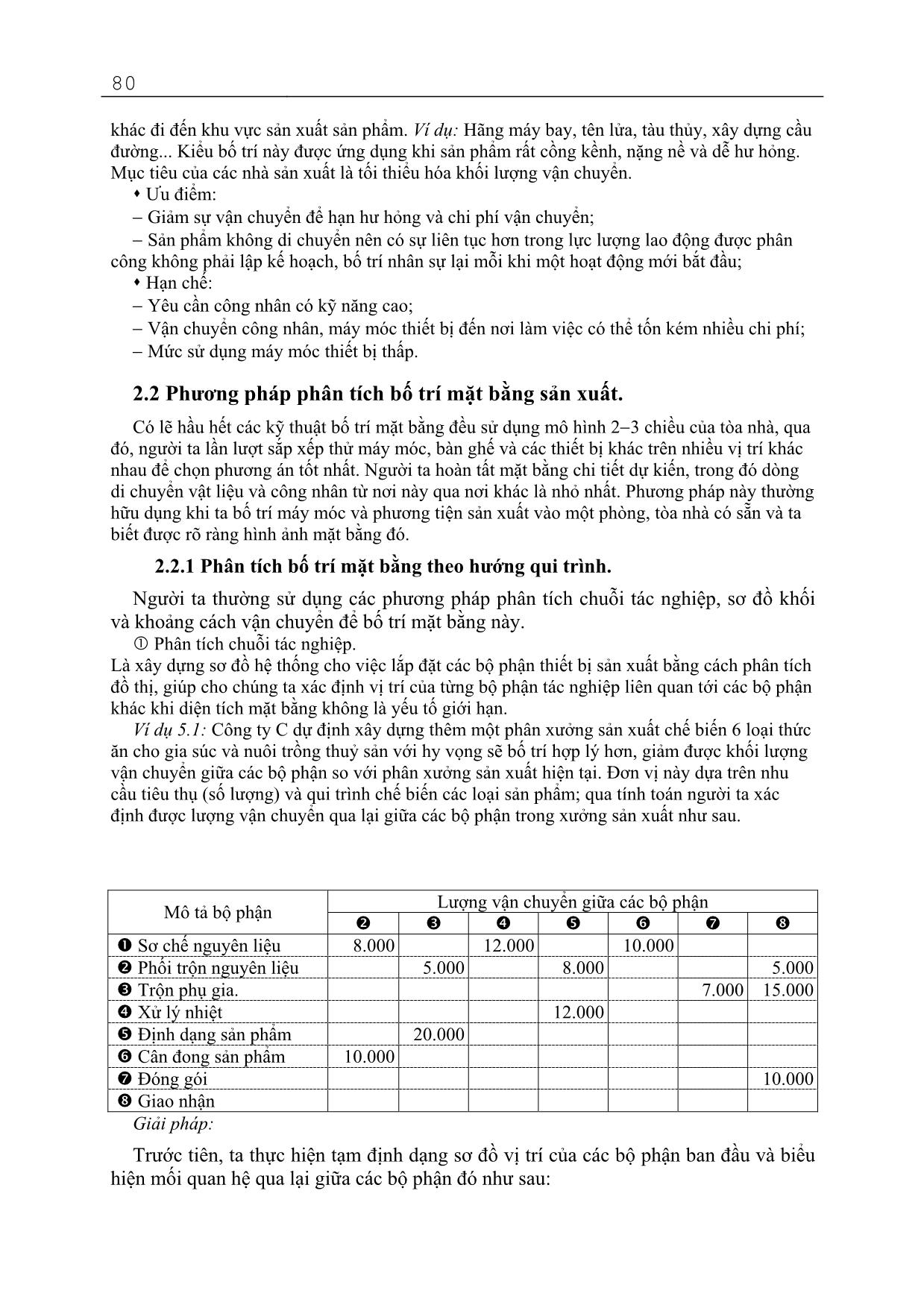
Trang 5
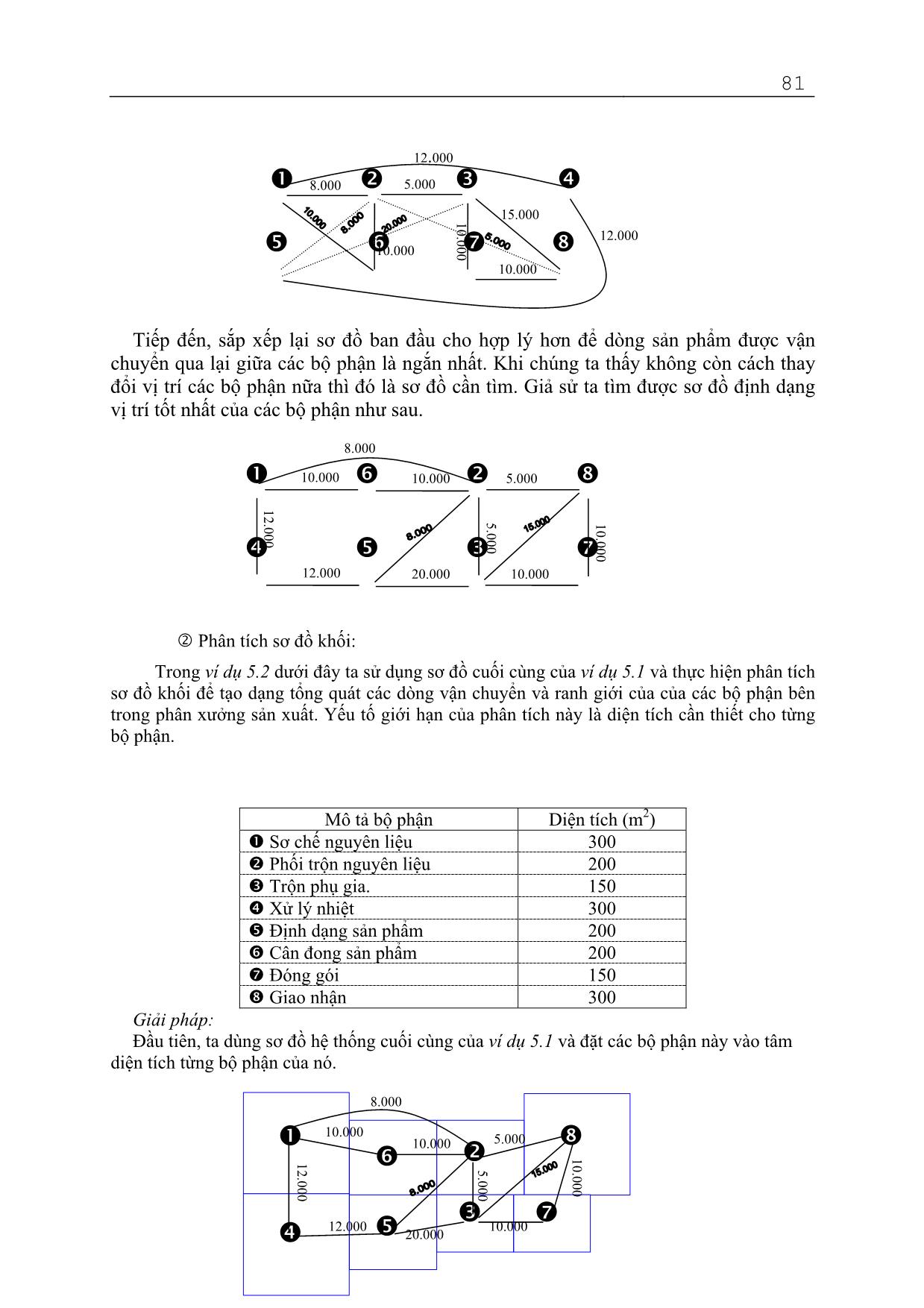
Trang 6
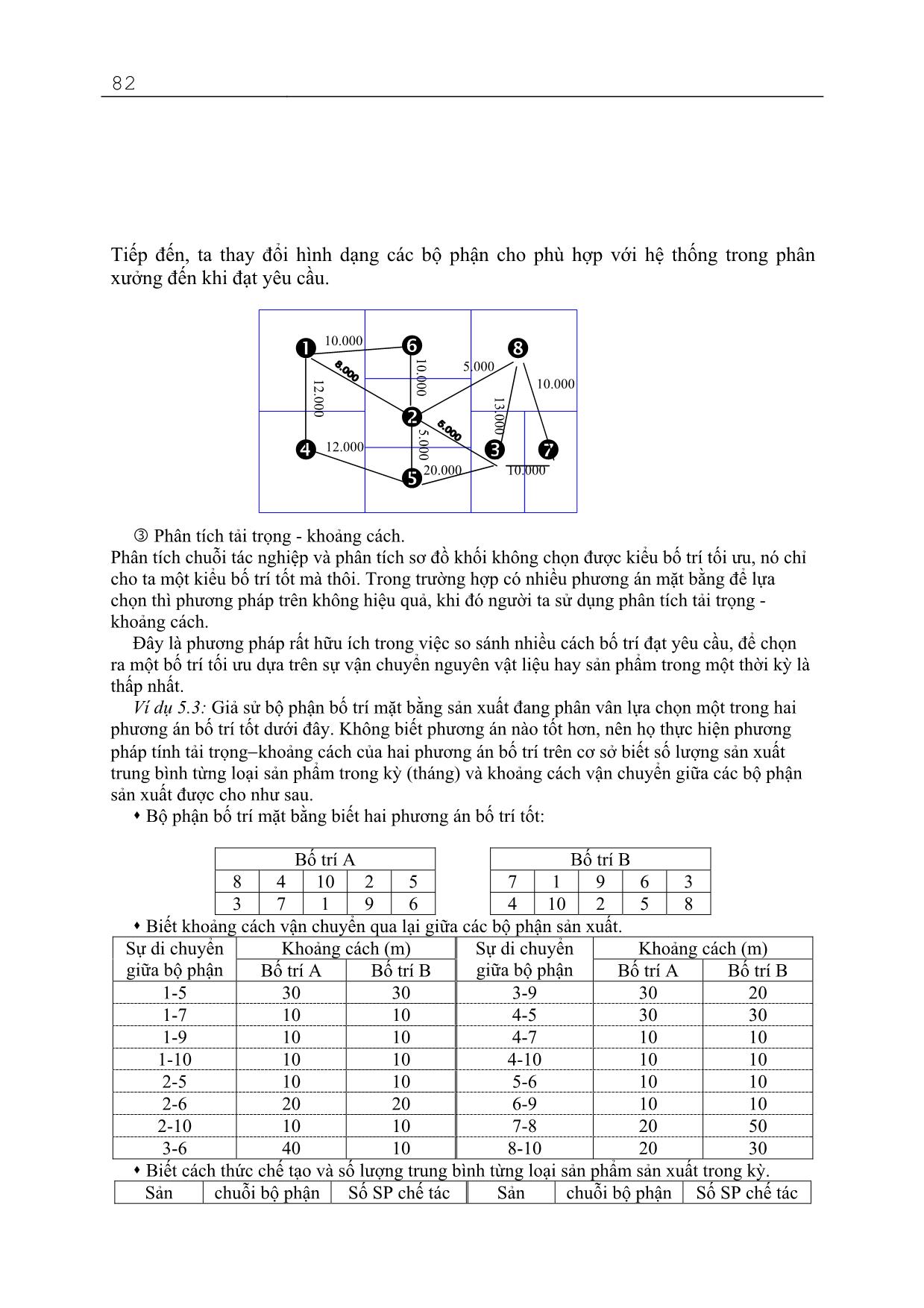
Trang 7
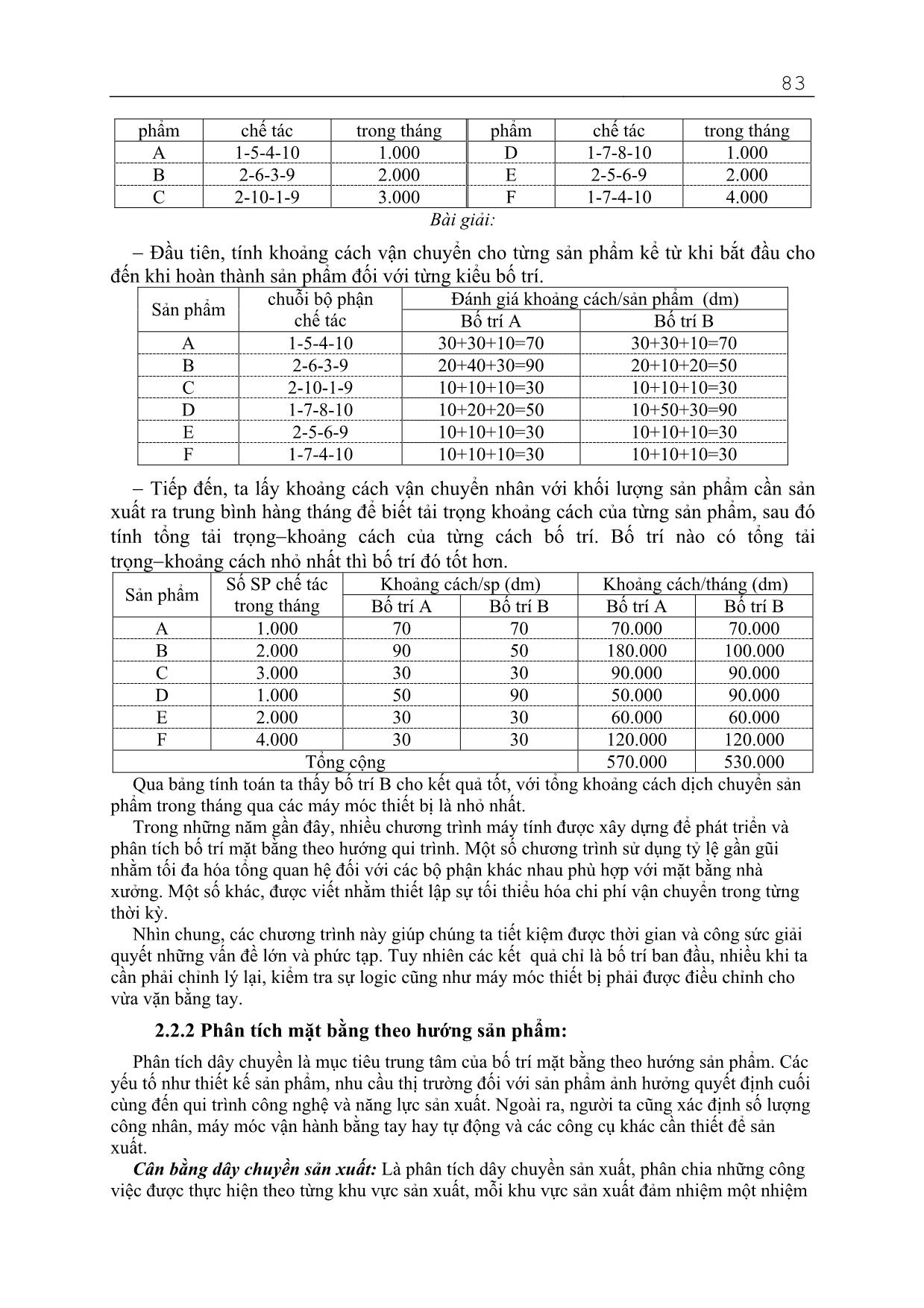
Trang 8
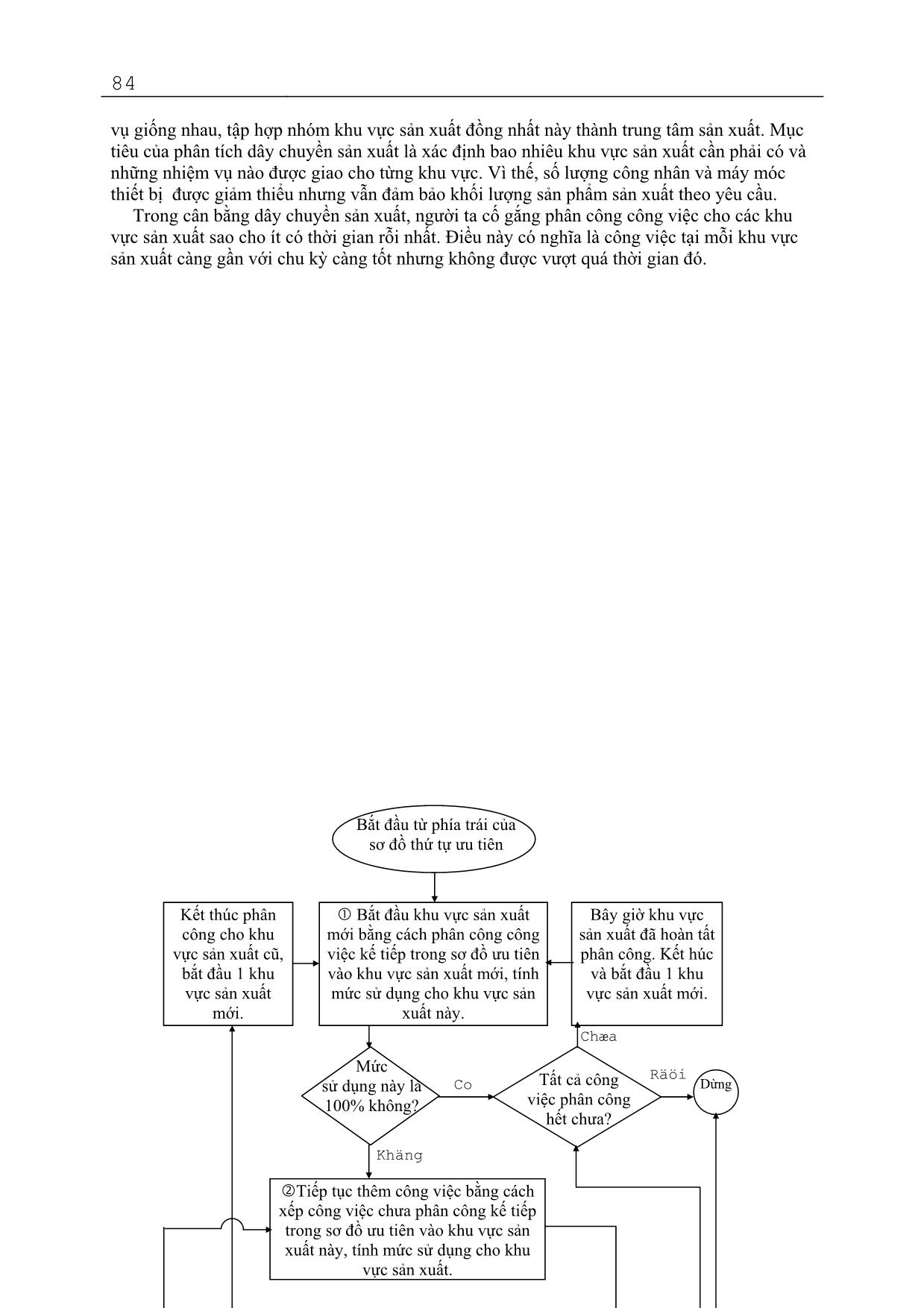
Trang 9
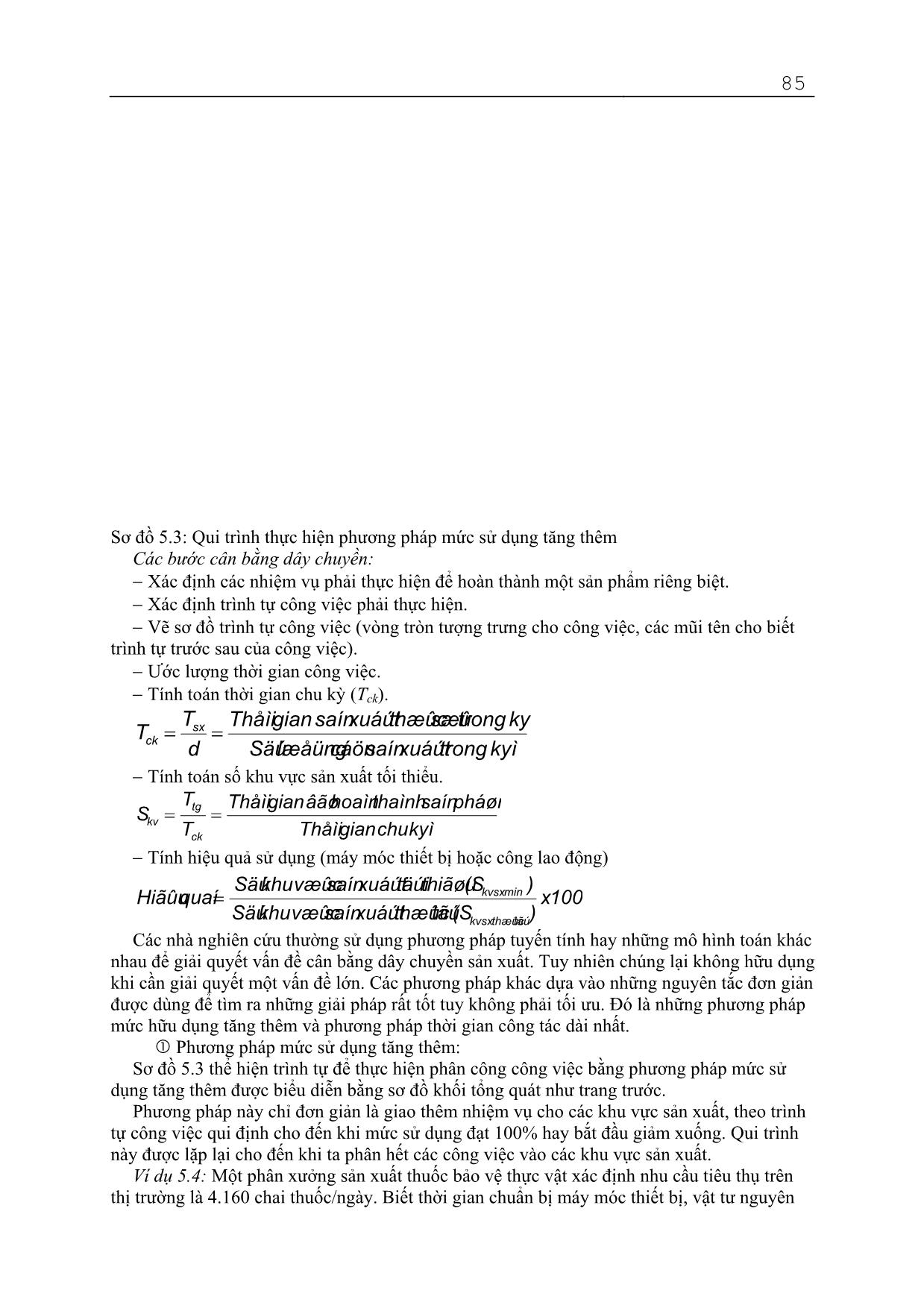
Trang 10
Tải về để xem bản đầy đủ
Tóm tắt nội dung tài liệu: Giáo trình Quản trị sản xuất (Phần 2)
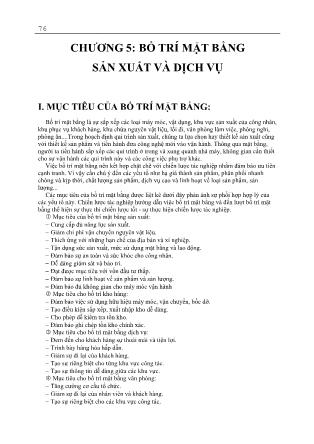
76 CHƯƠNG 5: BỐ TRÍ MẶT BẰNG SẢN XUẤT VÀ DỊCH VỤ I. MỤC TIÊU CỦA BỐ TRÍ MẶT BẰNG: Bố trí mặt bằng là sự sắp xếp các loại máy móc, vật dụng, khu vực sản xuất của công nhân, khu phục vụ khách hàng, khu chứa nguyên vật liệu, lối đi, văn phòng làm việc, phòng nghỉ, phòng ăn....Trong hoạch định qui trình sản xuất, chúng ta lựa chọn hay thiết kế sản xuất cùng với thiết kế sản phẩm và tiến hành đưa công nghệ mới vào vận hành. Thông qua mặt bằng, người ta tiến hành sắp xếp các qui trình ở trong và xung quanh nhà máy, không gian cần thiết cho sự vận hành các qui trình này và các công việc phụ trợ khác. Việc bố trí mặt bằng nên kết hợp chặt chẽ với chiến lược tác nghiệp nhằm đảm bảo ưu tiên cạnh tranh. Vì vậy cần chú ý đến các yếu tố như hạ giá thành sản phẩm, phân phối nhanh chóng và kịp thời, chất lượng sản phẩm, dịch vụ cao và linh hoạt về loại sản phẩm, sản lượng... Các mục tiêu của bố trí mặt bằng được liệt kê dưới đây phản ánh sự phối hợp hợp lý của các yếu tố này. Chiến lược tác nghiệp hướng dẫn việc bố trí mặt bằng và đến lượt bố trí mặt bằng thể hiện sự thực thi chiến lược tốt - sự thực hiện chiến lược tác nghiệp. c Mục tiêu của bố trí mặt bằng sản xuất: − Cung cấp đủ năng lực sản xuất. − Giảm chi phí vận chuyển nguyên vật liệu. − Thích ứng với những hạn chế của địa bàn và xí nghiệp. − Tận dụng sức sản xuất, mức sử dụng mặt bằng và lao động. − Đảm bảo sự an toàn và sức khỏe cho công nhân. − Dễ dàng giám sát và bảo trì. − Đạt được mục tiêu với vốn đầu tư thấp. − Đảm bảo sự linh hoạt về sản phẩm và sản lượng. − Đảm bảo đủ không gian cho máy móc vận hành d Mục tiêu cho bố trí kho hàng: − Đảm bảo việc sử dụng hữu hiệu máy móc, vận chuyển, bốc dỡ. − Tạo điều kiện sắp xếp, xuất nhập kho dễ dàng. − Cho phép dễ kiểm tra tồn kho. − Đảm bảo ghi chép tồn kho chính xác. e Mục tiêu cho bố trí mặt bằng dịch vụ: − Đem đến cho khách hàng sự thoải mái và tiện lợi. − Trình bày hàng hóa hấp dẫn. − Giảm sự đi lại của khách hàng. − Tạo sự riêng biệt cho từng khu vực công