Effect of seams on drape behaviour of cotton woven fabrics
Drape of fabric is one of the characteristics which influence significantly on the appearance
quality of clothes. The structure of patterns and seams affect the drape behaviour of fabric. Investigating
of the influence of seams to the drape behaviour of the fabric can improve apparel design and the
selection of the structure, the direction of seams in accordance with the requirements of aesthetic quality
as well as the shape of the garment. This article presents the effect of three seams on the drape behaviour
of five medium cotton woven fabrics. Experimental fabrics are given diametral seams. Warp, weft and 45o
bias seams were sewn. Three types of seams, which content 301, 401 and 504 stitches, were applied to
observe the effect of seams on the drape of fabrics. Drape properties of initial and seamed fabrics were
determined using ADS-LAST drapemeter according to BS 5058: 1973 standard. The experimental results
indicate that drape profile and number of folds are changed while changing type and direction of seams.
There is a significant proportional linear correlation between drape coefficients of seamed and initial
fabrics.
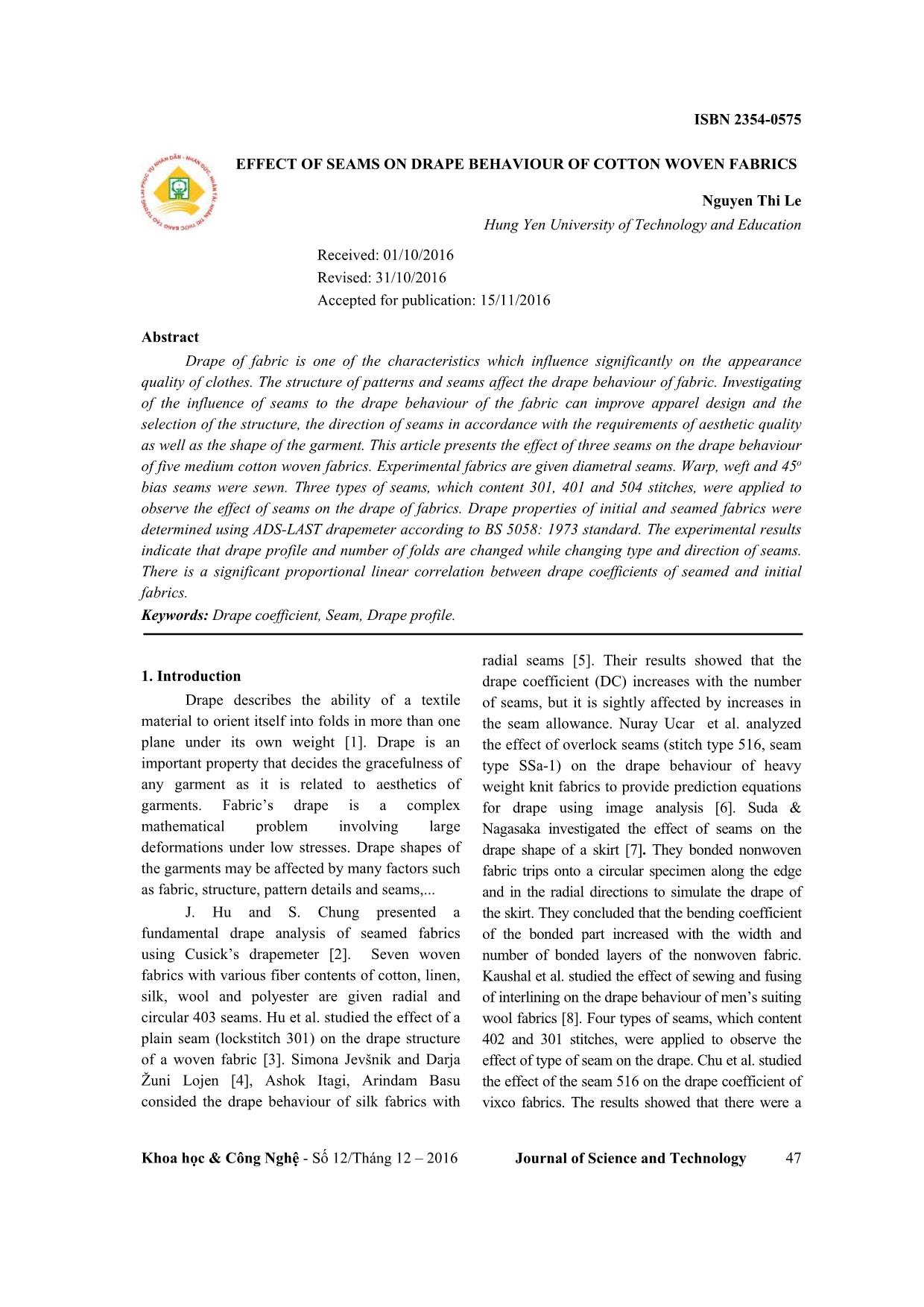
Trang 1
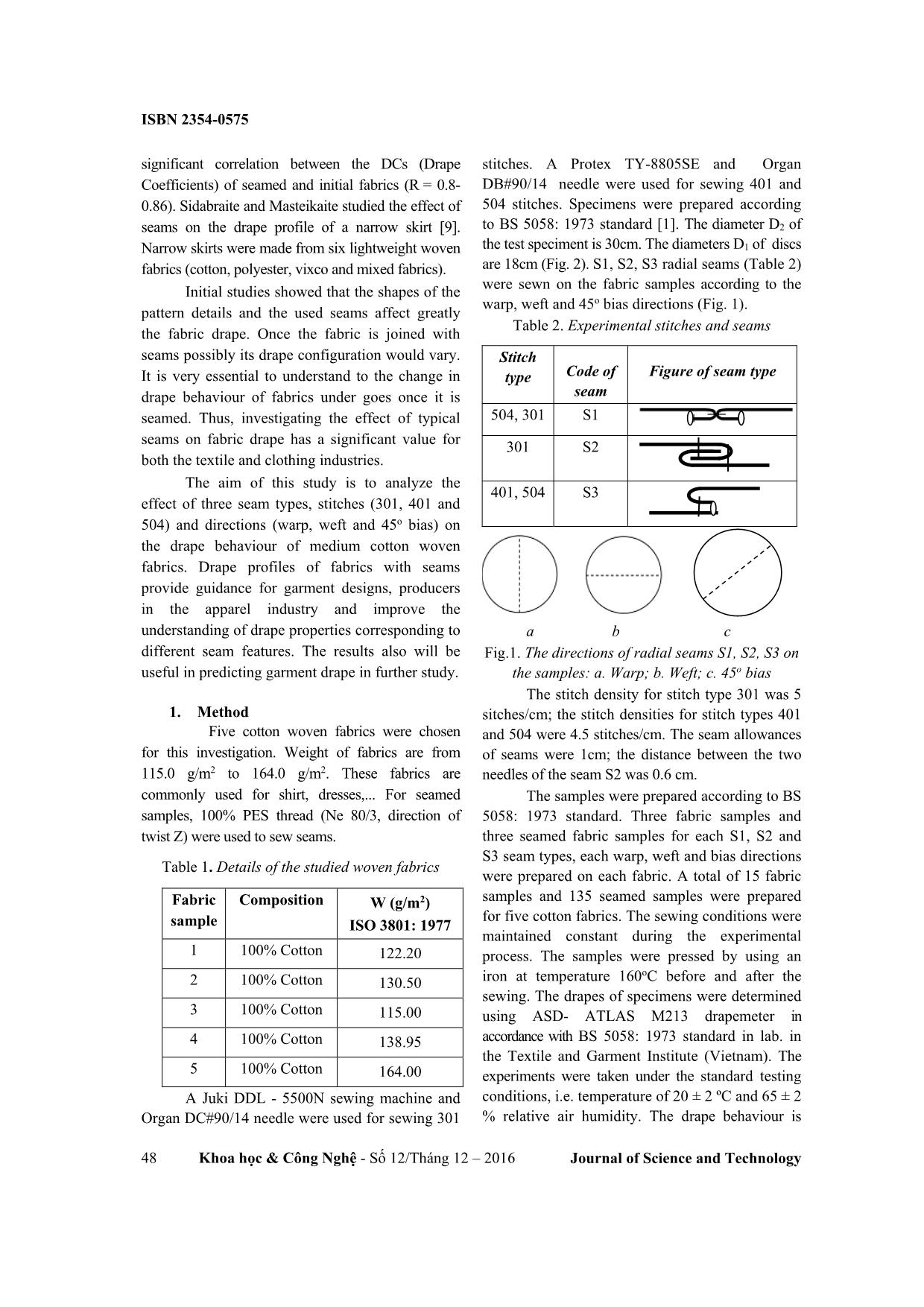
Trang 2
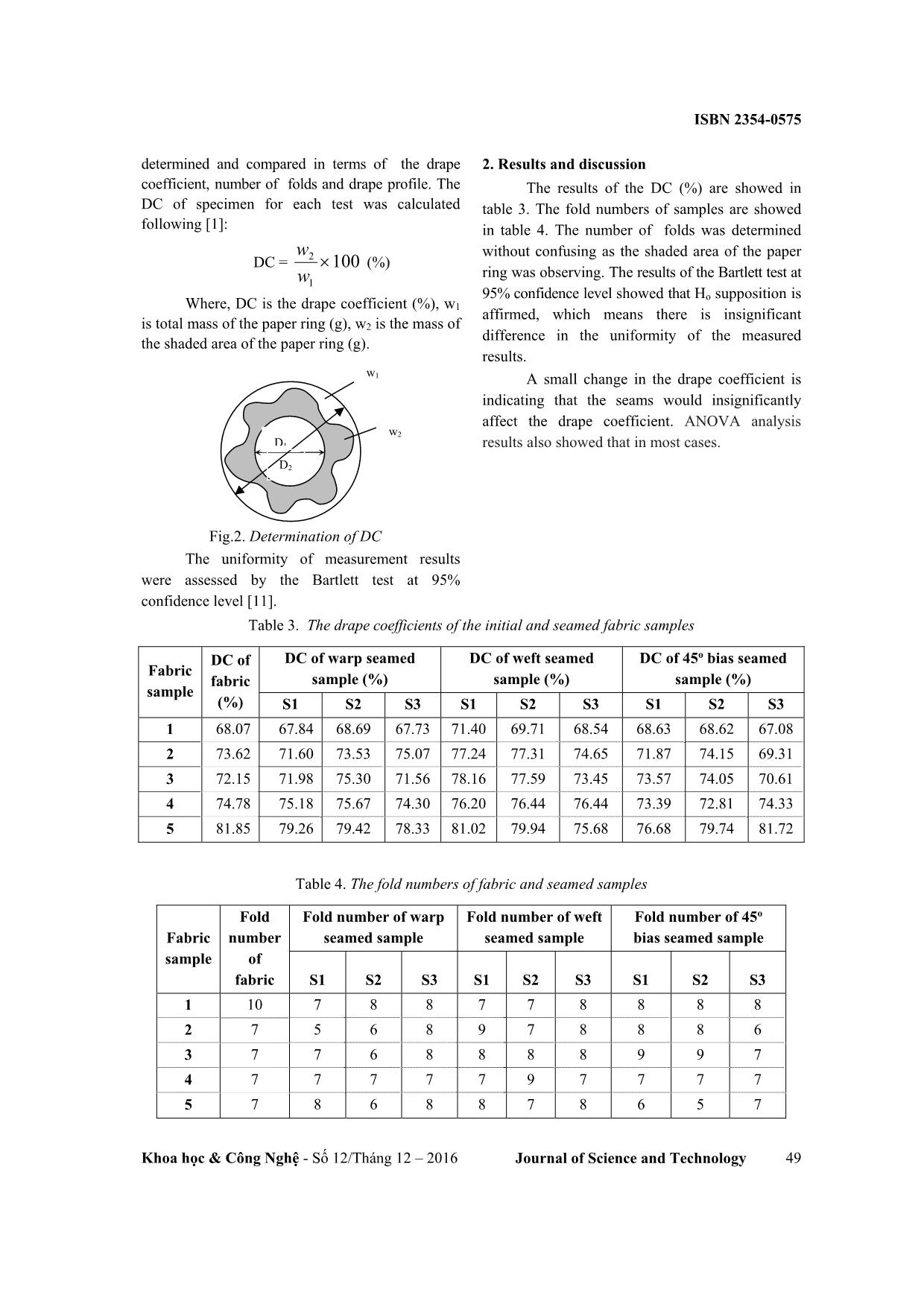
Trang 3
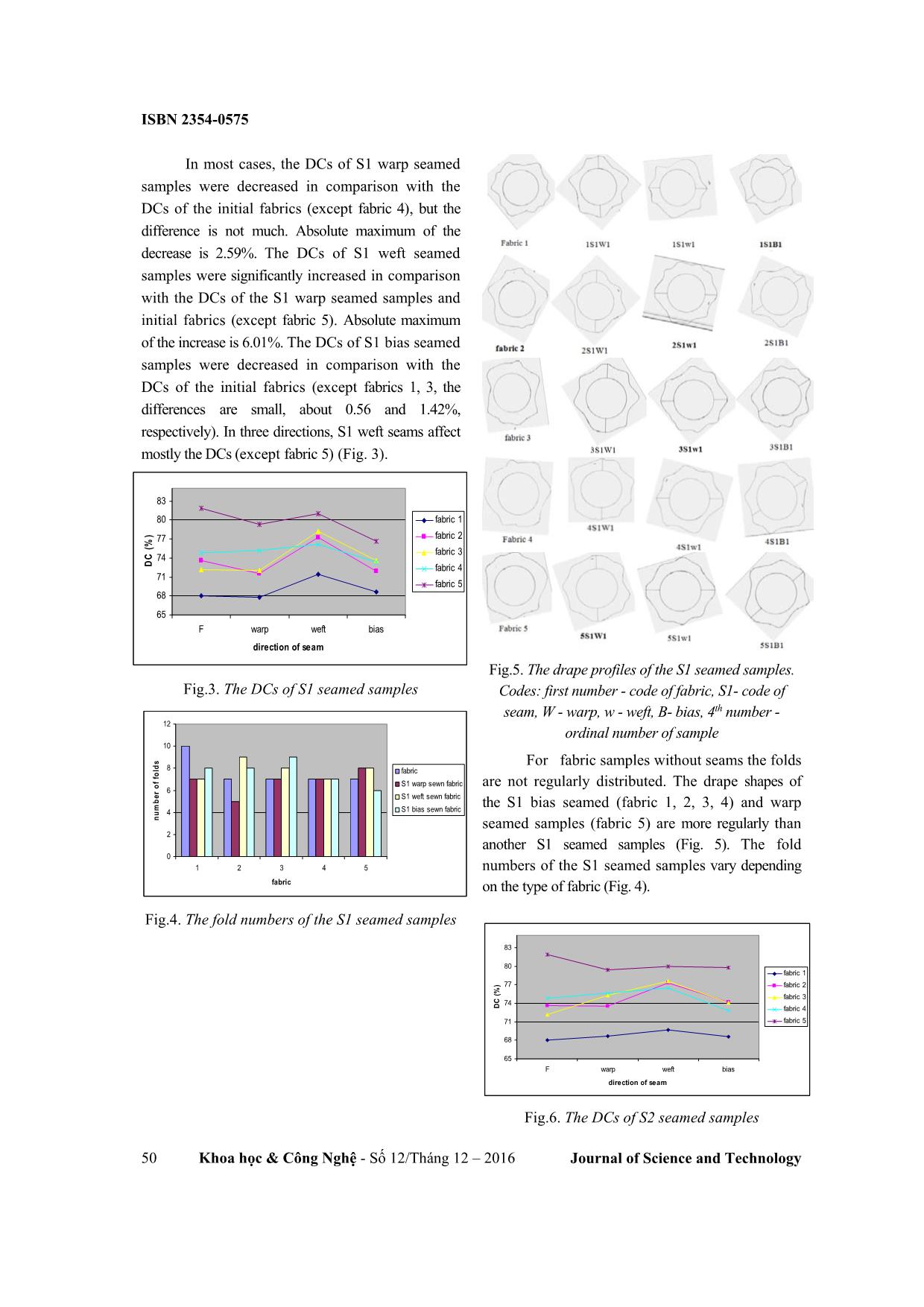
Trang 4
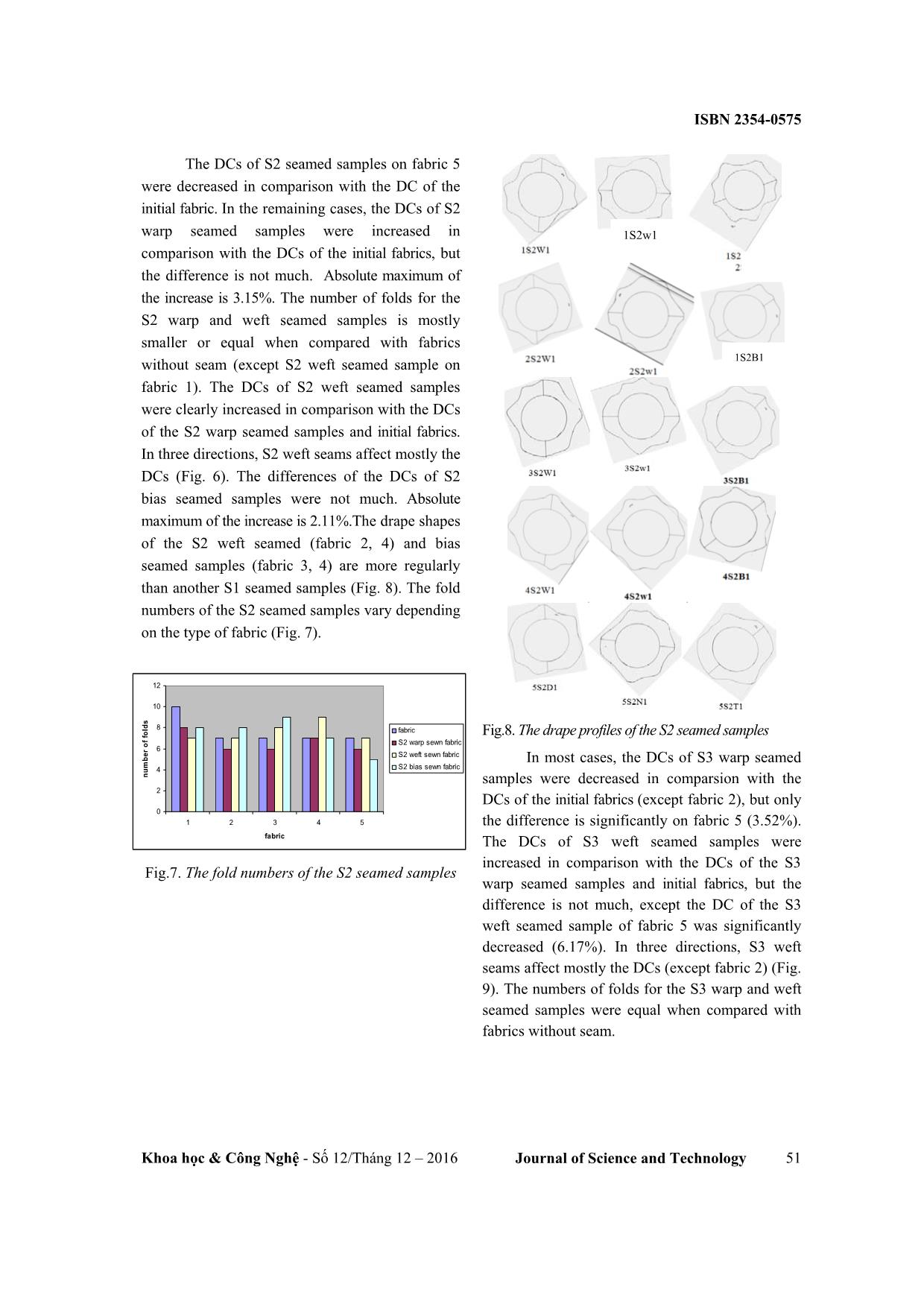
Trang 5
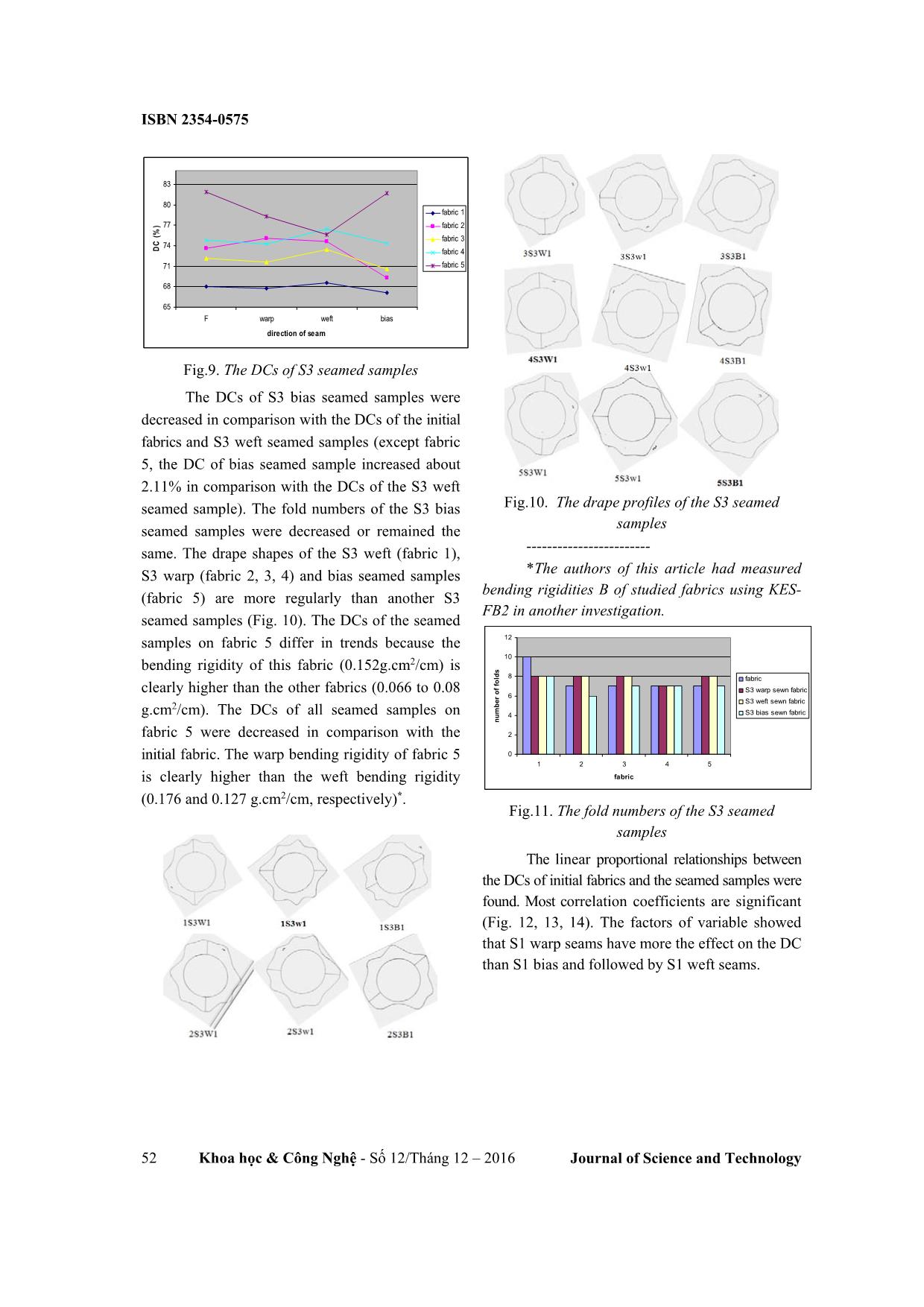
Trang 6
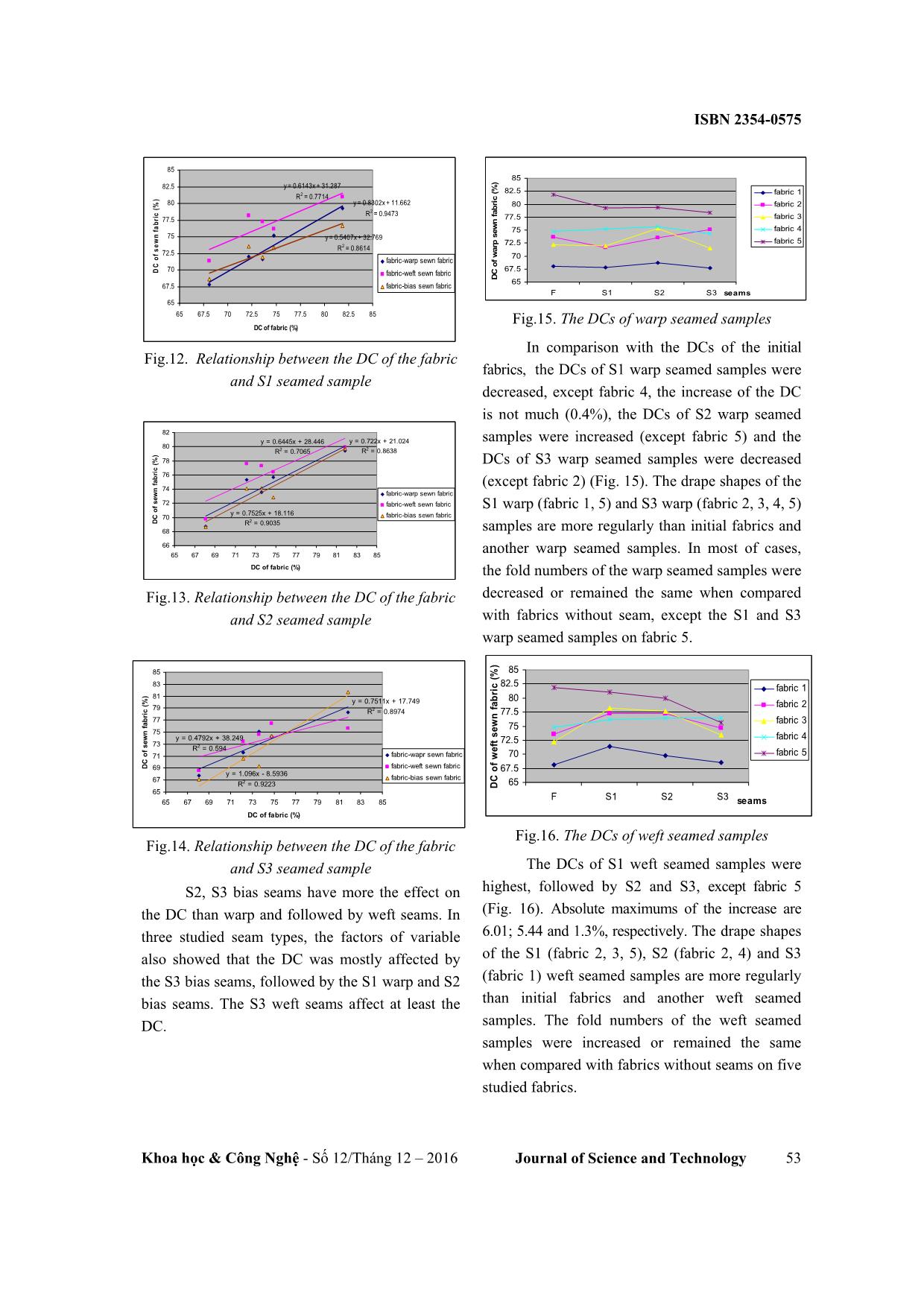
Trang 7
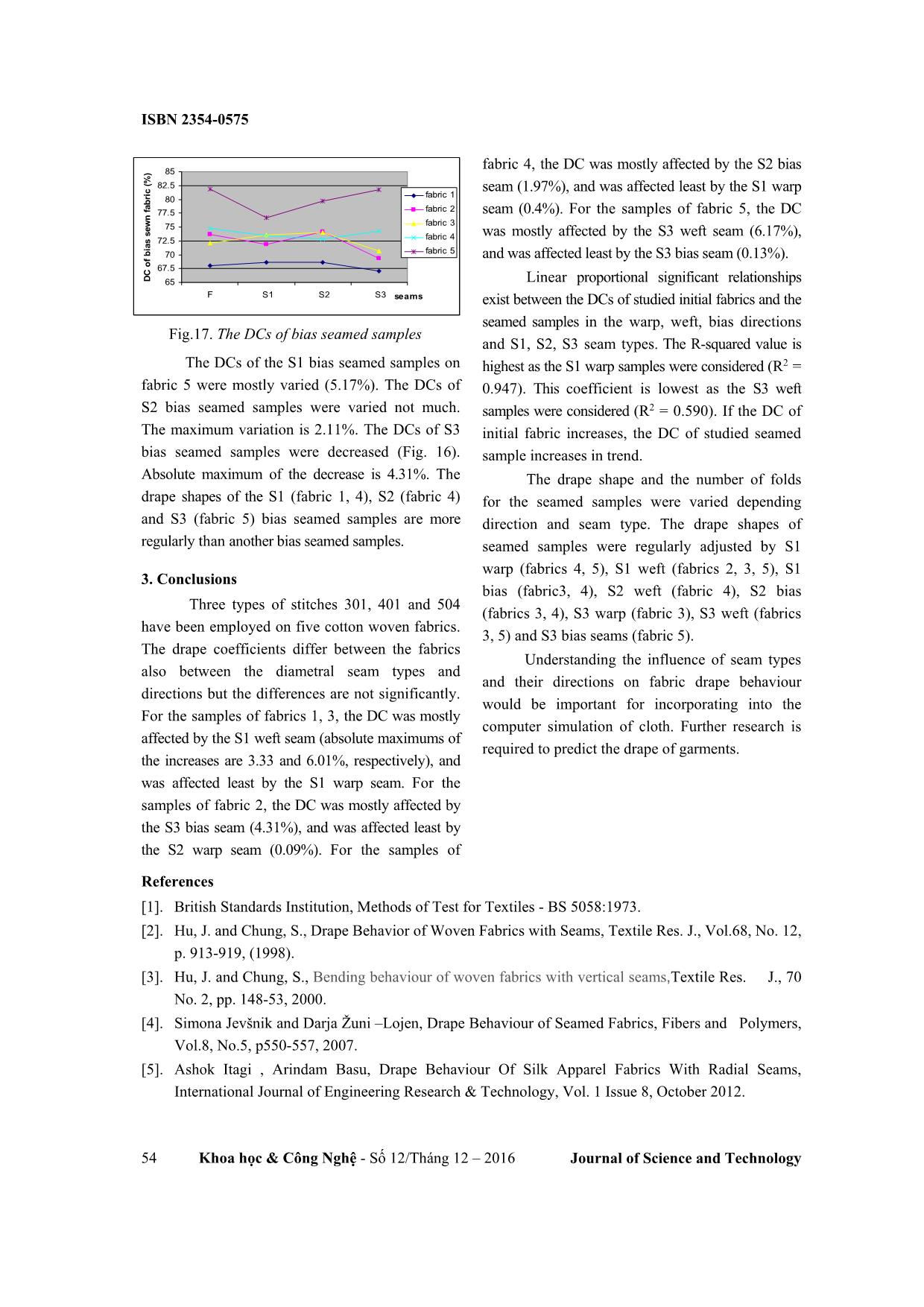
Trang 8
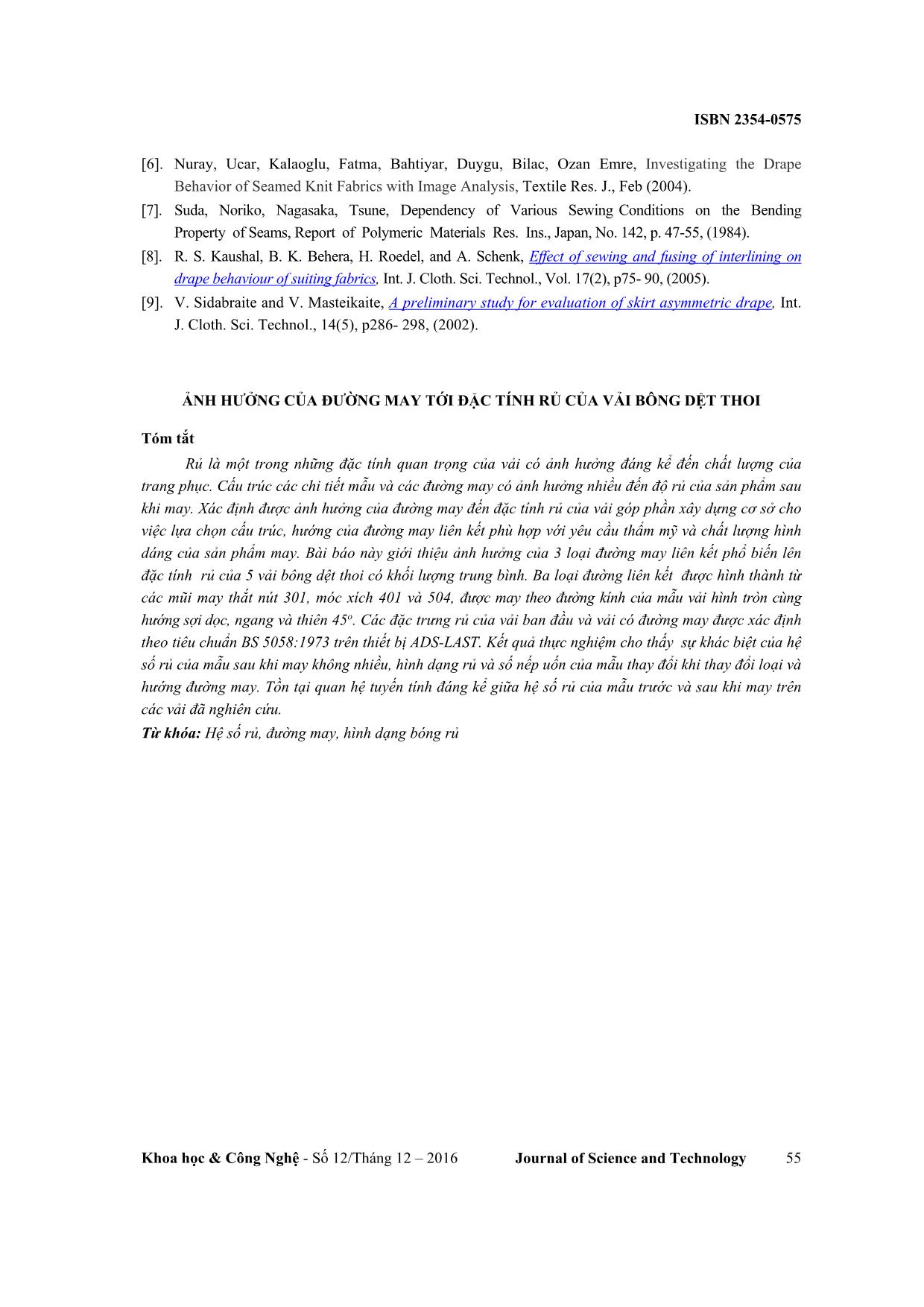
Trang 9
Tóm tắt nội dung tài liệu: Effect of seams on drape behaviour of cotton woven fabrics
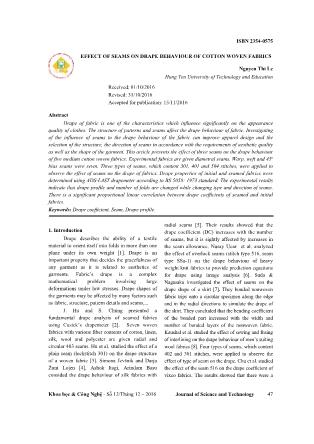
ISBN 2354-0575 EFFECT OF SEAMS ON DRAPE BEHAVIOUR OF COTTON WOVEN FABRICS Nguyen Thi Le Hung Yen University of Technology and Education Received: 01/10/2016 Revised: 31/10/2016 Accepted for publication: 15/11/2016 Abstract Drape of fabric is one of the characteristics which influence significantly on the appearance quality of clothes. The structure of patterns and seams affect the drape behaviour of fabric. Investigating of the influence of seams to the drape behaviour of the fabric can improve apparel design and the selection of the structure, the direction of seams in accordance with the requirements of aesthetic quality as well as the shape of the garment. This article presents the effect of three seams on the drape behaviour of five medium cotton woven fabrics. Experimental fabrics are given diametral seams. Warp, weft and 45o