Fabricating ultra - thin silicon nitride membranes suspended on silicon wafer
Abstract: Ultrathin silicon nitride SiNx membrane suspended on a silicon wafer is a popular twodimensional platform in MEMS applications. The unsupported membrane has a low thermal
conductivity, is electrically insulated, and very robust against mechanical impact. Remarkably thin,
it is difficult to fabricate and manipulate. Recently equipped with a dual chamber system for plasma
enhanced chemical vapor deposition (PECVD) and reactive ion etching, we calibrate it to deposit
silicon nitride Si3N4, silicon dioxide SiO2, and to dry etch these materials. Based on the superb
quality of Si3N4, we perform a through-wafer etch that creates suspended Si3N4 membranes. The
recipe is reliable and reproducible. We analyze the membrane’s chemical composition and optical
properties. Although created by PECVD, the membrane is so robust that it survives multiple
lithography steps. It extends our capability to study thermal transport at the submicron scale as well
as to fabricate micron size devices for MEMS applications.
Keywords: Power MEMS, Silicon nitride membranes, PECVD, silicon wafer.
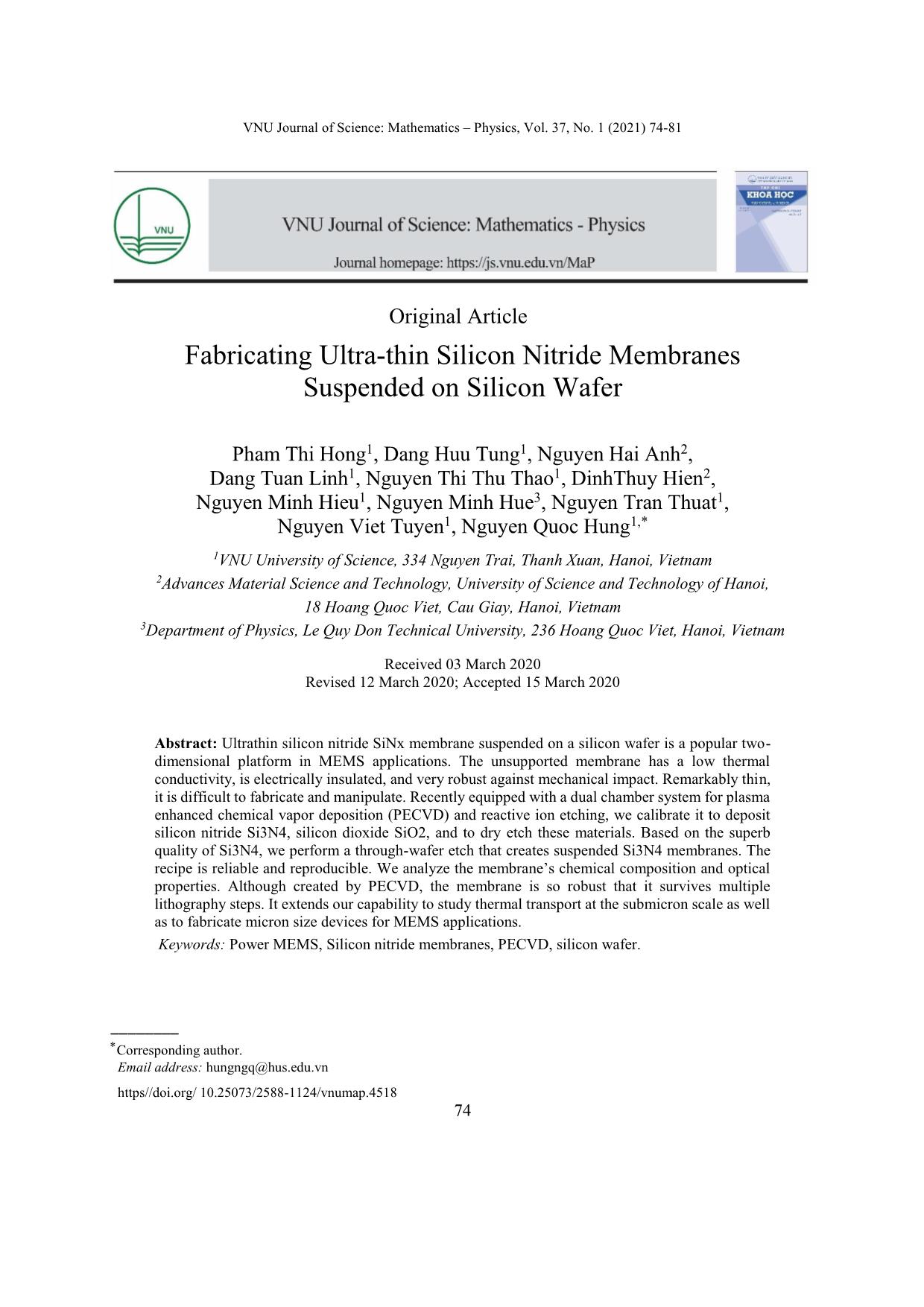
Trang 1
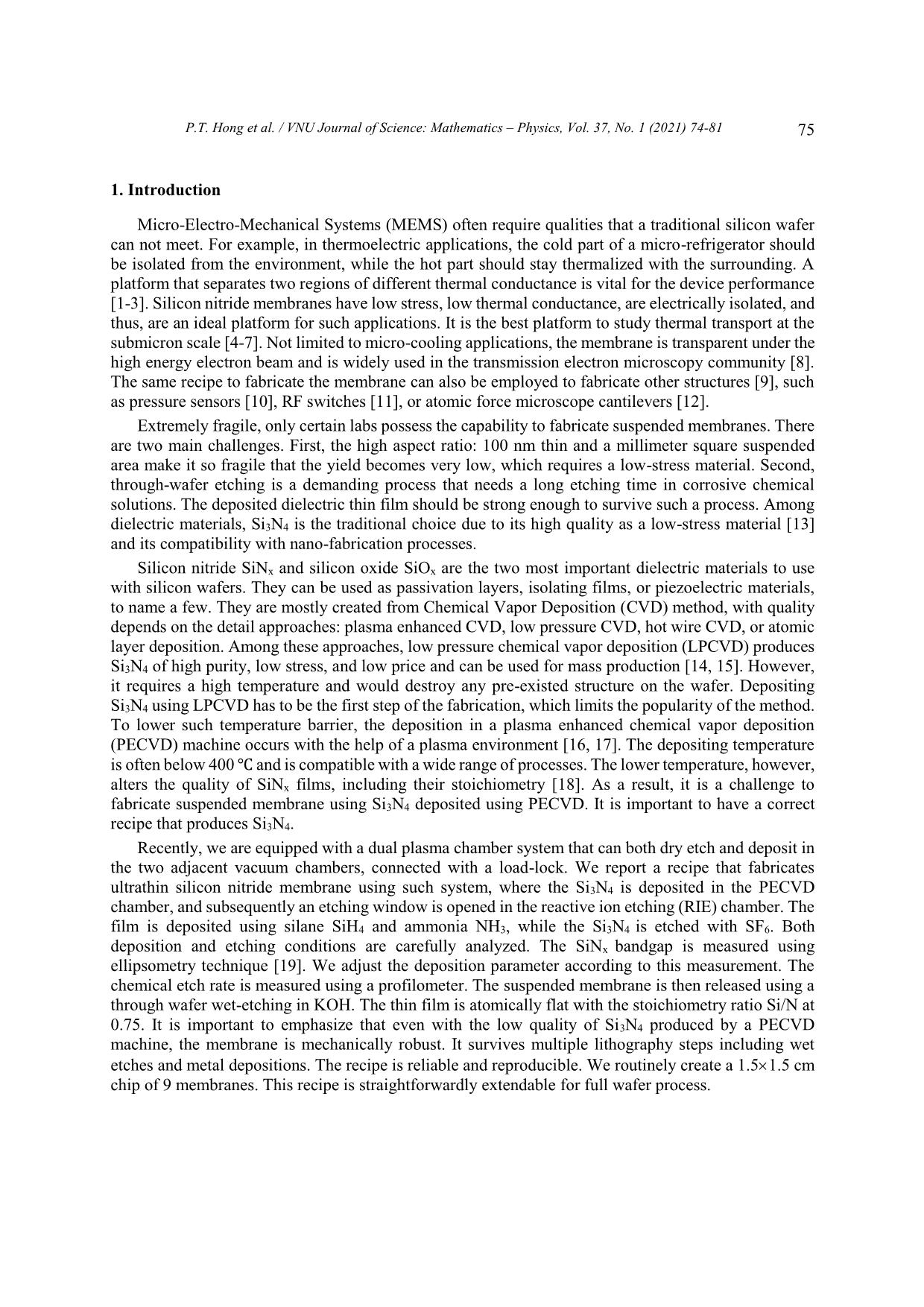
Trang 2
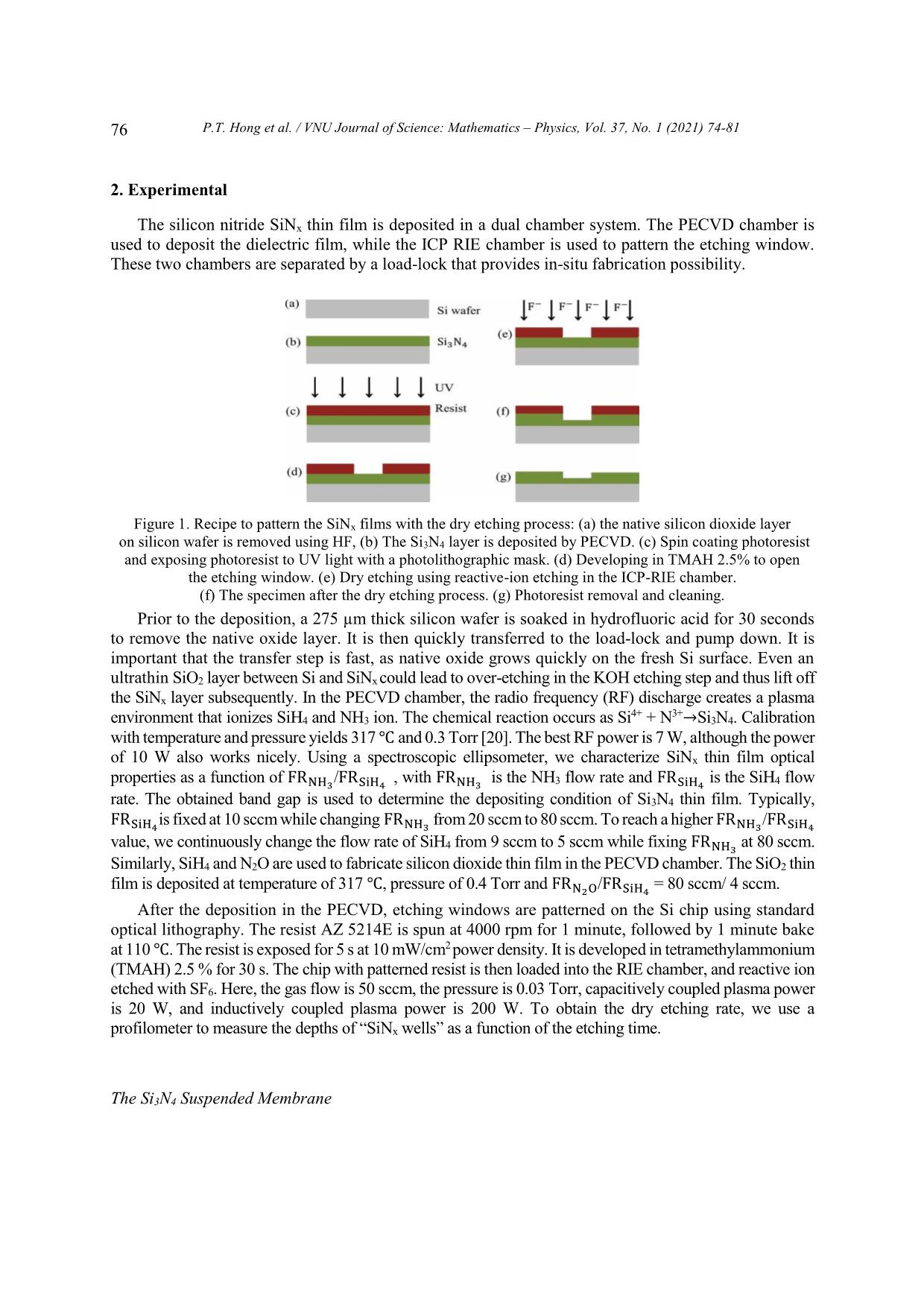
Trang 3
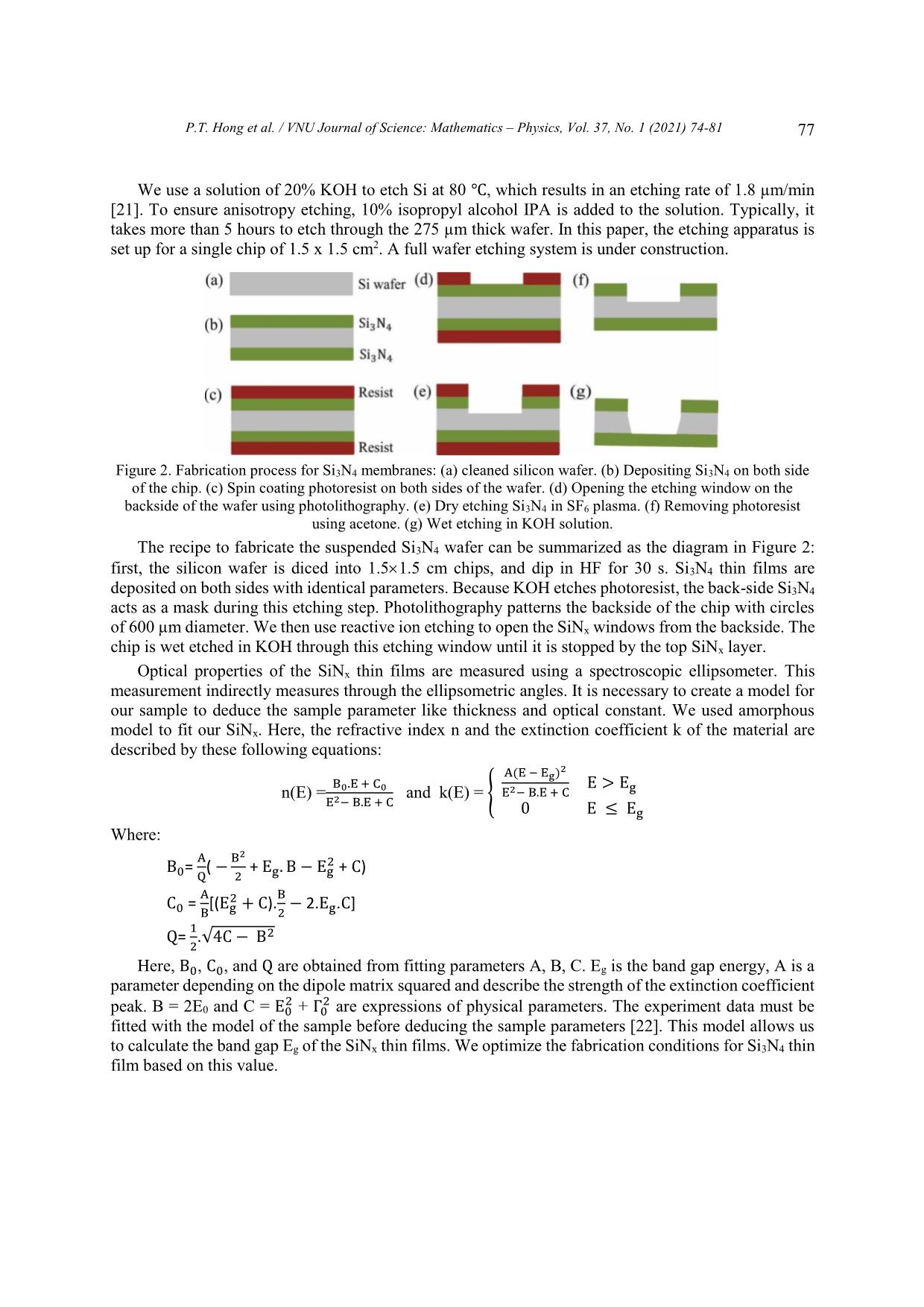
Trang 4
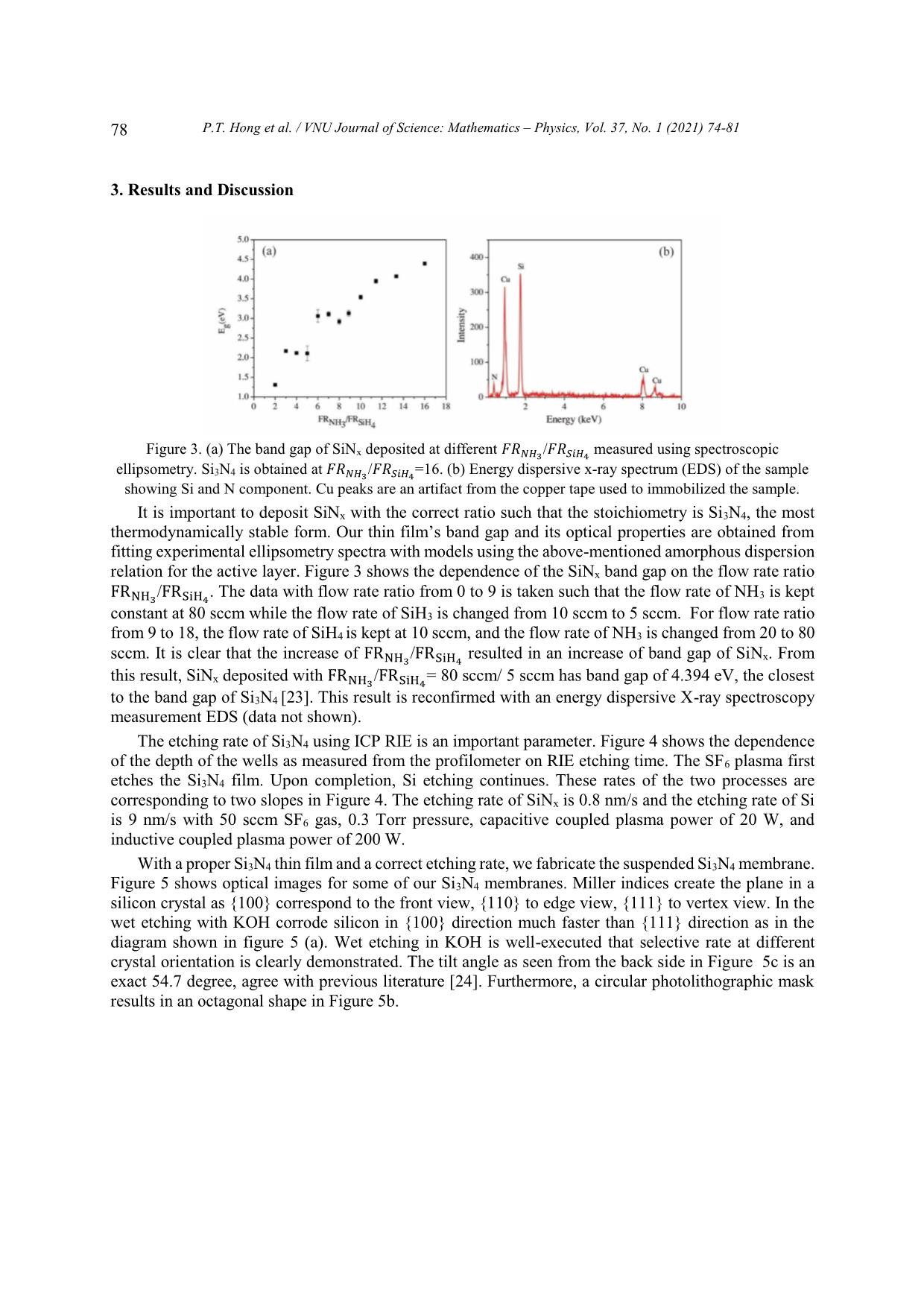
Trang 5
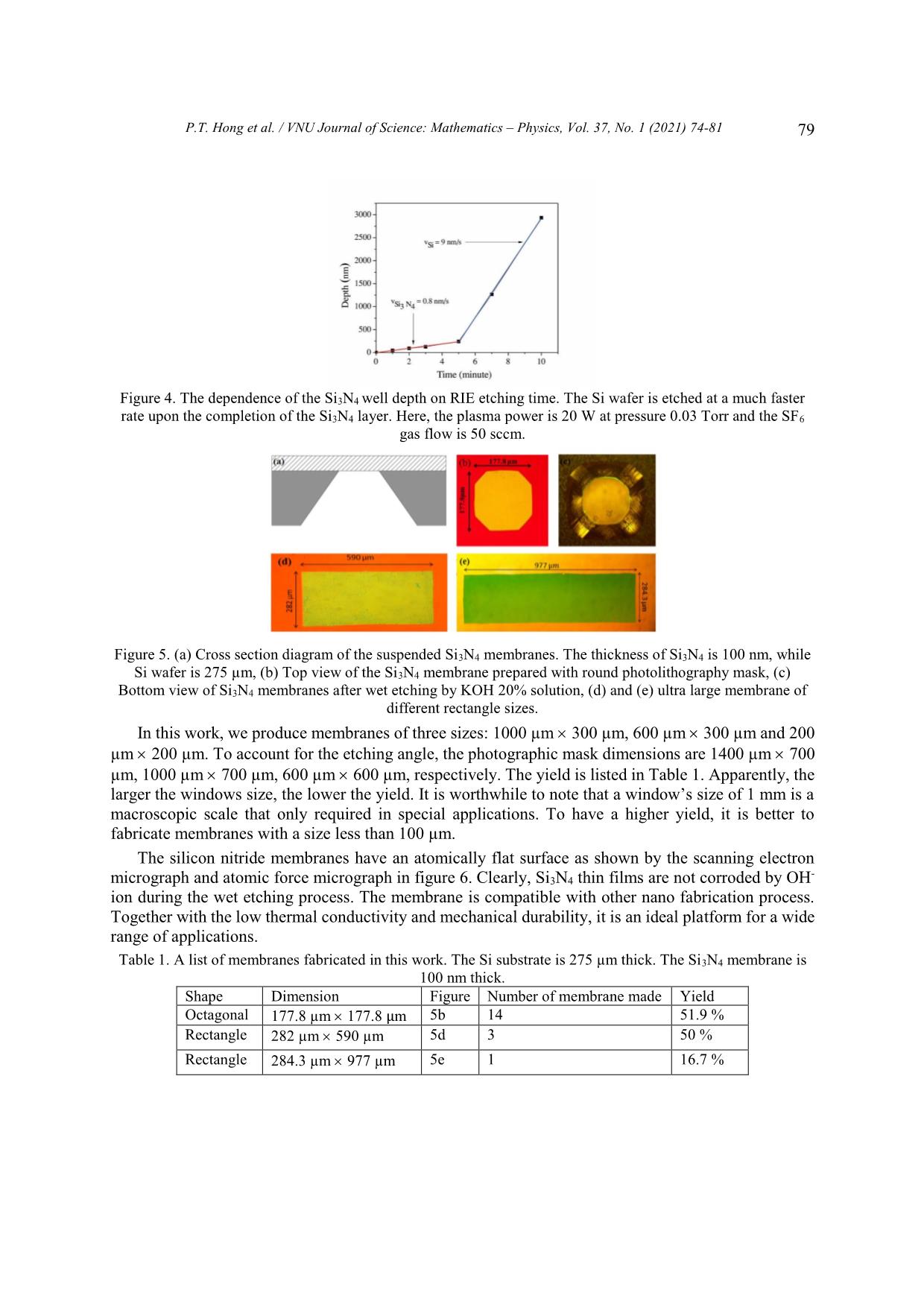
Trang 6
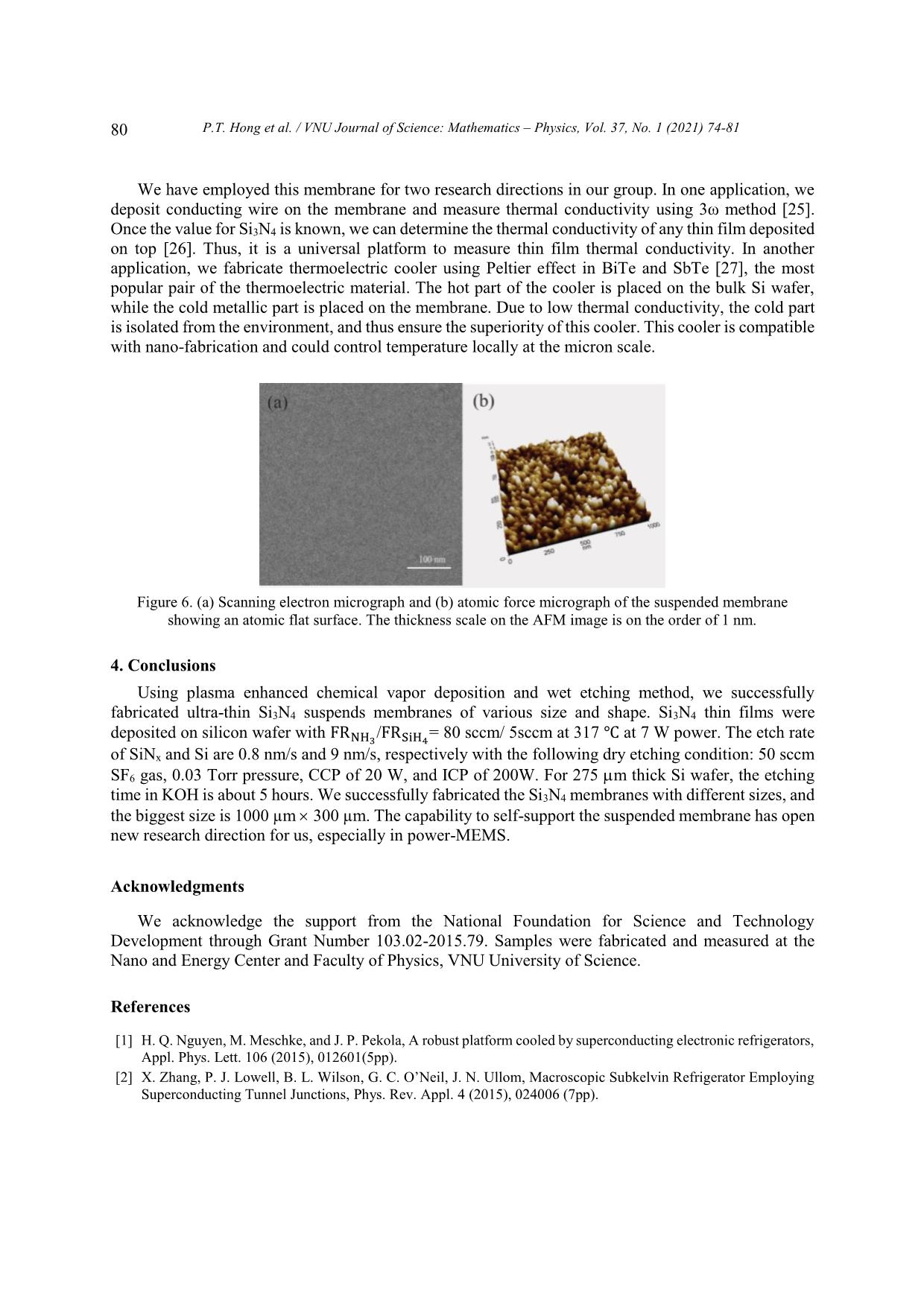
Trang 7
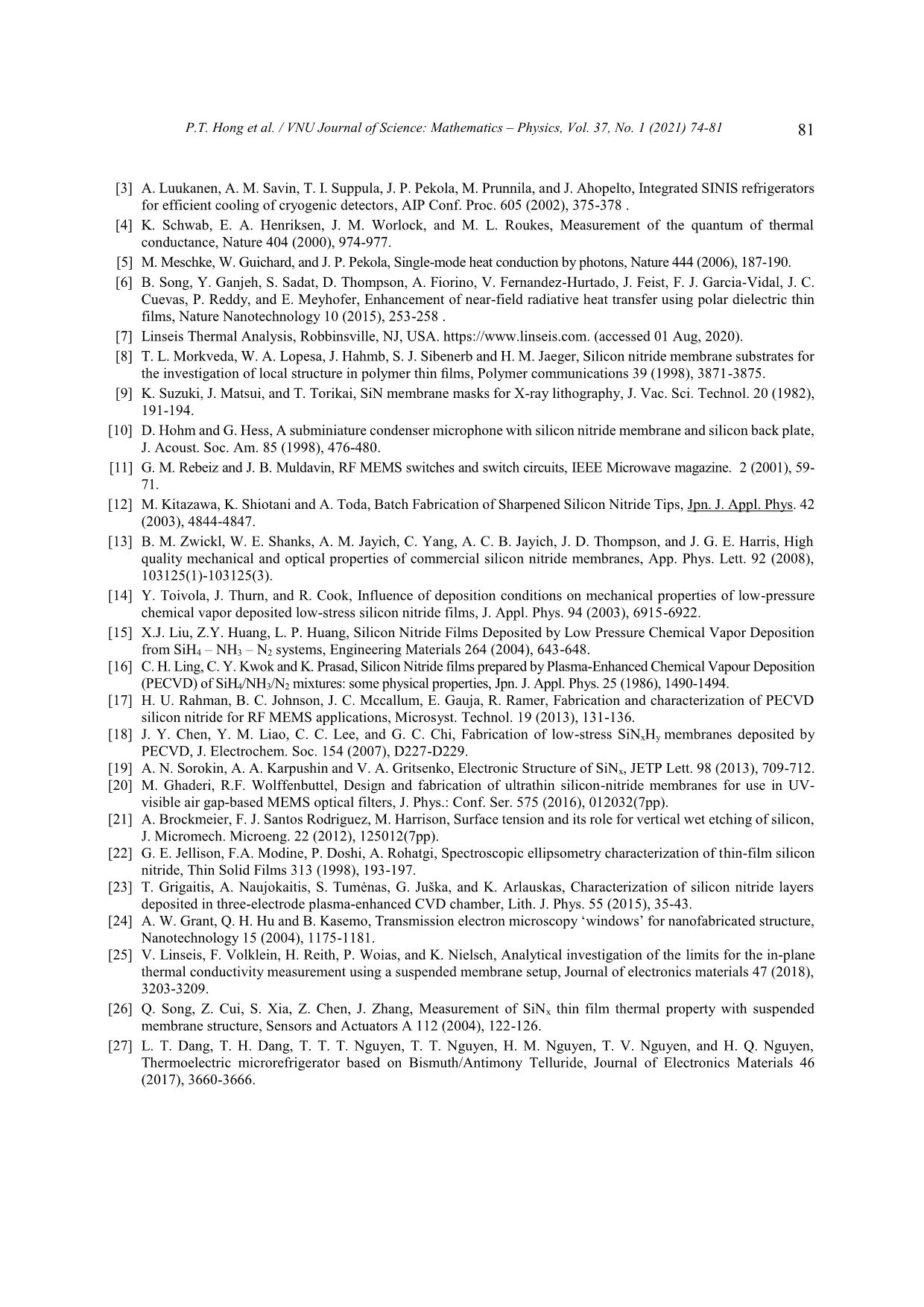
Trang 8
Tóm tắt nội dung tài liệu: Fabricating ultra - thin silicon nitride membranes suspended on silicon wafer
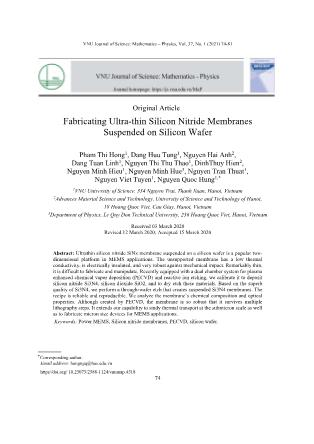
VNU Journal of Science: Mathematics – Physics, Vol. 37, No. 1 (2021) 74-81 Original Article Fabricating Ultra-thin Silicon Nitride Membranes Suspended on Silicon Wafer Pham Thi Hong1, Dang Huu Tung1, Nguyen Hai Anh2, Dang Tuan Linh1, Nguyen Thi Thu Thao1, DinhThuy Hien2, Nguyen Minh Hieu1, Nguyen Minh Hue3, Nguyen Tran Thuat1, Nguyen Viet Tuyen1, Nguyen Quoc Hung1,* 1VNU University of Science, 334 Nguyen Trai, Thanh Xuan, Hanoi, Vietnam 2Advances Material Science and Technology, University of Science and Technology of Hanoi, 18 Hoang Quoc Viet, Cau Giay, Hanoi, Vietnam 3Department of Physics, Le Quy Don Technical University, 236 Hoang Quoc Viet, Hanoi, Vietnam Received 03 March 2020 Revised 12 March 2020; Accepted 15 March 2020 Abstract: Ultrathin silicon nitride SiNx membrane suspended on a silicon wafer is a popular two- dimensional platform in MEMS applications. The unsupported membrane has a low thermal conductivity, is