tác. − Tạo sự thông tin dễ dàng giữa các khu vực. f Mục tiêu cho bố trí mặt bằng văn phòng: − Tăng cường cơ cấu tổ chức. − Giảm sự đi lại của nhân viên và khách hàng. − Tạo sự riêng biệt cho các khu vực công tác. 77 − Tạo sự thông tin dễ dàng giữa các khu vực Trong chương này chúng ta sẽ khảo sát các kiểu và các phương pháp phân tích bố trí mặt bằng áp dụng trong các lĩnh vực sản xuất (bao gồm cả kho hàng) và dịch vụ (bao gồm văn phòng). II. BỐ TRÍ MẶT BẰNG SẢN XUẤT: Trong nhiều mục tiêu của bố trí mặt bằng, mục tiêu chính cần quan tâm là tối thiểu hóa chi phí vận chuyển, chi phí sản xuất và tồn trữ nguyên vật liệu trong hệ thống sản xuất. Có nhiều loại nguyên vật liệu được dùng trong quá trình sản xuất như: nguyên liệu thô, các chi tiết mua ngoài, nguyên liệu đóng gói, cung cấp bảo trì sửa chữa, phế liệu và chất thải. Ngoài ra, còn sự đa dạng về hình dáng, màu sắc, kích thước, đặc tính hóa học. Sự đa dạng và đặc tính của nguyên vật liệu đã được xác định bởi các quyết định trong thiết kế sản phẩm. Việc bố trí mặt bằng chịu ảnh hưởng trực tiếp các đặc tính tự nhiên của nguyên liệu, như loại nguyên liệu to lớn, cồng kềnh, chất lỏng, chất rắn, nguyên liệu linh hoạt hay không linh hoạt trong điều kiện nóng, lạnh, ẩm ướt, ánh sáng, bụi, lửa, sự chấn động. Một hệ thống vận chuyển nguyên vật liệu là toàn bộ mạng lưới vận chuyển từ khâu tiếp nhận nguyên vật liệu, tồn trữ trong kho, vận chuyển chúng giữa các bộ phận sản xuất và cuối cùng là gửi thành phẩm lên xe để phân phối. Do đó thiết kế và bố trí nhà xưởng phải phù hợp với thiết kế hệ thống vận chuyển. Ví dụ: nếu muốn sử dụng băng tải trên cao thì nhà xưởng phải đủ vững chắc hoặc nếu dùng xe nâng hàng thì lối đi phải đủ rộng, mức chịu tải của sàn nhà thích hợp... Các nguyên tắc vận chuyển nguyên vật liệu. − Tối thiểu hóa việc vận chuyển nguyên vật liệu đến bộ phận sản xuất. − Các qui trình sản xuất liên quan được sắp xếp sao cho thuận lợi dòng cung cấp nguyên liệu. − Nên thiết kế và định vị các thiết bị vận chuyển, lựa chọn nơi tồn trữ nguyên liệu sao cho giảm tối đa sự nổ lực của công nhân: cúi xuống, với tay, đi lại... − Tối thiểu hóa số lần vận chuyển của từng loại nguyên liệu − Sự linh hoạt của hệ thống cho phép các tình huống bất thường: thiết bị vận chuyển nguyên liệu hỏng, thay đổi công nghệ sản xuất, mở rộng năng lực sản xuất. − Các thiết bị vận chuyển phải sử dụng hết trọng tải của nó 2.1 Các kiểu bố trí mặt bằng sản