bias seams were sewn. Three types of seams, which content 301, 401 and 504 stitches, were applied to observe the effect of seams on the drape of fabrics. Drape properties of initial and seamed fabrics were determined using ADS-LAST drapemeter according to BS 5058: 1973 standard. The experimental results indicate that drape profile and number of folds are changed while changing type and direction of seams. There is a significant proportional linear correlation between drape coefficients of seamed and initial fabrics. Keywords: Drape coefficient, Seam, Drape profile. radial seams [5]. Their results showed that the 1. Introduction drape coefficient (DC) increases with the number Drape describes the ability of a textile of seams, but it is sightly affected by increases in material to orient itself into folds in more than one the seam allowance. Nuray Ucar et al. analyzed plane under its own weight [1]. Drape is an the effect of overlock seams (stitch type 516, seam important property that decides the gracefulness of type SSa-1) on the drape behaviour of heavy any garment as it is related to aesthetics of weight knit fabrics to provide prediction equations garments. Fabric’s drape is a complex for drape using image analysis [6]. Suda & mathematical problem involving large Nagasaka investigated the effect of seams on the deformations under low stresses. Drape shapes of drape shape of a skirt [7]. They bonded nonwoven the garments may be affected by many factors such fabric trips onto a circular specimen along the edge as fabric, structure, pattern details and seams,... and in the radial directions to simulate the drape of J. Hu and S. Chung presented a the skirt. They concluded that the bending coefficient fundamental drape analysis of seamed fabrics of the bonded part increased with the width and using Cusick’s drapemeter [2]. Seven woven number of bonded layers of the nonwoven fabric. fabrics with various fiber contents of cotton, linen, Kaushal et al. studied the effect of sewing and fusing silk, wool and polyester are given radial and of interlining on the drape behaviour of men’s suiting circular 403 seams. Hu et al. studied the effect of a wool fabrics [8]. Four types of seams, which content plain seam (lockstitch 301) on the drape structure 402 and 301 stitches, were applied to observe the of a woven fabric [3]. Simona Jevšnik and Darja effect of type of seam on the drape. Chu et al. studied Žuni Lojen [4], Ashok Itagi, Arindam Basu the effect of the seam 516 on the drape coefficient of consided the drape behaviour of silk fabrics with vixco fabrics. The results showed