electrically insulated, and very robust against mechanical impact. Remarkably thin, it is difficult to fabricate and manipulate. Recently equipped with a dual chamber system for plasma enhanced chemical vapor deposition (PECVD) and reactive ion etching, we calibrate it to deposit silicon nitride Si3N4, silicon dioxide SiO2, and to dry etch these materials. Based on the superb quality of Si3N4, we perform a through-wafer etch that creates suspended Si3N4 membranes. The recipe is reliable and reproducible. We analyze the membrane’s chemical composition and optical properties. Although created by PECVD, the membrane is so robust that it survives multiple lithography steps. It extends our capability to study thermal transport at the submicron scale as well as to fabricate micron size devices for MEMS applications. Keywords: Power MEMS, Silicon nitride membranes, PECVD, silicon wafer. ________ Corresponding author. Email address: hungngq@hus.edu.vn https//doi.org/ 10.25073/2588-1124/vnumap.4518 74 P.T. Hong et al. / VNU Journal of Science: Mathematics – Physics, Vol. 37, No. 1 (2021) 74-81 75 1. Introduction Micro-Electro-Mechanical Systems (MEMS) often require qualities that a traditional silicon wafer can not meet. For example, in thermoelectric applications, the cold part of a micro-refrigerator should be isolated from the environment, while the hot part should stay thermalized with the surrounding. A platform that separates two regions of different thermal conductance is vital for the device performance [1-3]. Silicon nitride membranes have low stress, low thermal conductance, are electrically isolated, and thus, are an ideal platform for such applications. It is the best platform to study thermal transport at the submicron scale [4-7]. Not limited to micro-cooling applications, the membrane is transparent under the high energy electron beam and is widely used in the transmission electron microscopy community [8]. The same recipe to fabricate the membrane can also be employed to fabricate other structures [9], such as pressure sensors [10], RF switches [11], or atomic force microscope cantilevers [12]. Extremely fragile, only certain labs possess the capability to fabricate suspended membranes. There are two main challenges. First, the high aspect ratio: 100 nm thin and a millimeter square suspended area make it so fragile that the yield becomes very low, which requires a low-stress material. Second, through-wafer etching is a demanding process that needs a long etching time in corrosive chemical solutions. The deposited dielectric thin film should be strong enough to survive such a process. Among dielectric