xuất: Có nhiều kiểu bố trí mặt bằng sản xuất khác nhau, dưới đây chúng sẽ lần lượt khảo sát từng kiểu bố trí: theo quá trình, theo sản phẩm, theo khu vực sản xuất và kiểu bố trí cố định. 2.1.1 Bố trí theo quá trình: Hay còn gọi là bố trí chức năng theo sự đa dạng của thiết kế sản phẩm và các bước chế tạo. Kiểu bố trí này thường sử dụng nếu xí nghiệp sản xuất nhiều loại sản phẩm khác nhau với những đơn hàng nhỏ. Máy móc, thiết bị ... nh số lượng khu vực sản xuất tối thiểu (số công nhân hoặc máy móc thiết bị cần tối thiểu để sản xuất). kvsx 3,256 152 T T T d.T S ck tg sx tg kvsx ==== − Cân bằng dây chuyền sản xuất bằng phương pháp mức sử dụng tăng thêm. 87 Đầu tiên, chúng ta phân công công việc cho từng trung tâm sản xuất (trạm sản xuất), việc này cần phải tuân theo thứ tự trước sau của các công việc một cách chặt chẽ (C phải sau A, sau B; E phải sau C, sau D;...). Các nhiệm vụ được kết hợp theo thứ tự cho đến khi mức sử dụng của trung tâm sản xuất là 100%, hay khi quan sát thấy sự giảm xuống của nó so với phân công trước đó. Lúc này ta mở trung tâm sản xuất mới và bắt đầu lại trình tự. Trạm sản xuất (1) Công việc (2) Phút/máy (3) Số KVSX làm việc (4)=[(3)/thời gian chu kỳ] Số KVSX thực tế cần thiết (5) Mức sử dụng của KVSX (%) [(4)/(5)]x100 1 A 10 1,67 2 83,3 1 A,B 10+15=25 4,16 5 83,3 1 A,B,C 10+15+10=35 5,83 6 97,2 1 A,B,C,D 10+15+10+6=41 6,83 7 97,6 1 A,B,C,D,E 10+15+10+6+8=49 8,17 9 90,7 2 E 8 1,33 2 66,7 2 E,F 8+6=14 2,33 3 77,8 2 E,F,G 8+6+10=24 4,00 4 100,0 3 H 5 0,83 1 83,3 3 H,I 5+7=12 2,00 2 100,0 4 J 8 1,33 2 66,7 4 J,K 8+12=20 3,33 4 83,3 4 J,K,L 8+12+10=30 5,00 5 100,0 5 M 15 2,50 3 83,3 5 M,N 15+20=35 5,83 6 97,2 5 M,N,O 15+20+10=45 7,50 8 93,8 26 Tóm tắt phân công công việc vào khu vực sản xuất trên dây chuyền như sau: Trạm sản xuất 1 2 3 4 5 Công việc trong trạm sản xuất A,B,C,D E,F,G H,I J,K,L M,N,O Số khu vực sản xuất thực tế 7 4 2 5 8 Tổng: 26 Như vậy, để hoàn thành khối lượng sản phẩm cần sản xuất trong 1 ngày là 4.160 chai thuốc thì chúng ta cần có 5 trạm làm việc, tuỳ vào mỗi trạm mà cần số khu vực sản xuất (số công nhân hoặc máy móc thiết bị) − Tính hiệu quả sử dụng máy móc thiết bị (Msd) %3,97100x 26 25,3 S S M tãú thæûckv mimkv sd === d Phương pháp thời gian công tác dài nhất. Trong phương pháp này ta lần lượt thêm công việc cho một khu vực sản xuất theo thứ tự bước sau. Nếu có sự lựa chọn giữa 2 hay nhiều công việc thì công việc có thời gian công