Determining of the laser heat flux for three - dimensional conduction model by the sequential method
In recent years, the rapid development of laser processing technology has gradually
replaced the traditional processing techniques. Comparing the conventional machining
processing, laser processing technology is not affected by the wear of the tool and the
friction during processing because of its non-contact property. Moreover, laser processing
technology has many advantages, such as high energy density, quick fabrication, high
precision, and low cost and non-pollution [1,2].
The absorbed energy of a laser beam known as laser heat flux is an important parameter in laser processing such as laser cladding, laser surface hardening, and laser welding.
However, the direct measurement of this parameter during the process is difficult. As a
result, many researchers used the inverse method to determine this parameter. For instance, Wang et al. [3] calculated this parameter on the surface. His work used the conjugate gradient method (CGM) in the surface hardening process by the laser to determine
this parameter inversely. Chen and Xu [4] applied Laplace transform to the governing
differential equation, boundary conditions, and initial condition to evaluate absorption
in the heating process for surface by laser. Yang et al. [5] applied CGM to estimate the
absorbed energy of the laser beam and depth of the melt zone simultaneously. Sun et
al. [6] used the method of direct sensitivity coefficient for the determining of the surface
heat flux and the absorptivity of the coating surface in the surface hardening process by
the laser. Nevertheless, these studies were only performed on a one-dimensional and
two-dimensional model. The obtained results may be less accurate than the truly threedimensional model. Nguyen and Yang [7] used the inverse algorithm in the modified
Newton–Raphson method (MNR method) to determine laser power in order to reach the
required width penetration in the laser welding process. Through two examples, with
every 7 iterations in each example, the speed of the method being applied is excellent.
The error between the estimated width penetration and the setup width penetration in
the two examples, respectively, is 0.25% and 0.2%. Nguyen and Yang [8] continued to use
the MNR method in estimating the absorption coefficient, which is one of the very important parameters during laser welding. The determination of this parameter depends on
the temperature is the complex non-linear inverse problem. The long rod with the small
diameter model is heated by the Gauss distribution laser source. The results of the two
examples in this study show that the number of future time step increases, the measurement error decreases, the determined value increases, and this result with the constant
relation of the future time step is less exact the linear type of the future time. Nguyen et
al. [9] used the sequential method to inverse evaluation of the absorption coefficient for