materials, Si3N4 is the traditional choice due to its high quality as a low-stress material [13] and its compatibility with nano-fabrication processes. Silicon nitride SiNx and silicon oxide SiOx are the two most important dielectric materials to use with silicon wafers. They can be used as passivation layers, isolating films, or piezoelectric materials, to name a few. They are mostly created from Chemical Vapor Deposition (CVD) method, with quality depends on the detail approaches: plasma enhanced CVD, low pressure CVD, hot wire CVD, or atomic layer deposition. Among these approaches, low pressure chemical vapor deposition (LPCVD) produces Si3N4 of high purity, low stress, and low price and can be used for mass production [14, 15]. However, it requires a high temperature and would destroy any pre-existed structure on the wafer. Depositing Si3N4 using LPCVD has to be the first step of the fabrication, which limits the popularity of the method. To lower such temperature barrier, the deposition in a plasma enhanced chemical vapor deposition (PECVD) machine occurs with the help of a plasma environment [16, 17]. The depositing temperature is often below 400 ℃ and is compatible with a wide range of processes. The lower temperature, however ... ded Membrane P.T. Hong et al. / VNU Journal of Science: Mathematics – Physics, Vol. 37, No. 1 (2021) 74-81 77 We use a solution of 20% KOH to etch Si at 80 ℃, which results in an etching rate of 1.8 µm/min [21]. To ensure anisotropy etching, 10% isopropyl alcohol IPA is added to the solution. Typically, it takes more than 5 hours to etch through the 275 µm thick wafer. In this paper, the etching apparatus is set up for a single chip of 1.5 x 1.5 cm2. A full wafer etching system is under construction. Figure 2. Fabrication process for Si3N4 membranes: (a) cleaned silicon wafer. (b) Depositing Si3N4 on both side of the chip. (c) Spin coating photoresist on both sides of the wafer. (d) Opening the etching window on the backside of the wafer using photolithography. (e) Dry etching Si3N4 in SF6 plasma. (f) Removing photoresist using acetone. (g) Wet etching in KOH solution. The recipe to fabricate the suspended Si3N4 wafer can be summarized as the diagram in Figure 2: first, the silicon wafer is diced into 1.5 1.5 cm chips, and dip in HF for 30 s. Si3N4 thin films are deposited on both sides with identical parameters. Because KOH etches photoresist, the back-side Si3N4 acts as a mask during this etching step. Photolithography patterns the backside of the chip with circles of 600 µm diameter. We then use reactive ion etching to open the SiNx windows from the backside. The