tác dài nhất được chọn phân công trước. Điều này có hiệu quả cho việc phân công nhanh chóng những công việc khó phân công vào khu vực sản xuất. A B C E F I K D HG J N L M O 1 2 3 4 5 88 Ví dụ 5.5: .Sử dụng tiếp ví dụ 5.4, giả sử đơn vị xác định lại nhu cầu sản xuất của phân xưởng này là 832 chai thuốc/ngày (thay vì 4.160 chai). Hãy cân bằng dây chuyền sản xuất trong trường hợp này. Bài giải: − Trước tiên, ta tính thời gian chu kỳ. ( )[ ] giáy/chai 30 832 60x6460x8 d TT sxck =−== − Số khu vực sản xuất tối thiểu. væû khu 07,5 30 152 T T S ck tg kv === − Phân công công việc vào các khu vực sản xuất. Khu vực sản xuất Các công việc Thời gian công việc mới Tổng thời gian thực hiện Thời gian thừa ở KVSX (1) (2) (3) (4) [30’’-(4)] 1 A 10 10 20 1 A,B 15 25 5 2 C 10 10 20 2 C,D 6 16 14 2 C,D,E 8 24 6 2 C,D,E,F 6 30 0 3 G 10 10 20 3 G,H 5 15 15 3 G,H,I 7 22 8 3 G,H,I,J 8 30 0 4 K 12 12 18 4 K,L 10 22 8 5 M 15 15 15 6 N 20 20 10 6 N,O 10 30 0 Tóm tắt sự phân công các công việc vào các khu vực sản xuất trên dây chuyền sản xuất. Khu vực sản xuất 1 2 3 4 5 6 Công việc thực hiện A,B C,D,E,F G,H,I,J K,L M N,O Thời gian thừa (giây) 5 0 0 8 15 0 − Tính toán mức sử dụng của máy móc thiết bị hoặc công lao động. %5,84100x 6 07,5100x S SM kctt minkv sd === A B C E F I K D HG J N L M O 1 2 3 4 5 6 89 Điều kiện để sử dụng phương pháp thời gian công tác dài nhất là: , tức là thời gian chu kỳ phải lớn hơn hoặc bằng thời gian lớn nhất cần để thực hiện công việc trong chuỗi công việc chế tạo sản phẩm. Theo như bài toán trên thì Tck = 30 giây, công việc tiêu hao thời gian lớn nhất là công việc N mất 20 giây. III. BỐ TRÍ MẶT BẰNG DỊCH VỤ: 3.1 Các kiểu bố trí mặt bằng dịch vụ: Bố trí mặt bằng dịch vụ tùy thuộc vào bản chất tự nhiên của dịch vụ và các mà các doanh nghiệp phối hợp và vận chuyển dịch vụ của họ: hàng không, ngân hàng, nhà bán lẻ, bệnh viện, nhà hàng, bảo hiểm, vận tải, giải trí, viễn thông....Ngoài ra, bố trí mặt bằng dịch vụ còn tùy thuộc vào máy móc chuyên dùng cho từng loại dịch vụ. Điểm khác biệt trong kinh doanh dịch vụ so với sản xuất là sự chạm trán giữa khách hàng và những dịch vụ mà các doanh nghiệp này cung cấp cho họ. Sự chạm trán này có thể mạnh mẽ vì khách hàng thực sự là một phần của qui trình sản xuất như trong bệnh viện, nơi mà dịch vụ thực sự được hình thành trên khách hàng. Hoặc sự chạm trán ít mạnh mẽ hơn trong các hiệu buôn lẻ vì ở đó khách chọn hàng, thanh toán và mang