the spot laser welding (three-dimensional cylindrical workpiece) with Friedman’s heat
source model. This assessment, through two examples, includes two main processes: direct analysis and inverse analysis. Firstly, this study applied the effective heat capacity
method to find temperature fields by finite element method (FEM) with the boundary
conditions, and the absorption coefficient assumed as specific values. In the inverse analysis process, the unknown variables are obtained from exploring points systematically
by the iterative method. With several iterations are performed, the intermediate values
are substituted for the undetermined variables for the next analysis. The numerical results show that the sequential method is the inverse solution to estimate the absorption
coefficient with high accuracy and stability in the spot weld by laser.
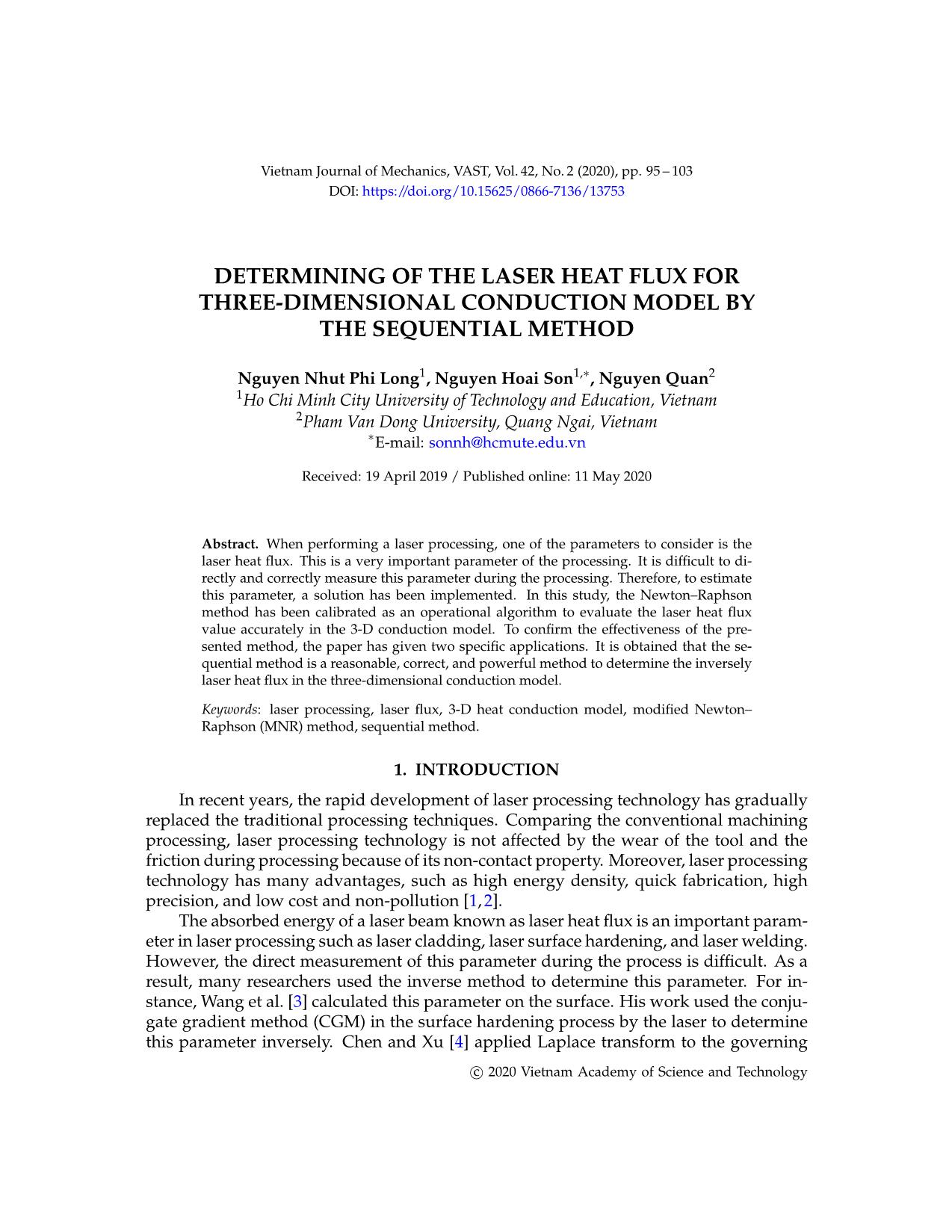
Trang 1
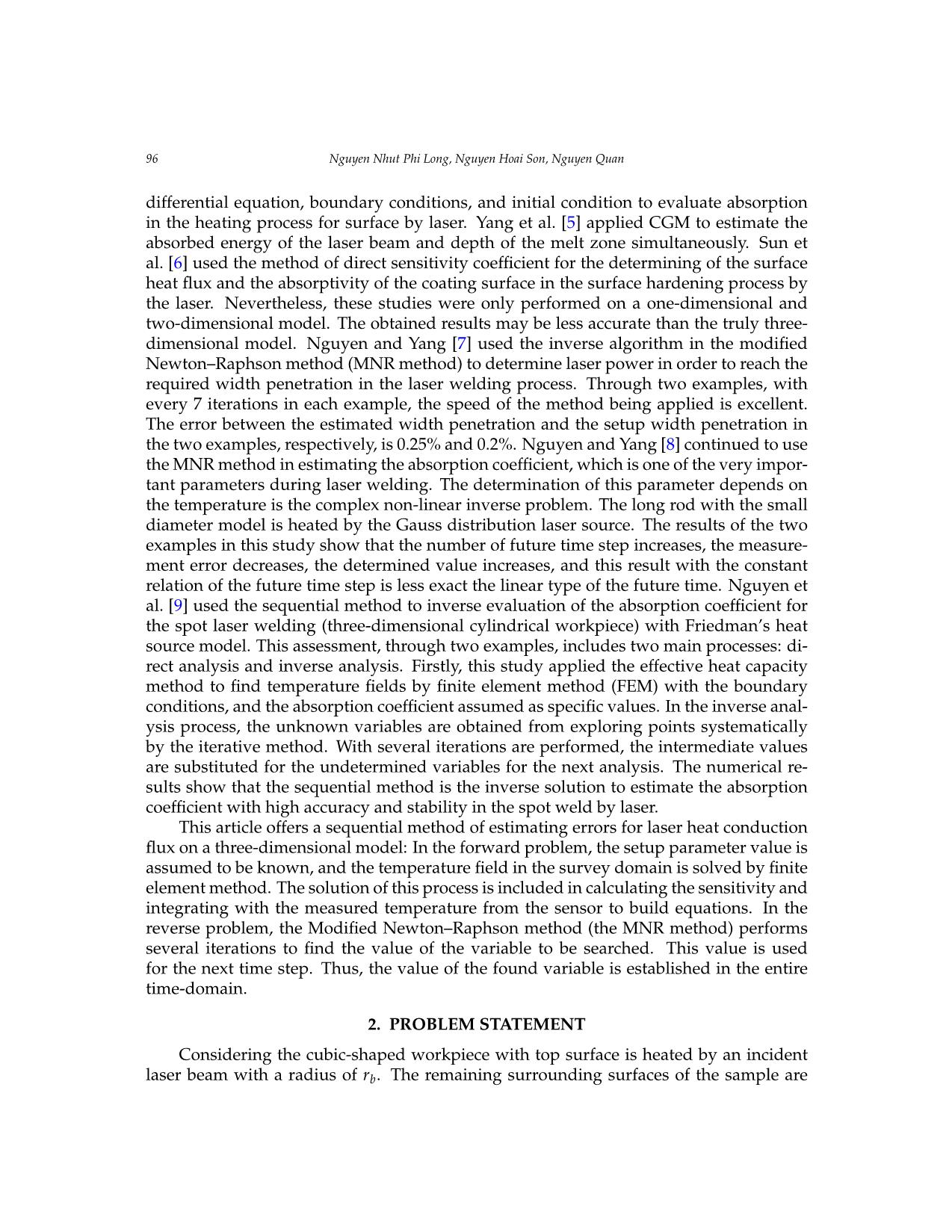
Trang 2
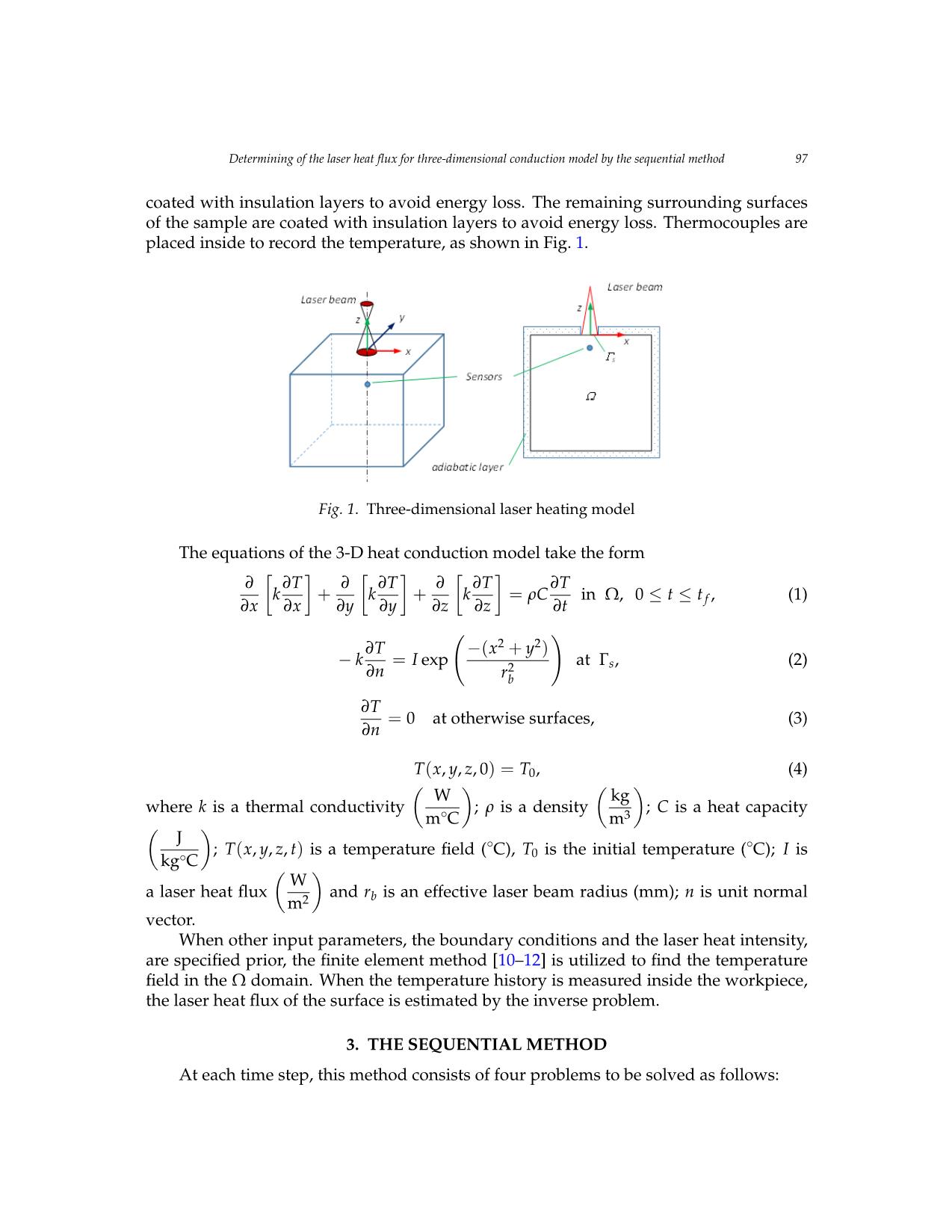
Trang 3
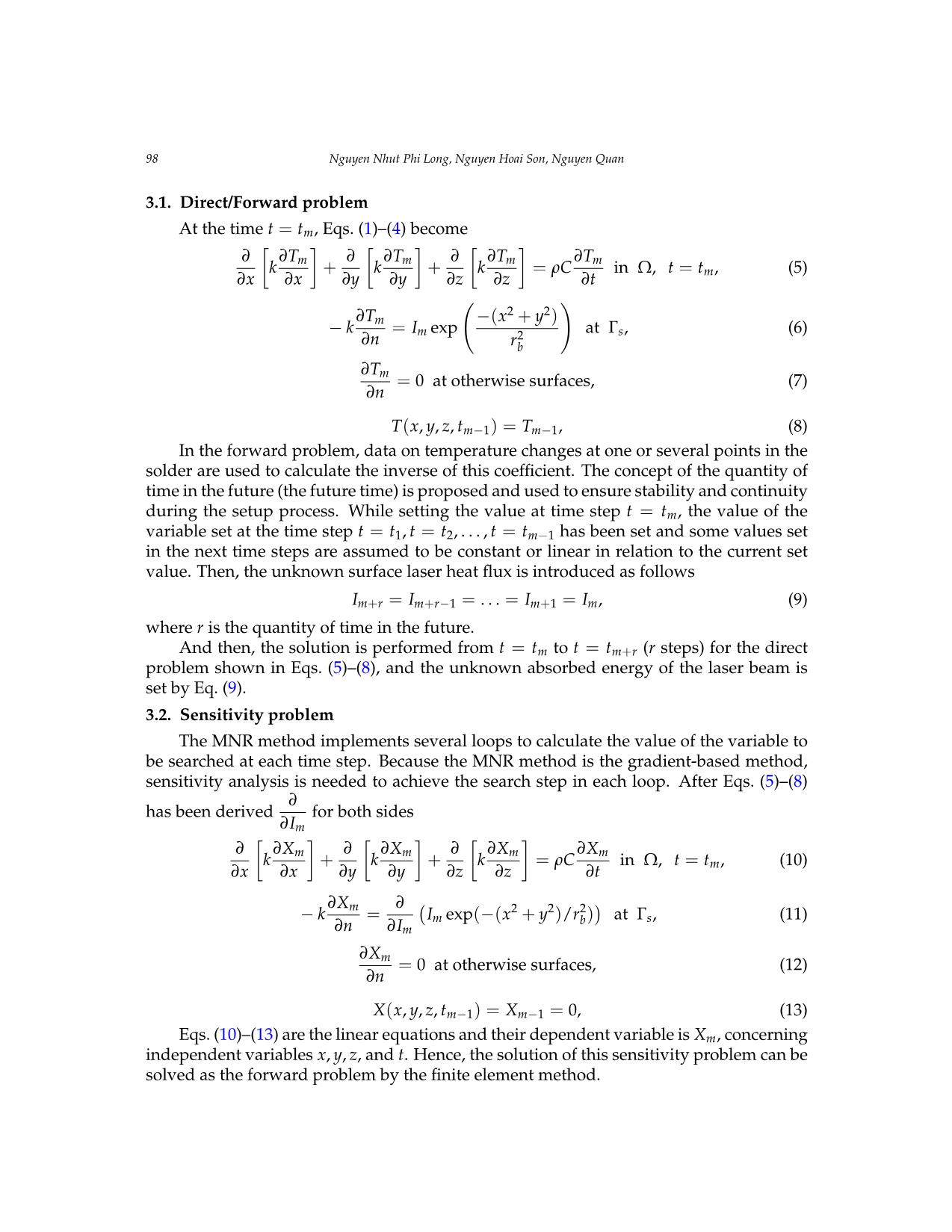
Trang 4
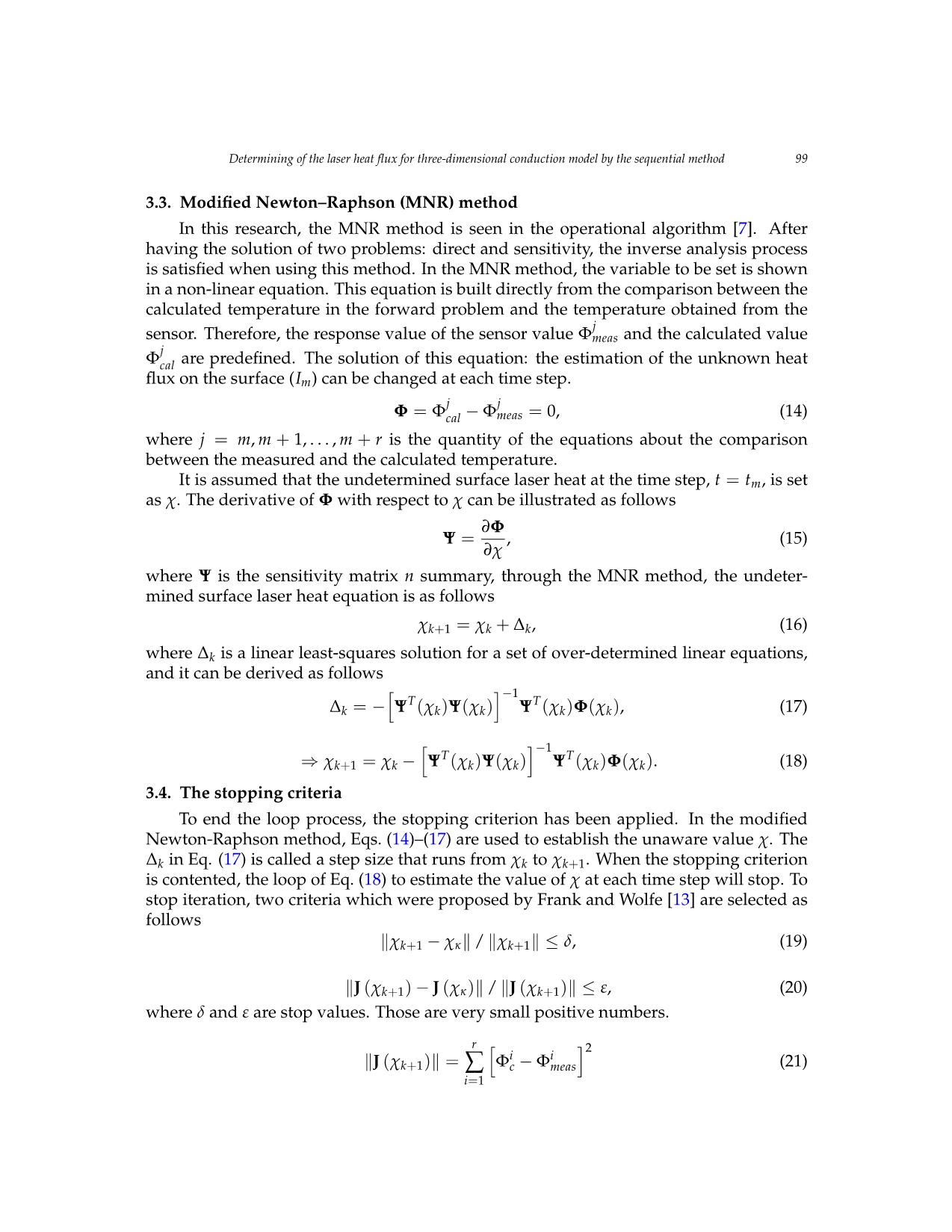
Trang 5
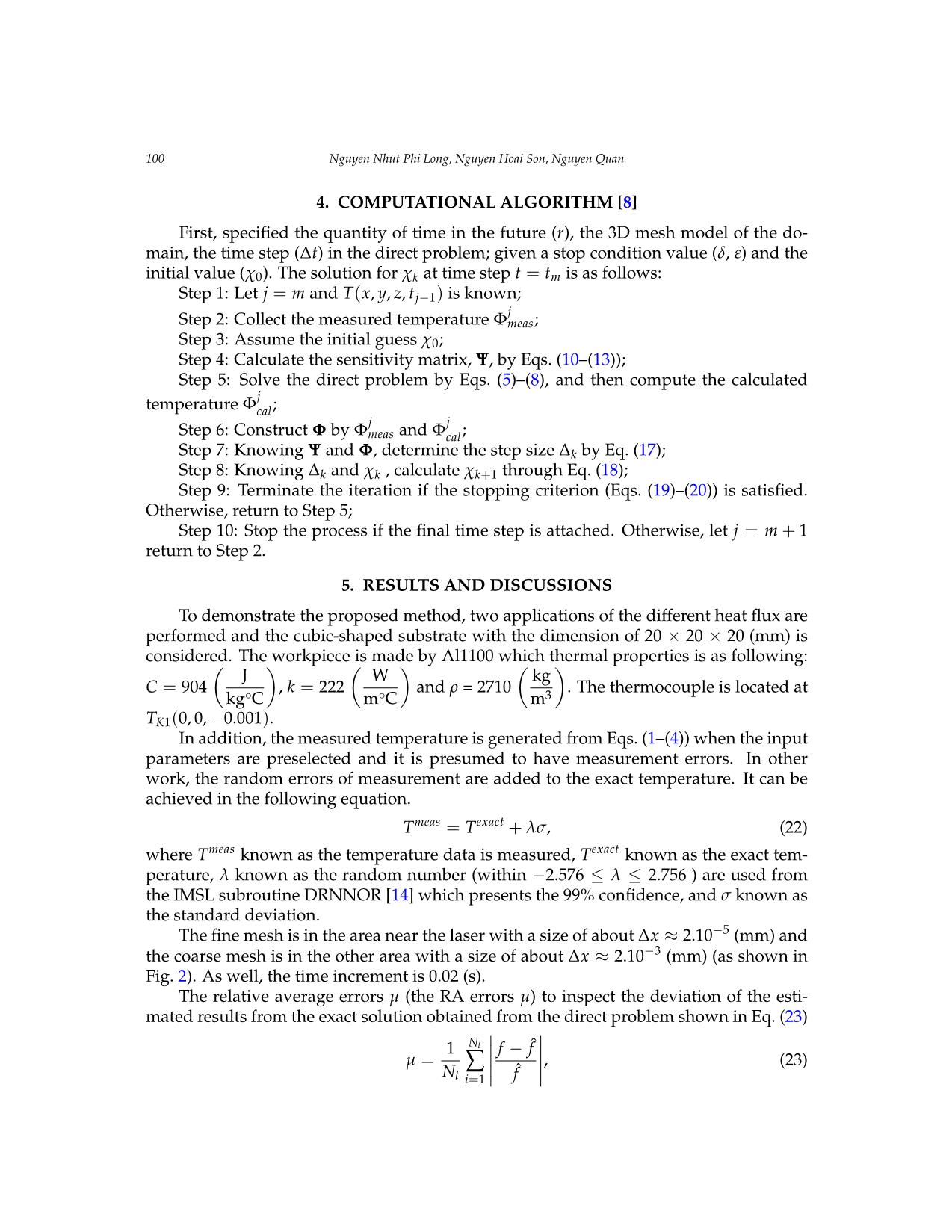
Trang 6
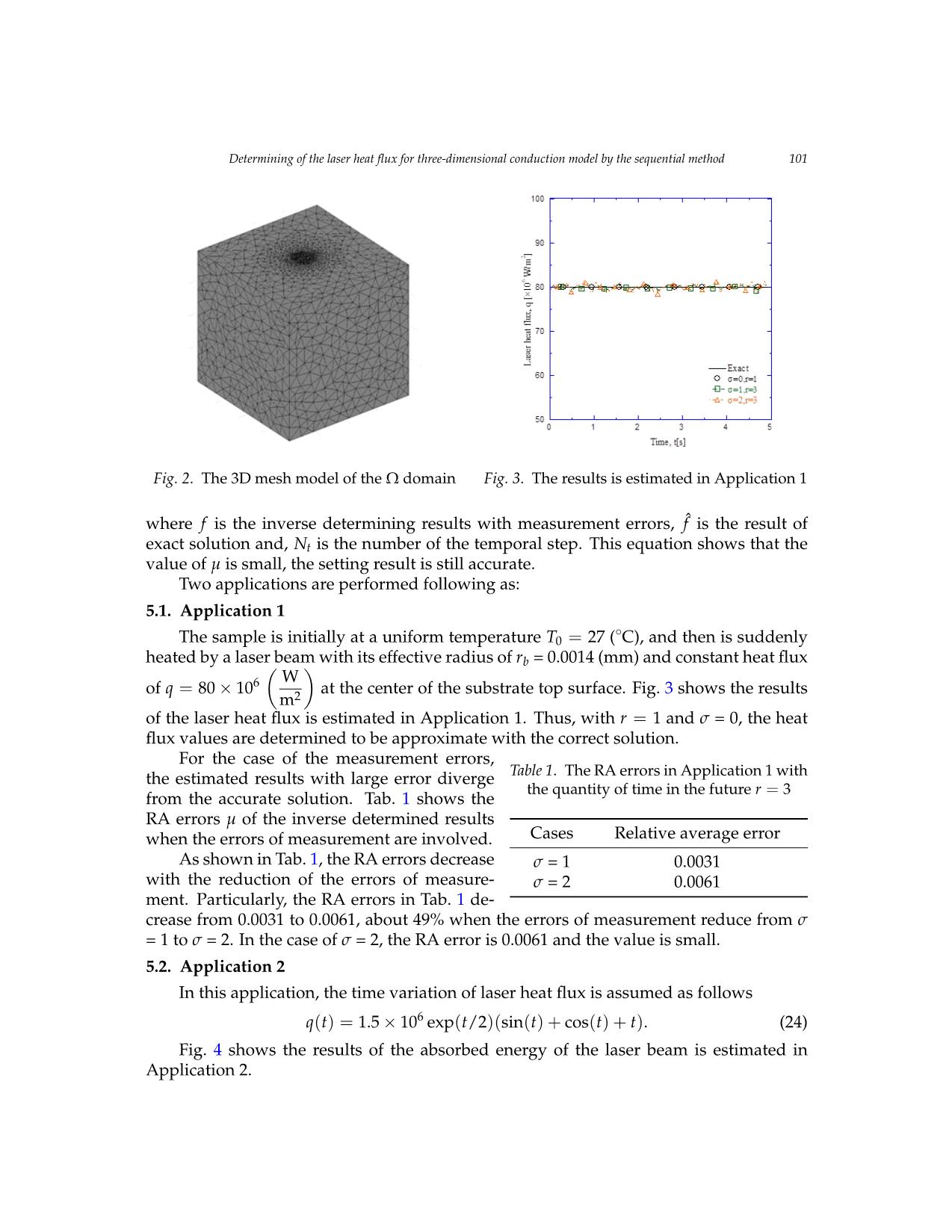
Trang 7
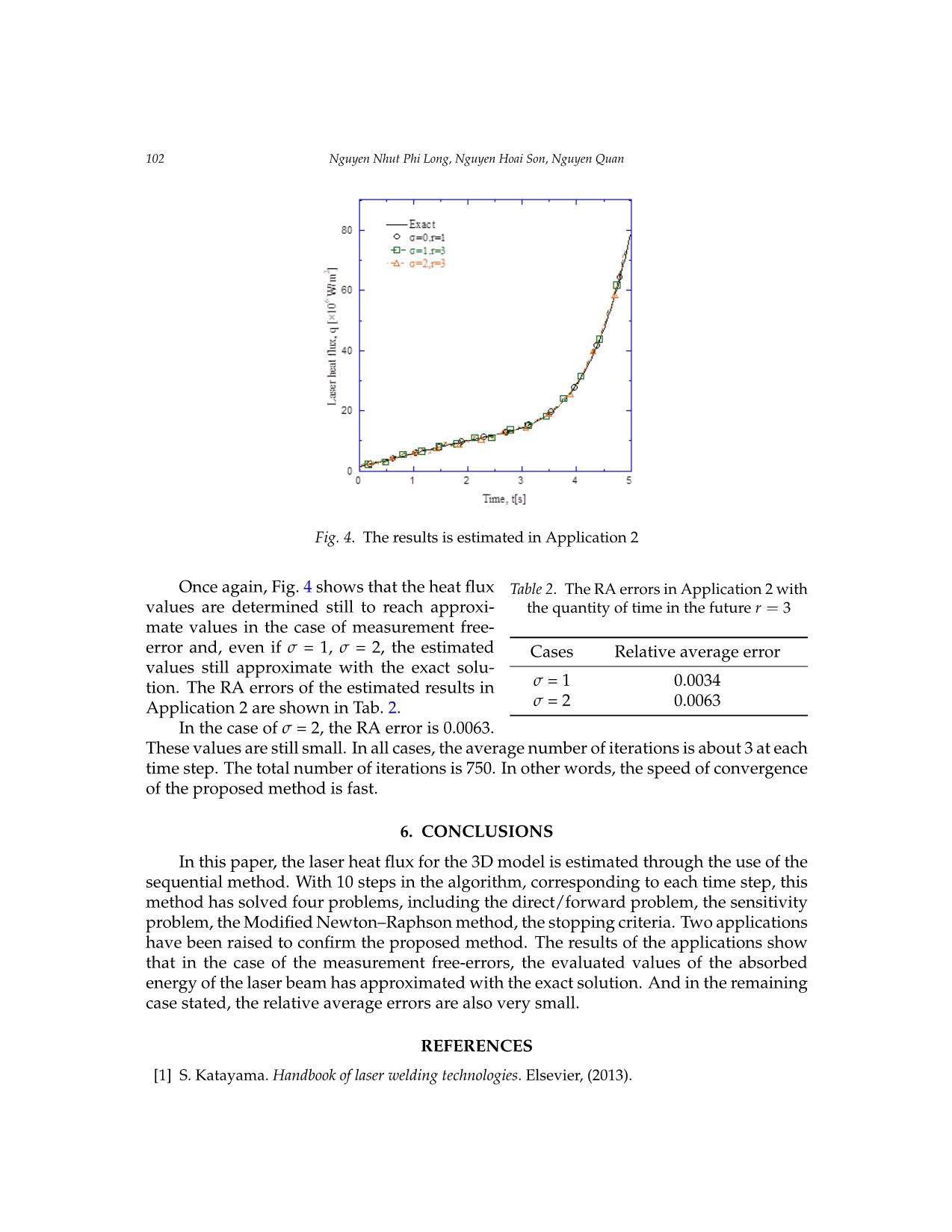
Trang 8
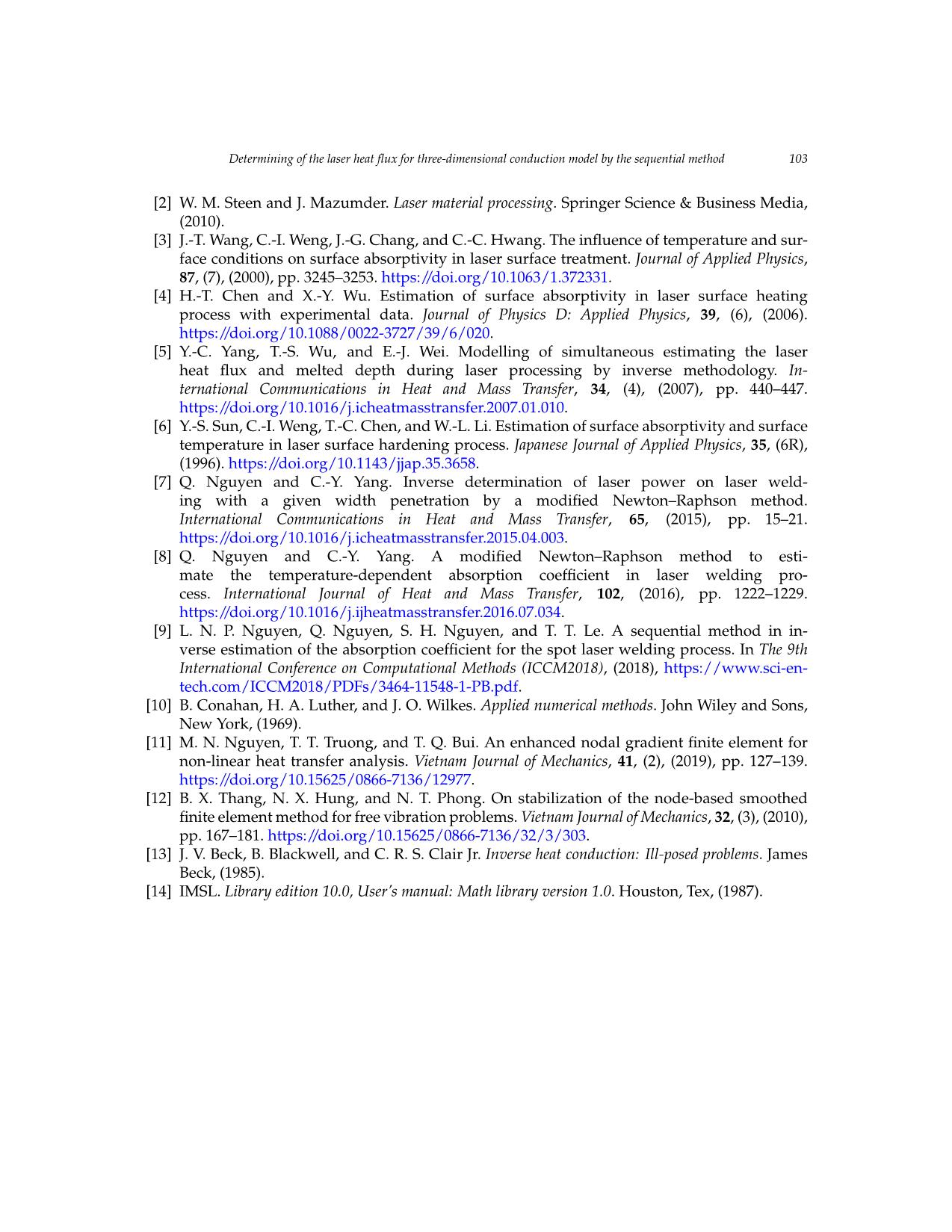
Trang 9
Tóm tắt nội dung tài liệu: Determining of the laser heat flux for three - dimensional conduction model by the sequential method
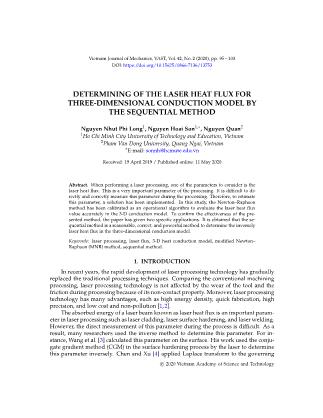
Vietnam Journal of Mechanics, VAST, Vol.42, No. 2 (2020), pp. 95 – 103 DOI: https://doi.org/10.15625/0866-7136/13753 DETERMINING OF THE LASER HEAT FLUX FOR THREE-DIMENSIONAL CONDUCTION MODEL BY THE SEQUENTIAL METHOD Nguyen Nhut Phi Long1, Nguyen Hoai Son1,∗, Nguyen Quan2 1Ho Chi Minh City University of Technology and Education, Vietnam 2Pham Van Dong University, Quang Ngai, Vietnam ∗E-mail: sonnh@hcmute.edu.vn Received: 19 April 2019 / Published online: 11 May 2020 Abstract. When performing a laser processing, one of the parameters to consider is the laser heat flux. This is a very important parameter of the processing. It is difficult to di- rectly and correctly measure this parameter during the processing. Therefore, to estimate this parameter, a solution has been implemented. In this study, the Newton–Raphson method has been calibrated as an operational algorithm to evaluate the laser heat flux value accurately in the 3-D conduction model. To confirm the effectiveness of the pre- sented method, the paper has given two specific applications. It is obtained that the se- quential method is a reasonable, correct, and powerful method to determine the inversely laser heat flux in the three-dimensional conduction model. Keywords: laser processing, laser flux, 3-D heat conduction model, modified Newton– Raphson (MNR) method, sequential method. 