that there were a Khoa học & Công Nghệ - Số 12/Tháng 12 – 2016 Journal of Science and Technology 47 ISBN 2354-0575 significant correlation between the DCs (Drape stitches. A Protex TY-8805SE and Organ Coefficients) of seamed and initial fabrics (R = 0.8- DB#90/14 needle were used for sewing 401 and 0.86). Sidabraite and Masteikaite studied the effect of 504 stitches. Specimens were prepared according seams on the drape profile of a narrow skirt [9]. to BS 5058: 1973 standard [1]. The diameter D2 of Narrow skirts were made from six lightweight woven the test speciment is 30cm. The diameters D1 of discs fabrics (cotton, polyester, vixco and mixed fabrics). are 18cm (Fig. 2). S1, S2, S3 radial seams (Table 2) were sewn on the fabric samples according to the Initial studies showed that the shapes of the warp, weft and 45o bias directions (Fig. 1). pattern details and the used seams affect greatly Table 2. Experimental stitches and seams the fabric drape. Once the fabric is joined with seams possibly its drape configuration would vary. Stitch It is very essential to understand to the change in type Code of Figure of seam type drape behaviour of fabrics under goes once it is seam seamed. Thus, investigating the effect of typical 504, 301 S1 seams on fabric drape has a significant value for 301 S2 both the textile and clothing industries. The aim of this study is to analyze the ... 5.68 76.68 79.74 81.72 Table 4. The fold numbers of fabric and seamed samples Fold Fold number of warp Fold number of weft Fold number of 45o Fabric number seamed sample seamed sample bias seamed sample sample of fabric S1 S2 S3 S1 S2 S3 S1 S2 S3 1 10 7 8 8 7 7 8 8 8 8 2 7 5 6 8 9 7 8 8 8 6 3 7 7 6 8 8 8 8 9 9 7 4 7 7 7 7 7 9 7 7 7 7 5 7 8 6 8 8 7 8 6 5 7 Khoa học & Công Nghệ - Số 12/Tháng 12 – 2016 Journal of Science and Technology 49 ISBN 2354-0575 In most cases, the DCs of S1 warp seamed samples were decreased in comparison with the DCs of the initial fabrics (except fabric 4), but the difference is not much. Absolute maximum of the decrease is 2.59%. The DCs of S1 weft seamed samples were significantly increased in comparison with the DCs of the S1 warp seamed samples and initial fabrics (except fabric 5). Absolute maximum of the increase is 6.01%. The DCs of S1 bias seamed samples were decreased in comparison with the DCs of the initial fabrics (except fabrics 1, 3, the differences are small, about 0.56 and 1.42%, respectively). In three directions, S1 weft seams affect mostly the DCs (except fabric 5) (Fig. 3). 