đi những hàng hóa vật chất. Nhưng bất kể trường hợp nào, bố trí mặt bằng dịch vụ có ảnh hưởng một cách sâu đậm. Nguyên tắc chung là phải bố trí sao cho khách hàng dễ dàng khi vào, ra và đi lại giữa các phần trong mặt bằng. Ngoài ra, cũng cần phân bố diện tích thích hợp cho hành lang, phòng chờ... Có 2 cực trong việc bố trí mặt bằng dịch vụ. Ví dụ, đa ngân hàng chẳng hạn, một cực là dịch vụ công khai, khi đó các máy móc thiết bị phải được bố trí xung quanh khách hàng, làm cho họ thuận lợi nhất (phòng chờ, nơi đậu xe, cửa sổ thu ngân...). Một cực khác là các dịch vụ bên trong với các máy móc phục vụ được bố trí chủ yếu theo công việc giao dịch tài chính (cập nhật tài khoản, lập báo cáo...) Hầu hết các bố trí đều xoay quanh hai cực này. Ví dụ, các nhà hàng bố trí nhằm nhấn mạnh sự chấp nhận và tiện lợi cá nhân của khách hàng hơn là chuẩn bị và chế biến thức ăn. 3.2 Phân tích bố trí mặt bằng dịch vụ: Trong hầu hết các loại dịch vụ, người ta cố gắng bố trí sao cho tổng cự ly di chuyển của khách hàng là ít nhất bên cạnh việc bố trí các máy móc phục vụ tiện lợi. Ngoài ra cần lưu ý việc bố trí phòng chờ, nơi xếp hàng sao cho thoải mái. Đối với nhiều loại dịch vụ, lý do khiến cho một bộ phận nào đó ở cạnh một bộ phận khác rất phức tạp. Khi đó người ta thường sử dụng tỷ lệ gần gũi nhằm phản ánh sự mong muốn một bộ phận nào cạnh bộ phận nào đó. Sau đó dùng phương pháp thử đúng - sai, phân tích chuỗi tác nghiệp hay phân tích sơ đồ khối, sử dụng tỷ lệ gần gũi để xây dựng bố trí mặt bằng tốt. Thí dụ 5.6: Giả sử một cửa hàng bán các loại thực phẩm, dự định bố trí 6 nhóm mặt hàng (A,B,C,D,E,F) theo mức độ quan hệ gần gũi giữa các nhóm mặt hàng như sau: Tỷ lệ gần gũi Ý nghĩa Tỷ lệ gần gũi Ý nghĩa (max)cvck TT ≥ 90 1 Cần thiết 4 Hơi quan trọng 2 Rất quan trọng 5 Không quan trọng 3 Quan trọng 6 Không mong muốn Dựa trên các nhóm mặt hàng, chúng ta biết được mối quan hệ gần gũi của chúng như sơ đồ dưới đây: Bộ phận A B C D E F Dùng phương pháp tỷ lệ gần gũi để bố trí 6 nhóm mặt hàng này vào mặt bằng của cửa hàng. Bài giải: Đầu tiên, chú ý rằng cặp bộ phận có tỷ lệ gần gũi 1 (cần thiết) là A-C, A-E, A-F, C- E, C-F và E-F. A phải tiếp cận C, E và F; C phải cạnh E và F; E phải cạnh F. Khi thử lần đầu tiên, cố gắn bố trí để A, C, E, F tất cả cạnh nhau. Bố trí dưới đây thích hợp với tất cả cặp bộ phận với tỷ lệ gần gũi 1. A C A C B E F E F D Kế đến, lưu ý rằng cặp bộ phận với tỷ lệ gần gũi 6 (không