1. INTRODUCTION In recent years, the rapid development of laser processing technology has gradually replaced the traditional processing techniques. Comparing the conventional machining processing, laser processing technology is not affected by the wear of the tool and the friction during processing because of its non-contact property. Moreover, laser processing technology has many advantages, such as high energy density, quick fabrication, high precision, and low cost and non-pollution [1,2]. The absorbed energy of a laser beam known as laser heat flux is an important param- eter in laser processing such as laser cladding, laser surface hardening, and laser welding. However, the direct measurement of this parameter during the process is difficult. As a result, many researchers used the inverse method to determine this parameter. For in- stance, Wang et al. [3] calculated this parameter on the surface. His work used the conju- gate gradient method (CGM) in the surface hardening process by the laser to determine this parameter inversely. Chen and Xu [4] applied Laplace transform to the governing c 2020 Vietnam Academy of Science and Technology 96 Nguyen Nhut Phi Long, Nguyen Hoai Son, Nguyen Quan differential equation, boundary conditions, and initial condition to evaluate absorption in the heating process for surface by laser. Yang et al. [5] applied CGM to estimate the absorbed energy of the laser beam and depth of the melt zone simultaneously. Sun et al. [6] used the method of direct sensitivity coefficient for the determining of the surface heat flux and the absorptivity of the coating surface in the surface hardening process by the laser. Nevertheless, these studies were only performed on a one-dimensional and two-dimensional model. The obtained results may be less accurate than the truly three- dimensional model. Nguyen and Yang [7] used the inverse algorithm in the modified Newton–Raphson method (MNR method) to determine laser power in order to reach the required width penetration in the laser welding process. Through two examples, with every 7 iterations in each example, the speed of the method being applied is excellent. The error between the estimated width penetration and the setup width penetration in the two examples, respectively, is 0.25% and 0.2%. Nguyen and Yang [8] continued to use the MNR method in estimating the absorption coefficient, which is one of the very impor- tant parameters during laser welding. The determination of this parameter depends on the temperature is the complex non-linear inverse problem. The long rod with the small diameter model is heated by the Gauss distribution laser source. The results of the two examples in this study show that the number of future time step increases, the measure- ment error decreases, the determined value increases, and this result with the constant relation of the future time step is less exact the linear type of the future time. Nguyen et al. [9] used the sequential method to inverse evaluation of the absorption coefficient for the spot laser welding (three-dimensional cylindrical workpiece) with Friedman’s heat source model. This assessment, through