chip is wet etched in KOH through this etching window until it is stopped by the top SiNx layer. Optical properties of the SiNx thin films are measured using a spectroscopic ellipsometer. This measurement indirectly measures through the ellipsometric angles. It is necessary to create a model for our sample to deduce the sample parameter like thickness and optical constant. We used amorphous model to fit our SiNx. Here, the refractive index n and the extinction coefficient k of the material are described by these following equations: 2 A(E − Eg) B .E + C E > E n(E) = 0 0 and k(E) = { E2− B.E + C g E2− B.E + C 0 E ≤ Eg Where: A B2 B = ( − + E . B − E2 + C) 0 Q 2 g g A B C = [(E2 + C). − 2.E .C] 0 B g 2 g 1 Q= .√4C − B2 2 Here, B0, C0, and Q are obtained from fitting parameters A, B, C. Eg is the band gap energy, A is a parameter depending on the dipole matrix squared and describe the strength of the extinction coefficient 2 2 peak. B = 2E0 and C = E0 + Γ0 are expressions of physical parameters. The experiment data must be fitted with the model of the sample before deducing the sample parameters [22]. This model allows us to calculate the band gap Eg of the SiNx thin films. We optimize the fabrication conditions for Si3N4 thin film based on this value. 78 P.T. Hong et al. / VNU Journal of Science: Mathematics – Physics, Vol. 37, No. 1 (2021) 74-81 3. Results and Discussion Figure 3. (a) The band gap of SiNx deposited at different 퐹푅 3/퐹푅푆푖 4 measured using spectroscopic ellipsometry. Si3N4 is obtained at 퐹푅 3/퐹푅푆푖 4=16. (b) Energy dispersive x-ray spectrum (EDS) of the sample showing Si and N component. Cu peaks are an artifact from the copper tape used to immobilized the sample. It is important to deposit SiNx with the correct ratio such that the stoichiometry is Si3N4, the most thermodynamically stable form. Our thin film’s band gap and its optical properties are obtained from fitting experimental ellipsometry spectra with models using the above-mentioned amorphous dispersion relation for the active layer. Figure 3 shows the dependence of the SiNx band gap on the flow rate ratio FRNH3/FRSiH4. The data with flow rate ratio from 0 to 9 is taken such that the flow rate of NH3 is kept constant at 80 sccm while the flow rate of SiH3 is changed from 10 sccm to 5 sccm. For flow rate ratio from 9 to 18, the flow rate of SiH4 is kept at 10 sccm, and the flow rate of NH3 is changed from 20 to 80 sccm. It is clear that the increase of FRNH3/FRSiH4 resulted in an increase of band gap of SiNx. From this result, SiNx deposited with FRNH3/FRSiH4= 80 sccm/ 5 sccm has band gap of 4.394 eV, the closest to the band gap of