mong đợi) là A-B và D- E. A phải không cạnh B và D phải không cạnh E. Bằng cách xếp 2 bộ phận D và E vào 2 chổ trống còn lại, bố trí hình trên đây thích hợp cho tất cả các cặp với tỷ lệ gần gũi 6. Chú ý rằng trong bước cuối cùng nêu trên, việc đặt bộ phận có tỷ lệ gần gũi là 6 lập tức thích hợp với những bộ phận có tỷ lệ gần gũi 1. Vấn đề không luôn đơn giản như vậy, có thể cần một vài vòng điều chỉnh các bộ phận để cải thiện, nếu có. --- o O o --- 1 3 1 5 5 5 1 1 5 1 6 5 5 6 1 91 TÓM LƯỢC CÔNG THỨC & BÀI TẬP CUỐI CHƯƠNG I. CÂU HỎI ÔN TẬP: 1. Hãy nêu mục tiêu bố trí của mặt bằng sản xuất? 2. Hãy cho biết các nguyên tắc vận chuyển nguyên vật liệu? 3. Hãy trình bày ưu điểm và hạn chế của cách bố trí mặt bằng theo qui trình? 4. Hãy trình bày ưu điểm và hạn chế của cách bố trí mặt bằng theo sản phẩm? 5. Nêu các bước cân bằng dây chuyền sản xuất? 6. Cho biết điều kiện để áp dụng được phương pháp cân bằng dây chuyền sản xuất bằng phương pháp thời gian công tác dài nhất? II. CÔNG THỨC ÁP DỤNG. Thời gian chu kỳ. ngaìy) giåì, 1 trong xuáút saíncáön pháøm saín(Læåüng d ngaìy) giåì, 1 trong xuáút saín sæûthæûc gian (Thåìi TT SXCK = Số khu vực sản xuất tối thiểu. SX TG CK TG KV T d.T T TS == TTG − Thời gian kể từ khi bắt đầu cho đến khi hoàn thành 1 sản phẩm. Mức sử dụng máy móc thiết bị. tãú thæûc xuáút saínvæûc khu Säú )S( thiãøu täúi xuáút saínvæûc khu Säú)(S )(M duûng sæí Mæïc KVthæûctãú KVmin SD = Điều kiện để áp dụng cân bằng dây chuyền bằng phương pháp thời gian công tác dài nhất. cv SX (max)cvck SX T TdTT d T ≤⇒≥= Nếu nhu cầu sản xuất sản phẩm của đơn vị là cv SX T Td ≤ c sử dụng t , thì đơn vị áp dụng được cả hai phương pháp cân bằng dây chuyền sản xuất (mứ ăng thêm và thời gian công tác dài nhất). Nếu cv SX T Td > thì chỉ áp dụng được một phương pháp mức sử dụng tăng thêm. III. BÀI TẬP CÓ LỜI GIẢI. Bài 1: Giả sử đơn vị có kế hoạch xây dựng thêm một phân xưởng chế biến các mặt hàng nông sản, đơn vị dựa trên nhu cầu tiêu thụ của thị trường và cách thức chế biến từng loại sản phẩm để xác định các dòng nguyên vật liệu phải vận chuyển qua lại giữa các bộ phận chế tác. Biết rằng phân xưởng chế biến các mặt hàng mới này gồm có 9 bộ phận như sau: Bộ phận d e f g h i j k c 1.000 3.000 9.000 4.000 d 5.000 92 e 2.000 4.000 2.000 f 4.000 5.000 1.000 g 5.000 h 5.000 3.000 i 4.000 1.000 j 8.000 Bạn hãy bố trí các bộ phận chế tác như thế nào để đảm bảo giảm khoảng cách vận chuyển giữa