two examples, includes two main processes: di- rect analysis and inverse analysis. Firstly, this study applied the effective heat capacity method to find temperature fields by finite element method (FEM) with the boundary conditions, and the absorption coefficient assumed as specific values. In the inverse anal- ysis process, the unknown variables are obtained from exploring points systematical ... M STATEMENT Considering the cubic-shaped workpiece with top surface is heated by an incident laser beam with a radius of rb. The remaining surrounding surfaces of the sample are Determining of the laser heat flux for three-dimensional conduction model by the sequential method 97 coated with insulation layers to avoid energy loss. The remaining surrounding surfaces of the sample are coated with insulation layers to avoid energy loss. Thermocouples are placed inside to record the temperature, as shown in Fig.1. Fig. 1. Three-dimensional laser heating model The equations of the 3-D heat conduction model take the form ∂ ∂T ∂ ∂T ∂ ∂T ∂T k + k + k = ρC in Ω, 0 ≤ t ≤ t , (1) ∂x ∂x ∂y ∂y ∂z ∂z ∂t f ! ∂T −(x2 + y2) − = k I exp 2 at Γs, (2) ∂n rb ∂T = 0 at otherwise surfaces, (3) ∂n T(x, y, z, 0) = T0, (4) W kg where k is a thermal conductivity ; ρ is a density ; C is a heat capacity m◦C m3 J ; T(x, y, z, t) is a temperature field (◦C), T is the initial temperature (◦C); I is kg◦C 0 W a laser heat flux and r is an effective laser beam radius (mm); n is unit normal m2 b vector. When other input parameters, the boundary conditions and the laser heat intensity, are specified prior, the finite element method [10–12] is utilized to find the temperature field in the Ω domain. When the temperature history is measured inside the workpiece, the laser heat flux of the surface is estimated by the inverse problem. 3. THE SEQUENTIAL METHOD At each time step, this method consists of four problems to be solved as follows: 98 Nguyen Nhut Phi Long, Nguyen Hoai Son, Nguyen Quan 3.1. Direct/Forward problem At the time t = tm, Eqs. (1)–(4) become ∂ ∂T ∂ ∂T ∂ ∂T ∂T k m + k m + k m = ρC m in Ω, t = t , (5) ∂x ∂x ∂y ∂y ∂z ∂z ∂t m ! ∂T −(x2 + y2) − m = k Im exp 2 at Γs, (6) ∂n rb ∂T m = 0 at otherwise surfaces, (7) ∂n T(x, y, z, tm−1) = Tm−1, (8) In the forward problem, data on temperature changes at one or several points in the solder are used to calculate the inverse of this coefficient. The concept of the quantity of time in the future (the future time) is proposed and used to ensure stability and continuity during the setup process. While setting the value at time step t = tm, the value of the variable set at the time step t = t1, t = t2,..., t = tm−1 has been set and some values set in the next time steps are assumed to be constant or linear in relation to the current set value. Then, the unknown surface laser heat flux is introduced as follows Im+r = Im+r−1 = ... = Im+1 = Im, (9) where r is the quantity of time in the future. And then, the solution is performed from t = tm to t = tm+r (r steps) for the direct problem shown in Eqs. (5)–(8), and the unknown absorbed energy of the laser beam is set by Eq. (9). 