Si3N4 [23]. This result is reconfirmed with an energy dispersive X-ray spectroscopy measurement EDS (data not shown). The etching rate of Si3N4 using ICP RIE is an important parameter. Figure 4 shows the dependence of the depth of the wells as measured from the profilometer on RIE etching time. The SF6 plasma first etches the Si3N4 film. Upon completion, Si etching continues. These rates of the two processes are corresponding to two slopes in Figure 4. The etching rate of SiNx is 0.8 nm/s and the etching rate of Si is 9 nm/s with 50 sccm SF6 gas, 0.3 Torr pressure, capacitive coupled plasma power of 20 W, and inductive coupled plasma power of 200 W. With a proper Si3N4 thin film and a correct etching rate, we fabricate the suspended Si3N4 membrane. Figure 5 shows optical images for some of our Si3N4 membranes. Miller indices create the plane in a silicon crystal as {100} correspond to the front view, {110} to edge view, {111} to vertex view. In the wet etching with KOH corrode silicon in {100} direction much faster than {111} direction as in the diagram shown in figure 5 (a). Wet etching in KOH is well-executed that selective rate at different crystal orientation is clearly demonstrated. The tilt angle as seen from the back side in Figure 5c is an exact 54.7 degree, agree with previous literature [24]. Furthermore, a circular photolithographic mask results in an octagonal shape in Figure 5b. P.T. Hong et al. / VNU Journal of Science: Mathematics – Physics, Vol. 37, No. 1 (2021) 74-81 79 Figure 4. The dependence of the Si3N4 well depth on RIE etching time. The Si wafer is etched at a much faster rate upon the completion of the Si3N4 layer. Here, the plasma power is 20 W at pressure 0.03 Torr and the SF6 gas flow is 50 sccm. Figure 5. (a) Cross section diagram of the suspended Si3N4 membranes. The thickness of Si3N4 is 100 nm, while Si wafer is 275 µm, (b) Top view of the Si3N4 membrane prepared with round photolithography mask, (c) Bottom view of Si3N4 membranes after wet etching by KOH 20% solution, (d) and (e) ultra large membrane of different rectangle sizes. In this work, we produce membranes of three sizes: 1000 µm 300 µm, 600 µm 300 µm and 200 µm 200 µm. To account for the etching angle, the photographic mask dimensions are 1400 µm 700 µm, 1000 µm 700 µm, 600 µm 600 µm, respectively. The yield is listed in Table 1. Apparently, the larger the windows size, the lower the yield. It is worthwhile to note that a window’s size of 1 mm is a macroscopic scale that only required in special applications. To have a higher yield, it is better to fabricate membranes with a size less than 100 µm. The silicon