các bộ phận. Bài giải Trước tiên, ta phác họa sơ đồ ban đầu biểu hiện mối quan hệ giữa các bộ phận như sau. Tiếp đến ta sắp xếp sơ đồ lại cho hợp lý hơn để sản phẩm vận chuyển giữa các bộ phận ngắn nhất. Cuối cùng, ta hoàn chỉnh lại sơ đồ để có bố trí hợp lý nhất. Bài 2: Giả sử các bộ phận chế tác ở bài 1 có diện tích cần thiết ở từng bộ phận là. Bộ phận Diện tích (m2) Bộ phận Diện tích (m2) 1.000 c d e f g h i j k 5.000 9.000 5.000 8.000 4.000 3.000 1.000 5.000 4.000 1 100 6 50 h 9.000 5.000 5.000 5.000 4.000 3.000 c e df j g i k 9.000 4.000 4.000 2.000 4.000 8.000 1.000 1.000 c e d f h j g i k 93 2 50 7 150 3 200 8 50 4 50 9 100 5 150 Hãy định vị các bộ phận sản xuất trên diện tích mặt bằng cho trước. Bài giải Đầu tiên, ta căn cứ vào sơ đồ bố trí hoàn chỉnh và đặt các bộ phận này vào tâm của diện tích cần thiết cho từng bộ phận tương ứng. Ta có dạng sơ bộ như sau: Tiếp theo, ta căn cứ vào chiều dài, chiều rộng mặt bằng của xí nghiệp để phân chia diện tích hợp lý cho từng bộ phận sản xuất. Ta có bố trí cuối cùng có dạng như sau. Bài 3: Giả sử chúng ta đang lựa chọn giữa 2 cách bố trí mặt bằng như sau. Bố trí I Bố trí II h c i d h i d g g j f e j c f e e i c k f d j g 1.000 4.000 4.000 2.000 1.000 h i e c f j h k g d 1.000 1.000 9.000 4.000 8.000 4.000 4.000 94 Biết rằng đơn vị chế tạo ra 6 loại sản phẩm (A, B, C, D, E và F) trong tháng tới theo trình tự các chuỗi chế tác như sau. Sản phẩm Chế tác Số lượng Sản phẩm Chế tác Số lượng A 1-4-3-7 4.500 D 1-4-3-5 4.000 B 2-3-4-8 3.000 E 1-5-6-8 2.000 C 1-2-3-5 5.500 F 3-4-7-6 3.500 Biết khoảng cách (m) giữa các bộ phận chế tác như sau. Khoảng cách các bộ phận (m) Khoảng cách các bộ phận (m) Bộ phận Bố trí I Bố trí II Bộ phận Bố trí I Bố trí II 1-2 20 15 3-7 15 25 1-4 15 10 4-7 10 15 1-5 15 25 4-8 10 20 2-3 10 15 5-6 10 30 3-4 10 10 6-7 20 10 3-5 30 10 6-8 15 10 Hãy lựa chọn cách bố trí sao cho dòng di chuyển giữa các bộ phận chế tác là ngắn nhất. Bài giải Trước tiên ta tính tổng khoảng cách vận chuyển để sản xuất được 1 sản phẩm giữa 2 phương án bố trí, kết quả tính toán như bảng sau. Khoảng cách VC giữa các bộ phận chế tác(m) Sản phẩm chuỗi chế tác Bố trí I Bố trí II A 1-4-3-7 15+10+15=40 10+10+25=45 B 2-3-4-8 10+10+10=30 15+10+20=45 C 1-2-3-5 20+10+30=60 15+15+10=40 D 1-4-3-5 15+10+30=55 10+10+10=30 E 1-5-6-8 15+10+15=40 25+30+10=65 F 3-4-7-6 10+10+20=40 10+15+10=35 Tổng 265 260 Như vậy theo tính toán tổng khoảng cách vận