83 80 fabric 1 77 fabric 2 fabric 3 74 DC (%) fabric 4 71 fabric 5 68 65 F warp weft bias direction of seam Fig.5. The drape profiles of the S1 seamed samples. Fig.3. The DCs of S1 seamed samples Codes: first number - code of fabric, S1- code of seam, W - warp, w - weft, B- bias, 4th number - 12 ordinal number of sample 10 For fabric samples without seams the folds 8 fabric S1 warp sewn fabric are not regularly distributed. The drape shapes of 6 S1 weft sewn fabric the S1 bias seamed (fabric 1, 2, 3, 4) and warp 4 S1 bias sewn fabric number of folds number of seamed samples (fabric 5) are more regularly than 2 another S1 seamed samples (Fig. 5). The fold 0 12345 numbers of the S1 seamed samples vary depending fabric on the type of fabric (Fig. 4). Fig.4. The fold numbers of the S1 seamed samples 83 80 fabric 1 77 fabric 2 fabric 3 74 DC (%) fabric 4 71 fabric 5 68 65 F warp weft bias direction of seam Fig.6. The DCs of S2 seamed samples 50 Khoa học & Công Nghệ - Số 12/Tháng 12 – 2016 Journal of Science and Technology ISBN 2354-0575 The DCs of S2 seamed samples on fabric 5 were decreased in comparison with the DC of the initial fabric. In the remaining cases, the DCs of S2 warp seamed samples were increased in 1S2w1 comparison with the DCs of the initial fabrics, but the difference is not much. Absolute maximum of the increase is 3.15%. The number of folds for the S2 warp and weft seamed samples is mostly smaller or equal when compared with fabrics without seam (except S2 weft seamed sample on 1S2B1 fabric 1). The DCs of S2 weft seamed samples were clearly increased in comparison with the DCs of the S2 warp seamed samples and initial fabrics. In three directions, S2 weft seams affect mostly the DCs (Fig. 6). The differences of the DCs of S2 bias seamed samples were not much. Absolute maximum of the increase is 2.11%.The drape shapes of the S2 weft seamed (fabric 2, 4) and bias seamed samples (fabric 3, 4) are more regularly than another S1 seamed samples (Fig. 8). The fold numbers of the S2 seamed samples vary depending on the type of fabric (Fig. 7). 12 10 8 fabric Fig.8. The drape profiles of the S2 seamed samples S2 warp sewn fabric 6 S2 weft sewn fabric In most cases, the DCs of S3 warp seamed 4 S2 bias sewn fabric number of folds of number samples were decreased in comparsion with the 2 DCs of the initial fabrics (except fabric 2), but only 0 12345 the difference is significantly on fabric 5 (3.52%). fabric The DCs of S3 weft seamed samples were increased in comparison with the DCs of the S3 Fig.7. The fold numbers of the S2 seamed samples warp seamed samples and initial fabrics, but the difference is not much, except the DC of the S3 weft seamed