nitride membranes have an atomically flat surface as shown by the scanning electron - micrograph and atomic force micrograph in figure 6. Clearly, Si3N4 thin films are not corroded by OH ion during the wet etching process. The membrane is compatible with other nano fabrication process. Together with the low thermal conductivity and mechanical durability, it is an ideal platform for a wide range of applications. Table 1. A list of membranes fabricated in this work. The Si substrate is 275 µm thick. The Si3N4 membrane is 100 nm thick. Shape Dimension Figure Number of membrane made Yield Octagonal 177.8 µm 177.8 µm 5b 14 51.9 % Rectangle 282 µm 590 µm 5d 3 50 % Rectangle 284.3 µm 977 µm 5e 1 16.7 % 80 P.T. Hong et al. / VNU Journal of Science: Mathematics – Physics, Vol. 37, No. 1 (2021) 74-81 We have employed this membrane for two research directions in our group. In one application, we deposit conducting wire on the membrane and measure thermal conductivity using 3ω method [25]. Once the value for Si3N4 is known, we can determine the thermal conductivity of any thin film deposited on top [26]. Thus, it is a universal platform to measure thin film thermal conductivity. In another application, we fabricate thermoelectric cooler using Peltier effect in BiTe and SbTe [27], the most popular pair of the thermoelectric material. The hot part of the cooler is placed on the bulk Si wafer, while the cold metallic part is placed on the membrane. Due to low thermal conductivity, the cold part is isolated from the environment, and thus ensure the superiority of this cooler. This cooler is compatible with nano-fabrication and could control temperature locally at the micron scale. Figure 6. (a) Scanning electron micrograph and (b) atomic force micrograph of the suspended membrane showing an atomic flat surface. The thickness scale on the AFM image is on the order of 1 nm. 4. Conclusions Using plasma enhanced chemical vapor deposition and wet etching method, we successfully fabricated ultra-thin Si3N4 suspends membranes of various size and shape. Si3N4 thin films were deposited on silicon wafer with FRNH3/FRSiH4= 80 sccm/ 5sccm at 317 ℃ at 7 W power. The etch rate of SiNx and Si are 0.8 nm/s and 9 nm/s, respectively with the following dry etching condition: 50 sccm SF6 gas, 0.03 Torr pressure, CCP of 20 W, and ICP of 200W. For 275 m thick Si wafer, the etching time in KOH is about 5 hours. We successfully fabricated the Si3N4 membranes with different sizes, and the biggest size is 1000 µm 300 µm. The capability to self-support the suspended membrane has open new research direction for us, especially in power-MEMS. Acknowledgments