chuyển của 1 sản phẩm giữa các bộ phận chế tác thì bố trí II có lợi thế hơn bố trí I. Tuy nhiên khối lượng của từng loại sản phẩm được chế tạo nhiều hay ít, nó sẽ quyết định tổng tải trọng-khoảng cách vận chuyển giữa các bộ phận của 2 bố trí này. KCVC/sp (m) KCVC/tháng (m) Sản phẩm chuỗi chế tác Bố trí I Bố trí II Bố trí I Bố trí II A 1-4-3-7 40 45 157.500 202.500 B 2-3-4-8 30 45 90.000 135.000 C 1-2-5-3 60 40 330.000 220.000 D 1-4-3-5 55 30 220.000 120.000 E 1-5-6-8 40 65 80.000 130.000 F 3-4-7-6 40 35 140.000 122.500 Tổng 265 260 1.040.000 930.000 95 Qua bảng tính toán ta thấy bố trí II có tổng tải trọng-khoảng cách vận chuyển nhỏ nhất. Do đó ta nên chọn cách bố trí II để thực hiện. Bài 4: Một công ty lắp ráp máy tính tay model AT75, những nhiệm vụ lắp ráp phải thực hiện cho ở bảng dưới đây. Công việc Công việc trước đó Thời gian hoàn thành công việc (phút) A. Đặt khung mạch điện lên. - 0,18 B. Đặt mạch điện #1 vào khung. A 0,12 C. Đặt mạch điện #2 vào khung. A 0,32 D. Đặt mạch điện #3 vào khung. A 0,45 E. Gắn mạch điện vào khung. B,C,D 0,51 F. Hàn nối mạch điện . E 0,55 G. Đặt mạch điện vào khung máy tính. F 0,38 H. Gắn vít giữa mạch và khung máy. G 0,42 I. Đặt và gắn màn hình. H 0,30 J. Đặt và gắn bàn phím. I 0,18 K. Đặt và gắn thân trên. J 0,36 L. Đặt và gắn bộ phận năng lượng. J 0,42 M. Đặt và gắn thân dưới. K,L 0,48 N. Kiểm tra mạch điện. M 0,30 O. Đặt máy và bảng hưởng dẫn vào hộp. N 0,39 Những chi tiết lắp ráp được di chuyển dọc theo băng tải giữa các khu vực sản xuất. Nếu biết thời gian chết trung bình mất 6 phút/giờ và đơn vị muốn sản xuất 540 máy tính/giờ thì cân bằng dây chuyền này thế nào? Bài giải: * Tính thời gian chu kỳ phuït/ma 1,0 540 54 d TT sxck === * Tính số lượng khu vực sản xuất tối thiểu: kvsx 6,53 1,0 36,5 T T T d.T S ck tg sx tg kvsx ==== * Sơ đồ trình tự các công việc. * Cân băng dây chuyền sản xuất: Kế đến, phân công công việc cho từng trung tâm sản xuất, việc này cần phải tuân theo thứ tự trước sau của các công việc một cách chặt chẽ (D phải sau A, G phải sau F...). Các nhiệm vụ được kết hợp theo thứ tự cho đến khi mức sử dụng của trung tâm sản xuất là 100%, hay khi quan sát thấy sự giảm xuống của nó so với bố trí trước đó. Lúc này ta mở trung tâm sản xuất mới và bắt đầu lại trình tự. Trạm SX Công việc Phút/máy Số KVSX tối thiểu Số KVSX thực tế Mức sử dụng (%) B C O A D F G H E N M L K J I
File đính kèm:
giao_trinh_quan_tri_san_xuat_phan_2.pdf