3.2. Sensitivity problem The MNR method implements several loops to calculate the value of the variable to be searched at each time step. Because the MNR method is the gradient-based method, sensitivity analysis is needed to achieve the search step in each loop. After Eqs. (5)–(8) ∂ has been derived for both sides ∂Im ∂ ∂X ∂ ∂X ∂ ∂X ∂X k m + k m + k m = ρC m in Ω, t = t , (10) ∂x ∂x ∂y ∂y ∂z ∂z ∂t m ∂Xm ∂ 2 2 2 − k = Im exp(−(x + y )/rb) at Γs, (11) ∂n ∂Im ∂X m = 0 at otherwise surfaces, (12) ∂n X(x, y, z, tm−1) = Xm−1 = 0, (13) Eqs. (10)–(13) are the linear equations and their dependent variable is Xm, concerning independent variables x, y, z, and t. Hence, the solution of this sensitivity problem can be solved as the forward problem by the finite element method. Determining of the laser heat flux for three-dimensional conduction model by the sequential method 99 3.3. Modified Newton–Raphson (MNR) method In this research, the MNR method is seen in the operational algorithm [7]. After having the solution of two problems: direct and sensitivity, the inverse analysis process is satisfied when using this method. In the MNR method, the variable to be set is shown in a non-linear equation. This equation is built directly from the comparison between the calculated temperature in the forward problem and the temperature obtained from the j sensor. Therefore, the response value of the sensor value Φmeas and the calculated value j Φcal are predefined. The solution of this equation: the estimation of the unknown heat flux on the surface (Im) can be changed at each time step. j j Φ = Φcal − Φmeas = 0, (14) where j = m, m + 1, . . . , m + r is the quantity of the equations about the comparison between the measured and the calculated temperature. It is assumed that the undetermined surface laser heat at the time step, t = tm, is set as χ. The derivative of Φ with respect to χ can be illustrated as follows ∂Φ Ψ = , (15) ∂χ where Ψ is the sensitivity matrix n summary, through the MNR method, the undeter- mined surface laser heat equation is as follows χk+1 = χk + ∆k, (16) where ∆k is a linear least-squares solution for a set of over-determined linear equations, and it can be derived as follows −1 h T i T ∆k = − Ψ (χk)Ψ(χk) Ψ (χk)Φ(χk), (17) −1 h T i T ⇒ χk+1 = χk − Ψ (χk)Ψ(χk) Ψ (χk)Φ(χk). (18) 3.4. The stopping criteria To end the loop process, the stopping criterion has been applied. In the modified Newton-Raphson method, Eqs. (14)–(17) are used to establish the unaware value χ. The ∆k in Eq. (17) is called a step size that runs from χk to χk+1. When the stopping criterion is contented, the loop of Eq. (18) to estimate the value of χ at each time step will stop. To stop iteration, two criteria which were proposed by Frank and Wolfe [13] are selected as follows kχk+1 − χκk / kχk+1k ≤ δ, (19) kJ (χk+1) − J (χκ)k / kJ (χk+1)k ≤ ε, (20) where δ and ε are stop values. Those are very small positive numbers. r 2 h i i i kJ (χk+1)k = ∑ Φc − Φmeas (21) i=1 100 Nguyen Nhut Phi Long, Nguyen Hoai Son, Nguyen Quan 4. COMPUTATIONAL ALGORITHM [8] First, specified the quantity of time in the future (r), the 3D mesh model of the do- main, the time step (∆t) in the direct problem; given a stop condition value (δ, ε) and the initial value (χ0). The solution for χk at time step t = tm is as follows: Step 1: Let j = m and T(x, y, z, tj−1) is known; j Step 2: Collect the measured temperature Φmeas; Step 3: Assume the initial guess χ0; Step 4: Calculate the sensitivity matrix, Ψ, by Eqs. (10–(13)); Step 5: Solve the direct problem by Eqs. (5)–(8), and then compute the calculated j temperature Φcal; j j Step 6: Construct Φ by Φmeas and Φcal; Step 7: Knowing Ψ and Φ, determine the step size ∆k by Eq. (17); Step 8: Knowing ∆k and χk , calculate χk+1 through Eq. (18); Step 9: Terminate the iteration if the stopping criterion (Eqs. (19)–(20)) is satisfied. Otherwise, return to Step 5; Step 10: Stop the process if the final time step is attached. Otherwise, let j = m + 1 return to Step 2. 5. RESULTS AND DISCUSSIONS To demonstrate the proposed method, two applications of the different heat flux are performed and the cubic-shaped substrate with the dimension of 20 × 20 × 20 (mm) is considered. The workpiece is made by Al1100 which thermal properties is as following: J W kg C = 904 , k = 222 and ρ = 2710 . The thermocouple is located at kg◦C m◦C m3 TK1(0, 0, −0.001). In addition, the measured temperature is generated from Eqs. (1–(4)) when the input parameters are preselected and it is presumed to have measurement errors. In other work, the random errors of measurement are added to the exact temperature. It can be achieved in the following equation. Tmeas = Texact + λσ, (22) where Tmeas known as the temperature data is measured, Texact known as the exact tem- perature, λ known as the random number (within −2.576 ≤ λ ≤ 2.756 ) are used from the IMSL subroutine DRNNOR [14] which presents the 99% confidence, and σ known as the standard deviation. The fine mesh is in the area near the laser with a size of about ∆x ≈ 2.10−5 (mm) and the coarse mesh is in the other area with a size of about ∆x ≈ 2.10−3 (mm) (as shown in Fig.2). As well, the time increment is 0.02 (s). The relative average errors µ (the RA errors µ) to inspect the deviation of the esti- mated results from the exact solution obtained from the direct problem shown in Eq. (23) 1 Nt f − fˆ µ = , (23) ∑ ˆ Nt i=1 f Determining of the laser heat flux for three-dimensional conduction model by the sequential method 101 Fig. 2. The 3D mesh model of the Ω domain Fig. 3. The results is estimated in Application 1 where f is the inverse determining results with measurement errors, fˆ is the result of exact solution and, Nt is the number of the temporal step. This equation shows that the value of µ is small, the setting result is still accurate. Two applications