We acknowledge the support from the National Foundation for Science and Technology Development through Grant Number 103.02-2015.79. Samples were fabricated and measured at the Nano and Energy Center and Faculty of Physics, VNU University of Science. References [1] H. Q. Nguyen, M. Meschke, and J. P. Pekola, A robust platform cooled by superconducting electronic refrigerators, Appl. Phys. Lett. 106 (2015), 012601(5pp). [2] X. Zhang, P. J. Lowell, B. L. Wilson, G. C. O’Neil, J. N. Ullom, Macroscopic Subkelvin Refrigerator Employing Superconducting Tunnel Junctions, Phys. Rev. Appl. 4 (2015), 024006 (7pp). P.T. Hong et al. / VNU Journal of Science: Mathematics – Physics, Vol. 37, No. 1 (2021) 74-81 81 [3] A. Luukanen, A. M. Savin, T. I. Suppula, J. P. Pekola, M. Prunnila, and J. Ahopelto, Integrated SINIS refrigerators for efficient cooling of cryogenic detectors, AIP Conf. Proc. 605 (2002), 375-378 . [4] K. Schwab, E. A. Henriksen, J. M. Worlock, and M. L. Roukes, Measurement of the quantum of thermal conductance, Nature 404 (2000), 974-977. [5] M. Meschke, W. Guichard, and J. P. Pekola, Single-mode heat conduction by photons, Nature 444 (2006), 187-190. [6] B. Song, Y. Ganjeh, S. Sadat, D. Thompson, A. Fiorino, V. Fernandez-Hurtado, J. Feist, F. J. Garcia-Vidal, J. C. Cuevas, P. Reddy, and E. Meyhofer, Enhancement of near-field radiative heat transfer using polar dielectric thin films, Nature Nanotechnology 10 (2015), 253-258 . [7] Linseis Thermal Analysis, Robbinsville, NJ, USA. https://www.linseis.com. (accessed 01 Aug, 2020). [8] T. L. Morkveda, W. A. Lopesa, J. Hahmb, S. J. Sibenerb and H. M. Jaeger, Silicon nitride membrane substrates for the investigation of local structure in polymer thin films, Polymer communications 39 (1998), 3871-3875. [9] K. Suzuki, J. Matsui, and T. Torikai, SiN membrane masks for X-ray lithography, J. Vac. Sci. Technol. 20 (1982), 191-194. [10] D. Hohm and G. Hess, A subminiature condenser microphone with silicon nitride membrane and silicon back plate, J. Acoust. Soc. Am. 85 (1998), 476-480. [11] G. M. Rebeiz and J. B. Muldavin, RF MEMS switches and switch circuits, IEEE Microwave magazine. 2 (2001), 59- 71. [12] M. Kitazawa, K. Shiotani and A. Toda, Batch Fabrication of Sharpened Silicon Nitride Tips, Jpn. J. Appl. Phys. 42 (2003), 4844-4847. [13] B. M. Zwickl, W. E. Shanks, A. M. Jayich, C. Yang, A. C. B. Jayich, J. D. Thompson, and J. G. E. Harris, High quality mechanical and optical properties of commercial silicon nitride membranes, App. Phys. Lett. 92 (2008), 103125(1)-103125(3). [14] Y. Toivola, J. Thurn, and R. Cook, Influence of deposition conditions on