sample of fabric 5 was significantly decreased (6.17%). In three directions, S3 weft seams affect mostly the DCs (except fabric 2) (Fig. 9). The numbers of folds for the S3 warp and weft seamed samples were equal when compared with fabrics without seam. Khoa học & Công Nghệ - Số 12/Tháng 12 – 2016 Journal of Science and Technology 51 ISBN 2354-0575 83 80 fabric 1 77 fabric 2 fabric 3 74 DC (%) fabric 4 71 fabric 5 68 65 Fwarpweftbias direction of seam Fig.9. The DCs of S3 seamed samples The DCs of S3 bias seamed samples were decreased in comparison with the DCs of the initial fabrics and S3 weft seamed samples (except fabric 5, the DC of bias seamed sample increased about 2.11% in comparison with the DCs of the S3 weft seamed sample). The fold numbers of the S3 bias Fig.10. The drape profiles of the S3 seamed samples seamed samples were decreased or remained the same. The drape shapes of the S3 weft (fabric 1), ------------------------ S3 warp (fabric 2, 3, 4) and bias seamed samples *The authors of this article had measured bending rigidities B of studied fabrics using KES- (fabric 5) are more regularly than another S3 FB2 in another investigation. seamed samples (Fig. 10). The DCs of the seamed samples on fabric 5 differ in trends because the 12 10 bending rigidity of this fabric (0.152g.cm2/cm) is 8 fabric clearly higher than the other fabrics (0.066 to 0.08 S3 warp sewn fabric 6 2 S3 weft sewn fabric g.cm /cm). The DCs of all seamed samples on 4 S3 bias sewn fabric number of folds number of fabric 5 were decreased in comparison with the 2 initial fabric. The warp bending rigidity of fabric 5 0 12345 is clearly higher than the weft bending rigidity fabric (0.176 and 0.127 g.cm2/cm, respectively)*. Fig.11. The fold numbers of the S3 seamed samples The linear proportional relationships between the DCs of initial fabrics and the seamed samples were found. Most correlation coefficients are significant (Fig. 12, 13, 14). The factors of variable showed that S1 warp seams have more the effect on the DC than S1 bias and followed by S1 weft seams. 52 Khoa học & Công Nghệ - Số 12/Tháng 12 – 2016 Journal of Science and Technology ISBN 2354-0575 85 85 82.5 y = 0.6143x + 31.287 82.5 fabric 1 R2 = 0.7714 80 y = 0.8302x + 11.662 80 fabric 2 R2 = 0.9473 77.5 77.5 fabric 3 75 fabric 4 75 y = 0.5407x + 32.769 72.5 fabric 5 R2 = 0.8614 72.5 70 fabric-warp sewn fabric 67.5 D C of s ewn fa bric (%70 ) fabric-weft sewn fabric DC of warp sewn fabric (%) fabric sewn warp of DC 65 67.5 fabric-bias sewn fabric F S1 S2 S3 seams 65 65 67.5 70 72.5 75 77.5 80 82.5 85 Fig.15. The DCs of warp