are performed following as: 5.1. Application 1 ◦ The sample is initially at a uniform temperature T0 = 27 ( C), and then is suddenly heated by a laser beam with its effective radius of rb = 0.0014 (mm) and constant heat flux W of q = 80 × 106 at the center of the substrate top surface. Fig.3 shows the results m2 of the laser heat flux is estimated in Application 1. Thus, with r = 1 and σ = 0, the heat flux values are determined to be approximate with the correct solution. For the case of the measurement errors, Table 1 the estimated results with large error diverge . The RA errors in Application 1 with the quantity of time in the future r = 3 from the accurate solution. Tab.1 shows the RA errors µ of the inverse determined results when the errors of measurement are involved. Cases Relative average error As shown in Tab.1, the RA errors decrease σ = 1 0.0031 with the reduction of the errors of measure- σ = 2 0.0061 ment. Particularly, the RA errors in Tab.1 de- crease from 0.0031 to 0.0061, about 49% when the errors of measurement reduce from σ = 1 to σ = 2. In the case of σ = 2, the RA error is 0.0061 and the value is small. 5.2. Application 2 In this application, the time variation of laser heat flux is assumed as follows q(t) = 1.5 × 106 exp(t/2)(sin(t) + cos(t) + t). (24) Fig.4 shows the results of the absorbed energy of the laser beam is estimated in Application 2. 102 Nguyen Nhut Phi Long, Nguyen Hoai Son, Nguyen Quan Fig. 4. The results is estimated in Application 2 Once again, Fig.4 shows that the heat flux Table 2. The RA errors in Application 2 with values are determined still to reach approxi- the quantity of time in the future r = 3 mate values in the case of measurement free- error and, even if σ = 1, σ = 2, the estimated Cases Relative average error values still approximate with the exact solu- tion. The RA errors of the estimated results in σ = 1 0.0034 Application 2 are shown in Tab.2. σ = 2 0.0063 In the case of σ = 2, the RA error is 0.0063. These values are still small. In all cases, the average number of iterations is about 3 at each time step. The total number of iterations is 750. In other words, the speed of convergence of the proposed method is fast. 6. CONCLUSIONS In this paper, the laser heat flux for the 3D model is estimated through the use of the sequential method. With 10 steps in the algorithm, corresponding to each time step, this method has solved four problems, including the direct/forward problem, the sensitivity problem, the Modified Newton–Raphson method, the stopping criteria. Two applications have been raised to confirm the proposed method. The results of the applications show that in the case of the measurement free-errors, the evaluated values of the absorbed energy of the laser beam has approximated with the exact solution. And in the remaining case stated, the relative average errors are also very small. REFERENCES [1] S. Katayama. Handbook of laser welding technologies. Elsevier, (2013). Determining of the laser heat flux for three-dimensional conduction model by the sequential method 103 [2] W. M. Steen and J. Mazumder. Laser material processing. Springer Science & Business Media, (2010). [3] J.