mechanical properties of low-pressure chemical vapor deposited low-stress silicon nitride films, J. Appl. Phys. 94 (2003), 6915-6922. [15] X.J. Liu, Z.Y. Huang, L. P. Huang, Silicon Nitride Films Deposited by Low Pressure Chemical Vapor Deposition from SiH4 – NH3 – N2 systems, Engineering Materials 264 (2004), 643-648. [16] C. H. Ling, C. Y. Kwok and K. Prasad, Silicon Nitride films prepared by Plasma-Enhanced Chemical Vapour Deposition (PECVD) of SiH4/NH3/N2 mixtures: some physical properties, Jpn. J. Appl. Phys. 25 (1986), 1490-1494. [17] H. U. Rahman, B. C. Johnson, J. C. Mccallum, E. Gauja, R. Ramer, Fabrication and characterization of PECVD silicon nitride for RF MEMS applications, Microsyst. Technol. 19 (2013), 131-136. [18] J. Y. Chen, Y. M. Liao, C. C. Lee, and G. C. Chi, Fabrication of low-stress SiNxHy membranes deposited by PECVD, J. Electrochem. Soc. 154 (2007), D227-D229. [19] A. N. Sorokin, A. A. Karpushin and V. A. Gritsenko, Electronic Structure of SiNx, JETP Lett. 98 (2013), 709-712. [20] M. Ghaderi, R.F. Wolffenbuttel, Design and fabrication of ultrathin silicon-nitride membranes for use in UV- visible air gap-based MEMS optical filters, J. Phys.: Conf. Ser. 575 (2016), 012032(7pp). [21] A. Brockmeier, F. J. Santos Rodriguez, M. Harrison, Surface tension and its role for vertical wet etching of silicon, J. Micromech. Microeng. 22 (2012), 125012(7pp). [22] G. E. Jellison, F.A. Modine, P. Doshi, A. Rohatgi, Spectroscopic ellipsometry characterization of thin-film silicon nitride, Thin Solid Films 313 (1998), 193-197. [23] T. Grigaitis, A. Naujokaitis, S. Tumėnas, G. Juška, and K. Arlauskas, Characterization of silicon nitride layers deposited in three-electrode plasma-enhanced CVD chamber, Lith. J. Phys. 55 (2015), 35-43. [24] A. W. Grant, Q. H. Hu and B. Kasemo, Transmission electron microscopy ‘windows’ for nanofabricated structure, Nanotechnology 15 (2004), 1175-1181. [25] V. Linseis, F. Volklein, H. Reith, P. Woias, and K. Nielsch, Analytical investigation of the limits for the in-plane thermal conductivity measurement using a suspended membrane setup, Journal of electronics materials 47 (2018), 3203-3209. [26] Q. Song, Z. Cui, S. Xia, Z. Chen, J. Zhang, Measurement of SiNx thin film thermal property with suspended membrane structure, Sensors and Actuators A 112 (2004), 122-126. [27] L. T. Dang, T. H. Dang, T. T. T. Nguyen, T. T. Nguyen, H. M. Nguyen, T. V. Nguyen, and H. Q. Nguyen, Thermoelectric microrefrigerator based on Bismuth/Antimony Telluride, Journal of Electronics Materials 46 (2017), 3660-3666.
File đính kèm:
fabricating_ultra_thin_silicon_nitride_membranes_suspended_o.pdf