seamed samples DC of fabric (%) In comparison with the DCs of the initial Fig.12. Relationship between the DC of the fabric fabrics, the DCs of S1 warp seamed samples were and S1 seamed sample decreased, except fabric 4, the increase of the DC is not much (0.4%), the DCs of S2 warp seamed 82 y = 0.6445x + 28.446 y = 0.722x + 21.024 samples were increased (except fabric 5) and the 80 R2 = 0.7065 R2 = 0.8638 78 DCs of S3 warp seamed samples were decreased 76 74 (except fabric 2) (Fig. 15). The drape shapes of the fabric-warp sewn fabric 72 fabric-weft sewn fabric S1 warp (fabric 1, 5) and S3 warp (fabric 2, 3, 4, 5) y = 0.7525x + 18.116 70 fabric-bias sewn fabric 2 DC of sewnfabric (%) R = 0.9035 68 samples are more regularly than initial fabrics and 66 65 67 69 71 73 75 77 79 81 83 85 another warp seamed samples. In most of cases, DC of fabric (%) the fold numbers of the warp seamed samples were Fig.13. Relationship between the DC of the fabric decreased or remained the same when compared and S2 seamed sample with fabrics without seam, except the S1 and S3 warp seamed samples on fabric 5. 85 85 83 82.5 fabric 1 81 y = 0.7511x + 17.749 80 79 fabric 2 R2 = 0.8974 77.5 77 fabric 3 75 75 y = 0.4792x + 38.249 fabric 4 73 72.5 R2 = 0.594 71 fabric-wapr sewn fabric 70 fabric 5 DC of sewn fabric (%) fabric sewn of DC 69 fabric-weft sewn fabric 67.5 y = 1.096x - 8.5936 67 fabric-bias sewn fabric R2 = 0.9223 65 DCof weft sewn fabric (%) 65 F S1 S2 S3 65 67 69 71 73 75 77 79 81 83 85 seams DC of fabric (%) Fig.16. The DCs of weft seamed samples Fig.14. Relationship between the DC of the fabric and S3 seamed sample The DCs of S1 weft seamed samples were S2, S3 bias seams have more the effect on highest, followed by S2 and S3, except fabric 5 the DC than warp and followed by weft seams. In (Fig. 16). Absolute maximums of the increase are three studied seam types, the factors of variable 6.01; 5.44 and 1.3%, respectively. The drape shapes also showed that the DC was mostly affected by of the S1 (fabric 2, 3, 5), S2 (fabric 2, 4) and S3 the S3 bias seams, followed by the S1 warp and S2 (fabric 1) weft seamed samples are more regularly bias seams. The S3 weft seams affect at least the than initial fabrics and another weft seamed DC. samples. The fold numbers of the weft seamed samples were increased or remained the same when compared with fabrics without seams on five studied fabrics. Khoa học & Công Nghệ - Số 12/Tháng 12 – 2016 Journal of Science and Technology 53 ISBN 2354-0575 85 fabric 4, the DC was mostly affected by the S2 bias 82.5 seam (1.97%), and was affected least by the S1 warp fabric 1 80 77.5 fabric 2 seam (0.4%). For the samples of fabric 5, the DC fabric 3 75 was mostly affected by the S3 weft seam (6.17%), 72.5 fabric 4 70 fabric 5 and was affected least by the S3 bias seam (0.13%). 