-T. Wang, C.-I. Weng, J.-G. Chang, and C.-C. Hwang. The influence of temperature and sur- face conditions on surface absorptivity in laser surface treatment. Journal of Applied Physics, 87, (7), (2000), pp. 3245–3253. https://doi.org/10.1063/1.372331. [4] H.-T. Chen and X.-Y. Wu. Estimation of surface absorptivity in laser surface heating process with experimental data. Journal of Physics D: Applied Physics, 39, (6), (2006). https://doi.org/10.1088/0022-3727/39/6/020. [5] Y.-C. Yang, T.-S. Wu, and E.-J. Wei. Modelling of simultaneous estimating the laser heat flux and melted depth during laser processing by inverse methodology. In- ternational Communications in Heat and Mass Transfer, 34, (4), (2007), pp. 440–447. https://doi.org/10.1016/j.icheatmasstransfer.2007.01.010. [6] Y.-S. Sun, C.-I. Weng, T.-C. Chen, and W.-L. Li. Estimation of surface absorptivity and surface temperature in laser surface hardening process. Japanese Journal of Applied Physics, 35, (6R), (1996). https://doi.org/10.1143/jjap.35.3658. [7] Q. Nguyen and C.-Y. Yang. Inverse determination of laser power on laser weld- ing with a given width penetration by a modified Newton–Raphson method. International Communications in Heat and Mass Transfer, 65, (2015), pp. 15–21. https://doi.org/10.1016/j.icheatmasstransfer.2015.04.003. [8] Q. Nguyen and C.-Y. Yang. A modified Newton–Raphson method to esti- mate the temperature-dependent absorption coefficient in laser welding pro- cess. International Journal of Heat and Mass Transfer, 102, (2016), pp. 1222–1229. https://doi.org/10.1016/j.ijheatmasstransfer.2016.07.034. [9] L. N. P. Nguyen, Q. Nguyen, S. H. Nguyen, and T. T. Le. A sequential method in in- verse estimation of the absorption coefficient for the spot laser welding process. In The 9th International Conference on Computational Methods (ICCM2018), (2018), https://www.sci-en- tech.com/ICCM2018/PDFs/3464-11548-1-PB.pdf. [10] B. Conahan, H. A. Luther, and J. O. Wilkes. Applied numerical methods. John Wiley and Sons, New York, (1969). [11] M. N. Nguyen, T. T. Truong, and T. Q. Bui. An enhanced nodal gradient finite element for non-linear heat transfer analysis. Vietnam Journal of Mechanics, 41, (2), (2019), pp. 127–139. https://doi.org/10.15625/0866-7136/12977. [12] B. X. Thang, N. X. Hung, and N. T. Phong. On stabilization of the node-based smoothed finite element method for free vibration problems. Vietnam Journal of Mechanics, 32, (3), (2010), pp. 167–181. https://doi.org/10.15625/0866-7136/32/3/303. [13] J. V. Beck, B. Blackwell, and C. R. S. Clair Jr. Inverse heat conduction: Ill-posed problems. James Beck, (1985). [14] IMSL. Library edition 10.0, User’s manual: Math library version 1.0. Houston, Tex, (1987).
File đính kèm:
determining_of_the_laser_heat_flux_for_three_dimensional_con.pdf