67.5 DC of DC bias sewn fabric (%) 65 Linear proportional significant relationships F S1 S2 S3 se a m s exist between the DCs of studied initial fabrics and the seamed samples in the warp, weft, bias directions Fig.17. The DCs of bias seamed samples and S1, S2, S3 seam types. The R-squared value is The DCs of the S1 bias seamed samples on highest as the S1 warp samples were considered (R2 = fabric 5 were mostly varied (5.17%). The DCs of 0.947). This coefficient is lowest as the S3 weft S2 bias seamed samples were varied not much. samples were considered (R2 = 0.590). If the DC of The maximum variation is 2.11%. The DCs of S3 initial fabric increases, the DC of studied seamed bias seamed samples were decreased (Fig. 16). sample increases in trend. Absolute maximum of the decrease is 4.31%. The The drape shape and the number of folds drape shapes of the S1 (fabric 1, 4), S2 (fabric 4) for the seamed samples were varied depending and S3 (fabric 5) bias seamed samples are more direction and seam type. The drape shapes of regularly than another bias seamed samples. seamed samples were regularly adjusted by S1 warp (fabrics 4, 5), S1 weft (fabrics 2, 3, 5), S1 3. Conclusions bias (fabric3, 4), S2 weft (fabric 4), S2 bias Three types of stitches 301, 401 and 504 (fabrics 3, 4), S3 warp (fabric 3), S3 weft (fabrics have been employed on five cotton woven fabrics. 3, 5) and S3 bias seams (fabric 5). The drape coefficients differ between the fabrics Understanding the influence of seam types also between the diametral seam types and and their directions on fabric drape behaviour directions but the differences are not significantly. would be important for incorporating into the For the samples of fabrics 1, 3, the DC was mostly computer simulation of cloth. Further research is affected by the S1 weft seam (absolute maximums of required to predict the drape of garments. the increases are 3.33 and 6.01%, respectively), and was affected least by the S1 warp seam. For the samples of fabric 2, the DC was mostly affected by the S3 bias seam (4.31%), and was affected least by the S2 warp seam (0.09%). For the samples of References [1]. British Standards Institution, Methods of Test for Textiles - BS 5058:1973. [2]. Hu, J. and Chung, S., Drape Behavior of Woven Fabrics with Seams, Textile Res. J., Vol.68, No. 12, p. 913-919, (1998). [3]. Hu, J. and Chung, S., Bending behaviour of woven fabrics with vertical seams,Textile Res. J., 70 No. 2, pp. 148-53, 2000. [4]. Simona Jevšnik and Darja Žuni –Lojen, Drape Behaviour of Seamed Fabrics, Fibers and Polymers, Vol.8, No.5, p550-557, 2007. [5]. Ashok Itagi , Arindam Basu, Drape Behaviour Of Silk Apparel Fabrics With Radial Seams, International Journal of Engineering Research & Technology, Vol. 1 Issue 8, October 2012. 54 Khoa học & Công Nghệ - Số 12/Tháng 12 – 2016 Journal of Science and Technology ISBN 2354-0575 [6]. Nuray, Ucar, Kalaoglu, Fatma, Bahtiyar, Duygu, Bilac, Ozan Emre, Investigating the Drape Behavior of Seamed Knit Fabrics with Image Analysis, Textile Res. J., Feb (2004). [7]. Suda, Noriko, Nagasaka, Tsune, Dependency of Various Sewing Conditions on the Bending Property of Seams, Report of Polymeric Materials Res. Ins., Japan, No. 142, p. 47-55, (1984). [8]. R. S. Kaushal, B. K. Behera, H. Roedel, and A. Schenk, Effect of sewing and fusing of interlining on drape behaviour of suiting fabrics, Int. J. Cloth. Sci. Technol., Vol. 17(2), p75- 90, (2005). [9]. V. Sidabraite and V. Masteikaite, A preliminary study for evaluation of skirt asymmetric drape, Int. J. Cloth. Sci. Technol., 14(5), p286- 298, (2002). ẢNH HƯỞNG CỦA ĐƯỜNG MAY TỚI ĐẶC TÍNH RỦ CỦA VẢI BÔNG DỆT THOI Tóm tắt Rủ là một trong những đặc tính quan trọng của vải có ảnh hưởng đáng kể đến chất lượng của trang phục. Cấu trúc các chi tiết mẫu và các đường may có ảnh hưởng nhiều đến độ rủ của sản phẩm sau khi may. Xác định được ảnh hưởng của đường may đến đặc tính rủ của vải góp phần xây dựng cơ sở cho việc lựa chọn cấu trúc, hướng của đường may liên kết phù hợp với yêu cầu thẩm mỹ và chất lượng hình dáng của sản phẩm may. Bài báo này giới thiệu ảnh hưởng của 3 loại đường may liên kết phổ biến lên đặc tính rủ của 5 vải bông dệt thoi có khối lượng trung bình. Ba loại đường liên kết được hình thành từ các mũi may thắt nút 301, móc xích 401 và 504, được may theo đường kính của mẫu vải hình tròn cùng hướng sợi dọc, ngang và thiên 45o. Các đặc trưng rủ của vải ban đầu và vải có đường may được xác định theo tiêu chuẩn BS 5058:1973 trên thiết bị ADS-LAST. Kết quả thực nghiệm cho thấy sự khác biệt của hệ số rủ của mẫu sau khi may không nhiều, hình dạng rủ và số nếp uốn của mẫu thay đổi khi thay đổi loại và hướng đường may. Tồn tại quan hệ tuyến tính đáng kể giữa hệ số rủ của mẫu trước và sau khi may trên các vải đã nghiên cứu. Từ khóa: Hệ số rủ, đường may, hình dạng bóng rủ Khoa học & Công Nghệ - Số 12/Tháng 12 – 2016 Journal of Science and Technology 55
File đính kèm:
effect_of_seams_on_drape_behaviour_of_cotton_woven_fabrics.pdf